Como reciclar máscaras usando Filastruder
A máscara, a primeira linha de defesa contra a propagação do COVID-19, um dispositivo simples projetado para proteger contra a inalação e transmissão de agentes infecciosos, afetou a vida de bilhões de pessoas em todo o mundo.
Desde o início da pandemia global, o uso de máscaras faciais tem sido uma necessidade e em muitos casos uma obrigação, mas por todo o bem que elas fizeram, sua eliminação representa um monumental desafio ecológico que tem sido amplamente ignorado em favor de medidas mais imediatas preocupações . Estima-se que aproximadamente 129 bilhões de respiradores tenham sido usados mensalmente em todo o mundo, a maioria dos quais foi projetada para uso único. Mitigar o impacto desses equipamentos de proteção individual (EPI) em nosso meio ambiente é um grande desafio, pois as máscaras podem levar mais de 400 anos para se decompor.
De acordo com a Conferência das Nações Unidas sobre Comércio e Desenvolvimento, cerca de 75 % das máscaras e outros resíduos relacionados à pandemia acabarão em aterros sanitários ou flutuando em nossos oceanos. Como eles não podem ser incinerados ou reciclados por meio de sistemas tradicionais, o que exatamente devemos fazer com eles?
Uma equipe de pesquisa da Universidade de Bristol, na Inglaterra, parece ter encontrado a solução . A ideia da iniciativa é recolher máscaras cirúrgicas e transformá-las em material de impressão 3D, nomeadamente filamento.
Nos primeiros testes, a equipe contatou um fabricante de EPI que forneceu 1kg de máscaras com defeito (varetas nasais soltas ou ausentes) feitas de polipropileno tipo IIR grátis. As máscaras eram produtos cirúrgicos certificados que estavam em conformidade com EN14683:2019 padrões Tipo IIR.
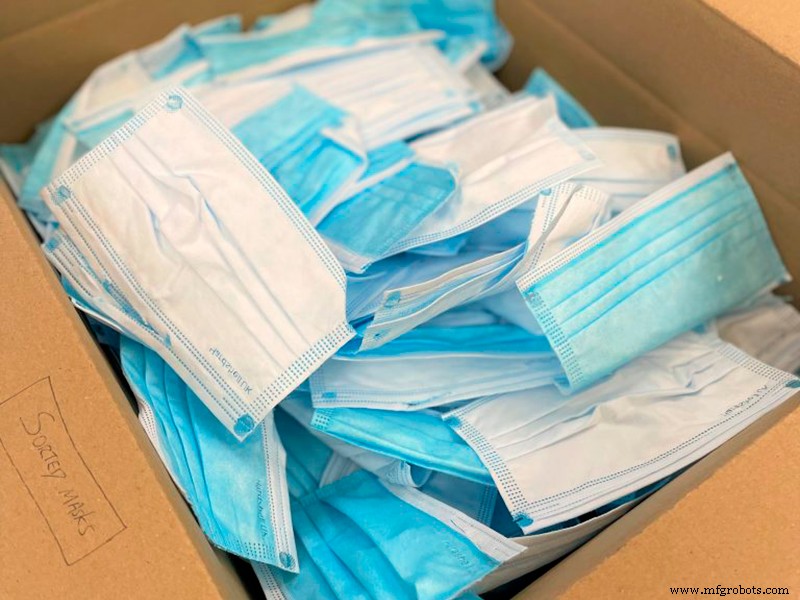
Imagem 1:Máscaras fornecidas para o projeto. Fonte:Universidade de Bristol.
O primeiro passo do processo, além de retirar os elásticos das orelhas e qualquer folha de metal que possa estar no nariz, é aquecer com um ferro de passar uma pilha de máscaras entre dois pedaços de papel antiaderente.
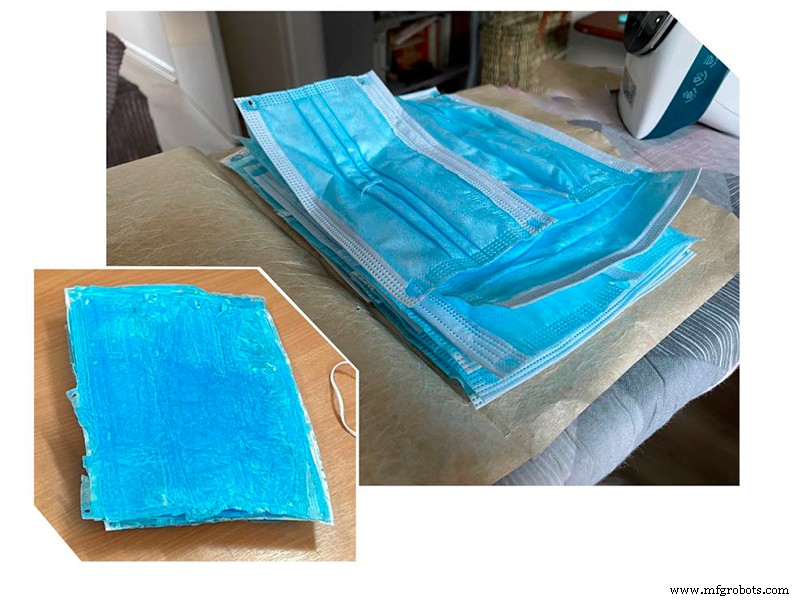
Imagem 2:Máscaras transformadas em folhas. Fonte:Universidade de Bristol.
Isso faz com que eles se derretam em uma folha sólida isso é muito mais fácil de trabalhar e evita o entupimento da retificadora. As folhas resultantes são passadas por um liquidificador para produzir grânulos finos de polipropileno azul que são adequados para o processo de extrusão.
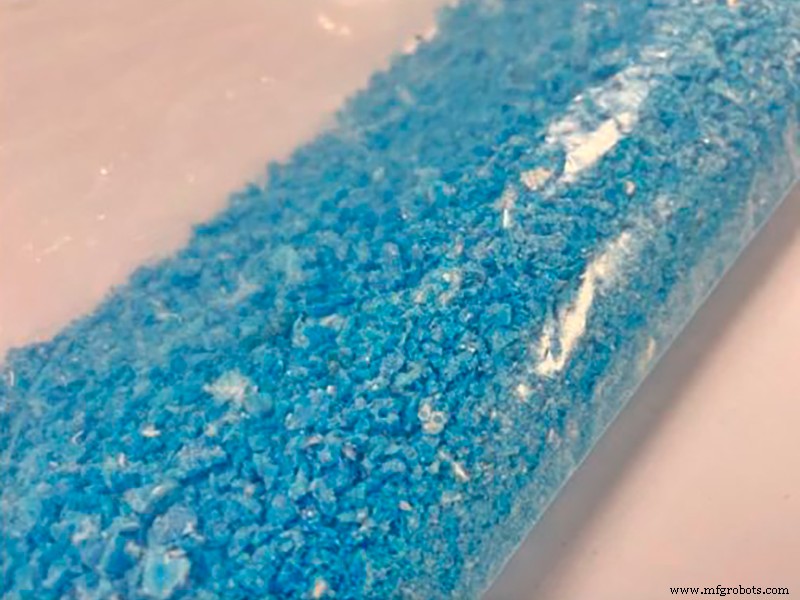
Imagem 3:Pelotas resultantes. Fonte:Universidade de Bristol.
Antes de passar para a próxima etapa, é necessário esclarecer que as máscaras são submetidas a altas temperaturas que os pesquisadores consideram suficientes para matar possíveis bactérias da COVID-19 e desinfetar o material. No entanto, os que eles usaram no projeto não haviam sido usados anteriormente.
Na terceira etapa, os pellets vão para a máquina e (a wire drawing machine) that turns them into filaments . To convert the mask material into the filament needed for a 3D printer, the researchers used Filastruder, an open source product that is constantly evolving thanks to the community of users who share their designs and configurations.
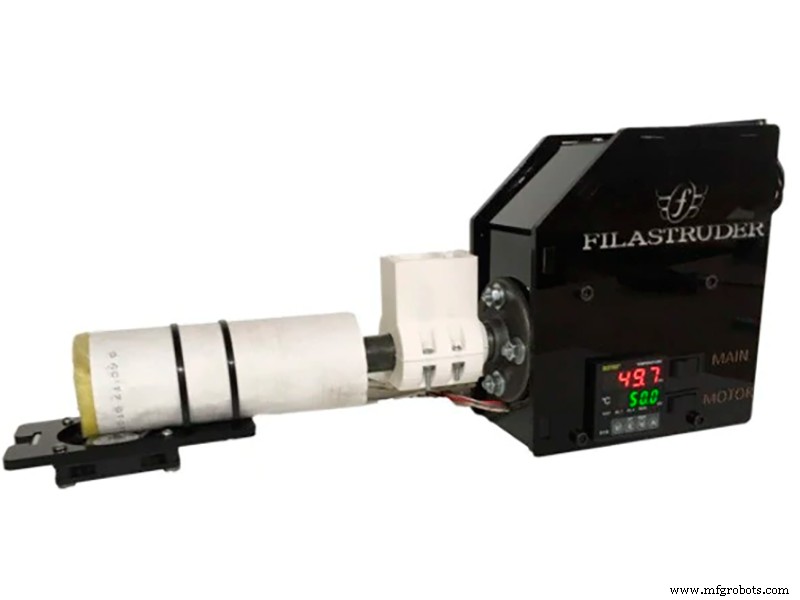
Image 4:Filastruder. Fuente:Filastruder.
The Filastruder is capable of producing filament on demand in the right colour and size for any 3D project. Its operation is simple, just set the desired extrusion temperature, wait until it is reached in the extruder, add the pellets and dyes in the chosen hopper (it can even be a plastic bottle) and turn on the gear motor to start the extrusion . To carry out the winding of the filament and facilitate its subsequent processing with a 3D printer, the ideal option is to use the Filawinder; designed especially for Filastruder users, which automatically winds the filament coming out of the drawing machine.
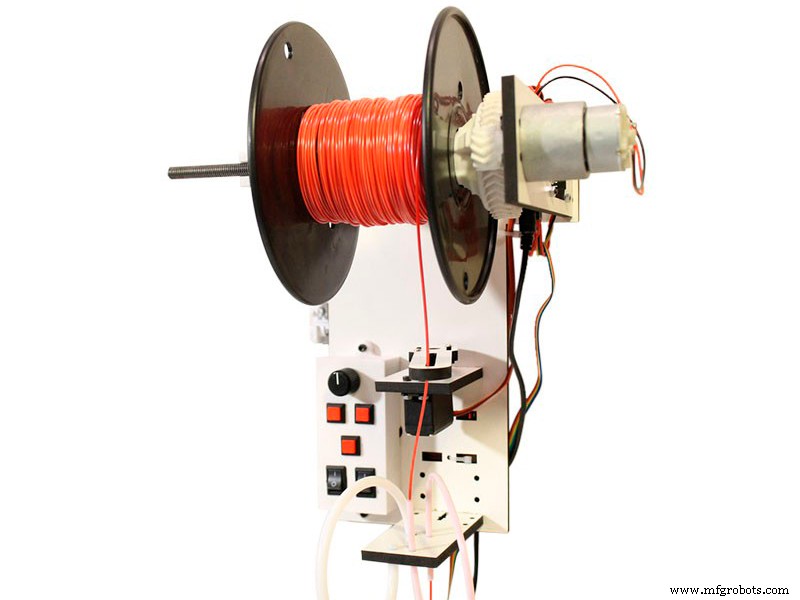
Image 5:Filawinder. Source:Filastruder.
It is advisable to place the Filastruder at a height of 1.5 m and let the filament hang down from there, so that it cools down before it touches the ground. The Filastruder should not be placed in a place where there are drafts, as these would cause the filament to oscillate and deform.
In this case, the team chose to mount the machine vertically and print a hopper to work in this position. The nozzle reached 170 °C and the pellets that passed through it were converted into filament. The team noted that in the first test the filament had only had an average diameter of 1.5 mm, but the results indicated that with further refinement it was be possible to achieve the standard 1.75 mm diameter, within a reasonable tolerance , so the nozzle was modified (drilled from 1.75 mm to 1.9 mm) and a more powerful feed mechanism was developed to get closer to the target diameter. Still, by activating the extrusion multiplier in the slicing software, the team was able to successfully print objects using the thin polypropylene filament.
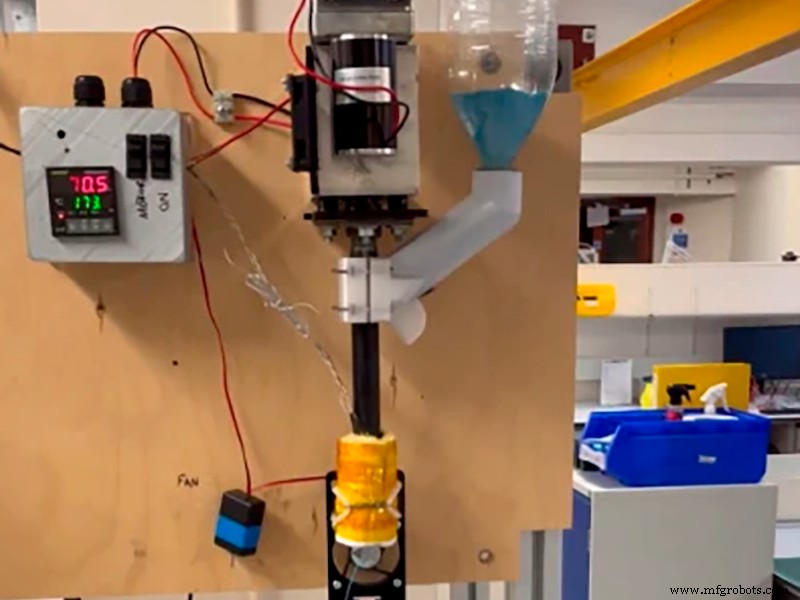
Image 6:Vertical mounting. Source:University of Bristol.
Polypropylene (PP) is notorious for being difficult to 3D print , as it does not adhere well to common printing surfaces. However, it does have good adhesion between layers. The trick employed by these scientists was to use normal transparent tape over the base, as it is often also made of PP. Using this method, it was very easy to 3D print with their limited rudimentary stock of filament on a low-cost 3D printing machine. It follows that the problems currently lie in the production of the filament and not in 3D printing with it.
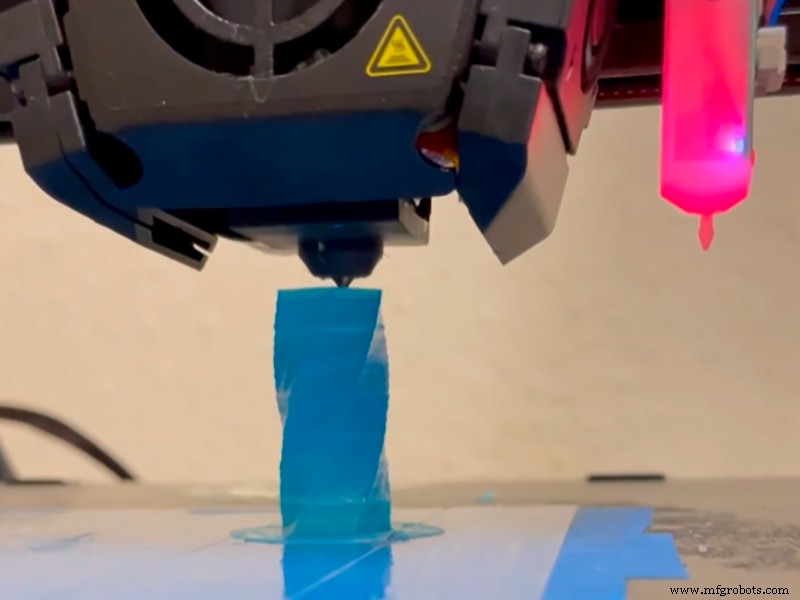
Image 7:Resulting piece. Source:University of Bristol.
The filament obtained , which is wound up, reached 7 metres in length . The piece of material that can be seen in the images provided by the University of Bristol is the result of transforming less than a third of an entire mask into filament.
Having achieved this result, the researchers are now looking at new challenges, such as the possibility of processing mixed materials by treating the mask with the handles in the same process. They also question whether the work can be automated on a large scale or whether universities would be able to create their own circular economy and oversee the distribution, collection and recycling of PPE.
Projects like the one at the University of Bristol can also be found in Spain.
For example, a group of scientists at the Universitat Politècnica de Catalunya (UPC) have devised a system for designing a mask created from used anti-covid masks . The mask has layers of recycled polypropylene fibre from discarded and properly sterilised surgical masks. A protective layer of silver oxide and cerium nanoparticles is also included, due to their antiviral and antibacterial function. The aim is to obtain a product that is protective, functional, innovative and sustainable. The recycling of used and discarded face masks begins with their autoclave sterilisation. The material is then granulated in such a way that polypropylene pellets are obtained for further processing and use to create a plastic filament which, using a 3D printer, results in a new mask. A protective coating with cerium oxide ions and silver can be applied to the printed mask, which increases its antibacterial protection. In addition to being reusable, the masks produced in this way can also be recycled into new masks, thus minimising waste generation to a minimum.
In the case of FILMA , a team made up of 4 young people, they came up with a project to recycle surgical masks that aims to give them a second life by transforming them into filament for 3D printers that can be used to create new products. Before being transformed into filament, the masks undergo a disinfection treatment. The materials are then separated and sent to a shredder that cuts them into small pieces. These pieces of plastic are mixed with some plastic pellets and finally fed into an extruder which melts the plastic, thus forming the filament. In addition to their own production of items from the filament, together with other brands, they design processes, campaigns and sustainable products to introduce the circular economy in companies and demonstrate to the new generations their commitment to the changes that are necessary for a better future.
impressao 3D
- Como criar um modelo CloudFormation usando AWS
- Passo a passo:Como obter dados de um PLC usando IIoT?
- Como você se prepara para IA usando IoT
- Como a IoT está perturbando o mundo ao nosso redor
- Como reverter uma string em Java usando recursão
- Python Average:Como encontrar a AVERAGE de uma lista em Python
- Como criar um site de comunicação do Arduino usando PHP
- Como fazer um mini osciloscópio em casa usando o Arduino Nano
- Como reciclar placas de circuito impresso
- Como evitar inconsistências ao usar tornos CNC