Um guia completo para manutenção de equipamentos pesados
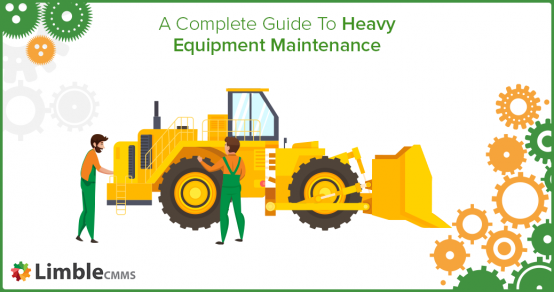
Equipamentos pesados são caros para adquirir e manter. Também é fundamental para as operações de negócios. Como você precisa disso, precisa de um bom programa de manutenção de equipamentos pesados para manter os ativos em condições de pico, aumentar sua utilização e estender sua vida útil.
Neste artigo, iremos guiá-lo através dos pontos mais importantes que você precisa considerar para a manutenção de equipamentos pesados. Também descreveremos como você pode estabelecer um sistema de manutenção de equipamentos pesados personalizado de acordo com suas necessidades.
Lá vamos nós!
O que podemos categorizar em equipamento pesado?
Equipamento pesado refere-se a máquinas especializadas construídas para uma tarefa específica ou uma série de tarefas semelhantes. O termo é amplo, cobrindo vários setores e usos. Alguns exemplos incluem:
- Máquinas de terraplenagem, como escavadeiras, raspadores ou tratores
- Equipamentos de construção, como guindastes e transportadores modulares
- Máquinas florestais, incluindo picadores ou puxadores de tocos
- Semi-caminhões e reboques
- Equipamentos agrícolas, como tratores e colheitadeiras
- Material rodante ferroviário
O termo tem menos a ver com peso do que com a função especializada para a qual o equipamento é usado. Hoje em dia, essas máquinas usam sistemas hidráulicos, pneumáticos e eletrônicos sofisticados para operar. Com a função crítica dessas máquinas e o custo de capital para adquiri-las e operá-las, uma manutenção abrangente e direcionada é essencial.
Os benefícios da manutenção proativa para equipamentos pesados
Estabelecer a manutenção de equipamentos pesados envolve investimento, com alguns operadores optando por fazer reparos no equipamento apenas quando ele quebrar. No entanto, esta é uma falsa economia, custando a esses operadores somas consideravelmente maiores a médio e longo prazo.
Estudos sugerem reduções de custo entre três a dez vezes ao usar a manutenção preventiva em vez de consertá-la em caso de falha do equipamento. Vejamos os benefícios obtidos com a manutenção regular, planejada e pesada de equipamentos:
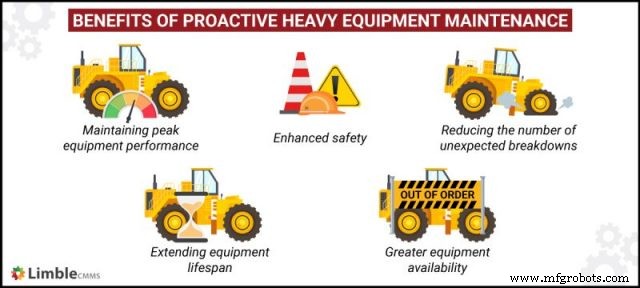
Segurança aprimorada
Como empregadores, não temos apenas o dever de cuidar de nossos trabalhadores; temos uma obrigação regulatória. Quando ocorrem acidentes, os reguladores investigam imediatamente as medidas preventivas e mitigadoras que o empregador tinha em vigor. Uma dessas mitigações é um plano de manutenção bem elaborado para ajudar a garantir que as máquinas não se degradem a ponto de causar ferimentos ou morte.
Manter o desempenho máximo do equipamento
Deterioração oculta custa dinheiro:válvulas de desvio não assentam corretamente, vazamento do sistema hidráulico, trocadores de calor sujos funcionando com menos eficiência ou lâminas cegas que não cortam corretamente. Todos contribuem para reduzir a capacidade operacional, aumentar o desgaste, reduzir a eficiência e reduzir a vida útil.
Cada um desses efeitos soma uma receita reduzida ou um aumento nos custos operacionais e de despesas de capital.
Reduzindo o número de avarias inesperadas
Interrupções inesperadas de paralisações corroem o valor da empresa. Os prazos são perdidos e os clientes ficam decepcionados. Os funcionários ficam frustrados, podendo causar incidentes de segurança.
Os custos de reparos de emergência podem ser duas a três vezes os custos de uma substituição planejada devido ao frete acelerado de peças sobressalentes, chamadas fora do expediente e aluguel de equipamento de reserva. Quando a manutenção é planejada , é realizado no momento e local de escolha da operadora, sem afetar as operações e com todos os recursos pré-planejados e disponíveis.
Estendendo a vida útil do equipamento
Todos os equipamentos possuem um ciclo de vida de projeto, cuja realização depende da realização de manutenções de rotina recomendadas. A amortização dos custos de compra ao longo da vida útil do equipamento é a base das taxas cobradas pelo operador. Quando o equipamento deixa de cumprir sua vida projetada devido à negligência, os custos são subestimados e as contribuições para os lucros do negócio são perdidas.
Existem inúmeras maneiras de estender a vida útil de equipamentos pesados, com a manutenção proativa e o treinamento do operador liderando o caminho.
Maior disponibilidade de equipamentos
A maioria dos equipamentos pesados é paga por hora. Quando o equipamento não está operando, as receitas diminuem e os custos aumentam. Quando um trabalho é avaliado como uma quantia total, as avarias podem impor custos de manutenção de emergência, custos extras de aluguel, tempo estendido na tarefa e eficiência reduzida da frota.
O fracasso em atingir as taxas de confiabilidade planejadas da frota de forma realista significa que uma empresa está perdendo receita ou carregando maiores custos operacionais e de despesas de capital.
Como configurar um programa proativo de manutenção de equipamentos pesados
As etapas a seguir irão guiá-lo através do processo de implementação de um programa abrangente de manutenção de equipamentos pesados. O valor que você recebe do programa refletirá diretamente a profundidade de detalhes que você considera durante a fase de design e implementação.
Etapa 1:Escolha um pioneiro
Se você não operou um programa de manutenção proativa em sua organização antes, comece devagar. Selecione uma peça de equipamento para seu programa piloto. Depois de implementar os sistemas necessários para dar suporte a essa máquina de forma adequada, é mais fácil replicar esse modelo em toda a sua frota.
Sua seleção deve se concentrar em um ativo que tem uma vida operacional considerável restante e deve atender a pelo menos um dos três critérios a seguir:
- Seu desempenho eficiente é fundamental para operações eficazes
- Requer manutenção intensiva
- Tem uma alta taxa de falha ou avaria
Etapa 2:Operação anterior do equipamento de linha de base
É difícil analisar a adequação de um programa de manutenção sem ter dados operacionais históricos e diagnósticos para medir as intervenções. Sempre que possível, verifique o custo operacional, a eficiência, os dados de solução de problemas, a disponibilidade e o uso sobressalente da máquina.
O histórico de desempenho e diagnóstico do equipamento, as queixas dos operadores e as experiências dos mantenedores fornecerão parâmetros úteis para medir a melhoria. Assim que o programa de manutenção estiver implementado e estabelecido, você pode comparar os novos dados com os antigos para avaliar a eficácia do programa.
Etapa 3:Colete os dados necessários
Ao construir um programa de manutenção de equipamentos pesados, sempre comece com os dados do fabricante do equipamento original (OEM). Todos os fabricantes de máquinas pesadas publicarão uma lista de tarefas de manutenção recomendadas e seus intervalos. As recomendações do fabricante formarão o núcleo de seu programa de manutenção.
Em seguida, considere os requisitos regulamentares que você deve cumprir na jurisdição em que está operando. A maioria dos países tem intervalos de manutenção específicos para equipamentos de elevação. A legislação de saúde e segurança pode impor requisitos específicos, assim como as leis ambientais que exigem um monitoramento regular de fluidos, gases e emissões.
Por último, você precisará considerar quais outras tarefas de manutenção você precisa adicionar com base nos requisitos da empresa, equipamentos pós-venda instalados e sua aplicação específica:
- Por exemplo, sua empresa pode usar um sistema de orientação de escavadeira GPS instalado como um produto pós-venda. O OEM desse equipamento terá requisitos de manutenção que farão parte do programa geral de manutenção da máquina.
- Da mesma forma, sua empresa pode exigir testes de óleo hidráulico e do motor. A tarefa de amostrar os óleos, enviá-los para análise e registrar os resultados recebidos em um gráfico de tendência se tornará uma tarefa de manutenção planejada.
Etapa 4:gerenciar peças de reposição, consumíveis e ferramentas especiais
Os programas de manutenção de equipamentos pesados exigem que certas peças sobressalentes sejam mantidas em estoque ou prontamente disponíveis no local de trabalho, de fornecedores terceirizados. Consumíveis e fluidos também precisam ser identificados, bem como ferramentas especializadas necessárias para executar tarefas específicas.
Quando um período de manutenção é planejado, é importante que todas as peças de reposição, vedações, fluidos e ferramentas estejam disponíveis para apoiar o processo de manutenção. Todas as ferramentas especializadas que requerem calibração devem ser incluídas em seu programa de manutenção preventiva para garantir que estejam em bom estado de funcionamento antes do uso.
Etapa 5:decidir sobre seu sistema de gestão
Neste ponto, você terá muitos dados. Agora você precisa decidir a melhor forma de gerenciar esses dados para chamar as tarefas no momento devido, levantar as planilhas necessárias e capturar os resultados da manutenção. Embora você possa usar sistemas manuais de cartão ou planilhas, eles são pesados, demorados e exigem vigilância constante para garantir que coisas importantes não sejam esquecidas ou perdidas.
Um moderno sistema de gerenciamento de manutenção computadorizado (CMMS) permite a fácil configuração dos dados iniciais. Ele olha para a próxima manutenção e cria um pacote de trabalho para tarefas a serem concluídas durante o período de manutenção. Depois de concluído, os dados são atualizados para mostrar o novo status da máquina.
Leia nosso guia essencial para CMMS para aprender como funciona um CMMS moderno e o que você pode esperar dele. Ou baixe a versão em PDF do mesmo artigo diretamente usando a caixa abaixo.
Etapa 6:Desenvolva programações de manutenção inicial
Neste ponto, você precisa acumular todos os dados coletados acima e sobrepô-los para alinhar as tarefas em agrupamentos óbvios.
A frequência de manutenção regular para cada tarefa pode ser baseada em ciclos, horas de equipamento, milhas, tempo de calendário ou uma mistura de todos. Se você tiver sensores de monitoramento de condição instalados em seu equipamento pesado, suas leituras de pressão / temperatura / vibração conduzirão muitas das suas ações de manutenção.
Organizações mais avançadas, com muitos dados de equipamento disponíveis, podem usar a manutenção centrada na confiabilidade e a manutenção baseada em riscos para decidir quais modos de falha desejam rastrear e quais estratégias de manutenção precisam implementar para que isso aconteça.
Etapa 7:Monitore e ajuste seu plano de manutenção de equipamentos pesados
Seu plano inicial de manutenção de equipamentos pesados não será perfeito. Quase imediatamente, você descobrirá que precisa fazer alguns ajustes.
Alguns períodos de manutenção podem ter muitas tarefas a serem concluídas, enquanto outros têm apenas algumas. Nesse caso, você pode agendar algumas tarefas com antecedência para redefinir quando chegarem, suavizando a carga de trabalho entre os períodos de manutenção consecutivos e equilibrando o tempo de inatividade e os requisitos de recursos.
Conforme você avança, você pode concluir algumas tarefas com muita frequência. Por exemplo, uma limpeza de inspeção do filtro pode ser desnecessária na frequência inicial selecionada. Você pode optar por prolongar o tempo entre as limpezas para evitar gastos e tempo desnecessários.
O oposto também é verdade. Algumas tarefas podem precisar de uma frequência mais alta devido à maneira como o ativo é usado ou às condições em que opera. Se você encontrar desgaste, falhas ou tempo de inatividade aumentados, é prudente aumentar a frequência de tarefas de manutenção específicas.
Etapa 8:implemente seu programa de manutenção proativa para outros ativos
Depois de concluir um programa de manutenção proativa em uma peça do equipamento pesado, você deve ter dados que comprovem os benefícios.
Com o modelo no lugar para sua primeira máquina, não é difícil concluir essas etapas para seu outro equipamento. Com um bom CMMS, o processo é tão simples quanto carregar os dados e deixar que o software de manutenção de equipamentos pesados faça o trabalho pesado por você.
Para obter mais informações, leia nosso guia completo sobre como configurar um programa de manutenção preventiva.
Conselhos gerais para manutenção de equipamentos pesados
As dicas a seguir o ajudarão a ajustar seu programa de manutenção para garantir que você extraia o valor máximo de cada intervenção de manutenção.
Use listas de verificação de manutenção de equipamentos pesados
Sem um grau de padronização e consistência, é difícil maximizar o retorno de sua manutenção regular. Se um técnico perde tarefas enquanto o outro as executa diligentemente, sua manutenção não é controlada nem eficaz.
Listas de verificação de manutenção e SOPs são uma ótima maneira de padronizar as tarefas de gerenciamento de equipamentos e o desempenho do técnico. Eles não precisam ser complicados - uma simples caixa de seleção para mostrar a absolvição da tarefa deve ser suficiente para uma pessoa devidamente treinada.
Para tarefas mais complexas, as listas de verificação são uma ótima maneira de destacar as etapas necessárias da manutenção do equipamento, ao mesmo tempo que adiciona um método a seguir, as ferramentas e sobressalentes necessários e fornece um espaço para capturar quem concluiu a tarefa. Também pode permitir espaço para registrar observações que formam uma boa narrativa sobre a condição contínua da máquina.
Se você usar um software CMMS, os técnicos geralmente serão solicitados a deixar as conclusões anotadas ao fechar OSs e PMs, para que esses tipos de observações sejam salvos diretamente no registro de manutenção desse ativo específico.
Use registros de defeitos para operadores de equipamento
Coloque um registro de defeito na cabine de todos os equipamentos pesados. Um registro permite que o operador anote quaisquer preocupações, vazamentos ou deterioração ou quebras.

Modelo de log de rastreamento de defeitos. Fonte: Modelos grátis do Excel
Certifique-se de que a data seja adicionada e a entrada rubricada. Os técnicos de manutenção podem verificar regularmente esses registros de defeitos para capturar as tendências de manutenção que podem estar em desenvolvimento. Ao planejar o próximo dia de manutenção, todos os defeitos devem ser removidos e adicionados ao pacote de trabalho de manutenção para informação dos técnicos.
Todos os itens no registro de defeitos devem ser considerados e endereçados, seja baixado como um item a monitorar, liberado como tendo sido retificado, ou ferramentas pendentes aguardando ou peças sobressalentes. Esse controle garante que os operadores tenham feedback sobre os problemas que levantaram e nenhuma preocupação escapará e voltará para assombrá-lo na forma de grandes preocupações de serviço.
Se você estiver usando um CMMS, todos os problemas verificados / endereçados devem ser registrados no registro de manutenção do equipamento para que você tenha o histórico de manutenção completo de um ativo em um só lugar.
Um exemplo de registro de manutenção de equipamentos dentro do Limble CMMS.
Desenvolva service packs para tarefas padronizadas
Um service pack é um conjunto de itens necessários para executar uma tarefa específica. Por exemplo, se você precisar de vedações, algum lubrificante e novos fixadores para completar uma inspeção, coloque-os todos em um pacote lacrado com um número de peça discreto relacionado à tarefa.
Você pode pedir a alguém que prepare o pacote antes do dia do serviço ou crie um número de peça e coloque-o em estoque.
Quando a tarefa é devida, o service pack é disponibilizado (junto com dicas de manutenção e listas de verificação, se necessário). Esse sistema evita que os técnicos percam tempo procurando esses itens antes de sair a campo.
Melhorar a rastreabilidade e responsabilidade do trabalho
Peça ao técnico ou operador que conclui uma tarefa específica para assinar e datar sua tarefa. Essa rastreabilidade permite que você fale com a pessoa se algo ocorrer nas semanas ou meses seguintes. Também permite um fácil acompanhamento se foram eles que encontraram defeitos durante a inspeção visual ou outro trabalho de manutenção.
Idealmente, você deve saber:
- Quem executou cada tarefa
- Quanto tempo eles passaram fazendo isso
- Quais peças sobressalentes eles usaram
Saber essas três coisas é essencial para calcular seus custos gerais de manutenção e dividi-los em custos de mão de obra, custos de peças e custos associados a cada fornecedor ou ativo.
Certifique-se de que seus técnicos dêem “tempo de conclusão” para tarefas maiores. Isso não precisa ser apenas para verificar seus funcionários. Juntamente com os cálculos de custo, é uma informação muito útil que permite aos planejadores de manutenção agendar tempo suficiente para a manutenção (tendo uma melhor compreensão do tempo médio de reparo para tarefas de manutenção específicas).
Os principais componentes, como gavetas hidráulicas, bombas e componentes eletrônicos, terão números de modelo e de série. Rastreie-os para saber o que está em seu equipamento, o que está em estoque e o que está sendo reparado.
Esses dados o ajudarão a decifrar por quanto tempo um componente está em operação antes que o reparo seja necessário. Se um componente falhar com mais frequência do que outros (tem MTBF inferior), você pode isolar essa parte e investigar o problema, consertando ou substituindo o componente para obter uma vida operacional aprimorada.
Your CMMS is invaluable here as it automates a significant portion of the data collection and tracking process, as well as allowing you (at least in the case of Limble CMMS) to generate highly-customized maintenance reports.
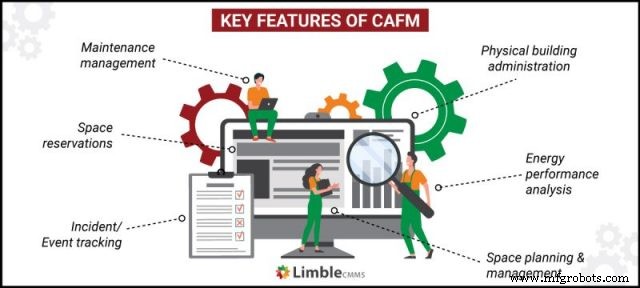
Limble CMMS dashboard can be populated with all kinds of custom metrics that refresh in real-time
Centralize service information and tooling
Be sure that your technicians are completing the task to your requirements, not their idea of what is needed. There should be only one place to access the service information and the tasks to be completed. No photocopied sheets of paper in people’s toolboxes.
Similarly, don’t allow each tech to have special tooling they’ve made up to do a job. If it’s a good idea, get it made and make it available, so everyone can use it. If it’s not a good idea, it could damage your equipment or injure your technician.
Provide common data and tools for all to access and use. By controlling the information, the task, and the tooling, you control the safety and quality of work being completed. In this way, you optimize equipment life and maintain peak reliability.
Again, CMMS can be used as your asset inventory management system, keeping track of tools and equipment.
Gather relevant maintenance statistics and metrics
The aviation industry uses metrics such as mean-time-between-unscheduled-removal (MTBUR) and total-time-in-service (TTIS). They help you find parts that are not achieving their intended life or compare parts from different vendors to see which one provides more value for the $$ spent.
An added bonus of tracking such maintenance metrics is the ability to plan maintenance before failure. This helps you avoid costly breakdowns. Your CMMS will allow you to mine that data, reducing cost and optimizing equipment uptime.
If you have the budget for it and truly want to optimize your maintenance resources, you will have to install condition-monitoring sensors on your heavy equipment and implement strategies like CBM or predictive maintenance.
Should you outsource heavy equipment maintenance to a vendor?
There is a line. At one end sits the option of doing all maintenance yourself in-house, while at the other end you outsource all maintenance to a third-party organization. There are unlimited options between those two extremes, where you complete some maintenance and have some done by others.
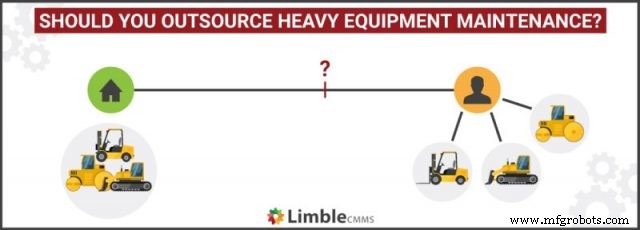
There are many reasons for outsourcing.
- You may consider that maintenance is not a business you should be in or want to be in, as it’s not your core competency.
- Some maintenance may require very specialized tools or skills that you don’t wish to purchase or train your employees for.
- You may wish to transfer the risk of maintenance onto a third party who specializes in the task. With service level agreements (SLA) in place, if your equipment availability drops, so too does the maintenance provider’s revenue.
- You may wish to reduce your permanent workforce.
- You don’t have the facilities or ground space to carry out the maintenance.
- The cost of your employees doing the maintenance may be more expensive than having a specialized contractor complete the task.
Whatever your decision, there are some key issues to consider before taking the large step into outsourcing.
1. Retain your information.
If you outsource everything to a service provider, who owns all the data that they gather? Where does that data go if you wish to change maintenance providers? Will their control of your data restrict you from changing providers – effectively holding you to ransom?
If you do choose to outsource completely, it is advisable to require them to use your CMMS. For example, Limble CMMS allows you to keep all of your data, giving contractors limited access to the software. Work Orders can be sent directly to the vendor through our software (see how this works in practice here). The vendor receives the WOs, performs the work, enters time and spare parts spent, and closes the WO.
This way, you have insight into how the maintenance is being acquitted. You also may carry out audits at your discretion. Should there be an issue with your provider, it is easy to transfer control to a new provider who can continue without an interruption to your business.
If you selectively outsource, you need to be clear in your SLA what data will be provided, in what format, and the timeframe in which you must receive it. An example of selective outsourcing is an electrical maintenance group carrying out specialized tests and inspections or a heavy maintenance workshop carrying out your annual inspections. Require them to upload their data to your maintenance program.
2. Design a customized SLA to suit your needs
You can shift business risk onto a third-party provider through a well-constructed SLA. If you stipulate a percentage of equipment availability in the SLA, you can gain share, and pain share, if the availability is higher or lower. Your maintenance contractor gets paid less as your availability reduces and receives a bonus if it improves.
Be clear on your expectations concerning the use of maintenance information, the application of safety procedures, and the desired outcomes.
Outsourcing maintenance to a contractor does not absolve you of all responsibility, as you cannot delegate regulatory compliance issues. If your equipment is found to be in breach of regulations, the law will hold you to account. Implement a strong governance system to audit ongoing contractor compliance .
3. Price isn’t everything
Do not base your contractor selection on price alone. Competence, capability, compliance, and compatibility are all factors you should consider. The price of that more expensive contractor may pay back tenfold in increased uptime, reduced inventory, and extended machine life.
Be the manager you were hired to be and think about the big picture.
To recap
While businesses still exist that only do reactive maintenance, they usually do so for specific reasons. The majority of operators now realize that proactive maintenance is significantly more cost-effective, especially for heavy equipment.
While the upfront administration for implementation may seem prohibitive, you can gently introduce your business, machinery, and technicians to a new paradigm through simple pilot projects. Proactive maintenance coupled with a reliable and modern CMMS will drive greater revenue, greater uptime, lower inventory costs, and improved earnings.
If you’re interested in using Limble CMMS as the foundation for your future heavy equipment maintenance efforts, you can request a demo or start a month-long free trial.
Manutenção e reparo de equipamentos
- Manutenção de terceiros
- Um guia para criar um programa de manutenção de equipamentos
- A oficina de máquinas CNC:um guia completo
- Guia de Serviço e Manutenção de Equipamentos Industriais
- Os prós e contras da manutenção de equipamentos pesados
- Dicas de segurança para equipamentos pesados
- Manutenção de equipamentos de construção
- Manutenção de equipamentos pesados nos meses de inverno
- Guia de uso de equipamentos pesados para demolição e desconstrução
- Qual a importância da manutenção de equipamentos pesados?