Espuma de poliestireno expandido (EPF)
Antecedentes
A espuma de poliestireno expandido (EPF) é um material plástico que possui propriedades especiais devido à sua estrutura. Composto por células individuais de poliestireno de baixa densidade, o EPF é extraordinariamente leve e pode suportar muitas vezes seu próprio peso em água. Como suas células não estão interconectadas, o calor não pode viajar pelo EPF facilmente, por isso é um ótimo isolante. O EPF é usado em dispositivos de flutuação, isolamento, caixas de ovos, planos para carne e produtos, caixas de sanduíches e hambúrgueres, café copos, pratos, embalagens de amendoim e caixas térmicas de piquenique. Embora seja geralmente chamado de isopor, o isopor é uma marca comercial da Dow Chemical Company e se refere especificamente a um tipo de EPF azul duro usado principalmente em passeios de barco.
Durante o final do século 19, os pesquisadores em busca de materiais adequados para fazer filmes, pára-brisas de carros e vários itens pequenos, como pentes, produziram os primeiros plásticos a partir de substâncias naturais e produtos químicos. Ao fazer esses plásticos, os cientistas exploraram a tendência natural para a polimerização, na qual duas ou mais pequenas moléculas, ou monômeros, se combinam para formar cadeias que costumam ser muito longas. As cadeias moleculares resultantes, ou polímeros, compreendem unidades estruturais repetidas das moléculas originais. Um dos polímeros naturais mais familiares é a celulose, a cadeia de moléculas de glicose que forma um componente principal das paredes das células vegetais, algodão, papel e raiom. O poliestireno está entre os polímeros sintéticos mais conhecidos (outros incluem polietileno, polipropileno e poliéster). O estireno, o hidrocarboneto líquido do qual o EPF é feito, foi derivado no final do século XIX do bálsamo de estórax, que vem de uma árvore na Ásia Menor chamada goma doce oriental. No início do século XIX, plásticos totalmente sintéticos foram desenvolvidos a partir de hidrocarbonetos, cuja estrutura é propícia para uma fácil polimerização. O poliestireno, o polímero do qual o EPF é feito, foi inventado em 1938.
Os plásticos espumantes foram descobertos indiretamente, porque no início ninguém conseguia ver suas vantagens. O Dr. Leo H. Baekeland, o químico americano que desenvolveu o primeiro plástico totalmente sintético, a baquelite, fez experiências com fenol (um composto ácido) e formaldeído (um gás incolor) enquanto tentava fazer uma resina não porosa. Quando uma de suas misturas começou a formar espuma inesperadamente, Baekeland tentou controlar a espuma antes de perceber que ela poderia ter vantagens. Após a morte de Baekeland em 1944, os primeiros compostos fenólicos espumosos foram desenvolvidos, logo seguidos pela espuma epóxi. Pouco tempo depois, o poliestireno foi espumado. No início, era usado principalmente em dispositivos de isolamento e flutuação para barcos, salva-vidas e bóias. Só depois que o EPF substituiu o papel, a sumaúma (feita com as fibras sedosas que envolvem as sementes da árvore de ceiba) e outras proteções naturais de embalagem é que a substância se tornou tão popular quanto é hoje. Sua familiaridade foi favorecida pelo enorme crescimento das indústrias de fast food e take away, que começaram a usar o EPF em caixas de hambúrguer e xícaras de café. Hoje o EPF é facilmente o plástico mais conhecido.
No entanto, apesar da popularidade e das características exclusivas do EPF, ele recentemente foi atacado por causa dos derivados gasosos do metano - clorofluorcarbonos (CFCs) - usados para espumá-lo. Os CFCs são inertes e inofensivos para os humanos e o meio ambiente após sua liberação. No entanto, muito depois de seu primeiro uso, os cientistas perceberam que os CFCs contribuem para a destruição da camada de ozônio à medida que se decompõem. A camada de ozônio é uma camada da atmosfera
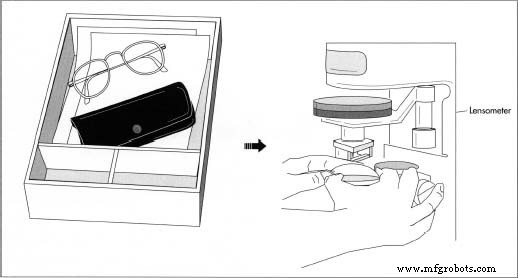
Matérias-primas
O principal componente do EPF é o estireno (C 8 H 8 ), que é derivado de petróleo ou gás natural e formado por uma reação entre etileno (C 2 H 4 ) e benzeno (C 6 H 6 ); o benzeno é produzido a partir do carvão ou sintetizado a partir do petróleo. O estireno é polimerizado por calor ou por um iniciador, como o peróxido de benzoíla. Parar a polimerização é difícil; entretanto, inibidores como oxigênio, enxofre ou quinol podem ser usados. Para formar as células de baixa densidade e frouxamente ligadas pelas quais o EPF é conhecido, o poliestireno deve primeiro ser suspenso em água para formar gotículas. Um agente de suspensão, como sulfato de bário especialmente precipitado ou copolímeros de ácido acrílico e metacrílico e seus ésteres (produto orgânico formado pela reação entre um ácido e um álcool), é então adicionado à água. Numerosos agentes de suspensão são usados comercialmente. Todos são igualmente viscosos e servem para reter as gotas, evitando que se colem. Os grânulos de poliestireno produzidos por polimerização em suspensão são minúsculos e duros. Para expandi-los, são usados agentes de expansão especiais, incluindo propano, pentano, cloreto de metileno e os clorofluorcarbonos.
Design
Como todos os plásticos, o EPF consiste em uma cadeia polimérica de grande peso molecular. O peso de uma molécula é equivalente à sua massa e pode ser calculado adicionando-se a massa de seus átomos constituintes. EPF é um polímero linear cuja unidade básica é o estireno (C 8 H 8 ) e cuja massa molecular é 104, mas quando está ligada como está no plástico, sua massa pode variar entre 200.000 e 300.000 (porque uma cadeia de polímero pode conter um número indefinido de ligações moleculares, uma massa terminal não pode ser determinada) .
O processo de fabricação
Primeiro, o estireno é feito pela combinação de etileno e benzeno. Em seguida, o estireno é submetido à polimerização em suspensão e tratado com um iniciador de polimerização, que juntos o convertem em poliestireno. Uma vez formada uma cadeia de polímero com o comprimento desejado, os técnicos param a reação com agentes de terminação. Os grânulos de poliestireno resultantes são então limpos e os grânulos anômalos filtrados. Para fazer EPF de células pequenas, os trabalhadores então derretem, adicionam um agente de expansão e extrudem os grânulos. Para produzir EPF de pele lisa, eles pré-expandem os grânulos, reduzindo drasticamente sua densidade. Em seguida, eles os aquecem e expandem antes de permitir que eles fiquem por 24 horas para que possam esfriar e endurecer. As contas são então alimentadas em um molde com a forma desejada.
Fabricação de estireno
- 1 A unidade básica do poliestireno é o estireno, que é o produto de uma reação dupla. Etileno e benzeno, na presença de um catalisador, como cloreto de alumínio, formam etilbenzeno (C 8 H 8 ), que é então desidrogenado (o hidrogênio é removido) a 1.112-1.202 graus Fahrenheit (600-650 graus Celsius) para formar o estireno (C 8 H 8 )
Fabricação de poliestireno
- 2 O poliestireno é formado a partir do estireno por meio da polimerização em suspensão, um processo pelo qual pequenas gotas do monômero (neste caso, o estireno) são completamente circundadas por água e uma substância mucilaginosa. Suportando e envolvendo os glóbulos de estireno, o agente de suspensão produz gotículas uniformes de poliestireno.
- 3 Em seguida, um iniciador de polimerização é adicionado às gotículas, que são suspensas por radiação de calor de cerca de 212 graus Fahrenheit (100 graus Celsius). Isso resulta em radicais livres, um grupo de átomos com probabilidade de reagir com outros porque contêm elétrons desemparelhados que estão disponíveis para ligações moleculares. Os radicais livres então se combinam aleatoriamente para formar cadeias de poliestireno.
- 4 Parar o processo de polimerização é difícil. Os exterminadores são apresentados ao processo para encerrá-lo no momento apropriado. Embora variável, o comprimento da cadeia deve estar dentro de uma certa faixa, porque o poliestireno com cadeias excessivamente longas não derrete prontamente e o poliestireno com cadeias curtas será quebradiço.
Preparando as contas
- 5 Depois que a polimerização for concluída, a mistura - consistindo de grânulos feitos de cadeias de poliestireno - é resfriada. Essas contas são então lavadas e secas. O tamanho uniforme do grânulo é obtido classificando-se os grânulos por meio de malhas que filtram os grânulos maiores e menores.
Fabricação de espuma de poliestireno expandido
- 6 Primeiro, os grânulos de poliestireno devem ser expandidos para atingir a densidade adequada. Esse processo é conhecido como pré-expansão e envolve o aquecimento do poliestireno com vapor (o método mais comum) ou com ar quente (para espuma de alta densidade, como a usada para uma xícara de café); o aquecimento é realizado em um recipiente contendo de 50 a 500 galões (189 a 1.892 litros). Durante a pré-expansão, um agitador é usado para evitar que os grânulos se fundam. Como as contas expandidas são mais leves do que as não expandidas, elas são forçadas para o topo da cavidade do vaso e descarregadas. Este processo reduz a densidade dos grânulos para três por cento de seu valor original e produz um EPF de célula fechada de pele lisa que é excelente para moldagem detalhada.
- 7 Em seguida, os grânulos pré-expandidos são geralmente "envelhecidos" por pelo menos 24 horas em silos de armazenamento de malha. Isso permite que o ar se espalhe pelas esferas, resfriando-as e tornando-as mais duras.
Moldagem
- 8 Após o envelhecimento, as contas são alimentadas em um molde com o formato desejado. O vapor de baixa pressão é então injetado dentro e entre os grânulos, expandindo-os mais uma vez e fundindo-os.
- 9 O molde é então resfriado, seja por circulação de água através dele ou por pulverização de água na parte externa. O EPF é um isolante tão bom que é difícil resfriar o molde. O uso de moldes pequenos pode reduzir o tempo de aquecimento e resfriamento e, assim, acelerar o processo.
Fabricação de espuma de poliestireno expandido extrudado
- 10 Este processo produz EPF com tamanho de célula pequeno que pode ser usado para fabricar placas usadas para isolamento. As contas são derretidas e um agente de expansão é adicionado. O poliestireno fundido é então extrudado na forma adequada sob condições de alta temperatura e pressão.
Corte, colagem e revestimento
- 11 EPF geralmente é cortado com ferramentas de trabalho Wood-I comuns, que devem ser mantidas muito afiadas o tempo todo para um corte suave. Também pode ser colado com adesivos que não o destroem. Os adesivos à base de água são bons, assim como os fenólicos, os epóxis, os resorcinóis e as ureias. EPF não é resistente a intempéries ou
Fazer o EPF envolve uma série de etapas. Primeiro, os grânulos de poliestireno passam por uma pré-expansão, na qual são expandidos para dar a eles a densidade adequada. Depois de envelhecer em um silo de armazenamento, os grânulos são alimentados em um molde e injetados com vapor, que expande os grânulos mais uma vez e os funde. Após o resfriamento, o EPF moldado é cortado no formato adequado e revestido com epóxi ou ponta protetora. luz solar e é inflamável, então geralmente revestimentos como epóxi, diferentes tipos de tinta e substâncias não inflamáveis são aplicados na superfície.
Controle de qualidade
O EPF está sujeito a vários testes e padrões formulados pela American Society for Testing and Materials (ASTM) para plásticos em geral. Alguns desses padrões dizem respeito ao EPF em particular por causa de suas propriedades únicas, mas alguns dos testes aplicados ao EPF foram desenvolvidos para medir as propriedades de outros plásticos.
O poliestireno fundido é testado para determinar se é suficientemente viscoso para produzir EPF com as propriedades desejadas. Além disso, as contas de poliestireno subsequentes devem ser de tamanho uniforme. O padrão para contas perfeitamente esféricas é baseado naquelas formadas em experimentos com ônibus espaciais sob condições de gravidade zero.
O EPF moldado também é testado quanto à resistência, inflamabilidade e densidade, o que é particularmente importante ao testar dispositivos de flutuação. A resiliência do EPF é medida batendo um pêndulo contra o material e observando o quão longe ele ricocheteia. O EPF é então testado quanto à porosidade. Isso envolve determinar quantas células abertas e fechadas existem, depois de considerar a área de superfície do produto e o número de células cortadas por modelagem. A permeabilidade é então testada. Um teste simples envolve colocar um pedaço de EPF em uma substância e, em seguida, medir quanto dele é absorvido.
A condutividade térmica é importante sempre que o EPF é usado para isolamento. Os plásticos celulares têm a menor condutividade térmica (transmissão de calor) de qualquer material sólido conhecido. Eles isolam tão bem que o teste de condutividade térmica é demorado, mesmo quando folhas finas são usadas. A folha fina (0,79-2 polegadas ou 2-5 centímetros) de EPF é colocada ao lado de uma placa de aquecimento e ambas são envolvidas por placas frias para minimizar a perda de calor. Uma pequena quantidade controlada de calor é então aplicada a um lado da folha e, após várias horas, a quantidade de calor que penetra no outro lado é medida. Obviamente, todos os dados devem atender aos padrões do EPF.
O Futuro
O EPF pode ser incinerado com segurança e produzirá apenas dióxido de carbono e água se o procedimento for realizado corretamente, mas a tendência tem sido reciclá-lo sempre que possível. EPF pode ser reciclado em concreto, caixas de ovos, produtos de escritório, isolamento de espuma e latas de lixo. Infelizmente, apenas um por cento dos 11 bilhões de quilos de EPF jogados fora a cada ano está sendo reciclado. A National Polystyrene Recycling Company, que consiste em sete grandes corporações, incluindo Amoco, Dow e Mobil, planeja aumentar para 25% até 1995, concentrando-se em grandes usuários de EPF - lojas de fast food e restaurantes universitários. Desde o Protocolo de Montreal de 1988, novas pesquisas têm se concentrado em maneiras de reduzir o uso de CFC e no desenvolvimento de agentes de expansão alternativos que não prejudiquem a camada de ozônio. Desenvolvimentos recentes incluem um processo que usa dióxido de carbono pressurizado para produzir células menores e mais uniformes. Estes, por sua vez, fornecem uma espuma que é mais forte e mais lisa do que as anteriores.
Processo de manufatura