Bloco de concreto
Antecedentes
Um bloco de concreto é usado principalmente como material de construção na construção de paredes. Às vezes é chamada de unidade de alvenaria de concreto (CMU). Um bloco de concreto é um dos vários produtos de concreto pré-moldado usados na construção. O termo pré-moldado se refere ao fato de que os blocos são formados e endurecidos antes de serem trazidos para o local de trabalho. A maioria dos blocos de concreto tem uma ou mais cavidades ocas, e seus lados podem ser moldados lisos ou com um desenho. Em uso, os blocos de concreto são empilhados um de cada vez e mantidos juntos com argamassa de concreto fresca para formar o comprimento e a altura desejados da parede.
A argamassa de concreto era usada pelos romanos já em 200 a.C. para ligar pedras moldadas na construção de edifícios. Durante o reinado do imperador romano Calígula, em 37-41 D.C. , pequenos blocos de concreto pré-moldado foram usados como material de construção na região em torno da atual Nápoles, Itália. Muito da tecnologia de concreto desenvolvida pelos romanos foi perdida após a queda do Império Romano no século V. Somente em 1824 o pedreiro inglês Joseph Aspdin desenvolveu o cimento portland, que se tornou um dos principais componentes do concreto moderno.
O primeiro bloco de concreto oco foi projetado em 1890 por Harmon S. Palmer nos Estados Unidos. Após 10 anos de experimentos, Palmer patenteou o projeto em 1900. Os blocos de Palmer tinham 8 pol. (20,3 cm) por 10 pol. (25,4 cm) por 30 pol. (76,2 cm), e eram tão pesados que tiveram que ser erguidos no lugar com um pequeno guindaste. Em 1905, cerca de 1.500 empresas estavam fabricando blocos de concreto nos Estados Unidos.
Esses primeiros blocos eram geralmente moldados à mão e a produção média era de cerca de 10 blocos por pessoa por hora. Hoje, a fabricação de blocos de concreto é um processo altamente automatizado que pode produzir até 2.000 blocos por hora.
Matérias-primas
O concreto comumente usado para fazer blocos de concreto é uma mistura de cimento Portland em pó, água, areia e cascalho. Isso produz um bloco cinza claro com uma textura de superfície fina e uma alta resistência à compressão. Um bloco de concreto típico pesa 38-43 lb (17,2-19,5 kg). Em geral, a mistura de concreto usada para blocos tem uma porcentagem maior de areia e uma porcentagem menor de cascalho e água do que as misturas de concreto usadas para fins gerais de construção. Isso produz uma mistura muito seca e rígida que mantém sua forma quando é removida do molde de bloco.
Se carvão granulado ou cinzas vulcânicas forem usados em vez de areia e cascalho, o bloco resultante é comumente chamado de bloco de concreto. Isso produz um bloco cinza escuro com uma textura de superfície média a grossa, boa resistência, boas propriedades de amortecimento de som e um valor de isolamento térmico mais alto do que um bloco de concreto. Um bloco de concreto típico pesa 26-33 lb (11,8-15,0 kg).
Os blocos de concreto leves são feitos substituindo a areia e o cascalho por argila expandida, xisto ou ardósia. Argila expandida, xisto e ardósia são produzidos triturando as matérias-primas e aquecendo-as a cerca de 2.000 ° F (1093 ° C). Nessa temperatura, o material incha, ou incha, por causa da rápida geração de gases causada pela combustão de pequenas quantidades de matéria orgânica aprisionada em seu interior. Um bloco de peso leve típico pesa 22-28 lb (10,0-12,7 kg) e é usado para construir paredes e divisórias não resistentes. A escória expandida de alto-forno, bem como materiais vulcânicos naturais, como pedra-pomes e escória, também são usados para fazer blocos leves.
Além dos componentes básicos, a mistura de concreto usada para fazer os blocos também pode conter vários produtos químicos, chamados de aditivos, para alterar o tempo de cura, aumentar a resistência à compressão ou melhorar a trabalhabilidade. A mistura pode ter pigmentos adicionados para dar aos blocos uma cor uniforme por completo, ou a superfície dos blocos pode ser revestida com um esmalte cozido para dar um efeito decorativo ou para fornecer proteção contra ataques químicos. Os esmaltes são geralmente feitos com um aglutinante resinoso termoendurecível, areia de sílica e pigmentos coloridos.
Design
As formas e tamanhos dos blocos de concreto mais comuns foram padronizados para garantir a construção uniforme do edifício. O tamanho de bloco mais comum nos Estados Unidos é referido como um bloco de 8 por 8 por 16, com as medidas nominais de 8 pol (20,3 cm) de altura por 8 pol. (20,3 cm) de profundidade por 16 pol. (40,6 cm) de largura. Esta medida nominal inclui espaço para um cordão de argamassa, e o bloco em si mede 7,63 pol. (19,4 cm) de altura por 7,63 pol. (19,4 cm) de profundidade por 15,63 pol. (38,8 cm) de largura.
Muitos fabricantes de blocos progressivos oferecem variações do bloco básico para obter efeitos visuais exclusivos ou para fornecer recursos estruturais desejáveis para aplicações especializadas. Por exemplo, um fabricante oferece um bloco projetado especificamente para resistir ao vazamento de água pelas paredes externas. O bloco incorpora uma mistura repelente de água para reduzir a absorção e permeabilidade do concreto, uma borda superior chanfrada para eliminar a água da junta de argamassa horizontal e uma série de ranhuras e canais internos para direcionar o fluxo de qualquer vazamento induzido por fissura para longe do superfície interior.
Outro desenho de bloco, denominado bloco de face dividida, inclui uma textura áspera semelhante a uma pedra em uma das faces do bloco, em vez de uma face lisa. Isso dá ao bloco a aparência arquitetônica de uma pedra lapidada e polida.
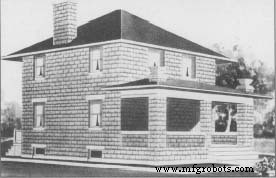
Os blocos de concreto foram usados pela primeira vez nos Estados Unidos como substitutos de pedra ou madeira na construção de casas. O primeiro exemplo conhecido de uma casa construída neste país inteiramente de blocos de concreto foi em 1837 em Staten Island, Nova York. As casas construídas com blocos de concreto mostraram um uso criativo de materiais comuns e baratos feitos para se parecerem com os mais caros e tradicionais edifícios de alvenaria de pedra com estrutura de madeira. Este novo tipo de construção se tornou uma forma popular de construção de casas no início dos anos 1900 até a década de 1920. Os estilos de casas, muitas vezes chamados de "modernos" na época, variavam de Tudor a Quadrangular, Revival Colonial a Bangalô. Enquanto muitas casas usaram os blocos de concreto como estrutura, bem como a superfície da parede externa, outras casas usaram estuque ou outros revestimentos sobre a estrutura do bloco. Centenas de milhares dessas casas foram construídas especialmente nos estados do meio-oeste, provavelmente porque as matérias-primas necessárias para fazer blocos de concreto eram abundantes em bancos de areia e poços de cascalho em toda a região. Os blocos de concreto foram confeccionados com desenhos de faces para simular texturas de pedra:face rochosa, face granítica ou rusticada. Inicialmente consideradas um material experimental, as casas construídas com blocos de concreto eram anunciadas nos catálogos de muitos fabricantes de cimento de Portland como "à prova de fogo, à prova de vermes e à prova de intempéries" e como um substituto barato para o suprimento cada vez mais escasso de madeira. Muitos outros tipos de edifícios, como garagens, silos e correios, foram construídos e continuam a ser construídos hoje usando esse método de construção por causa dessas qualidades.
Cynthia Read-Miller
Quando os fabricantes projetam um novo bloco, eles devem considerar não apenas a forma desejada, mas também o processo de fabricação necessário para fazer essa forma. Formas que requerem
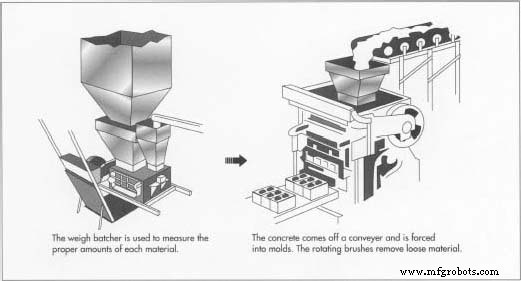
O processo de fabricação
A produção de blocos de concreto consiste em quatro processos básicos:mistura, moldagem, cura e cubagem. Algumas fábricas produzem apenas blocos de concreto, enquanto outras podem produzir uma ampla variedade de produtos de concreto pré-moldado, incluindo blocos, pedras de pavimentação planas e peças decorativas de paisagismo, como bordas de gramado. Algumas fábricas são capazes de produzir 2.000 ou mais blocos por hora.
As etapas a seguir são comumente usadas para fabricar blocos de concreto.
Mistura
- 1 A areia e o cascalho são armazenados externamente em pilhas e são transferidos para caixas de armazenamento na planta por uma correia transportadora conforme necessário. O cimento Portland é armazenado externamente em grandes silos verticais para protegê-lo da umidade.
- 2 Quando uma operação de produção começa, as quantidades necessárias de areia, cascalho e cimento são transferidas por gravidade ou por meios mecânicos para um dosador de pesagem que mede as quantidades adequadas de cada material.
- 3 Os materiais secos fluem para um misturador estacionário onde são misturados por vários minutos. Existem dois tipos de misturadores comumente usados. Um tipo, chamado de misturador planetário ou panela, assemelha-se a uma panela rasa com uma tampa. As lâminas de mistura são fixadas a um eixo rotativo vertical dentro do misturador. O outro tipo é chamado de mixer de bateria horizontal. Ele se assemelha a uma lata de café virada de lado e tem lâminas de mistura presas a um eixo giratório horizontal dentro do misturador.
- 4 Depois que os materiais secos são misturados, uma pequena quantidade de água é adicionada ao misturador. Se a planta estiver localizada em um clima sujeito a extremos de temperatura, a água pode primeiro passar por um aquecedor ou resfriador para regular sua temperatura. Produtos químicos de mistura e pigmentos corantes também podem ser adicionados neste momento. O concreto é então misturado por seis a oito minutos.
Moldagem
- 5 Uma vez que a carga de concreto esteja completamente misturada, ela é despejada em um local inclinado
transportador de caçamba e transportado para uma tremonha elevada. O ciclo de mistura começa novamente para a próxima carga.
- 6 Da tremonha, o concreto é transportado para outra tremonha no topo da máquina de blocos em uma taxa de fluxo medida. Na máquina de blocos, o concreto é forçado para baixo em moldes. Os moldes consistem em uma caixa de molde externa contendo vários revestimentos de molde. Os liners determinam a forma externa do bloco e a forma interna das cavidades do bloco. Até 15 blocos podem ser moldados de uma vez.
- 7 Quando os moldes estão cheios, o concreto é compactado pelo peso da cabeça superior do molde descendo nas cavidades do molde. Esta compactação pode ser complementada por cilindros de pressão pneumática ou hidráulica atuando na cabeça do molde. A maioria das máquinas de bloco também usa uma curta explosão de vibração mecânica para auxiliar ainda mais na compactação.
- 8 Os blocos compactados são empurrados para baixo e para fora dos moldes em um palete plano de aço. O palete e os blocos são empurrados para fora da máquina e para um transportador de corrente. Em algumas operações, os blocos passam sob uma escova rotativa que remove o material solto da parte superior dos blocos.
Cura
- 9 Os paletes de blocos são transportados para um empilhador ou carregador automatizado que os coloca em uma prateleira de cura. Cada rack contém várias centenas de blocos. Quando um rack está cheio, ele é enrolado em um conjunto de trilhos e movido para um forno de cura.
-
10 O forno é uma sala fechada com capacidade para conter várias estantes de blocos ao mesmo tempo. Existem dois tipos básicos de fornos de cura. O tipo mais comum é um forno a vapor de baixa pressão. Nesse tipo, os blocos são mantidos no forno por uma a três horas em temperatura ambiente para permitir um leve endurecimento. O vapor é então introduzido gradualmente para aumentar a temperatura a uma taxa controlada de não mais do que 60 ° F por hora (16 ° C por hora). Os blocos de peso padrão são geralmente curados a uma temperatura de 150-165 ° F (66-74 ° C), enquanto os blocos leves são curados a 170-185 ° F (77-85 ° C). Quando a temperatura de cura é atingida, o vapor é desligado e os blocos são deixados de molho no ar quente e úmido por 12-18 horas. Após a imersão, os blocos são secos exaurindo o ar úmido e aumentando ainda mais a temperatura no forno. Todo o ciclo de cura leva cerca de 24 horas.
Outro tipo de forno é o forno a vapor de alta pressão, às vezes chamado de autoclave. Neste tipo, a temperatura é elevada para 300-375 ° F (149-191 ° C) e a pressão é elevada para 80-185 psi (5,5-12,8 bar). Os blocos são deixados de molho por cinco a 10 horas. A pressão é então liberada rapidamente, o que faz com que os blocos liberem rapidamente a umidade presa. O processo de cura em autoclave requer mais energia e um forno mais caro, mas pode produzir blocos em menos tempo.
Cubos
- 11 As estantes de blocos curados são desenroladas para fora do forno e os paletes de blocos são desempilhados e colocados em uma esteira transportadora. Os blocos são empurrados para fora dos paletes de aço e os paletes vazios são alimentados de volta na máquina de blocos para receber um novo conjunto de blocos moldados.
- 12 Se os blocos devem ser feitos em blocos de faces divididas, eles são primeiro moldados como dois blocos unidos. Depois que esses blocos duplos estão curados, eles passam por um divisor, que os atinge com uma lâmina pesada ao longo da seção entre as duas metades. Isso faz com que o bloco duplo se quebre e forme uma textura áspera de pedra em uma das faces de cada peça.
- 13 Os blocos passam por um cubador que alinha cada bloco e os empilha em um cubo de três blocos de largura por seis de profundidade por três ou quatro blocos de altura. Esses cubos são transportados para fora com uma empilhadeira e armazenados.
Controle de qualidade
A fabricação de blocos de concreto requer monitoramento constante para produzir blocos que tenham as propriedades exigidas. As matérias-primas são pesadas eletronicamente antes de serem colocadas no misturador. O conteúdo de água presa na areia e no cascalho pode ser medido com sensores ultrassônicos e a quantidade de água a ser adicionada à mistura é ajustada automaticamente para compensar. Em áreas com temperaturas extremas, a água pode passar por um resfriador ou aquecedor antes de ser usada.
Conforme os blocos emergem da máquina de blocos, sua altura pode ser verificada com sensores de feixe de laser. No forno de cura, as temperaturas, pressões e tempos de ciclo são todos controlados e registrados automaticamente para garantir que os blocos sejam curados adequadamente, a fim de atingir a resistência necessária.
O Futuro
O bloco de concreto simples continuará a evoluir à medida que arquitetos e fabricantes de blocos desenvolvem novas formas e tamanhos. Esses novos blocos prometem tornar a construção civil mais rápida e econômica, além de resultar em estruturas mais duráveis e energeticamente eficientes. Alguns dos projetos de blocos possíveis para o futuro incluem o bloco biaxial, que tem cavidades que correm tanto horizontal quanto verticalmente para permitir o acesso para encanamentos e conduítes elétricos; o bloco de revestimento empilhado, que consiste em três seções que formam as paredes internas e externas; e o bloco de aquecimento, que armazena calor para resfriar os cômodos internos no verão e aquecê-los no inverno. Esses projetos foram incorporados a um protótipo de casa, denominado Lifestyle 2000, que é o resultado de um esforço cooperativo entre a National Association of Home Builders e a National Concrete Masonry Association.
Processo de manufatura