Ferramentas de análise de falhas:escolhendo a certa para o trabalho
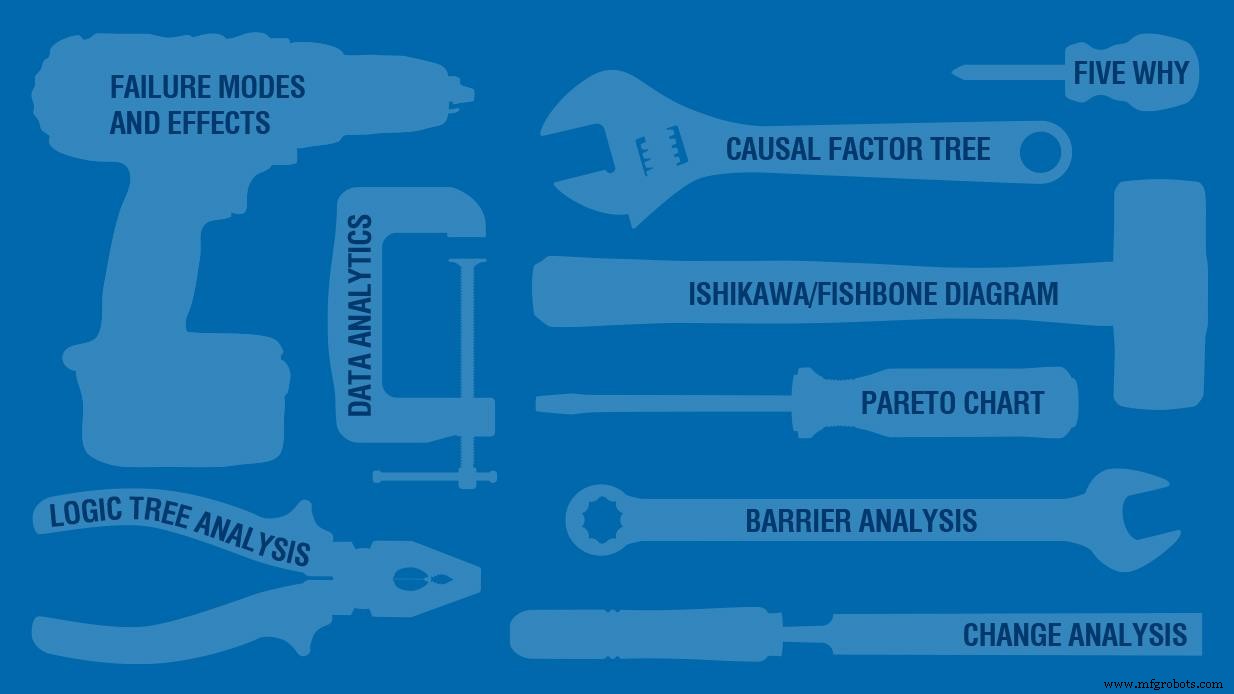
Há uma variedade de métodos de análise de falha e solução de problemas usados para analisar falhas de equipamentos e processos. Os diferentes métodos são descritos e comparados para que os profissionais de manutenção e confiabilidade possam selecionar a ferramenta certa de análise de falhas ou solução de problemas para produzir a melhor solução com o menor custo.
Quem você gostaria que trabalhasse em seu equipamento? A pessoa que seleciona a (s) ferramenta (s) certa (s) em uma caixa de ferramentas bem equipada e as usa habilmente para concluir o trabalho rapidamente sem erros ou alguém que possui algumas ferramentas básicas, mas se esforça para concluir o trabalho no prazo e sem erros.
Qual ferramenta funcionará melhor, um micrômetro ou uma pinça? Um micrômetro é necessário para medir um ajuste de rolamento, mas uma braçadeira C pode ser necessária ao soldar duas peças de aço.
Sua caixa de ferramentas mental também deve conter uma variedade de ferramentas de análise. Você deve selecionar o método de análise mais adequado para resolver o problema em questão. Lembre-se de que cada ferramenta tem seus próprios pontos fortes, pontos fracos e área de aplicação preferida.
Problemas e falhas ocorrem todos os dias. Normalmente, só temos tempo e recursos para prestar socorro. Nem todo problema justifica uma análise de causa raiz.
Nosso trabalho é separar os problemas e as falhas que exigem alívio daqueles em que precisamos prevenir a ocorrência no futuro. Para ajudar a separá-los, pergunte-se algumas perguntas:
-
Qual é o impacto real atual do problema?
-
Qual é o impacto potencial se o problema não for resolvido?
-
Com que nível de risco podemos conviver que seja apoiado de um ponto de vista moral / legal / contratual?
-
O que é um resultado aceitável que equilibra risco, custo e benefícios?
Quando nos concentramos em uma resposta que fornece o alívio necessário e, conforme necessário, a descoberta das causas básicas, nos tornamos mais produtivos.
Vejamos algumas das ferramentas de análise de causa raiz disponíveis, incluindo seus pontos fortes e fracos, para que você possa selecionar e usar aquela para obter o insight de que precisa para resolver seus problemas.
Análise de causa raiz (RCA) não é um único método bem definido; existem muitos processos e métodos diferentes para realizar a análise RCA que são definidos por sua abordagem ou campo de origem :
-
Segurança - análise de acidentes, segurança e saúde ocupacional
-
Produção - controle de qualidade na manufatura industrial
-
Processo - o escopo da produção é expandido para incluir práticas comerciais
-
Falha do equipamento - inspirado nas forças armadas, depois customizado pela indústria e usado em engenharia e manutenção
-
Sistemas - incorpora todos os itens acima e adiciona gerenciamento de mudança
Uma pesquisa de “análise de causa raiz” produzirá dezenas de resultados. Infelizmente, não existem definições uniformes, portanto, um método ou processo fundamental pode ter vários nomes e descrições diferentes. Esses métodos variam em escopo e complexidade. É tão importante usar o método de análise correto, de forma que corresponda ao escopo e à complexidade do problema.
Algumas das técnicas comuns de análise de causa raiz (RCA) são:
-
Cinco porquê - Pergunta por quê, por quê, por quê até que as causas fundamentais sejam identificadas.
-
Diagrama de Ishikawa / espinha de peixe - As causas e efeitos são listados em categorias.
-
Análise de causa e efeito / árvore do fator causal - Os fatores causais são exibidos em uma árvore para que as dependências de causa e efeito possam ser identificadas.
-
Modos de falha e efeitos / análise de criticidade - São definidos os possíveis modos de falha; os efeitos e probabilidades dessas falhas são descritos para identificar contra-medidas apropriadas começando com o equipamento mais crítico.
-
Análise de falha ou árvore lógica - Uma falha é identificada e os modos de falha são descritos e testados até que as raízes sejam identificadas.
-
Análise de barreiras - Examina os caminhos pelos quais um perigo pode afetar um alvo e as barreiras nos caminhos.
-
Análise de mudança / Kepner-Tregoe - Comparar uma situação que não apresenta problemas com outra que apresenta, para identificar as mudanças ou diferenças que explicam o que aconteceu.
-
Gráfico de Pareto - Mostra a frequência relativa de problemas ou falhas na ordem de classificação, de modo que as atividades de melhoria de processo possam ser focadas em alguns poucos significativos.
-
Análise de dados - É um processo de transformação e modelagem de dados com o objetivo de descobrir informações úteis.
A seguir, vamos descrever cada um desses métodos em mais detalhes e explicar suas vantagens e limitações.
Cinco porquês
Cinco porquês é uma técnica de questionamento usada para determinar a causa e os efeitos de um problema ou falha específica. Ele pergunta por quê. A resposta forma a base para a próxima pergunta. Você continua até chegar a algo fundamental ou completamente fora de seu controle. O número cinco é baseado na observação de que perguntar “por que” cinco vezes normalmente resolve o problema. Pode levar apenas três iterações, ou você ainda pode estar se perguntando “por que” daqui a um mês. Depende do problema.
Figura 1 . Cenário dos cinco porquês
Nem todas as falhas têm uma única causa raiz. Para determinar as causas adicionais, o questionamento deve ser repetido começando com uma observação diferente.
Vantagens
Não é necessário um grande grupo para completar a análise. Freqüentemente, uma ou duas pessoas são suficientes. Para falhas de componentes, a mecânica, a química e a física são bem definidas, por isso funciona melhor neste nível. Não funciona tão bem para causas humanas e organizacionais.
O método é flexível, sem regras sobre quais linhas de perguntas explorar ou por quanto tempo pesquisar por causas-raiz adicionais. Conseqüentemente, o resultado depende do conhecimento e da persistência das pessoas envolvidas.
Limitações
Este método parte do conceito de que todo efeito tem uma única causa. Se várias causas podem resultar no mesmo efeito ou uma combinação de causas é necessária para produzir um efeito, elas podem ser negligenciadas. É raro que uma única causa em cada nível do motivo seja suficiente para explicar o efeito em questão.
Quando vários caminhos de cinco porquês são usados, pode haver mais de uma resposta para alguns dos porquês, e é muito fácil que a análise se torne muito complexa. Para resolver este problema, a análise da árvore de fatores causais foi desenvolvida. Se uma de suas respostas estiver errada, pode ter sido possível, mas não foi uma causa real e foi algo totalmente diferente.
Diagrama de Ishikawa / Espinha de Peixe
O diagrama Ishikawa / espinha de peixe (Figura 2) é uma ferramenta gráfica usada para identificar as causas raízes potenciais e qual categoria de entradas do processo representa a maior fonte de variabilidade na saída. Um diagrama de espinha de peixe concluído inclui uma espinha central e galhos que lembram um esqueleto de peixe. Os ramos são usados para categorizar as causas, seja por sequência de processo ou função. Em cada categoria, as causas potenciais são listadas e testadas quanto à validade usando evidências ou outra ferramenta analítica.
Figura 2 . Diagrama de Ishikawa / Espinha de Peixe
Vantagens
Um diagrama em espinha de peixe é útil porque mostra as relações entre as causas potenciais e é uma boa maneira de envolver as pessoas na resolução de problemas. Também é eficaz quando usado por uma única pessoa.
Limitações
Envolver várias pessoas em um diagrama de espinha de peixe pode limitar sua eficácia, porque incentiva uma abordagem divergente, onde a tentação de identificar e consertar tudo que pode causar o problema é forte. Para que um diagrama em espinha de peixe seja bem-sucedido, é necessária uma seleção implacável de causas que não são suficientes, necessárias ou existem para resultar no problema.
Análise de causa e efeito / Árvore de fatores causais
Uma análise de causa e efeito combina a pergunta usada em cinco porquês com a estrutura de árvore de uma árvore lógica ou de falha. Isso ajuda a pensar nisso como uma expansão do método dos cinco porquês em um formato de árvore lógica. Ele pode examinar várias causas em um único efeito.
O problema, falha ou desvio (o efeito) é colocado no topo da árvore ou um único item à esquerda de uma página. Ao perguntar "por quê", os fatores que foram as causas imediatas desse efeito são exibidos abaixo e vinculados por meio de ramificações. Essas causas são testadas quanto à necessidade, suficiência e existência. As causas que não atendem a esse teste são removidas da árvore.
A seguir, as causas imediatas de cada um desses fatores são adicionadas. Cada causa adicionada à estrutura deve atender aos mesmos requisitos de necessidade, suficiência e existência.
Alguns analistas começam com uma declaração do problema respondendo quem, o quê, quando e onde, seguida por uma lista de metas que o evento impactou. Em seguida, uma árvore de fator causal é desenvolvida para cada uma das metas impactadas. Essa construção simultânea ajuda a revelar lacunas no conhecimento.
As árvores de fator causal geralmente têm muitos pontos finais. Os pontos de extremidade que requerem ação corretiva são as causas básicas.
Várias vantagens resultam da construção de uma árvore de fatores causais:
-
Fornece uma estrutura para registro de causas e evidências que é fácil de seguir.
-
Pode lidar com vários cenários.
-
Funciona bem como uma técnica de análise mestre.
-
Pode incorporar resultados de outras ferramentas.
Árvores de fator causais também têm limitações:
-
É difícil manipular e exibir eventos dependentes de tempo.
-
A complexidade torna mais difícil tratar dependências de sequência.
-
Identifica lacunas de conhecimento, mas não tem meios de preenchê-las.
-
Os pontos de parada podem ser arbitrários.
No exemplo da árvore do fator causal na Figura 3, existem várias causas potenciais para um único efeito. Na terceira linha a partir da parte inferior, duas causas estavam presentes que resultaram na superação da resistência do material. Primeiro foi uma concentração de tensão causada pelo desgaste de um ajuste de rolamento no eixo. Em segundo lugar, estava o aumento da tensão da correia, causado pelo aumento da velocidade da máquina vários meses antes da falha. Embora qualquer um deles pudesse ser a causa, a presença de ambos acelerou a fratura por fadiga da diáfise. Isso resultou em uma falha catastrófica da unidade quando o eixo se quebrou.
Figura 3. Árvore do fator causal da seção do secador da máquina de papel
Modos de falha e análise de efeitos
A análise de efeitos e modos de falha (FMEA) é de longe a ferramenta de análise de causa raiz mais abrangente e complexa disponível. Pode ser combinado com a análise de criticidade ou análise de árvore de falha para identificar ainda mais os modos de falha com a maior probabilidade de gravidade das consequências . É um processo indutivo que pode ser iniciado no nível do componente (eixo, engrenagem do rolamento, etc.) ou no nível funcional (bombas de carga, hidráulica de prensa, etc.).
FMEA é uma análise detalhada de alto nível do tipo “e se” de um problema. Uma análise básica do tipo “e se” é mostrada na Figura 4. Inclui um método de brainstorming usando perguntas do tipo “e se” para identificar possíveis variações e falhas em um sistema. Uma vez identificadas, essas preocupações e suas consequências potenciais são avaliadas quanto ao risco.
Figura 4 . Uma declaração simples do tipo “e se”
Ajuda pensar no processo de FMEA como um processo "e se" muito detalhado e rigoroso.
A análise de FMEA começa com a definição do sistema a ser estudado e avança por uma série de etapas até que uma correção seja feita e o acompanhamento para avaliar sua eficácia seja concluído. FMEA foi desenvolvido para avaliar o impacto de falhas de componentes em um sistema. É usado para identificar onde uma falha pode ocorrer (modo de falha) e o impacto dessa falha (efeitos).
Vantagens
FMEA é mais útil no planejamento de contingência, onde é usado para avaliar o impacto de várias falhas possíveis (contingências). O FMEA pode ser usado no lugar de uma análise do tipo “e se” caso sejam necessários mais detalhes.
Quando combinada com a análise de criticidade, a análise estabelecerá sistematicamente relações entre as causas e efeitos da falha, bem como a probabilidade de ocorrência, e apontará modos de falha individuais para ação corretiva. Quando FMEA é usado para complementar a análise da árvore de falhas, mais modos de falha e causas podem ser identificados.
Limitações
FMEA é amplamente utilizado na aviação e em algumas indústrias, mas tem as seguintes limitações:
-
O tempo e esforço necessários para completar a análise
-
Diluição do esforço com casos inconseqüentes
-
Incapacidade de lidar com eventos de falha combinados
-
Normalmente não inclui interações humanas
-
Ele examina os riscos associados a falhas, não durante a operação normal
Análise de falha ou árvore lógica
Uma falha ou árvore lógica é um processo para descobrir as raízes físicas, humanas e latentes de uma falha. Ele começa com uma descrição do problema que descreve a falha. A descrição precisa da falha é crítica para o sucesso da construção da árvore lógica. As descrições de falhas são funcionais ou componentes.
As falhas funcionais descrevem uma variação de um estado desejado, como a bomba não fornece a pressão necessária ou é incapaz de manter a velocidade do projeto sem vibração elevada. Eles devem ser descritos quantitativamente. A análise da árvore de falhas na Figura 4 começa com uma falha funcional de uma bomba; não há fluxo da bomba. Se a bomba foi capaz de produzir algum fluxo, o fluxo ou pressão deve ser incluído.
As falhas de componentes descrevem o estado de um componente específico. Nesse caso, a análise começaria com uma declaração, como o eixo da caixa de engrenagens fraturado ou o rolamento do transportador externo falhou.
A segunda etapa lista os modos de falha logo abaixo da descrição da falha. Um erro comum é listar todos os modos de falha possíveis. O discernimento é necessário para listar aqueles que são relevantes para o fracasso. Por exemplo, a fratura é um modo de falha de um rolamento, mas se o rolamento não estiver fraturado, não será um modo de falha. É útil perguntar:“Como pode ...?”
Uma hipótese para cada modo é feita e, em seguida, cada hipótese é testada usando as evidências. Se a evidência não pode apoiar a hipótese, a hipótese não é usada.
Este processo é repetido até que as raízes físicas sejam alcançadas. Iterações adicionais serão necessárias para chegar às raízes humanas e latentes. Deve-se perguntar:"Como pode ...?" seguido por “ O que as evidências confirmam? ” Lembre-se de que cada hipótese deve ser testada e verificada com evidências. É aqui que muitos esforços de análise de causa raiz entram em problemas.
Vantagens
A análise da árvore de falhas é muito boa para mostrar a resistência de um sistema a falhas de inicialização simples ou múltiplas. Ele pode começar em um nível funcional ou de componente. A OSHA reconhece a análise da árvore de falhas como um método aceitável para a análise de riscos do processo em seu padrão de gerenciamento de segurança do processo.
Limitações
Árvores de falhas e lógicas requerem uma definição cuidadosa do problema. Dependendo da definição do problema, ele nem sempre encontra todas as falhas de inicialização possíveis. Se o escopo do problema for muito grande, o processo ficará atolado na análise de elementos não conseqüentes e se tornará uma abordagem dispersa para tentar abordar as raízes que não são causais à falha.
O exemplo na Figura 5 é uma árvore lógica para uma bomba que parou de bombear. A desmontagem da bomba revelou um eixo fraturado. A fratura por fadiga que causou a falha da bomba começou com uma concentração de tensão. Essa era a raiz física. Uma investigação mais aprofundada descobriu que o eixo da bomba foi feito a partir de uma impressão que não especificava os raios em locais críticos. A omissão dos raios foi a das raízes humanas. A impressão do eixo da bomba foi feita como uma medida de corte de custos, portanto, os eixos da bomba poderiam ser feitos pelo licitante de menor custo. O esforço para cortar custos era uma das raízes organizacionais ou latentes.
Figura 5 . Análise da árvore de falhas de uma falha funcional da bomba
Análise de barreira
A análise de barreiras examina os caminhos pelos quais um perigo pode afetar um alvo. Ele identifica as barreiras ou controles reais ou potenciais usados para proteger o alvo. O destino deve existir dentro de um conjunto especificado de condições. A ideia de um alvo significa que quase tudo pode ser um alvo - uma peça de equipamento, dados, edifício ou pessoa.
Em seguida, o meio pelo qual um alvo é adversamente afetado é chamado de perigo. Um efeito adverso é qualquer coisa que desloca um alvo para fora de seu conjunto especificado de condições. Então, torna-se possível identificar exclusivamente pares de alvo e perigo pelo caminho através do qual os perigos afetam os alvos.
Uma vez que os perigos, alvos e caminhos através dos quais os perigos afetam os alvos são identificados, controles e barreiras usados para proteger, mitigar danos e / ou manter um alvo dentro de um conjunto especificado de condições podem ser descritos.
Barreiras e controles são geralmente projetados em sistemas para proteger pessoas, equipamentos, dados, etc. Todos os perigos podem não ser identificados durante o projeto ou existem caminhos não reconhecidos. As barreiras e controles existentes podem não estar presentes ou, mesmo que estejam, podem não ser tão eficazes quanto originalmente pretendido. Conseqüentemente, os alvos podem carecer de proteção adequada.
O objetivo da análise de barreira é identificar caminhos desprotegidos ou barreiras e controles que não são mais eficazes. Historicamente, a energia que pode causar danos tem sido usada para caracterizar vias. Os caminhos podem incluir elétricos, mecânicos, fluidos, químicos, calor, radiação, etc. Consequentemente, as barreiras e controles foram físicos ou estão relacionados a danos físicos.
A análise de barreira na Figura 6 é um sistema de monitoramento de lubrificação típico encontrado em muitas turbinas. O perigo é a perda de um rolamento de filme fluido devido ao fluxo insuficiente de óleo. As barreiras de prevenção incluem instrumentação para monitorar temperaturas, fluxo e nível de óleo do reservatório. Além do monitoramento, são utilizadas barreiras adicionais de bombas de óleo em espera e de emergência. A mitigação começa quando um nível de alarme é excedido, exigindo intervenção do operador. A barreira final seria um desligamento de emergência da turbina que poderia ser acionado pela temperatura do mancal e perda de fluxo de óleo.
Mudança na condição do alvo, física ou não física, pode ser prejudicial ou indesejada. Agora, a consideração de outros mecanismos além dos físicos direciona a atenção para áreas que são mais baseadas em conhecimento, software, política ou administrativa.
Vantagens
A análise de barreiras tem a vantagem de ser conceitualmente simples, fácil de usar, exigir recursos mínimos e funcionar bem com outros métodos de análise de causa raiz. Os resultados da análise são prontamente traduzidos em ações corretivas.
Limitações
No entanto, a análise de barreiras é de natureza subjetiva. Não há dois analistas iguais e nem sempre chegarão a conclusões iguais ou semelhantes. Também é fácil confundir causas e contramedidas, portanto, não deve ser usado como um método único para determinar as causas raízes.
Figura 6. Análise de barreira do sistema de monitoramento de lubrificação da turbina
Análise de Mudança / Kepner-Tregoe
A análise de mudanças compara a especificação de um único problema ou evento a uma situação desejada, de forma que mudanças e / ou diferenças podem ser encontradas comparando-as. A situação desejada pode ser uma tarefa ou operação que foi realizada corretamente antes, uma tarefa ou operação semelhante, ou um modelo detalhado ou simulação da tarefa ou operação.
As causas potenciais são estudadas e aquelas que requerem o mínimo de suposições ou condições adicionais são testadas para verificar quais são as verdadeiras causas. O sucesso depende da precisão da especificação do desvio e do teste de verificação.
As vantagens da análise de mudança são:
- A capacidade de encontrar causas diretas importantes que não são claras ou estão ocultas.
- Os resultados da análise migram facilmente para ações corretivas.
- É complementar a outros métodos.
- Funciona melhor para analisar falhas funcionais.
Limitações de análise de mudança são:
- Deve haver uma base de comparação.
- Funciona apenas para um único desvio específico.
- Identifica apenas as causas diretas de um desvio.
- Os resultados podem não ser conclusivos e serão necessários testes.
Kepner-Tregoe é uma análise de mudança aprimorada que usa quatro categorias (quem, onde, quando e extensão) e dois filtros (é e não é) para desenvolver uma lista de características que descrevem a condição de desvio. Cada característica desviada ou combinação delas torna-se uma causa potencial da condição geral de desvio. No sistema Kepner-Tregoe, a análise de mudança é chamada de análise de problema. Esta é uma das três ferramentas usadas para avaliar um problema.
O processo Kepner-Tregoe normalmente começa com uma avaliação da situação para esclarecer a situação do problema (o que aconteceu) e, em seguida, usa um dos seguintes subconjuntos para completar a análise . A relação desses métodos é mostrada na Figura 7.
-
Análise do problema:aqui a causa real do problema e a relação entre causa e resultado são pesquisadas (por que isso aconteceu).
-
Análise de decisão:Com base nos critérios de tomada de decisão, as escolhas são feitas para chegar a soluções de problemas potenciais (como devemos agir).
-
Análise de problemas potenciais:os problemas futuros potenciais são antecipados e ações preventivas são desenvolvidas (qual será o resultado).
Figura 7 . O modelo Kepner-Tregoe
Ferramentas estatísticas
Existem dezenas de métodos e ferramentas estatísticas disponíveis. Eles são comumente usados para descrever variações de processo e produto. As informações estatísticas são úteis para identificar tendências de desempenho do equipamento, como tempo médio entre falhas (MTBF), tempo médio de reparo (MTTR), cumprimento do cronograma, carteira de pedidos de trabalho, idade do pedido de trabalho, etc. As ferramentas estatísticas normalmente não são consideradas como um ferramenta de análise de falhas, mas sua importância na identificação de tendências e desvios de um resultado desejado são essenciais para um esforço de manutenção bem-sucedido. Uma importante ferramenta estatística frequentemente usada na análise de falhas de equipamentos é o gráfico de Pareto.
Análise de Pareto
A teoria de Pareto foi desenvolvida pelo economista italiano Vilfredo Pareto em 1897 para explicar a distribuição desigual da riqueza. O Dr. J.M. Juran começou a aplicar esse princípio à análise de defeitos, separando os "poucos vitais" dos "muitos triviais" e chamou-o de "gráfico de Pareto". Isso é freqüentemente referido como a regra 80-20, já que 20% dos problemas causam 80% dos problemas, ou um número relativamente pequeno de problemas é responsável por uma parcela esmagadora dos problemas.
O gráfico de Pareto mostra a frequência relativa de defeitos em ordem de classificação, permitindo organizar esforços de confiabilidade para "obter o máximo retorno do investimento" ou "colher os frutos mais fáceis".
Você pode gerar um gráfico de Pareto usando virtualmente qualquer planilha ou software de gráficos. O gráfico na Figura 8 mostra os resultados de uma análise real de Pareto. A correção do primeiro item no gráfico diminuiu os gastos com manutenção em mais de $ 1 milhão por ano e, o mais importante, permitiu que os recursos de manutenção fossem usados para outros trabalhos de confiabilidade. Os primeiros cinco itens no gráfico resultaram em US $ 18 milhões em aumento de receita por ano.
O gráfico de Pareto é um gráfico poderoso e simples de usar para identificar a origem da maioria dos problemas em uma planta. Não vai ajudar com falhas catastróficas, mas é uma ferramenta extremamente útil para encontrar os problemas crônicos que ao longo do tempo consomem tantos recursos de confiabilidade e manutenção quanto as falhas catastróficas.
Figura 8. Gráfico de Pareto
Análise de dados
Nas indústrias de manufatura e de processo, a Internet das Coisas (IoT) ou análise de dados é uma aplicação de métodos estatísticos para processar dados. A análise de dados na análise de falhas é normalmente a confirmação ou refutação de uma hipótese existente ou a descoberta de novas informações nos dados.
A análise de dados é um processo de inspeção, limpeza, transformação e modelagem de dados com o objetivo de descobrir informações úteis, sugerir conclusões e apoiar a tomada de decisão (Figura 9).
Figura 9. Fluxograma do processo de ciência de dados de "Doing Data Science", de Cathy O'Neil e Rachel Schutt
Quando alguém ouve falar de “big data”, vem à mente Google, Facebook, Amazon, Apple e outras empresas de consumo, já que organizações que reúnem enormes quantidades de dados sobre nós e através da ciência de dados os usam para prever como nos comportaremos no futuro. Anúncios direcionados são apenas um exemplo.
Nas indústrias de manufatura e de processo, a situação é diferente. O desenvolvimento de sensores sem fio nos permitiu coletar grandes quantidades de dados de maneira econômica. Podemos reunir dados de processo rapidamente e usar métodos estatísticos para confirmar ou descobrir novos relacionamentos em nossas fábricas e fábricas. Uma década atrás, o monitoramento de uma variável de processo, como temperatura, exigia a instalação e a fiação de um RTD de temperatura com energia e uma conexão de volta a um PLC ou DCS para que os dados pudessem ser capturados. Agora, é possível instalar um RTD com alimentação própria e um transmissor com um link de dados sem fio para a IoT.
Uma variedade de ferramentas estatísticas podem ser aplicadas aos dados para confirmar ou refutar hipóteses ou descobrir novas relações entre as variáveis do processo. Essa capacidade adiciona uma ferramenta poderosa para uma análise de causa raiz, particularmente de falhas funcionais. Dependendo da qualidade dos dados no histórico de manutenção, também é possível descobrir relacionamentos ocultos nos dados de manutenção usando analítica de texto.
O número de pessoas empregadas na indústria está diminuindo. Experiência e conhecimento estão saindo pela porta na forma de baby boomers que se aposentam. A análise de dados mostra a promessa de ajudar a fechar a lacuna entre uma base de conhecimento cada vez menor e a necessidade de uma melhor análise da causa raiz. No mundo da análise de falha mecânica, ainda existe uma lacuna entre a necessidade de dados de vibração espectral e a análise de dados. Os níveis gerais de vibração podem ser processados, mas o software de análise de dados tem espaço considerável para melhorias no tratamento de dados de vibração espectral.
Na próxima década, você pode esperar uma mudança acelerada em direção a instrumentos inteligentes, a IoT e a análise de dados. Por exemplo, pense em como um posicionador de válvula de controle pode se calibrar e configurar automaticamente, fazer diagnósticos para manter os níveis de desempenho do circuito, melhorar a precisão do controle para reduzir a variabilidade do processo e informá-lo sobre isso.
Armadilhas na análise da causa raiz
Há uma forte tentação de confiar cegamente em modelos específicos de análise de causa raiz. Afinal, eles comprovadamente funcionam, e por que reinventar a roda? Processos estruturados predefinidos podem economizar um tempo valioso. No entanto, é importante lembrar que as respostas podem estar fora de um processo escolhido. Os modelos podem ser úteis porque ajudam a eliminar dados sem importância. Se usarmos modelos sem conhecimento de suas premissas e limitações, podemos perder fatos importantes e direcionar nossa análise de forma incorreta.
Não tente incluir muito em sua análise. É forte a tentação de adicionar todas as causas possíveis, mesmo quando não são necessárias, suficientes ou presentes para causar um efeito. Lembre-se de que a inclusão não garante que você seja eficaz ou correto.
Verifique todas as evidências e hipóteses. É muito fácil tomar o caminho errado se uma hipótese estiver errada. Esteja ciente de que só porque o chefe tem uma hipótese, ela não é necessariamente correta.
Decidir por onde começar e como você descreve a falha tem um enorme impacto no esforço de tempo e no resultado de sua investigação. Começar com uma falha funcional quando houve impacto ambiental, lesão ou custo substancial ajuda na descoberta das causas humanas e organizacionais que, com poucas exceções, estão presentes e desempenham papéis significativos na falha. Quando uma falha não resulta em danos ambientais, danos ou despesas significativas, começar no nível do componente ajuda a agilizar a análise e normalmente torna a identificação das raízes físicas mais fácil. Conforme a análise avança, o grau de investigação das causas humanas e organizacionais pode ser equilibrado em relação ao nível de risco e custo aceitável para você e para a organização.
Fazendo acontecer
Idealmente, seria bom ter um complemento completo de ferramentas de análise de causa raiz em sua planta. As escolhas devem ser feitas porque não se tem tempo e dinheiro ilimitados. As escolhas tornam-se mais fáceis de fazer quando se leva um momento para considerar onde está a necessidade, com que freqüência uma análise de causa raiz será necessária e quais recursos estão disponíveis. Se a necessidade for maior para falhas funcionais ou problemas de qualidade e eficiência do produto, as ferramentas usadas serão diferentes daquelas usadas para falhas de componentes. Se você está lendo este artigo, é razoável concluir que seu foco estará nas falhas de componentes. A Tabela 1 resume o tempo necessário.
Identificar e compreender as causas raízes das falhas de componentes é melhor quando iniciado na fábrica ou no chão de fábrica. Técnicos e supervisores de linha de frente que podem identificar modos de falha física e usar ferramentas de análise básicas, mas poderosas, são frequentemente os melhores meios para prevenir a ocorrência de falhas no futuro. Técnicos e supervisores de linha de frente teriam as seguintes habilidades:
-
Cinco porquês - Aprender cinco por que a análise pode ser feita em menos de um dia. O CMMS deve ser capaz de dar suporte ao que é aprendido com uma análise de Cinco Por que com modos de falha ou um meio de capturar as causas.
-
Diagrama de Ishikawa / espinha de peixe - Isso também pode ser ensinado em menos de um dia. Ele apresenta às pessoas uma análise de causa e efeito mais ampla para identificar os efeitos que podem ter várias causas.
-
Análise de barreiras - uma introdução à análise de barreiras ajuda a mudar a cultura de soluções simplistas para o conceito de risco e redução de risco.
-
Causal factor tree or fault tree analysis – Not everyone needs to be able to construct a tree, but they should be able to participate in the development of one when led by a facilitator. People closest to the point of action have information and insights that are frequently vital to identify root causes and more importantly make changes to prevent future failures. Training to introduce people to either causal factor or fault trees typically takes one day to complete.
-
Failure mode identification – This is frequently considered as a subset of the root cause analysis methods. Frequently, incorrectly identified failure modes lead analysis efforts astray. Technicians, front-line supervisors and reliability engineers must be able to correctly identify physical failure modes. This training takes four days to complete. It also helps a Pareto analysis because failure modes are correctly identified.
In every plant, there should be at least one person who has received facilitator training on causal factor or fault tree analysis and change analysis. This helps ensure consistency and reinforces the use of root cause analysis. Vendors of these methods frequently tout their system as superior to others. They all have certain strengths and weaknesses. Causal factor and fault tree analysis are very similar, so having both may lead to confusion. It is important that one is selected and used. Training for each of these methods usually takes four or five days to complete.
Reliability engineers should receive training on the following:
-
Five whys
-
Ishikawa/fishbone diagrams
-
Cause and effect/causal factor tree
-
Fault or logic tree
-
Pareto chart
-
Change analysis
-
Statistical methods - If they are involved in production issues, training on statistical methods including data analytics should be included.
Unless there is personal injury, an environmental accident or a large cost involved, don’t start every effort with an expensive analysis. You can often be more effective by using the five whys, Ishikawa/fishbone or a simple cause and effect analysis to solve many problems. A situation appraisal may help you select another method when it appears the problem can be solved with a simpler method. Causal factor trees, fault or logic trees can take a substantial amount of time to complete. This can range from a day to several weeks. Failure mode and effect analysis takes weeks or months to complete.
Additional Resource
A resource you may find useful for additional information on root cause analysis:
The Rootisseriet. This website has a wealth of articles on root cause analysis as well as links to additional resources.
Tecnologia da Internet das Coisas
- ips para escolher o serviço de reparo CNC correto
- ips para a inspeção correta das ferramentas CNC
- Sistemas de soldagem robótica:escolhendo o correto
- A diferença entre corte por oxicorte e corte por plasma e escolha do método certo para sua aplicação
- Tremonha de descarga automática - A ferramenta certa para o trabalho
- Escolhendo as ferramentas certas para trabalhar em ambientes de trabalho explosivos
- Encontrando as ferramentas certas para prototipagem dentro do orçamento
- 5 dicas para escolher o sistema de gerenciamento de pedidos certo
- Como escolher o guindaste certo para seu projeto
- Escolhendo o acessório certo para o aluguel de seu equipamento