Lança traseira VBO fora de autoclave, costelas termoplásticas alvo Wing of Tomorrow
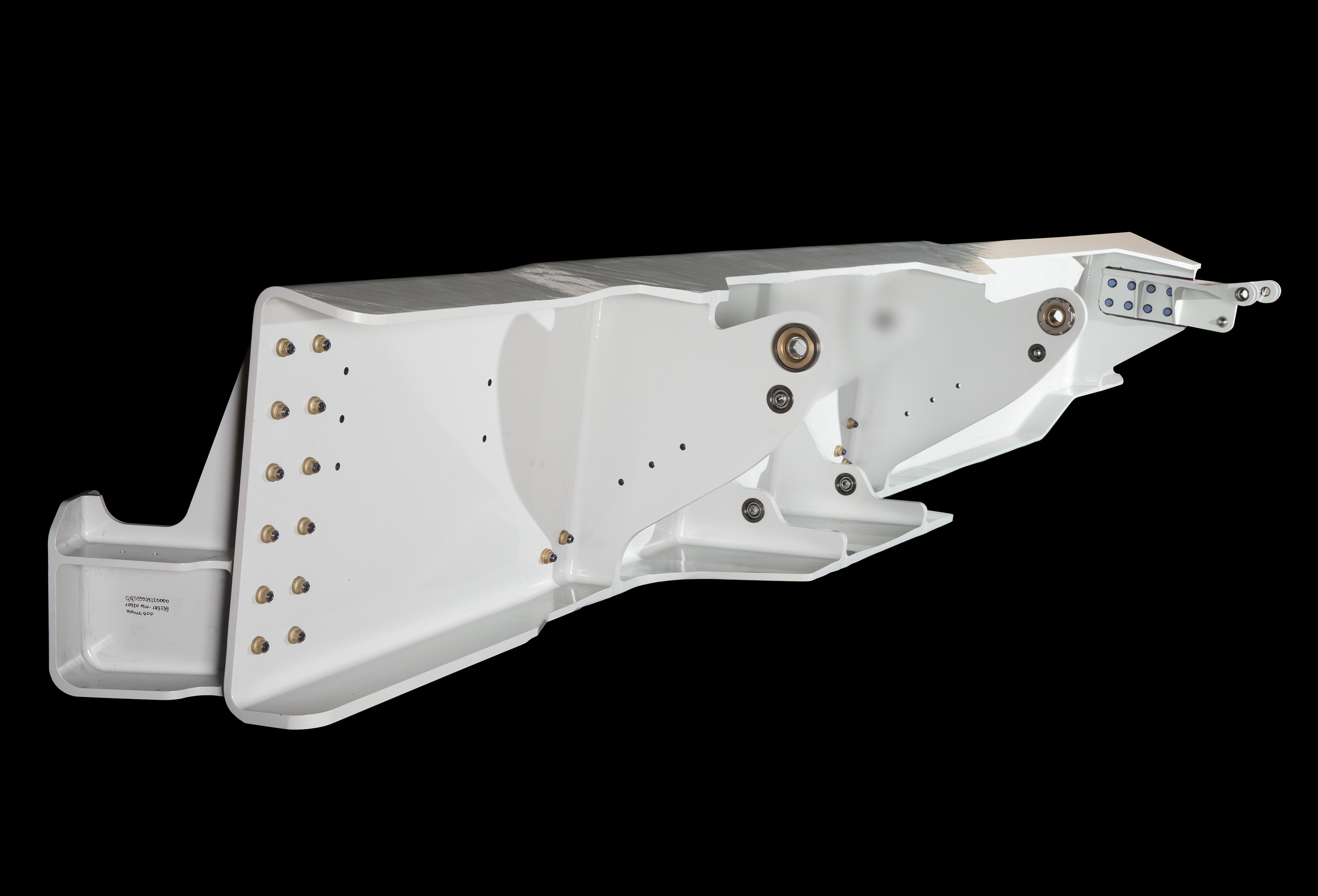
A Airbus (Toulouse, França) está no meio de um amplo esforço para trabalhar com fabricantes de aerocompósitos no desenvolvimento de estruturas fora de autoclave (OOA) para o programa Wing of Tomorrow (WOT) da empresa. Essas estruturas serão entregues à Airbus em 2021 e serão montadas em uma asa de demonstração que será testada e avaliada para uso potencial em uma aeronave de corredor único de próxima geração. Não se sabe quando tal programa pode ser anunciado e sujeito a muita especulação, mas toda a cadeia de suprimentos de aerocompósitos está se posicionando para fazer parte da próxima geração de fabricação de aeronaves, seja para Airbus ou Boeing, ou ambos.
CW relatou algumas dessas atividades WOT já em histórias sobre a pele da asa inferior produzida pela Spirit AeroSystems (Wichita, Kan., EUA) e costelas termoplásticas produzidas pela GKN Aerospace (Hoogeveen, Holanda). Juntando-se ao esforço da WOT está o fabricante de aeronaves e fornecedor de aeroestruturas Daher (Paris, França), que desenvolveu, fabricou e entregou uma longarina traseira OOA e cinco nervuras termoplásticas para o programa.
“Daher tem orgulho de participar deste programa WOT. Este desenvolvimento confirma a posição de Daher como um dos líderes mundiais em tecnologias termoplásticas e em estruturas de funções integradas termofixos, bem como um forte parceiro para fabricantes de aeronaves e um Tier 1 para peças complexas ”, disse Dominique Bailly, VP de P&D da Daher.
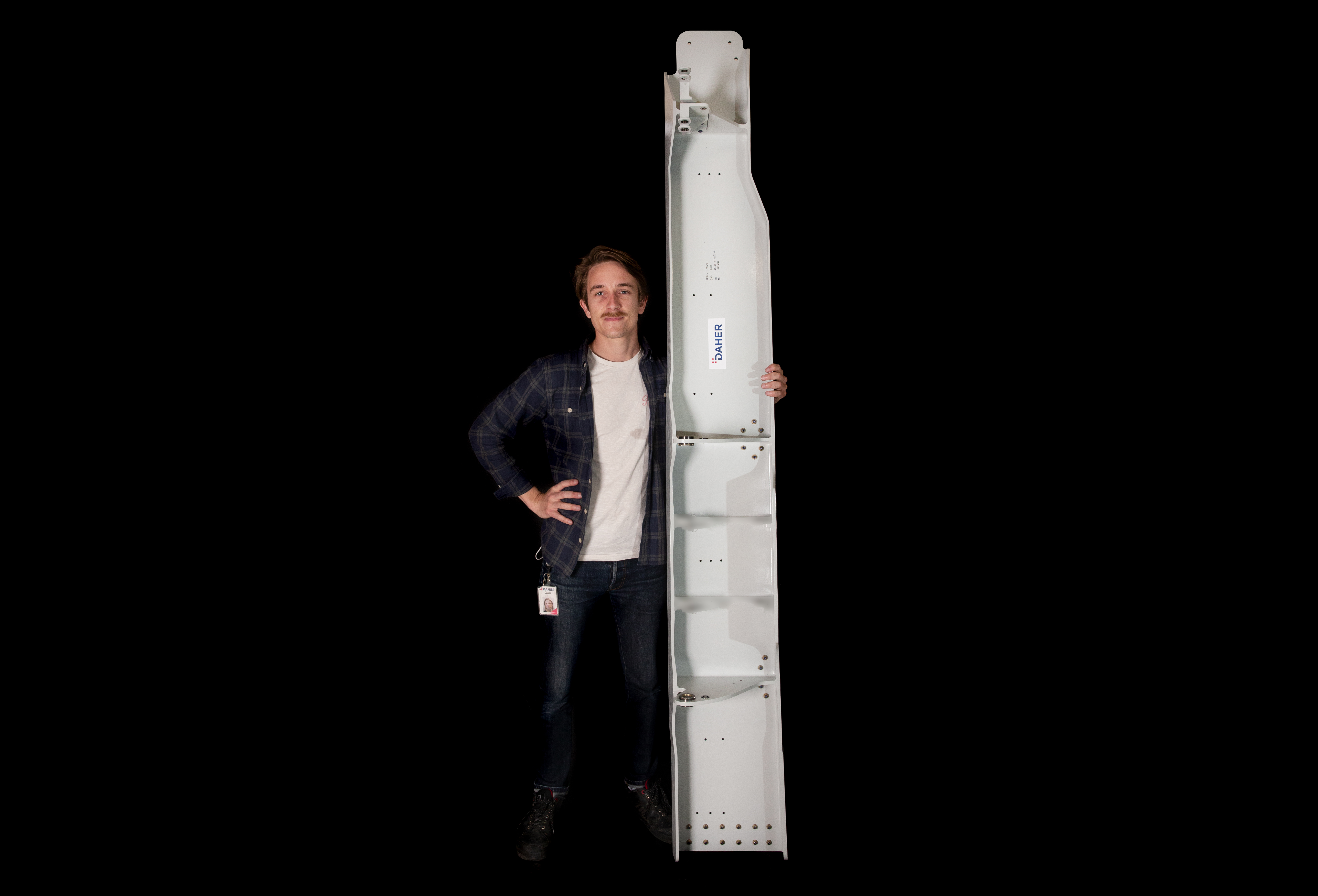
longarina de alto desempenho
O demonstrador WOT, como qualquer asa de aeronave comercial, tem várias estruturas de longarina. O mastro traseiro Daher desenvolvido para WOT está fora do tanque e o segundo mais próximo dos dois mastros imediatamente adjacentes à fuselagem, localizado logo acima do trem de pouso. Ele mede mais de dois metros de comprimento e 10 milímetros de espessura e deve atender aos requisitos de resistência e rigidez significativos - "algumas toneladas aplicadas em recursos e várias dez de toneladas para cisalhamento e tração na direção da envergadura", diz Bailly - devido à sua proximidade com à fuselagem e ao sistema de trem de pouso.
Além disso, diz Alexandre Condé, engenheiro-chefe da Daher que trabalhou no spar, a Airbus estava procurando o desenvolvimento de um processo de fabricação altamente automatizado que permitiria à empresa reduzir o peso da aeronave e atender a taxas de produção de aeronaves de 60-100 navios com economia por mês. Daher propôs um projeto capaz de substituir 15 componentes metálicos e fixadores originais do projeto da longarina composta de linha de base. “A ideia era integrar o máximo de recursos para ter um bom custo-benefício e economizar peso”, diz Condé.
A estrutura da longarina resultante é um subproduto de uma longarina termofixa somente com saco a vácuo OOA (VBO) desenvolvida pela Daher em 2018 para um jato executivo da Dassault Aviation (Paris, França). Bailly diz que a longarina Dassault foi fabricada com pré-impregnado à base de resina epóxi M56 da Hexcel (Stamford, Conn., EUA), curado OOA VBO. Posteriormente, conforme Daher se envolveu com o programa Airbus WOT, a empresa decidiu adaptar o projeto, processos e justificativa da longarina Dassault e aplicá-los à nova estrutura WOT Airbus, selecionando o Hexcel M56 350 ° F cure OOA epóxi, pré-impregnado em Tecido em fibra de carbono Hexcel AS4 e fibra de carbono IM7 UD.
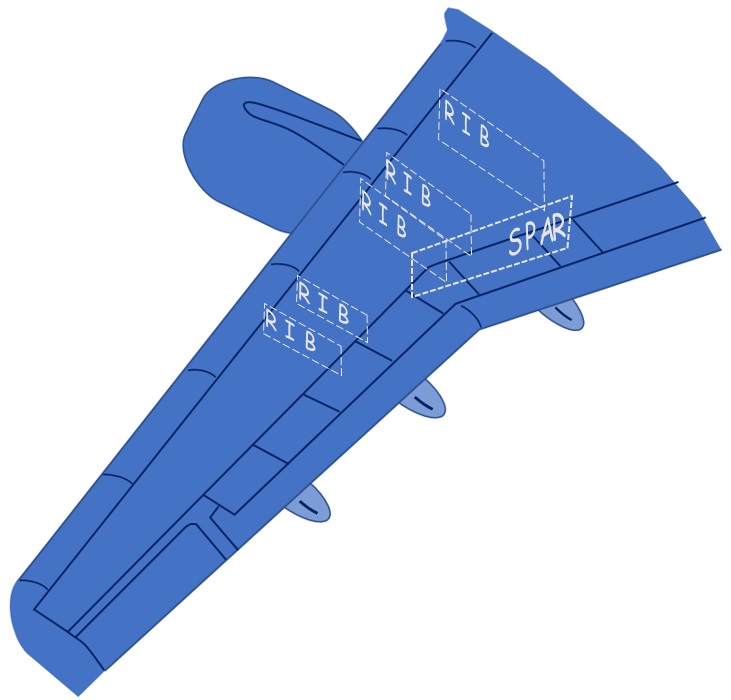
O processo de fabricação usado para fabricar a longarina é a colocação automática de fibras (AFP) usando um sistema Coriolis Composites (Queven, França), que aplica o material sobre um molde macho. A cura é realizada em saco de vácuo em um forno. A parte resultante, diz Condé, tem porosidade de 0,1%.
Condé diz que o pré-impregnado foi escolhido em vez da moldagem de resina líquida pela mesma razão que o pré-impregnado se tornou um produto básico da fabricação aeroespacial nos últimos 30 anos:ele fornece um volume de resina / fibra consistente e confiável que permite a produção de peças com dimensões consistentes e confiáveis e massa. “Usando esta nova geração de resina OOA apenas com vácuo, você tem uma robustez perfeita no conteúdo de fibra na espessura do composto após a cura”, diz Condé. “Além disso, o peso da peça é muito estável porque você não está empurrando a resina para fora da fibra.”
Daher diz que foi o primeiro parceiro a entregar, no final de 2020, um componente WOT - um spar para a Airbus em Bristol, Reino Unido - para integração no primeiro demonstrador WOT; a empresa está em processo de entrega de mais dois. Além desta fase de demonstração, Daher também está pensando na industrialização da fabricação de longarinas e trabalhando em uma análise de projeto de sistema de manufatura (MSD) que estima e simula operações, instalações, equipamentos e requisitos de pessoal para a produção plena de um corredor único de próxima geração aeronaves.
Várias costelas, vários tamanhos
O esforço da Daher para desenvolver costelas pois o programa WOT foi mais complexo e exigente. A empresa projetou cinco costelas de tamanhos e dimensões variados no interior da asa; as outras nervuras são uma combinação de designs de alumínio e composto, incluindo uma nervura composta termoplástica projetada pela GKN Aerospace.
Em um projeto anterior com a Dassault Aviation, Daher demonstrou sua capacidade de projetar e fabricar costelas relativamente pequenas de compostos termoplásticos, explica Bailly. Com o WOT, a empresa teve a oportunidade de estender suas habilidades para o desenvolvimento de costelas maiores (~ 2 metros de comprimento) e de maior carga.
Além disso, de acordo com as metas do WOT, Daher tem como meta um nível de preparação tecnológica (TRL) de 6 até o final de 2023. “No final do programa WOT, quando provamos que estamos no TRL 6 para costelas grandes, entre estes dois programas [WOT e Dassault Aviation], teremos demonstrado que somos capazes de cobrir toda a parte das costelas da asa - essa é a ideia ”, diz Bailly.
“Aproveitamos este programa para examinar as diferentes maneiras de fabricar peças e comparar comportamentos mecânicos, e também para observar o impacto na fabricação. Paralelamente, estamos trabalhando na simulação para prever o comportamento do componente, como efeito de retorno ou estampagem. O objetivo é reduzir os ensaios durante o desenvolvimento, portanto o custo não recorrente ”, afirma Condé.
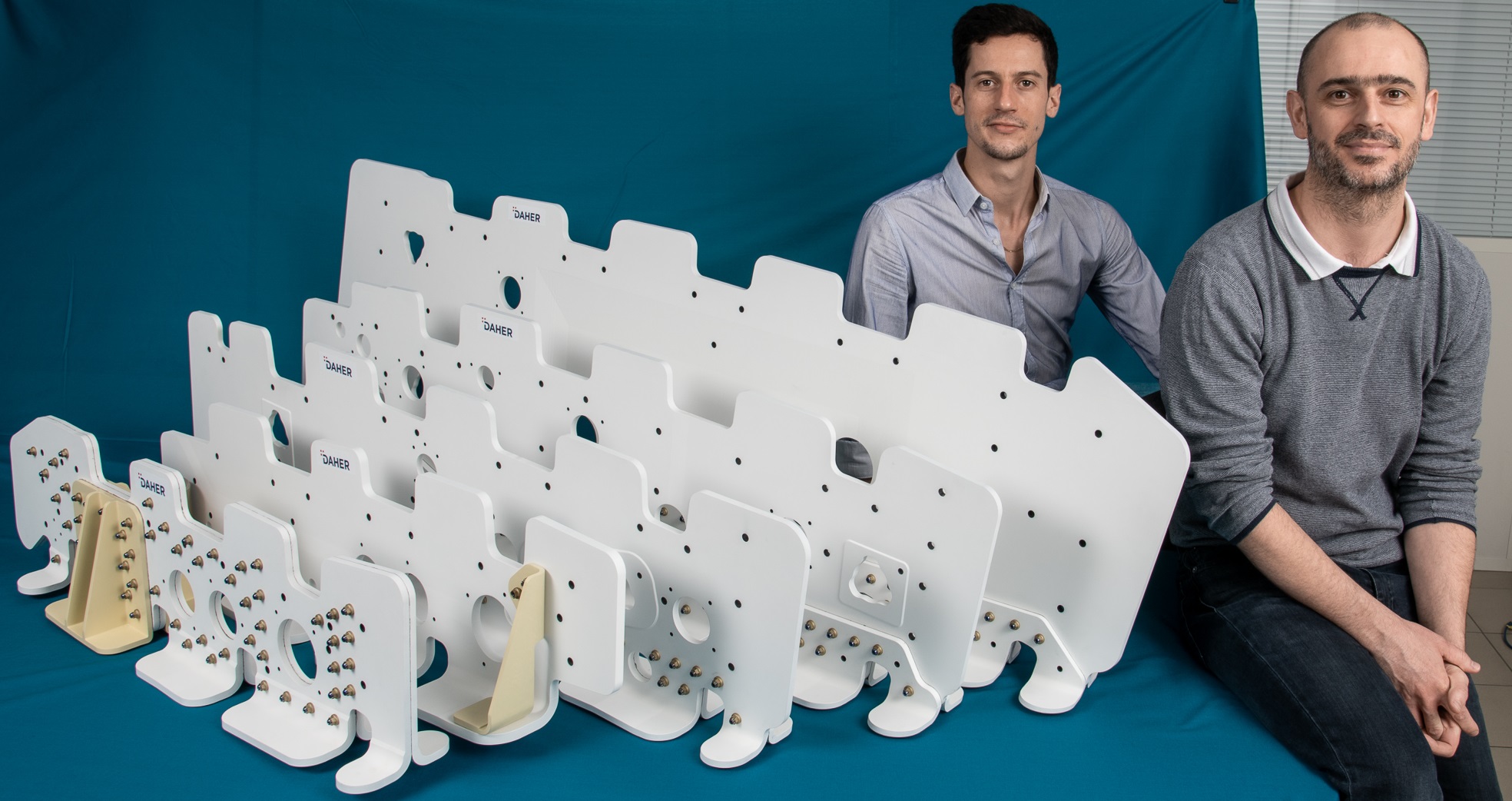
Como a longarina, o desenvolvimento começou no nível de cupom, elemento e detalhe, seguido pela fabricação de peças da subescala antes que as peças finais em tamanho natural fossem construídas. Os testes foram conduzidos em cada nível, observa Condé, incluindo testes específicos desenvolvidos por Daher para características de costelas.
Para todas as cinco costelas, Daher finalmente decidiu usar fitas de fibra de carbono unidirecional (UD) / poliariletercetona de baixo ponto de fusão (PAEK) fornecidas pela Toray Advanced Composites (Morgan Hill, Califórnia, EUA) usando resina fabricada pela Victrex (Cleveleys, Lancashire, Reino Unido ) Para fabricar as nervuras, os blanks planos são feitos usando AFP seguido de consolidação em forno - em alguns casos, os materiais são pré-consolidados antes da formação do selo. Conforme necessário, flanges adicionais ou outros componentes são fixados mecanicamente nas peças formadas por estampagem.
Cada nervura foi projetada de acordo com sua posição ao longo da asa, especificações de tamanho e requisitos de carga (uma tonelada a 50 toneladas), portanto, cada uma é única de várias maneiras. A maior costela mede 2 metros de comprimento x 1 metro de largura. Independentemente disso, cada um começa com uma teia plana, que é estampada em forma de “L” para criar um flange ao longo da parte inferior da peça onde se conecta à pele da asa. Para estabilidade adicional, várias das nervuras compreendiam dois componentes em forma de “L” mecanicamente fixados costas com costas para formar uma forma de “T” com flanges bidirecionais.
Recursos especializados incluem um suporte (fabricado em compostos termofixos) para conexão com a trilha da aba fixada na nervura e uma série de orifícios ou quedas de lona em certas nervuras para reduzir o peso da peça.
“Durante todo o tempo que estávamos projetando, tivemos que gerenciar a complexidade versus o custo”, diz Bailly. “Isso sempre esteve em nossa mente, fazer algo simples, mas com boa relação custo-benefício.” A simplicidade também era fundamental do ponto de vista da taxa de produção, observa Condé. “Se for muito complexo, não será competitivo do ponto de vista do cliente, com as taxas muito altas que eles desejam ter.”
Um desafio que introduziu complexidade no projeto foi a espessura relativa de cada uma das nervuras - até 12 milímetros para a nervura maior. Tecidos mais grossos tendem a enrugar ou formar incorretamente quando formados por estampagem, e peças mais grossas podem ser difíceis de usinar no formato final.
Para usinagem, Daher usou uma mistura de corte por jato de água e usinagem mecânica dependendo das necessidades da peça, tanto para mitigar problemas na espessura da peça quanto para controlar a temperatura. Além disso, na nervura de 12 milímetros de espessura, a equipe projetou uma janela de queda de lona no meio do componente para reduzir o peso geral da peça. Além de resolver esses problemas potenciais, Condé observa que a janela de queda de camadas também permitiu a Daher "tentar diferentes tipos de recursos de fabricação nas peças, para aumentar nossa compreensão do comportamento das peças."
O processo de formação de carimbo revelou-se um desafio ainda maior. “Tivemos que imaginar uma nova forma de estampar para mitigar o risco de rugas”, diz Bailly. Daher acabou desenvolvendo um método proprietário para resolver o problema.
Próximas etapas
Além de WOT, Daher está avaliando métodos alternativos de fabricação para a produção de reforços termoplásticos, enquanto faz planos para desenvolver uma linha de produção completa para manufatura de alta taxa no futuro.
Por exemplo, enquanto os demonstradores WOT usam fixadores, Bailly observa que, por meio de sua aquisição em 2019 de compósitos termoplásticos e especialista em soldagem por indução KVE Composites (Haia, Holanda), Daher possui a capacidade para componentes soldados no futuro. “Estamos trabalhando em outro projeto separado para alcançar um nível mais alto de TRL na soldagem de peças grossas UD [para uso em aeronaves de corredor único de próxima geração]”, diz ele.
Daher também está trabalhando no desenvolvimento de uma linha de produção completa para produzir nervuras termoplásticas no futuro. “Estamos realmente aprimorando o conceito e reduzindo o número de máquinas necessárias para todas as tarefas e reduzindo os custos do processo”, diz Bailly, com o objetivo de atingir as metas de produção de aeronaves de alto volume.
Resina
- Covestro Aumenta o Investimento em Compósitos Termoplásticos
- Lances mestre termoplásticos reforçados com grafeno lançados
- Solvay Expande a Capacidade do Composto Termoplástico
- Compostos termoplásticos na Oribi Composites:CW Trending, episódio 4
- Suprem expande as capacidades termoplásticas
- Kordsa expande a linha de termoplásticos pré-impregnados
- Compostos termoplásticos LANXESS usados na concha do banco traseiro do Audi A8
- Tecnologia de produção de painel de favo de mel termoplástico EconCore
- Compostos termoplásticos:Vista panorâmica
- Compósitos termoplásticos de soldagem