Controle de Poluição do Ar – Controle de Emissões de Particulados
Controle de Poluição do Ar – Controle de Emissões de Partículas
A siderurgia possui vários processos metalúrgicos que ocorrem em altas temperaturas. Além disso, muitos desses processos lidam com matérias-primas, alguns deles na forma de finos. Portanto, todos esses processos são propensos a emitir gases poluentes e material particulado na atmosfera. Isso, de fato, afeta a qualidade do ar ao redor da planta. A fim de melhorar e proteger a qualidade do ar, diferentes dispositivos de controle de poluição são utilizados para o controle das emissões.
Anteriormente, por vários anos, os equipamentos de controle de poluição eram usados apenas para aqueles processos em que as quantidades de poluentes eram muito altas ou eram de natureza tóxica. Estes equipamentos também foram usados anteriormente onde tinham algum valor de recuperação. Mas hoje, com as regulamentações ambientais cada vez mais rigorosas e com as crescentes preocupações da sociedade com o meio ambiente, tornou-se necessário que a indústria siderúrgica apurasse suas emissões e instalasse equipamentos em todas as áreas para reduzir ao mínimo as emissões. níveis possíveis. Os equipamentos de controle de emissão são basicamente de dois tipos (i) equipamentos de controle de emissão de partículas e (ii) equipamentos de controle de emissão de gases. Este artigo descreve os sistemas de controle de emissão de partículas.
As regulamentações de material particulado (PM) adotadas nos últimos trinta anos mudaram gradualmente da regulação das partículas de modo grosseiro que compreendiam partículas suspensas totais (TSP) para a regulação das partículas muito pequenas nas faixas de tamanho PM10 e PM2,5. Essa mudança ocorreu principalmente porque os dados da pesquisa de efeitos à saúde indicaram que as partículas pequenas estão mais intimamente relacionadas aos efeitos adversos à saúde
A regulação das emissões de material particulado remonta aos primeiros estágios da revolução industrial. Mesmo em 1600, as pessoas podiam ver a relação entre as emissões de material particulado e problemas como deposição de sólidos, sujidade de tecidos, corrosão de materiais e descoloração de edifícios. À medida que a tecnologia e a conscientização pública se expandiram, tornou-se evidente que as emissões de material particulado também contribuíam para certos tipos de doenças pulmonares e doenças relacionadas.
No final da década de 1940, vários tipos de sistemas de controle de material particulado avançaram de projetos relativamente rudimentares para formas que se assemelham aos atuais sistemas de alta eficiência. Por exemplo, os precipitadores eletrostáticos (ESPs) avançaram de unidades tubulares de um campo para controle de névoa ácida para precipitadores do tipo placa de um campo e dois campos. Os depuradores Venturi também começaram a ser usados para controle de material particulado. Esses sistemas de controle foram instalados principalmente para minimizar os incômodos e os problemas criados pela poeira.
O material particulado pode ser dividido em duas categorias:(i) material particulado primário e (ii) material particulado secundário. O material particulado primário é o material emitido diretamente para a atmosfera. Essas emissões têm sido o foco de todas as ações de controle de material particulado anteriores a 1997. O material particulado primário pode consistir de partículas de menos de 0,1 micrômetro a mais de 100 micrômetros. No entanto, a maior parte do material particulado primário cai na categoria grosseira.
Com a promulgação do padrão PM2.5 voltado para partículas finas e ultrafinas, há uma atenção crescente em relação ao material particulado secundário. Este é o material particulado que se forma na atmosfera devido às reações de precursores gasosos. Os processos de formação secundária podem resultar na formação de novas partículas ou na adição de material particulado a partículas pré-existentes. Os gases mais comumente associados à formação de material particulado secundário incluem dióxido de enxofre, óxidos de nitrogênio, amônia e compostos orgânicos voláteis (VOCs). A maioria desses precursores gasosos é emitida por fontes antropogênicas; no entanto, as fontes biogênicas também contribuem com alguns óxidos de nitrogênio, amônia e compostos orgânicos voláteis.
O material particulado secundário pode ser subdividido em duas categorias:(i) material particulado secundário formado a partir de vapores condensados emitidos por fontes antropogênicas e biogênicas, e (ii) material particulado secundário formado devido a reações atmosféricas de precursores gasosos. VOCs e ácido sulfúrico são dois exemplos comuns de emissões que podem condensar para formar partículas secundárias. Esses materiais passam por sistemas de controle de material particulado, incluindo dispositivos de alta eficiência, devido à sua forma de vapor na corrente de gás fonte estacionária. No entanto, o material da fase de vapor pode, sob algumas condições, potencialmente condensar no ar ambiente para formar partículas medidas por sistemas de amostragem ambiente. A importância relativa do material particulado condensável está apenas começando a ser avaliada.
A faixa de tamanhos de partículas formadas em um processo é amplamente dependente dos tipos de mecanismos de formação de partículas presentes. É possível estimar a faixa de tamanho geral simplesmente reconhecendo qual delas é importante no processo que está sendo avaliado. Os mecanismos de formação de partículas mais importantes nas fontes de poluição do ar incluem (i) atrito físico/dispersão mecânica, (ii) queima de partículas de combustão, (iii) condensação homogênea, (iv) nucleação heterogênea e (v) evaporação de gotículas
O atrito físico ocorre quando duas superfícies se esfregam. Além disso, quando as partículas de combustível são injetadas na área do forno quente do processo de combustão, a maioria dos compostos orgânicos é vaporizada e oxidada na corrente de gás. As partículas de combustível ficam menores à medida que a matéria volátil sai. As partículas de combustível são rapidamente reduzidas a apenas a matéria incombustível (cinzas) e carvão de combustão lenta composto por compostos orgânicos. Eventualmente, a maior parte do carvão também queima, deixando principalmente o material incombustível. À medida que a oxidação progride, as partículas de combustível, que começaram como partículas de 100 mm a 1.000 mm, são reduzidas a partículas de cinzas e carvão que estão principalmente na faixa de 1 mm a 10 mm. Este mecanismo para a formação de partículas pode ser denominado queima de combustível de combustão.
A nucleação homogênea e a nucleação heterogênea envolvem a conversão de materiais em fase de vapor em uma forma de material particulado. A nucleação homogênea é a formação de novas partículas compostas quase inteiramente do material da fase de vapor. A nucleação heterogênea é o acúmulo de material nas superfícies das partículas que se formaram devido a outros mecanismos. Em ambos os casos, as correntes de gás contendo vapor são necessárias para resfriar até a temperatura na qual a nucleação pode ocorrer.
Alguns sistemas de controle de poluição do ar usam água contendo sólidos reciclada de lavadores úmidos para resfriar os fluxos de gás. Esta prática cria inadvertidamente outro mecanismo de formação de partículas que é muito semelhante à queima de combustível. As correntes de água são atomizadas durante a injeção nas correntes de gás quente. À medida que essas pequenas gotículas evaporam até a secura, os sólidos suspensos e dissolvidos são liberados como pequenas partículas. A faixa de tamanho de partícula criada por este mecanismo não foi extensivamente estudada. No entanto, provavelmente cria partículas que variam em tamanho de 0,1 mm a 2,0 mm.
Os sistemas de controle da poluição do ar aplicam forças às partículas para removê-las do fluxo de gás. As forças são basicamente as “ferramentas” que podem ser usadas para a coleta de partículas. Todas essas forças do mecanismo de coleta são fortemente dependentes do tamanho das partículas. As forças que são aplicadas são (i) sedimentação por gravidade, (ii) impactação e interceptação inercial, (iii) movimento browniano de partículas, (iv) atração eletrostática, (v) termoforese e (vi) difusioforese.
A aplicação de uma ou mais dessas forças, como força eletrostática ou força inercial, acelera a partícula em uma direção onde ela pode ser coletada. A extensão em que a partícula é acelerada é indicada pela equação 'F =Mp x Ap', onde F é a força sobre a partícula em gramas de centímetro por segundo quadrado, Mp é a massa da partícula em gramas e Ap é a aceleração da partícula em cm/sq seg. Os dispositivos de controle da poluição do ar são projetados para aplicar a força máxima possível nas partículas no fluxo de gás. Quanto mais a partícula (ou massa aglomerada de partículas) é acelerada, mais eficaz e econômico pode ser o dispositivo de controle da poluição do ar.
Existem três etapas fundamentais envolvidas na coleta de material particulado em sistemas de controle de partículas de alta eficiência, como filtros de tecido e precipitadores eletrostáticos. Estas são (i) captura inicial de partículas em superfícies verticais, (ii) sedimentação por gravidade de sólidos na tremonha e (iii) remoção de sólidos da tremonha. Os mecanismos de coleta de partículas controlam a eficácia das duas primeiras etapas, ou seja, a captura inicial das partículas que chegam e a sedimentação por gravidade dos sólidos coletados. A distribuição do tamanho das partículas é importante em cada uma dessas etapas.
Todos os equipamentos de controle de emissão de particulados coletam o material particulado por mecanismos que envolvem uma força aplicada. Vários equipamentos particulados são câmaras de decantação, ciclones, filtros de mangas e precipitadores eletrostáticos. Os mecanismos de remoção de poeira nestes equipamentos e a força aplicada são dados na Fig 1.
Fig 1 Mecanismos de remoção de poeira
Câmaras de decantação
As câmaras de decantação foram um dos primeiros dispositivos usados para controlar as emissões de partículas. No entanto, é muito raramente usado hoje em dia, pois sua eficácia na coleta de partículas é muito baixa. A força de coleta na câmara de decantação é a gravidade. Partículas grandes que se movem devagar o suficiente em um fluxo de gás podem ser superadas pela gravidade e são coletadas na câmara de decantação.
A unidade é construída como uma longa caixa horizontal com uma entrada, câmara, saída e funis de coleta de poeira. A velocidade do fluxo de gás carregado de partículas é reduzida na câmara. Todas as partículas na corrente de gás estão sujeitas à força da gravidade. Na velocidade reduzida do gás na câmara, as partículas maiores (maiores que 40 micrômetros) são superadas e caem nos funis. É usado principalmente como um pré-limpador para outros dispositivos de controle de emissão de partículas para remover partículas muito grandes. A Fig. 2 apresenta um projeto simples de câmara de decantação por gravidade.
Fig 2 Um projeto simples de câmara de decantação por gravidade
Ciclones
Os ciclones são dispositivos mecânicos simples que são normalmente usados para remover partículas relativamente grandes de correntes de gás. Eles são usados como pré-limpadores para equipamentos de controle de poluição do ar mais sofisticados, como precipitadores eletrostáticos ou filtros de mangas. Os ciclones são mais eficientes do que as câmaras de decantação.
Dispositivos mecânicos usam a inércia das partículas para coleta. O fluxo de gás carregado de partículas é forçado a girar de maneira ciclônica. A massa das partículas faz com que elas se movam para fora do vórtice. A maioria das partículas de grande diâmetro entra em um funil abaixo dos tubos ciclônicos enquanto o fluxo de gás gira e sai do tubo.
Existem dois tipos principais de ciclones:(i) ciclones de grande diâmetro e (ii) multiciclones de pequeno diâmetro. Os ciclones de grande diâmetro têm normalmente 300 mm a 2 m de diâmetro. Os multiciclones de pequeno diâmetro normalmente têm diâmetros entre 80 mm e 300 mm.
A corrente de gás entra tangencialmente no ciclone e cria um vórtice fraco de gás giratório no corpo do ciclone. Partículas de grande diâmetro se movem em direção à parede do corpo do ciclone e então se acomodam na tremonha do ciclone. O gás limpo gira e sai do ciclone. Ciclones de grande diâmetro são usados para coletar partículas que variam em diâmetros de 1,5 mm a mais de 150 mm.
As forças de coleta usadas para coleta de partículas em um ciclone são forças centrífugas e gravitacionais. A forma ou curvatura do ciclone faz com que o fluxo de gás gire em um movimento espiral. Partículas maiores se movem para fora da parede em virtude de seu momento. As partículas perdem energia cinética e são separadas do fluxo de gás. Essas partículas são então superadas pela força gravitacional e caem para serem coletadas. A entrada dos ciclones é projetada para alterar o padrão de fluxo do gás de entrada de fluxo direto para um padrão circular para formar o vórtice.
No caso de multiciclone, ciclones axiais são usados em paralelo. Em ciclones axiais, o gás entra pelo topo e é direcionado para um padrão de vórtice pelas palhetas presas ao tubo central. No multi-ciclone, o gás sujo entra uniformemente através de todos os ciclones individuais. A Fig. 3 apresenta dispositivos de ciclone.
Fig 3 Dispositivos Cyclone
Filtros de bolsa
Os filtros de mangas usam um material filtrante como nylon ou lã para remover partículas dos gases carregados de poeira. As partículas são retidas no material de tecido. Enquanto o gás limpo passa pelo material. As partículas coletadas são então removidas do filtro de tecido por um mecanismo de limpeza que é a agitação mecânica ou o uso de jato de ar. As partículas removidas são armazenadas em um funil de coleta. Vários materiais de fibra usados em filtros de mangas, juntamente com suas propriedades, são apresentados na Tabela 1.
Guia 1 Tecidos típicos usados para bolsas | |||||
Fibra | Temperaturas máximas | Resistência a ácidos | Resistência a álcalis | Resistência à abrasão flexível | |
Contínuo | Surge | ||||
graus C | graus C | ||||
Algodão | 82 | 107 | Pobre | Muito bom | Muito bom |
Polipropileno | 88 | 93 | Bom a excelente | Muito bom | Excelente |
Nilon | 93-107 | 121 | Pobre a razoável | Bom a Excelente | Excelente |
Orlon | 116 | 127 | Bom a excelente | Regular a bom | Bom |
Dácron | 135 | 163 | Bom | Bom | Muito bom |
Nomex | 204 | 218 | De ruim a bom | Bom a Excelente | Excelente |
Teflon | 204-232 | 250 | Excelente, exceto pobre em flúor | Excelente, exceto pobre em trifluoreto, cloro e metais alcalinos fundidos | Regular a bom |
Fibra de vidro | 260 | 288 | Regular a bom | Regular a bom | Justo |
Nos filtros de mangas, três forças distintas, a saber:impactação, interceptação direta e difusão, são responsáveis pela remoção de partículas dos gases e sua coleta. A impactação ocorre quando a partícula é tão grande que não pode seguir o fluxo de gás e atinge ou impacta a fibra do filtro de mangas e se separa do fluxo de gás. No caso de impactação direta, a partícula segue o fluxo de gás ao redor das fibras até que ocorra uma colisão devido à distância entre o centro da partícula e a fibra ser menor que o raio da partícula. A difusão ocorre porque partículas muito pequenas sofrem movimento browniano ao longo do volume de gás. Partículas muito pequenas são afetadas pela colisão de moléculas na corrente de gás. Essas partículas que se movem aleatoriamente se difundem através do gás para impactar a fibra e serem coletadas.
Os filtros de manga normalmente possuem um grande número de mangas cilíndricas de fibra que ficam penduradas verticalmente no filtro de manga. Quando as camadas de poeira acumulam uma espessura suficiente, os sacos são limpos, fazendo com que as partículas de poeira caiam em uma tremonha de coleta. Os sacos podem ser limpos por vários métodos. Os três métodos mais comuns são agitação, limpeza de ar reversa e jato de pulso. Na agitação mecânica, os sacos são sacudidos suavemente por um sistema de acionamento para a remoção do pó depositado. No mecanismo de limpeza de ar reverso, o compartimento do filtro de mangas é retrolavado com um fluxo de ar de baixa pressão. A poeira é removida simplesmente permitindo que os sacos desmoronem. O mecanismo de limpeza por jato de pulso é o mecanismo mais popular. Ele usa um jato de ar de alta pressão para remover a poeira do saco. A torta de poeira é removida do saco por um jato de ar comprimido injetado na parte superior do tubo do saco. O jato de ar de alta pressão interrompe o fluxo normal de ar através do filtro. O ar se desenvolve em uma onda de choque que faz com que a bolsa se flexione ou se expanda à medida que a onda de choque percorre o tubo da bolsa. À medida que a torta se flexiona, a torta se quebra e as partículas depositadas caem do saco. A onda de choque viaja para baixo e para cima no tubo em cerca de 0,5 segundos. O jato de ar comprimido deve ser forte o suficiente para percorrer o comprimento do saco e quebrar ou quebrar o bolo de poeira.
A bolsa de filtros de manga tem vida útil e precisa ser substituída quando esta vida acabar. Três condições afetam negativamente a vida útil dos sacos. Estes são abrasão, alta temperatura e ataque químico.
Uma das variáveis importantes no projeto de um filtro de mangas é a relação ar/tecido. Uma proporção muito alta de ar para tecido resulta em quedas de pressão excessivas, eficiência de coleta reduzida, sacos ficando solidamente endurecidos com poeira e rápida deterioração do saco. A Fig. 4 mostra o filtro de saco de jato de pulso.
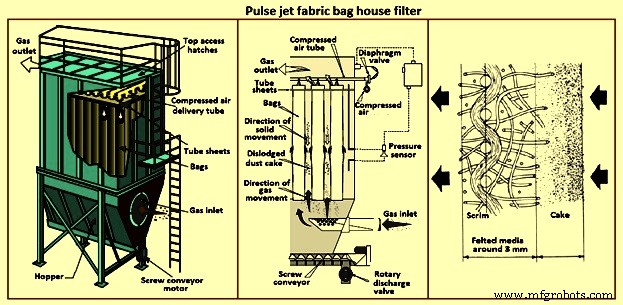
Fig 4 Filtro do compartimento do saco de jato de pulso
Precipitador eletrostático
O precipitador eletrostático é usado para coletar partículas com diâmetros na faixa de tamanho de 0,1 micrômetros a 10 micrômetros. Ele usa campos não uniformes de alta tensão para aplicar grandes cargas elétricas às partículas que se movem pelo campo. As partículas carregadas se movem em direção a uma superfície de coleta de carga oposta, onde se acumulam. Sua eficiência de coleta é alta e às vezes excede até 99%. Os ESPs podem lidar com grandes volumes de gases de escape na faixa de temperatura de 175 graus C a 700 graus C.
Existem três estilos principais de precipitadores eletrostáticos:(i) precipitadores secos carregados negativamente, (ii) precipitadores de parede úmida carregados negativamente e (ii) precipitadores de dois estágios carregados positivamente. Os precipitadores secos carregados negativamente são o tipo mais utilizado em grandes aplicações. Precipitadores de parede úmida (às vezes chamados de precipitadores úmidos) são frequentemente usados para coletar névoa e/ou materiais sólidos que são moderadamente pegajosos. Os precipitadores de dois estágios carregados positivamente são usados apenas para a remoção de névoas. A Fig. 5 mostra o precipitador eletrostático e seu conceito.
Fig 5 Precipitador eletrostático
O mecanismo de coleta de partículas envolvido em um ESP é a força eletrostática. As partículas de poeira suspensas no gás de combustão são carregadas à medida que passam pelo ESP. Uma corrente contínua pulsante de alta voltagem é aplicada a um sistema de eletrodos que consiste em um eletrodo de descarga de pequeno diâmetro e um eletrodo de coleta. O eletrodo de descarga normalmente é carregado negativamente. O eletrodo de coleta normalmente é aterrado. A tensão aplicada é aumentada até produzir uma descarga corona que pode ser vista como um brilho azul luminoso ao redor do eletrodo de descarga. A coroa faz com que as moléculas de gás se ionizem. Os íons de gás negativos que são produzidos migram em direção ao eletrodo de coleta aterrado. Os íons de gás negativos bombardeiam as partículas suspensas na corrente de gás de combustão e conferem uma carga negativa a elas. Partículas carregadas negativamente então migram para o eletrodo de coleta e são coletadas.
O ESP tem seis elementos essenciais. Estes são (i) eletrodo de descarga, (ii) eletrodo de coleta, (iii) sistema elétrico, (iv) rapper, (v) tremonha e (vi) invólucro. O eletrodo de descarga é normalmente um fio de metal de pequeno diâmetro. Este eletrodo é usado para ionizar o gás que carrega as partículas de poeira e para criar um forte campo elétrico. O eletrodo de coleta é uma placa plana ou tubo com carga oposta à do eletrodo de descarga. Este eletrodo coleta as partículas carregadas. O sistema elétrico consiste em componentes de alta tensão usados para controlar a intensidade do campo elétrico entre os eletrodos de descarga e coleta. O rapper transmite uma vibração ou choque aos eletrodos para remover a poeira coletada. Os batedores removem a poeira acumulada nos eletrodos de coleta e nos eletrodos de descarga. Os funis estão na parte inferior dos ESPs e são usados para coletar e armazenar temporariamente a poeira removida durante o processo de batida. Shell envolve os eletrodos e suporta todo o ESP.
A resistividade das partículas de poeira afeta drasticamente a eficiência de coleta do ESP. A resistividade descreve a resistência da camada de poeira coletada ao fluxo de corrente elétrica. Partículas com alta resistividade são mais difíceis de coletar do que aquelas com resistividade normal. A alta resistividade pode ser reduzida ajustando a temperatura e o teor de umidade do gás de combustão que flui para o ESP. No entanto, ao ajustar a temperatura e a umidade, deve-se garantir que a temperatura do gás de combustão esteja acima do ponto de orvalho, caso contrário, haverá corrosão das placas.
Um dos parâmetros importantes no projeto do ESP é a área de coleta específica que é definida como a razão entre a área da superfície de coleta e a taxa de fluxo de gás no ESP. Aumentar a área de superfície para uma determinada vazão de gás de combustão normalmente aumenta a eficiência de coleta do precipitador.
Processo de manufatura
- Purificador de ar
- Oxigênio
- Detector de poluição do ar
- Controle de enchimento da piscina
- Melhorar o monitoramento da poluição do ar com sensores IoT
- A poluição do ar pode tornar tóxicos os exercícios ao ar livre nas grandes cidades
- Considerações na elaboração de uma estratégia eficaz de controle da qualidade do ar
- O que são filtros de partículas para compressores de ar?
- Manutenção da válvula de controle de ar
- O posicionamento do receptor de ar é importante?