Compostos termoplásticos:Suporte de pára-choque estrutural
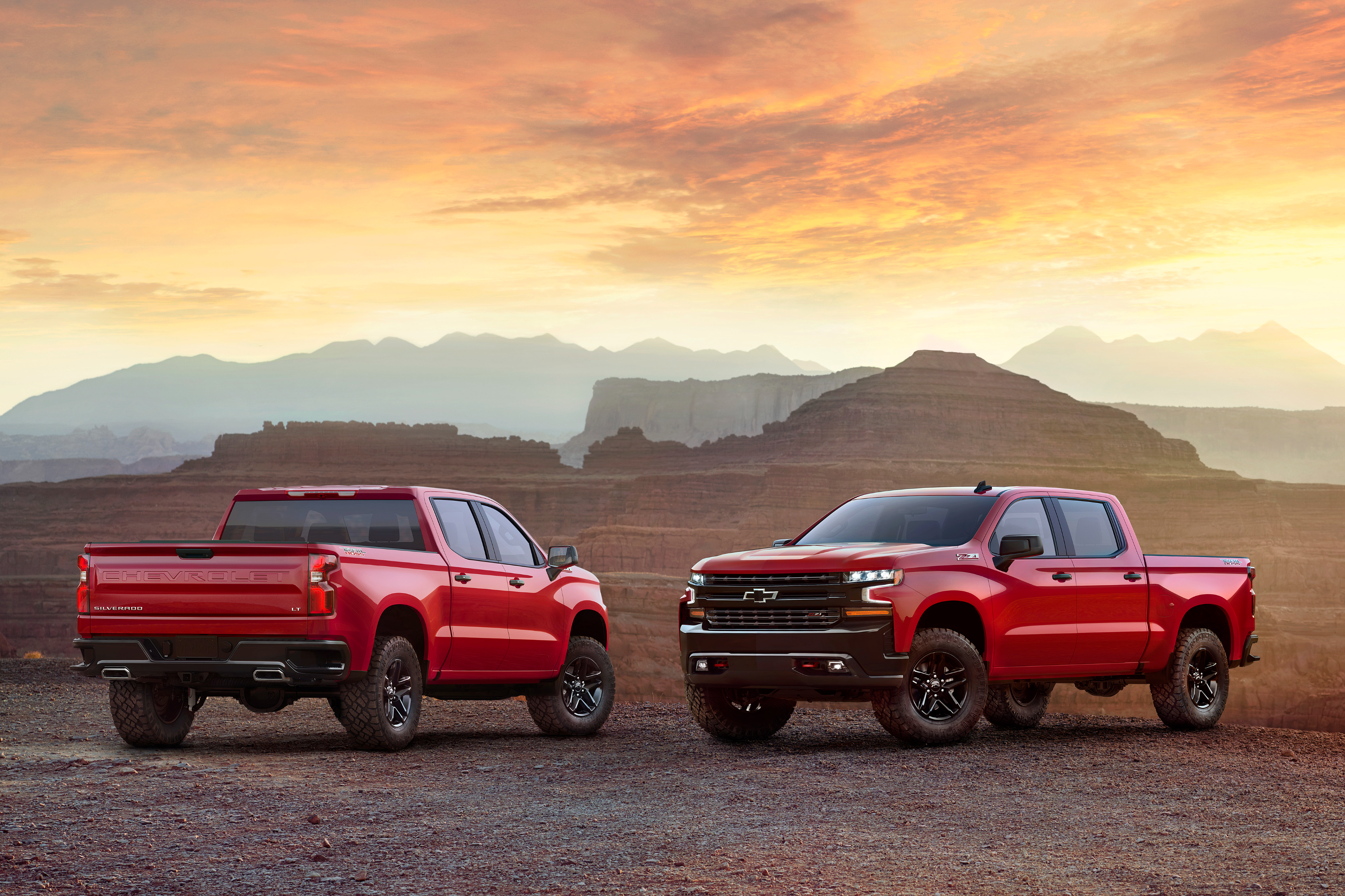
Ano modelo 2019 da GM (MY) Chevrolet Silverado As picapes apresentam uma nova aplicação estrutural para compósitos em um local oculto, mas muito eficaz:nos lados dianteiros esquerdo e direito, atrás do pára-choque de aço. O suporte de metal / composto termoplástico híbrido reduz a massa, atinge desempenho equivalente ou melhor em testes modal, de tensão, fadiga e de colisão em espaço limitado da embalagem, reduz os riscos de corrosão e de garantia e permite a consolidação significativa de peças. Todos os créditos das fotos:General Motors Co.
Não é fácil ser um engenheiro de design OEM trabalhando em programas de coleta em tamanho real. Por um lado, você deseja tornar esses veículos tão seguros, ricos em recursos e econômicos quanto possível. Por outro lado, seus clientes - particularmente aqueles nas indústrias de construção e agricultura - empurram seus veículos com força todos os dias e têm certas ideias sobre o que é ou não um material durável. Eles conhecem e confiam no aço. Compósitos? Talvez nem tanto.
Como Chris Heo, engenheiro chefe de lançamento de design para picapes de tamanho normal na General Motors Co. (GM, Detroit, Michigan, EUA), e sua equipe começaram a trabalhar na última geração do Chevrolet Silverado pickups, eles discutiram quais aplicações eles podem ser capazes de converter de metal em compósitos para reduzir a massa do veículo.
Para o modelo do ano de 2019 (MY), a decisão já tinha sido tomada para manter as barras de impacto do pára-choque estilizadas - para-choques de aço estampado com superfícies e acabamentos do lado A estilizado (seja cromado ou pintura da cor da carroceria) - na parte dianteira e traseira do veículo . Devido à forma orientada ao estilo e à massa dos invólucros de aço, tais pára-choques normalmente requerem um ou mais suportes de reforço de aço para unir o pára-choque à estrutura do veículo e atender à durabilidade do pára-choque da GM, danos ao veículo, desempenho em colisões e requisitos de embalagem. Nesse caso, um par de colchetes enrolado nos cantos esquerdo e direito do pára-choque. Os membros da equipe se perguntaram se poderiam converter essas peças estampadas pesadas, complexas e com várias peças em algo mais leve sem sacrificar o desempenho ou a durabilidade.
“Discutimos maneiras de manter a pele de metal do pára-choque, mas converter componentes ocultos em materiais leves”, lembra Heo. “Sabíamos que isso seria um desafio porque você precisa de suportes robustos para segurar uma parte pesada, como um pára-choque, e tanto os para-choques quanto os suportes devem funcionar por toda a vida do veículo. Além disso, esses suportes são essenciais para atender aos exigentes testes de colisão de barreira de compensação e - mesmo em metais - esses são testes desafiadores para passar. ”
Primeiro a tentar
Sem se intimidar com o desafio, a equipe da GM começou a trabalhar e logo trouxe o fornecedor de pára-choques designado do veículo, Flex-N-Gate Corp. (FNG, Urbana, Illinois, EUA). Inicialmente, como o estilo do veículo externo ainda estava sendo finalizado, a equipe conjunta passou um ano pesquisando opções na indústria e discutindo abordagens que poderiam funcionar. “Estávamos esperando o momento certo porque, dependendo do estilo final, isso poderia mudar o design que usamos e a abordagem que adotamos”, explica Heo.
“Sabíamos que outra empresa havia convertido um suporte muito pequeno - que não era estrutural - em compósito em um de seus pára-choques de caminhão, o que nos deu um ponto de partida”, acrescenta Steve Perucca, gerente do grupo de engenharia da FNG - plásticos de P&D / metais. A FNG já tinha muita experiência na conversão de peças de metal estruturais em compostos termoplásticos em veículos de passageiros, o que deu à equipe confiança para seguir em frente.
Considerações de design
Como o design exterior foi firmado na picape, a equipe combinada começou seu próprio trabalho de design nos suportes com uma lista de desejos e necessidades. Os suportes de referência foram estampados em aço de alta resistência / baixa liga (HSLA), selecionado por sua mecânica superior e resistência à corrosão aprimorada em comparação ao aço carbono. Os braquetes tinham espessura nominal de 3 milímetros e cada um pesava 4,362 kg. Primeiro, os suportes compostos precisavam caber aproximadamente no mesmo espaço da embalagem, que era limitado atrás do pára-choque. Assim, um material com resistência suficiente era necessário para que a espessura da peça não aumentasse significativamente.
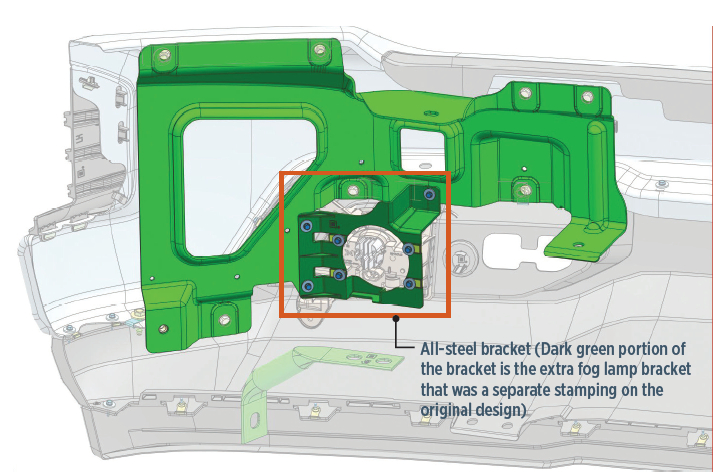
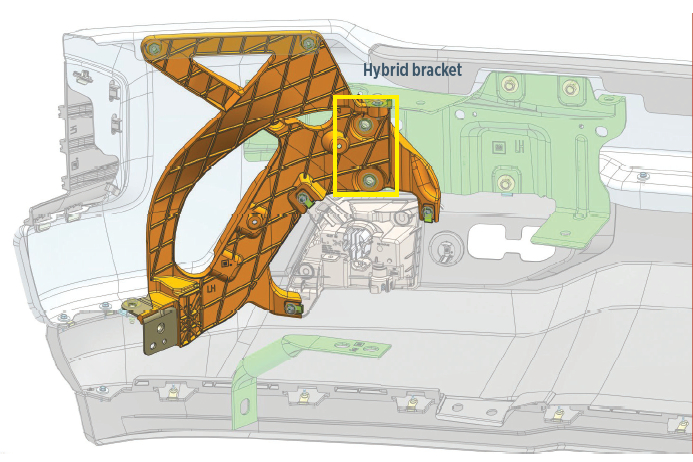
Em segundo lugar, os pára-choques dianteiros normalmente envolvem os cantos dianteiros do veículo para obter dicas de estilo que o estúdio de design deseja. No entanto, como eles são presos ao quadro pelos suportes de aço rígidos, durante eventos de colisão em alta velocidade, o pára-choque pode ser esmagado para dentro da roda, impactando negativamente a orientação da roda e travando a direção. Para proteger a roda no lado impactado pelo maior tempo possível, é desejável que os suportes do pára-choque se quebrem durante o impacto. Por outro lado, para evitar problemas de garantia, o pára-choque precisa permanecer preso durante o uso normal durante a vida útil do veículo. Portanto, a equipe teve que determinar como equilibrar essas necessidades concorrentes.
Ainda outro problema que a equipe queria abordar era que, devido às limitações de formabilidade do aço, os suportes de referência não podiam ser moldados para conter os faróis de neblina do veículo, o que exigia o uso de outro par de suportes de metal pesado. Se fosse possível, a equipe queria consolidar o suporte do farol de neblina no suporte composto.
Além disso, era importante evitar um ponto de esmagamento do chicote de fios quando ele passava pelo suporte para evitar que os chicotes e os fios se desgastassem e quebrassem, o que levaria a curtos-circuitos de características importantes como faróis e ventiladores. Evitá-los, fornecendo um orifício nos suportes de metal através do qual os fios poderiam passar, levou ao uso de uma operação de puncionamento adicional, o que acrescentou mais custos de ferramentas devido às limitações na liberdade de design. Era, portanto, desejável tentar resolver esse problema no colchete composto. Claro, também era importante evitar ter que fazer alterações na montagem do veículo para usar suportes compostos. E, como costuma ser o caso em aplicações automotivas, os suportes compostos seriam, idealmente, mais leves e menos caro do que os benchmarks metálicos. Uma última preocupação era se os modelos CAE atualmente disponíveis poderiam prever com precisão a fadiga / durabilidade de alto ciclo em um termoplástico reforçado com fibra descontínua.
Abordagem híbrida
Com a lista de desejos em mãos, a equipe se ocupou. Uma decisão inicial foi selecionar o material a ser usado - ou seja, um com o qual a FNG já tinha experiência e que tinha aprovações da GM. Eles escolheram um polipropileno de fibra de vidro longa (LFT-PP) preto com fração de peso de fibra de 40% (FWF) da Lotte Chemical (Seul, Coréia do Sul) chamado Supran PP1340 GMW15890P. Uma vez que os suportes não são expostos à luz solar e estão suficientemente distantes do calor do motor, o polímero de olefina resistente ofereceria desempenho térmico adequado. O grau moldável por injeção de alto fluxo tinha um índice de melt-flow (MFI) de 40, garantindo um bom preenchimento de geometria complexa sem a necessidade de adicionar portas extras; portas extras criam malhas que são mais fracas do que o material ao redor e devem ser evitadas em uma parte estrutural, especialmente uma que tenha de passar em testes de colisão.
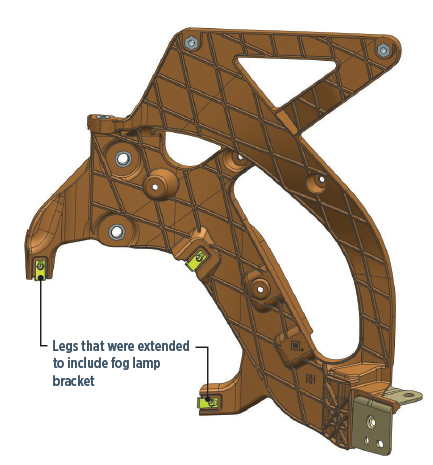
Para equilibrar as necessidades concorrentes de durabilidade de longo prazo com alto desempenho em colisões, a equipe fez uma abordagem híbrida e dividiu a chave. A parte que unia o pára-choque à estrutura permaneceria em aço HSLA, mas a parte externa seria convertida em composto. Esta abordagem permitiria maior liberdade de projeto para consolidar as peças, reduzir a massa e permitir a incorporação de faróis de nevoeiro, mas a porção composta seria projetada para quebrar em uma colisão lateral de alta velocidade para garantir que a orientação da roda permanecesse longitudinal pelo maior tempo possível para ajudam a manter a capacidade de direção. Para atender a todos os requisitos da GM, algumas inserções de metal foram adicionadas ao lado composto do suporte, junto com três buchas, que permitem o ajuste durante a montagem. Os projetistas descobriram que o material não tinha problemas para permitir que a perna do suporte (as peças finais curvas mostradas no design CAE composto / marrom) fosse estendida para abranger a luz de neblina, eliminando a necessidade de um suporte separado nesse local (Fig. 1).
À medida que o projeto avançava e as peças físicas eram produzidas e testadas, a equipe ficou feliz em saber que seus modelos CAE eram bastante precisos. “Inicialmente, nos perguntamos se seríamos capazes de simular a peça corretamente, visto que estávamos tentando prever a fadiga de alto ciclo, em termos de durabilidade, e carregamento G alto, na modelagem de colisão”, observa Heo. “Surpreendentemente, a correlação entre os resultados previstos e medidos do teste do agitador foi próxima, mesmo em colisão.” O desenho final do suporte foi concluído em menos de seis meses. Mede aproximadamente 41 x 46 centímetros, tem uma parede nominal de 3 milímetros e possui nervuras para mecânicos superiores.
O ferramental foi produzido pela Integrity Tool &Mold Inc. (Oldcastle, Ontário, Canadá) e apresentava um molde de pilha 2 + 2 bem ventilado com duas cavidades / placa e duas gotas diretas (canais frios) com passagem de válvula sequencial que produz quatro peças / ciclo devido ao alto volume de construção do Silverado plataforma. A divisão Ventra Evart da FNG é a moldadora. O tempo de ciclo de botão a botão é de 60 segundos.
Conquistas significativas
Em seu primeiro uso comercial, a abordagem híbrida da GM no suporte do pára-choque estrutural (Fig. 2) trouxe vários benefícios. Primeiro, obteve desempenho equivalente ou superior em testes modais, de estresse, de fadiga e de colisão (consulte a tabela abaixo).
Projeto
10 Gx
20 Gx
1 st Frequência do modo (Hz)
Deslocamento Máximo (mm)
Tensão Máxima (MPa)
Deslocamento Máximo (mm)
Tensão Máxima (MPa)
Suporte híbrido de aço / composto
2,00
213
3,97
381
31,7
Suporte de referência todo em aço
2,36
259
4,45
480
30,1
Não apenas o suporte de composto híbrido com pastilhas de metal reduziu a massa, mas sua geometria sob medida melhorou a tensão e o desempenho modal.
Em segundo lugar, a liberdade de design dos compostos permitiu um estilo mais agressivo em um espaço de embalagem relativamente pequeno. Terceiro, a massa do par de suportes híbridos foi reduzida em 2,5 kg / veículo em relação ao benchmark. E graças aos efeitos de decomposição de massa, os cantos do pára-choque mais leves possibilitaram a redução da bitola na cinta de montagem do pára-choque, bem como em outros componentes, de modo que a massa total do sistema de pára-choque dianteiro foi reduzida em 7,3 kg em relação ao modelo 2016 anterior.
Além disso, o risco de corrosão e os custos de garantia foram reduzidos, uma vez que o suporte composto não enferruja. A redução de massa beneficia os consumidores, contribuindo para uma maior economia de combustível ou permitindo que uma carga útil mais pesada seja transportada sem exceder os limites legais de carga em estradas.
Com base no preço da peça, o suporte híbrido foi uma lavagem, devido ao custo adicional do molde de injeção. Com base no custo do sistema, houve economia devido à capacidade de reduzir os componentes adicionais, embora a economia real seja difícil de quantificar. O suporte está em produção há mais de três anos sem problemas.
Para o Silverado de próxima geração , A equipe de Heo planeja continuar usando suportes híbridos no pára-choque dianteiro, mas ele já desafiou os membros da equipe a começar a pensar em como fazer uma abordagem híbrida nos suportes do para-choque traseiro. Isso é complicado pelo fato de que os para-choques traseiros contêm recursos de auxílio de passo nos cantos para permitir que as pessoas subam / saiam da caixa de recolhimento com mais facilidade e segurança. Além disso, mais componentes (como sensores de alerta de backup) são embalados atrás da capa de aço, reduzindo o espaço da embalagem.
“Continuaremos usando uma abordagem de engenharia inteligente para examinar os problemas, descobrir como os produtos estão sendo usados e quais são seus requisitos funcionais e, em seguida, ir além”, conclui Heo.
Resina
- Covestro Aumenta o Investimento em Compósitos Termoplásticos
- Compostos termoplásticos na Oribi Composites:CW Trending, episódio 4
- Resolução de problemas de termoformação de compósitos termoplásticos
- Toray Advanced Composites expande as capacidades de compósitos termoplásticos
- A Teledyne CML Composites investe em capacidade de processamento termoplástico
- Cato Composites expande capacidade de produção de compósitos termoplásticos
- ACMA lança programa da Conferência de Compostos Termoplásticos em 2020
- Porta termoplástica a primeira para compósitos automotivos
- Compostos termoplásticos:Vista panorâmica
- Compósitos termoplásticos de soldagem