Laser semicondutor
Antecedentes
Um laser, que é um acrônimo para amplificação de luz por emissão estimulada de radiação, é um dispositivo que converte energia em luz. Energia elétrica ou óptica é usada para excitar átomos ou moléculas, que então emitem luz. Um laser consiste em uma cavidade, com espelhos planos ou esféricos nas extremidades, que é preenchida com material lasável. Este material pode ser excitado a um estado semi-estável pela luz ou por uma descarga elétrica. O material pode ser um cristal, vidro, líquido, corante ou gás, desde que possa ser excitado dessa forma.
A cavidade mais simples possui dois espelhos, um que reflete totalmente e outro que reflete entre 50 e 99%. Conforme a luz é refletida entre esses espelhos, a intensidade aumenta. Como a luz do laser viaja como um feixe intenso, o laser produz uma luz muito brilhante. Os feixes de laser também podem ser projetados a grandes distâncias e podem ser focados em um ponto muito pequeno.
O tipo de espelho determina o tipo de feixe. Um feixe muito brilhante, altamente monocromático (um comprimento de onda ou uma cor) e coerente é produzido quando um espelho transmite apenas 1-2% da luz. Se espelhos planos são usados, o feixe é altamente colimado (feito paralelo). O feixe sai perto de uma extremidade da cavidade quando espelhos côncavos são usados. O tipo de feixe no primeiro caso torna os lasers muito úteis na medicina, pois essas propriedades permitem ao médico direcionar a área desejada com mais precisão, evitando danos ao tecido circundante.
Um laser semicondutor converte energia elétrica em luz. Isso é possível com o uso de um material semicondutor, cuja capacidade de conduzir eletricidade está entre a dos condutores e os isolantes. Dopando um semicondutor com quantidades específicas de impurezas, o número de elétrons carregados negativamente ou buracos carregados positivamente pode ser alterado.
Comparados com outros tipos de laser, os lasers semicondutores são compactos, confiáveis e duram muito tempo. Esses lasers consistem em dois componentes básicos, um amplificador óptico e um ressonador. O amplificador é feito de um material semicondutor de gap direto baseado em substratos de arsenieto de gálio (GaAs) ou InP. Estes são compostos baseados nos elementos do Grupo III e Grupo V da tabela periódica. Ligas desses materiais são formadas nos substratos como estruturas em camadas contendo quantidades precisas de outros materiais.
O ressonador recircula continuamente a luz através do amplificador e ajuda a focalizá-la. Este componente geralmente consiste em um guia de ondas e dois espelhos planos paralelos. Esses espelhos são revestidos com um material para aumentar ou diminuir a refletividade e para melhorar a resistência a danos causados por altas densidades de potência.
O desempenho e o custo de um semicondutor dependem de sua potência de saída, brilho e vida útil operacional. A potência é importante porque determina o rendimento máximo ou a taxa de alimentação de um processo. O alto brilho, ou a capacidade de focar a saída do laser em um pequeno ponto, determina a eficiência energética. A vida útil é importante porque quanto mais tempo dura um laser, menos custa para operar, o que é especialmente crítico em aplicações industriais.
Os lasers semicondutores mais simples consistem em um único emissor que produz mais de um watt de energia de onda contínua. Para aumentar a potência, foram desenvolvidos módulos ou pilhas de barras e multibares. Uma barra é uma matriz de 10 a 50 lasers semicondutores individuais lado a lado integrados em um único chip e uma pilha é uma matriz bidimensional de várias barras. As barras podem produzir 50 watts de potência de saída e durar mais de 5.000 horas. Como essas altas potências produzem muito calor, os sistemas de resfriamento devem ser incorporados ao projeto.
História
O conceito por trás dos lasers foi proposto pela primeira vez por Albert Einstein, que mostrou que a luz consiste em energias de ondas chamadas fótons. Cada fóton possui uma energia que corresponde à frequência das ondas. Quanto mais alta a frequência, maior a energia transportada pelas ondas. Einstein e outro cientista chamado S. N. Bose desenvolveram a teoria por trás do fenômeno da tendência dos fótons de viajarem juntos.
A ação do laser foi demonstrada pela primeira vez na região das microondas em 1954 pelo vencedor do Prêmio Nobel Charles Townes e seus colegas de trabalho. Eles projetaram um feixe de moléculas de amônia por meio de um sistema de eletrodos de foco. Quando a potência de microondas de frequência apropriada foi passada através da cavidade, ocorreu a amplificação e o termo Amplificação de Microondas por Emissão Estimulada de Radiação (M.A.S.E.R.) nasceu. O termo laser foi cunhado pela primeira vez em 1957 pelo físico Gordon Gould.
Townes também trabalhou com Arthur Schawlow e os dois propuseram o laser em 1958, recebendo uma patente em 1960. O primeiro laser prático foi inventado no mesmo ano por um físico chamado Theodore Maiman, enquanto trabalhava no Hughes Research Laboratories. Este laser usava um cristal de rubi rosa rodeado por um tubo de flash fechado em uma cavidade cilíndrica de alumínio polido resfriado por ar forçado. Dois anos depois, um rubi contínuo foi feito substituindo a lâmpada de flash por uma lâmpada de arco.
Em 1962, a ação do laser em um material semicondutor foi demonstrada por Robert Hall e pesquisadores da General Electric, com outros pesquisadores dos Estados Unidos logo em seguida. Demorou cerca de outra década para o primeiro laser de diodo semicondutor ser desenvolvido e operar em temperatura ambiente, o que foi demonstrado pela primeira vez por pesquisadores russos. Bell Labs acompanhou o sucesso dos pesquisadores russos, ao mesmo tempo em que melhorou a vida útil do laser. Em 1975, o Diode Laser Labs de New Jersey lançou o primeiro laser semicondutor comercial à temperatura ambiente.
Apesar desse progresso, esses lasers ainda eram inadequados para aplicações em telecomunicações. Em vez disso, eles encontraram amplo uso (após outras melhorias de desempenho e vida útil) em discos compactos de áudio depois que a Philips (Holanda) e a Sony (Japão) desenvolveram um CD em 1980 usando um laser de diodo. No final da década, dezenas de milhões de CD players eram vendidos todos os anos. Mais recentemente, os discos de vídeo digital tornaram-se disponíveis para armazenamento óptico, que também são baseados em lasers de diodo.
À medida que a potência aumenta, os lasers semicondutores se expandem para outras aplicações. Desde 1995, o desempenho dos lasers de diodo de alta potência aumentou 25 vezes. Com essa confiabilidade mais alta, grandes grupos de lasers de diodo agora podem ser combinados para criar "pilhas" de até 25 lasers de diodo individuais.
Em 1999, as receitas de diodo laser representaram 64% de todos os lasers vendidos, contra 57% em 1996, e foram projetadas para atingir 69% em 2000. Em termos de unidades vendidas, os lasers semicondutores representaram cerca de 99% do total ( mais de 400 milhões de unidades), o que significa que a maior parte da luz laser agora é produzida direta ou indiretamente (via bombeamento de diodo) por lasers semicondutores. Além de aplicações industriais, os lasers semicondutores estão sendo usados como fontes de bombeamento para lasers de estado sólido e lasers de fibra, em aplicações gráficas, como prova de cor e impressão digital direta na placa, e para várias aplicações médicas e militares (iluminação e alcance ) Em 2000, Laser Focus World estimou que cerca de 34% dos lasers de terapia médica eram do tipo semicondutor.
Matérias-primas
O laser semicondutor convencional consiste em um semicondutor composto, arsenieto de gálio. Esse material vem na forma de lingotes que são posteriormente processados em substratos aos quais são adicionadas camadas de outros materiais. Os materiais usados para formar essas camadas são pesados com precisão de acordo com uma fórmula específica. Outros materiais que são
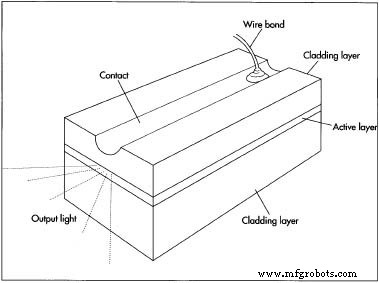
Design
O projeto básico de um laser semicondutor consiste em uma "dupla heteroestrutura". Isso consiste em várias camadas com funções diferentes. Uma camada de amplificação ativa ou leve é ensanduichada entre duas camadas de revestimento. Essas camadas de revestimento fornecem injeção de elétrons na camada ativa. Como a camada ativa tem um índice de refração maior do que o das camadas de revestimento, a luz fica confinada na camada ativa.
O desempenho do laser pode ser melhorado alterando o projeto da junção de modo que a perda de difração na cavidade óptica seja reduzida. Isso é possível modificando o material do laser para controlar o índice de refração da cavidade e a largura da junção. O índice de refração do material depende do tipo e quantidade de impureza. Por exemplo, se parte do gálio na camada carregada positivamente for substituído por alumínio, o índice de refração é reduzido e a luz do laser é melhor confinada à cavidade óptica.
A largura da junção também pode afetar o desempenho. Uma dimensão estreita confina a corrente a uma única linha ao longo do comprimento do laser, aumentando a densidade da corrente. O pico de potência de saída deve ser limitado a não mais de 400 watts por cm (0,4 pol.) De comprimento da junção e a densidade de corrente a menos de 6.500 amperes por centímetro quadrado na junção para estender a vida útil do laser.
O processo de fabricação
Fazendo o substrato
- 1 Os substratos são feitos usando uma técnica de extração de cristal chamada método Czochralski, em que um cristal é cultivado a partir de uma fusão. Os elementos são primeiro misturados e depois aquecidos para formar uma solução. A solução é então resfriada, o que solidifica o material. Um cristal de semente é preso à parte inferior de um braço vertical de forma que a semente quase não entre em contato com o material na superfície do fundido. O braço é levantado lentamente e um cristal cresce por baixo na interface entre o cristal e o fundido. Normalmente, o cristal é girado lentamente para evitar a produção de impurezas no cristal. Medindo o peso do cristal durante o processo de extração, os controles do computador podem variar a taxa de extração para produzir qualquer diâmetro desejado.
Aumentando as camadas
-
2 O método mais comum para o crescimento das camadas no substrato é denominado epitaxia de fase líquida (LPE). Camadas que têm a mesma direção de crescimento de cristal ou fixa como aquela do substrato podem ser crescidas no substrato quando o substrato entra em contato com uma solução da composição desejada. À medida que a temperatura diminui, o composto semicondutor (como GaAs) sai da solução na forma cristalina e é depositado no substrato.
Um sistema LPE consiste em um reator (onde as camadas são cultivadas), um sistema de carregamento de substrato, uma bomba e sistema de exaustão (para remover o ar ou gases impuros após os materiais serem colocados ou retirados), um sistema de fluxo de gás (para mover gás hidrogênio através do reator para remover gases impuros) e um sistema de controle de temperatura. Materiais puros são usados para fazer o reator para que as camadas não sejam contaminadas. A caixa de carga geralmente é preenchida com gás nitrogênio para purgar o ar ao abrir o reator. O reator normalmente consiste em um tubo de quartzo, no qual um barco de grafite e um suporte de barco são colocados. O barco de grafite consiste em uma estrutura externa, um suporte de substrato, um espaçador e uma caixa de fusão.
- 3 Os materiais de base para as camadas são primeiro enxaguados e gravados para limpar a superfície. Depois de secar os materiais gravados, eles são carregados em cada caixa de fusão do barco de grafite. Para fazer crescer cada camada, os materiais são primeiro derretidos por aquecimento a uma temperatura específica e, em seguida, o suporte do substrato é puxado junto com o substrato do primeiro fundido para o próximo. O substrato é mantido a cada fusão por um certo tempo sob uma taxa de resfriamento fixa, geralmente 33 ° F (0,5 ° C) por minuto, de acordo com um programa específico projetado para cada composição. A temperatura é controlada automaticamente usando sensores termopar.
Fabricação do dispositivo a laser
- 4 Após o crescimento da estrutura em camadas, vários outros processos são concluídos para formar o dispositivo a laser. Primeiro, o substrato é polido mecanicamente até que a espessura diminua para 70-100 mícrons na preparação para clivagem. A seguir, um silício muito fino filme de dióxido é formado na superfície do substrato. As listras são formadas por fotolitografia e corrosão química. Eletrodos de contato são aplicados usando um método de evaporação. Em seguida, um ressonador a laser é formado pela clivagem do wafer ao longo de planos de cristal paralelos. Os dispositivos a laser completos são então conectados a um dissipador de calor de cobre de um lado e a um pequeno contato elétrico do outro.
Controle de qualidade
O substrato no qual a estrutura do semicondutor é cultivada deve atender a certos requisitos em relação à direção do cristal, densidade do poço de corrosão (EPD), concentração de impurezas, espessura do substrato e tamanho do wafer. A direção do cristal deve estar dentro de vários graus. Os poços de corrosão, que são colinas ou buracos retangulares, são revelados ao atacar seletivamente o substrato com algum tipo de solução ácida. A densidade do ponto de corrosão (número de pontos de corrosão por centímetro quadrado) é usada para estimar a densidade de deslocamento, que afeta a vida útil do laser. Um EPD de 10 3 por centímetro quadrado ou menos é necessário. As concentrações de impurezas estão em torno de 10 18 por centímetro cúbico. Os substratos podem variar em tamanho até 3 pol. (7,6 cm) de diâmetro e normalmente são fatiados em pedaços de 350 mícrons de espessura.
Após o processo de crescimento, a superfície da pastilha semicondutora é examinada por um microscópio óptico. Para examinar a estrutura em camadas, uma seção transversal do solo ou clivada de wafer é manchada e gravada para aumentar o contraste das camadas usando um microscópio eletrônico de varredura. A difração de raios-X é usada para determinar as composições das camadas e para medir os padrões de rede da estrutura. A concentração de impurezas e o índice de refração das camadas também são medidos usando vários métodos analíticos. Depois que o dispositivo a laser é fabricado, parâmetros operacionais como curvas de tensão / corrente, densidade de corrente de limiar e características espectrais são medidos.
O Futuro
Os analistas de indústria da Frost &Sullivan preveem que o mercado de sistemas de laser de diodo atingirá quase US $ 4,6 bilhões em 2005. Esse crescimento se deve parcialmente à expansão das aplicações no processamento de materiais, já que os lasers de diodo de alta potência se tornam menos caros do que os lasers de estado sólido. O tamanho compacto e a eficiência elétrica também tornam os lasers semicondutores de alta potência atraentes para aplicações industriais, como tratamento térmico e soldagem. Novas composições de materiais e métodos de processamento também estão sendo desenvolvidos para expandir as aplicações.
Processo de manufatura