Testes contínuos de resistência de isolamento aumentam a produtividade do motor
Durante décadas, o pessoal da fábrica realizou testes de resistência de isolamento com megômetros portáteis para evitar falhas do motor que levam a desligamentos não planejados dispendiosos, penalidades por falha na produção e reparos de rebobinamento. No entanto, esses testes fornecem apenas um “instantâneo” da saúde motora. Em questão de dias, enrolamentos e cabos do motor expostos à umidade, produtos químicos, contaminantes ou vibração podem ser comprometidos e falhar na partida.
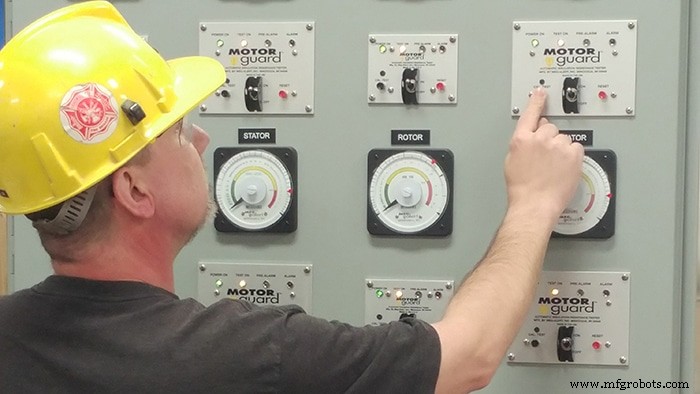
Os megaohmímetros portáteis também exigem que os técnicos elétricos desconectem manualmente os cabos do equipamento e conectem as pontas de prova em equipamentos potencialmente energizados ou danificados para realizar o teste manual. Esses testes expõem os técnicos a potenciais arcos elétricos quando acessam o gabinete. Nos Estados Unidos, os incidentes de arco elétrico não fatais ocorrem aproximadamente cinco a dez vezes por dia, com fatalidades na taxa de aproximadamente uma por dia.
Com tanto em risco, os gerentes de fábrica estão reconhecendo o valor do monitoramento contínuo de megohms da resistência de isolamento que inicia no momento em que o motor é desligado até que seja reiniciado.
Armado com essas informações em tempo real, o pessoal de manutenção pode tomar ações corretivas antecipadamente para evitar uma falha que interromperia a produção. Ao fazer isso, eles podem economizar centenas de milhares de dólares em taxas de reparo para rebobinamento caro, multas por falha na produção e perda de tempo de produção.
Além disso, os dispositivos de teste automáticos instalados permanentemente permitem o monitoramento “sem intervenção” sem ter que acessar os gabinetes – mantendo os técnicos fora de perigo.
Proteção de motores em concessionárias
Não importa a indústria, as plantas de fabricação e processamento dependem muito de motores, embora o número e o tipo variem dependendo do tamanho da planta e do tipo de combustível queimado. Algumas plantas podem ter de 20 a 30 motores críticos, com cinco a dez em média.
Motores críticos são aqueles que podem prejudicar significativamente a capacidade de atender aos objetivos de negócios com segurança ou afetar os níveis de produção se ficarem offline inesperadamente. Exemplos incluem motores que variam de 480 a 13.800 V usados para operar compressores, bombas e ventiladores.
A maioria das concessionárias mantém esses motores por meio de programas de manutenção preventiva (PM) baseados em tempo. Os testes de resistência de isolamento são normalmente programados semestralmente. No entanto, dada a redução de pessoal na maioria das fábricas, pode até ser menos frequente. Com base nesses testes, os motores podem ser programados para serem enviados para oficinas de reparo para recondicionamento.
Normalmente, os testes de resistência de isolamento também são realizados no início de revisões anuais ou interrupções planejadas para identificar quaisquer motores que também precisem de reparos. Ainda assim, apesar dos programas de PM, os motores que estão off-line ou com ciclos frequentes podem ser rapidamente comprometidos. “Tivemos nosso quinhão de falhas de motor e ficou bastante caro”, disse Richard Hohlman, que se aposentou após 37 anos trabalhando em usinas de geração de energia.
“Às vezes, as falhas podem ser muito caras”, disse ele. “Naquela planta em particular, tínhamos alguns motores de indução PAM AC de duas velocidades Westinghouse e rebobinar um deles teria sido uma despesa de seis dígitos.”
Do ponto de vista de O&M (Operações e Manutenção), “se pudermos identificar um motor fraco e evitar o risco de tentar dar a partida e falhar, isso é uma grande economia”, acrescentou.
Para evitar motores com falha, Hohlman disse que exigia que todos os motores críticos em uma usina de Long Island Sound de 1.500 mW que foram desligados por 24 horas ou mais fossem testados manualmente com um megôhmetro antes de serem reiniciados. “Isso se tornou uma despesa em si, porque os testes geralmente são realizados em diferentes horas do dia, com taxas de horas extras”, disse Hohlman. “Mas, ao fazê-lo, evitamos uma série de falhas no motor.”
Hohlman disse que um membro de sua equipe descobriu o Meg-Alert, um dispositivo de teste e monitoramento contínuo fabricado pela Meg-Alert, Minocqua, Wisconsin. A planta o instalou inicialmente em quatro bombas de circulação e vários ventiladores de tiragem induzida. Mais tarde, os dispositivos também foram adicionados a vários ventiladores de tiragem forçada e outros motores críticos em toda a planta.
A unidade Meg-Alert é instalada permanentemente dentro do compartimento de alta tensão do CCM ou quadro e conecta-se diretamente aos enrolamentos do motor ou gerador. A unidade detecta quando o motor ou gerador está off-line e realiza um teste dielétrico contínuo no isolamento do enrolamento até que o equipamento seja reiniciado.
A unidade funciona aplicando uma tensão de teste CC não destrutiva e com limitação de corrente aos enrolamentos de fase e, em seguida, mede com segurança qualquer corrente de fuga através do isolamento de volta ao terra. O sistema usa níveis de tensão CC de 500, 1.000, 2.500 ou 5.000 V que atendem aos padrões internacionais IEEE, ABS, ANSI/NETA e ASTM para tensão de teste de resistência de isolamento adequada com base na tensão de operação do equipamento.
O teste não causa qualquer deterioração do isolamento e inclui tecnologia de limitação de corrente que protege o pessoal.
“Com monitoramento contínuo, a equipe de O&M está sempre ciente da aptidão do motor para o trabalho”, disse Hohlman. “Toda vez que o motor desliga – seja por segundos, um dia ou pelos 10 dias de interrupção – o motor está sendo testado. E se ficar abaixo de um nível seguro, ele alarma imediatamente e pode travar o motor desde a partida.”
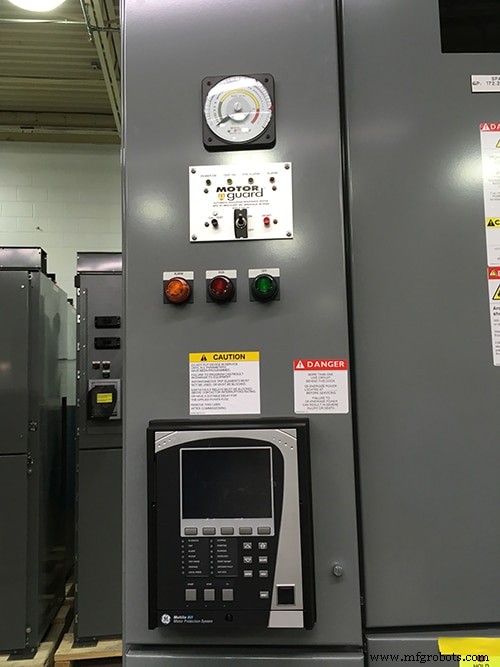
Isso contrasta fortemente com o instantâneo tirado por um megôhmetro no início de um desligamento. O motor pode absorver rapidamente umidade considerável devido à umidade e contaminação.
“Um motor elétrico pode absorver umidade suficiente em apenas algumas horas na região sul do país para causar danos na partida”, disse Ricky Loupe, gerente elétrico e de instrumentos de uma grande fábrica que produz uma forma de policloreto de vinila em pó. PVC), bem como o ingrediente principal componente, cloreto de vinil. “Tem muitos dias de chuva com alta umidade aqui no Sul, e umidade e eletricidade não se misturam.
“Quando um motor está cheio de umidade e é ligado, os enrolamentos vão para o solo e danificam o motor”, continuou Loupe. “Então agora você tem um motor crítico com enrolamentos danificados que custarão uma quantia significativa de dinheiro para consertar.”
Engenheiro na época, ele e sua equipe realizaram uma análise para determinar a causa raiz do problema e como evitá-lo. Depois de aprender mais sobre o Meg-Alert, ele comprou um como teste. Loupe disse que foi instalado em um motor de gabinete WP de 4.160 V e 1.200 hp que foi usado para acionar um compressor em uma unidade de resfriamento.
Com base nos requisitos de produção, alguns dos chillers foram desligados e usados apenas quando necessário. Isso significava que os motores em algumas das unidades poderiam ficar ociosos. Antes de operar um chiller novamente, os motores tiveram que ser testados usando megôhmetros portáteis. “Muitas vezes, esse trabalho era fora do expediente, devido às demandas das operações e à necessidade de iniciá-las o mais rápido possível”, explicou Loupe. “Tínhamos técnicos que vinham nos fins de semana – frequentemente em horas extras – apenas para testar os motores para que pudessem dar partida.”
Loupe disse com as unidades Meg-Alert, que as informações já estão disponíveis em tempo real. Ele ficou ainda mais convencido depois que o dispositivo, que está conectado ao motor de partida, não permitiria que o motor ligasse devido a baixas leituras de resistência de megohm após um dia chuvoso. “O Meg-Alert não permitia a partida do motor porque havia muita umidade no motor”, explicou Loupe. “Isso, ali mesmo, pagou dez vezes mais pela unidade de monitoramento contínuo.”
Hoje, a planta possui Meg-Alerts em todos os dez motores do chiller, bem como em quatro bombas de torre de resfriamento de 900 hp em outra área da planta.
Monitoramento "interno"
O sistema de monitoramento contínuo também permite uma abordagem “sem intervenção” que não exige que os técnicos de serviço acessem os gabinetes de controle para realizar um teste manual de resistência de isolamento. Em vez disso, um medidor analógico externo na porta do gabinete de controle mostra as leituras de resistência de isolamento medidas em megaohms em tempo real. O medidor também indica níveis de isolamento bom, razoável e ruim por meio de um esquema de cores simples “verde, amarelo, vermelho”.
Quando os níveis predeterminados do ponto de ajuste da resistência de isolamento são atingidos, as luzes indicadoras acendem para sinalizar uma condição de alarme e notificações automáticas podem ser enviadas para a rede de monitoramento. O monitoramento contínuo também pode mostrar se os aquecedores usados para manter as temperaturas térmicas ou evitar a condensação estão funcionando corretamente.
A maioria dos motores utiliza aquecedores para manter a temperatura dentro do motor para que não varie drasticamente da temperatura de operação ou da temperatura ambiente fora da unidade. Se ficar abaixo do ponto de orvalho, o motor começará a coletar condensação enquanto estiver offline.
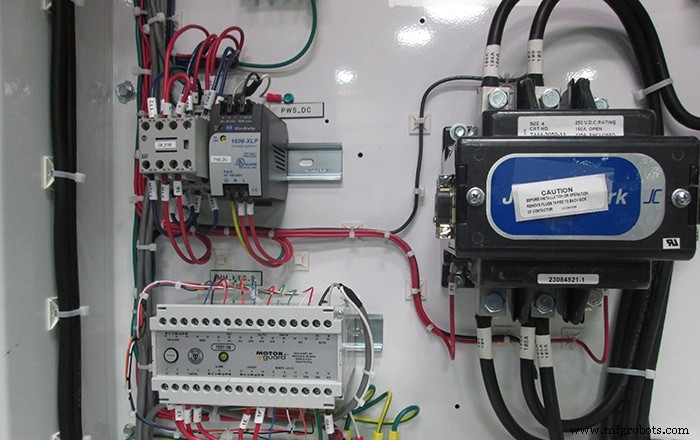
No entanto, se esses aquecedores não funcionarem corretamente ou o disjuntor for desarmado, o pessoal de manutenção pode não estar ciente disso até que o motor falhe na partida. Embora esses aquecedores de motor sejam verificados regularmente, isso pode deixar motores e geradores críticos desprotegidos por semanas ou até meses.
Evitando arcos elétricos
Talvez mais importante, Loupe disse que a abordagem prática reduz a exposição dos funcionários a possíveis danos causados por arcos elétricos. “Com os dispositivos de monitoramento contínuo da resistência de isolamento, você elimina o dano potencial dos arcos elétricos por não ter o técnico aberto os gabinetes para testes de megohm”, disse Loupe.
Os flashes de arco são uma descarga elétrica indesejada que viaja pelo ar entre condutores ou de um condutor para o solo. O flash é imediato e pode produzir temperaturas quatro vezes maiores que a da superfície do sol. O calor intenso também causa uma expansão repentina do ar, o que resulta em uma onda de choque que pode arremessar os trabalhadores pelas salas e derrubá-los das escadas. As lesões por arco elétrico incluem queimaduras de terceiro grau, cegueira, perda auditiva, danos nos nervos, parada cardíaca e até morte.
Entre as causas potenciais de um arco voltaico listadas pela NFPA 70E inclui “uso impróprio de equipamento de teste”. Embora seja recomendado desenergizar o equipamento antes de testar e usar equipamento de proteção individual (EPI) apropriado, a melhor solução é eliminar a necessidade de acessar os painéis de controle para realizar testes de resistência de isolamento.
Além do risco de arcos elétricos, a Lupa testemunhou em primeira mão outro risco potencial que pode ocorrer se um motor entrar em curto a poucos metros de um funcionário. Na fábrica, o pessoal está a apenas cerca de um metro e meio de distância do motor ao dar partida no resfriador. Se o motor entrar em curto, ele pode fazer um barulho enorme e lançar uma massa de faíscas.
“Com o monitoramento contínuo da resistência de isolamento, você não tem um funcionário em perigo se o motor falhar na partida”, disse Loupe. “O dispositivo também evita essa preocupação de segurança.”
Para obter mais informações, visite www.megalert.com ou ligue para 800-778-5689.
Sistema de controle de automação
- Motores de indução monofásicos
- Motores do comutador CA
- Dica de teste:Defeitos de armadura em motores DC
- Dica técnica:Motores
- IQ Motion Control lança nova linha de servomotores
- A área cinzenta entre servomotores e motores de passo
- Sobre motores industriais e aplicações
- Uma introdução ao motor BLDC
- Emparelhamento de redutores com servomotores
- Manutenção adequada dos motores do compressor