Compostos termoplásticos:preparados para avançar
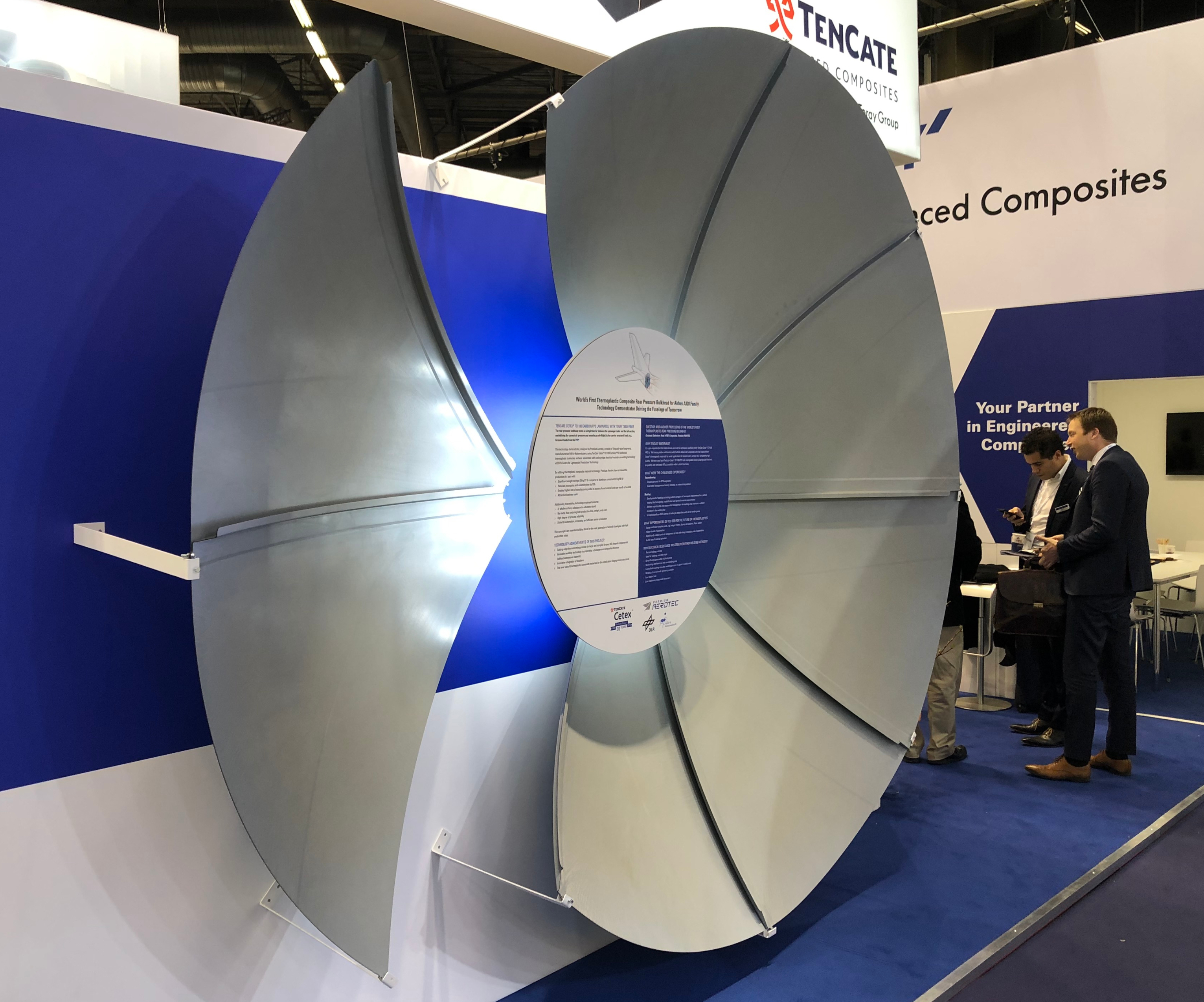

Compósitos termoplásticos (TPC) não são novos para o setor aeroespacial, mas nos últimos dois anos viram o uso de termoplásticos em aeronaves comerciais atingir um ponto crítico. Embora os TPCs tenham sido usados por algum tempo para peças menores, como clipes e suportes, ou componentes internos menores, os termoplásticos têm trabalhado em estruturas de aeronaves maiores de forma incremental e agora parecem destinados a desempenhar um papel maior no futuro das aeronaves comerciais.
Em março de 2018, Toray Industries Inc. (Tóquio, Japão), o maior fabricante de fibra de carbono do mundo, adquiriu TenCate Advanced Composites (Morgan Hill, Califórnia, EUA e Nijverdal, Holanda) por € 930 milhões (TenCate mudou desde então seu nome para Compostos avançados Toray). A mudança parecia ser um esforço para fortalecer as capacidades de termoplásticos de Toray em preparação para a próxima onda de desenvolvimento de aeronaves comerciais. Pouco depois desse anúncio, a Hexcel (Stamford, Connecticut, EUA) e a Arkema Inc. (King of Prussia, Pa., EUA) anunciaram uma aliança estratégica para desenvolver soluções de compósitos termoplásticos para a indústria aeroespacial, combinando a habilidade da Hexcel na fabricação de fibra de carbono com a polietercetonecetona da Arkema (PEKK) experiência em resinas. E, ao longo do ano, várias outras peças do quebra-cabeça dos termoplásticos pareceram se encaixar.
Em abril de 2018, a Premium Aerotec GmbH (Augsburg, Alemanha) apresentou um demonstrador para uma antepara de pressão A320 da Airbus (Toulouse, França) desenvolvida e fabricada com fibra de carbono em uma matriz termoplástica. O demonstrador, que consiste em oito segmentos soldados, ilustra como a soldabilidade dos termoplásticos tem o potencial de habilitar componentes maiores de aeronaves. (Saiba mais sobre o demonstrador de anteparo de pressão A320 da Premium Aerotec).
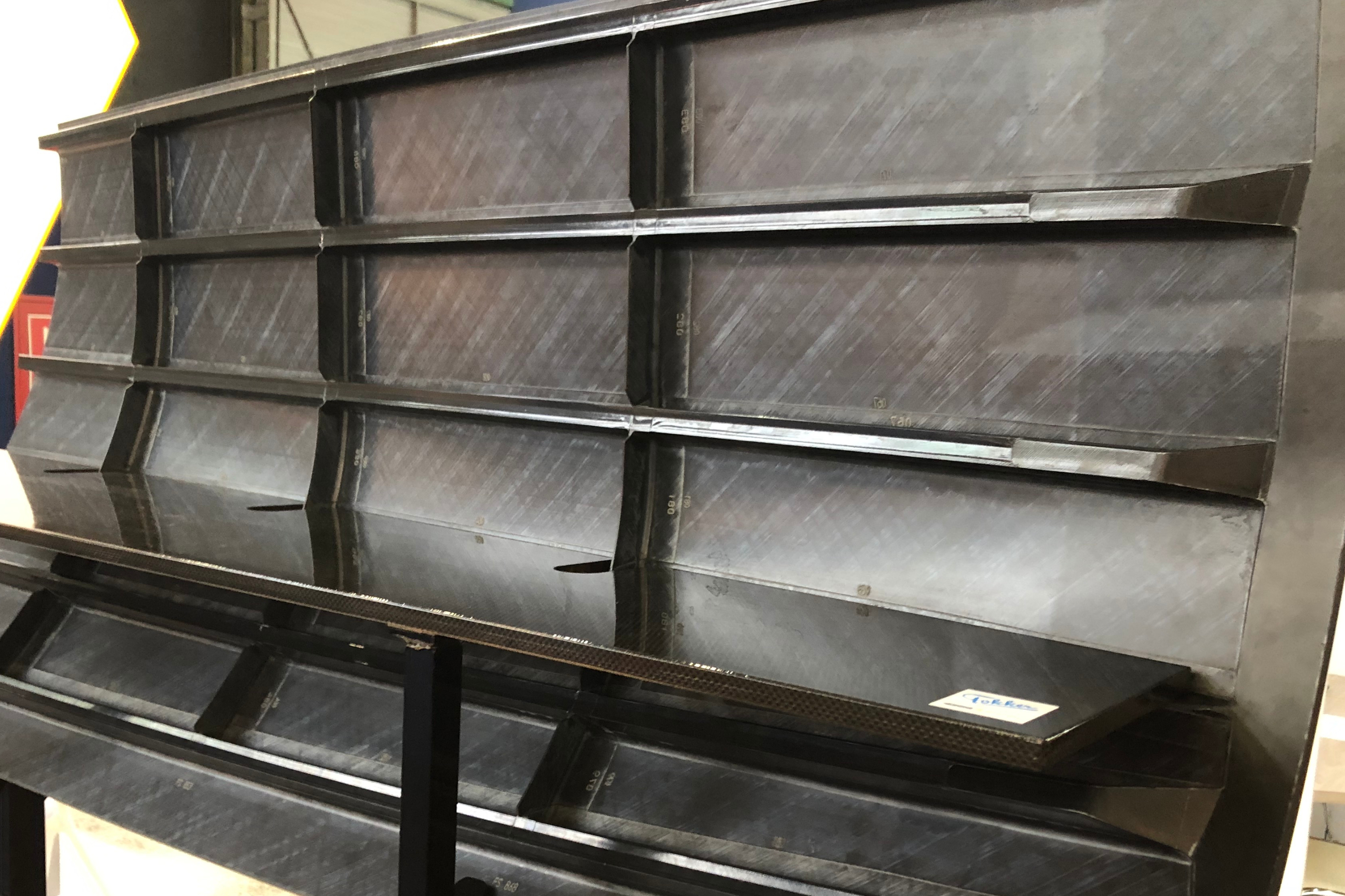
Em agosto de 2018, Solvay (Alpharetta, Ga., US), Premium Aerotec e Faurecia Clean Mobility (Columbus, Ohio, EUA) lançaram o IRG CosiMo (Grupo de Pesquisa da Indústria:Compostos para Mobilidade Sustentável), um consórcio focado no desenvolvimento de materiais e tecnologias de processo destinadas a permitir a produção em alto volume de compostos termoplásticos para os mercados aeroespacial e automotivo. O consórcio reúne empresas ao longo de toda a cadeia de processos de compósitos termoplásticos, de materiais a máquinas e aplicações automotivas e aeroespaciais. (Saiba mais sobre o consórcio IRG CosiMo aqui).
A Solvay fez parceria com a GKN Fokker (Hoogeveen, Holanda) para o avanço da tecnologia e adoção de TPCs para grandes estruturas aeroespaciais desde junho de 2017. A empresa lançou a produção de polímero PEKK em setembro de 2017 e, em seguida, dobrou sua capacidade de fita termoplástica UD qualificada em 2018. Anteriormente em 2019, a Solvay comissionou um laboratório de pesquisa TPC dedicado em Alpharetta, Geórgia, EUA, voltado para o desenvolvimento de materiais de próxima geração. A Solvay planeja iniciar a qualificação de uma nova linha de fitas UD no final de 2019.
Teijin Ltd. (Tóquio, Japão) anunciou em janeiro de 2019 que sua fibra de carbono TENAX e fibra de carbono / fita termoplástica pré-impregnada unidirecional (TENAX TPUD) foi qualificada pela Boeing (Chicago, Illinois, EUA) para uso como um avançado intermediário material composto para peças estruturais primárias (leia a notícia completa aqui).
À medida que essas e outras tecnologias e materiais semelhantes progridem, uma imagem de como a indústria aeroespacial pode começar a parecer nos anos e décadas que virão gradualmente entra em foco. O papel dos TPCs está se tornando uma parte cada vez maior dessa imagem.
Os fabricantes estão interessados em aproveitar os benefícios da fabricação e os tempos de processamento rápidos dos termoplásticos, e em usar TPCs para começar a fazer estruturas maiores, como painéis de fuselagem e nervuras. Além disso, os termoplásticos apresentam alta resistência à fratura; boas propriedades mecânicas; reciclabilidade; chama baixa, fumaça e toxicidade (FST), e pode ser armazenado em temperatura ambiente. E conforme os OEMs e fornecedores de nível aeroespacial se tornam mais familiarizados com os termoplásticos, eles estão sendo usados para peças mais complexas, conjuntos soldados e estruturas primárias.
De acordo com Steve Mead, diretor administrativo da Toray Advanced Composites (anteriormente TenCate), “[os principais fusíveis] estão realmente procurando uma solução de material que tenha as capacidades de taxa de alumínio e as capacidades de peso de material à base de fibra de carbono - termoplásticos tipo ponte essa lacuna. ”
Processabilidade de TPCs
Uma grande parte do motivo pelo qual os TPCs estão encontrando seu lugar nos programas de aeronaves é sua processabilidade. Como os termoplásticos já estão totalmente polimerizados, eles apresentam taxas de produção mais rápidas do que os termofixos, que devem sofrer cura.
“Quando você olha para a quantidade de tempo que leva para fazer uma peça termofixa hoje e compara com a quantidade de tempo que leva para fazer uma peça de composto termoplástico, [termoplástico] é cerca de 10 vezes mais rápido”, diz Mike Favaloro, presidente e CEO da CompositeTechs LLC (Amesbury, Mass., EUA), uma consultoria da indústria de compostos.
Uma grande vantagem da colocação automática de fibra termoplástica (AFP) em comparação com a AFP termofixa - principalmente devido à falta de ciclo de cura - são as taxas de produção mais altas devido ao tempo de processamento mais rápido. Há economia de custos a ser encontrada na laminação in-situ e pós-consolidação fora de autoclave (OOA). Além disso, retirar a autoclave da equação permite o desenvolvimento de estruturas maiores.
David Leach, diretor de desenvolvimento de negócios da ATC Manufacturing (Post Falls, Idaho, EUA), reconhece que o custo unitário dos termoplásticos excede o custo dos termofixos, mas argumenta que os preços dos materiais TPC cairão. Além disso, diz ele, as eficiências de processamento oferecem uma oportunidade de reduzir custos hoje. O consenso geral na indústria de compósitos é que os processos termoplásticos OOA, agora, oferecem economia de custos de mais de 30 por cento em comparação com os termofixos.
“Os termoplásticos estão encontrando seu lugar nos programas, mesmo depois que os aviões entraram em produção”, ressalta Leach. “É uma prova dos benefícios de custo dos termoplásticos.”
O potencial dos polímeros de matriz de alto desempenho vai além do que está atualmente disponível no mercado. Doug Brademeyer, chefe de Materiais de Ultra-Polímeros da Solvay, diz que a empresa está trabalhando tanto internamente quanto com parceiros para desenvolver polímeros sob medida para os diferentes processos de fabricação.
“Estamos entusiasmados com essas soluções PAEK personalizadas e podemos rapidamente colocá-las na comercialização em nossos ativos em escala mundial, com base nas necessidades do cliente”, disse Brademeyer.
PAEK com baixo ponto de fusão
Com OEMs e fornecedores de aeronaves lutando por taxas de produção mais altas e tempos de ciclo mais curtos, a capacidade de processamento é fundamental. A poliéteretercetona (PEEK) há muito é o polímero termoplástico preferido, pois tem o maior banco de dados e é o mais amplamente qualificado. Mas, de acordo com Favaloro, a poliarlyetherketone de baixo ponto de fusão (LM PAEK) oferece algumas vantagens, especialmente para métodos de processamento automatizados como ATL.
“PEEK é processável por meio de formação de carimbo e moldagem contínua, mas LM PAEK processa a uma temperatura mais baixa, tem uma viscosidade de trabalho mais baixa que permite um processamento melhor automatizado e tem um grau de cristalinidade mais baixo que reduz as tensões de moldagem residuais”, diz ele. “O objetivo final é usar uma máquina ATL para colocar [a fita] e acabar com ela - você precisa do grau certo de cristalinidade, uma boa janela e boas velocidades de deposição.”
O LM PAEK tem uma ampla janela de processo de 350-385ºC. Para referência, as temperaturas de processamento do sulfeto de polifenileno (PPS) variam de 330-350 ° C, enquanto as temperaturas de processamento da polietercetonecetona (PEKK) e PEEK são 380 ° C e 400 ° C, respectivamente.
“O material ganhou muita força por causa de sua processabilidade”, disse Scott Unger, diretor técnico da Toray Advanced Composites. A Toray Advanced Composites colaborou com a Victrex (Lancashire, Reino Unido) para produzir Cetex TC1225, uma fita unidirecional usando LM PAEK.
“A intenção com o desenvolvimento do TC1225 era criar um produto que processasse facilmente em temperaturas próximas às usadas para PPS, tivesse uma posição de custo favorável para o usuário final e tivesse as propriedades mecânicas e de resistência a fluidos de PEEK”, diz Unger. “Com o TC1225 LM PAEK, sinto que alcançamos todos esses objetivos.”
Cetex TC1225 está atualmente passando por qualificação pelo Centro Nacional de Desempenho de Materiais Avançados (NCAMP, Wichita, Kan., EUA). Além disso, Toray diz que há duas grandes qualificações baseadas em airframer em andamento para o material, bem como alguns programas de qualificação baseados em mercados emergentes, como táxis aéreos e mobilidade aérea urbana.
As fitas usando LM PAEK estão supostamente produzindo velocidades de laydown aprimoradas. Tim Herr, diretor de SBU aeroespacial da Victrex, diz:“As taxas de laydown que podemos alcançar tanto para AFP in-situ quanto para AFP consolidada fora de autoclave não têm precedentes”. Ele indica que 60 metros por minuto podem ser alcançados em painéis consolidados em forno; 20 metros por minuto é supostamente possível com a consolidação in-situ.
Em termos de qualidade, Unger afirma que o PAEK de baixo ponto de fusão oferece a capacidade de obter a mesma qualidade de laminado usando a colocação de fibra in-situ como com um laminado colocado de fibra que foi colocado através de uma consolidação de forno de colocação pós-fibra.
Ligação de compósitos
A soldabilidade dos TPCs é uma grande vantagem do material para uso no desenvolvimento de aeronaves. A colagem / soldagem por fusão oferece uma alternativa à fixação mecânica e ao uso de adesivos, ambos métodos empregados para a união de peças compostas termofixas.
Stephen Heinz, diretor de desenvolvimento de produto da Solvay, afirma:“A união e a soldagem desempenham um papel importante no futuro da montagem e têm o potencial de cortar custos e melhorar a confiabilidade das aeroestruturas. Empresas como a GKN Fokker estão assumindo a liderança na demonstração de soldagem. ”
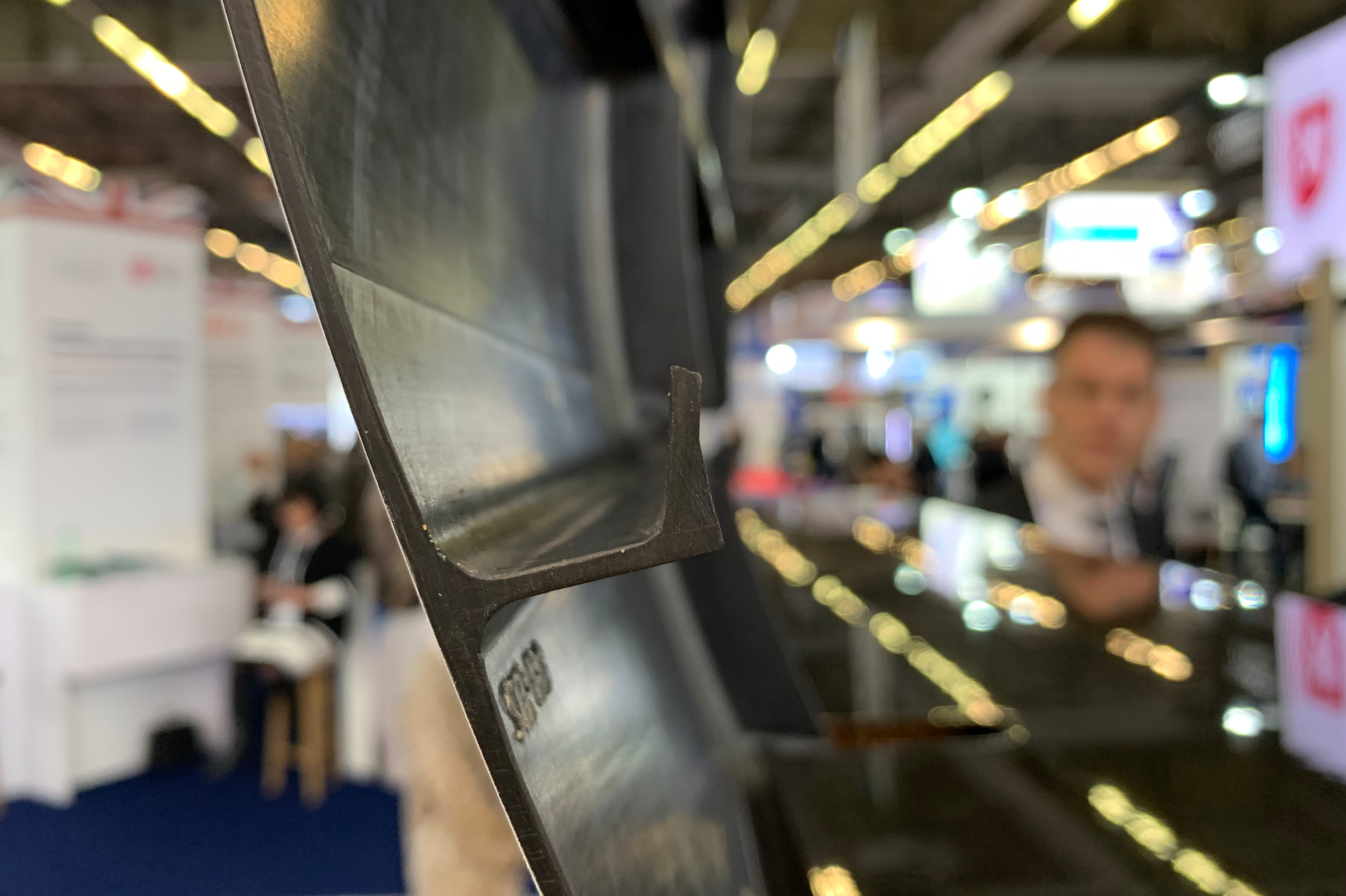
GKN Fokker (Hoogeveen, Holanda) tem trabalhado para desenvolver TPCwelding por algum tempo, tendo iniciado experiências com soldagem por resistência de termoplásticos na década de 1990. A empresa tem usado processos de soldagem termoplástica para unir nervuras e revestimentos internos de ponta. No JEC World 2019, a empresa apresentou um painel de fuselagem composto termoplástico controlado por área fabricado com fita UD APC (PEKK-FC) da Solvay. O painel é o resultado de um projeto conjunto de P&D entre a GKN Fokker e a Gulfstream Aerospace (Savannah, Geórgia, EUA). A peça é declaradamente o painel composto de mais baixo custo, devido ao endurecimento simples da ortogrelha “com junta de topo” e estruturas totalmente soldadas.
“Com termoplásticos, uma ortogrelha pode ser bastante simplificada pela‘ junção de topo ’da grade à pele”, explica Arnt Offringa, chefe de Desenvolvimento de Tecnologia de Compósitos Termoplásticos da GKN Fokker. “A grade agora é composta apenas de pré-formas simples e planas que são co-consolidadas com o laminado de pele para formar uma casca integralmente rígida de baixo custo. As molduras são soldadas à grade. Essas soldas são carregadas em cisalhamento, tornando viável deixar de fora todos os parafusos. ”
Embora estruturas termoplásticas soldadas tenham sido usadas em aeródromos por algum tempo, a tecnologia agora parece bem posicionada para uso em estruturas primárias. Mike Favaloro acredita que os fabricantes aeroespaciais e OEMs estão ganhando confiança com os TPCs, especialmente com o controle de processo. “Em um horizonte de 10 anos, começaremos a vê-lo adotado muito mais”, diz ele.
Leia mais sobre tecnologia de soldagem no artigo de Ginger Gardiner "Soldando compostos termoplásticos".
Sem ferramentas
Outra inovação no horizonte que pode permitir a aceleração do uso de termoplásticos é a fabricação de compósitos sem ferramentas. O conceito, como o nome indica, dispensa a necessidade de moldes e ferramentais tradicionais, substituindo-os pela robótica.
O fabricante aeroespacial General Atomics Aeronautical Systems Inc. (GA-ASI, San Diego, Califórnia, EUA) está desenvolvendo um tal processo para a fabricação de estruturas compostas termoplásticas. A Composite Automation LLC (Cape Coral, Flórida, EUA), utilizando equipamento Mikrosam (Prilep, Macedônia), trabalhou com a GA-ASI para desenvolver a automação. O processo usa dois robôs de 6 eixos trabalhando juntos para colocar fita termoplástica. Um robô consiste em um sistema de colocação de fita unidirecional padrão que fornece aquecimento a laser para realizar a consolidação in-situ do material termoplástico. O segundo robô fornece suporte, trabalhando em frente à camada de fita automatizada (ATL) para fornecer uma superfície de ferramenta móvel contra a qual o ATL coloca a fita. (Para saber mais, consulte “Processo de compósitos termoplásticos sem ferramentas de desenvolvimento geral Atomics Aeronautical.”)
Reciclagem
Outro benefício dos TPCs é a reciclabilidade. Como os polímeros termoplásticos podem ser fundidos e remodelados, várias empresas estão buscando os TPCs como uma forma de reutilizar materiais.
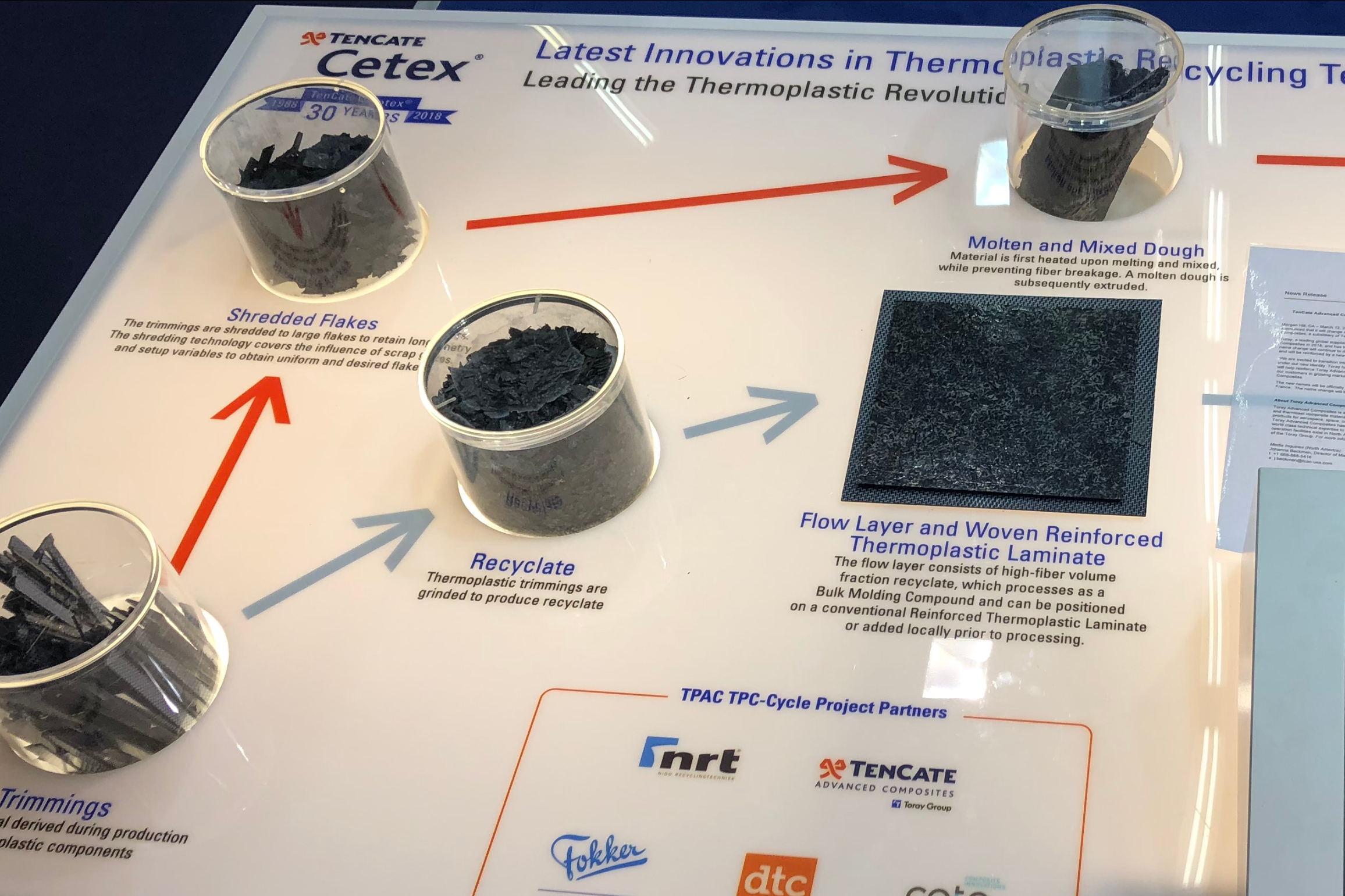
Uma dessas iniciativas de reciclagem, operada pelo Thermoplastic CompositesApplication Center (TPAC, Enschede, Holanda) e o Thermoplastic Composites Research Center (TPRC, Enschede, Holanda), está focada na reutilização de sucata de produção do processamento de TPC, da coleta à trituração e reprocessamento até a aplicação. O projeto TPC-Cycle está trabalhando para desenvolver uma rota de reciclagem econômica e ecologicamente correta para mercados de alto volume e alto padrão - ao mesmo tempo em que produz um material que retém o máximo possível das propriedades mecânicas dos materiais termoplásticos originais. O projeto possui tempos de ciclo curtos, fabricação em formato líquido e permite a produção de formas complexas.
A colaboração inclui vários parceiros industriais na cadeia de valor, desde material, fabricação, design e aplicação, incluindo GKN Fokker, Toray Advanced Composites, Cato Composite Innovations (Rheden, Holanda), Dutch Thermoplastic Components (Almere, Holanda) e Nido RecyclingTechniek (Nijverdal , Países Baixos).
O material certo para o trabalho certo
Portanto, em meio ao barulho de empolgação com relação a esses materiais, a questão que se coloca é:os TPCs chegaram? Os fornecedores aeroespaciais de nível 1 e nível 2 estão investindo em termoplásticos. Há mais interesse e investimento de fornecedores de pequeno e médio porte. Consórcios como o IRG CosiMo estão olhando para os mercados aeroespacial e automotivo para avançar nas tecnologias de processo para atingir a produção de alto volume.
“É o Trifecta”, diz Mead, “os OEMs estão investindo, o pessoal do maquinário está investindo, o material certo foi desenvolvido. Todos os componentes da receita estão se encaixando. ”
Em um escopo mais amplo, o que tudo isso significa quando se trata de materiais usados em aeronaves de próxima geração? Afinal, existem inúmeros materiais competindo por um lugar na aeronave do futuro, e a inovação não está diminuindo - os compósitos termofixos continuam a evoluir; o alumínio e o titânio continuarão a desempenhar um papel importante.
“À medida que os airframers desenvolvem uma base de qualificação com termoplásticos, eles agora têm uma escolha”, diz Unger. “E essa escolha será baseada na seleção do material certo para uma determinada aplicação que atenda aos requisitos de taxa de produção e custo para o componente ou estrutura em questão. Ao olhar para a aviação comercial daqui para frente, o que eu acredito que você verá os pilotos fazendo é usar o material certo para o trabalho certo. Se um material permitir a estrutura mais apropriada pelo menor custo e atender aos requisitos de taxa de construção do programa, ele ganhará seu lugar no avião. ”
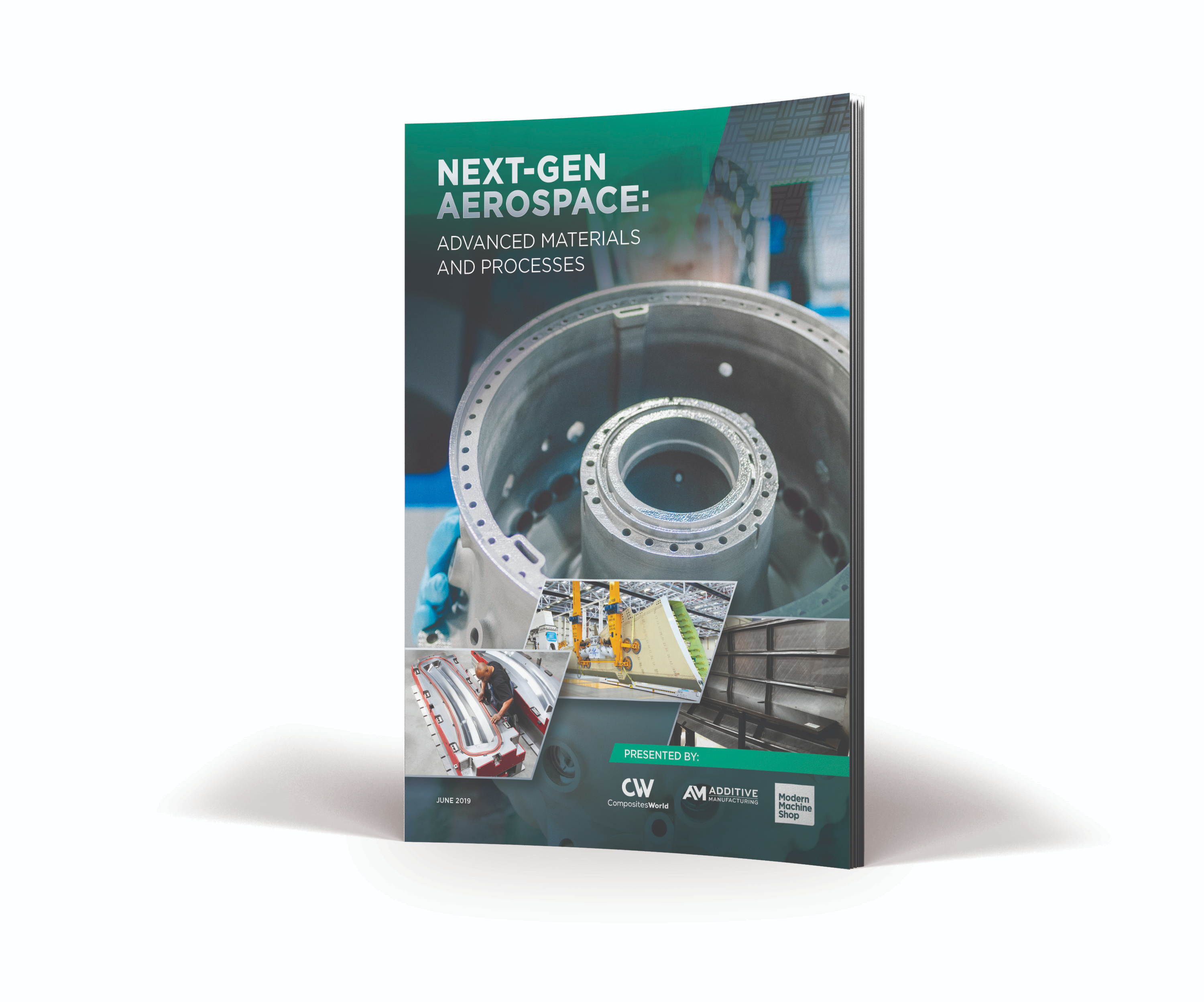
A próxima geração de fabricação aeroespacial
Com o setor de aviação comercial projetado para dobrar nos próximos 20 anos, atender à demanda por aeronaves de passageiros e carga exigirá novas tecnologias e taxas de fabricação sem precedentes.
Saiba mais sobre os materiais e processos que moldarão as aeronaves de última geração em uma coleção de histórias de CompositesWorld, Modern Machine Shop e Fabricação de aditivos , disponível para ler ou baixar gratuitamente . Venha aqui.
Resina
- Covestro Aumenta o Investimento em Compósitos Termoplásticos
- Compostos termoplásticos na Oribi Composites:CW Trending, episódio 4
- Resolução de problemas de termoformação de compósitos termoplásticos
- Compostos termoplásticos:Suporte de pára-choque estrutural
- Toray Advanced Composites expande as capacidades de compósitos termoplásticos
- ACMA lança programa da Conferência de Compostos Termoplásticos em 2020
- Porta termoplástica a primeira para compósitos automotivos
- Compostos termoplásticos:Vista panorâmica
- Visualização do CAMX 2018:TenCate Advanced Composites
- Compósitos termoplásticos de soldagem