Tepex reforça o demonstrador de apoio de cabeça para cadeirinha de criança
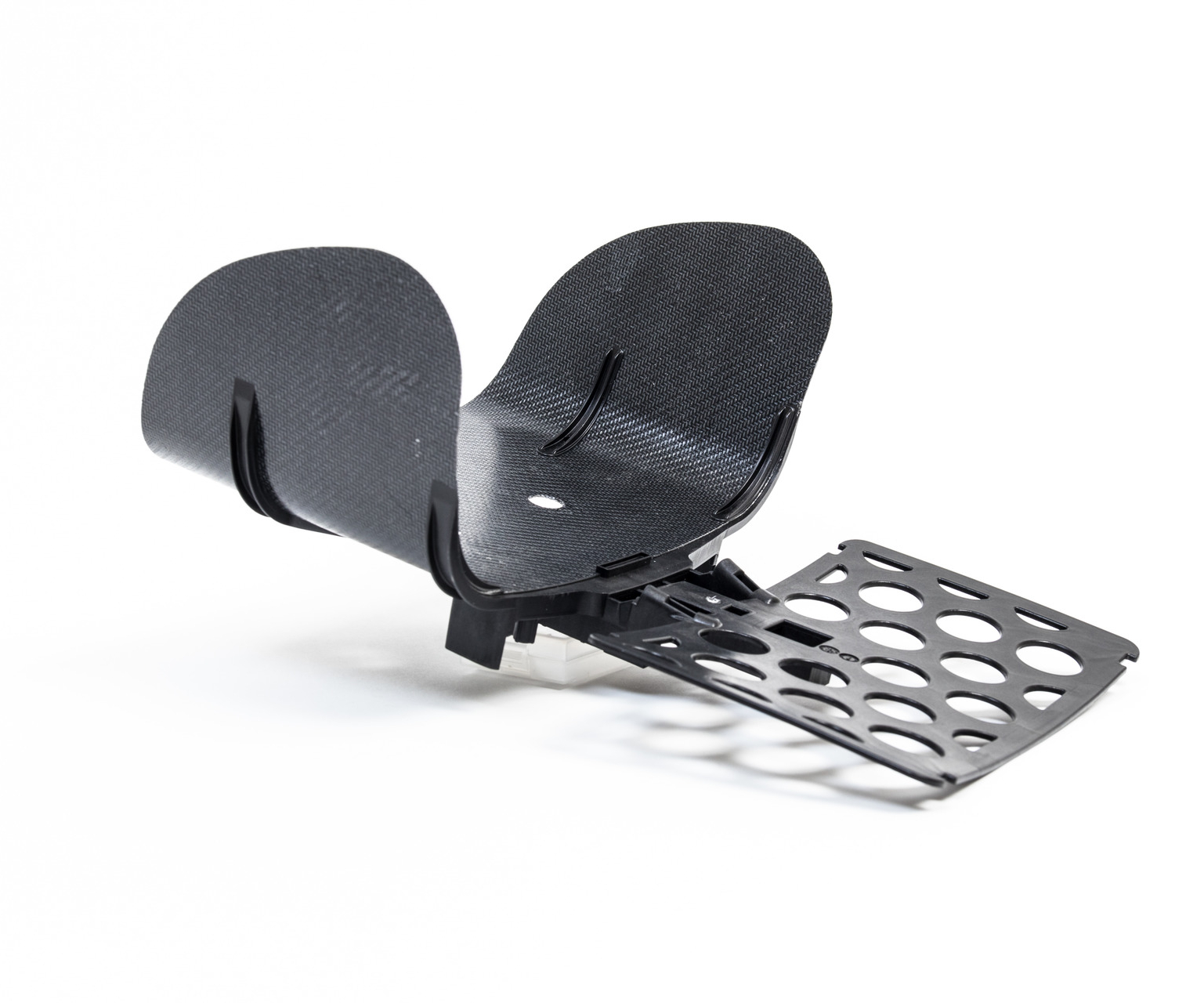
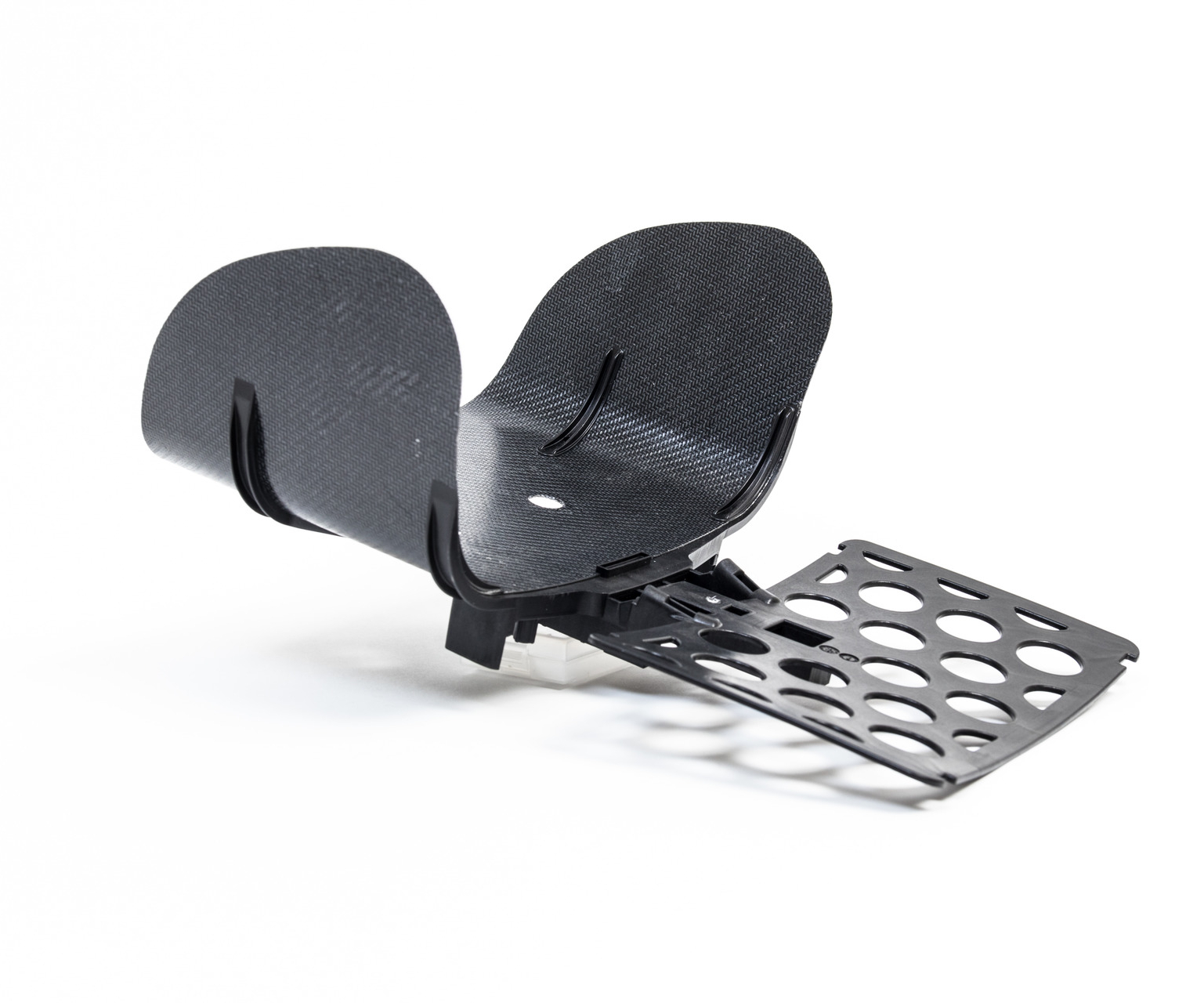
Os materiais compósitos termoplásticos reforçados com fibra contínua Tepex da LANXESS (Pittsburgh, Pa., EUA) mostraram potencial para uma variedade de aplicações automotivas - aquelas CW abrangeu recentemente o suporte para um pilar A automotivo de composto metálico híbrido, uma concha do banco traseiro automotivo e um demonstrador de apoio de braço no console central. Um estudo de caso recente da empresa adiciona construção leve de componentes de segurança estrutural à lista.
A LANXESS desenvolveu recentemente um encosto de cabeça para cadeirinha infantil como um demonstrador de tecnologia para ilustrar as oportunidades de materiais neste mercado. O componente é produzido em um processo de moldagem por injeção de compósito de espuma de partículas (PCIM).
“O inserto feito de Tepex pode reduzir o peso do encosto de cabeça em até 30% em comparação com a variante de componente produzida comercialmente - e com desempenho em colisões comparativamente bom também. Também simplifica o processo de produção ”, afirma o Dr. Klaus Vonberg, do Tepex Automotive Group da LANXESS. Tepex é desenvolvido e produzido pela subsidiária da LANXESS, Bond-Laminates GmbH (Brilon, Alemanha).

O demonstrador é o resultado de um projeto de pesquisa transnacional financiado pelo Ministério Federal da Economia e Energia da Alemanha como parte do Programa Central de Inovação para Pequenas e Médias Empresas (PMEs) (acrônimo alemão:ZIM). Participam deste programa o Departamento de Estruturas Leves e Tecnologia de Polímeros (SLK) da Universidade de Tecnologia de Chemnitz, Polycomb GmbH (Auengrund, Alemanha) e o fabricante de cadeiras infantis Avionaut (Szarlejka, Polônia).
Para o encosto de cabeça, os parceiros do projeto desenvolveram um processo de produção alternativo baseado no PCIM. Para reforçar o encosto de cabeça em locais individuais e reduzir o peso, eles usaram um inserto personalizado feito de dinalite Tepex 104-FG290 (4) / 47%. Este é um material composto à base de polipropileno que é reforçado com duas camadas de mechas de fibra de vidro contínua. O inserto é formado em uma única operação de processo usando uma ferramenta de moldagem por injeção com placa giratória e injetada de volta com um composto de polipropileno reforçado com fibra de vidro curta para integrar a estrutura de suporte para o encosto de cabeça e encosto. O inserto pré-fabricado é então espumado de volta em uma segunda ferramenta usando espuma de partículas com base em polipropileno expandido (EPP).
O encosto de cabeça de referência, ao contrário, é atualmente produzido em série usando vários componentes individuais, de acordo com a LANXESS. A estrutura de suporte consiste em polipropileno reforçado com fibra de vidro longa. Ele é montado com um componente de EPP espumado separadamente usando quatro pinos transportadores de polipropileno.
“O novo processo de produção altamente integrado não apenas é mais eficiente em termos de energia do que o procedimento anterior, mas também resulta diretamente no componente acabado. Isso reduz o número total de peças de seis para uma, o que também diminui os custos de produção em termos de logística e os gastos com máquinas necessários ”, diz Norbert Schramm, assistente científico da Universidade de Tecnologia de Chemnitz e chefe do projeto ZIM local.
A redução de peso com a versão atual do componente do apoio de cabeça com fibra de vidro é de aproximadamente 26%, embora os participantes do projeto observem potencial para mais. De acordo com Schramm, “se um reforço à base de fibras de carbono for usado no produto semiacabado e no material de moldagem por injeção, o resultado é uma montagem quase 30% mais leve”.
Para o projeto, o SLK escolheu os materiais, analisou a aderência do compósito, projetou a estrutura e realizou a otimização da topologia. A Polycomb liderou o desenvolvimento e a implementação do design do demonstrador, a produção de protótipos e a otimização do conceito do sistema. A Avionaut analisou as áreas de transmissão de força, desenvolveu o projeto e examinou o comportamento em colisões do encosto de cabeça e de todo o assento em testes de colisão realistas, por exemplo. A LANXESS ajudou os parceiros do projeto na escolha dos materiais e também auxiliou em tarefas como o desenvolvimento do processo de moldagem híbrida.
A LANXESS vê potencial para a Tepex e o novo processo na produção de transportadores infantis, encostos e apoios de braço, bem como conchas de assento para novos conceitos de assento altamente complexos em carros autônomos ou para assentos confortáveis para ônibus, ônibus VIP e familiares e veículos elétricos.
Resina
- Assento para bicicleta
- Monociclo
- Assento para criança
- Tampa do assento do vaso sanitário de fibra de carbono
- Lanxess adiciona duas novas linhas de produção para material composto Tepex
- Parte traseira composta leve desenvolvida pela Covestro e a montadora chinesa GAC
- Primeiro pedal de freio totalmente de plástico para carro esportivo elétrico a bateria
- Composto termoplástico reforçado com fibra contínua feito inteiramente de recursos naturais
- Compostos termoplásticos LANXESS usados na concha do banco traseiro do Audi A8
- JEC World 2019:Demonstrador da nacela do motor Cevotec