Garantia de qualidade para impressão 3D de metal:Resolvendo 3 desafios comuns
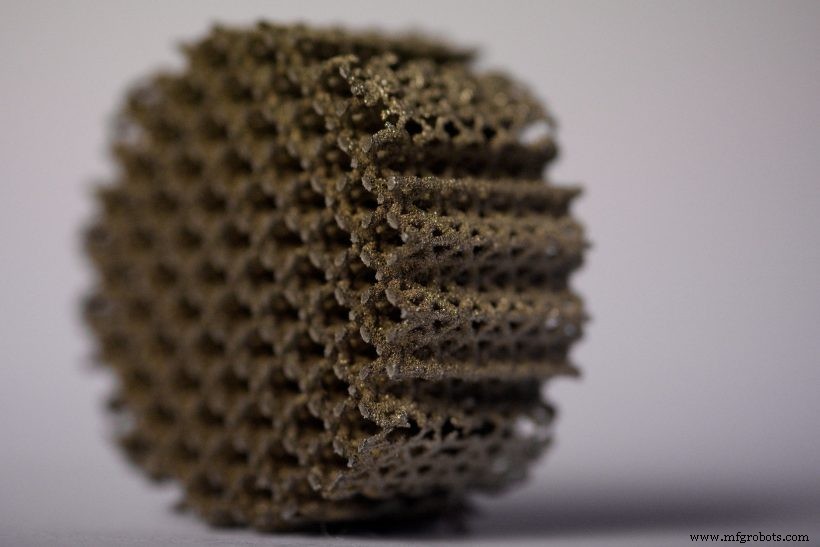
A garantia de qualidade (QA) é indiscutivelmente a mais importante e ainda uma das etapas mais desafiadoras na impressão 3D.
Com a impressão 3D sendo cada vez mais usada em aplicações industriais de alto desempenho, a tecnologia deve fornecer peças de alta qualidade de forma consistente e confiável com as propriedades necessárias para atender a aplicações exigentes. Quando se trata de impressão 3D de metal, no entanto, este tem sido um desafio contínuo para muitos fabricantes que buscam investir em tecnologia.
O artigo de hoje abordará alguns dos principais desafios que as empresas enfrentam ao tentar estabelecer processos de controle de qualidade para peças metálicas impressas em 3D e explorar algumas das soluções disponíveis.
Desafio 1:Garantir a qualidade de seus materiais
Garantir que uma peça impressa em 3D atenda aos padrões de aplicações altamente exigentes depende muito da qualidade do material usado.
No entanto, a qualificação do material é um desafio constante para as empresas que produzem ou manuseiam pós metálicos. Um fator que complica o processo é a necessidade de manter a pureza dos pós metálicos usados na fabricação de aditivos.
Isso é especialmente o caso para aplicações críticas de segurança, como peças de aeronaves ou dispositivos médicos, onde o material usado deve estar 100% livre de contaminação. As impurezas podem alterar as propriedades da peça final, o que pode, por sua vez, levar a uma impressão malsucedida.
No entanto, existem várias maneiras pelas quais os pós metálicos podem ser contaminados.
Por exemplo, o risco de contaminação pode surgir durante o próprio processo de impressão ou durante o armazenamento, transporte e manuseio. Tomando o primeiro exemplo:pode haver, por exemplo, algum resíduo de outro pó deixado na placa de impressão, levando à mistura de dois pós diferentes. A limpeza completa da placa de impressão após cada execução de produção é, portanto, uma importante etapa preventiva. Outro risco surge quando o pó, sobras do processo de impressão, é reaproveitado. Embora a capacidade de reutilizar o material em pó possa ajudar a reduzir o desperdício, é importante observar que a reutilização repetida do pó desta forma pode alterar potencialmente a composição das partículas, à medida que umidade, oxigênio e nitrogênio são absorvidos.
Inevitavelmente, métodos de teste, adequados para a fabricação de aditivos, serão necessários para garantir que não haja contaminação.
Solução:Considere tomografia computadorizada
Uma das maneiras mais precisas de detectar a contaminação em pós de metal é usando a tomografia computadorizada (TC).
Um scanner de TC funciona tirando centenas de imagens de raios-X de diferentes ângulos, a partir das quais uma imagem 3D é criada. Os modernos scanners de TC podem capturar detalhes de até três mícrons, com alguns scanners microCT de alta resolução, que funcionam em uma escala de micrômetros muito menor, chegando a tamanhos de voxel de até 0,5 mícrons.
O equipamento microCT atual pode inspecionar metais que variam de alumínio e titânio a ligas de metal mais pesadas, como aço inoxidável e Inconel.
Quando usado para pós de metal de qualificação para impressão 3D, os scanners de TC podem fornecer aos engenheiros dados detalhados sobre a microestrutura do pó. Esses dados podem ser usados para detectar contaminantes de partículas estranhas, bem como medir o tamanho da partícula e distribuições de forma e detectar a porosidade dentro das partículas. A obtenção dessas informações é uma das maneiras pelas quais os engenheiros podem confirmar a aplicabilidade do pó para a produção.
Uma empresa que fornece serviços de tomografia computadorizada para manufatura aditiva é a Expanse Microtechnologies.
Falando em uma entrevista com a AMFG, James Hinebaugh, presidente e cofundador da empresa, observa que “Os pós são o principal ponto de interesse em toda a cadeia de fornecimento de manufatura aditiva. Entender o que faz um bom pó que se espalha e imprime bem é uma preocupação fundamental para as empresas.
“É importante entender 1) se existe uma morfologia ideal ou um tamanho ou distribuição morfológica ideal que pode interagir bem com uma ampla variedade de recobridores e impressoras e 2) como podemos reduzir os defeitos em pós, como inclusões e porosidade intrapartícula que, estudos têm mostrado, muitas vezes ficam presos em uma peça e não podem escapar da peça durante o processo de impressão. ”
Estas são as duas áreas que a Expanse Microtechnologies está abordando com sua solução proprietária de digitalização MicroCT.
A empresa desenvolveu métodos avançados de processamento de imagens, a partir dos quais é capaz de gerar relatórios aprofundados sobre a porosidade do material, a morfologia das partículas e dos poros, bem como as distribuições de tamanho e forma das partículas.
Ter essas informações permite que os usuários de manufatura aditiva identifiquem quaisquer problemas de matéria-prima e entendam as ligações entre os materiais que usam e o nível de qualidade dos componentes impressos.
Embora o teste e a qualificação de matéria-prima para fabricação de aditivos possam ser desafiadores, é uma das etapas mais importantes para garantir a qualidade de uma peça fabricada aditivamente. Atualmente, a tomografia computadorizada oferece uma das ferramentas mais robustas e úteis que podem ser usadas para validar matérias-primas AM.
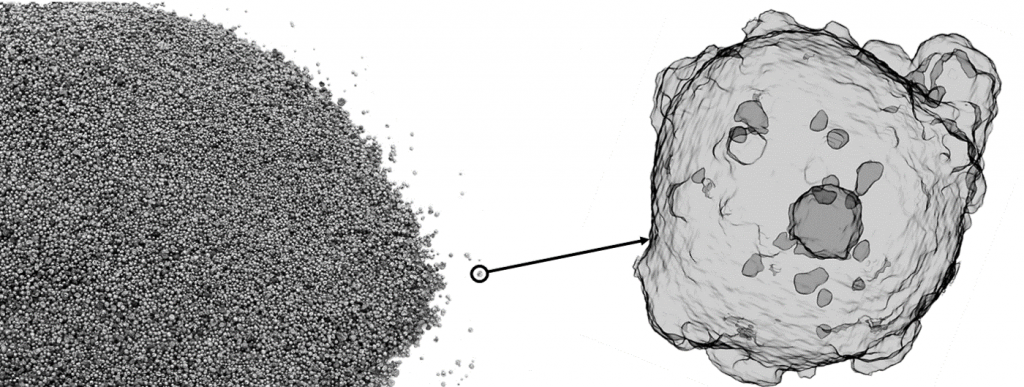
Desafio 2:Estabelecendo o controle do processo
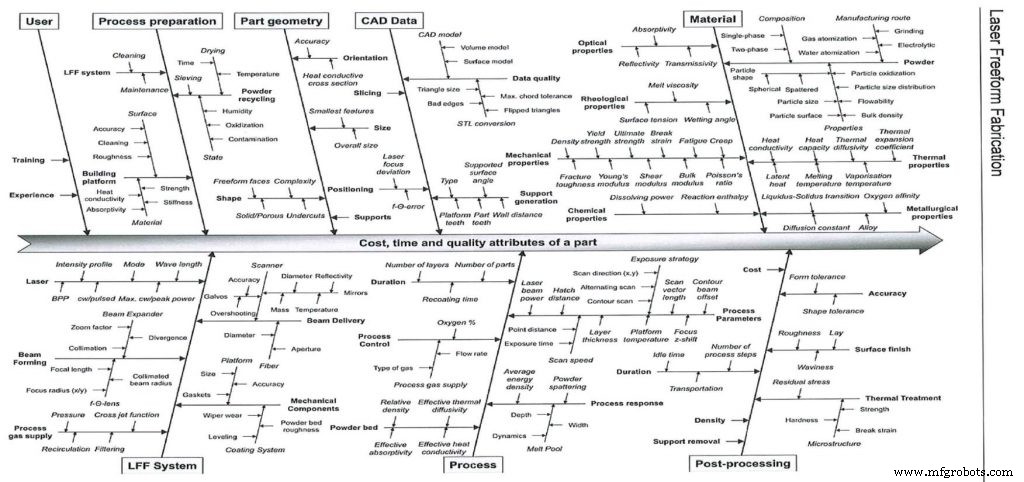
Quando se trata de impressão 3D de metal - e tecnologias de fusão de leito de pó em particular - há uma ampla gama de variáveis que podem afetar a forma e a estrutura de uma peça. Essas variáveis abrangem todo o fluxo de trabalho do AM, desde o design até a preparação da construção e pós-processamento.
Tomemos o processo de impressão como exemplo. Aqui, apenas alguns dos parâmetros que determinam o sucesso ou falha do processo incluem o caminho e a intensidade do laser e a velocidade da lâmina do recobridor da impressora. Outros fatores incluem o design das estruturas de suporte e até sutilezas como o número de vezes que o pó foi reciclado.
Embora esta lista não esteja nem perto de ser exaustiva, cada fator tem um impacto no resultado de uma construção e desvio de qualquer forma pode afetar a qualidade da peça final.
Atualmente, uma tentativa e erro é a abordagem mais comum para lidar com uma ampla gama de variáveis, a fim de alcançar um processo que produza repetibilidade partes. No entanto, isso pode envolver a fabricação da peça final várias vezes, bem como testes extensivos da própria peça. Claro, adotar essa abordagem é um processo altamente caro e ineficiente, e nega um dos principais benefícios da tecnologia - ser capaz de produzir pequenos lotes de peças de maneira econômica.
As empresas, portanto, precisam adotar uma abordagem mais sustentável e viável para o controle do processo e qualificação das peças fabricadas aditivamente.
Solução:desenvolver um sistema de controle de qualidade de ciclo fechado
Três elementos precisam ser combinados para permitir um processo de garantia de qualidade mais rápido, confiável e sustentável para peças impressas em 3D. Isso inclui planejamento de construção, monitoramento de construção e controle de feedback.
- Planejando a construção
Uma forma de entender melhor o processo de impressão é por meio de simulação. Usando simulação, os engenheiros podem testar como uma peça se comportará em um ambiente digital virtual antes que um projeto seja enviado para impressão.
Simular o processo AM permite que os engenheiros analisem os processos complexos que ocorrem durante o processo de impressão.
Como a impressão 3D em metal está sujeita a problemas como empenamento e distorção, a simulação oferece uma visão importante sobre como uma peça será distorcida durante o processo de impressão, por exemplo. Outro exemplo é o uso de simulação para determinar exatamente como o material irá derreter e solidificar.
Os engenheiros podem então usar esses dados para planejar a construção, selecionando a orientação da peça e as estratégias de suporte mais bem-sucedidas.
Dito isso, o software de simulação tem suas limitações. “Todo software de simulação de hoje tem algum nível de suposições embutidas que limitam a precisão que pode oferecer. Essa é provavelmente a maior desvantagem no momento:eles não podem ser tão precisos quanto você gostaria que fossem ”, disse Dave Conover, tecnólogo-chefe da ANSYS, falando em uma entrevista recente à AMFG.
No entanto, a tecnologia de simulação está evoluindo rapidamente, com os fornecedores de software continuando a refinar suas ofertas. Em última análise, a integração do software de simulação nas fases de projeto e planejamento ajudará a eliminar a tentativa e erro, ao mesmo tempo que reduz significativamente as chances de falhas na impressão.
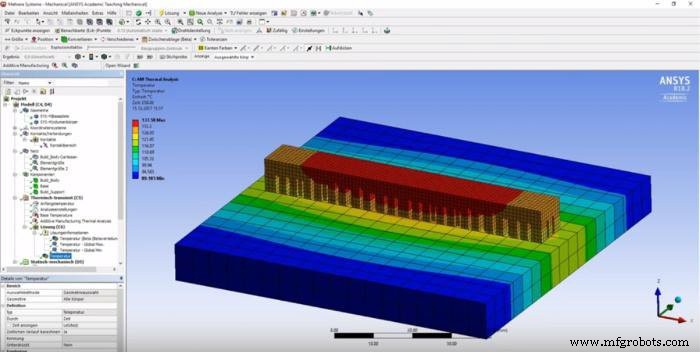
- Monitorando a construção
Os sistemas de monitoramento em processo podem auxiliar ainda mais no processo de qualificação da peça. Sensores e câmeras podem ser usados para medir vários aspectos da construção em tempo real, ajudando a documentar o processo de construção e garantir que os requisitos sejam atendidos.
Com os processos AM do leito de pó, as câmeras podem capturar o tamanho e a temperatura da piscina de fusão, que impacta diretamente a microestrutura, as propriedades do material, o acabamento da superfície e o desempenho geral da peça.
Engenheiros pode então usar esses dados para prever a probabilidade de defeitos, como empenamento ou rachadura, e intervir no processo bem antes que os defeitos ocorram. Como esses dados são documentados, isso pode ajudar a evitar as condições do processo que podem levar a esses defeitos no futuro.
Atualmente, há um número limitado de tecnologias de monitoramento em processo otimizadas para AM.
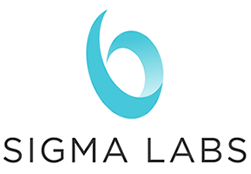
Esta combinação multifacetada, registrada como tecnologia IPQA, permite que as condições da piscina de fusão sejam otimizadas durante o processo AM, usando dados do sensor e estabelecendo métricas de qualidade no processo. Usando a análise estatística dos dados do processo, relatórios sobre a qualidade da peça podem ser gerados e usados para validar a repetibilidade.
No futuro, a empresa planeja adicionar um módulo de software ANALYTICS, com foco no aproveitamento de análises de Big Data. O módulo será capaz de extrair informações significativas e acionáveis dos dados coletados durante os processos de impressão para simplificar ainda mais o controle de qualidade no processo.
Quanto às próprias impressoras 3D, algumas já possuem a capacidade de monitoramento em processo embutida. Por exemplo, o fabricante de impressoras 3D EOS oferece o pacote de monitoramento EOSTATE. A solução de hardware e software é baseada em quatro módulos de monitoramento diferentes, incluindo System and Laser, PowderBed, MeltPool e Exposure OT (tomografia óptica), que podem capturar dados relevantes para a qualidade em tempo real. Com o EOSTATE Exposure OT, a EOS afirma ser o único fabricante de sistemas de leito de pó metálico, oferecendo aos seus clientes uma ferramenta de garantia de qualidade que incorpora tomografia óptica.
Este sistema de monitoramento utiliza uma câmera que coleta as emissões de luz no espectro do infravermelho próximo, semelhante a uma câmera de imagem térmica. Ele pode mapear totalmente cada parte em todo o processo de construção, camada por camada, independentemente de sua geometria e tamanho. Com esta abordagem, os engenheiros podem expandir a gama de fenômenos detectáveis relevantes para a qualidade das peças AM.
MTU Aero Engines é uma empresa que já começou a usar esta solução de monitoramento em suas linhas de produção em série para AM peças do motor aeronáutico.
- Fechando o ciclo
Detectar e documentar os parâmetros durante o processo de impressão é crucial. Mas a capacidade de agir com base nessas informações em tempo real - um processo conhecido como controle de feedback - é o que torna essa abordagem ainda mais eficaz. O controle de feedback, também conhecido como sistema de loop fechado, refere-se à capacidade de detectar desvios durante o processo de impressão e ajustar automaticamente o sistema para compensá-los. Manter o controle sobre o processo de construção permite que os fabricantes obtenham geometrias, acabamentos de superfície e propriedades de material consistentes que sustentam a qualidade.
Uma empresa que desenvolveu um processo AM controlado por feedback é a Velo3D. Depois de levantar mais de $ 92 milhões em financiamento, a Velo3D surgiu no verão passado com o lançamento de sua solução de metal AM de ponta a ponta. É composto pela impressora 3D Velo3D Sapphire, o software de preparação de impressão Flow e o que a empresa chama de tecnologia Intelligent Fusion.
Com estes elementos-chave fortemente integrados uns com os outros, a tecnologia permite a simulação de processos térmicos, previsão de desempenho de impressão e processamento de controle de circuito fechado. Como resultado, o sistema Sapphire pode produzir peças com geometrias desafiadoras, como saliências, virtualmente sem estruturas de suporte, de forma repetida e consistente.
O software Flow da Velo3D desempenha um papel fundamental na ativação desses benefícios. O software executa uma simulação e correção pré-impressão, otimizando o projeto e ajustando a geometria e a orientação da peça. Isso ajuda a preparar o arquivo, equilibrando as deformações, para que a peça saia corretamente. A metrologia de processo in-situ acompanhada por controle de piscina de fusão em circuito fechado funciona em conjunto com o software, aumentando, em última análise, o sucesso da primeira peça para mais de 90%.
Desafio 3:Reduzindo o erro humano
O erro humano é indiscutivelmente o maior fator de risco para garantir que uma peça impressa em 3D atenda a todos os padrões exigidos.
Isso ocorre porque a impressão 3D ainda requer mais intervenção humana do que você poderia esperar, desde o projeto e remoção dos suportes até o pós-processamento e verificação manual de que os requisitos estão sendo atendidos em todas as fases.
Este nível de intervenção humana aumenta inevitavelmente o risco de comprometimento da parte final.
Tomemos a fase de pós-produção como exemplo.
Assim que uma compilação estiver concluída, ela precisará ser descompactada e as várias partes que foram impressas nessa compilação deverão ser identificadas e inspecionadas antes de serem enviadas para o pós-processamento.
O engenheiro de produção que executa esta tarefa normalmente precisa consultar uma folha de trabalho impressa, essencialmente combinando uma imagem 2D com sua contraparte física e checando uma lista de requisitos manualmente.
Esta abordagem de inspeção não é apenas demorada, mas também remove a visibilidade do fluxo de trabalho da equação.
No entanto, muitas empresas que adotam AM consideram difícil transformar o manual tarefas envolvidas em um processo mais rápido, mais preciso e automatizado.
Visto que reduzir a probabilidade de erro humano é tão importante para garantir a qualidade das peças impressas em 3D, uma maneira de conseguir isso é usando métodos digitais para automatizar o máximo possível das etapas de inspeção.
Solução:Implementar software de fluxo de trabalho para manufatura aditiva
O software de fluxo de trabalho oferece uma plataforma digital centralizada para ajudar as equipes de projeto e produção a gerenciar seus processos de produção AM.
No contexto da garantia de qualidade, o software de fluxo de trabalho pode frequentemente fornecer a estrutura completa para ajudar as empresas a garantir que os requisitos de todas as peças sejam atendidos. Além disso, os gerentes de produção podem usar software de fluxo de trabalho para tornar o processo de inspeção de peças sem papel e rastreável. Em vez de inspecionar manualmente cada peça, com a folha de trabalho em mãos, as peças físicas podem ser comparadas com suas contrapartes digitais em 3D.
Por exemplo, a ferramenta de gerenciamento de pós-produção da AMFG fornece um visualizador 3D, que inclui todos os dados da peça, permitindo aos usuários inspecionar uma peça e suas propriedades com mais precisão.
A ferramenta permite aos usuários rastrear a proporção entre as peças bem-sucedidas e as que falharam. As peças marcadas como com falha são devolvidas automaticamente à fila de produção interna da plataforma para serem reproduzidas. A maior vantagem disso é permitir que os usuários rastreiem cada ação realizada em uma peça - adicionando rastreabilidade e responsabilidade à necessidade de gerenciamento de qualidade.
Existem padrões de controle de qualidade em todo o setor para AM?
Até agora, vimos que entender como qualificar processos, materiais e implementar estratégias digitais são essenciais para garantir que as empresas possam se beneficiar da impressão 3D para a produção.
Os padrões de toda a indústria desempenharão um papel fundamental na Este processo. Com a fabricação tradicional, os padrões já são comuns, ajudando as empresas a garantir a qualidade de seus produtos e a encontrar um terreno comum. É claro que a manufatura tradicional teve décadas, senão séculos, para desenvolver padrões relevantes. A impressão 3D, ao contrário, ainda é um processo relativamente novo e muitos padrões e certificações ainda estão em desenvolvimento. No futuro, a indústria precisará desenvolver métodos de teste, protocolos e dados de referência para reduzir o custo e o tempo para qualificar materiais, processos e peças AM. Felizmente, esta é uma área que está evoluindo rapidamente. No ano passado, a AMST International publicou seu padrão F3303, que descreve maneiras de qualificar máquinas e processos usados para construir peças usando laser ou fusão de leito de pó de feixe de elétrons. Também foi observado que um padrão adicional para apoiar a qualificação de peças, garantia de qualidade e pós-processamento de peças de fusão em leito de pó já está em andamento.
Juntamente com a ASTM International, o Instituto Nacional de Padrões e Tecnologia (NIST) está trabalhando no desenvolvimento de padrões de controle de qualidade para a indústria de AM. Por exemplo, o NIST lançou o projeto AM Part Qualification, focado em “as medições, métodos e sistemas metrológicos necessários para criar medições pós-processo robustas, desenvolver uma forte compreensão do desempenho mecânico e qualificar as peças AM”.
De olho na qualidade
Garantir a qualidade do material e o controle do processo são cruciais para a produção consistente de peças de metal de alta qualidade com impressão 3D.
Por mais complexo que possa parecer à primeira vista, os fabricantes podem se animar, pois existem soluções para apoiar o processo de garantia de qualidade, apoiadas pelo desenvolvimento contínuo de padrões para toda a indústria.
Aceitar esses desafios e implementar estrategicamente as soluções certas para a sua empresa irá ajudá-lo significativamente a capturar os benefícios da impressão 3D para aplicações exigentes e de alto valor.
impressao 3D
- Espera-se que pós de metal refratário se tornem matéria-prima para impressão 3D
- Pós de metal refratário VS Tecnologia de impressão 3D
- Considerando o que a nova tecnologia de impressão em metal significa para AM
- Controle de qualidade em tempo real:qual sistema é o certo para você?
- Estruturas de suporte para impressão 3D com metal - uma abordagem mais fácil
- H.C. AMPERPRINT de Starck:uma nova ferramenta para impressão 3D de metal
- Que pó de impressão 3D de metal você pode usar em 2020? [Guia]
- 6 Considerações importantes de projeto para impressão 3D em metal
- Dicas de design para impressão 3D de sinterização direta de metal a laser
- Visão geral da tecnologia:quando você deve realmente optar pela impressão 3D de metal