Provando soldagem LM PAEK para Demonstrador de Fuselagem Multifuncional
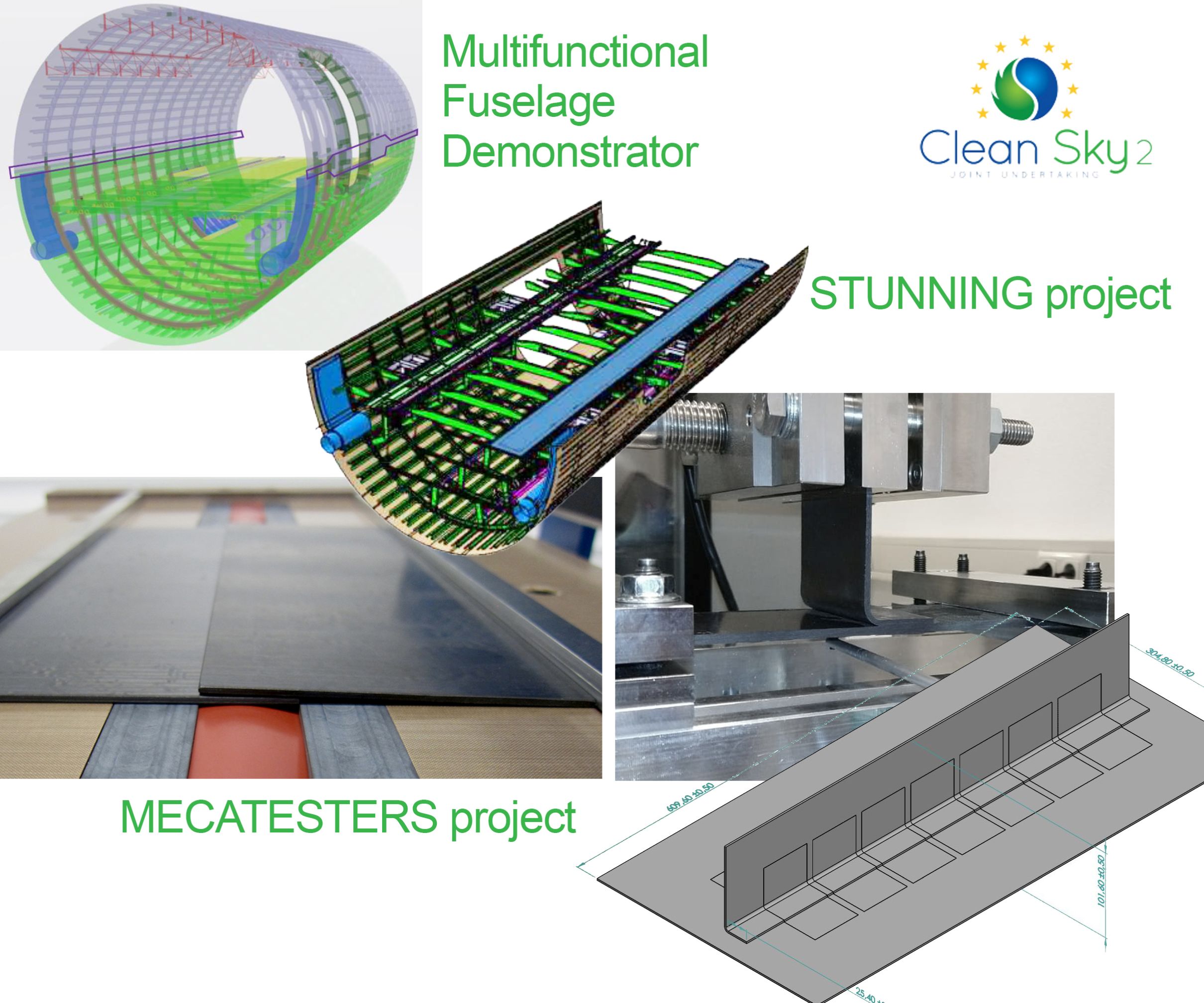
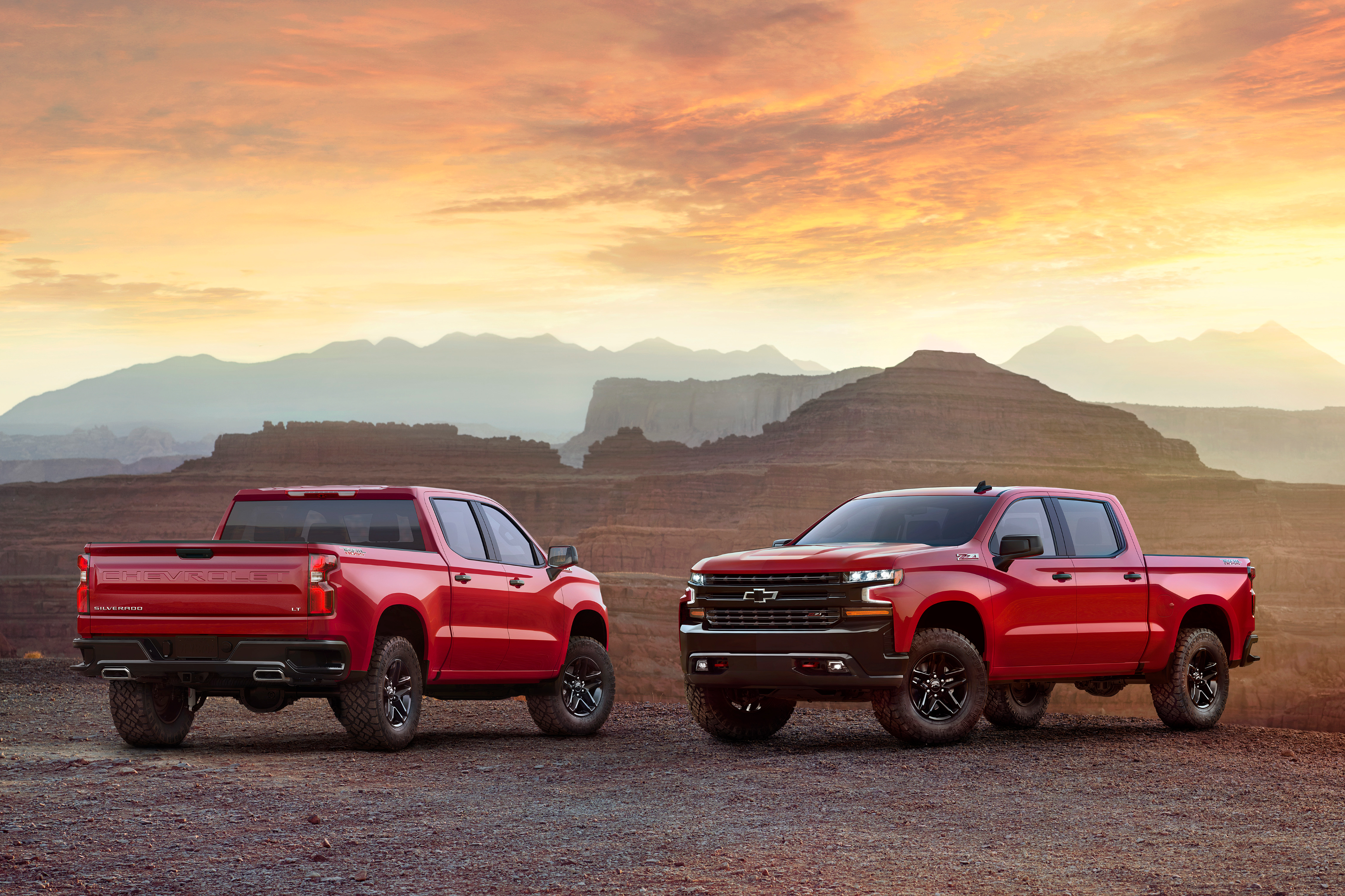
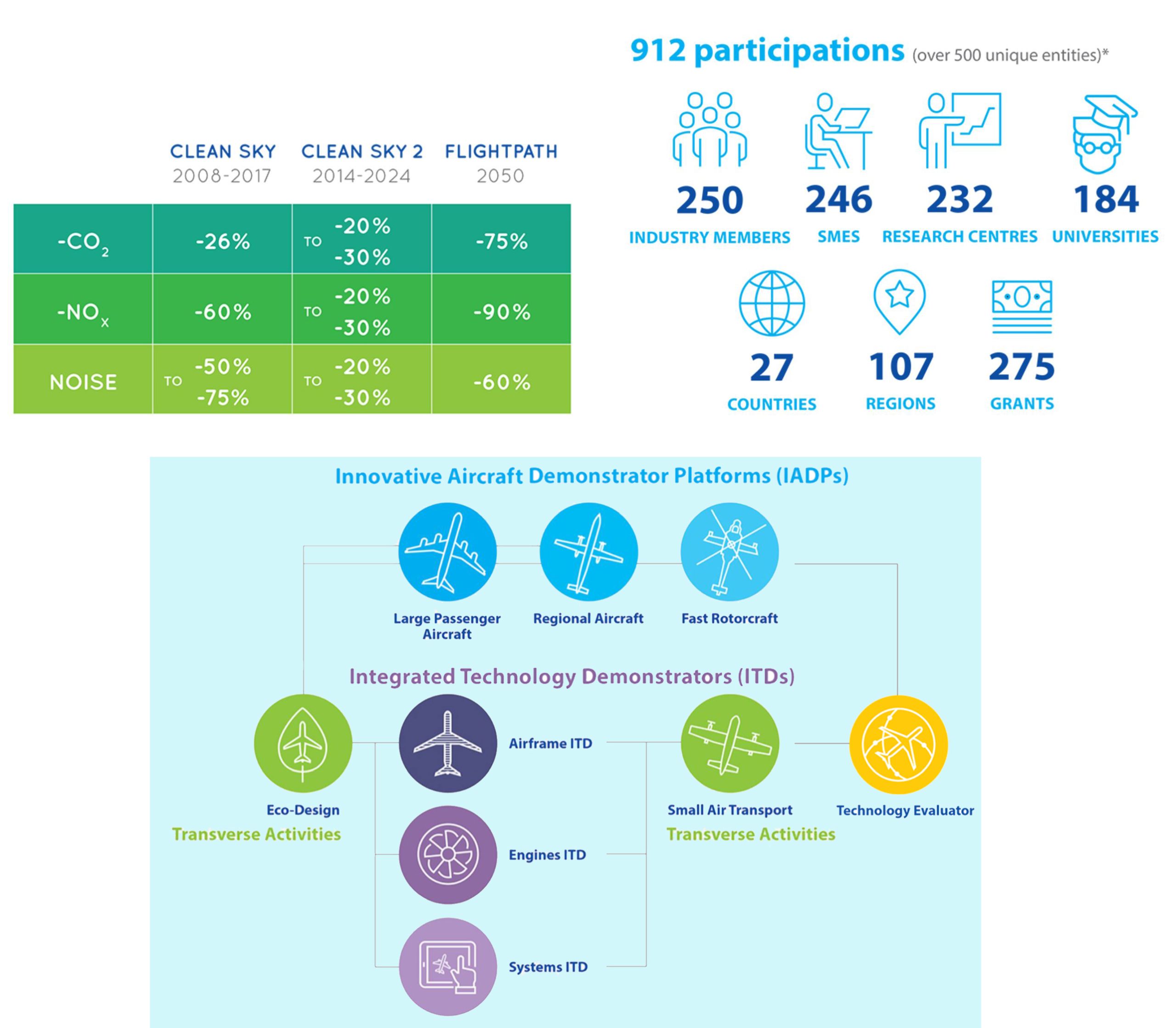
Este tipo de investigação aeronáutica começou com o Programa-Quadro da Comissão Europeia (FP) para financiamento de I&D, abrangendo o FP2 (1987-1991) ao FP7 (2007-2013). Esses programas contribuíram substancialmente para o amadurecimento de uma ampla variedade de tecnologias para o nível de preparação de tecnologia (TRL) 6 e implementação em aeronaves como o Airbus A350.
Um dos diferenciais do Clean Sky 2 é sua organização em torno de grandes manifestantes. O MFFD é uma das três seções de fuselagem em escala real que estão sendo produzidas na Plataforma de Demonstração de Aeronaves Inovadoras (IADP) de Grandes Aeronaves de Passageiros (LPA) (veja o texto em azul no topo do quadrado azul no infográfico acima) . No LPA IAPD, existem três plataformas. O MFFD fica dentro da Plataforma 2 “Estrutura de Sistema-Cabine-Integração Física Inovadora”, que apresenta dois outros grandes demonstradores.
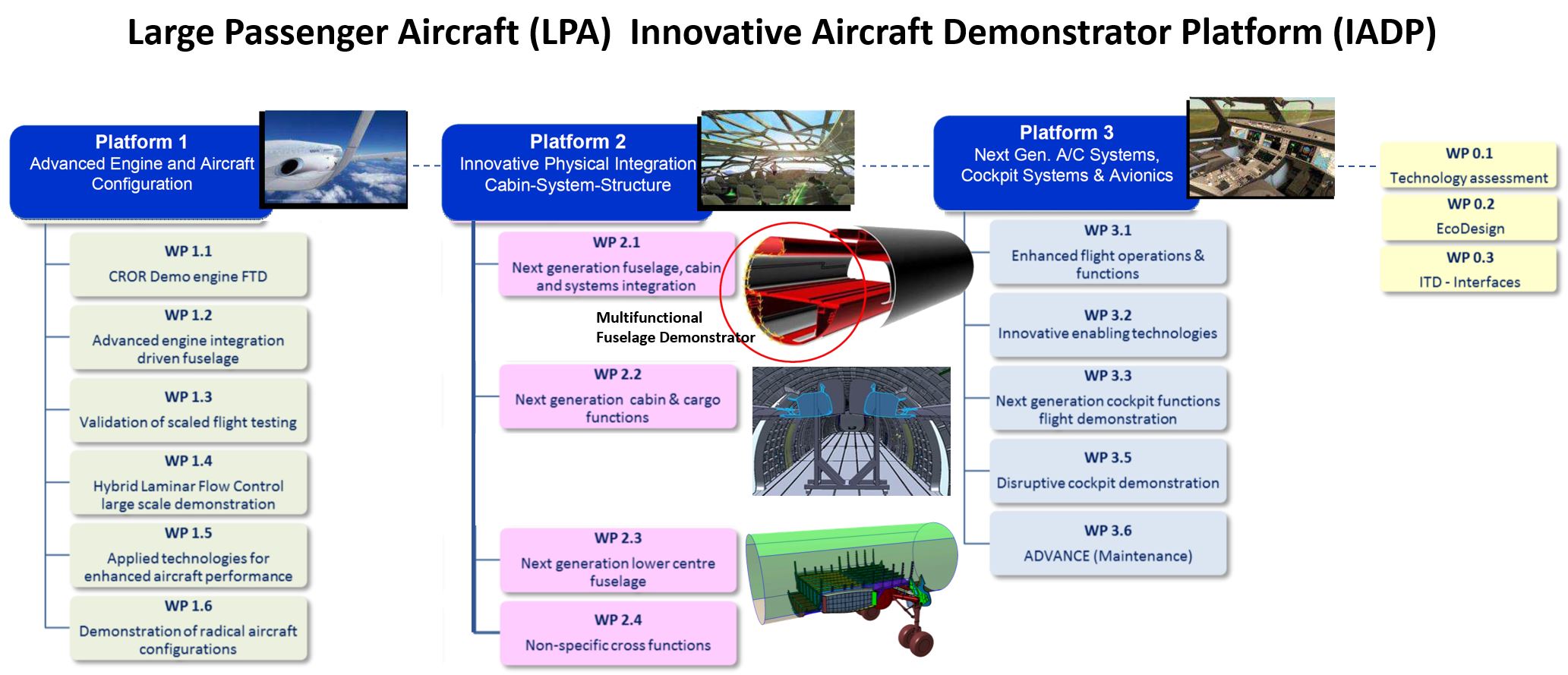
Para entender o que isso significa, volto a algo que engenheiros da Airbus Airframe Research &Technology (R&T) de Getafe, na Espanha, me disseram enquanto eu pesquisava compostos multifuncionais em 2015. Eles disseram, em essência, “Não queremos mais a duplicação e desperdício de fazer um cilindro estrutural externo e um cilindro interno; queremos integrar a fuselagem estrutural com os sistemas de cabine. ” Lutei para visualizar o que isso significava - até que vi um esboço do MFFD.
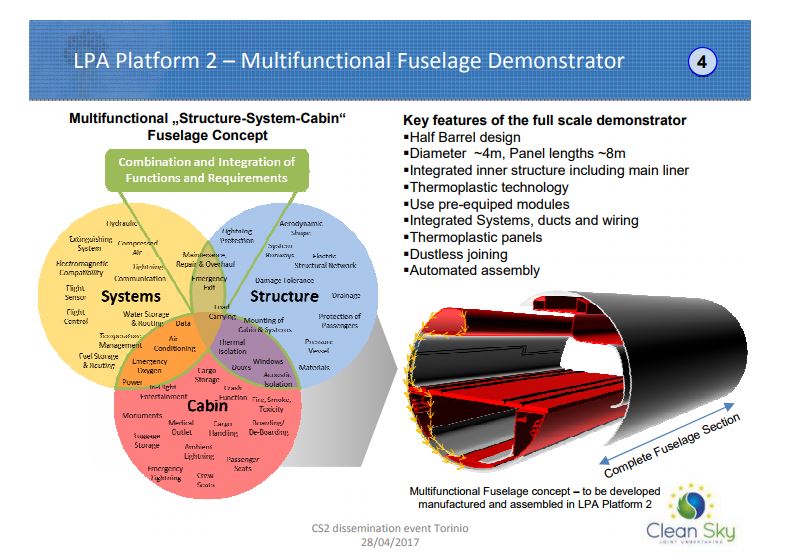
FONTE | Disseminação do Clean Sky 2 (CS2) e “Demonstradores de compostos termoplásticos - Roteiro da UE para fuselagens futuras”.
“Modularidade, integração e criação de plataformas comuns são fundamentais”, diz Ralf Herrmann, Airframe R&T Típica Fuselagem da Airbus Operations GmbH (Bremen, Alemanha) e líder do programa MFFD. Estou citando aqui da página MFFD no site Clean Sky 2:
Herrmann:"Já sabemos há muito tempo que os benefícios da redução de peso e da redução de custos recorrentes na produção de aeronaves - ao usar compósitos termoplásticos - só pode ser alcançado pela integração de várias disciplinas. Isso significa que focar apenas na estrutura não pode alcançar todos os benefícios da tecnologia de compósitos. ”
A versatilidade dos termoplásticos precisa ser aplicada em combinação com uma abordagem de design, de acordo com o oficial de projeto da Clean Sky 2, Paolo Trinchieri:“É necessário remover a separação artificial de funções na fase de pré-projeto da aeronave e planejar uma alta taxa de produção de fabricação, montagem e instalação de aeronaves logo no início. ”
Herrmann foi anteriormente o gerente de projeto para o projeto FP7 MAAXIMUS (estrutura de aeronaves mais acessíveis por meio de dimensionamento nUmérico estendido, integrado e maduro). Executando de abril de 2008 a setembro de 2016, MAAXIMUS incluiu 60 parceiros e teve como objetivo demonstrar o rápido desenvolvimento e validação certa na primeira vez - amadurecendo habilitadores virtuais e físicos simultaneamente - de uma fuselagem composta altamente otimizada para atingir 50% de redução no tempo de montagem de grandes seções da fuselagem, redução de 10% nos custos recorrentes, peso estrutural 10% menor e ciclo de desenvolvimento 20% mais curto. Os objetivos do MFFD podem ser vistos como uma extensão:
- Ative taxas de produção de 70-100 aeronaves / mês
- Reduza o peso da fuselagem em 1.000 kg
- Reduza os custos recorrentes em 20%.
Um facilitador chave é a união sem poeira (sem orifícios, sem fixadores) por meio de componentes compostos termoplásticos soldados. Herrmann explica que a abordagem sequencial atual para a fabricação de aeronaves - onde a estrutura da fuselagem deve estar razoavelmente completa antes que os sistemas mais a cabine e os recursos de carga possam ser instalados - é demorada e “sensível a falhas”. Em vez disso, o MFFD busca elementos estruturais e módulos de sistema pré-equipados e altamente integrados que podem ser instalados bem cedo, muito antes da montagem final.
Mudança para juntas longitudinais e LM PAEK
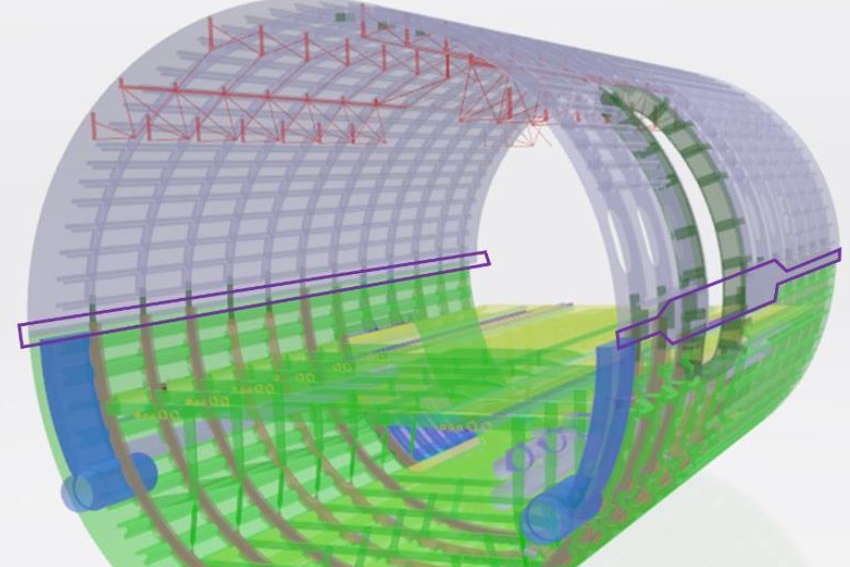
As atividades do projeto MFFD começaram em 2017. Todos os anos há pelo menos uma chamada de propostas (CFP) em que os líderes do projeto descrevem tópicos que precisam de ser desenvolvidos. Como pode ser visto na imagem abaixo, o projeto da junta de polarização mostrado no CFP08 (abril de 2018) foi alterado para uma junta longitudinal no CFP09 (setembro de 2018).
“A junta polarizada apresentou problemas em relação à acessibilidade e fixação de estruturas de piso que percebemos que seriam difíceis de superar dentro do prazo determinado”, explica Herrmann. “Portanto, decidimos voltar ao design convencional para diminuir o risco. Nosso principal interesse é mostrar como integrar todos os sistemas e elementos da cabine que podem ser instalados antes da Montagem de Componentes Principais (MCA). Esta também será a primeira vez que este material composto termoplástico será aplicado em estruturas de fuselagem primária em escala real para grandes aeronaves de passageiros. ”
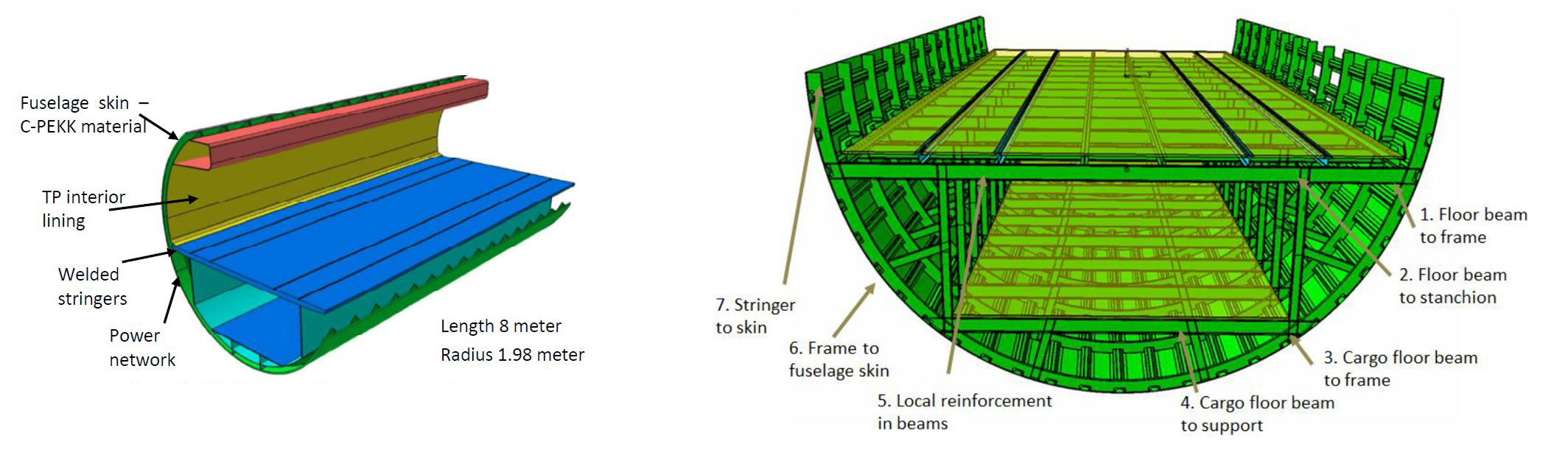
O projeto MFFD mudou de um projeto de junta de polarização para uma junta longitudinal mais convencional em 2018. FONTE | CFP08 p.87 (esquerda) e CFP09 p. 133 (certo).
Outra mudança foi no material da matriz do composto termoplástico (TPC). Os tópicos de MFFD em CFP08 e CFP09 referem-se a fibra de carbono / PEKK (polietercetonocetona), mas pelo CFP10 (março de 2019), o material de linha de base foi descrito como fibra de carbono e PAEK (poliariletercetona). PAEK é a família geral de polímeros dentro da qual residem PEEK, PEKK e LM PAEK.
Conforme descrito em meu blog em PEEK vs. PEKK vs. PAEK, o fornecedor de materiais da Cetex TenCate, agora Toray Advanced Composites, produz todos os três polímeros como fita reforçada com fibra de carbono e afirma que as propriedades são basicamente as mesmas. No entanto, Cetex TC1225 CF / LM PAEK a fita derrete a 305 ° C enquanto TC1320 CF / PEKK fita derrete a 340 ° C . E, de acordo com o CTO global da Toray Advanced Composites, Scott Unger, “LM PAEK tem um fluxo muito melhor ... e também pode ser processado em velocidades mais altas do que PEKK e PEEK.” TC1225 também custa menos.
Fuselagem inferior do MFFD:projeto IMPRESSIONANTE
STUNNING é o nome do projeto para o desenvolvimento e fabricação da metade inferior totalmente equipada do MFFD. O projeto visa amadurecer ainda mais:
- Processos de montagem automatizados
- Tecnologias de fabricação e montagem de termoplásticos
- Tecnologias integradas de desenvolvimento de design e manufatura
- Desenvolvimento de arquiteturas avançadas de sistemas elétricos.
Bas Veldman, gerente de programa da GKN Fokker (Hoogeveen, Holanda) e gerente de projeto da STUNNING, explica que o MFFD terá 8 metros de comprimento e 4 metros de largura com um raio de 2 a 2,5 metros, que é a escala real para um corredor único Aviões da família A320. “É semelhante ao A321, que não é exatamente circular, mas tem a forma de um ovo (um pouco mais alto do que largo)”, acrescenta.
A seção inferior da fuselagem em 180 ° compreenderá o casco inferior da fuselagem com longarinas e armações soldadas, a estrutura da cabine e do piso de carga, e os principais elementos internos e do sistema relevantes. “Vamos entregar módulos grandes pré-equipados para uma montagem plug-and-play muito rápida”, diz Veldman.
GKN Fokker é o principal parceiro da STUNNING e tem quatro divisões participantes, incluindo Aerostructures (Papendrecht, Holanda), Fokker ELMO (Hoogerheide, Holanda), GKN Fokker Engineering Romênia (Bucareste) e GKN Fokker Technologies (Papendredcht, Holanda). GKN Fokker ELMO é um fornecedor de chicotes de fiação para aeronaves e tecnologia de sistemas elétricos. “É responsável pela arquitetura de sistemas em STUNNING e se concentrará na otimização do sistema elétrico”, explica Veldman, “e colabora com o consórcio CFP08 MISSION no desenvolvimento de um sistema de barramento de força inovador.”
“Diehl Aviation (Laupheim, Alemanha) é responsável pela estrutura interna, incluindo subsistemas e piso, painéis das paredes laterais e como eles são unidos, interfaces de monumentos e sistemas multiportas inteligentes”, continua Veldman. “A NLR (Netherlands Aerospace Centre, Amsterdam) é responsável pela fabricação da pele da fuselagem e longarinas, e a TU Delft está ajudando na montagem, com base em sua experiência em soldagem ultrassônica.” (Veja "Soldagem de compostos termoplásticos" para mais informações sobre soldagem ultrassônica.)
Programa de teste de soldagem MECATESTERS
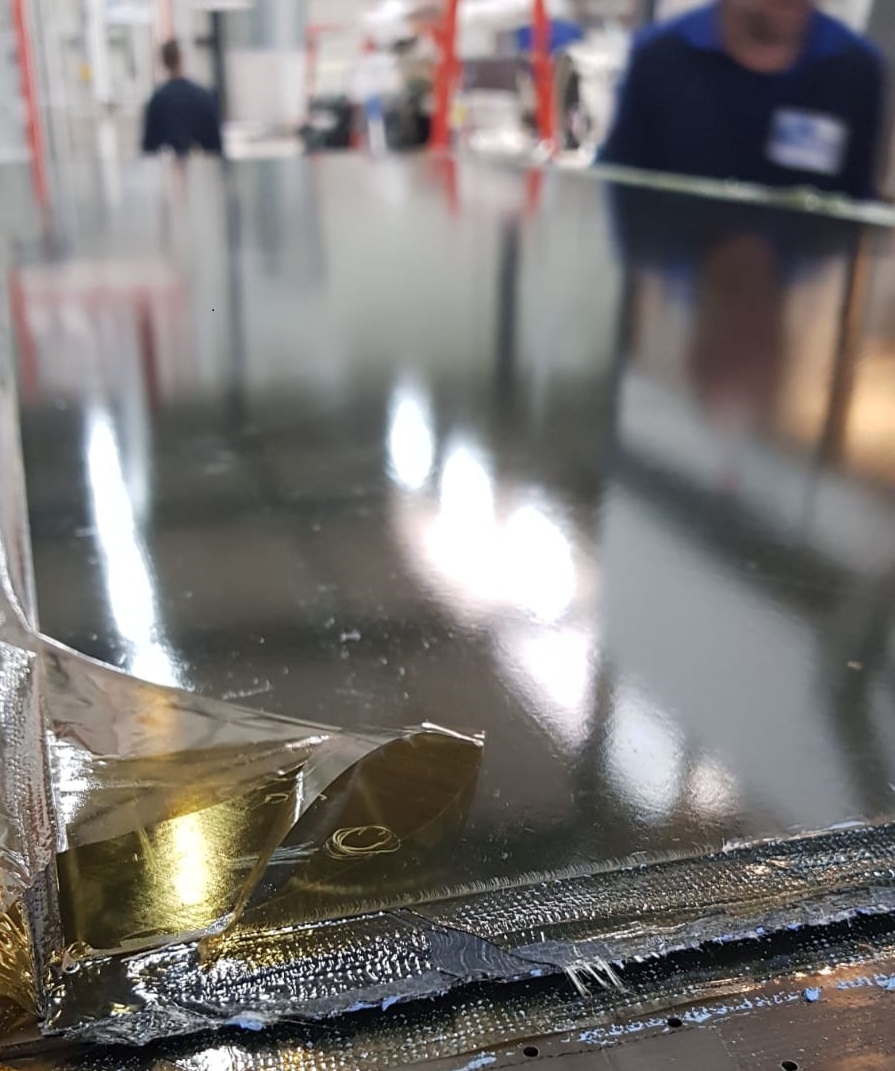
“STUNNING lançou sete tópicos de CFP e cinco já começaram a funcionar, incluindo MAYA, MISSION, EMOTION, TCTool e MECATESTERS”, diz Veldman. O último é um grande programa de teste de soldagem com KVE Composites (Haia, Holanda) e Rescoll (Pessac, França) que teve início em abril de 2019 com duração de 30 meses. Veldman explica que embora a KVE tenha uma longa história com soldagem por indução de tecidos e compósitos termoplásticos de fita UD, as peças soldadas por indução voando em aeronaves até agora usaram tecido. “Na STUNNING estamos estabelecendo as melhores práticas com reforços UD e materiais LM PAEK, e também comparando a soldagem por indução com a soldagem por condução sob carga em serviço e condições ambientais típicas.” Embora a soldagem por resistência e a soldagem ultrassônica estejam incluídas em outros pacotes de trabalho MFFD e CFPs (consulte “ Juntando as duas metades ”Abaixo), a soldagem por indução e a soldagem por condução são as duas únicas técnicas no MECATESTERS.
Labordus na KVE explica que para os três pacotes de trabalho MECATESTERS (WP 1, 2 e 3), KVE fará todos os laminados de teste usando fibra de carbono TC1225 UD curada em autoclave / fita LM PAEK (consulte “Primeiro laminado Toray LM-PAEK para Projeto Clean Sky MECATESTERS ”). A KVE também preparará amostras soldadas por indução para teste, enquanto o GKN Fokker produzirá amostras soldadas por condução e a Rescoll executará todos os testes físicos. “O nome Rescoll deriva de pesquisa e colagem, que significa ligação em francês”, diz Labordus. “Eles são conhecidos por suas pesquisas em todos os tipos de ligação e oferecem um laboratório de testes bem equipado para polímeros e compostos, incluindo mecânicos, ambientais, de inflamabilidade e todos os testes possíveis para qualificação nas indústrias aeroespacial, automotiva, ferroviária e outras.”
Parâmetros e testes do processo
“Na verdade, estamos começando com o WP 2 para definir os parâmetros do processo, como limites superior e inferior para temperatura e pressão de soldagem por indução”, diz Labordus. “Por exemplo, temos um nominal pressão que normalmente usamos, mas iremos para pressões mais baixas até começarmos a ver defeitos como vazios, e então avaliaremos essas propriedades de solda para estabelecer o limite de pressão inferior. ” Os testes também avaliarão a velocidade de solda, que afeta a taxa de resfriamento e a cristalinidade da solda e, potencialmente, as propriedades mecânicas. Os mesmos parâmetros serão investigados na Fokker para soldagem por condução.
Para avaliação, o programa MECATESTERS realizará vários testes, incluindo:
- Teste de lapshear de acordo com ASTM D5868–01
- Teste de tração e cisalhamento em cupons de perfil L
- GIC e GIIC por ISO 15024 e ISO 15114, respectivamente
(este teste de resistência será realmente concluído no WP 1)
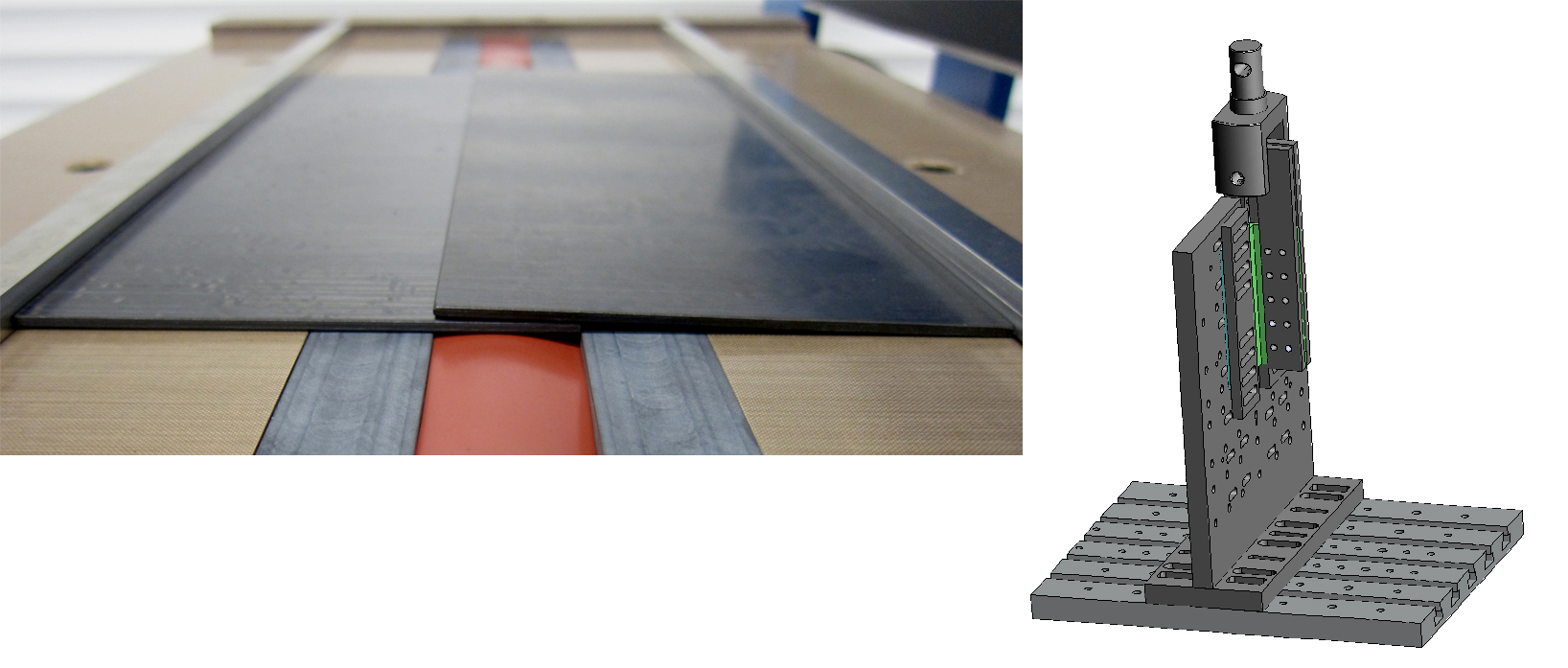
Cupom de cisalhamento de uma única volta do laminado de fita UD pronto para soldagem por indução (à esquerda) e acessório de teste para testes combinados de cisalhamento e remoção de cupom de perfil L soldado usando a ferramenta desenvolvida pela Rescoll (à direita). FONTE | KVE Composites, Rescoll.
“O método de teste de pull-off vem de um padrão interno desenvolvido por GKN Fokker”, explica o engenheiro da Rescoll, Thomas Salat. “O teste de retirada dos perfis soldados é perpendicular à pele para carregamento de casca”, observa Labordus, “e paralelo à pele para carga de cisalhamento. Descascar e cisalhar são os dois extremos, mas também testaremos novas combinações destes que refletem condições práticas de carga em serviço. ” Este teste será concluído para duas espessuras de laminado distintas derivadas do projeto da fuselagem MFFD - 2,2 e 2,8 milímetros - em temperatura ambiente (RT), temperatura fria (-55 ° C) e alta temperatura (80 ° C) usando carga estática.
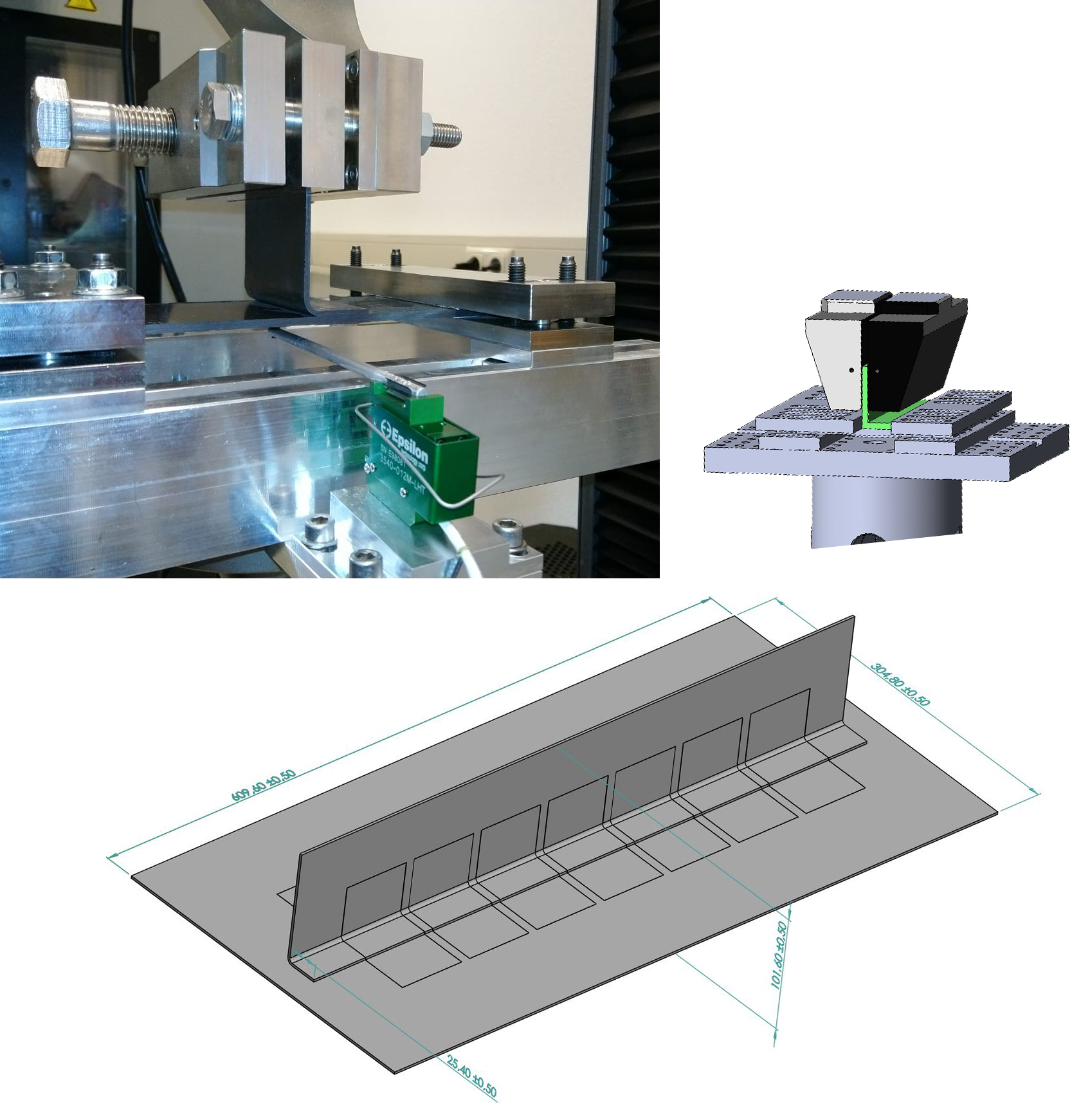
Testes de pull-off em cupons de perfil L na KVE Composites (canto superior esquerdo). No MECATESTERS, esse tipo de teste usará uma pinça e uma configuração de teste desenvolvida pela Rescoll para eliminar a deflexão da pele (canto superior direito). Os cupons de teste serão cortados de painéis soldados (parte inferior). FONTE | Rescoll, KVE Composites.
Preparação da superfície, envelhecimento e fadiga
O WP 1 começará com o teste de resistência. “Para os testes de fissurização (GIC e GIIC), iniciaremos uma trinca no compósito e mediremos como essa trinca se comporta quando carregada”, explica Salat. “Um deles é um teste estático que aumenta a carga até a falha. Também faremos um teste dinâmico em que repetimos a carga estática um milhão de vezes, o que leva de uma a duas semanas para ser concluído. Veremos se a solda composta pode suportar essa fadiga. Este modo II é um novo tipo de teste cíclico. Estamos desenvolvendo um método retirado de um artigo técnico publicado pela Universidade da Europa e finalizando os parâmetros agora. ”
Também no WP 1, os parâmetros de soldagem estabelecidos no WP 2 serão usados para examinar os efeitos da preparação da superfície, bem como do envelhecimento e da fadiga. “Veremos os contaminantes de superfície e como eles podem afetar a solda”, diz Labordus. “Também investigaremos três tipos diferentes de desmoldantes usados comumente no processamento de prensagem e autoclave; tipos específicos de preparação de superfície, incluindo lixamento, abrasivos e tratamento de plasma; e também o uso de um filme extra de resina na superfície a ser soldada. Além disso, estudaremos a influência da orientação da fibra, por exemplo, mais / menos 45 graus na interface de solda. ”
A Rescoll também usará uma câmara de condicionamento a 70 ° C e 90% de umidade para simular o envelhecimento em serviço, diz Salat. “Em seguida, realizaremos os testes padrão para ver se isso afeta o desempenho da soldagem.” Labordus acrescenta que um número limitado de amostras será coletado a 100 ° C e 120 ° C, "para validar a alegação de que os compósitos termoplásticos não têm uma queda brusca acima de 80 ° C."
Além do teste de fissurização dinâmica / GIIC, o teste de fadiga será realizado nos modos de cisalhamento de volta única e pull-off. “Começaremos com 80% da carga de falha estática e atingiremos 50 ou 75% disso em fadiga por um milhão de ciclos”, diz Labordus. “Faremos outros testes também, mas ainda estamos discutindo sobre eles”, acrescenta Salat.
Soldagem em colchetes compostos curtos
Embora os detalhes do WP 3 ainda estejam sendo finalizados, ele visa investigar as soldas de braquetes moldados por compressão feitos de material de fibra curta à pele laminada UD. “Faremos novamente benchmark dos parâmetros do processo e caracterizaremos as propriedades mecânicas da solda”, diz Labordus, “mas ainda estamos trabalhando para definir a geometria para teste”.
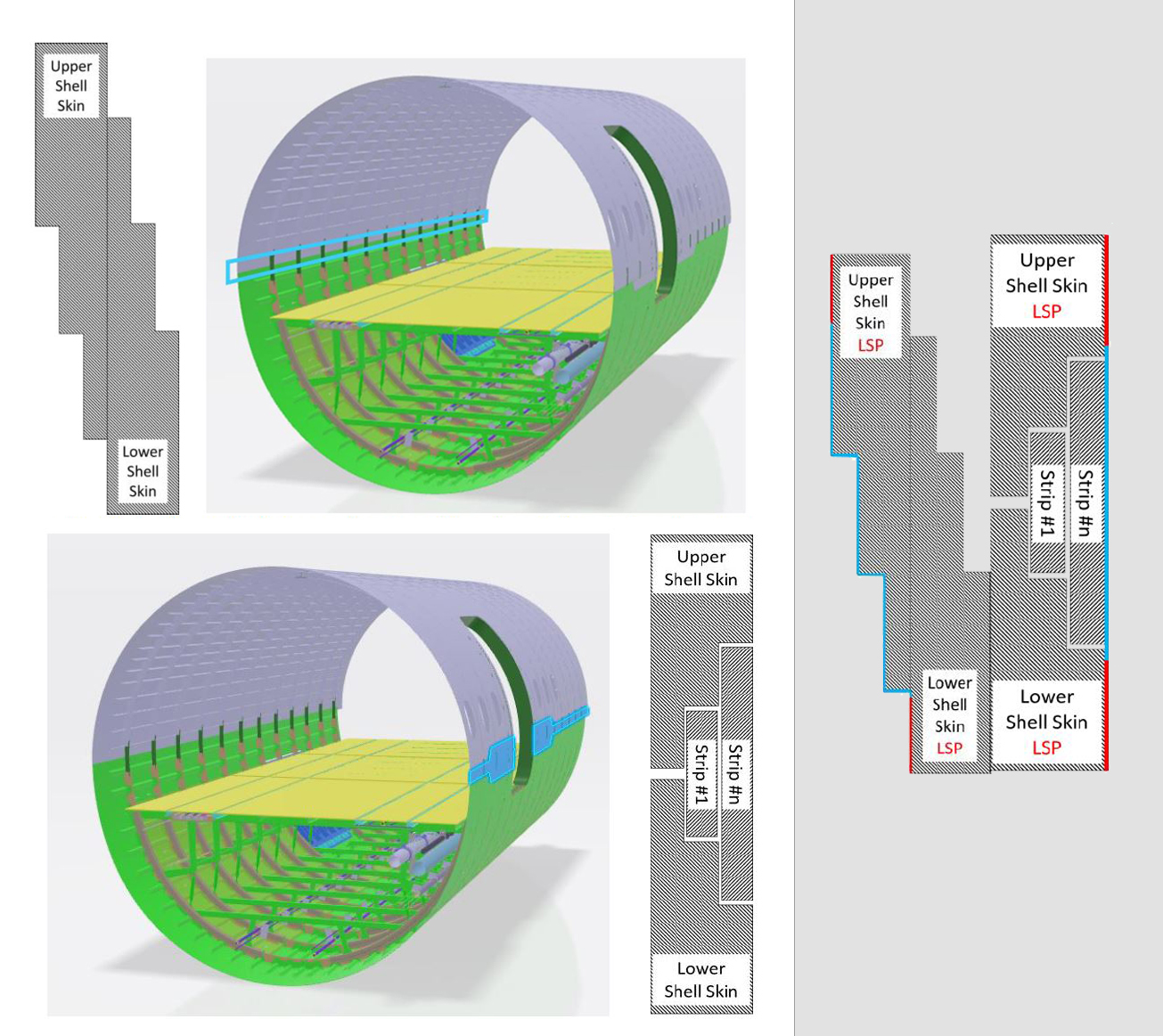
Longarinas e clipes soldados a uma fuselagem termoplástica. FONTE:Clean Sky 2 11 th Chamada de Propostas JTI-CS2-2020-CfP11-LPA-02-35, “Recursos inovadores de detenção de desagregação para juntas soldadas termoplásticas longas”, Figura 2, p. 94
Grampos e suportes soldados
Conforme descrito no tópico CFP10 JTI-CS2-2019-CfP10-LPA-02-31, todos os clipes de estrutura e suportes do sistema para a fuselagem inferior do MFFD serão fabricados por meio de moldagem por injeção de compostos de fibra curta feitos pela reutilização de resíduos de fábrica de a produção de laminados TPC de fibra contínua do gerente de tópico GKN Fokker. CF / PAEK é o material da linha de base e a soldagem é o método de junção da linha de base, embora o método de soldagem específico não seja prescrito.
De acordo com o texto do CFP10, a fuselagem inferior do MFFD terá 13 quadros e cerca de 36 longarinas, exigindo cerca de 500 clipes de quadro (observe que estas são estruturas primárias que requerem testes estruturais e este total inclui clipes usados para teste) e aproximadamente 270 suportes de sistema (que são estruturas secundárias) divididas pelos tipos mostrados abaixo:20 suportes do sistema (1), 120 suportes do sistema (2), 50 suportes do sistema (3) e 80 suportes do sistema (4).
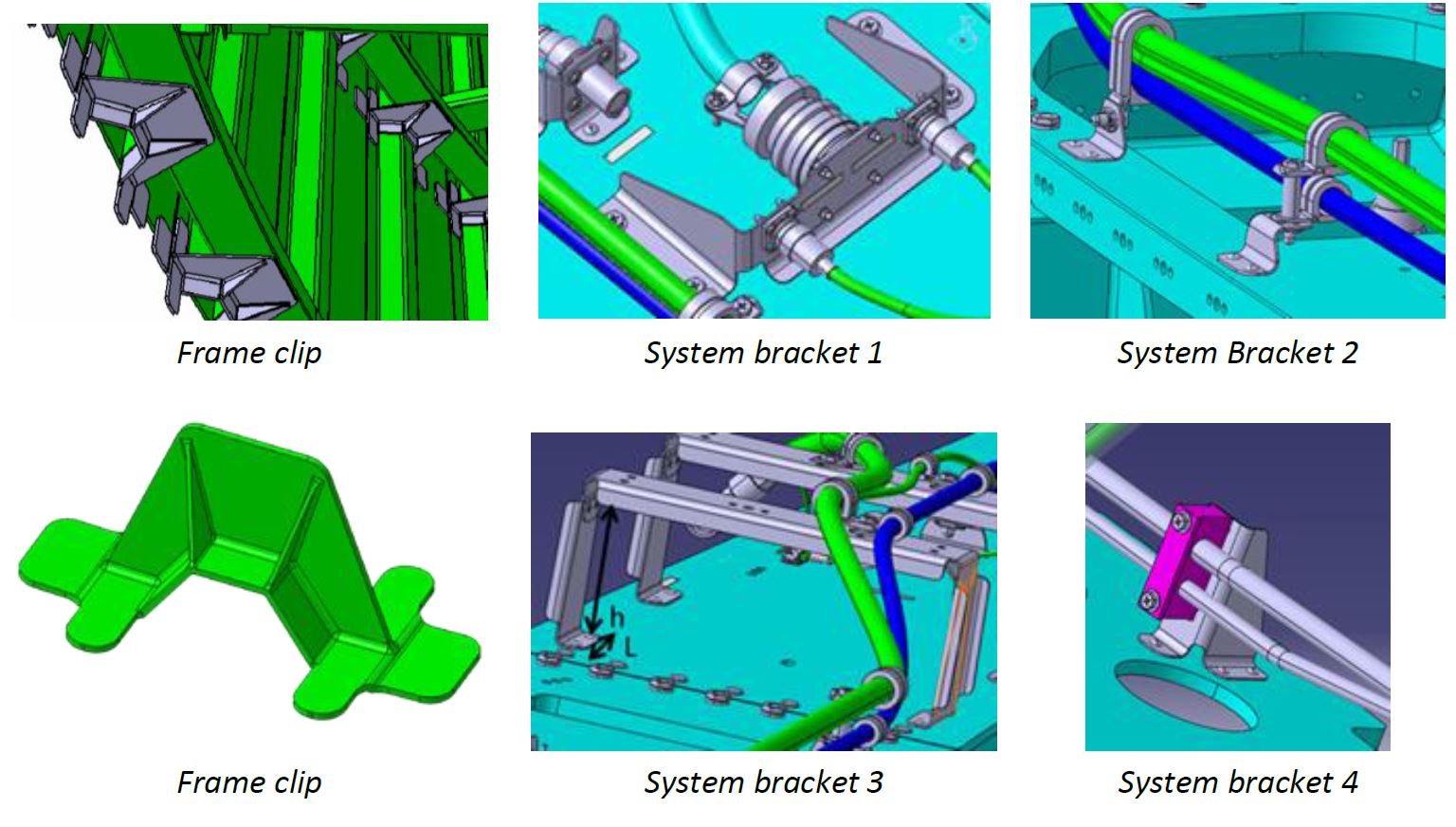
Exemplos de peças a serem entregues no Clean Sky 2 tópico JTI-CS2-2019-CfP10-LPA-02-31, Figura 2. FONTE | Clean Sky 2 CFP10, pág. 146
Também no CFP10 está o tópico MFFD fuselagem superior JTI-CS2-2019-CfP10-LPA-02-30, “Desenvolvimento de sistemas de soldagem inovadores para juntas estruturais de compósitos à base de matriz termoplástica” liderado por Aernnova Composites Illescas (Illescas, Espanha). Previsto para começar após o 1T 2020, seu escopo é desenvolver um sistema de soldagem para obter uma ligação estrutural entre as peças de reforço (reforços, cunhas, acessórios) e quadros estruturais para obter uma Estrutura Envolvente de Porta (DSS) altamente integrada. Espero dar mais detalhes sobre a fuselagem superior do MFFD em um futuro blog. Por enquanto, é suficiente entender por que o pacote de trabalho MECATESTERS 3 é importante e quanto será alcançado uma vez que MECATESTERS, STUNNING e o MFFD sejam concluídos.
Juntando as duas metades
Depois de concluído, a metade inferior do MFFD irá para o Instituto Fraunhofer de Tecnologia de Fabricação e Materiais Avançados IFAM (Stade, Alemanha) para ser unida à metade superior, explica Veldman. “Estamos comprometidos em entregar nossa metade da fuselagem até o final de 2021”, acrescenta.
Conforme observado acima, Ralf Herrmann da Airbus é o líder do projeto MMFD; assim, a Airbus integra o trabalho do Fraunhofer IFAM e do consórcio CFP07 MultiFAL (Sistema de automação multifuncional para linha de montagem de fuselagem) - que se encarrega de unir as duas metades da fuselagem, trabalhando em conjunto com as equipes do STUNNING e da fuselagem superior —Para desenvolver soluções para os inúmeros desafios.
Alguns deles são revelados em dois tópicos no 11 th Chamada de propostas (novembro de 2019), ambas lideradas pela Airbus para começar após o quarto trimestre de 2020 e intituladas "Ferramentas, equipamentos e auxiliares para o fechamento de uma junta de barril longitudinal:"
- JTI-CS2-2020-CfP11-LPA-02-33, “:Integração da alça e continuidade da proteção contra descargas atmosféricas”
- JTI-CS2-2020-CfP11-LPA-02-34, “:Junta de sobreposição e integração de acoplamento de estrutura”
Escrito por Piet-Christof Woelcken, gerente de tópico da Airbus Bremen e líder do pacote de trabalho MFFD, os principais desafios nesses tópicos incluem:
JTI-CS2-2020-CfP11-LPA-02-33
- Junta da tira inferior (Fig. 3 abaixo):
- O lado esquerdo do demonstrador (na direção do vôo) inclui a porta do passageiro surround. A variação da espessura da pele nesta área necessita de uma integração escalonada da alça da bunda, unindo as películas superior e inferior.
- Dada a complexidade da junta, soldagem por condução usar uma placa de pressão aquecida é a tecnologia de união preferida.
- Continuidade elétrica da proteção contra raios (Fig. 4 abaixo):
- A continuidade elétrica da proteção metálica contra raios (LSP) deve ser alcançada em ambas as juntas longitudinais na parte externa da fuselagem.
- Espera-se que o cabeçote de ferramenta fornecido para a integração da alça de topo possa ser usado para este propósito.
JTI-CS2-2020-CfP11-LPA-02-34
- Junta de sobreposição (Fig. 2 abaixo):
- A junta de sobreposição de 8 metros de comprimento no lado direito dos demonstradores (na direção do vôo) conecta as películas superior e inferior da fuselagem. No sentido longitudinal, a espessura da pele abaixo de 3 mm é constante na zona de soldagem. Na direção circunferencial, as capas apresentam uma geometria escalonada para melhorar o desempenho estrutural.
- Soldagem ultrassônica é a união preferida para atingir uma alta taxa de produção.
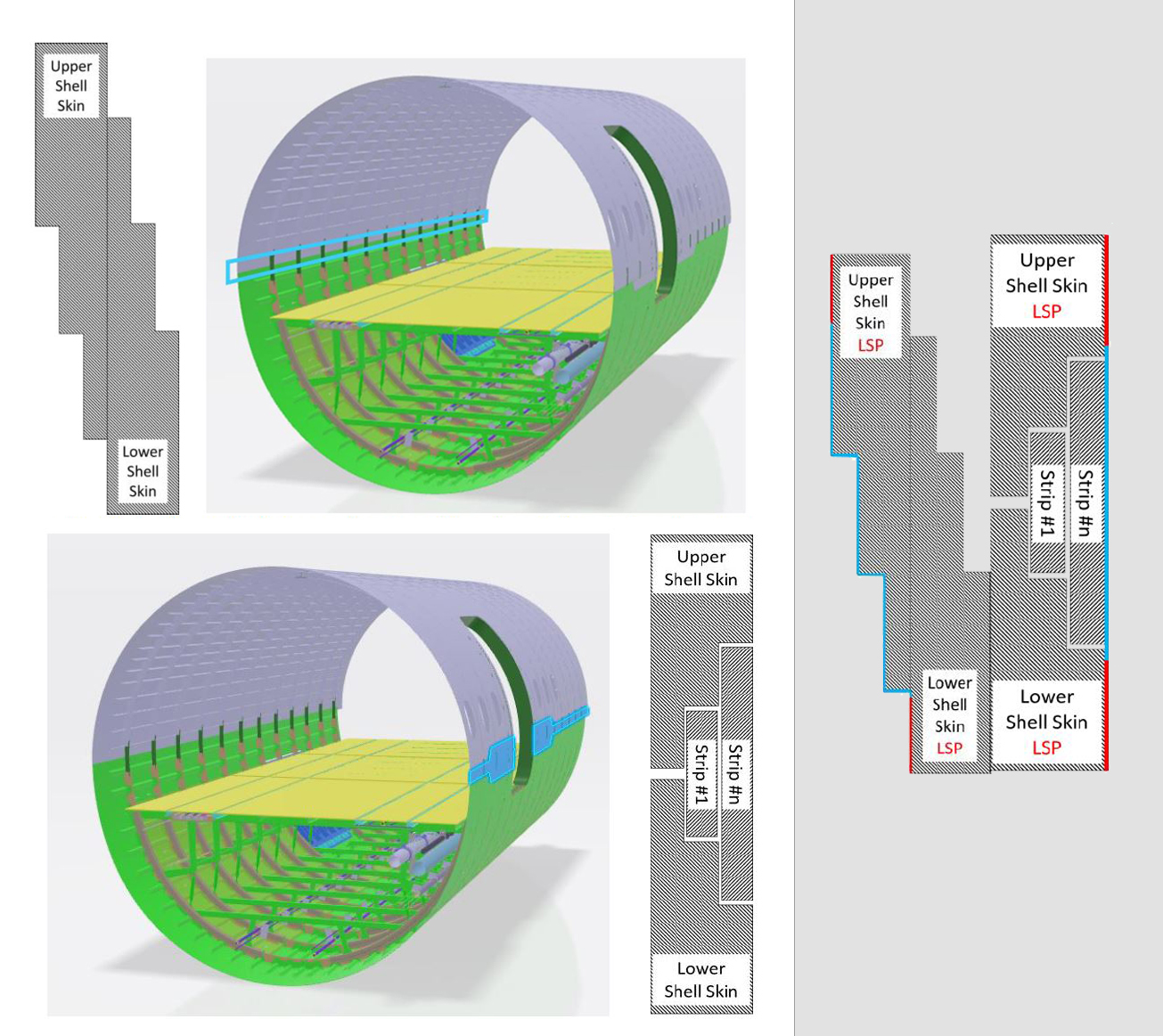
Fig. 2 (canto superior esquerdo) :Junta de sobreposição:Uma abordagem escalonada foi adotada no projeto de junta de sobreposição. Observe que a concha inferior fica no lado interno da fuselagem. Fig. 3 (Inferior esquerdo) : Integração da tira de topo:uma série de tiras sobrepostas requerem integração através da junta escalonada. Observe que a alça de bunda fica do lado de fora da fuselagem. Fig. 4 (direita) :A continuidade elétrica do LSP metálico deve ser alcançada através das juntas longitudinais do lado de fora da fuselagem CFRP. Vermelho indica LSP pré-equipado, azul indica LSP a ser aplicado como parte deste tópico. FONTE | Clean Sky 2 11 th Convite à apresentação de propostas JTI-CS2-2020-CfP11-LPA-02-33 e -34, “Integração da alça de topo e continuidade da proteção contra descargas atmosféricas”, pp. 78 e 86.
JTI-CS2-2020-CfP11-LPA-02-34
- Integração de acoplamento de estrutura (Fig. 5):
- Junta de sobreposição:os acoplamentos de estrutura abaixo da junta de sobreposição precisam unir estruturalmente as estruturas de casca superior e inferior.
- Alça de bunda:os acoplamentos da estrutura abaixo da tira de bunda precisam unir estruturalmente as armações de casca superior e inferior, bem como se conectar à pele.
- Soldagem por resistência é a tecnologia preferida para este desafio técnico.
Integração de acoplamento de quadro. Observe que os acoplamentos da estrutura diferem de acordo com o lado, como parte da demonstração da tecnologia. FONTE | Clean Sky 2 11 th Chamada de Propostas JTI-CS2-2020-CfP11-LPA-02-34, “Ferramentas, Equipamentos e Auxiliares para o Fechamento de uma Junta de Barril Longitudinal:Junta de Sobreposição e Integração de Acoplamento de Estrutura”, Fig. 5, p. 86
Métodos de soldagem, cabeçotes de ferramenta e tolerâncias
Herrmann explica que a soldagem por condução será demonstrada no lado esquerdo através da junta da tira de topo e a soldagem ultrassônica no lado direito através da junta de sobreposição, enquanto a soldagem por resistência será usada para os acoplamentos da estrutura. “O MFFD demonstrará muitas abordagens técnicas, por isso não é o mesmo que fabricar uma fuselagem real, mas, em vez disso, é projetado como um veículo para demonstrar e amadurecer tecnologias”, acrescenta.
Desenvolvimento de cabeçotes de ferramentas de soldagem
O objetivo desses dois tópicos escritos por Woelcken é desenvolver os cabeçotes de ferramentas necessários para essas juntas soldadas. “Quando você solda duas peças, deve aplicar calor e pressão”, explica ele. “Então, isso é aplicado pelo cabeçote da ferramenta durante a soldagem. Para o processo de soldagem por condução do tipo Fokker, você aplica calor e pressão ativamente de um lado e a pressão passiva de um suporte é exercida do outro. A junta de topo é uma pilha de seis fitas e, na união, colocaremos a pilha e aqueceremos durante a soldagem. No entanto, como o material da fita LM PAEK UD é relativamente novo na soldagem, devemos entender as condições do processo e como podemos compensar as tolerâncias. Portanto, devemos definir os materiais e a espessura, bem como a geometria do cabeçote da ferramenta. ”
“Observe que usar este tipo de junta de topo é um processo padrão para o que estamos fazendo em outras juntas em nossa aeronave”, ressalta Woelcken. “Para o MFFD, queremos deixar a fuselagem superior e inferior inalteradas em relação a esta prática padrão, a fim de minimizar a quantidade de material que temos que personalizar.”
Flexibilidade nas tolerâncias
Woelcken observa que, como as superfícies de soldagem superiores são essencialmente derretidas em líquido e, em seguida, pressionadas juntas, "isso dá muita flexibilidade para acomodar as tolerâncias". Observe, atualmente, com termofixo asas e fuselagens de polímero reforçado com fibra de carbono (CFRP), esses problemas de tolerância são resolvidos aplicando um adesivo de calço líquido. Embora poucas pessoas queiram discutir isso publicamente, a questão geral de calços em aeroestruturas compostas foi amplamente reconhecida e iniciativas para reduzi-la e / ou eliminá-la foram divulgadas, como o método de montagem Flexmont para aviões de cauda vertical.
“ Esperamos obter vantagens ao abordar as tolerâncias com o uso de compostos termoplásticos ”, diz Woelcken,“ principalmente ao explorar nossos conceitos de projeto e basear-se em nossa experiência com CFRP termofixo e soldagem metálica. A chave será o monitoramento in situ durante o aquecimento e a aplicação de pressão. ” Ele enfatiza que o calor é o parâmetro número um. “Estou surpreso com a tolerância dos processos de soldagem de compósito termoplástico à pressão. O principal desafio é a contenção dessa pressão e como ela cai. Atualmente, estamos monitorando a parte traseira da junta soldada. ”
Sistema de montagem automatizada Fraunhofer IFAM (canto superior esquerdo) com dimensões no início do tópico de trabalho CFP07 (canto superior direito) está sendo modificado para acomodar uma fuselagem de 360 ° para soldar as juntas longitudinais e circunferenciais do MFFD. FONTE | Fraunhofer IFAM e cfk-valley.com, Clean Sky 2 7 th Convite à apresentação de propostas, JTI-CS2-2017-CfP07-LPA-02-22, p. 76
Automação de montagem
No sétimo th Convite à apresentação de propostas, o tópico JTI-CS2-2017-CfP07-LPA-02-22, “Desenvolvimento de um sistema automatizado de tamanho real para juntas longitudinais e circunferenciais da fuselagem” é liderado pelo Fraunhofer IFAM dentro do consórcio MultiFAL. O trecho abaixo lança alguma luz sobre como os cabeçotes de ferramentas de soldagem discutidos acima, agora em desenvolvimento, podem ser implementados:
“Para realizar o processo de montagem de uma fuselagem termoplástica, as tolerâncias se tornam um tópico importante. O posicionamento e orientação das conchas da fuselagem, bem como as deformações resultantes causadas pelo processo de soldagem, precisam ficar dentro das tolerâncias. Precisões comparáveis podem ser orientadas para o processo de última geração de junta longitudinal. Here, the position error in each direction should be within 0.5 mm (in some exceptions up to 1 mm). … it can be assumed that a pre-load on the joint surface from both sides of approximately 1000N (independent of the welding technology) for a welding seam of 20 mm width is required by the automation system.”
Fraunhofer IFAM — which was also CTC Stade’s partner in developing the Flexmont VTP assembly process — describes its starting point:an in-house assembly plant system which can manipulate parts from 2 to 8 meters long and up to 6 meters high, including a 180° shell of a single-aisle aircraft. The system is enabled by a flexible arrangement of 10 cooperating hexapods (see “Reconfigurable Tooling:Revolutionizing composites manufacturing”), 24 linear units and modular rack elements. Vacuum grippers with 6-axis force and torque sensors adjust the pose and shape of the part, as required, to manage tolerances during assembly. The guidance and monitoring of these rapid, iterative adjustments is achieved through optical measuring devices.
According to the CFP07 text, Fraunhofer IFAM will modify this assembly plant system for holding a complete 360° fuselage, with work scheduled to begin in Q2 2018 and completed in 36 months.
The STUNNING consortium is working with SAM|XL to develop automation for assembling the MFFD lower fuselage. SOURCE | samxl.com
Within STUNNING, activities are planned with the collaborative research center SAM|XL (Smart Advanced Manufacturing XL, Delft, Netherlands) to demonstrate automated welding techniques for assembling the lower fuselage. Specializing in automation for manufacturing large, lightweight composite structures, SAM|XL brings together TU Delft’s Aerospace Engineering group and Robotics Institute. GKN-Fokker is a major participant. One of the methods being investigated is sequential spot ultrasonic welding, which was proven in the Clean Sky 1 Eco Design project and TAPAS 2 as a fast and effective for connecting short fiber-reinforced brackets or clips to fuselage structures.
In her 2016 paper, titled “Smart ultrasonic welding of thermoplastic composites,” Villegas states that it is possible to scale up the ultrasonic welding process via sequential welding — that is, letting a continuous line of adjacent spot welds serve the same purpose as a continuous weld bead. Lab-scale sequential spot welding was used in the Clean Sky EcoDesign demonstrator’s TPC airframe panel, using flat energy directors to weld a CF/PEEK hinge and CF/PEKK clips to CF/PEEK C-frames (Fig. 6). Experimental comparisons with mechanically fastened joints in double-lap shear and pull-through tests showed promise. The process is further explored in 2018 papers {and 2019 papers} by Villegas’ TU Delft team member Tian Zhao {and in Villegas’ 2019 paper}.
— “Welding thermoplastic composites”, G. Gardiner, 2018.
The STUNNING consortium’s work with TU Delft and SAM|XL is adapting this technology to weld multiple system and semi-structural brackets, stiffening elements and stringers to the MFFD lower fuselage shell.
Work breakdown and timeline for MFFD assembly. SOURCE | Clean Sky 2 11
th
Call for Proposals JTI-CS2-2020-CfP11-LPA-02-33, “Tooling, Equipment and Auxiliaries for the closure of a longitudinal Barrel Joint:Butt strap integration and Lightning Strike Protection continuity”, pp. 79 and 82.
Digital twin phase, 2020 and beyond
According to the Clean Sky website, the MFFD program reached an important milestone in Nov 2019 with the successful passing of its Critical Design Review (CDR). In the timeline above, the MFFD design enters a “Digital Twin Phase” in 2020-2021. What does this mean? “Though we have wrapped up the majority of the design phase, we are taking it a bit further by working with a specific lifecycle management approach,” explains Herrmann. “We are modeling imperfections and nonconformities from the NDT results and process parameters during component manufacturing. We want to combine this Industry 4.0 data with lifecycle management so that we continue to tailor the design according to what we are actually manufacturing. We want to see how far we can push this and what we can accomplish by the end of Clean Sky 2.”
For 2020, the chief agenda is manufacturing. “We hope to present various parts as they come together this year,” says Veldman. What will the largest challenge be for the STUNNING program? “Assembly,” he answers. “Not so much within STUNNING, but our lower fuselage has interfaces with the door surround structure, multiple Airbus-delivered components and the whole upper fuselage. Getting everything delivered at the right time and then bringing it all together will require a number of developments yet.”
That brings us to perhaps the biggest question:Will thermoplastic composites be used on the next aircraft entering production in 2030-35? “For sure, we want to try to use the technologies we are working on,” says Herrmann, “but I cannot say if or when thermoplastic composites will be on future aircraft. The most important part for us is that they are an enabler for dustless joining regarding ramping production to more than 70 aircraft per month. We have to show that it is feasible, not only with metallics but also with thermoplastic composites.”
“By the end of this project, we will have a more complete understanding of thermoplastic composite welding and will gain approval for its use in large primary aircraft structures,” says Salat. “If we can use this for future aircraft, we can achieve significant weight savings and improved sustainability.” But perhaps just as important is Clean Sky’s ability to bring Europe’s aviation research and innovation stakeholders closer together. “We have quarterly meetings where I sit with all of the LPA steering committee,” says Veldman. “I’m talking to the whole of the European aerospace industry, and it most certainly helps to open up opportunities for the future, not only for companies who can supply to us, but for a wide range of collaborations.”
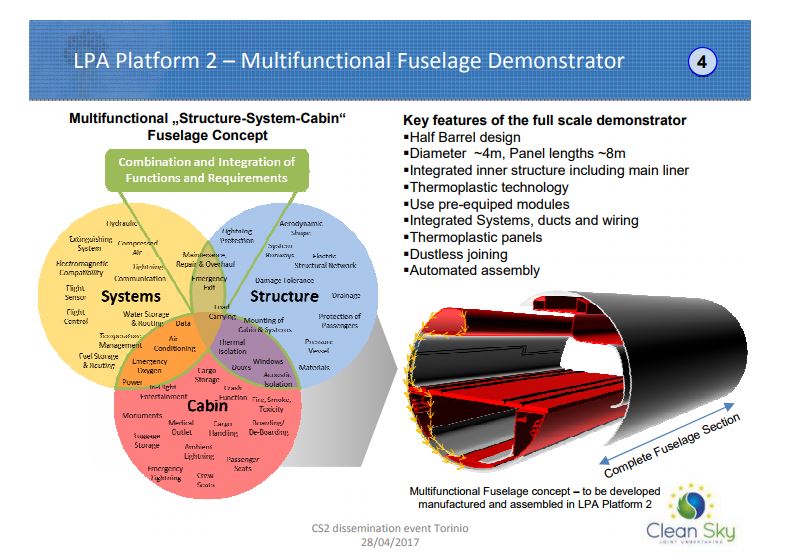
Resina
- 10 Startups de impressão 3D a serem observados em 2020
- Destaque do aplicativo:Impressão 3D para cabines de aeronaves
- Comprimindo o valor dos dados para AI
- 6 Dicas de soldagem para manutenção da planta
- Procurando um plástico ultra-resistente? Confira FR-4!
- Materiais:Compostos e concentrados de grau médico para soldagem a laser
- Dicas e truques para soldagem Inconel
- Victrex e parceiro Bond para impressão 3D de peças PAEK
- A primeira seção composta da fuselagem para o primeiro jato comercial composto
- Dicas para soldar alumínio