Fazendo ondas com automação de torno
Como orgulho do estado Badger, a Mercury Marine é conhecida localmente simplesmente como “Merc”. As raízes de 81 anos deste ícone americano lhe conferem uma rica história, tornando-o o orgulho da comunidade e o favorito do público náutico. Enquanto isso, seu sucesso faz da Merc a inveja de seus concorrentes. A Mercury Marine é uma fabricante líder mundial de todos os tipos de sistemas de propulsão marítima — uma divisão de US$ 2,6 bilhões da Brunswick Corp. que emprega mais de 5.200 pessoas em vários locais ao redor do mundo.
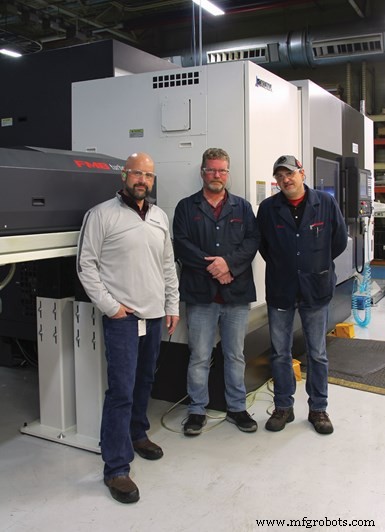
Jason Noworatzky, Bill Cusick e Chris Erke ( L-R) fazem parte da equipe que produz todas as engrenagens e eixos para acionamentos internos e externos da Mercury Marine usados em todo o mundo.
Mais de 80 anos de desenvolvimento inovador de motores de barcos tornaram o local de Fond du Lac, Wisconsin, um repositório extremamente conhecido de proezas de engenharia e excelência de produção. O amplo campus de hoje ao lado da Interestadual 41 possui mais de 2,5 milhões de pés quadrados de espaço que contém todos os tipos de disciplinas de engenharia e fabricação, juntamente com os aproximadamente 3.300 indivíduos que fazem tudo acontecer.
Na Fábrica 4, todas as engrenagens e eixos são produzidos para todos os acionamentos internos e externos da Mercury Marine fabricados em suas fábricas ao redor do mundo. Este empreendimento maciço inclui eixos de hélice, eixos de transmissão, eixos de direção, marchas à frente, marchas à ré e pinhões para todos os motores de centro e tração de popa MerCruiser, rabetas MerCruser Alpha e Bravo, motores diesel Mercury e rabetas diesel, o Mercury SportJet e todos os motores externos. O homem responsável pela equipe de engenheiros de manufatura, engenheiros industriais e programadores necessários para esta tarefa pesada é Jason Noworatzky, gerente de engenharia da Planta 4. Para tudo o que tem a ver com o processo de fabricação de eixos e engrenagens, o Sr. Noworatzky e sua equipe criam e estabelecem os procedimentos de fabricação e qualidade juntamente com os gastos de capital necessários para produzir as peças com eficiência e, mais importante, para atender às especificações rigorosas da Mercury . Em seguida, eles selecionam as melhores máquinas e automação com base na velocidade, custo de mão de obra e perfeição das peças. “Qualidade – construímos o processo em torno disso”, diz Noworatzky.
Esta seção do eixo de direção para motores de popa da empresa foi originalmente produzido em uma célula de cinco máquinas com dois operadores, mas agora é manuseado por um torno de duas torres e dois fusos que é combinado com um alimentador de barras e um descarregador.
Um componente que era particularmente trabalhoso é uma seção oca de eixos de direção que são usados em motores de popa Mercury Marine. O processo anterior era uma célula multi-máquina. Iniciando o processo foi um torno de eixo único com uma única torre e um cabeçote móvel com um alimentador de barras. Em seguida, seria transportado para outra máquina para uma operação de furadeira. Em seguida, as peças foram movidas para outra máquina para uma operação de retificação sem centro e, em seguida, transportadas para uma operação final de fresagem. Este método de produção de peças foi empregado por décadas. “Estou aqui há 25 anos e sempre foi assim”, diz Bill Cusick, engenheiro de fabricação. Esse processo de célula multimáquina anterior usava dois operadores.
Eventualmente, tornou-se evidente que as máquinas nessas células precisariam ser substituídas. Procurando uma solução moderna, o Sr. Cusick investigou máquinas novas e modernas. “A tecnologia finalmente alcançou, então agora podemos empregar todos os processos em uma máquina”, observa Cusick. “Não precisávamos mais executá-los nas velhas fresadoras.”
Chris Erke, programador sênior, avalia a questão da qualidade. “É difícil manter a verdadeira posição e o desvio de uma máquina para outra, em vez de fazer tudo em uma máquina onde você pode controlá-la.”
Um bom equilíbrio
“Grande parte dessa mudança para nós foi de qualidade”, diz Cusick. “Isso significa feito em uma máquina.” A equipe teve que fazer um bom equilíbrio entre a capacidade e as capacidades da máquina, o número de máquinas e os requisitos de produção projetados. Depois de criar uma espécie de placar, uma solução venceu. O Sr. Cusick foi ao revendedor local de máquinas-ferramenta da empresa, Morris Midwest, e iniciou um diálogo sobre a substituição das antigas células de cinco máquinas. “Criamos uma SOW (Statement of Work) que explicava que queríamos um torno que completasse nosso processo de usinagem”, diz Cusick. “Tínhamos uma boa ideia sobre o que pensávamos que isso implicaria para obter o tempo de ciclo necessário ao adicionar as operações adicionais.”
Cusick e Erke disseram a Morris Midwest que acreditavam que um torno com duas torres e dois fusos, combinado com um alimentador de barras e um descarregador, funcionaria. “Com as novas tecnologias, não achamos que seria um problema produzi-lo, então ele entra em uma extremidade e sai pronto”, observa Erke. “Nós sabíamos como fazer isso completo, mas Morris Midwest selecionou a máquina adequada, fez toda a engenharia e lidou com todos os escoamentos.”
A Ascensão de Frankenlathe
Em 2017, a primeira nova célula de combinação de alimentador/torno/descarregador de barras foi entregue na Fábrica 4. Devido ao seu tamanho e capacidades, o novo Okuma LT3000 EX foi carinhosamente apelidado de “Frankenlathe”. Logo depois, uma segunda célula (uma duplicata exata do número um) foi posicionada ao lado da primeira e foi rapidamente chamada de “Noiva de Frankenlathe” pelo pessoal da loja.
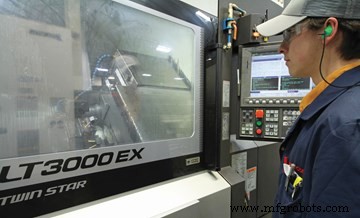
Três tornos Okuma LT3000 EX, com alimentadores de barras e descarregadores, foram adicionados para lidar com a produção dos eixos.
Os “Frankenlathes” são ambos ladeados pelo maquinário da Edge Technologies que torna o processo uma verdadeira vantagem tecnológica única. A automação empregada nesta configuração atual era a peça que faltava para produzir a peça “one-and-done” com a qualidade exigida. O Okuma LT3000 EX é um torno do tipo arquitetura aberta, um centro de torneamento de eixo duplo altamente flexível na classe de mandril de 8 polegadas. Esta máquina multifuncional horizontal de eixo duplo integra as funções de torno e fresadora/furadeira em todas as torres.
As duas primeiras células foram equipadas com alimentadores de barra FMB Turbo 5-65. Estas são unidades estilo magazine que alimentam barras de até 12 pés e apresentam canais cheios de óleo que criam um efeito de rolamento hidrodinâmico em torno das barras giratórias para um funcionamento suave. A capacidade de armazenamento da revista é de 11 polegadas nas unidades padrão. Com o comprimento da peça e o tempo de ciclo para esta seção de eixo, o Okuma pode processar um pouco de metros lineares de tubos durante um turno, então a Edge Technologies adicionou o Edge BarLift, um sistema de carregamento de carregador estendido que apresenta 28 polegadas adicionais de estoque para por mais tempo sem que o operador precise carregar manualmente o alimentador.
O FMB Turbo 5-65 12 pés Os alimentadores de barras estilo magazine apresentam canais cheios de óleo que criam um efeito hidrodinâmico em torno das barras giratórias para um funcionamento suave.
“Podemos ter tido um ou dois tornos com um descarregador no passado, mas este é de longe o maior passo no produto mais convencional que fizemos (um descarregador)”, diz Noworatzky. “Não podemos deixar cair esta parte porque danificaria as splines. A peça concluída tem requisitos de acabamento de superfície.”
As células um e dois foram instaladas em 2017 e foram equipadas com unidades FleXsys LE (Load/Extract) da Edge Technologies para o processo de descarregamento de peças. Esta unidade foi projetada para automação em peças maiores—especificamente trabalhos de eixo longo. Ele é projetado para alimentar e retrair barras cortadas no comprimento da peça – tão grande quanto 2,5 polegadas de diâmetro e 37 polegadas de comprimento – para produção com tornos CNC de eixo único. O tubo de 12 pés é alimentado no eixo principal do Okuma com o FMB Turbo 5-65.
O sistema de carregamento de carregador estendido Edge BarLift apresenta um 28 polegadas adicionais de estoque para uma operação mais longa sem intervenção do operador.
Frankenlathe 3:A ascensão da automação
A terceira célula chegou no final de 2019 com o novo Rebel 80 Servo Unloader, o mais recentemente desenvolvido sistema de remoção automática de peças da Edge Technologies para extração de peças em uma faixa de diâmetro de 8 a 80 mm. Esta é uma unidade mais versátil do que a versão anterior que está sendo executada nas células um e dois. As unidades mais antigas não tinham um sistema de controle que se comunicasse com o torno como os alimentadores de barras FMB. Foi necessária uma programação adicional do FleXsys LE. Embora as unidades funcionassem bem depois de ajustadas, a Mercury Marine pediu à Edge Technologies que fornecesse uma configuração atualizada do descarregador que corrigiria essa falha. O desenvolvimento do Rebel 80 Servo Unloader foi a resposta. A Edge estava trabalhando no novo descarregador e tornou o problema de comunicação uma prioridade principal para a instalação da Mercury. Agora, na terceira célula, o Okuma LT3000 EX, o alimentador de barras FMB e o descarregador Edge se comunicam e funcionam como uma máquina com otimização do tipo Indústria 4.0.
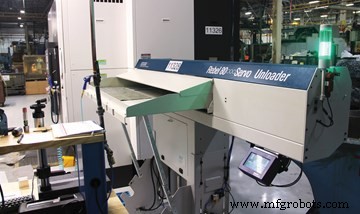
Enquanto os dois primeiros tornos foram equipados com FleXsysLE Descarregadores, projetados para automação em peças maiores, o terceiro Okuma conta com o Descarregador Rebel 80 Servo Unloader, que é projetado para extrair peças de 8 a 80 mm de diâmetro e possui recursos de comunicação otimizados com o alimentador de barras e a máquina-ferramenta.
O Servo Unloader Rebel 80 apresenta várias maneiras de remover peças com vários métodos de fixação do extrator na peça para puxá-la do subspindle. Esses dispositivos são conhecidos como efetores finais. Os mecanismos efetores de extremidade disponíveis incluem pinças de barra para garras OD, garras de expansão ID, garras OD de três pontos, dedos de alimentação, garras angulares, eletroímãs para materiais ferromagnéticos e soluções especiais de engenharia para estoque perfilado e de formato ímpar.
Para proteger os acabamentos das peças, no caso das estrias no eixo de direção, a bandeja em V de extração coloca suavemente os eixos na superfície do carregador, que é revestida com um material não metálico. A mesa de inclinação é ajustável, permitindo que o descarregador “descarregue facilmente” peças de grande diâmetro.
O Descarregador Rebel 80 Servo possui uma pista de deslocamento axial que permite que a unidade deslize facilmente para fora do torno para trocas do revestimento do fuso e acesso de manutenção à parte traseira do torno. Ele vem equipado com um pingente de controle remoto e um controle de conversação que apresenta uma tela sensível ao toque e programação orientada por menus. O controle também armazena programas de peças ilimitados.
A terceira célula também se beneficiou de um avanço na tecnologia de alimentação de barras. O FMB Turbo 5-65 veio equipado como modelo A, apresentando o novo sistema de canal guia de ajuste automático. Os canais de guia de poliuretano se ajustam automaticamente ao diâmetro adequado, permitindo que um canal de guia execute diâmetros de barra de 5 mm a 65 mm. Esse recurso dá à Mercury Marine a capacidade de mudar rapidamente para diferentes diâmetros de eixo sem alterações no conjunto de canais de guia. Este design ajuda em configurações rápidas para produção just-in-time.
Juntamente com o aumento da qualidade das peças, essas células oferecem a vantagem de reduzir os custos de mão de obra e oferecer um melhor aproveitamento do espaço. Idealmente, o Sr. Noworatzky teria uma lousa em branco para reconfigurar sua área de produção como desejar. Ele explica que as duas coisas que impulsionam sua equipe são combinar as operações e tentar compartilhar o trabalho.
No futuro, Noworatzky acredita que adicionar automação, como os alimentadores e descarregadores de barras que foram empregados com esses tornos, será a norma. “Não prevejo nenhuma célula nova chegando aqui a partir de agora que não tenha algum tipo de automação. Seja um robô FANUC, um sistema de pórtico, um alimentador de barras ou descarregadores.” Ele prevê que será algo para minimizar a quantidade de trabalho necessária para fazer um trabalho. “A mão de obra é um prêmio”, conclui Noworatzky.
Devido ao maior conhecimento técnico necessário para operar células como essas, a Mercury Marine oferece aulas aos funcionários para aprimorar suas habilidades. “Isso exige que você tenha um nível mais alto de operador”, diz Noworatzky. Para conseguir isso, a Mercury envia seus operadores para uma faculdade comunitária local onde eles se matriculam em cursos de usinagem de nível 1 e nível 2. Uma vez concluído, eles podem testar para receber a certificação NIMS.
Mercúrio Marinho | Mercurymarine. com
Tecnologias de ponta | 314-692-8388 | edgetechnologies.com
Sobre o autor
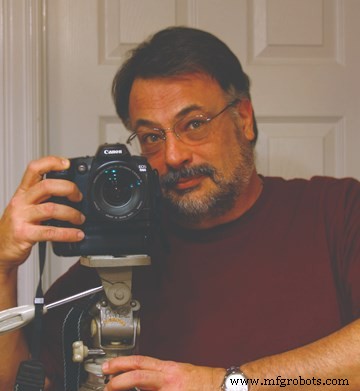
Kevin Shults
Kevin Shults é um profissional de publicidade e design. Ele tem 24 anos de experiência na indústria de máquinas-ferramenta, os últimos 20 dos quais atuou como diretor de marketing de um OEM na indústria de usinagem de precisão. Entre em contato com o Sr. Shults em [email protected].
Equipamento industrial
- Ganhando dinheiro com o roteador CNC
- Evolução da automação de testes com inteligência artificial
- Automação de negócios com plataformas de baixo código
- Impulsionando a experiência do cliente com automação inteligente
- Torno padrão com controles de tela sensível ao toque
- Torno com CNC
- Torno CNC com sistema de guia linear hidrostático
- Torno de ferramenta de grupo com base de polímero--SNK
- Controle de recursos de torno inclinado com gráficos de verificação
- Torno capaz de operação manual com assistência CNC