Poliéster
Antecedentes
Poliéster é uma fibra sintética derivada de carvão, ar, água e petróleo. Desenvolvidas em um laboratório do século 20, as fibras de poliéster são formadas a partir de uma reação química entre um ácido e um álcool. Nessa reação, duas ou mais moléculas se combinam para formar uma grande molécula cuja estrutura se repete em todo o seu comprimento. As fibras de poliéster podem formar moléculas muito iônicas que são muito estáveis e fortes.
O poliéster é usado na fabricação de muitos produtos, incluindo roupas, artigos de decoração, tecidos industriais, fitas de computador e de gravação e isolamento elétrico. O poliéster tem várias vantagens em relação aos tecidos tradicionais, como o algodão. Não absorve umidade, mas absorve óleo; essa qualidade torna o poliéster o tecido perfeito para a aplicação de acabamentos resistentes à água, sujeira e fogo. Sua baixa absorção também o torna naturalmente resistente a manchas. As roupas de poliéster podem ser pré-encolhidas no processo de acabamento e, a partir daí, o tecido resiste ao encolhimento e não fica fora de forma. O tecido pode ser facilmente tingido e não é danificado por mofo. As fibras texturizadas de poliéster são um isolante eficaz e não alérgico, portanto, o material é usado para encher travesseiros, acolchoados, agasalhos e sacos de dormir.
História
Em 1926, a E.I. com sede nos Estados Unidos. du Pont de Nemours and Co. começou a pesquisar moléculas muito grandes e fibras sintéticas. Esta pesquisa inicial, liderada por W.H. Carothers, centrado no que se tornou o náilon, a primeira fibra sintética. Logo depois, nos anos 1939-41, pesquisadores químicos britânicos se interessaram pelos estudos du Pont e conduziram suas próprias pesquisas nos laboratórios da Calico Printers Association, Ltd. Esse trabalho resultou na criação da fibra de poliéster conhecida na Inglaterra como Terileno .
Em 1946, a du Pont adquiriu o direito de produzir essa fibra de poliéster nos Estados Unidos. A empresa conduziu mais algum trabalho de desenvolvimento e, em 1951, começou a comercializar a fibra com o nome de Dacron. Nos anos seguintes, várias empresas se interessaram pelas fibras de poliéster e passaram a fabricar suas próprias versões do produto para diversos usos. Hoje, existem dois tipos principais de poliéster, PET (tereftalato de polietileno) e PCDT (poli-1,4-ciclohexileno-tereftalato de dimetileno). PET, o tipo mais popular, é aplicável a uma ampla variedade de usos. É mais forte do que o PCDT, embora o PCDT seja mais elástico e resiliente. O PCDT é adequado para os usos mais pesados do consumidor, como cortinas e revestimentos de móveis. O PET pode ser usado sozinho ou misturado com outros tecidos para fazer roupas resistentes a rugas e manchas e manter sua forma.
Matérias-primas
Poliéster é um termo químico que pode ser dividido em poli, significando muitos, e éster, um composto químico orgânico básico. O principal ingrediente utilizado na fabricação do poliéster é o etileno, derivado do petróleo. Nesse processo, o etileno é o polímero, o bloco de construção químico do poliéster, e o processo químico que produz o poliéster acabado é chamado de polimerização.
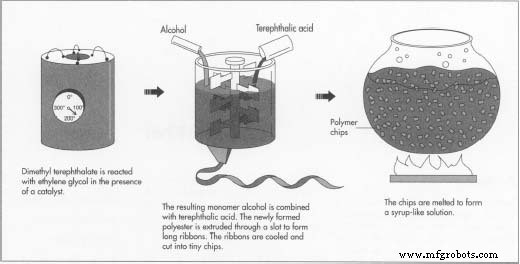
O processo de fabricação
O poliéster é fabricado por um de vários métodos. O usado depende da forma que o poliéster acabado vai assumir. As quatro formas básicas são filamento, grampo, estopa e fibra de enchimento. Na forma de filamento, cada fio individual de fibra de poliéster é contínuo em comprimento, produzindo tecidos com superfície lisa. Na forma de grampo, os filamentos são cortados em comprimentos curtos predeterminados. Nesta forma, o poliéster é mais fácil de se misturar com outras fibras. O reboque é uma forma na qual os filamentos contínuos são unidos frouxamente. Fiberfill é a forma volumosa usada na fabricação de colchas, travesseiros e casacos. As duas formas usadas com mais freqüência são filamento e grampo.
Fabricação de fios de filamentos
Polimerização
- 1 Para formar poliéster, o tereftalato de dimetila é primeiro reagido com etilenoglicol na presença de um catalisador a uma temperatura de 302-410 ° F (150-210 ° C).
- 2 O produto químico resultante, um álcool monômero (molécula única sem repetição), é combinado com ácido tereftálico e elevado a uma temperatura de 472 ° F (280 ° C). O poliéster recém-formado, que é transparente e derretido, é extrudado através de uma fenda para formar longas fitas.
Secagem
- 3 Depois que o poliéster emerge da polimerização, as longas fitas derretidas podem esfriar até que se tornem quebradiças. O material é cortado em minúsculas lascas e completamente seco para evitar irregularidades na consistência.
Fiação derretida
- 4 Fragmentos de polímero são fundidos a 500-518 ° F (260-270 ° C) para formar uma solução semelhante a um xarope. A solução é colocada em um recipiente de metal chamado fieira e forçada através de seus minúsculos orifícios, que geralmente são redondos, mas podem ser pentagonais ou de qualquer outra forma para produzir fibras especiais. O número de orifícios na fieira determina o tamanho do fio, pois as fibras emergentes são reunidas para formar um único fio.
- 5 Na fase de centrifugação, outros produtos químicos podem ser adicionados à solução para tornar o material resultante retardante de chamas, antiestático ou mais fácil de tingir.
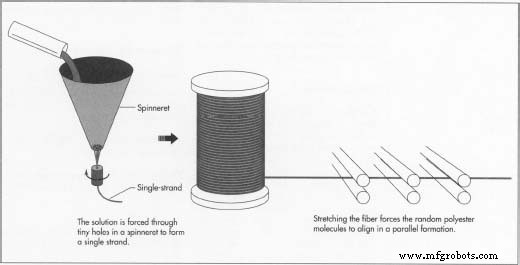
Desenhando a fibra
- 6 Quando o poliéster emerge da fieira, ele é macio e facilmente alongado até cinco vezes seu comprimento original. O alongamento força as moléculas de poliéster aleatórias a se alinharem em uma formação paralela. Isso aumenta a resistência, tenacidade e resiliência da fibra. Desta vez, quando os filamentos secam, as fibras tornam-se sólidas e fortes em vez de quebradiças.
- 7 As fibras estiradas podem variar muito em diâmetro e comprimento, dependendo das características desejadas do material acabado. Além disso, conforme as fibras são desenhadas, elas podem ser texturizadas ou torcidas para criar tecidos mais macios ou opacos.
Enrolamento
- 8 Depois que o fio de poliéster é estirado, ele é enrolado em bobinas grandes ou pacotes enrolados de forma plana, pronto para ser tecido no material.
Fabricação de fibras descontínuas
Na fabricação de fibras descontínuas de poliéster, a polimerização, a secagem e a fiação por fusão (etapas 1-4 acima) são praticamente as mesmas que na fabricação de fios de filamento. No entanto, no processo de fiação por fusão, a fieira tem muito mais orifícios quando o produto é fibra curta. Os feixes de poliéster em forma de corda que emergem são chamados de reboque.
Reboque de desenho
- 1 A estopa recém-formada é resfriada rapidamente em latas que reúnem as fibras grossas. Vários pedaços de estopa são reunidos e, em seguida, puxados em rolos aquecidos até obterem três ou quatro vezes o seu comprimento original.
Crimpagem
- 2 A estopa puxada é então alimentada em caixas de compressão, que forçam as fibras a se dobrarem como um acordeão, a uma taxa de 9-15 dobras por polegada (3-6 por cm). Esse processo ajuda a fibra a se manter unida durante os estágios posteriores de fabricação.
Configuração
- 3 Depois que a estopa é frisada, ela é aquecida a 212-302 ° F (100-150 ° C) para secar completamente as fibras e definir a crimpagem. Algumas das ondulações inevitavelmente serão puxadas para fora das fibras durante os processos a seguir.
Corte
- 4 Após o aquecimento, o reboque é cortado em comprimentos menores. O poliéster que será misturado ao algodão é cortado em pedaços de 1,25-1,50 polegadas (3,2-3,8 cm); para misturas de rayon, são cortados comprimentos de 2 polegadas (5 cm). Para tecidos mais pesados, como carpete, os filamentos de poliéster são cortados em comprimentos de 6 polegadas (15 cm).
O Futuro
Após sua introdução nos Estados Unidos em 1951, o poliéster rapidamente se tornou a fibra de crescimento mais rápido do país. O cuidado fácil com o tecido de prensagem permanente tornou as malhas duplas de poliéster extremamente populares no final dos anos 1960. No entanto, o poliéster sofreu um "problema de imagem" desde aquela época, e as roupas feitas de poliéster eram muitas vezes desvalorizadas e até ridicularizadas. Várias novas formas de poliéster introduzidas no início da década de 1990 podem ajudar a revitalizar a imagem do poliéster. Uma nova forma de fibra de poliéster, chamada microfibra, foi apresentada ao público em 1991. Mais luxuosos e versáteis do que o poliéster tradicional, os tecidos de microfibra são difíceis de distinguir dos tecidos de seda. Designers de roupas como Mary McFadden criaram uma linha de roupas usando essa nova forma de poliéster. Pesquisadores têxteis da North Carolina State University estão desenvolvendo uma forma de poliéster que pode ser tão forte quanto o Kevlar, um material de superfibra usado para fazer coletes à prova de balas. Esse tipo de poliéster pode eventualmente ser usado como materiais compostos para carros e aviões.
Processo de manufatura
- Fusão de leito de pó:uma forma inovadora de impressão 3D
- Um ecossistema completo para impressão 3D SLA de formato grande
- PrintCity apresenta aos clientes o Form 3 e Fusion 360
- PTC, Formulário de Parceria IoT da Rockwell Automation
- Danaher, Cooper Industries para combinar negócios de ferramentas, formar nova empresa
- Resinas de poliéster:O básico
- Vídeo:Ferramentas de forma em tornos CNC
- Fiel to Form:O valor da fiação de metal e hidroformagem
- FANUC, Plus One Form Alliance
- FANUC, Rockwell Automation Form Coalition