Cortador de grama
Antecedentes
O cortador de grama é um dispositivo mecânico que literalmente raspa a superfície da grama usando uma lâmina ou lâminas de rotação rápida.
Durante séculos, a grama foi cortada por trabalhadores que caminhavam por pastagens ou campos empunhando foices pequenas e afiadas. Além de ser cansativo e lento, o corte manual era ineficaz - as foices funcionavam bem apenas quando a grama estava molhada. O primeiro dispositivo mecânico de corte de grama apareceu em 1830, quando um trabalhador têxtil inglês chamado Edwin Budding desenvolveu um cortador de grama supostamente baseado em uma máquina têxtil usada para cortar o tecido do tecido. O cortador cilíndrico de Budding era preso a um rolo traseiro que o impulsionava com uma transmissão por corrente e raspava a grama com uma lâmina cortante curva presa ao cilindro. Ele criou dois tamanhos, grandes e pequenos. O grande cortador teve de ser puxado por cavalos, cujos cascos foram temporariamente calçados com botas de borracha para evitar que danificassem a grama; o jardineiro-chefe do zoológico de Londres foi um dos primeiros a adquirir este modelo. Budding vendia o cortador de grama menor para cavalheiros do campo, que iriam, afirmou ele, "encontrar em [sua] máquina um exercício divertido, útil e saudável".
O corte mecanizado da grama evidentemente demorou a pegar, talvez porque o cortador de grama de Budding fosse muito pesado, além de ser engrenado de maneira ineficiente. Apenas dois fabricantes de cortadores de grama exibiram suas máquinas na Grande Exposição da Inglaterra em 1851. No entanto, várias décadas depois, as novas máquinas ganharam popularidade devido ao interesse pelo tênis de grama que surgiu na Inglaterra durante o final do período vitoriano. Antes da virada do século, os projetos iniciais de Budding foram aprimorados. Pesando consideravelmente menos do que seus antecessores e com base no design da roda lateral ainda usado nos cortadores de grama mais populares de hoje, essas máquinas refinadas logo se tornaram visíveis em estaleiros por toda a Inglaterra.
Os primeiros cortadores de grama movidos a gás foram projetados em 1897 pela Benz Company da Alemanha e pela Coldwell Lawn Mower Company de Nova York. Dois anos depois, uma empresa inglesa desenvolveu seu próprio modelo; no entanto, nenhuma dessas empresas produziu em massa seus projetos. Em 1902, o primeiro cortador de grama produzido comercialmente, projetado por James Edward Ransome, foi fabricado e vendido. Embora o cortador de grama de Ransome apresentasse um assento de passageiro, a maioria dos primeiros cortadores não tinha, e ainda hoje os modelos mais populares são empurrados por trás.
Atualmente, os cortadores de grama estão disponíveis em quatro designs básicos:o cortador de grama rotativo, o cortador de grama hidráulica, o cortador de grama e o trator. Como o cortador de grama rotativo é de longe o mais comum, ele é o foco desta entrada. Empurrados por trás, os cortadores de grama rotativos apresentam uma única lâmina giratória encerrada em uma caixa e apoiada por rodas. Conforme o motor gira, ele gira a lâmina. A lâmina gira a 3.000 rotações por minuto, virtualmente 19.000 pés (5.800 metros) por minuto na ponta da lâmina onde o corte realmente ocorre. Os melhores rotativos apresentam um chifre da abundância (cornucópia) ou forma de túnel de vento curvando-se ao redor da parte frontal da caixa e terminando na calha de descarga através da qual a grama cortada voa. Os modelos automotores são acionados por uma corrente ou correia conectada ao eixo de transmissão do motor. Uma caixa de câmbio geralmente gira um eixo horizontal que por sua vez gira as rodas. Alguns modelos têm uma grande unidade móvel acionada por corrente ou correia que se levanta e se acomoda nas rodas.
O cortador de grama elétrico apresenta várias lâminas presas em ambas as extremidades a tambores presos às rodas. O eixo de transmissão do motor acoplado que gira o carretel também pode ser equipado para impulsionar o cortador, se desejado. Sobrepondo a grama, as cinco a sete lâminas desta máquina a puxam contra uma barra de corte na parte inferior do cortador. Em seguida, um ou mais rolos alisam e compactam os recortes à medida que o cortador passa por cima deles. Os cortadores de grama são mais eficientes do que os cortadores de grama porque estes usam apenas a extremidade da lâmina para fazer a maior parte do corte, enquanto as lâminas fixas em um cortador de rolos cortam com todo o comprimento de ambas as bordas. No entanto, os cortadores rotativos são mais fáceis de fabricar porque o design básico é mais simples e eles também são preferidos aos cortadores de carretel na maioria dos tipos de grama. Pelas estimativas da indústria, a maioria dos 40 milhões de cortadores em uso em qualquer sábado de verão são cortadores rotativos.
Matérias-primas
O cortador a gás típico pode ter até 270 peças individuais, incluindo um motor tecnologicamente avançado de dois ou quatro tempos, uma variedade de peças usinadas e moldadas, vários subconjuntos adquiridos de empreiteiros externos e muitas peças padrão hardware. A maioria dessas peças é de metal, incluindo os componentes principais:bandeja do cortador, guidão, motor e lâminas. Alguns, no entanto, são feitos de plástico, como calhas de descarga laterais, tampas e plugues.
O processo de fabricação
A fabricação do cortador de grama rotativo convencional requer controle de estoque de precisão, posicionamento estratégico de peças e pessoal e sincronização de pessoas e tarefas. Em alguns casos, as células robóticas são usadas em conjunto com uma força de trabalho treinada.
Descarregando e distribuindo os componentes
- 1 Transportados de caminhão para a doca de carregamento da fábrica, os componentes são movidos por empilhadeiras ou carrinhos suspensos para outros centros para conformação, usinagem, pintura ou, se não exigirem trabalho adicional na chegada, montagem.
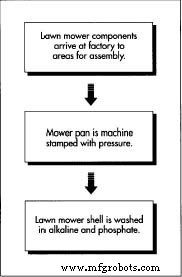
A bandeja do cortador
- 2 O prato cortador de aço, a maior peça única e usado em vários modelos, é primeiro estampado à máquina sob grande calor e pressão. A bandeja é então transportada para uma célula robótica, onde um cortador de plasma cria aberturas. O termo plasma refere-se a qualquer um de uma série de gases (argônio é comumente usado) que podem ser elevados a alta temperatura e altamente ionizados ao serem passados por um arco elétrico restrito. Quando direcionado através da abertura estreita de uma tocha, este gás quente ionizado pode ser usado tanto para corte quanto para soldagem.
- 3 Depois que outros elementos, como defletores (placas defletoras) são soldados, a panela acabada e várias outras partes expostas são pintadas com pó em uma sala selada. A pintura a pó envolve a lavagem cuidadosa das peças em soluções alcalinas e de fosfato e o enxágue para selar as superfícies. As peças são então fixadas em transportadores aéreos e passam por uma pintura cabine. Partículas finas de tinta são pulverizadas de uma arma que as imbui com uma carga eletrostática - oposta à carga dada à peça que está sendo pintada - que faz com que a tinta adira à superfície das peças por igual. Em seguida, as peças são cozidas em fornos para produzir um revestimento semelhante a esmalte permanentemente fixo. A panela
A casca é pintada eletrostaticamente e então cozida para selar a tinta. Enquanto isso, o guiador é dobrado e perfurado por robôs e, em seguida, os componentes restantes são montados. e outras peças agora estão prontas para resistir a anos de exposição a fluidos corrosivos de grama e ao constante salpicar de sujeira e detritos levantados no processo de corte.
Moldar o guiador
- 4 O guiador é criado em uma célula robótica cujos braços mecânicos realizam três operações. Em um dobrador, o tubo é primeiro dobrado em pelo menos quatro lugares. Uma segunda operação de prensagem achata as extremidades e uma terceira perfura cerca de catorze orifícios redondos e quadrados no tubo. Esses orifícios acomodam o mecanismo de partida, o controle da tração da lâmina e da roda e o acessório do prato. O guidão acabado é então transportado para uma estação de submontagem, onde muitos dos controles são adicionados.
Outras submontagens
- 5 Os outros subconjuntos principais também são criados em vários centros de fábrica usando materiais formados, usinados ou adquiridos e hardware padrão. As peças adquiridas de fornecedores externos incluem motores construídos de acordo com as especificações físicas e de desempenho do fabricante, pneus, mecanismos de mudança, chicotes elétricos e rolamentos. As peças de plástico moldadas por injeção são adquiridas para uso em chutes de descarga laterais, tampas e plugues. A moldagem por injeção se refere a um processo no qual o plástico derretido é esguichado em um molde e, em seguida, deixado esfriar. À medida que esfria, o plástico assume a forma do molde.
- 6 As equipes de montagem colocam os seis ou mais subconjuntos principais juntos em uma linha de rolamento em um ritmo determinado pela tarefa e habilidades necessárias. O motor é primeiro colocado de cabeça para baixo em uma estrutura e a bandeja do cortador de grama é aparafusada junto com o mecanismo de acionamento. Em seguida, vêm o eixo traseiro, suportes e hastes para proteger os controles de mudança. A lâmina e as rodas e peças da embreagem que a acompanham são presas ao motor através da abertura da bandeja com chaves de torque acionadas a ar predefinidas. Depois que outro membro da equipe adiciona hardware e rodas, a unidade é virada sobre suas rodas. O guidão está conectado e os cabos de controle são fixados e ajustados. Finalmente, o cortador - cada cortador - tem seu desempenho testado antes do envio aos revendedores, onde alguns ajustes finais de configuração são feitos.
Controle de qualidade
Os inspetores monitoram o processo de fabricação em toda a execução, verificando ajustes, costuras, tolerâncias e acabamentos. Em particular, a operação de pintura é examinada. Amostras de cada peça pintada são regularmente retiradas da linha para testes ultrassônicos, um processo que utiliza a atividade de corrosão criada em um banho de sal para simular 450 horas de exposição contínua ao ambiente natural. As partes pintadas também são marcadas e a deterioração da superfície exposta é observada em busca de sinais indicadores de ferrugem. Se necessário, os ciclos de pintura ou limpeza são ajustados para garantir acabamentos de alta qualidade e durabilidade.
O teste de desempenho final - a última etapa na sequência de montagem - garante confiabilidade e segurança para os usuários. Uma pequena quantidade de uma mistura de gás / óleo é adicionada a cada motor. Um técnico dá partida no motor e verifica sua rotação com um medidor; os elementos de acionamento e as chaves de segurança também são verificados. Conforme exigido pelos regulamentos atuais da Comissão de Segurança de Produtos do Consumidor, a lâmina do cortador, quando funcionando, deve parar dentro de três segundos após a alavanca de controle ser liberada.
O Futuro
Como muitas outras máquinas, o cortador de grama se beneficiará do desenvolvimento de fontes de energia novas e mais eficientes. Uma invenção recente é o cortador de grama movido a energia solar, que usa a energia do sol em vez da gasolina como combustível. Não precisa de ajustes ou trocas de óleo e funciona muito silenciosamente. Talvez sua maior desvantagem seja a quantidade de energia de sua bateria pode armazenar:apenas o suficiente para duas horas de corte, que devem ser seguidas por três dias de carregamento. No entanto, à medida que as baterias com mais recursos de armazenamento forem desenvolvidas, essa desvantagem desaparecerá.
Processo de manufatura
- O que é VMC Machining?
- Guia para marcação a laser em alumínio
- Soldagem MIG vs. Soldagem TIG
- Guia para marcação a laser
- Considerações para usinagem suíça de alta produção
- Guia de Prototipagem CNC
- Compreendendo o Processo de Fabricação do Eixo
- O que é marcação a laser a fibra?
- Eletropolimento vs. Passivação
- O que é passivação de aço inoxidável?