Entrevista com especialista:Arevo Co-Founder Wiener Mondesir na produção da primeira armação de bicicleta de fibra de carbono impressa em 3D do mundo

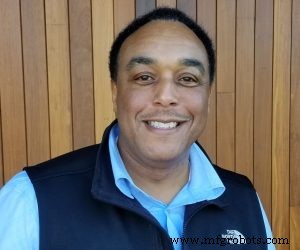
A Arevo, empresa sediada no Vale do Silício, ganhou as manchetes em 2018 após revelar o que chamou de o primeiro quadro de bicicleta de fibra de carbono impresso em 3D do mundo. O caso de uso apresentou os recursos exclusivos da tecnologia de impressão 3D composta de propriedade da Arevo, que combina robótica e software para produzir peças compostas personalizadas e leves.
Desde então, a Arevo fez parceria com o fabricante de bicicletas, Franco Bicycles, para fornecer quadros monobloco de fibra de carbono impressos em 3D para uma nova marca de eBikes.
Esta semana, temos o prazer de falar com Wiener Mondesir, cofundador e diretor de tecnologia da Arevo, sobre a tecnologia proprietária da Arevo, os benefícios da impressão 3D composta e o que o futuro reserva para a fabricação de compostos.
Você poderia nos falar um pouco sobre o Arevo?
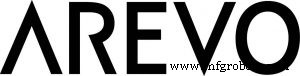
Quando você olha para a indústria de compósitos, a fabricação de peças de compósitos representa uma grande oportunidade. A fibra de carbono pode ser mais forte do que alguns metais e é leve, por isso tem um amplo apelo em muitos setores.
Mas por uma série de razões, a adoção da fabricação de compósitos foi sufocada, então a oportunidade não está sendo explorada. Uma razão para isso é por causa dos processos de manufatura ineficientes.
A manufatura de compósitos é atualmente muito intensiva em mão de obra, recursos e capital, o que significa que não é realmente escalável para grandes volumes. Os setores que realmente conseguiram capitalizar na fabricação de compostos foram aqueles que podiam bancar o caso de negócios, como os setores aeroespacial e automotivo de ponta.
Além disso, há longos ciclos de projeto devido ao software inadequado e à simulação ineficiente. Outro motivo frequentemente esquecido é a falta de compreensão dos compósitos em outras indústrias.
A Arevo está tratando de todas essas questões. Estamos repensando a fabricação de compósitos usando o que chamamos de digitalização de compósitos.
Decidimos resolver este problema desenvolvendo um software que elimina a lacuna de conhecimento.
Você começa com um modelo 3D e nosso software faz a análise, chega com a orientação final ideal, a quantidade certa de material e produz instruções para fabricar a peça usando nossa tecnologia de fabricação.
Vamos pegar uma teia de aranha como exemplo. Quando você olha para uma teia de aranha, é uma estrutura 3D que tem a quantidade certa de material para seu propósito.
A fibra, ou a seda no caso da teia de aranha, usa apenas a quantidade certa de material e está perfeitamente posicionada onde precisa estar. Tiramos inspiração disso quando criamos uma maneira otimizada de imprimir peças compostas em 3D.
Portanto, essa é a nossa missão como empresa:possibilitar a fabricação de compósitos em escala.
Quais são os benefícios da impressão 3D composta?
Os compostos de fibra de carbono oferecem uma ótima relação resistência-peso, então você obtém um material realmente forte, mas leve.
Quando você olha para a tendência na impressão 3D, muitas técnicas diferentes usam estruturas reticuladas em metal leve, que é naturalmente denso e pesado.
Mas se você começar com um material leve e forte como a fibra de carbono desde o início, você chegará ao resultado final muito mais rápido. Portanto, os compósitos são muito mais adequados para certas aplicações do que até mesmo os tipos de produtos com estrutura reticulada de metal, que têm uma ótima aparência, mas não necessariamente atendem ao propósito.
A complicação com a fibra de carbono é que ela é anisotrópica, o que significa que é forte em uma direção. Isso é o que torna um pouco mais difícil de lidar sem ferramentas especializadas.
Na Arevo, desenvolvemos o conjunto de ferramentas para designers, então você não precisa ter um PhD para fabricar com compósitos de fibra de carbono. Nosso software cuida disso.
O quadro da sua bicicleta impresso em 3D de fibra de carbono foi amplamente divulgado quando foi revelado. Qual foi o processo de criação do quadro da bicicleta, do design à produção?
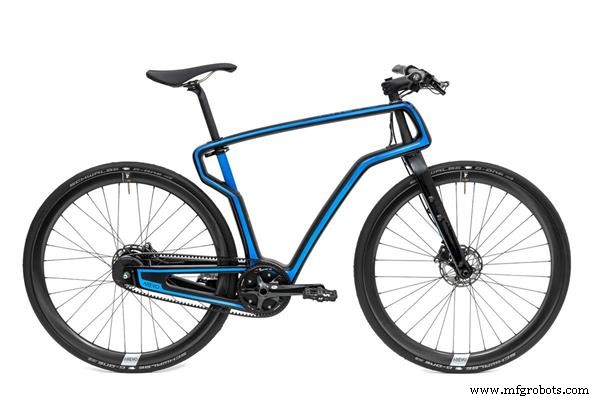
Essa aplicação particular começou como uma forma de mostrar o que é possível com a tecnologia.
O quadro de uma bicicleta é muito acessível, mas tem um formato muito complexo e é uma estrutura grande que requer carga, torção e capacidade de suportar peso. Portanto, foi o aplicativo perfeito para demonstrar nossa tecnologia.
Se você der um passo para trás e olhar para as bicicletas compostas tradicionais de hoje, elas vão desde um design até uma iteração de prototipagem e, em seguida, todo o caminho até a produção. Esse processo leva cerca de um ano. Além disso, as bicicletas compostas tradicionais são fabricadas usando um processo muito manual. As armações são unidas por 20 a 30 peças e até 40 pessoas tocam cada uma. É um processo muito trabalhoso e você acaba com um produto de custo muito alto que não é necessariamente escalável.
Os designs também são muito semelhantes, então você não pode obter muitas personalizações.
Com nossa tecnologia, encurtamos esse processo de quase um ano para apenas alguns dias. O software da Arevo pega um design CAD e faz um design generativo isotrópico na estrutura que um designer apresenta. Ele também otimiza a orientação e faz uma análise preditiva.
A próxima etapa ocorre em nossa fábrica. Construímos uma fábrica na Califórnia que pode produzir quadros de bicicletas personalizados sob demanda, utilizando nossa robótica e tecnologia de deposição.
Quando lançamos a bicicleta, fomos procurados por todos os grandes fabricantes de bicicletas porque eles estavam interessados na liberdade de design que a tecnologia oferecia.
Quando você olha para o design do quadro da bicicleta Arevo, ele realmente se afasta do design convencional da bicicleta. Ela não tem um suporte de assento, por exemplo, e é muito diferente de uma bicicleta tradicional.
A bicicleta da Arevo é uma bicicleta monobloco feita com fibras de carbono muito fortes orientadas na orientação ideal no espaço 3D. Conseguimos obter o design em uma estrutura monobloco que o torna muito sólido e leve.
Podemos ajustar o percurso real da bicicleta usando ferramentas de software. Podemos ajustar a rigidez em certas regiões da bicicleta e permitir um passeio ainda mais flexível, se desejar, sob demanda. Com bicicletas tradicionais, você está essencialmente sempre tentando fazer o mesmo quadro repetidamente.
Um quadro impresso em 3D, por outro lado, abre um novo modelo de negócio para uma indústria acostumada ao longo processo de introdução de uma nova bicicleta no mercado. Hoje, há cerca de um milhão de quadros compostos produzidos por ano. E agora você pode realmente introduzir quadros muito personalizados sob demanda com nossa tecnologia.
Nosso objetivo é continuar a criar novos aplicativos que aproveitem esta capacidade.
A abordagem personalizada para a produção é um modelo de negócios escalonável?
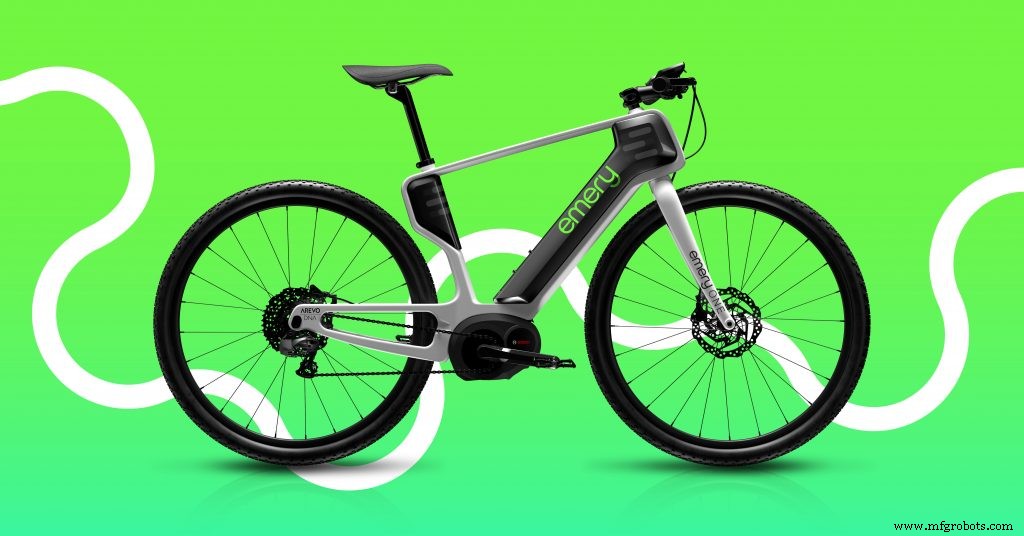
Há um grande valor na personalização quando se trata de bicicletas. Cada pessoa é única. Você fica mais cansado quando não está andando de bicicleta projetada, configurada ou ajustada para o seu quadro. Portanto, uma bicicleta é, na verdade, um bom veículo para demonstrar o valor da personalização.
Há toda uma tendência em torno da micromobilidade e da capacidade de andar por aí com um veículo muito conveniente. A bicicleta representa isso. Em muitos países diferentes, é uma forma dominante de transporte.
Quando você precisa de personalização para forma e função, você não pode fazer isso de uma forma de mercado de massa. Mas com nossa tecnologia, um consumidor pode projetar a moldura e nosso software pode garantir que a moldura que eles projetaram é estruturalmente sólida.
Então eles podem enviar isso para nossas células de impressão 3D para fazer aquela bicicleta sob demanda. Portanto, o processo desde o conceito até a produção é muito simplificado.
Que outros aplicativos você imagina com sua tecnologia?
Hoje estamos focados nas aplicações de bicicletas e mobilidade. Estas são aplicações que podem tirar proveito da proposta de valor que oferecemos, que é muito leve, com alta relação resistência / peso e produtos personalizados.
Quando você olha para todos os setores, é realmente importante melhorar o desempenho no setor esportivo, bem como nas indústrias automotiva, energética e aeroespacial.
Temos um monte de aplicativos diferentes nos quais estamos trabalhando, onde são necessários leveza, alto desempenho e alta personalização. E essas são as principais áreas onde nossa tecnologia pode ser usada.
Como a robótica se encaixa na sua tecnologia?
Quando você olha através da impressão 3D, a maior parte da impressão 3D é baseada em camadas e as camadas são depositadas nos planos X e Y. Quando você olha as propriedades das peças feitas com esse processo, elas tendem a sofrer na direção Z.
Nós usamos um robô de seis eixos totalmente articulado para depositar nossa fibra de carbono nas direções X, Y e Z. Eliminamos o problema de força Z que assola outras tecnologias baseadas em camadas porque somos capazes de estabelecer na direção Z. Essa é uma das capacidades únicas de nossa tecnologia de deposição. A robótica desempenha um grande papel nisso.
O segundo aspecto é a escala das peças que podem ser impressas. Hoje, a maioria dos sistemas é relegada a um determinado envelope de construção, o que significa que você só pode fazer peças de um determinado tamanho. Se você ultrapassar um determinado tamanho, a peça precisará ser cortada em submontagens para fazer uma estrutura maior.
Nossos robôs fornecem capacidade de envelope de construção infinita porque podemos colocar nossos robôs no pórtico para fazer peças aeroespaciais. Ao mesmo tempo, o mesmo robô pode fazer uma bicicleta. O alcance de nossos robôs é de quatro metros de altura. Essencialmente, é muito escalonável em termos de nos dar aquele envelope grande com impressão.
Como você descreveria o estado atual do mercado de impressão 3D composta? Quão avançada é a tecnologia?
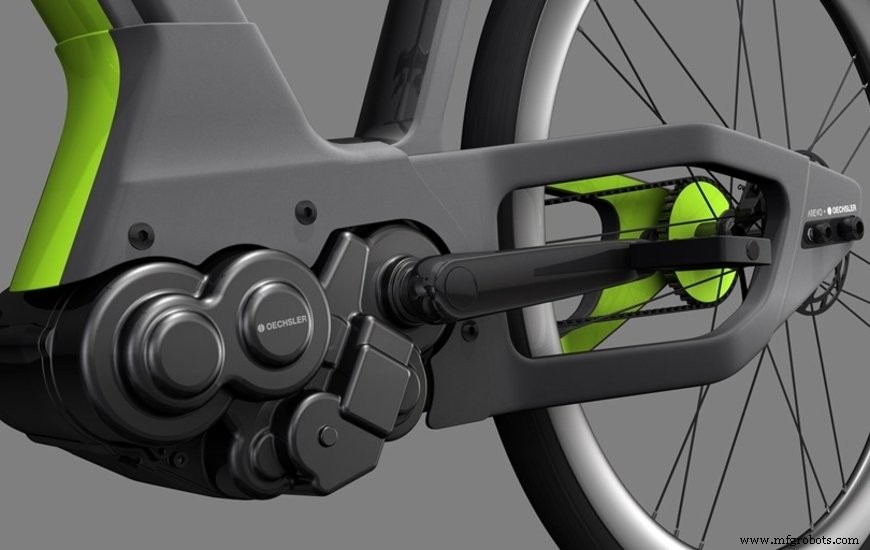
A indústria de compósitos já faz aditivos há algum tempo. Acontece que a complexidade das geometrias foi muito limitada ao que você poderia encaixar em um molde, como peças com uma curvatura muito pequena. Além disso, as camadas geralmente são dispostas manualmente, resultando em uma parte com complexidade bastante limitada.
Portanto, a impressão 3D composta já existe há algum tempo. Mas agora coisas como robótica automatizada ou sistemas mecatrônicos, que automatizam a colocação da fibra, permitem geometrias mais complexas.
Existem muitas empresas que adotam uma abordagem diferente para automatizar a fabricação de compósitos, desde diferentes tipos de sistemas de resina até diferentes casos de uso.
E isso é muito útil.
No geral, acho que o setor de impressão 3D composta está em um estado saudável, com a Arevo liderando o ataque.
Quais são alguns dos desafios que a indústria enfrenta, seja impressão 3D em geral ou impressão 3D composta especificamente?
Acho que os maiores desafios decorrem da falta de ferramentas de software disponíveis para explorar o que é possível com o aditivo. Você tem uma mentalidade de olhar para as técnicas de manufatura tradicionais e nós fomos educados com técnicas de manufatura tradicionais.
As pessoas geralmente começam com peças que foram feitas usando a maneira tradicional e querem forçar o ajuste de aditivo a essa peça, mas isso nem sempre corresponde.
Mas quando você realmente explora o que pode fazer com o aditivo, seja ele à base de metal, composto ou polímero, em termos de exclusividade e complexidade, você realmente precisa de ferramentas para guiá-lo através desse processo e informar os designers e engenheiros.
Como você vê a evolução do setor nos próximos cinco anos?
É muito encorajador. Desde o início da Arevo, sempre estivemos focados em peças de produção.
Quando você olha para a indústria hoje, é realmente encorajador ver que todos estão falando sobre peças de produção. Esse é o tema comum.
Daqui para frente, espero ver a indústria começar a falar sobre qualidade e escalabilidade também. Conforme você começa a fazer produtos, produzir em escala e com maior repetibilidade será o foco principal da indústria.
Garantir a qualidade das peças e processos é um grande ponto de discussão para a manufatura aditiva no momento. Qual é a abordagem da Arevo para isso?
Um dos principais avanços que a Arevo foi capaz de alcançar é nosso processo de deposição baseado em laser.
Além disso, empregamos algoritmos de aprendizado de máquina que são capazes de fazer inspeção in situ. Temos um conjunto de sensores e podemos fazer uma inspeção in situ em uma peça enquanto ela está sendo fabricada.
Isso nos permite obter um material impresso muito homogêneo com menos de 1% de vazios. Você pode fazer um corte transversal de uma peça e, ao examiná-la ao microscópio, pode observar um material impresso muito homogêneo.
Isso se traduz em peças de alta qualidade quando você vai para aplicações muito exigentes, como a aeroespacial. Este controle de qualidade in situ, combinado com nosso monitoramento de circuito fechado, é o que nos permite ter uma qualidade repetível e previsível.
O que os próximos 12 meses reservam para a Arevo?
Nos próximos 12 meses, estaremos focados na execução da manufatura. Desde que lançamos a bicicleta, temos mais demanda do que somos capazes de atender. Nossa meta para o próximo ano é continuar a lançar novos aplicativos, mas principalmente aumentar nossa capacidade para atender à demanda atual.
Para saber mais sobre o Arevo, visite: https://arevo.com/
impressao 3D
- Entrevista com especialista:Nanoe CEO Guillaume de Calan sobre o futuro da impressão 3D em cerâmica
- Entrevista com especialista:Ultimaker Presidente John Kawola sobre o futuro da impressão 3D
- Entrevista com especialista:Nano Dimension Co-Fundador Simon Fried sobre a ascensão da impressão 3D para eletrônicos
- Entrevista com especialista:Co-fundador da Carbon, Philip DeSimone, sobre como avançar para a produção de alto volume com impressão 3D
- Entrevista com especialista:Jabil’s Rush LaSelle sobre o futuro da fabricação de aditivos
- Entrevista com especialista:Greg Paulsen da Xometry sobre a ascensão da manufatura como modelo de negócios de serviços
- Entrevista com especialista:VP de parcerias de tecnologia da VELO3D na expansão das capacidades de impressão 3D em metal
- Entrevista com especialista:John Barnes, fundador do The Barnes Group Advisors, sobre o futuro da fabricação de aditivos
- Apresentando o primeiro smartphone de fibra de carbono do mundo
- Toray cria a primeira fibra de carbono porosa do mundo com estrutura de poro contínua nanométrica