Molde de fundição sob pressão:um guia detalhado de ferramentas para moldes de fundição sob pressão
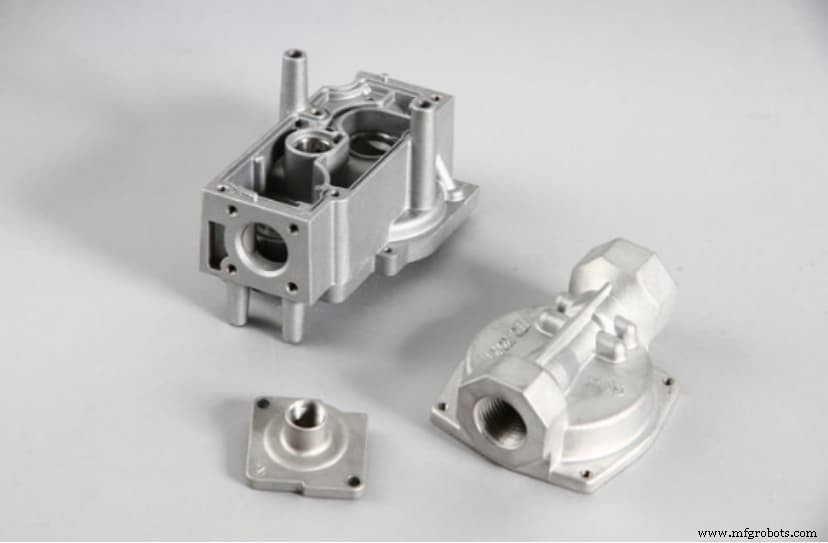
A fundição sob pressão é um processo significativo para aplicações em várias indústrias. Um componente essencial do processo de fundição sob pressão é o molde de fundição sob pressão. A forma e as características do molde afetam as características do produto final.
Portanto, há uma necessidade de entender o projeto do molde de fundição. Isso ajudará você a projetar e escolher o molde certo para seus projetos de fundição. Além disso, você pode ter certeza de que o produto final atenderá aos requisitos exclusivos de fabricação.
Assim, este artigo lhe dará uma visão detalhada dos diferentes tipos de ferramentas de fundição. Você também aprenderia como projetar um molde e os fatores que você precisa considerar ao fazer ferramentas de fundição.
Por que o molde é importante para fundição sob pressão?
O design do molde fundido desempenha um papel vital na forma da peça. Além disso, afeta a qualidade, uniformidade e configuração dos componentes do processo de fundição .
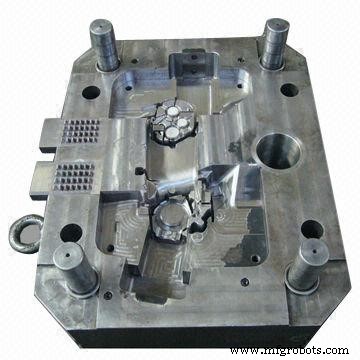
Especificações erradas podem resultar em corrosão do material ou da ferramenta. No entanto, um projeto de molde adequado pode aumentar o tempo e a eficiência do produto. Em última análise, a qualidade da estrutura do molde determinará se a produção prosseguirá sem problemas e as peças fundidas serão da melhor qualidade.
Além disso, o design da ferramenta de fundição reflete essencialmente os diferentes fatores que podem ocorrer durante a produção. Assim, você deve analisar a estrutura de uma peça fundida durante o projeto. Também é essencial dominar as condições de arquivamento, implementar parâmetros críticos do processo e considerar outros efeitos econômicos. Isso garantirá que as ferramentas de fundição possam atender aos requisitos essenciais de produção.
Molde de fundição Componentes
A compreensão do molde de fundição sob pressão começa com o conhecimento da estrutura do molde. Os componentes essenciais do molde fundido incluem:
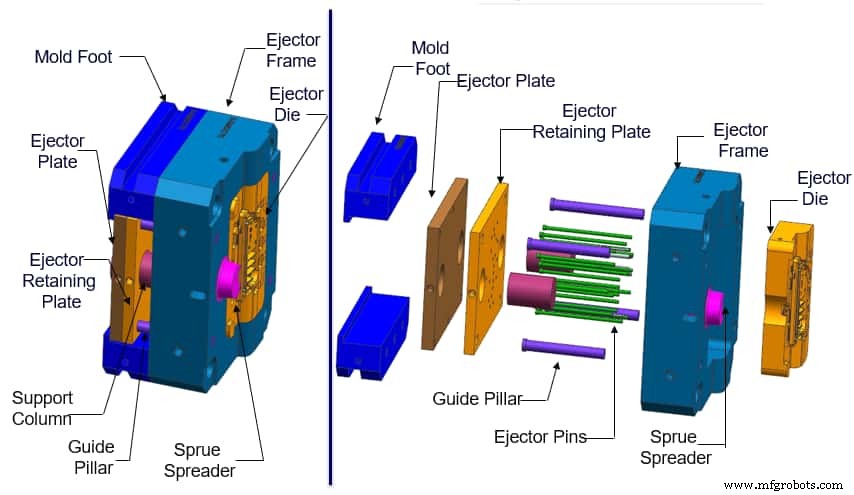
· Sistema de Moldagem
Isso inclui a cavidade, núcleo, inserções, controles deslizantes e pinos de inserção. A cavidade de fundição sob pressão determina a forma de fundição à medida que o núcleo móvel se fecha.
· Sistema de base do molde
Os componentes primários do sistema de base do molde fundido são placas e armações de aço. Este sistema combina diferentes partes do molde e permite a instalação do molde na máquina de fundição.
· Sistema de ejeção
Este sistema funciona para ejetar peças do molde. Essas peças incluem peças de ejeção, retorno e guia.
· Sistema Executor
O sistema do corredor se conecta com a peça de fundição e a câmara de pressão. Assim, ele guia o material metálico na cavidade da matriz em uma direção específica. Este sistema impacta diretamente na pressão e velocidade do metal fundido. Os componentes do sistema de corrediças são uma corrediça, um sprue, uma comporta interna, etc.
· Sistema de estouro
Este canal remove o ar da câmara de pressão. Geralmente, os componentes primários são ranhuras de transbordamento e ranhuras de ventilação. No entanto, os fabricantes instalam tampões de ventilação nas cavidades profundas para melhorar as condições de ventilação.
· Outros
Outros componentes do molde de fundição incluem peças de posicionamento para colocar as peças corretamente no molde. Além disso, existem pinos e parafusos para fins de fixação.
Tipos de moldes de fundição
Existem vários tipos de ferramentas de fundição sob pressão e têm funções diferentes dependendo dos requisitos. Eles incluem:
Modelos de prototipagem
Um investimento significativo em fundição sob pressão é uma matriz feita sob medida com todos os recursos. Portanto, um molde de protótipo ajuda a fazer um grande número de moldes para testar as diferentes peças. As estratégias de prototipagem são fundição por gravidade, saídas de porco usinadas e peças impressas em 3D. No entanto, eles envolvem trade-offs em propriedades, tolerância e design.
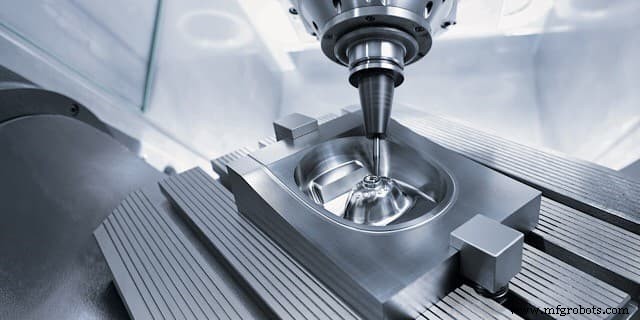
Um protótipo de fundição de alta pressão será sua melhor opção sempre que você precisar da mesma liga, propriedades, processo e geometria para produção. As matrizes de prototipagem podem utilizar aços ferramenta pré-endurecidos e não revestidos e componentes padronizados. Como resultado, eles podem ser produzidos em tempos curtos e a um custo reduzido.
Ao contrário de outras técnicas de produção, esses moldes também utilizam técnicas de ejeção ou resfriamento menos eficientes. Portanto, você deve observar que a ferramenta não durará muito e a matriz não será tão eficiente quanto uma produção. No entanto, isso não será um problema se você precisar apenas de uma pequena quantidade de elenco.
Matrizes para ferramentas rápidas
O ferramental rápido refere-se a pastilhas e matrizes produzidas usando métodos com prazos de entrega mais curtos do que os métodos convencionais. Ao contrário da usinagem de desbaste e tratamento térmico, os métodos de ferramentas rápidas são sinterização seletiva a laser, deposição direta de metal, modelagem de rede projetada a laser, etc.
Portanto, você esperaria que a criação dessas ferramentas de fundição sob pressão fosse muito mais rápida. Os fabricantes podem usar essas matrizes como matrizes de prototipagem ou como matrizes de produção. A escolha mais viável dependerá dos requisitos de volume de produção.
Morres de produção
Esses moldes são os tipos mais comuns de moldes de fundição. As matrizes de produção são essenciais quando todo o design foi finalizado e está pronto para ser lançado em um produto autêntico.
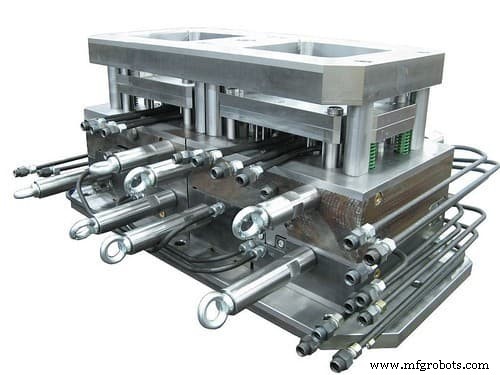
Nós podemos ter:
- Fórmulas de cavidade única sem lâminas
- Matrizes de múltiplas cavidades com várias opções de deslizamento
O material da cavidade é aço de alta qualidade e muitas vezes é retido em um bloco de suporte. O design das matrizes de produção garante que elas tenham dimensões críticas. Assim, você pode ter certeza de que eles permitem as especificações de usinagem necessárias.
Unidade morre
O molde unitário é um tipo especial de molde de fundição sob pressão. Um suporte de unidade de fundição mantém as matrizes da unidade ou a cavidade de propriedade do cliente dentro da cavidade intacta. Podemos ter cotistas simples ou duplos. Exemplos típicos de tamanhos de blocos de cavidades que as matrizes suportam são 8 x 10, 10 x 12, 12 x 15 e 15 x 18 (todos em polegadas).
As matrizes unitárias empregam peças genéricas utilizadas para componentes menos complexos e de baixo volume. Uma matriz personalizada é mais eficaz para peças de maior volume com geometria complexa. Essas matrizes são projetadas especificamente para uma peça, proporcionando o máximo controle e eficiência.
Matrizes de guarnição
A CMW usa matrizes de corte para produção de alto volume e as matrizes de produção. A matriz de corte apara o flash, o canal e o transbordamento da peça imediatamente após a conclusão da fundição. Algumas matrizes de corte precisam de movimentos ou cames operados hidraulicamente, enquanto outras exigem funções de abertura e fechamento para remover o flash de forma eficaz.
A geometria da peça impede totalmente a remoção do flash com uma matriz de corte. Portanto, as estratégias de remoção de flash manual e o serviço de corte personalizado são uma opção ideal nessa situação.
Precisa de peças de aparência moderna com melhor resistência e maior durabilidade? Escolha o processo de fundição sob pressão que requer ferramentas para produzir suas peças de uso final. E a boa notícia é que os serviços de fundição sob pressão da RapidDirect fornecem uma solução completa.
Processo de projeto de molde para fundição
Esta seção descreverá o processo envolvido no projeto de um molde para projetos de fundição de alta pressão. O processo tem cinco grandes categorias:
Fase preliminar
Antes de projetar o molde, é importante verificar a fabricação da peça com tecnologia de fundição sob pressão. Esta fase envolve julgar a praticabilidade do produto do ponto de vista geométrico e dimensional.
Vista dimensional :Existe a necessidade de conhecer a dimensão da peça e o número de cavidades necessárias para cada peça fundida. Isso ajudará a conhecer a força de abertura e o volume da fundição. O conhecimento desses dados facilitará muito os estudos de viabilidade.
Vista geométrica :A geometria das peças inclui o desenho da linha de partição. A linha de separação divide o molde de fundição em dois, permitindo fácil abertura do molde e ejeção do fundido. Além disso, a superfície das peças depende de sua posição das linhas de partição. Consequentemente, as superfícies devem ser projetadas na direção da abertura do molde.
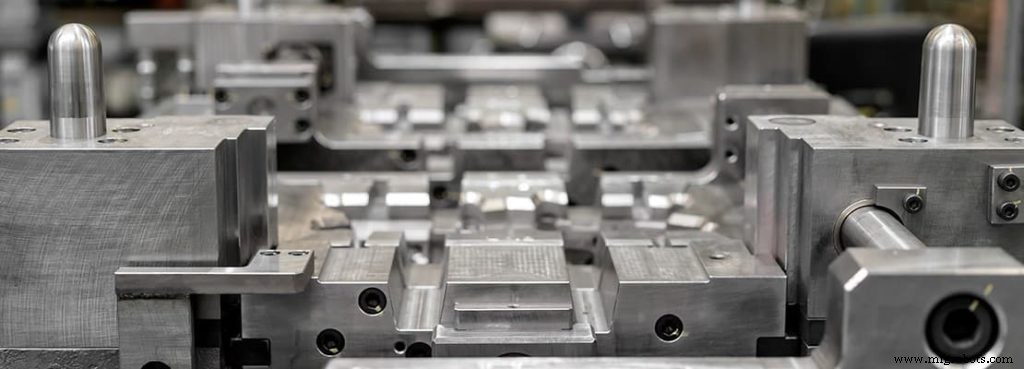
A tolerância geométrica das cotações encontradas no modelo 2D pode ser bastante difícil de produzir devido ao encolhimento causado pelo resfriamento do metal. Quanto maior o número de cotações, mais difícil é obter o mesmo valor no casting. Portanto, você pode prosseguir com o projeto do molde fundido assim que confirmar a fabricação da peça.
Número de cavidades
Para saber o número de cavidades, você deve considerar o número de peças a serem produzidas, a orientação da cavidade e o tempo de ciclo hipotético. Dessa forma, você pode decidir a melhor opção entre um molde multicavidade ou um molde de cavidade única.
Ao optar por um molde multicavidade, lembre-se de que, além do aumento das fases de ejeção e da complexidade do enchimento, o processo de produção pode ser afetado pela dimensão da cavidade e disposição do produto.
Área de projeção
A área de projeção é a superfície obtida a partir da projeção de cavidades no plano. É perpendicular à direção da abertura do molde. A área de projeção é um componente vital da fase de projeto. Relaciona a força de abertura do metal fundido com as paredes da matriz. Como resultado, a intensidade da força dependerá da orientação da dimensão da forma. Uma força forte causará um transbordamento de material, resultando na formação de rebarbas.
Portanto, você precisa estimar as forças produzidas pelo metal fundido para evitar esse defeito de fundição. A força é o produto da pressão específica da máquina, área de projeção e fatores de segurança pré-definidos. O fator oferece uma margem mais ampla para ajudar a combater a pressão máxima após o enchimento. Muitas pessoas se referem a ele como um golpe de aríete.
A máquina transfere a força dinâmica e estática no final do processo. Assim, há a produção de um pico de pressão que a força da máquina de fechamento deve absorver. Esta força de fechamento depende da dimensão do curso e do modelo da prensa.
Volume e forma do dado
O volume e a forma da matriz são essenciais para o projeto do molde. Além do volume desejado, considere que as peças grandes encolherão devido ao maior tempo de resfriamento, aumentando a taxa de retração. Portanto, há a necessidade de dimensionar as cavidades do molde de acordo.
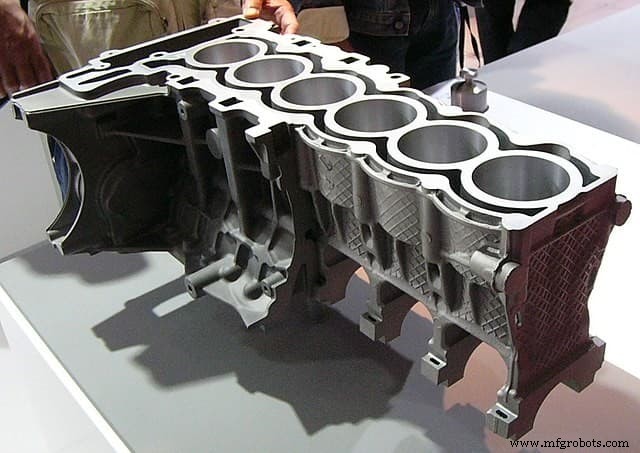
Além disso, é aconselhável considerar diferentes variáveis que afetam o tamanho final do molde. Os fatores mais importantes a serem considerados são:
Canais de injeção :O tamanho dos canais de injeção varia com o número de cavidades e a posição das comportas e peças. A forma dos canais de injeção deve atender a alguns requisitos de dinâmica de fluidos. Por exemplo, os fabricantes diminuem a seção para aderir corretamente à parede do molde ao se mover na direção do metal fundido. Devido ao encolhimento, há um fluxo acelerado e eles se desprendem das paredes. Uma camada externa mais suave evitará turbulência, aprisionamento de ar e outros defeitos.
Tipo de fechamento de matriz :O fechamento de molde aberto/fechado é o fechamento de molde mais simples. É melhor para produtos com formas simples e limpas que podem ser facilmente ejetadas. No entanto, não é a melhor opção para peças com geometria complexa. Produtos com geometria complexa seriam difíceis de remover, então o fabricante precisa adicionar ao tamanho geral da matriz.
Presença de estouros :Overflows são pequenos poços projetados em partes estratégicas do molde. Eles são importantes na coleta dos primeiros tiros de metal porque geralmente é mais frio do que os seguintes. Como resultado, você pode evitar lapsos frios e outros defeitos estéticos semelhantes. Além disso, os transbordamentos servem como fonte de calor, aumentando a temperatura da matriz em áreas críticas para a fundição final.
Simulação por meio de modos semi-empíricos
Após a conclusão do estágio inicial de projeto, o próximo estágio é a simulação do preenchimento do molde usando modos semi-empíricos. A simulação auxilia no cálculo da modalidade de preenchimento do molde. Além disso, a modalidade depende da função da peça fundida e do processo de enchimento. Para peças com estruturas complexas, é melhor induzir compacidade e resistência mecânica. Enquanto isso, para peças estéticas, o acabamento da superfície deve ser de primeira qualidade.
As características podem ser alteradas variando o tempo de enchimento. Quanto mais rápido o preenchimento, maior a qualidade da superfície, enquanto o preenchimento mais longo impactará mais a resistência dos componentes. Depois que a análise estiver concluída, é mais fácil perceber se haverá algum problema de elenco.
O projeto do molde de fundição de alumínio começa com a análise da fabricação, depois calcula as forças e verifica os canais de injeção. A otimização e o design desses canais são feitos através de simulação para conhecer o modo de arquivamento e detectar qualquer problema. Após a conclusão bem-sucedida desta etapa, você pode passar para a produção do molde projetado.
Factors to Consider for Making Perfect Die Casting Tooling
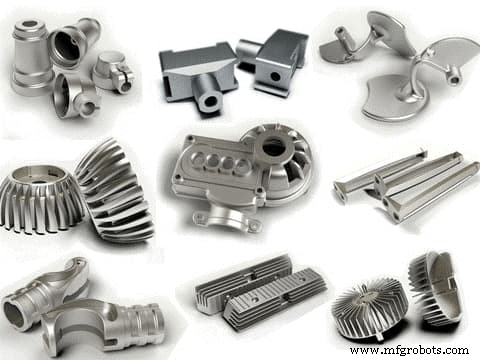
Before making die cast tooling, there are some things to look out for to guide in die cast tool design. Eles incluem:
Die Draft
The draft is the degree to which you can tamper with a mold core. You need a precise draft to remove the casting from the die safely. However, the draft is not constant, varying according to the angle of the wall. Thus, characteristics like the type of molten alloy used, the mold’s depth, and the mold’s shape can affect the whole process.
Another factor that can affect drafts is mold geometry. Generally, untapped holes need tapping because of the risk of shrinkage. Likewise, inner walls need more drafting than outer walls because inner walls tend to shrink.
Fillets
A Fillet is a concave junction that helps to smoothen an angled surface. A curved surface disturbs the casting process, so folds have fillets to produce a honed edge and limit the risk of production errors. Although there is an exception to the parting lines, you can add fillets to any part of the mold.
The fillet will increase the lifespan of the tool. To allow for continuity of smoothness, make a constant-radius fillet. Furthermore, tools that have a deep inside will need larger fillets.
Parting Lines
Parting lines, also known as parting surfaces, join various mold sections together. If the parting line is deformed due to work strain or it is wrongly positioned, materials can pass through the space between the mold pieces. This may lead to excessive and non-uniform seaming.
Bosses
Bosses are die-cast knobs that serve as stand-offs or mounting points in die cast tooling. Manufacturing industries usually add a hole to the internal structure of the boss to make sure the walls have a uniform thickness. It is challenging to fill bosses with metal, and thus, ribbing and filleting are essential to eliminate this issue.
Ribs
Die casting ribs to help improve the strength of the material for a product lacking the desired wall thickness. Selective rib placement improves fill capability and decreases product weight. It also reduces the occurrence of non-uniform thickness and stress cracking.
Holes and Windows
Having holes and windows in aluminum die casting mold allows for the creation of substantial drafts and ease in removing a completed mold. However, features like flashovers, cross feeders, and overflow are necessary to prevent material flow and unwanted cast in the holes. Holes and windows are among the essential things in design geometry. They affect the flow of molten metal and play a vital role in the product’s final quality.
Symbols
Manufacturers always add product logos or brand names in the mold design in die casting. Some casting has a date to differentiate a batch from another batch. Although symbols do not make the design process complex, they can add to the cost of production. A raised logo will require a different metal for every manufactured part, while an indented symbol will require a lesser amount of metal.
Wall Thickness
Die castings have a thin wall that has no fast and hard rules for maximum and minimum wall thickness. It is necessary to create a uniform wall thickness throughout the part. Uniformity will provide a smooth metal flow when filling and reduce distortion resulting from cooling and shrinkage. The main aim is for the die casting mould to fill before the solidification process to prevent cold shuts.
RapidDirect Chasing for Perfect Die Casting Parts
Understanding die casting mold design will make your die casting project easier. It will also help you save some time and money. However, you need the service of experts to get the right tool for the best results. RapidDirect offers the best precision die casting services for custom metal parts, providing quality tools, experts, and easy processes.
We have a wide range of materials, manufacturing processes, and surface finishing options for your die casting parts. Also, our experts offer you manufacturing suggestions to ensure you get the most effective solution. After placing the order for die casting parts, RapidDirect manufacturing partners would produce perfect die casting tooling to make the best die-casted parts. Upload your design file today and get an instant quote.
Perguntas frequentes
Is Die Casting Permanent Mold?For permanent mold, the metal flows directly into the cavity from the reservoir. The molten metal is forced into the cavity under high pressure in die casting.
What is the Mold in Die Casting?
The mold consists of two parts – the ejector and the stationary part. It contains the space forming the dimension and contour of the casting. The mold is also known as the die, and they are made from hardened steel to meet the shape requirement of the die casting part.
How are Molds Made for Die Casting?
Molds production involves passing a molten metal under high pressure into a metal die. The creation of the mold occurs in sections to allow for easy removal before placing them in machines such that one is removable and the other is fixed. The molten metal would pass through the cavity, and it will then solidify.
Tecnologia industrial
- O que é fundição com molde não expansível?
- O que é fundição em molde permanente?
- Como soldar ferro fundido:um guia completo
- Fundição x moldagem por injeção
- Controle de temperatura e influência durante o processo de fundição
- Noções básicas sobre fundição
- Guia de fundição de precisão
- O que é CI Casting?
- O que é uma máquina de fundição sob pressão?
- Entendendo a fundição