Análise de criticidade:O que é e como é feito?
Criticidade e confiabilidade andam de mãos dadas. Pense nisso:somos orientados a priorizar os PMs para ativos críticos, a construir um plano de TPM que acomode peças críticas de equipamentos e a realizar análises de causa raiz em máquinas que consideramos de alta prioridade com base na criticidade. Mas como realmente decidimos o que torna uma peça de equipamento “crítica”? Resumindo, tudo se resume a risco. A realização de uma análise de criticidade permite que você entenda os riscos potenciais que podem impactar seus negócios.
O que é análise de criticidade?
A análise de criticidade é um processo pelo qual os ativos são atribuídos a uma classificação de criticidade com base em seu risco potencial. Ainda soa meio abstrato, certo? Como o risco pode ser quantificado? Isso ajuda a pensar sobre a análise de criticidade como parte de uma análise mais ampla de modos de falha, efeitos [e criticidade] (FMEA / FMECA). Como definimos recentemente, FMEA é uma abordagem que identifica todas as maneiras possíveis pelas quais o equipamento pode falhar e analisa o efeito que essas falhas podem ter no sistema como um todo. O FMECA dá um passo adiante, avaliando o risco associado a cada modo de falha e, em seguida, priorizando as ações corretivas que devem ser tomadas.
Aprenda como consertar uma estratégia de manutenção quebrada com FMEA
Leia mais
Baixe seu modelo FMEA gratuito aqui
Por que a análise de criticidade é importante?
Como descreve James Kovacevic da Eruditio, usar um sistema predeterminado para avaliar o risco permite remover a emoção da equação. Isso garante que a confiabilidade seja realmente abordada de um ponto de vista baseado em risco, ao invés da percepção individual. Depois que o equipamento é classificado com base em sua criticidade, o trabalho pode ser priorizado de maneira adequada. A realização de uma análise de criticidade também ajuda a esclarecer o que pode ser feito para reduzir o risco associado a cada ativo.
Quem é responsável pela análise de criticidade?
Então, quem realmente realiza uma análise de criticidade? Os especialistas do setor afirmam que deve ser um esforço multifuncional, e não poderíamos estar mais de acordo. É um processo muito mais eficaz se as entradas das funções de operações, manutenção, engenharia, gerenciamento de materiais e saúde e segurança do funcionário forem consideradas. Afinal, o risco pode ser definido de maneiras diferentes para equipes diferentes. E uma vez que a atribuição de risco sempre será um tanto subjetiva, ter uma base diversificada de conhecimento para recorrer ajudará a conter isso.
Como realizar uma análise de criticidade
Segundo Kovacevic, existem duas maneiras de fazer uma análise de criticidade. Ambas as abordagens produzem um número de prioridade de risco (RPN) como produto final que permite classificar a criticidade de cada ativo.
A primeira abordagem usa uma grade 6 × 6, onde a gravidade de uma determinada consequência (no eixo X) é plotada contra a probabilidade de ocorrência dessa consequência (eixo Y). Naturalmente, se houver uma grande probabilidade de que uma peça do equipamento falhe de uma forma que cause grandes ferimentos pessoais ou graves problemas operacionais, essa peça do equipamento é altamente crítica e deve ser priorizada de acordo. O número na seção transversal de gravidade e prioridade para qualquer equipamento é aquele RPN.
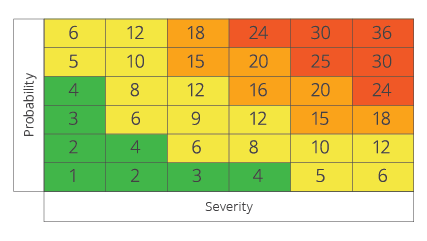
Fonte:accendoreliability.com
A segunda abordagem recomendada é separar as categorias de conseqüências por tipo (por exemplo, saúde e segurança, meio ambiente e operacional). Dessa forma, você pode avaliar a gravidade de uma falha de equipamento para cada categoria de consequência. Por exemplo, uma peça de maquinário que poderia causar ferimentos graves em caso de falha seria 5 ou 6 na categoria de saúde e segurança, mas quase sem consequência para a categoria ambiental (talvez 1 ou 2) e moderadamente impactante para as operações (Em algum lugar no meio). Depois de determinar a gravidade de cada categoria de consequência para um determinado equipamento, você pode multiplicar cada uma das categorias para aquele equipamento para obter seu RPN.
Fonte:accendoreliability.com
Uma vez que cada peça do equipamento tem um RPN anexado a ele, você pode classificá-los para avaliar quais ativos são críticos. Kovacevic recomenda agrupar os equipamentos em categorias com base em seu RPN. Aqui estão as categorias que ele sugere:
Fonte:accendoreliability.com
Depois que cada peça do equipamento é classificada, os gerentes de manutenção podem tomar decisões que são informadas pelo risco, ao invés de intuição. A partir daqui, todas as atividades e processos relacionados à confiabilidade serão executados com muito mais facilidade.
Manutenção e reparo de equipamentos
- O que é 6G e quão rápido será?
- O que é a cavitação da bomba e como evitá-la?
- O que é sílica e como ela prejudica os motores a diesel em equipamentos pesados?
- O que é o corte a plasma e como funciona o corte a plasma?
- O que é solda? - Tipos e como soldar
- O que é moagem eletroquímica e como é feito?
- O que é brasagem e como brasar metal?
- O que é brasagem de cobre e como fazê-lo?
- O que é soldagem por vara? - Equipamento e como fazê-lo
- O que é diagrama de tubulação e instrumentação (P&ID)?