Novos horizontes na soldagem de compósitos termoplásticos
Este blog acompanha o artigo de setembro de 2018 “Compostos termoplásticos de soldagem”. É uma compilação de imagens e detalhes que não cabem no artigo impresso, incluindo uma linha do tempo de desenvolvimentos de soldagem por indução e detalhes sobre qualificação para aeronaves comerciais futuras, bem como seções curtas sobre reparos, desenvolvimentos para automóveis e termofixos para termoplásticos (TS -TP) soldagem.
Apenas para reiterar porque os conjuntos de composto termoplástico soldado (TPC) são de interesse para estruturas leves aeroespaciais e automotivas, compare as duas imagens abaixo da antepara de pressão traseira do Airbus A320. A imagem superior é a versão atual em alumínio. Observe o grande número de rebites. Agora compare isso com o demonstrador TPC soldado apresentado pela Premium Aerotec no airshow ILA 2018 em Berlim. Observe a ausência de rebites. Para os compósitos, isso não apenas elimina o peso, o tempo e o custo dos fixadores, mas também o tempo e o custo de posicionamento e perfuração dos orifícios, além da limpeza e inspeção desses orifícios. Isso também significa estruturas muito mais leves, sem as almofadas laminadas necessárias para compensar os cortes nas fibras de suporte de carga.
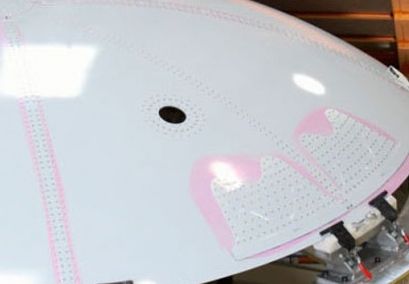
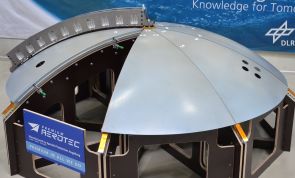
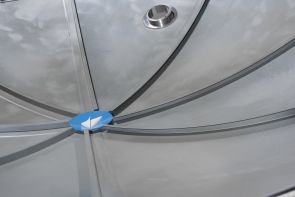
Uma antepara de pressão traseira A320 composta termoplástica soldada (parte inferior) oferece uma solução sem rebites em comparação com a construção atual de alumínio (parte superior).
FONTE:RUAG (topo) e Premium Aerotec (abaixo), DLR Center for Lightweight Production Technology (Augsburg, Alemanha)
“Outro benefício é que a inspeção de estruturas soldadas é mais fácil do que os conjuntos colados”, disse o Dr. Hans Luinge, diretor de P&D e desenvolvimento de produtos de compósitos termoplásticos do fornecedor de materiais TPC TenCate-Toray Group. “O C-scan funciona bem, mostrando se não há porosidade no laminado, o que significa que a solda está boa. Para estruturas coladas com adesivo, você pode ter um laço de beijo ou contaminantes que são difíceis de detectar. ” Embora o TenCate-Toray não desenvolva a tecnologia de soldagem por si só, ele apóia uma variedade de indústrias e projetos de clientes. “Otimizamos nossos materiais conforme necessário”, diz Luinge, “e tentamos ajudar a orientar os desenvolvimentos na direção certa com base em nossa participação de longa data em esforços como a TAPAS e com parceiros como KVE Composites, o TPRC, fornecedores de nível e OEMs.”
Desenvolvimentos de soldagem por indução
A KVE Composites desenvolve solda por indução para TPCs desde 2001. As primeiras aplicações usavam tecido de fibra de carbono / laminados PPS, incluindo elevadores e leme para os aviões a jato executivo Gulfstream G650 e Dassault Falcon 5X.
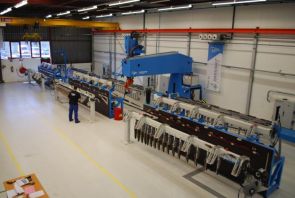
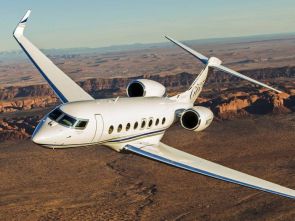
KVE Composites ajudou para desenvolver a produção da GKN Fokker de elevadores e leme soldados por indução (à esquerda) para as aeronaves Gulfstream G650 (à direita) e Dassault Falcon 5X.
FONTE:KVE Composites, GKN Fokker (à esquerda) e Gulfstream (à direita).
Outras aplicações TPC soldadas por indução incluem portas de acesso a tanques de combustível produzidas pela AVIACOMP S.A.S. (Launaguet, França e agora parte do Grupo Sogeclair) para a asa do Airbus A220 (anteriormente Bombardier CSeries). (A Aviacomp também produziu longarinas para a fuselagem TPC soldada da STELIA mostrada no Paris Air Show 2017.)
Aviacomp usa indução tecnologia de soldagem desenvolvida pela KVE Composites em sua produção de portas de acesso ao tanque de combustível TPC para aeronaves de corpo estreito Airbus A220.
FONTE:Aviacomp, parte do Grupo Sogeclair.
Esta categoria geral de portas de acesso é uma oportunidade para a soldagem TPC economizar custos, mostrado em um estudo de design e fabricação concluído pela KVE Composites. Mesmo aeronaves menores podem ter até 60 desses painéis de acesso, todos com formatos diferentes e, normalmente, feitos de construção em sanduíche composta com núcleo em favo de mel usinado. “Se você usar um conjunto termoplástico soldado, poderá fazer todos os diferentes painéis de acesso para uma aeronave com apenas US $ 100.000 em custos de ferramentas, o que é uma economia dramática”, disse Harm van Engelen, diretor administrativo da KVE Composites. “Não precisamos usinar o núcleo, apenas usamos componentes 'semelhantes aos do lego' - folhas planas e reforços estampados - soldados entre si para formar as várias formas. Além disso, nosso ferramental é mais como um gabarito de soldagem, portanto, custo relativamente baixo em comparação com o que eles estão usando hoje. Todos os painéis de acesso de uma aeronave podem ser feitos em uma única célula de soldagem. ”
Conjunto termoplástico soldado para painéis salientes de aeronaves pode ser feito usando células de formação e soldagem automatizadas e economize $ 100.000 em custos de ferramentas. FONTE:KVE Composites.
A KVE Composites está continuando seu desenvolvimento de tecnologias de soldagem TPC, conforme ilustrado nos cronogramas abaixo. A célula de produção mostrada na parte inferior para 2019 é a máquina Falko ATL (colocação automática de fita), produzida pela Boikon (Leek, Holanda) usando um efetor de extremidade de soldagem ultrassônico desenvolvido pela GKN Fokker. “Esta célula robótica permite um processo mais eficiente e sistema de controle para o próximo nível de produção de peças TPC de volume em comparação com os métodos de separação e colocação usados hoje”, explica KVE Composites, chefe de P&D Maarten Labordus. “Por exemplo, você pode colocar de forma totalmente automática a pele e os laminados de nervura para uma superfície de controle de jato regional (que tem aproximadamente 60 mm x 3 m), aplicar uma consolidação fora da autoclave e uma etapa de formação e, em seguida, concluir a montagem em um célula de soldagem adjacente. ” A máquina Falko ATL também demonstra controle de malha fechada já desenvolvido pela GKN Fokker para soldagem ultrassônica. “A máquina é capaz de controlar o nível de energia conforme necessário por tipo de material, espessura e forma, no entanto, a consolidação total por fusão da pré-forma plana é necessária depois durante a moldagem da peça TPC acabada”, explica Arnt Offringa, chefe de Aeroestruturas R&T da GKN Fokker.
FONTE:Compostos KVE
Qualificação
Mostrado acima como uma iniciativa-chave de desenvolvimento em 2017, qualificação de processos de soldagem por indução para aeroestruturas TPC é uma prioridade contínua. De acordo com o resumo da próxima apresentação da KVE Composites no 4º th Int. Conf. e a Exposição sobre Compósitos Termoplásticos (ITHEC, 30-31 de outubro de 2018 em Bremen, Alemanha), nos últimos anos a soldagem de compósitos termoplásticos (TPC) viu uma mudança de polímeros como PPS e PEI para polímeros de ponta como PEEK , PEKK e agora Low Melt PAEK (LM PAEK, leia mais em meu blog “PEEK vs. PEKK vs. PAEK ...”), bem como para fitas UD colocadas automaticamente e laminados mais espessos para estruturas mais carregadas. Em resposta, a KVE Composites buscou melhorar e padronizar ferramentas e equipamentos, bem como modelos de simulação baseados em FEA.
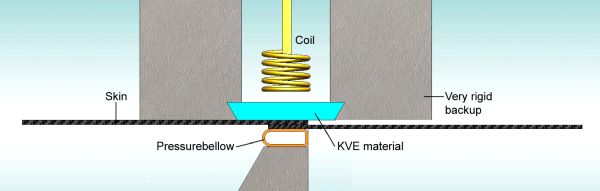
Configuração padronizada para qualificação de soldagem por indução com novos materiais.
FONTE:KVE Composites
Para auxiliar na maturação e qualificação do processo de soldagem por indução com esses novos laminados compostos, a KVE Composites desenvolveu uma configuração padronizada para soldagem de cisalhamento de volta única e também cupons de teste de pull-off em L e em T. Esta configuração inclui:
- Uma estrutura rígida para suportar as cargas da aplicação de pressão ao laminado durante a soldagem.
- Um bloco de ferramentas inferior que pode ser posicionado sob a estrutura para permitir a soldagem reproduzível de painéis padrão.
- Um mandril inflável (pressão abaixo na figura acima) no bloco de ferramentas inferior que pode se expandir em apenas uma direção para comprimir o laminado sendo soldado contra um dissipador de calor especial ("material KVE" na figura acima) para confinar o calor na soldagem interface.
Ao trocar os blocos de ferramentas inferiores, uma variedade de cupons padrão podem ser soldados e depois inspecionados por ultrassom, após o que cupons menores podem ser cortados e testados mecanicamente. Esta configuração padronizada já foi instalada por:
- Centro de pesquisa termoplástica (TPRC, Enschede, Holanda)
- McNair Center da University of South Carolina (Columbus, SC, EUA)
- Centro Aeroespacial da Holanda (NLR, Marknesse, Holanda).
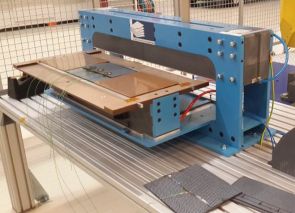

Soldagem por indução padronizada configuração em KVE (esquerda) e amostra de fibra de carbono UD / PEKK soldada com termopares para registrar a temperatura na linha de solda (direita).
FONTE:KVE Composites.
Reparar
Outra área de desenvolvimento chave é como reparar estruturas aerodinâmicas TPC. “Estamos nos concentrando primeiro em estruturas de tecido CF / PPS que são qualificadas e voadoras”, diz Labordus. “O processo é basicamente o mesmo usado para reparos de compostos termofixos:remova o material danificado, prepare a área com um lenço cônico e, em seguida, cole em um remendo de reparo pré-impregnado. Labordus diz que um dos problemas é que o pré-impregnado termoplástico à temperatura ambiente é resistente e não gruda, "por isso é difícil fazer com que a geometria corresponda". No entanto, ele acredita que os sistemas de reparo robótico desenvolvidos pela Airbus, Lufthansa e outros oferecem uma solução.
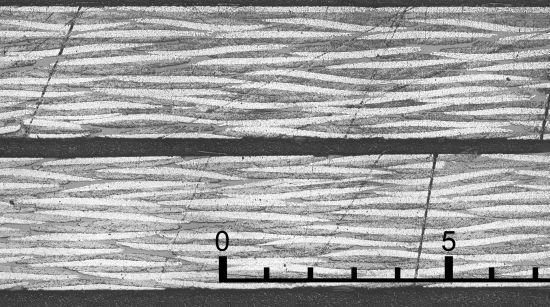
Como parte de seu desenvolvimento contínuo de reparos de compósitos termoplásticos estruturais soldados, a KVE Composites conseguiu juntas cônicas lineares 2D soldadas por indução em tecido CF / laminados PPS com espessura uniforme e 90% de propriedades de material virgem.
FONTE:KVE Composites.
Esses sistemas usam metrologia para medir com precisão lenços cônicos usinados de forma robotizada e, em seguida, unir um remendo pré-fabricado que foi usinado de maneira robotizada para corresponder. “Queremos usar solda por indução para soldar um remendo termoplástico à estrutura original”, diz Labordus, mas ainda há questões a serem resolvidas. “Dependendo da forma da peça e do remendo, correntes parasitas não se formam em todos os lugares, então podemos obter áreas de frio ou superaquecimento. A KVE Composites trabalhou nisso e foi capaz de obter uma junta cônica linear 2D em tecido CF / laminados PPS com espessura uniforme e uma soldagem perfeita. “Estávamos dentro de 10% das propriedades do material virgem”, diz Labordus.
A próxima etapa será soldar por indução duas partes retangulares, cada uma com uma borda chanfrada e, em seguida, soldar um remendo cônico a um orifício circular / elíptico com um lenço cônico, que é essencialmente o método usado para reparos de compósitos termofixos. “Se funcionar, passaremos para os laminados UD feitos com PEEK e PEKK”, diz Labordus. Ele observa que um sistema para usar uma bobina de indução para fazer reparos no campo ainda não foi demonstrado, “mas pode fazer isso no laboratório”. Outra questão é como aplicar pressão para um contato suficientemente próximo entre o remendo de reparo e a superfície cônica. “No momento, a pressão usada na ferramenta de laboratório é de 5 bar. Não tenho certeza se a pressão da bolsa a vácuo é suficiente, mas com material UD mais plano, 1 bar da bolsa a vácuo pode ser suficiente. ”
A soldagem por indução sob um saco a vácuo - um possível facilitador para futuros reparos de compósitos termoplásticos em campo - está sendo desenvolvida por Michel van Tooren e sua equipe no McNair Center da University of South Carolina. FONTE:Michel van Tooren.
Este trabalho na KVE Composites está sendo estendido por Michel van Tooren, diretor do SmartState Center for Multifunctional Materials and Structures, parte do McNair Center da University of South Carolina (Columbia, SC, EUA). “Estamos soldando compósitos termoplásticos por indução sob um saco a vácuo, o que é muito semelhante a como os reparos de compósitos em campo são feitos hoje com um adesivo quente e manta térmica”, explica ele. “O saco de vácuo se comporta como uma ferramenta macia para compressão das duas partes. Você aplica corrente de indução e consegue um reparo de fusão. Você só precisa ter os limites e parâmetros do processo definidos. De certa forma, é mais fácil do que consertar termofixo porque você sempre pode fundir novamente o conserto, se necessário, mesmo do outro lado do mundo ou após 20 anos de serviço. E o resultado não é uma ligação adesiva, mas uma parte coesiva, assim você elimina todos os problemas com a ligação e como saber se você tem uma boa ligação em um reparo termofixo. ” Ele também acredita que, com as tecnologias de reparo robótico automatizado que estão sendo desenvolvidas agora, “um reparo por soldagem por indução seria relativamente simples”.
Soldagem termoendurecível para termoplástico
Van Tooren também está desenvolvendo soldagem por indução para unir compostos termofixos e termoplásticos. “Introduzimos o termoplástico em um compósito termofixo, mas apenas onde queremos soldar”, explica ele. “Nós enxertamos em uma nanopartícula e fazemos uma pequena polimerização cruzada. O resultado é uma ilha de termoplástico implantada e quimicamente co-fundida com o compósito termofixo. Posso então soldar na ilha de termoplástico. ” Mais uma vez, a visão são métodos alternativos para a união e montagem de compósitos que evitam fazer furos e os problemas associados à colagem convencional.
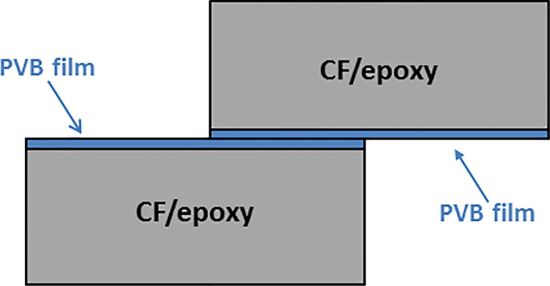
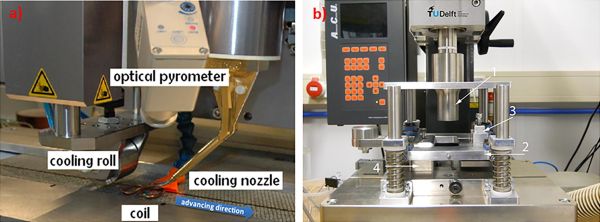
Esquema de uma junta TSC-TSC via camada de acoplamento termoplástico PVB antes da soldagem (topo). Configurações (inferior) para soldagem por indução (esquerda) e soldagem ultrassônica (direita).
FONTE:“Soldagem híbrida de compósitos à base de CF / epóxi”.
A soldagem de laminados compostos termofixos (TSC) em laminados TPC (ou soldagem TS-TP) está sendo realizada por várias organizações de pesquisa. Irene Fernandez Villegas da TU Delft - mencionada no artigo impresso como líder no desenvolvimento de soldagem ultrassônica contínua de TPCs - foi coautora de um artigo de 2017 intitulado "Soldagem híbrida de compósitos à base de epóxi reforçado com fibra de carbono" junto com Francesca Lionetto no Universidade de Salento (Lecce, Itália), Silvio Pappadà em CETMA Composites (Brandisi, Itália) e outros. Os princípios básicos são os seguintes:
- Polivinilbutiral (PVB) é um polímero termoplástico semicristalino de baixo custo com uma temperatura de fusão de 150-170 ° C caracterizada por excelente ligação e capacidade de formação de filme e adesão a muitas superfícies.
- PVB (Mowital, fornecido por Kurakay) foi usado como uma camada de acoplamento, adicionado e co-curado a um tecido de fibra de carbono de 14 camadas / laminado de TSC de epóxi (Hexcel 3501-6 prepreg com um teor de volume de fibra de 58% e 180 Cura ° C).
- O intertravamento macromecânico entre a camada de acoplamento de PVB e o compósito CF / epóxi foi obtido por meio da penetração parcial da resina de PVB na primeira camada do TSC (normalmente entre 10 e várias centenas de mícrons de espessura) durante a co-cura e difusão dos monômeros de epóxi no filme termoplástico de PVB.
- Os processos de soldagem por indução e soldagem ultrassônica resultaram em juntas soldadas adequadamente fortes, com as juntas CF / epóxi a CF / epóxi resultantes soldadas através das camadas de acoplamento PVB mostrando uma resistência ao cisalhamento de ≈25 MPa, que está dentro da faixa típica de valores de resistência para juntas CF / epóxi coladas.
Automotivo
Quase todas as empresas incluídas no artigo de impressão de soldagem termoplástica estão olhando para aplicações automotivas e aeroespaciais. “A soldagem ajuda a tornar os compósitos competitivos em relação ao alumínio”, diz Offringa, da GKN Fokker. “O setor automotivo também está considerando a soldagem como uma alternativa rápida para a colagem. Conversamos com várias empresas automotivas sobre o processamento rápido de compósitos. ” Ele ressalta que as carrocerias de fibra de carbono são, em sua maioria, termofixas, coladas com uma espessura específica de adesivo. “Se você pudesse fazer essas peças usando termoplástico compõe e elimina lacunas entre os componentes soldando a montagem, então você pode fazer uma estrutura de corpo mais rígida, o que traz benefícios de peso, custo e desempenho. ”
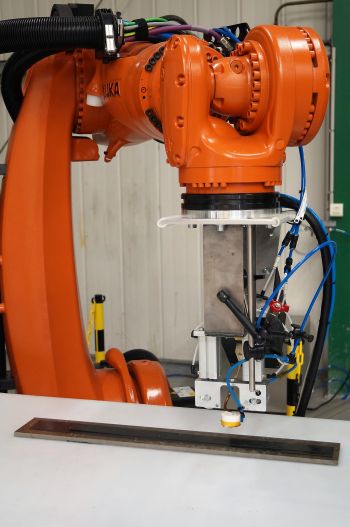
Composite Integrity's dynamic configuração do processo de soldagem por indução.
FONTE:Integridade composta.
Jérôme Raynal, gerente de desenvolvimento de negócios da Composite Integrity, também vê potencial. Sua empresa trabalhou com a STELIA Aerospace para desenvolver o processo de soldagem por indução dinâmica usado para juntar longarinas de fita CF / PEKK UD e películas de fuselagem no demonstrador TP, revelado no 2017 Paris Air Show. “Desenvolvemos soldagem resistiva para automotivo com compósitos de poliamida [PA, náilon] e polipropileno [PP]”, diz Raynal. “Temos uma variedade de tecnologias diferentes para isso. Por exemplo, podemos embutir um fio metálico em uma parte, colocá-lo em contato com outra parte e injetar corrente. Também podemos colocar um remendo resistivo de fibra de carbono na interface de soldagem para gerar o calor de soldagem necessário. ” Em um desenvolvimento, dois componentes feitos de CF / PA foram soldados usando um remendo resistivo especialmente projetado feito com o mesmo polímero e um velo de fibra de vidro para isolar eletricamente o laminado adjacente e concentrar a energia na linha de solda. E as pastilhas de metal que são muito típicas em peças automotivas? “As peças com insertos de metal não são problema para a soldagem por resistência, e com a soldagem por indução você usaria uma bobina especialmente projetada ou modificaria os campos eletromagnéticos e a corrente de alguma outra forma”, responde Raynal. “This would have to be developed, but it is similar to what we have already demonstrated for automated production of aircraft structures.”
Further developments and other projects
One note regarding the opening image. It shows a CAD rendering of the automated process developed by the DLR Center for Lightweight Production Technology (DLR ZLP, Augsburg, Germany) using an ultrasonic welding head on a KUKA Quantec KR210 industrial robot to join eight TPC sections into a rear pressure bulkhead (RPB) for an A320-type aircraft. In the accompanying print article on TPC welding, I discussed DLR ZLP’s development of a resistance welding method which was used on Premium Aerotec’s A320 RPB demonstrator exhibited at the 2018 ILA air show in Berlin. According to Lars Larsen, group manager for assembly and joining technologies at DLR ZLP, “In parallel to the resistance welding process using a ‘welding bridge’, we have also developed a robotically actuated ultrasonic welding head. We have completed preliminary tests to determine the relevant welding process parameters, and in the next months we will refine the integration of that ultrasonic welding end-effector in our robot. Our goal is to develop a single industrial process for welding both aircraft fuselage stringers and rear pressure bulkhead made using thermoplastic composites.”
Other projects that I did not have a chance to cover this time around include EireComposites and its participation in the Ybridio and Innova projects, pursuing the potential for welding to reduce cost and increase automation. The company reports induction welding and resistance welding capability for CF/PEEK, CF/PEKK and GF/PP composites and that thermoplastic welding was evaluated for the Bombardier CSeries (now the Airbus A220) wing.
Tods Aerospace, now part of Unitech Aerospace, participated in a National Aerospace Technology Exploitation Programme (NATEP) sponsored by Rolls-Royce which looked at development of a resistance welding technique that does not use metallic embedded implants. TenCate-Toray and the National Composites Centre (Bristol, UK) were also partners.
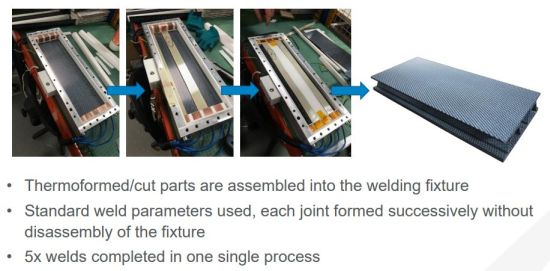
This process demonstrator explored a method for manufacturing a hat-stiffened TPC structures. SOURCE:Unitech Aerospace (start at Section 6, p. 39)
Stay tuned, as I plan to cover Laser Zentrum Hannover’s (LZH) developments with laser welding of thermoplastic composites in the near future.
SOURCE:LZH Laser Zentrum Hannover e.V.
Resina
- Covestro Aumenta o Investimento em Compósitos Termoplásticos
- Compostos termoplásticos na Oribi Composites:CW Trending, episódio 4
- Projeto RECONTRAS valida o uso de microondas e soldagem a laser para obter compósitos recicláveis
- A nova bota de caminhada da Salewas apresenta compostos termoplásticos
- Resolução de problemas de termoformação de compósitos termoplásticos
- Compostos termoplásticos:Suporte de pára-choque estrutural
- Toray Advanced Composites expande as capacidades de compósitos termoplásticos
- Consórcio de compostos termoplásticos IRG CosiMo revela novas instalações
- Compostos termoplásticos:Vista panorâmica
- Compósitos termoplásticos de soldagem