Coleta de dados da máquina:como ativar a fabricação orientada a dados
Uso de dados de máquina para impulsionar a otimização do chão de fábrica
Equipamentos de fabricação automatizados (máquinas CNC, se preferir) e as pessoas que operam esses equipamentos são o coração de qualquer operação de fabricação e representam uma das maiores despesas de capital para os fabricantes. Essas máquinas valem centenas de milhares de dólares e produzem mais dados do que qualquer outro setor, mas esses dados não estão sendo capturados ou analisados para melhorar a eficiência, apesar de todas as inovações em robótica e automação
Essas máquinas produzem centenas de pontos de dados a cada milissegundo, e a estrutura de dados é diferente para cada máquina. Isso torna incrivelmente importante padronizar os dados em todas as diferentes máquinas. No entanto, isso é difícil de fazer para certos equipamentos.
Não é tão simples como padronizar via OPC-UA ou MTConnect, porque apenas uma fração das máquinas suporta esses protocolos. Temos clientes que passaram ANOS tentando alavancar soluções DIY para coletar e transformar dados em modelos padrão de seus ativos, codificando manualmente os pontos de dados um por um, máquina por máquina. Isso geralmente resulta em anos de desenvolvimento e integração personalizados antes de obter o valor inicial, uma terrível alocação de recursos para os fabricantes.
Os insights e ações gerados a partir dos dados fornecem a base para que os fabricantes expandam seus negócios e se diferenciem competitivamente. Hoje, os fabricantes se encontram em diferentes estágios de uma jornada para aproveitar os dados e o segmento digital para otimizar e automatizar seus processos de negócios.
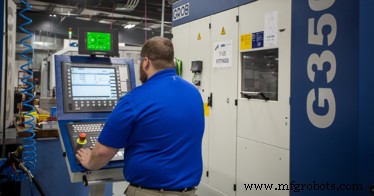
Na MachineMetrics, nos envolvemos com muitos fabricantes que descobrem no início de sua jornada que os dados de suas operações de fábrica são insuficientes e não confiáveis. Para métricas-chave, como a utilização de equipamentos, os fabricantes que não possuem sistemas automatizados para capturar dados transformados ou contextualizados de seus ativos de máquinas, muitas vezes acreditam erroneamente que estão funcionando em um nível satisfatório. Na realidade, nosso cliente médio de manufatura começa com uma utilização de 28%, significativamente menor do que o percebido. Estatísticas insatisfatórias semelhantes também são encontradas para OEE, tempo de inatividade e outras métricas importantes
A desvantagem da coleta manual de dados
A causa subjacente da percepção de desempenho abaixo da média, ainda que inflada, se origina com dados que são capturados manualmente. A captura manual de dados geralmente resulta em dados imprecisos, manipulados ou ausentes. É uma base instável que racha e cede quando são feitas tentativas de impulsionar a melhoria contínua e a inovação.
Por outro lado, dados precisos em tempo real capturados e transformados automaticamente dos ativos da máquina criam uma base sólida para capturar insights e gerar valor. Claro, isso é mais fácil dizer do que fazer.
Desafios da coleta de dados de máquina
Os fabricantes entendem o valor dos dados, e uma grande razão para a falta de coleta eficiente de dados e uso de dados na tomada de decisões é dupla:
- Os fabricantes são avessos à tecnologia ou continuam a usar práticas desatualizadas, o que resulta na coleta manual de dados e suas consequências associadas.
- Os fabricantes lutam com as muitas barreiras para construir uma infraestrutura de cultura e tecnologia que suporte com sucesso a coleta automatizada de dados em tempo real. Cobrimos esses desafios abaixo:
Variedade de dados
Não só existem muitos tipos distintos de equipamentos — Tornos, Fresadoras, Moldagem por Injeção de Plástico, Estampagem, Cortadores a Laser, Robótica, etc — dependendo dos mecanismos disponíveis para aquisição de dados desses sistemas, os pontos de dados podem ser muito diversos. Para fornecer ferramentas eficazes para analisar esses dados nesses sistemas distintos, os dados devem ser transformados em um modelo de dados comum. Não apenas cada controle de máquina tem seu próprio mecanismo para coletar dados, mas os pontos de dados também podem diferir pela família, marca e modelo da máquina que usa esse controle, bem como a versão do software em execução nesse controle.
Volume de dados
Equipamentos de fabricação, e equipamentos de fabricação discretos em particular, são muito complexos. Uma máquina é um grande sistema de componentes que trabalham em coordenação, resultando em centenas de pontos de dados distintos que mudam constantemente. Dependendo da aplicação, pode haver situações em que seja necessário capturar dados em taxas de 100Hz ou 100KHz. As plataformas que consomem essas informações devem analisar os dados em vários níveis dentro do sistema para evitar o envio e armazenamento de dados desnecessários quando apenas o resultado agregado ou calculado for suficiente. Esses sistemas devem ser capazes de realizar processamentos complexos onde for mais apropriado — tanto na borda quanto na nuvem.
A conexão direta ao controle de um CNC fornece um grande volume de dados de máquina em diversos pontos de dados.
Velocidade dos dados
Embora alguns sistemas possam fornecer valor com baixa fidelidade e alta latência, certos casos de uso de IoT exigem muito mais dados em tempo real para serem eficazes. A tecnologia de ponta é necessária para processar grandes volumes de dados, tomar decisões em milissegundos ou menos e agir para evitar danos à máquina ou à peça de trabalho. Mesmo os painéis que fornecem visibilidade do desempenho de um trabalho podem obter um enorme valor com baixas latências, chamando a atenção imediata para um processo que está ficando para trás ou falhando.
A fabricação discreta introduz ainda mais complexidade. Isso começa com a variabilidade das máquinas em fábricas discretas. Existem muitos fabricantes de máquinas diferentes e nenhuma fábrica possui apenas uma marca de máquina. As muitas máquinas diferentes também possuem diferentes sistemas de controle e protocolos de comunicação. Eles são de diferentes safras, variando de novos com controles modernos a 20-30 anos com capacidade de controle limitada. Conectar-se e coletar dados dos vários ativos da fábrica também é um empreendimento significativo, considerando que a maioria dessas máquinas nunca foi projetada para fornecer dados para o tipo de soluções analíticas holísticas, de fábrica ou corporativas que as empresas estão focadas em habilitar hoje .
Fontes de dados de usinagem
A beleza de uma operação conectada é que os fabricantes podem coletar e usar dados de várias fontes. Desde que os dados sejam contextualizados e relevantes, isso pode ajudar os gerentes a obter uma visibilidade mais profunda do status e do desempenho do chão de fábrica, ajudando até mesmo a preencher lacunas e adicionar contexto aos dados existentes.
Ferramentas de máquina
Como a fonte mais valiosa de dados de produção, a máquina-ferramenta fornece um fluxo de dados que é contextualizado pelo MachineMetrics e usado para painéis de produção, relatórios e notificações em tempo real. As partes interessadas podem ser notificadas instantaneamente sobre eventos de tempo de inatividade da máquina e ver quando a produção está atrasada com acesso aos dados da máquina que incluem status da máquina, alarmes, substituições, cargas, velocidades e alimentações.
Sistemas conectados
Para preencher lacunas nos dados de produção e adicionar camadas adicionais de contexto, pode ser útil compartilhar dados entre os diferentes sistemas em um ambiente de fabricação, como ERP, MES, CMMS, CAM etc.
A MachineMetrics possui interfaces de programação de aplicativos (APIs) que podem extrair informações de fontes externas. Essa combinação de dados operacionais e de máquina podem ser aproveitados juntos para gerar insights ou impulsionar a automação. Por exemplo, dados de máquina que indicam uma falha podem acionar automaticamente uma ordem de serviço em um CMMS.
Operadores
A Interface do Operador MachineMetrics, que reside em cada máquina, fornece uma ferramenta de comunicação para os operadores adicionarem contexto aos dados da máquina. Esta é uma camada de dados essencial, pois ajuda a explicar o “porquê” por trás de paradas de máquinas, alarmes, peças de sucata, etc.
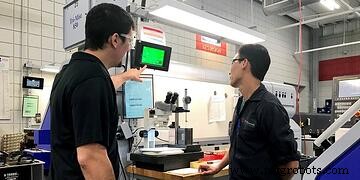
Com Tablets em cada máquina, os operadores podem fornecer um contexto valioso para os dados da máquina, documentando motivos para eventos de tempo de inatividade e peças de sucata.
A abordagem da MachineMetrics para automatizar a coleta de dados de máquina
Na fabricação, a borda é necessária para capturar dados de máquinas e transformar esses dados em um modelo de dados comum para que a análise possa ser realizada. Ele deve ser capaz de oferecer suporte a vários protocolos de CLP para permitir conectividade em vários ativos no chão de fábrica. Ele também deve suportar a captura de dados de sensores para ativos mais simples ou quando um método de conectividade padrão não estiver disponível no PLC. A MachineMetrics desenvolveu e suporta a maioria dos protocolos industriais padrão com suas várias nuances, além de construir conectores personalizados para muitos controles de máquinas CNC diferentes.
Os protocolos padrão suportados incluem:
- OPC-UA
- MTConnect
- Modbus TCP
- Ethernet/IP
Os conectores de controle de máquina personalizados construídos incluem:
- FANUC FOCAS
- Heidenhain iTNC530 e iTNC640
- Cidadão M700
- Mitsubishi M70/M80
- Irmão Speedio
- Serial HAAS
- Matsuura CNC (alarmes personalizados adicionados ao conector FANUC FOCAS)
Para máquinas legadas, a conexão por meio de um sensor simples é suficiente para determinar a atividade da máquina e relatar a utilização. Um sensor de corrente analógico é frequentemente usado e há suporte para vários dispositivos de aquisição digital e analógica, incluindo o Labjack. Isso permitiu outros casos de uso que exigem a captura de temperatura, vibração, pressão e a capacidade de se conectar a relés na máquina.
As conexões PLC/Controle e Sensor podem ser mantidas por meio da interface online, e os dados podem ser filtrados, processados e transformados com uma linguagem de script simples projetada especificamente para dados de IoT.
Os dados podem ser transmitidos em baixa frequência (em uma mudança de evento ou 1 amostra por segundo) ou podem ser transmitidos em alta frequência (1.000 amostras por segundo) para determinados controles e sensores. O suporte para dados de alta frequência exigiu que a MachineMetrics criasse sua própria tecnologia de ponta para dar suporte a esse alto nível de processamento e streaming de dados.
Para dimensionar a borda em milhares de máquinas e poder manter, atualizar e oferecer suporte remotamente ao software de borda, a plataforma MachineMetrics Edge permite o gerenciamento remoto de dispositivos criado para configurar, atualizar e gerenciar remotamente dispositivos de borda coletando dados em nossos clientes locais. Os técnicos de suporte e os próprios clientes podem solucionar problemas, executar diagnósticos, configurar redes e testar seus firewalls usando essas ferramentas integradas. Uma interface de linguagem comum (CLI) foi desenvolvida de forma personalizada para oferecer diagnósticos e suporte adicionais. Essa CLI pode ser usada para atualizar dispositivos, mas em breve os clientes terão a opção de atualizar o software de borda por conta própria.
MachineMetrics Edge Platform fornece uma solução escalável para fabricantes que podem ser auto-instalados para coletar facilmente dados de qualquer parte do equipamentos e permitir insights de máquina acionáveis em questão de minutos.
Coleta de dados de máquina como base para a fabricação inteligente
A coleta de dados de máquinas CNC começa com a conexão de suas máquinas por meio de vários métodos, incluindo soluções com e sem fio.
Uma vez que os dados podem ser coletados, eles são contextualizados e padronizados para serem usados em painéis e notificações em tempo real, além de relatórios históricos para análise mais profunda. Mas este é apenas o começo.
Os dados de máquina representam a base do segmento digital, capacitando um número ilimitado de casos de uso para otimizar e automatizar processos de negócios, permitindo que os fabricantes expandam seus negócios e se diferenciem competitivamente.
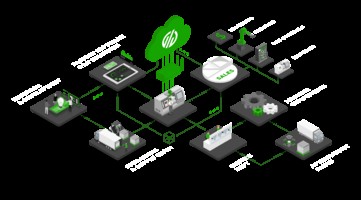
O que vimos com os clientes que abordam isso com soluções baseadas em papel e outras soluções manuais é que os dados de produção são muito menos eficazes, pois são atrasados, imprecisos, descontextualizados e não são dimensionados além dos casos de uso simplificados. Ou pior, é preenchido com lacunas ou inexistentes.
Por outro lado, dados precisos em tempo real capturados e transformados automaticamente dos ativos da máquina criam uma base sólida para capturar insights e gerar valor.
O desempenho pode ser baseado em máquinas, linhas e fábricas semelhantes com confiança, sabendo que os dados subjacentes são precisos. O desempenho de ativos de máquinas pode até ser medido e comparado a ativos semelhantes em um setor específico fora da empresa.
No final, há apenas uma versão da verdade e a máquina não mente. Com a captura e transformação de dados precisas, combinadas com visibilidade e capacidade de ação por meio de acionadores de notificação e fluxo de trabalho, uma melhoria de 15 a 20% no desempenho de utilização pode ser alcançada em questão de meses.
Podemos seguir esse segmento digital para ver onde o contexto adicional é adicionado e como esses dados são usados em outros processos e sistemas para aumentar a eficiência em escala.
Dados operacionais
A fonte de sua produção inclui o equipamento e as pessoas no chão de fábrica. Os dados das máquinas são coletados automaticamente, mas ainda temos que discutir o impacto dos dados do operador.
Com tablets colocados em cada máquina, os operadores podem adicionar contexto aos dados da máquina, o que fornece uma compreensão mais profunda do desempenho do equipamento.
Por exemplo, os operadores podem documentar o motivo de um determinado evento de tempo de inatividade, para que os gerentes de fábrica que analisam o tempo de inatividade não apenas tenham uma visão precisa de quanto tempo de inatividade sua fábrica experimentou, mas também os principais motivos. O mesmo vale para peças de sucata.
Um exemplo de um operador categorizando um motivo de tempo de inatividade como uma "falha catastrófica de ferramenta" em uma interface de tablet.
Isso dá à gerência uma melhor compreensão do problema para que processos mais eficientes possam ser desenvolvidos para gerenciar os motivos mais flagrantes de inatividade e refugo.
Além disso, esses dados da máquina, combinados com o contexto dos operadores, podem permitir notificações baseadas em tempos de inatividade específicos que alertam os operadores e membros da equipe de manutenção sobre eventos de inatividade, para que possam resolver o problema o mais rápido possível.
Máquinas, Pessoas e Sistemas
A linha digital une vários componentes da fábrica digital. À medida que seguimos o fio, os dados da máquina começam a impactar outros sistemas usados pelos fabricantes.
Quando os dados da máquina são coletados automaticamente, eles podem ser integrados a sistemas, como ERP, MES ou CMMS, para gerenciar processos de forma mais eficaz ou para tomar melhores decisões operacionais com base nos dados combinados.
Alguns exemplos para ilustrar a importância disso:
Sistemas de planejamento de recursos empresariais
Os fabricantes geralmente gerenciam trabalhos e agendamentos em ERPs, onde as informações serão armazenadas sobre padrões de trabalho e tempos de ciclo. No entanto, há uma alta probabilidade de que os padrões de trabalho e os tempos de ciclo sejam imprecisos, o que afeta muito os tempos de execução esperados dos trabalhos, além de distorcer os preços, pois as lojas geralmente precificam com base no tempo necessário para usinar um determinado produto.
Se um fabricante estiver coletando dados de máquina em tempo real, os tempos de ciclo podem ser atualizados no ERP para desenvolver padrões mais precisos e garantir que os preços estejam alinhados com os tempos de execução do trabalho esperados. Isso dá aos líderes de manufatura uma melhor compreensão do que a fábrica é capaz de assumir e quanto lucro eles devem gerar.
Sistemas informatizados de gerenciamento de manutenção
Outro exemplo de aproveitamento de dados operacionais e de máquina em outros sistemas é melhorar e automatizar a manutenção com um CMMS.
Existem muitas estratégias quando se trata de manutenção de equipamentos, mas a maioria dos fabricantes continua confiando na manutenção reativa ou manutenção baseada em calendário (com um cronograma recomendado fornecido pelo fabricante da máquina).
A manutenção reativa tende a resultar em quantidades significativas de tempo de inatividade. E a manutenção baseada em calendário (uma estratégia de manutenção preventiva) tende a ser cara devido ao trabalho de manutenção desnecessário.
A zona "Goldilocks" entre manutenção preventiva cara baseada em calendário e manutenção reativa que leva a grandes períodos de inatividade e grandes custos de reparo.
Ao inserir dados e insights de ativos de máquina no CMMS, os fabricantes podem transformar uma estratégia de manutenção reativa e baseada em calendário para uso ou baseada em condições. Sem um thread digital originado no ativo da máquina, o valor que um fabricante pode esperar obter com um investimento em CMMS é significativamente reduzido.
Com os dados da máquina disponíveis, os cronogramas de manutenção podem ser otimizados para alinhar com os dados de uso e condição que saem das máquinas e esses dados podem até ser usados para acionar fluxos de trabalho que geram automaticamente ordens de serviço no CMMS e notificam a pessoa correta sobre a condição da máquina , evento de tempo de inatividade, alarme, falha iminente, etc. para que possam corrigir o problema o mais rápido possível, ou mesmo antes que ocorra uma falha.
O segmento digital de dados de máquina:desbloqueando a indústria 4.0
À medida que os fabricantes habilitam soluções que podem capturar e transformar melhor seus dados de produção, eles não apenas poderão conduzir melhores decisões baseadas em fatos, mas também poderão aproveitar os dados para desenvolver melhores processos e impulsionar a automação no chão de fábrica.
Os dados de máquina abrem um mundo inteiro de casos de uso, tornando-os a base dos dados de produção e capacitando os fabricantes com uma profunda vantagem competitiva.
Ficaremos felizes em discutir como a MachineMetrics Industrial IoT Platform pode ajudá-lo, não importa em que estágio da jornada você esteja, seja monitorando seu equipamento para identificar tempos de inatividade mais rapidamente ou aproveitando dados de alta frequência para prever e evitar falhas de máquina.
Tire suas dúvidas ou agende uma demonstração hoje mesmo.
Tecnologia industrial
- Como se tornar um fabricante orientado a dados
- Fabricação baseada em dados está aqui
- No Limite da Glória:Habilitando uma Nova Era da Máquina da Internet
- Um guia definitivo para a fabricação sem iluminação
- 7 estratégias de fabricação comprovadas para aumentar o rendimento
- 3 exemplos principais de tecnologia de fabricação avançada de ponta
- Coleta de dados de fabricação:impulsionando a otimização do chão de fábrica
- O Impacto dos Sensores na Manufatura
- Benefícios de uma oficina mecânica conectada
- 5 tecnologias que interrompem a fabricação