Ferramentas personalizadas, suporte de trabalho ajudam a moldar os rotores
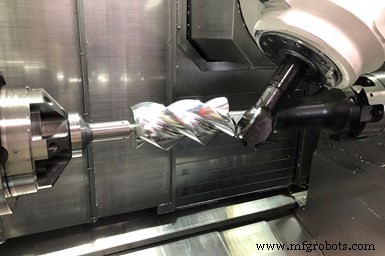
Desenvolvendo um processo de usinagem mais preciso para acasalamento rotores helicoidais, os modelos de supercharger deste Whipple Supercharger podem forçar de forma mais eficiente o ar em um motor para maiores ganhos de potência. Ferramentas personalizadas de fixação e forma permitem que a empresa fresar com precisão rotores de superalimentadores em uma configuração em seu torno-fresador de eixo B.
Fundada pelo ex-chefe da equipe de corrida e proprietário do carro Art Whipple em 1987, a Fresno's Whipple Superchargers fabrica compressores de parafuso duplo para pilotos automotivos e marítimos e outros que buscam melhorar o desempenho de seus motores. Esses tipos de “adicionadores de potência” (turbocompressores e óxido nitroso são outros) introduzem ar adicional em um motor além do que o motor pode puxar sozinho. Mais ar significa que mais combustível pode ser adicionado, aumentando essencialmente o deslocamento de um motor, bem como sua potência.
A chave aqui é a malha precisa e sem contato de dois rotores helicoidais dentro da carcaça do superalimentador. Com o design Whipple, o rotor macho tem três lóbulos helicoidais e a fêmea tem quatro, explica o Supercharger Designer Garrett Bright. Estes giram em sentido contrário entre si e extremamente próximos. À medida que os lóbulos de cada um passam pelas portas de entrada de ar, o ar fica preso entre os rotores e a carcaça. A rotação do rotor reduz progressivamente o espaço que o ar ocupa, comprimindo-o. A compressão continua até que o espaço do lóbulo interno fique exposto a uma porta de saída, através da qual o ar é descarregado acima da pressão atmosférica no coletor de admissão que fica no topo do motor.
A eficiência do superalimentador depende da eficácia da vedação entre os rotores de acoplamento e a carcaça. Anteriormente, a Whipple usava apenas rotores fabricados e fornecidos por uma empresa externa. Ele ainda usa os rotores fornecidos para alguns de seus modelos de superalimentadores. No entanto, a empresa começou a projetar e usinar seus próprios rotores internamente, e o processo de usinagem que desenvolveu produz rotores mais cilíndricos e precisos do que os fornecidos por seu fornecedor, resultando em projetos de superalimentadores que são 5% mais eficientes do que os usando os rotores fornecidos.
As medições feitas neste CMM permitiram que a Whipple determinasse a precisão de seus rotores fornecidos e os rotores em máquinas internas. Seu objetivo é atingir uma folga de 125 mícrons entre os rotores de acoplamento, o que agora pode ser alcançado com seus recursos internos de usinagem multitarefa.
Bright explica que a Whipple foi estimulada a usinar seus próprios rotores depois de ver os resultados das medições dos rotores de seu fornecedor feitas em sua máquina de medição coordenada Zeiss Accura (CMM). Esta CMM possui uma mesa rotativa, bem como a tecnologia de digitalização Vast da Zeiss e a opção Gear Pro em seu software de medição Calypso. Bright diz que este software é particularmente eficaz para medir rotores de acoplamento porque ele pode atribuir pontos de controle específicos nos perfis helicoidais do rotor macho e fêmea onde eles se encontram para determinar a folga entre os dois nesses pontos. Ele determinou que o perfil de cada rotor deveria ser de ±63 mícrons com o objetivo de atingir uma folga de aproximadamente 125 mícrons. A Whipple não estava conseguindo isso de seu fornecedor de rotores.
Trazendo Usinagem Interna
O processo de usinagem de rotor interno da empresa usando ferramentas de forma é semelhante ao de seu fornecedor, mas com modificações de fixação para aumentar a rigidez.
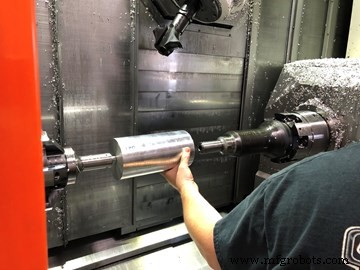
À medida que um operador carrega o rotor de alumínio 6061 vazio em o torno-fresador, o fuso principal da máquina e, em seguida, o subfuso prendem os moentes de aço salientes do eixo.
A máquina que adquiriu há alguns anos para esta aplicação é um torno-fresador Mazak Integrex e-420H-S II com cabeçote de fresagem de eixo B. Na verdade, este torno-fresador não realiza torneamento.
Os blanks cilíndricos de rotor de alumínio 6061 são primeiro perfurados longitudinalmente em outra máquina para permitir que um eixo de aço seja pressionado neles. À medida que um operador carrega um blank no Integrex, o eixo principal da máquina e, em seguida, o subspindle prende os munhão salientes do eixo. Em seguida, o eixo B da máquina é drasticamente inclinado para orientar uma ferramenta de forma personalizada que corresponde ao perfil de canal do rotor desejado quando nesse ângulo. Finalmente, a ferramenta de forma giratória é movida ao longo do eixo Z à medida que o rotor é girado lentamente para criar cada canal em várias passagens.
Inicialmente, a Whipple usou pinças ER estilo pullback de comprimento estendido para prender os munhão do eixo. O comprimento estendido foi necessário para posicionar os blanks longe do subspindle para fornecer folga suficiente para o fuso do eixo B inclinar-se tanto sobre o mandril do subspindle quanto necessário para acomodar a ferramenta de forma. No entanto, a funcionalidade de pullback dessas pinças tornou o carregamento de blanks de rotor demorado e desafiador. O aperto da pinça (resultando em recuo) colocou carga excessiva no fuso principal, o que significa que o subspindle do eixo W teve que ser tracionado para ajudar a discar a carga. Caso contrário, podem ocorrer vibrações ou acabamentos de superfície ruins. Como resultado, os operadores grampeavam e grampeavam continuamente até que a maior parte da carga fosse eliminada, o que normalmente levava 10 minutos. Além disso, a Whipple estava constantemente substituindo as pinças devido ao desgaste que elas experimentavam ao serem apertadas e afrouxadas tantas vezes.
Ao contrário das pinças ER usadas anteriormente, dead- as pinças de comprimento não puxam as peças de trabalho e colocam carga no fuso principal que teria que ser eliminada. Isso reduziu as configurações de 10 para dois minutos.
Seguindo o conselho de Kellen Bush, engenheiro de aplicação da Mazak que trabalhou com Whipple neste projeto, a empresa entrou em contato com a Hainbuch para elaborar uma abordagem alternativa de fixação. O gerente de vendas da Hainbuch, Tom Chambers, explica que a solução de fixação personalizada da empresa não apenas fornece o alcance estendido necessário para permitir que o eixo B da máquina se incline para o ângulo necessário sem interferência, mas também oferece maior rigidez enquanto simplifica as trocas. Isso é possível em grande parte porque pinças de comprimento morto são usadas em vez de tipos de pullback. Chambers diz que as pinças de comprimento morto “fixam no espaço”, o que significa que as peças do rotor não se moverão quando as pinças forem fixadas. Como resultado, nenhuma carga adicional que teria que ser discada é aplicada ao fuso principal. As trocas agora levam apenas dois minutos.
As ferramentas de forma da Kyocera Unimerco que a Whipple usa para usinar seus rotores (assim como o fornecedor de rotores da Whipple) na verdade não são comumente usadas para cortar metal. Anders Varga, gerente de vendas da Kyocera Unimerco, diz que esse tipo de ferramenta é normalmente usado para cortar madeira, compósitos e outros materiais fibrosos. Isso se deve principalmente à quantidade de pressão que seria exercida na ferramenta como resultado da alta área de contato entre uma peça de metal e as arestas de corte da pastilha longa. O fato de essas ferramentas poderem ser usadas nesta aplicação de usinagem de rotores mostra a rigidez da máquina com a interface do fuso Capto e sua fixação personalizada.
O uso de ferramentas de forma que combinam com o perfil de canal helicoidal dos rotores (perfis que Bright refinou) elimina o polimento que pode ser necessário se várias fresas de topo fossem usadas para esculpir os canais. Os rotores são usinados para que seus lóbulos sejam os maiores possíveis, mas ligeiramente subdimensionados para permitir um revestimento proprietário subsequente. A Whipple normalmente mantém duas ferramentas de desbaste e três ferramentas de acabamento à mão para rotores macho e fêmea. As ferramentas usam pastilhas de metal duro micro-grão sem cobertura. As pastilhas para as ferramentas de desbaste são fixadas aos corpos das ferramentas por meio de parafusos; ferramentas de acabamento são soldadas a eles.
Ao usar ferramentas de formulário, o Whipple não tem para realizar o acabamento secundário como faria se usasse fresas de topo para criar as ranhuras do rotor.
Agora, não apenas este processo de usinagem está atingindo a meta de folga de 125 mícrons da Bright entre os rotores de acoplamento, mas a cilindricidade do rotor de ponta a ponta é mais consistente. Ele diz que, com a abordagem original de fixação, a diferença na cilindricidade de uma extremidade de um rotor em comparação com a outra pode chegar a 10 mícrons. Isso foi reduzido para 1 mícron. Os tempos de ciclo do rotor também são um pouco mais rápidos. Os tempos de ciclo para um rotor macho são 14 minutos e um rotor fêmea leva 20 minutos. Mas, para Whipple, isso é molho. Seus principais objetivos eram alcançar maior precisão de usinagem do rotor e mudanças de velocidade, ambas as quais ela realizou.
Equipamento industrial
- Mecademic Robotics se expande para grandes mercados com seu pequeno robô
- Schilling Robotics integrará o software Energid em seu robô submarino Gemini
- Serviço de ferramentas rápidas e suas aplicações eficazes
- Como as ferramentas impressas em 3D podem moldar o futuro da prototipagem
- Ferramentas para máquinas do tipo suíço
- Transformando as coisas difíceis
- Fazendo conexões enxutas
- Pensando em entrar no Live Tooling? Aqui está o que você precisa saber
- 5 principais vantagens da fabricação de metal personalizada
- O que é Kevlar? Um breve guia