Lata de alumínio para bebidas
Antecedentes
Noventa e cinco por cento de todas as cervejas e refrigerante as latas nos Estados Unidos são feitas de alumínio. Os fabricantes de latas americanos produzem cerca de 100 bilhões de latas de alumínio para bebidas por ano, o equivalente a uma lata por americano por dia. Embora quase todas as latas de alimentos sejam feitas de aço, as propriedades exclusivas do alumínio o tornam ideal para conter bebidas carbonatadas. A lata de alumínio típica pesa menos de meia onça, mas suas paredes finas suportam mais de 36 quilos de pressão por polegada quadrada exercida pelo dióxido de carbono na cerveja e refrigerantes. O acabamento brilhante do alumínio também o torna um fundo atraente para impressão decorativa, importante para um produto que deve chamar a atenção dos consumidores em um mercado competitivo.
O alumínio foi identificado pela primeira vez como um elemento em 1782, e o metal gozava de grande prestígio na França, onde na década de 1850 estava mais na moda do que ouro e prata para joias e utensílios de cozinha. Napoleão III ficou fascinado com os possíveis usos militares do metal leve e financiou os primeiros experimentos na extração de alumínio. Embora o metal seja encontrado em abundância na natureza, um processo de extração eficiente permaneceu indefinido por muitos anos. O alumínio permaneceu extremamente caro e, portanto, de pouco uso comercial ao longo do século XIX. Os avanços tecnológicos no final do século 19 finalmente permitiram que o alumínio fosse fundido de forma barata, e o preço do metal caiu drasticamente. Isso abriu o caminho para o desenvolvimento de usos industriais do metal.
O alumínio não era usado para latas de bebidas até depois da Segunda Guerra Mundial. Durante a guerra, o governo dos Estados Unidos despachou grandes quantidades de cerveja em latas de aço para seus soldados no exterior. Depois da guerra, a maior parte da cerveja foi novamente vendida em garrafas, mas os soldados que voltaram mantiveram um gosto nostálgico por latas. Os fabricantes continuaram a vender cerveja em latas de aço, embora as garrafas fossem mais baratas de produzir. A Adolph Coors Company fabricou a primeira lata de cerveja de alumínio em 1958. Sua lata de duas peças só podia conter 7 onças (198 g), em vez das 12 (340 g) usuais, e havia problemas com o processo de produção. No entanto, a lata de alumínio se mostrou popular o suficiente para incitar a Coors, junto com outras empresas de metal e alumínio, a desenvolver latas melhores.
O próximo modelo era uma lata de aço com tampa de alumínio. Este híbrido pode ter várias vantagens distintas. A ponta do alumínio alterou a reação galvânica entre a cerveja e o aço, resultando em cerveja com o dobro da vida útil daquela armazenada em latas de aço. Talvez a vantagem mais significativa da parte superior de alumínio fosse que o metal macio podia ser aberto com uma simples aba de puxar. As latas de estilo antigo exigiam o uso de um abridor especial popularmente chamado de "chave da igreja", e quando a Schlitz Brewing Company introduziu sua cerveja em uma lata "pop top" de alumínio em 1963, outros grandes fabricantes de cerveja rapidamente aderiram ao vagão da banda. No final daquele ano, 40% de todas as latas de cerveja dos EUA tinham tampas de alumínio e, em 1968, esse número dobrou para 80%.
Enquanto as latas de alumínio dominavam o mercado, vários fabricantes buscavam uma lata de bebida mais ambiciosa, toda em alumínio. A tecnologia que a Coors usou para fazer sua lata de alumínio de 7 onças dependia do processo de "extrusão por impacto",
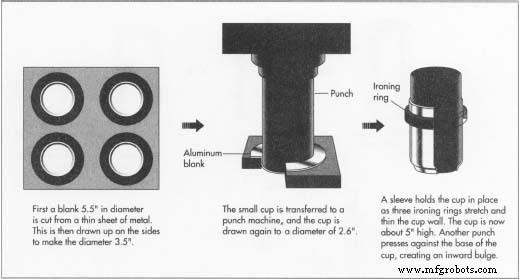
Matérias-primas
A matéria-prima da lata de alumínio para bebidas é, obviamente, o alumínio. O alumínio é derivado de um minério chamado bauxita. Os produtores de alumínio dos EUA importam bauxita, principalmente da Jamaica e da Guiné. A bauxita é refinada e fundida, e o alumínio fundido resultante é fundido em lingotes. A base de alumínio para latas de bebidas consiste principalmente em alumínio, mas também contém pequenas quantidades de outros metais. Normalmente, são 1% de magnésio, 1% de manganês, 0,4% de ferro, 0,2% de silício e 0,15% de cobre. Grande parte do alumínio usado na indústria de latas de bebidas é derivado de material reciclado. Vinte e cinco por cento do suprimento total de alumínio da América vem de sucata reciclada, e a indústria de latas de bebidas é a principal usuária do material reciclado. A economia de energia é significativa quando as latas usadas são fundidas novamente, e a indústria de latas de alumínio agora recupera mais de 63% das latas usadas.
O processo de fabricação
Cortando o espaço em branco
- 1 O método moderno para fazer latas de bebidas de alumínio é chamado de desenho de duas peças e passagem de parede. O processo começa com um lingote de alumínio que foi fundido para ter cerca de 30 polegadas (76 cm) de espessura e, em seguida, enrolado em uma folha fina. A primeira etapa na fabricação real da lata é cortar a folha em um círculo, chamado de blank, que formará o fundo e as laterais da lata. Cada peça em branco tem 5,5 polegadas (14 cm) de diâmetro. Algum material é necessariamente
As pequenas ondulações no topo do metal são chamadas de "orelhas". "Earing" é um efeito inevitável da estrutura cristalina da folha de alumínio. perdidos entre cada círculo, mas os fabricantes descobriram que o alumínio mínimo é perdido quando as folhas são largas o suficiente para conter duas fileiras escalonadas de sete blocos cada. Cerca de 12-14% da folha é desperdiçada, mas pode ser reutilizada como refugo. Depois que a peça em branco circular é cortada, ela é "desenhada" ou puxada para formar um copo de 3,5 polegadas (8,9 cm) de diâmetro.
Redesenhando a xícara
- 2 O copinho resultante do sorteio inicial é então transferido para uma segunda máquina. Uma manga mantém o copo precisamente no lugar e um punção baixado rapidamente para dentro do copo o redesenha para um diâmetro de cerca de 2,6 polegadas (6,6 cm). A altura do copo aumenta simultaneamente dos 3,3 a 5,7 cm iniciais (1,3 a 2,25 polegadas). O ponche então empurra o copo contra três anéis chamados anéis de passar, que esticam e afinam as paredes do copo. Toda essa operação - esticar e passar - é feita em um golpe de punção contínuo, que leva apenas um quinto de segundo para ser concluído. O copo agora tem cerca de 13 cm de altura. Em seguida, outro soco pressiona a base do copo, fazendo com que o fundo se projete para dentro. Essa forma neutraliza a pressão do líquido carbonatado que a lata contém. As paredes inferior e inferior da lata também são um pouco mais grossas do que as paredes superiores, para maior resistência.
Cortando as orelhas
- 3 O processo de estampagem e passagem a ferro deixa a lata levemente ondulada na parte superior. Essas pequenas ondulações no metal são chamadas de "orelhas". "Earing" é um efeito inevitável da estrutura cristalina da folha de alumínio. As empresas de alumínio estudaram esse fenômeno extensivamente e foram capazes de influenciar o posicionamento e a altura das orelhas controlando o enrolamento da folha de alumínio. No entanto, algum material é perdido nesta fase. Cerca de um quarto de polegada é aparado do topo da lata, deixando as paredes superiores retas e niveladas.
Limpeza e decoração
- 4 O processo de estampagem e passagem a ferro deixa a parede externa da lata com uma superfície lisa e brilhante, não necessitando de outros acabamentos como polimento. Depois que as orelhas são aparadas, a lata é limpa e impressa com seu rótulo. Depois que a lata é decorada, ela é pressionada ligeiramente na parte superior para formar um gargalo, e o gargalo recebe uma aba para fora na borda superior, que será dobrada assim que a tampa for colocada.
A tampa
- 5 A tampa é feita de uma liga ligeiramente diferente do alumínio para a base e as laterais da lata. A protuberância interna do fundo da lata ajuda a suportar a pressão exercida pelo líquido dentro dela, mas a tampa plana deve ser mais rígida e forte do que a base, por isso é feita de alumínio com mais magnésio e menos manganês do que o resto a lata. Isso resulta em um metal mais forte e a tampa é consideravelmente mais espessa do que as paredes. A tampa é cortada em um diâmetro de 2,1 polegadas (5,3 cm), menor do que o diâmetro de 2,6 polegadas (6,6 cm) das paredes. O centro da tampa é esticado ligeiramente para cima e puxado por uma máquina para formar um rebite. A aba de puxar, uma peça separada de metal, é inserida sob o rebite e fixada por ele. Em seguida, a tampa é ranhurada para que, quando a aba for puxada pelo consumidor, o metal se solte facilmente e saia pela abertura adequada.
Para garantir que as latas sejam feitas corretamente, elas são verificadas automaticamente quanto a rachaduras e furos. Normalmente, uma em cada 50.000 latas apresenta defeito.
Preenchimento e costura
- 6 Após a formação do gargalo, a lata está pronta para ser enchida. A lata é mantida firmemente contra o assento de uma máquina de enchimento e uma bebida é vertida. A tampa é adicionada. A flange superior formada quando a lata recebeu seu gargalo é então dobrada em torno da tampa e fechada com costura. Nesse momento, a lata está pronta para venda.
Subprodutos / resíduos
Algum alumínio se perde em vários pontos do processo de fabricação - quando os espaços em branco são cortados e as orelhas, aparadas - mas esse refugo pode ser reutilizado. Latas que foram usadas e descartadas pelos consumidores também podem ser reaproveitadas e, conforme mencionado acima, o material reciclado representa uma porcentagem significativa do alumínio usado nas latas de bebidas. A economia com a reciclagem é bastante significativa para a indústria. A maior despesa com a lata de bebida está na energia necessária para produzir o alumínio, mas a reciclagem pode economizar até 95% do custo de energia. Os produtores de latas também tentam controlar o desperdício desenvolvendo folhas de latas mais resistentes, de modo que menos alumínio entre em cada lata, e controlando cuidadosamente o processo de fabricação para reduzir a perda por meio do espigão. A tampa de uma lata típica tem diâmetro menor que as paredes para conservar a quantidade de alumínio que entra nela, e como a demanda mundial por latas de bebidas continua crescendo, a tendência é tornar a tampa ainda menor. Uma nova lata lançada em 1993 com uma tampa um quarto de polegada menor em diâmetro do que a maioria das latas pode economizar aos fabricantes US $ 3 por mil. Este número parece pequeno até ser multiplicado pelas centenas de milhões de latas produzidas a cada dia nos EUA. Torna-se claro que qualquer pequena economia em matéria-prima ou energia pode ser um passo importante na conservação de dinheiro e recursos.
O Futuro
A produção mundial de latas de alumínio para bebidas está aumentando continuamente, crescendo vários bilhões de latas por ano. Diante dessa demanda crescente, o futuro das latas de bebidas parece estar em designs que economizem dinheiro e materiais. A tendência para tampas menores já é aparente, assim como diâmetros de pescoço menores, mas outras mudanças podem não ser tão óbvias para o consumidor. Os fabricantes empregam técnicas diagnósticas rigorosas para estudar as chapas de latas, por exemplo, examinando a estrutura cristalina do metal com difração de raios X, na esperança de descobrir melhores formas de fundir os lingotes ou laminar as chapas. Mudanças na composição da liga de alumínio, ou na forma como a liga é resfriada após a fundição, ou na espessura com que a folha de lata é enrolada podem não resultar em latas que pareçam inovadoras para o consumidor. No entanto, são provavelmente os avanços nessas áreas que levarão a uma fabricação mais econômica no futuro.
Processo de manufatura