Botão
Antecedentes
Os primeiros botões datam dos tempos pré-históricos e, apesar de milênios de mudanças na moda e nas técnicas de fabricação, o botão perdurou como o fecho de tecido mais comum. Embora os botões tenham sido usados por milhares de anos, a casa de botão não foi inventada até o século XIII. Acredita-se que a casa de botão tenha sido trazida do Oriente Médio para a Europa por cavaleiros que retornavam das Cruzadas, e seu advento levou a um aumento no uso de botões. Os botões se tornaram um grampo da moda masculina na Renascença, quando as jaquetas costumavam apresentar fileiras de botões do queixo à cintura, as mangas eram bem abotoadas do cotovelo ao pulso e as calças também exibiam botões na cintura, joelho ou coxa. Guildas de fabricantes de botões existiam em Paris no século 13, onde os botões eram feitos de uma variedade de materiais, incluindo madeira, osso, latão, estanho, ouro e prata.
No século 18, a indústria de botões floresceu em toda a Europa e os artesãos desenvolveram muitas técnicas diferentes para fazê-los. A corte de Luís XIV da França deu início à moda de botões intrincados de metais preciosos e joias e botões de tecido bordado. Os fabricantes ingleses inventaram os botões de aço, e os botões de vidro ou vidro e metal eram populares na França. Muitos artistas famosos em outros ramos também emprestaram suas habilidades para a indústria de botões. O pintor francês Antoine Watteau fez botões, e alguns dos principais nomes da porcelana fina como Wedgwood, Limoges e Staffordshire também estão associados a botões finos.
No final do século 18, os botões começaram a ser feitos nas fábricas. Botões de metal foram perfurados por matrizes e os fabricantes de matrizes foram proibidos de emigrar da Inglaterra, para que não levassem seus segredos comerciais para o exterior. Mesmo assim, a tecnologia se espalhou e os botões começaram a ser produzidos em massa em metal, vidro e outros materiais. Botões extravagantes ainda eram elementos populares da moda do século XIX. Diemakers produziu projetos complexos usando cenas de peças, romances e canções de ninar, e óperas de Wagner e as operetas de Gilbert e Sullivan eram rotineiramente comemoradas com botões representando cenas e personagens.
No início do século 20, o estilo predominante era muito mais simples, refletindo a aparência mais serena da crescente classe de colarinho branco. Botões de camisa baratos combinados para homens e mulheres estavam disponíveis em lojas de cinco e dez centavos por volta de 1910. Os botões de plástico tornaram-se amplamente disponíveis na década de 1930, embora a maioria dos botões de camisa típicos ainda fossem feitos de conchas do mar ou outros materiais naturais. A Segunda Guerra Mundial trouxe muitos avanços na tecnologia do plástico. Os botões de acrílico eram, na verdade, feitos de material que sobrou da fabricação de torres de bombardeiros. A indústria de botões se converteu quase inteiramente em plástico após a guerra. Os botões de plástico podem ser feitos por uma variedade de métodos. Eles podem ser fundidos em molde, onde pedaços de plástico cortados de uma longa haste são colocados em um molde de duas partes. O molde é fechado e calor e pressão são aplicados para finalizar o botão. Outro processo é a moldagem por injeção. Neste método, o plástico derretido é forçado a entrar em um molde com uma cavidade em forma de botão. Descrito abaixo é o processo mais comum para fazer
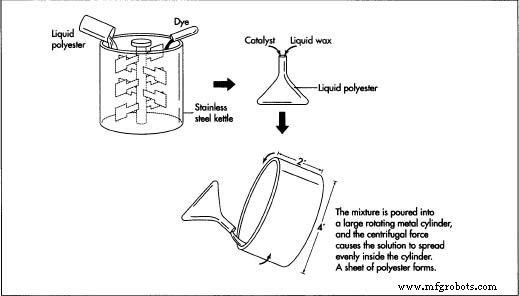
Matérias-primas
Os botões ainda são feitos de produtos naturais, mas exigem mais trabalho manual do que os botões de plástico, e alguns materiais de botões antes comuns não estão mais disponíveis. Por exemplo, botões de marfim de baleia, marfim de elefante ou casco de tartaruga não podem ser feitos nos EUA por causa das leis promulgadas para proteger animais em extinção. Os botões de chifre são feitos de cascos e chifres de vacas e búfalos, mas os aficionados por botões afirmam que os chifres modernos são de baixa qualidade e cor porque os animais pastam em grama de baixa qualidade. Os botões de buzina antigos costumam ser listrados e vêm em uma variedade de cores, enquanto os botões de buzina modernos são de um marrom claro ou escuro mais opaco. Os botões de chifre ainda são um elemento da moda masculina da melhor qualidade, mas custam até um dólar a peça, em comparação com o preço de meio centavo de um botão padrão. Os botões de madrepérola, derivados de conchas do mar, ainda são apreciados por seu brilho. Mas depois da Segunda Guerra Mundial, os mergulhadores nas ilhas do Pacífico Sul que forneciam a maior parte das madrepérolas começaram a cobrar muito mais por seu trabalho perigoso, e o preço do material subiu drasticamente. Botões de vidro, amplamente importados da Alemanha em meados deste século, agora também são muito menos comuns. Os botões de vidro eram feitos de fábrica, mas exigiam muito trabalho manual sob condições de calor desagradável, e essa indústria também diminuiu após a Segunda Guerra Mundial.
O material comum para botões é o poliéster, um tipo especial de plástico com propriedades que o tornam adequado para botões. Uma variedade de corantes químicos são adicionados ao poliéster para fazer cores diferentes. Para fazer botões com o brilho perolado dos botões de concha, carbonato vermelho é adicionado ao poliéster. Os botões pretos são feitos com a adição de negro de fumo e os botões brancos são feitos de titânio. O processo de fabricação do botão também requer um catalisador químico que endurece o poliéster e a cera.
O processo de fabricação
Mistura de poliéster
- 1 O poliéster chega à fábrica de botões na forma líquida. No início do processo de fabricação, o poliéster é drenado de seu
tanque de armazenamento e medido em uma chaleira de aço inoxidável. Em seguida, é adicionado corante, se os botões tiverem de ser de qualquer cor diferente da translucidez natural do poliéster. Depois que o corante é misturado, o poliéster líquido é despejado em um copo de metal de 3 galões (11 litros). O catalisador e a cera líquida são adicionados.
Derramando no cilindro
- 2 A mistura de poliéster, catalisador e cera é então despejada em um grande cilindro giratório de metal. Os cilindros são feitos de aço e revestidos de cromo e têm normalmente 61 cm de comprimento e 122 cm de diâmetro. Os cilindros ficam de lado em rolos que giram os tambores a 250 rpm. A solução de poliéster é lentamente derramada no interior rotativo do cilindro, e a força centrífuga da rotação faz com que a solução se espalhe, revestindo o cilindro com uma folha uniforme. Uma quantidade maior de poliéster é usada para botões mais grossos e menos para os mais finos. Uma borda de 5 cm ao redor das extremidades do cilindro evita que o poliéster vaze.
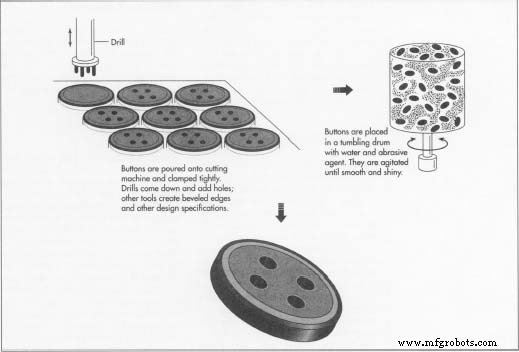
Endurecimento da folha
- 3 Conforme o poliéster gira no cilindro, ele começa a interagir com o catalisador químico e endurece. A cera sobe para o topo da folha e também afunda para o fundo, de modo que o poliéster endurecido é eventualmente mantido entre duas camadas de cera. Este processo é concluído após 20 minutos de rotação. A folha de poliéster resultante mudou de seu estado líquido para um sólido quebradiço semelhante à consistência de queijo velho.
Cortando a folha
- 4 Quando a folha atinge a dureza adequada, o tambor para e a folha é cortada. Em seguida, ele é enrolado para fora do cilindro em um tubo de madeira. A cera facilita a remoção do tambor, mas o material ainda é muito delicado. A camada superior de cera é então removida e a folha é transferida para uma máquina de estampagem.
Cortando os espaços em branco
- 5 A máquina de moldagem move a folha de poliéster ao longo de uma correia transportadora. Conforme a folha passa ao longo da correia, matrizes circulares de corte de aço descem e perfuram círculos do tamanho de botões, chamados de espaços em branco. Os botões vêm em tamanhos padrão e matrizes de diâmetros diferentes podem ser carregadas na máquina de estampagem, dependendo do tamanho necessário. Depois que os espaços em branco são cortados, eles caem em uma rampa, e a folha de poliéster perfurada rola sob a rampa. O corte dos espaços em branco da folha leva de dois a quatro minutos, dependendo do tamanho dos botões que estão sendo feitos.
Resfriando os espaços vazios
- 6 Os blanks neste estágio estão quentes, porque o poliéster ainda está reagindo com o catalisador, liberando calor. Então, neste ponto, os espaços em branco são removidos da rampa e colocados em um saco de náilon. A bolsa é então baixada para um tanque de água salgada, que é aquecida a 230 ° F (110 ° C). Os espaços em branco flutuam na água salgada por 15 minutos. A água esfria lentamente e as placas de poliéster endurecem. Em seguida, a bolsa de náilon é transferida para um tanque de água fria, e os blanks atingem seu estado final de dureza. Após os banhos quentes e frios, os blanks são secos em uma máquina de secagem centrífuga, que os gira em uma cesta de tela de arame.
Estilo dos espaços em branco
- 7 Os espaços em branco agora estão prontos para serem cortados em sua forma de botão acabada. O desenho exato do botão pode ser especificado por um fabricante de roupas, e o fabricante do botão deve fazer uma ferramenta de corte de aço de acordo com o desenho que lhe foi dado. Uma ferramenta de corte diferente é necessária, por exemplo, para fazer uma borda chanfrada ou plana, ou para fazer um botão ligeiramente côncavo. Quando a ferramenta de corte apropriada está no lugar, os botões são colocados em uma tremonha na parte superior da máquina de corte. Os espaços em branco caem em um suporte onde são presos com firmeza e movidos em direção à ferramenta de corte. A lâmina giratória avança e corta o botão, depois se retrai. Em seguida, o botão se move para baixo de um conjunto de brocas, que criam os orifícios. Como a ferramenta de corte, as brocas devem ser projetadas de acordo com as especificações do fabricante de roupas. O projeto especifica não apenas dois ou quatro furos, mas também o diâmetro dos furos e a distância entre eles. Depois que os botões passam por baixo da furadeira, eles são sugados por vácuo para fora do suporte e para uma caixa embaixo da máquina. Centenas de botões por minuto podem ser feitos dessa forma, embora o número varie de acordo com o tamanho do botão e a complexidade do design.
Finalizando os botões
- 8 Depois que os botões são cortados e perfurados, eles apresentam bordas ásperas ou afiadas, arranhões e marcas de ferramenta. Eles são colocados em tambores giratórios hexagonais, que contêm água, um material abrasivo e um agente espumante. A bateria gira por até 24 horas. Os botões saltam no tambor até ficarem lisos e brilhantes. Depois de revolvidos, os botões são lavados e secos.
Controle de qualidade
Depois que os botões estão totalmente acabados, eles são colocados em uma esteira transportadora e inspecionados visualmente quanto a defeitos. O inspetor deve verificar cada botão em busca de falhas e remover quaisquer rachaduras ou cortes incorretos. Os botões agora estão prontos para embalagem e venda.
O Futuro
O século 20 viu fechos de roupa inteiramente novos, como zíper e velcro, e agora podemos fabricar tecidos elásticos que não requerem nenhum tipo de fecho. No entanto, o botão não parece correr o risco de desaparecer. É utilitarista e está na moda e provavelmente estará por muito tempo conosco. No entanto, a tecnologia de botão não é totalmente séria. Um desenvolvimento recente é um botão de resistência superior, um botão de cerâmica feito de óxido de zircônio. O magnata da cerveja Joseph Coors Jr. decidiu em 1989 que havia a necessidade de um botão indestrutível e ele usou uma unidade de pesquisa de cerâmica na Adolph Coors Company para desenvolver este novo produto. O botão Diamond Z resultante foi lançado em 1993. Diz-se que é mais duro que o aço, com 2,5 vezes a resistência à flexão do aço. Os botões dessas camisas masculinas são disparados a 3200 ° F (1760 ° C), depois polidos e revestidos com um acabamento semelhante ao marfim. A prova da indestrutibilidade do Diamond Z é um "teste de queda" onde uma pesada haste pontiaguda cai por um longo tubo no botão. O botão pode resistir a essa provação rigorosa, bem como ao desgaste diário de lavagens e passadas repetidas. O botão Diamond Z é, no entanto, bastante caro para fazer em comparação com o botão de poliéster comum e, por esse motivo, não é provável que substitua a tecnologia existente.
Processo de manufatura