Fabricação de compósitos termoplásticos de alta velocidade e alta taxa
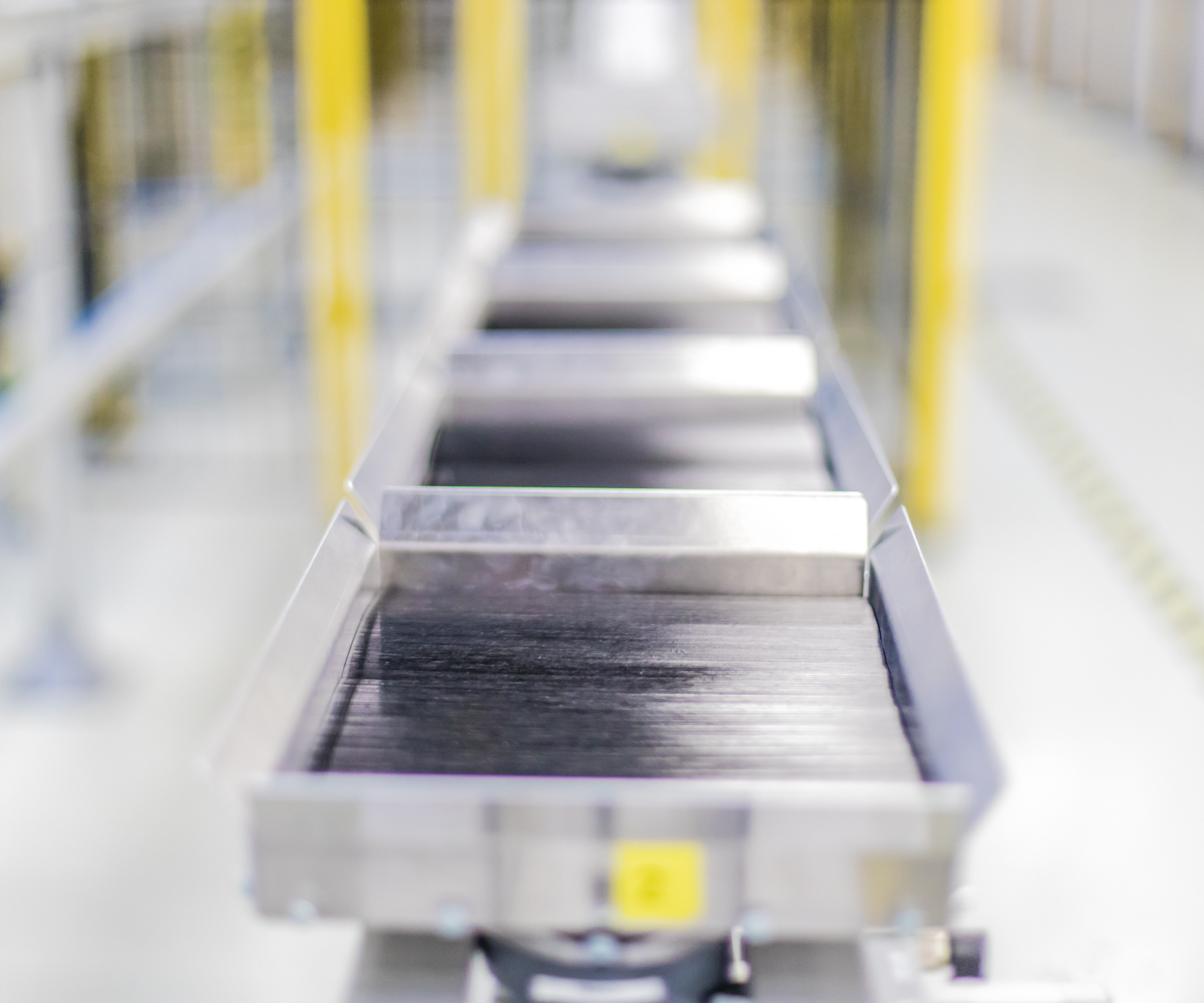
Para acelerar o layup e ainda oferecer boa flexibilidade de design, a SABIC e a Airborne pegaram uma ideia do sistema postal ao desenvolver o processo de layup de camadas para fitas compostas termoplásticas. Múltiplas bandejas baratas que se movem em um sistema de transporte (mostrado aqui) param brevemente sob as unidades de alimentação. Cada alimentador corta e solta uma folha de fita com as dimensões e orientação corretas na bandeja, que avança para a próxima unidade de alimentação. As bandejas continuam a circular de volta através das unidades de alimentação até que o número e a orientação adequados das camadas sejam alcançados em cada pilha para atender aos requisitos de design de um determinado laminado. Fonte | SABIC
Um novo sistema de alta velocidade para a produção de laminados consolidados a partir de fitas compostas termoplásticas, a Linha de Fabricação de Compósitos Digitais (DCML) promete ser capaz de produzir até quatro laminados (com até 15 camadas cada) por minuto e 1,5 milhão de laminados por ano a partir de uma única linha de produção - incluindo inspeção completa, que é 100% digital, incluindo medições e rastreamento de dados - do material que entra e dos laminados que saem. Essa taxa de produção é, aparentemente, significativamente mais rápido do que qualquer outro sistema de manuseio de fita comercial disponível - para termoplásticos ou termofixos - e este sistema foi projetado especificamente para atender a alta produção e custos de conversão efetivos exigidos pela indústria de eletrônicos de consumo (consulte “Produtos eletrônicos de consumo:tampas compostas híbridas”). Felizmente, as peças para este mercado não são enormes - não na escala aeroespacial ou automotiva - mas os OEMs precisam de muitas delas, na ordem de dezenas de milhões por ano.
“Um processo de conversão de fita termoplástica de alta velocidade era realmente necessário porque a tecnologia atual é relativamente trabalhosa, cara e lenta”, explica Gino Francato, líder global de compostos da SABIC. “Isso torna difícil justificar economicamente e aproveitar os muitos benefícios desses materiais - para produzir peças finas e leves com alta estética, resistência ao impacto e desempenho mecânico, além de reciclabilidade - em indústrias com volumes de produção altos a muito altos. Sem a capacidade de aumentar amplamente as velocidades de produção e usar o manuseio e a inspeção totalmente automatizados, as fitas termoplásticas permanecerão como produtos de nicho caros, principalmente limitados ao uso no setor aeroespacial e automotivo. ”
O DCML é fruto da imaginação da SABIC (Bergen op Zoom, Holanda) e da Airborne (Haia, Holanda), com tecnologia da Siemens AG (Munique, Alemanha) e KUKA AG (Augsburg, Alemanha). A SABIC contribuiu com tecnologia de materiais e ferramentas de modelagem de compostos para acelerar o desenvolvimento de materiais personalizados e prototipagem virtual de peças. A Airborne construiu a linha e também contribuiu com expertise em automação, digitalização e industrialização do processo de produção de compósitos. A Siemens contribuiu com o gerenciamento integrado do ciclo de vida do produto (PLM) e o software de controlador lógico programável (PLC) para aprimorar a automação e facilitar o aprendizado de máquina. A KUKA contribuiu com robôs industriais e soluções de automação de fábrica. Embora o novo processo de alta velocidade tenha sido descrito em termos gerais em vários eventos de imprensa desde 2018, há muitos detalhes que ainda não foram divulgados. Aqui está o que sabemos no momento.
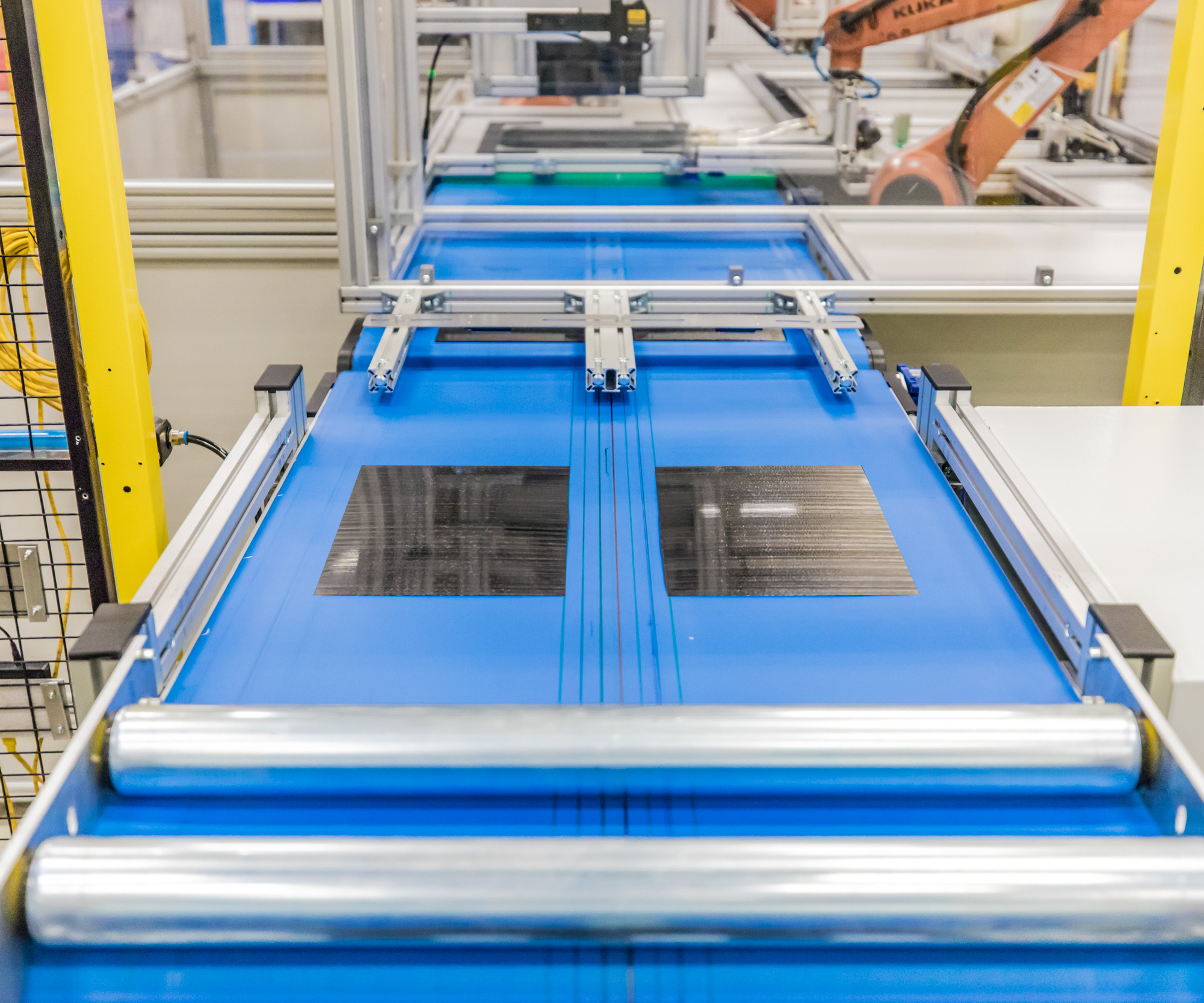
Assim que a bandeja deixa o loop do transportador, ela segue para a estação de soldagem, onde cada pilha é soldada por pontos em dois locais para facilitar o manuseio robótico na estação de consolidação. Após a consolidação, o laminado se move para aparar e inspecionar (mostrado aqui). Fonte | SABIC
A linha é projetada para produzir laminados planos personalizáveis de formato quase líquido a partir de fitas termoplásticas unidirecionais (UD) e fornece layup, consolidação, recorte, inspeção digital e visual, liberação automatizada e embalagem para envio aos clientes. Podem ser produzidos até quatro laminados por minuto, e cada laminado pode ter um cronograma de layup diferente, orientação e número de camadas e, teoricamente, até usar materiais diferentes (com diferentes reforços e matrizes de resina, embora isso exija a adição de unidades de alimentação extras).
Atingir diferentes layups simultaneamente é apenas uma questão de quantas vezes uma determinada bandeja (com um design laminado específico) passa sob cada alimentador para atingir o número correto de camadas e orientações para completar sua programação de layup. Dada a rapidez com que os modelos mudam em produtos eletrônicos de consumo, a flexibilidade é central para o sistema, que pode ser estendida adicionando alimentadores adicionais na extremidade dianteira ou funcionalidade (por exemplo, perfuração, pré-formação, etc.) na extremidade traseira. Inicialmente, a linha foi configurada para executar fitas de policarbonato reforçado com fibra de carbono unidirecional da SABIC, mas supostamente o sistema é flexível o suficiente para executar fitas termoplásticas que variam de polietileno (PE) e polipropileno (PP) a poliéteretercetona (PEEK) reforçada com fibra de carbono unidirecional ou fibra de vidro - ou ambos - ou mesmo tramas de tecido.
O sistema é compatível com a indústria 4.0 e permite a digitalização ponta a ponta - do desenvolvimento de produtos compostos à produção física no chão de fábrica - com controle de qualidade total baseado no aprendizado de máquina para alcançar melhorias de qualidade contínuas automaticamente ao longo do tempo. A linha pode ser monitorada e controlada remotamente, permitindo que os fabricantes alterem as configurações (como cronogramas de layup, número de camadas, etc.) em tempo real para modificar o design e as propriedades do material.
Funcionalmente, existem três seções principais na DCML:disposição das camadas, consolidação e corte / inspeção.
Exclusivamente, a seção de layup de camadas não usa máquinas de layup de fita automatizadas (ATL), que normalmente cortariam as fitas no comprimento e as colocaria na orientação e localização necessárias em uma mesa de indexação movendo-se sob o cabeçote de corte. Em vez disso, a equipe adotou uma abordagem inovadora e de alta velocidade, supostamente baseada na forma como a correspondência é classificada e distribuída, para construir pilhas de camadas. Múltiplas bandejas baratas que se movem em um sistema de transporte param brevemente sob as unidades de alimentação. Cada unidade de alimentação corta e solta uma folha de fita com as dimensões e orientação corretas (verificada por câmeras de alta resolução, que inspecionam as fitas em busca de defeitos e alterações e medem a largura e a espessura em vários locais) na bandeja, que então avança para a próxima unidade de alimentação. Para reduzir o desperdício e acelerar o layup, as fitas serão produzidas com a largura necessária para um projeto específico. As bandejas circulam de volta através dos alimentadores até que o número adequado de camadas seja depositado em cada pilha antes de prosseguir com a soldagem por pontos em dois locais para facilitar o manuseio na estação de consolidação. Essa abordagem permite que o layup ocorra rapidamente, mas com flexibilidade de design.
Na consolidação, um robô levanta quatro pilhas soldadas (duas pilhas por vez) de suas bandejas e as coloca entre um conjunto de placas de metal em um sistema de transporte separado. As placas aquecem e, portanto, aquecem e consolidam os laminados (via aquecimento de contato), e os laminados são então resfriados e descarregados roboticamente em um terceiro sistema de transporte. As placas de metal usadas na última operação de consolidação são recicladas de volta para a linha de retorno da placa e de volta para o sistema de consolidação. Quatro pilhas entram e saem desta seção a cada minuto.
A última parada para os laminados agora consolidados é a inspeção, corte e embalagem. Nesta estação, cada laminado é inspecionado em um lado e aparado, antes de se mover para um segundo robô que vira o laminado e o inspeciona do outro lado. Não há detalhes disponíveis sobre a tecnologia de corte usada.
O DCML tem suas limitações, como qualquer sistema de manufatura. Primeiramente, há algum sacrifício em termos de orientações de camada disponíveis, tamanho e forma da camada, tamanho final do laminado e a capacidade de criar orifícios / janelas. No entanto, o sistema mais do que compensa isso em termos de velocidade, produção, taxa de sucata e custos de conversão.
Alegadamente, a primeira linha comercial em grande escala da Airborne na Holanda começará a produção no próximo ano, com a empresa produzindo laminados termoplásticos personalizados para clientes de eletrônicos de consumo. Uma segunda linha do tamanho de um laboratório já está disponível no Centro de Desenvolvimento de Processamento de Polímero da SABIC (PPDC, Pittsfield, Mass., EUA) para clientes que desejam experimentar a tecnologia e avaliar a qualidade do laminado.
Além de eletrônicos de consumo, outros setores considerados alvos potenciais para a tecnologia incluem aeroespacial, automotivo, transporte de massa, artigos esportivos e saúde.
Resina
- Covestro Aumenta o Investimento em Compósitos Termoplásticos
- Compostos termoplásticos na Oribi Composites:CW Trending, episódio 4
- Resolução de problemas de termoformação de compósitos termoplásticos
- Compostos termoplásticos:Suporte de pára-choque estrutural
- Toray Advanced Composites expande as capacidades de compósitos termoplásticos
- A Teledyne CML Composites investe em capacidade de processamento termoplástico
- Cato Composites expande capacidade de produção de compósitos termoplásticos
- Antevisão do JEC World 2019:SABIC
- Compostos termoplásticos:Vista panorâmica
- Compósitos termoplásticos de soldagem