Usinagem Suíça a Seco em Medicina
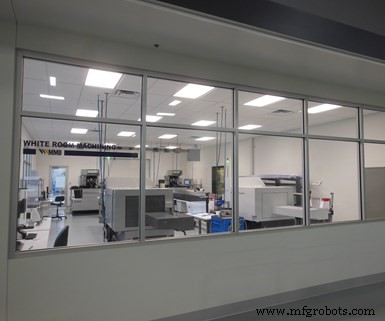
A MMD Medical construiu uma sala branca separada com um sistema HVAC dedicado para manter as operações de usinagem suíças secas livres de outros contaminantes potenciais ao redor da fábrica.
No mundo acelerado e altamente regulamentado da fabricação de dispositivos médicos Classe II e Classe III, as empresas geralmente são desafiadas pela necessidade de um ambiente de usinagem sem refrigeração que elimine o potencial de contaminação em dispositivos altamente críticos. Um fabricante sediado em Minnesota continua a fazer investimentos adicionais para garantir que seus clientes sejam capazes de atingir objetivos críticos de negócios e fabricação, montando salas individuais nas instalações dedicadas às necessidades específicas dos clientes. Essa abordagem ajudou a empresa a atender com sucesso a demanda do mercado por dispositivos médicos críticos e complexos, com uma redução significativa nos custos e, ao mesmo tempo, aumentando a velocidade de lançamento no mercado.
A MMD Medical (Brooklyn Park, Minnesota) foi fundada em 1973, originalmente focada principalmente na fabricação de moldes. Ao longo dos anos, a empresa expandiu suas capacidades para incluir moldagem por injeção, usinagem de precisão e montagem. No início de 2018, a MMD Medical consolidou essas operações em uma única instalação de 100.000 pés quadrados que apresenta, entre outros recursos, uma sala branca de quase 2.000 pés quadrados que abriga operações de usinagem suíças que funcionam sem fluidos de corte.
Os desafios de usinar uma cânula
Um cliente em potencial abordou a MMD Medical com uma necessidade de produção anual de 600.000 cânulas, com tolerâncias rígidas, para atender a uma variedade de procedimentos cirúrgicos. A cânula é um componente vital de um dispositivo usado no reparo de hérnias e outras cirurgias abdominais. Ele canaliza o ar para um balão anatômico que cria a quantidade exata de espaço dentro do corpo para ajudar o médico a realizar o procedimento médico.
Uma das características complicadas da cânula é um lúmen que percorre todo o comprimento do tubo de plástico. Embora esse lúmen não seja usinado (ele faz parte de um processo de extrusão), seu pequeno diâmetro e comprimento criam desafios de risco de contaminação em certos ambientes de usinagem, particularmente aqueles que usam fluidos de corte – retirar fluidos da peça é difícil e caro.
O fornecedor anterior cortou os tubos extrudados no comprimento antes de executar um processo de fresagem vertical durante o qual apenas um lado do tubo foi usinado. Em seguida, o tubo foi virado manualmente para usinagem do outro lado. O processo de produção anterior mostrou-se ineficiente e incapaz de atender às demandas do cliente.
Uma abordagem criativa para usinagem médica
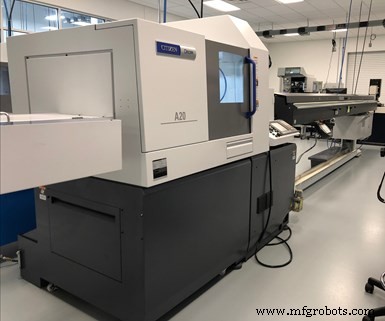
A MMD Medical atualmente usa máquinas do tipo suíço para usinagem a seco dos componentes médicos plásticos.
Examinando a peça, a equipe da MMD Medical sabia que poderia aproveitar a formação diversificada de seu pessoal para entender o processo - e a tecnologia necessária - para atingir as metas de redução de custos e metas de produção do cliente. A equipe viu a chance de provar o valor da empresa e, consequentemente, a oportunidade de aprofundar ainda mais o relacionamento com o cliente. A MMD Medical conseguiu adquirir rapidamente um torno automático CNC Marubeni Citizen-Cincom A20 tipo suíço através da Productivity Inc. para se dedicar ao desenvolvimento e à comprovação do conceito do projeto. A MMD Medical especificou que todos os tubos extrudados seriam entregues em comprimentos de 12 pés e equipou o A20 com um alimentador automático de barras estilo revista Citizen C-320.
“Anteriormente, as peças eram montadas em um monte de cada vez e todos os recursos precisavam ser interpolados”, diz Tim Schmit, gerente de operações de usinagem de precisão. “Foi uma grande vitória para nós podermos executá-los automatizados em um torno tipo suíço com uma barra de 12 pés para que não tivéssemos que cortá-los. Eles apenas continuam produzindo em alta velocidade sem o trabalho manual de fixação.”
“Operar um alimentador de barras a seco não é uma prática comum na indústria”, diz o vice-presidente Darren Bjork. “Nossa equipe precisava fazer algumas tentativas e erros para entender os efeitos do funcionamento a seco para poder desenvolver um processo eficiente e bem-sucedido”. Como as peças são de plástico e nenhum refrigerante é usado, ter as geometrias de ferramenta corretas foi vital para remover o calor do cavaco. A sala onde as peças são fabricadas também possui seu próprio sistema HVAC para separá-la ainda mais das áreas onde são utilizados óleos. Embora a usinagem sem fluidos de corte e usando um ambiente de produção controlado com rigorosos processos de controle de qualidade permita que a empresa elimine o risco de contaminação no dispositivo, isso não resolve todos os desafios.
Sendo peças plásticas, elas são altamente suscetíveis a estragar, mas como é típico na usinagem médica, o acabamento da superfície é crítico. Evitar arranhões é difícil, pois o material gira em alta rotação enquanto passa por um alimentador automático de barras e pelo cabeçote de um torno tipo suíço.
Inicialmente, à medida que as peças se moviam através da bucha, elas recebiam arranhões longitudinais ao longo do comprimento e linhas de chicote se formavam onde as barras se esfregavam no alimentador de barras. Para aliviar o problema, a empresa adicionou espaçadores em vários lugares e, para qualquer componente da máquina que fosse de metal que entrasse em contato com a peça, fazia componentes de reposição de outros materiais que não marcariam a peça. A empresa adicionou um revestimento personalizado para a bucha de ajuste automático e um revestimento espaçador personalizado no subspindle.
O Sr. Schmit diz que os componentes personalizados mais significativos que a empresa construiu foram os novos conjuntos de canais para o alimentador de barras. “Os alimentadores de barras são feitos para serem altamente lubrificados, cheios de óleo”, diz ele. Esse óleo é o que mantém a barra funcionando fria e evita arranhões. “Levamos três iterações, mas conseguimos projetar e construir conjuntos de canais internamente que nos permitem executar o material em RPM normal, completamente seco, sem marcar as peças.”
Um outro ajuste veio em cooperação com o fabricante da máquina. Para manter a máquina mais limpa, eles minimizam o óleo lubrificante para usar apenas o necessário, em vez de lubrificação excessiva, e a MMD Medical mantém um protocolo para limpar a máquina em intervalos regulares.
As primeiras cânulas prontas para produção foram entregues em dois meses, quatro meses antes do previsto. O custo do programa foi reduzido em US$ 150.000 por ano e os prazos de entrega foram reduzidos em 67%. A disposição da empresa em investir no equipamento certo e projetar e executar a melhor solução valeu a pena na entrega para o cliente. E a MMD Medical continuou a fortalecer o programa após o lançamento, desenvolvendo uma maneira mais eficiente de aplicar um filme de poliuretano quase microscópico em cada tubo após a usinagem, eliminando ainda mais etapas no processo de produção e reduzindo ainda mais os custos.
Aplicando estas lições à usinagem de peças novas
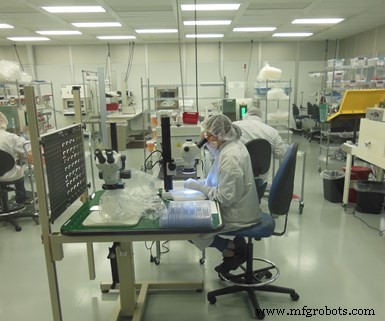
A empresa possui salas limpas ISO Classe 7 adicionais para outras operações de usinagem e montagem.
Devido ao seu sucesso com a cânula, a MMD Medical conseguiu rapidamente garantir trabalho adicional com o mesmo cliente. A próxima parte é um componente para um dispositivo de ligadura, um tubo longo e estreito que é projetado para ser inserido em um corpo durante a cirurgia para agarrar e amarrar partes do corpo por meio de um laço - uma sutura de polipropileno - que é amarrado no centro do dispositivo. A alça de ligação é comumente usada para apendicectomias, bem como para aplicações veterinárias.
Muitas das estratégias implementadas na primeira parte também foram transferidas para este componente. É uma peça bastante simples, mas também requer um manuseio cuidadoso tanto dentro como fora da máquina. O material para esta parte também é entregue em tubos de 12 pés que se parecem muito com espaguete pré-cozido. Embora as barras sejam um pouco rígidas, nesse comprimento elas cedem consideravelmente, portanto, deve-se tomar cuidado mesmo nas estantes para evitar empenamento do material. As peças também são executadas em uma máquina Citizen Swiss.
Na extremidade traseira de cada parte há uma ranhura projetada para permitir a quebra fácil da última seção, ou aba, durante o uso (uma vez que o laço esteja no lugar). Uma extremidade da sutura é presa a essa aba para que possa ser puxada através do tubo para apertar a sutura. A profundidade do sulco é vital para permitir uma quebra fácil, mas não prematura.
Um dos desafios da peça estava no desenho original da ranhura, que era difícil de fazer e permitia uma quebra adequada e consistente. A MMD Medical recomendou uma modificação na forma, de um entalhe quadrado para um entalhe em V, que fornece um ponto muito distinto no qual ele quebra. A empresa ainda executa testes regulares de força de ruptura do sulco, mas atinge consistentemente dentro dos parâmetros especificados.
Trabalho de fabricação médica vencedor
O modelo de negócios da empresa se concentra em oportunidades selecionadas com os principais fabricantes de dispositivos médicos, permitindo que a equipe forneça o máximo valor. “Seguimos o princípio 80/20 para nos permitir focar em ajudar nossos principais clientes a resolver seus maiores desafios de negócios”, diz Bjork. “Nosso objetivo é construir relacionamentos duradouros com os principais fabricantes de dispositivos médicos.”
Um atributo que torna a empresa atrativa para potenciais clientes é a capacidade de identificar a melhor solução para os problemas dos clientes e implementá-la com rapidez, mesmo quando se trata de trazer tecnologia de ponta. À medida que as discussões estão se desenvolvendo para trabalhos futuros, o Sr. Schmit já está se comunicando com os distribuidores de máquinas sobre quais equipamentos podem ser necessários. Com a devida justificativa, a gerência é rápida em puxar o gatilho para novas máquinas e, na maioria dos casos, esses distribuidores conseguiram entregar imediatamente.
“Todo mundo está procurando economia de custos”, diz Bjork. “A vantagem que trazemos é que temos uma equipe de solucionadores de problemas criativos que podem apresentar soluções criativas – e a força financeira para apoiar as soluções investindo na tecnologia e nos equipamentos mais recentes.”
Desde que consolidaram as operações da empresa sob o mesmo teto, as equipes puderam colaborar melhor para alavancar suas diversas perspectivas e conhecimentos para fornecer soluções criativas para os maiores problemas dos clientes.
Para obter mais informações da MMD Medical, ligue para 763-428-8310 ou visite mmdmedical.com.
Equipamento industrial
- Por que a usinagem CNC está em demanda na indústria médica?
- Além da precisão suíça
- 8 Táticas obrigatórias para usinagem médica de precisão
- O que é usinagem suíça e de onde ela veio?
- Como a usinagem de precisão influencia os dispositivos médicos?
- Prototipagem
- Usinagem Suíça de eletrodos médicos feitos de MP35N®
- Usinagem Suíça de Buchas Personalizadas para Dispositivos Médicos
- Usinagem Suíça de Parafusos e Ancoragens Ósseas
- Deflexão e precisão em usinagem suíça CNC