Usando susceptores móveis para inovar a soldagem por indução termoplástica
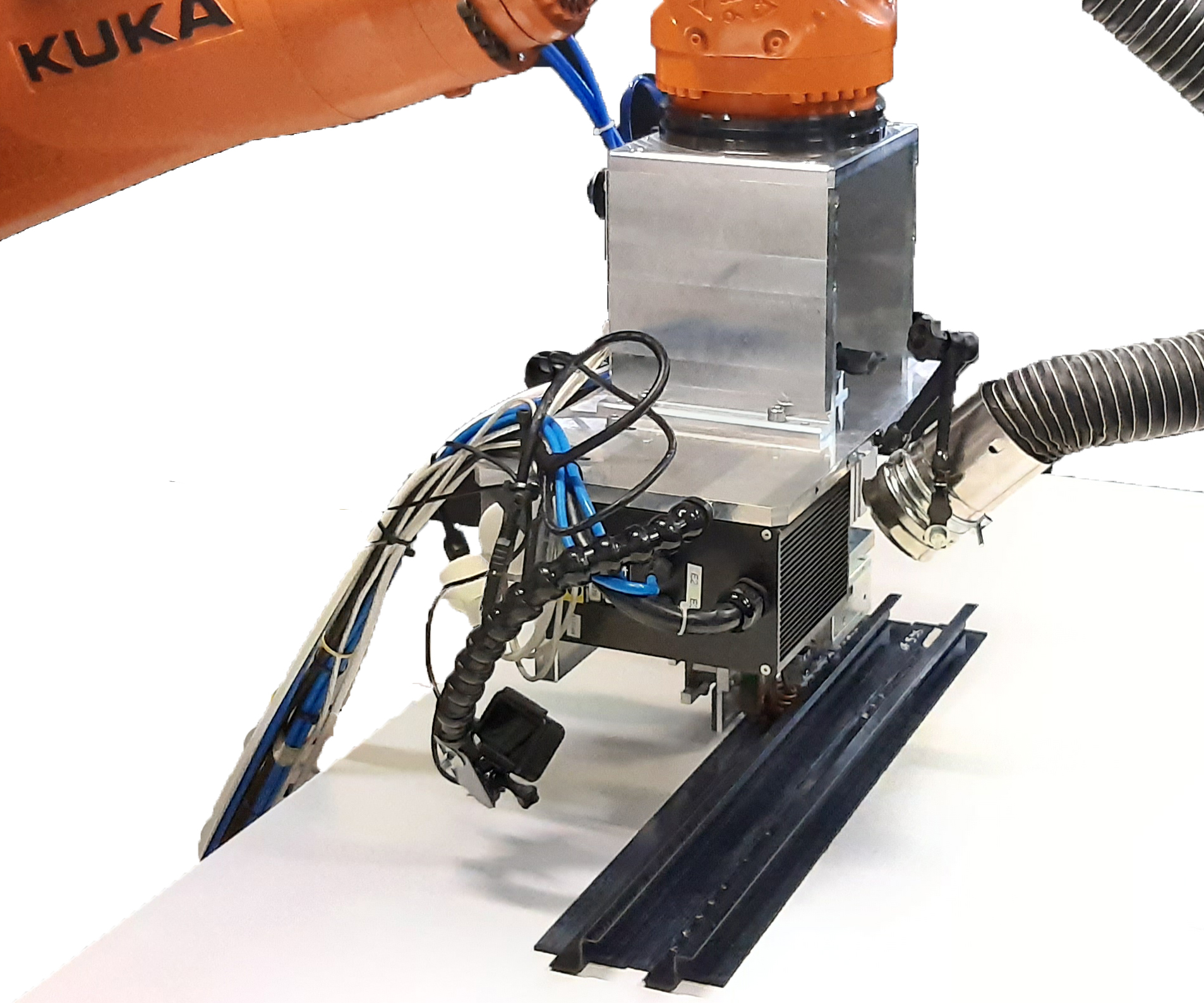
O Grupo Institut de Soudure (IS Groupe, Villepinte, França) - literalmente “o instituto de soldagem” da França - tem mais de 100 anos de experiência em soldagem de metais e agora está se estabelecendo como líder na soldagem de compósitos termoplásticos. Conforme relatado em CW 2018 apresenta "Compostos termoplásticos de soldagem", IS Groupe e sua marca de compostos Composite Integrity desenvolveu o processo de “soldagem por indução dinâmica” usado para unir longarinas de fita de fibra de carbono (CF) / polietercetonecetona (PEKK) unidirecional (UD) e películas de fuselagem no projeto de demonstração “Arches TP” com o fornecedor Airbus Tier 1 STELIA Aerospace (Toulouse, França) , que foi revelado no 2017 Paris Air Show.
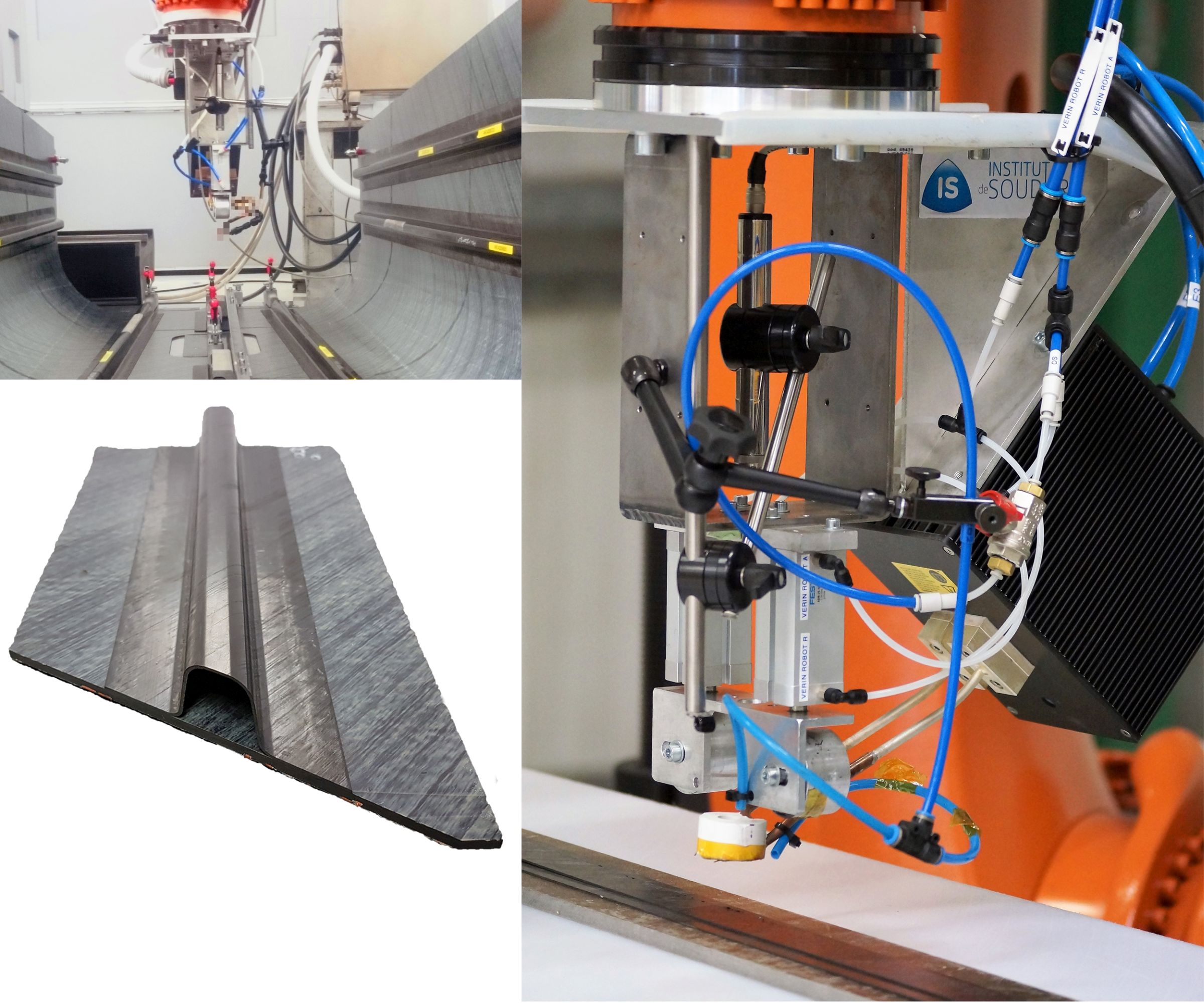
“Este foi o início do nosso desenvolvimento com soldagem por indução para peças estruturais aeronáuticas”, explica Jérôme Raynal, diretor de aeronáutica e compósitos do IS Groupe. “Embora o processo de soldagem por indução dinâmica que desenvolvemos tenha sido bem-sucedido, ele teve algumas limitações em relação ao desempenho no raio da longarina colada e ao aquecimento global do painel porque não há suscetor na interface.”
Um susceptor é um material colocado entre os dois aderentes de uma junta composta termoplástica soldada que é aquecida pela bobina de indução na cabeça de soldagem. O susceptor pode ser eletricamente condutor para aquecimento resistivo ou magnético para aquecimento por histerese, derretendo a matriz na interface de solda que é pressionada simultaneamente para criar uma junta ligada por fusão com resistência muito alta. Conforme explicado pelo artigo de janeiro de 2000, "Projeto de um Susceptor Resistivo para Aquecimento Uniforme Durante a Ligação por Indução de Compósitos" por Bruce Fink, Shridhar Yarlagadda e John W. (Jack) Gillespie, suscetores usados em compósitos termoplásticos soldados por indução eram inicialmente um metal tela ou malha, às vezes impregnada com polímero.
O IS Groupe acreditava que os problemas iniciais que encontrou poderiam ser resolvidos com mais desenvolvimento. “Começamos uma nova rodada de reflexão interna”, diz Raynal. Isso incluiu discussões com o fornecedor de materiais termoplásticos (TP) Arkema (Colombes, França), que deu início a uma parceria de desenvolvimento. “Agora desenvolvemos e co-patenteamos uma nova tecnologia com a Arkema, chamada Innovative Solution for Welding (ISW),” acrescenta Raynal.
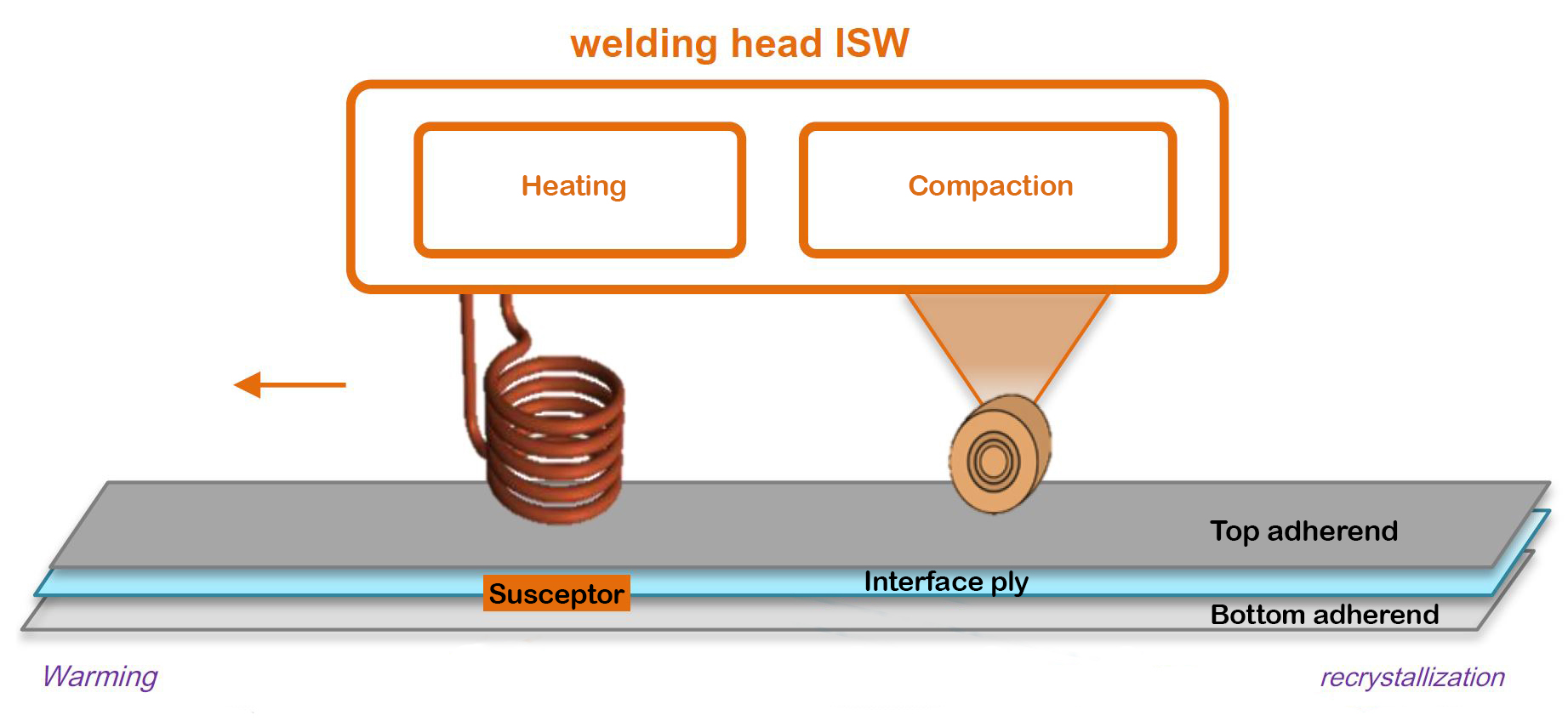
Noções básicas de ISW
“A base do ISW é usar um suscetor para aquecer a interface de soldagem, mas este é um suscetor móvel ligado ao cabeçote de soldagem”, explica Raynal. "O susceptor nos permite localizar perfeitamente a zona de aquecimento na solda, mas a cabeça de soldagem com o susceptor está se movendo de modo que nada permanece na interface para perturbar as propriedades da estrutura soldada." Nas primeiras iterações da soldagem por indução, os susceptores da malha de metal foram deixados na solda, mas isso foi visto como indesejável. As técnicas mais recentes foram capazes de eliminar os susceptores porque a fibra de carbono nos laminados aeroespaciais comuns é eletricamente condutora. Isso também permitiu o uso de materiais de fibra de carbono como susceptores.
Outra parte da solução ISW é usar uma matriz TP pura ou camada de baixo volume de fibra na interface de solda para aumentar o fluxo de resina. A temperatura de fusão e a viscosidade desta camada de interface podem ser ajustadas e também podem ser funcionalizadas para fornecer condutividade elétrica ou isolamento para evitar corrosão galvânica, por exemplo, entre fibra de carbono e alumínio ou aço.
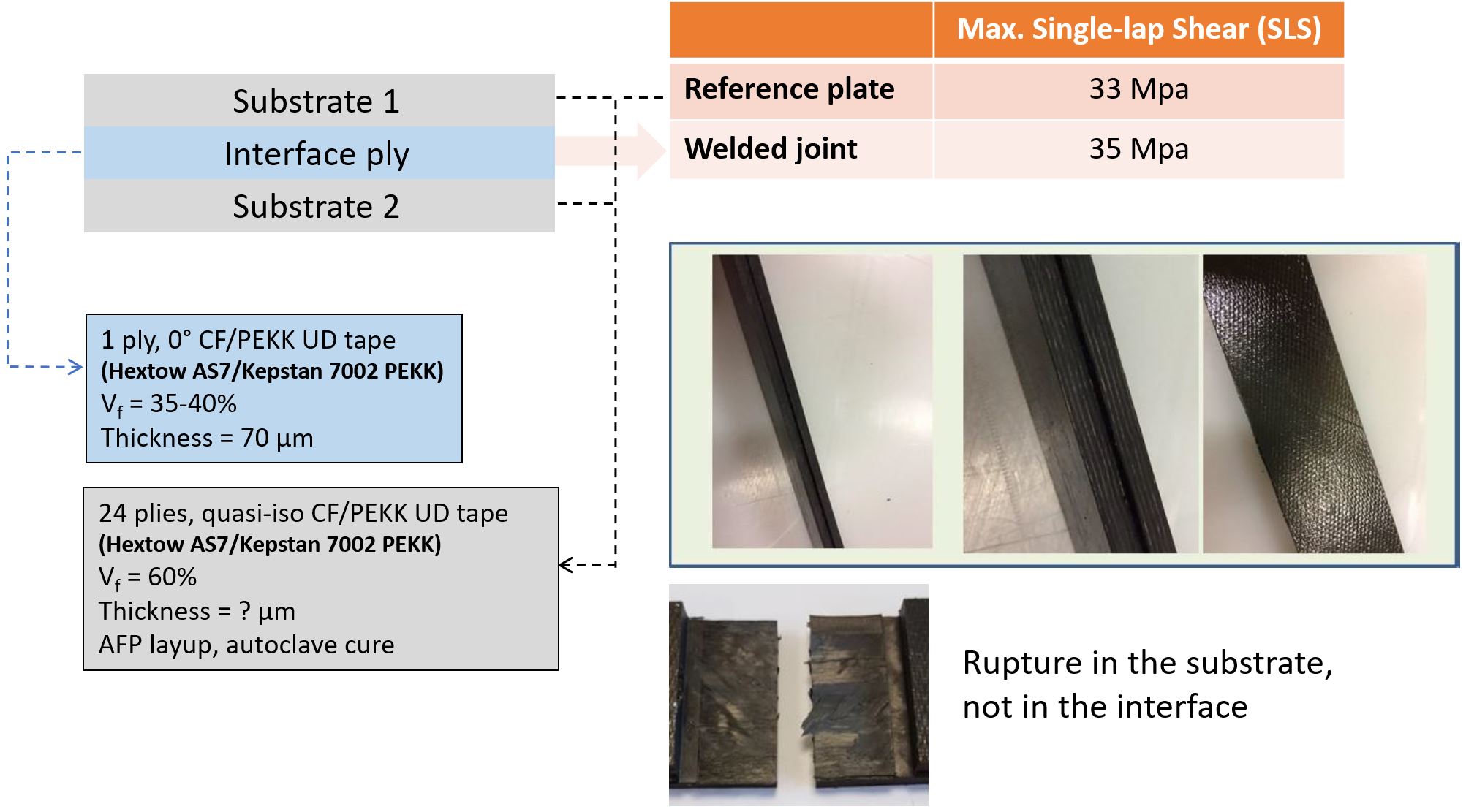
resultados de ISW
“Acabamos com um coeficiente de união de 80-90%”, diz Raynal. O coeficiente de junta corresponde à resistência da solda e é usado com metais, plásticos e compósitos. “Em testes de cisalhamento de volta única de duas placas pré-consolidadas soldadas usando ISW, alcançamos 80-90% das propriedades das placas de referência consolidadas em autoclave não soldadas.” Esses testes usaram fita UD feita com fibra de carbono Hextow AS7 (Hexcel, Stamford, Conn., EUA) e Arkema Kepstan 7002 PEKK.
Raynal diz que o ISW pode ser usado para soldar qualquer tipo de matriz:PE, PA, PEKK, PEEK, bem como compósitos termoplásticos reforçados com fibra de carbono, vidro ou aramida. “Também mostramos que não há problema em soldar componentes que possuem malha de cobre para proteção contra raios (LSP), que é fundamental para a produção de aeroestruturas”, acrescenta. O ISW foi projetado para ser totalmente automatizado com o cabeçote de soldagem conectado a um braço robótico de 6 eixos.
Controle de temperatura
Conforme explicado no artigo Kirk / Yarlagadda / Gillespie acima, um problema comum com suscetores de malha de metal sujeitos a um campo magnético é a distribuição não uniforme de temperatura resultante na peça a ser soldada. “Estamos controlando isso usando um susceptor para derreter apenas a interface de soldagem”, explica Raynal. “Nós sentimos a temperatura com um pirômetro a laser que realmente mede a borda do susceptor pela lateral. Portanto, sabemos exatamente a temperatura na interface. Também usamos resfriamento para ajudar a controlar a temperatura e garantir cristalização suficiente no material termoplástico durante a soldagem. ”
Ensaios de soldagem de longarina STELIA
O fornecedor Tier 1 da Airbus, STELIA (Toulouse, França), é um dos primeiros clientes para este desenvolvimento de soldagem por indução. IS Groupe e Arkema realizaram um estudo específico para STELIA para soldar uma longarina de 7 camadas CF / PEKK em uma pele de 14 camadas com malha de cobre para proteção contra raios (LSP). O objetivo final é soldar estruturas de 30 metros de comprimento, com seções retas e curvas duplas. Os componentes foram feitos usando fita UD de 194 gsm compreendendo fibra de carbono Tenax HST45 (Teijin, Osaka, Japão) e Kepstan 7002 PEKK. A STELIA especificou uma solda homogênea com desempenho mecânico> 85% do material de referência consolidado na autoclave e sem degradação térmica ou mecânica das propriedades dos aderentes. Ele também solicitou um processo robusto no que diz respeito à mudança na espessura aderente. Testes químicos e de propriedade nos componentes soldados foram realizados pelo IS Groupe.
IS Groupe e Arkema foram capazes de atender aos requisitos da STELIA, alcançando> 85% do desempenho de cisalhamento de volta única (SLS) e resistência ao cisalhamento interlaminar (ILSS) em comparação com os laminados de referência consolidados em autoclave. Não houve desempacotamento ou degradação nos laminados componentes ou na malha LSP. A única área em que eles ficaram aquém é a velocidade. STELIA solicitou uma velocidade de soldagem ≥ 1 metro / minuto. “Atualmente, estamos a 0,3 metros (10 polegadas) por minuto”, reconhece Raynal, “mas continuamos a trabalhar em direção a essa velocidade alvo.” Existe um limite na espessura do substrato que pode ser soldado? “Podemos soldar espessuras típicas de estruturas aeroespaciais e soldar componentes de 5 mm de espessura em um substrato de 5 mm.”
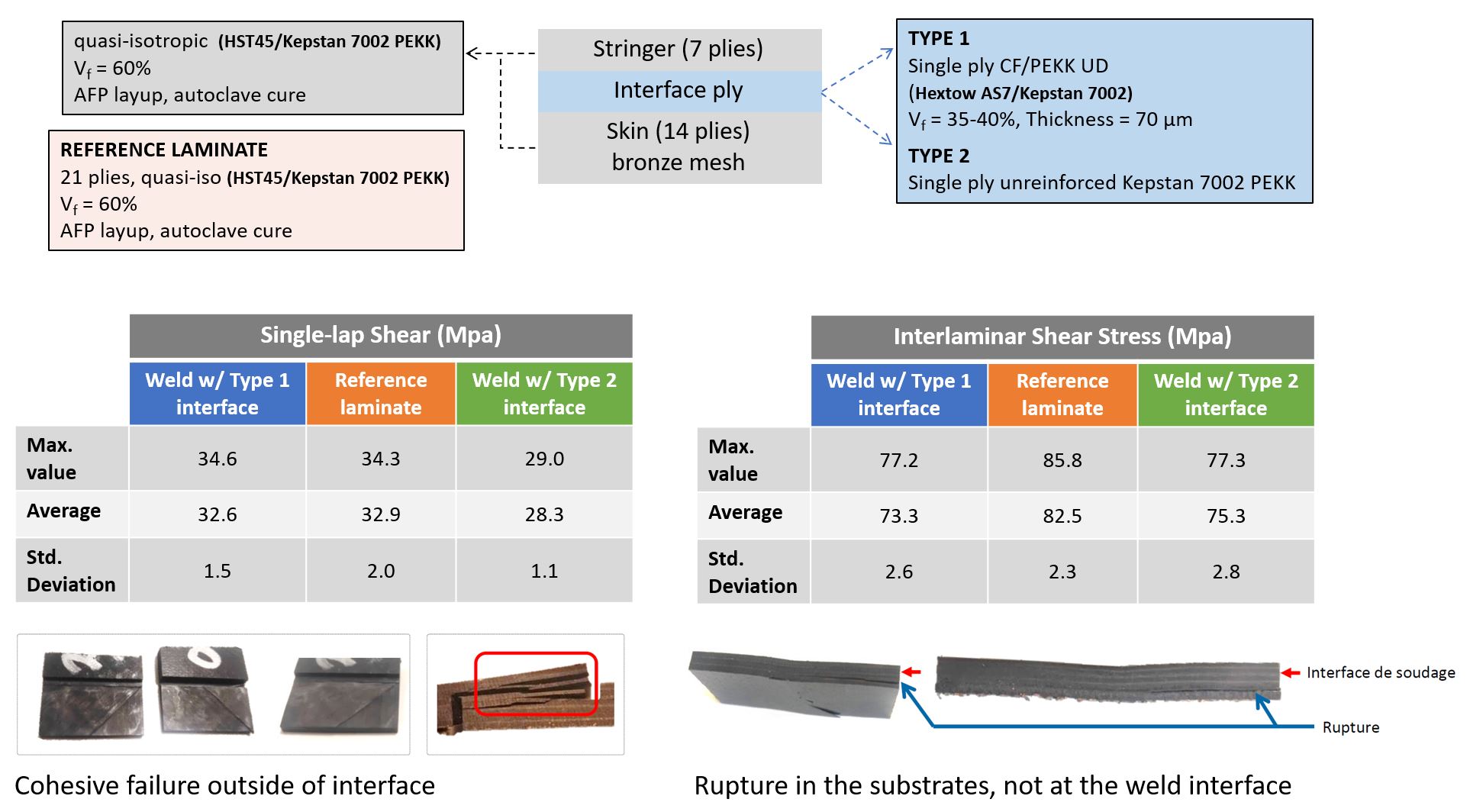
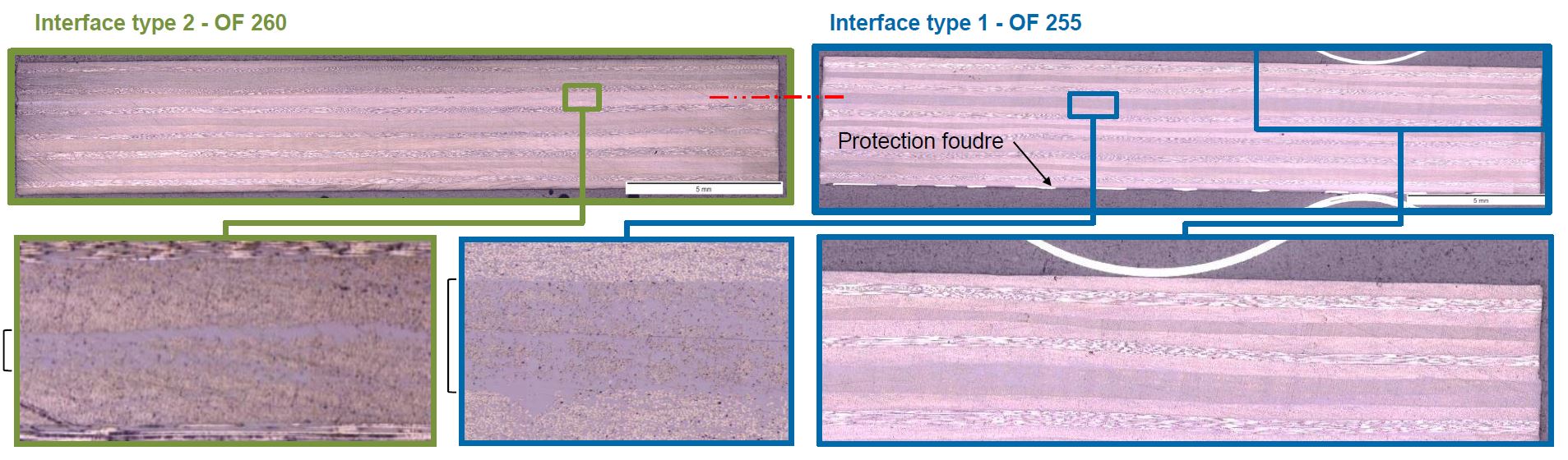
Parceria, oportunidades e desafios da Arkema
Por que trabalhar com a Arkema? “Porque existe uma relação entre a tecnologia e os materiais”, explica Raynal. “Por exemplo, os materiais na interface e sua fração de volume fazem a diferença. Somos especialistas em processo, mas precisávamos trabalhar em estreita colaboração com um parceiro para materiais. Este desenvolvimento conjunto foi necessário para otimizar completamente a tecnologia de soldagem. ”
O IS Groupe e a Arkema são co-proprietários da tecnologia ISW e protegeram essa tecnologia por um sólido portfólio de patentes que já inclui cinco pedidos de patentes franceses e internacionais. O ISW pode ser usado com qualquer matriz de composto termoplástico, e o IS Groupe está demonstrando a tecnologia por meio de programas que possui com empresas na Europa e nos EUA, incluindo Latécoère (Toulouse, França) e Collins Aerospace Aerostructures (Chula Vista, Califórnia, EUA).
Para a Arkema, o foco está no PEKK, diz Raynal, observando sua aliança estratégica de 2018 com a Hexcel para desenvolver fitas CF / termoplásticas para aeronaves futuras, com foco em fornecer custos mais baixos e velocidades de produção mais rápidas para seus clientes. Como parte dessa parceria, um laboratório conjunto de P&D está sendo estabelecido na França.
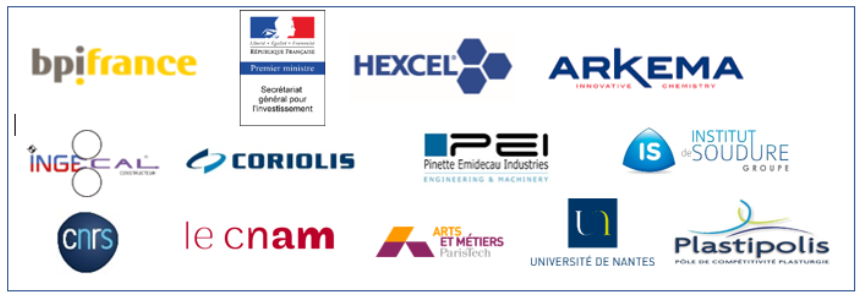
Os compósitos integrados altamente automatizados para estruturas adaptáveis de desempenho de 13,5 milhões de euros com prazo de 48 meses (HAICoPAS) é uma continuação da aliança estratégica Arkema-Hexcel. Esta colaboração totalmente francesa inclui o IS Groupe, bem como o designer de máquinas personalizadas Ingecal (Chassieu), Coriolis Composites (Quéven), Pinette Emidecau Industries (Chalon Sur Saone) e um consórcio de laboratórios universitários. HAICoPAS irá otimizar o projeto e fabricação de materiais para a produção de peças compostas para atingir custos competitivos em alta velocidade. Visa também desenvolver uma tecnologia mais produtiva para colocação / layup de materiais compósitos e um novo sistema de montagem de peças finais por soldagem com controle de qualidade online.
As aplicações direcionadas incluem estruturas primárias de aeronaves, peças estruturais para a indústria automotiva e oleodutos para a indústria de petróleo e gás. Os benefícios de reciclabilidade e sustentabilidade proporcionados por materiais termoplásticos também são importantes para esses mercados e serão demonstrados e quantificados no HAICoPAS.
“Um dos benefícios que podemos oferecer com o ISW é uma redução de mais de 50% na energia elétrica necessário versus nosso processo de soldagem por indução dinâmica de 2017 ”, destaca Raynal. “Com a indução convencional, você precisa de alta potência para aquecer a superfície. Mas com um susceptor na interface, a superfície que você aquece é muito menor, exigindo muito menos energia. ” Ele observa que isso também ajuda a evitar a descompactação no raio das longarinas. “Se você aquecer muito, pode amolecer o material no raio e permitir que as fibras aqui se movam. Portanto, precisamos aquecer perfeitamente apenas a zona de contato para os substratos soldados sem aquecer o raio. Com o ISW, isso não é um problema. ”
Ainda existem problemas térmicos, no entanto. “Com formas planas, o controle térmico é direto, mas se torna mais desafiador com o aumento da complexidade da forma”, diz Raynal. “Para 2020, o principal objetivo é continuar o desenvolvimento e conseguir a soldagem de longarinas na pele em escala representativa. Nosso foco também é introduzir a tecnologia em novos programas de desenvolvimento de aeronaves ”.
Para obter mais detalhes, consulte Integridade composta no JEC World 2020, Hall 5, Estande N89.
Resina
- Os 5 principais benefícios da soldagem por indução
- C# usando
- Uma introdução à soldagem ultrassônica de plásticos
- Covestro Aumenta o Investimento em Compósitos Termoplásticos
- Lances mestre termoplásticos reforçados com grafeno lançados
- Solvay Expande a Capacidade do Composto Termoplástico
- Compostos termoplásticos na Oribi Composites:CW Trending, episódio 4
- Compósitos termoplásticos de soldagem
- O que os municípios estão perdendo se não estiverem usando inspeções móveis
- Evitando problemas e defeitos de soldagem usando metais verificados