O monitoramento da condição da máquina mantém a fábrica funcionando
Em 1901, uma patente foi emitida para Ransom E. Olds para a ideia de uma linha de montagem em movimento contínuo, que ele usou para construir os primeiros veículos Oldsmobile. Em 1913, Henry Ford melhorou o conceito adicionando correias transportadoras móveis e com essas duas inovações, o tempo necessário para montar um carro passou de 1 ½ dia para 1 ½ hora. Nascia a moderna fábrica de montagem.
Durante as quatro décadas seguintes, a ideia de uma linha de produção móvel foi adotada por inúmeras indústrias, de rádios a navalhas, relógios a berços, pregos a jornais. Durante a Segunda Guerra Mundial, os EUA construíram 300.000 aeronaves usando linhas de produção móveis. A ideia tornou-se a espinha dorsal da fabricação em todo o mundo e continua sendo a principal maneira de fornecer produtos aos mercados de massa.
As ferramentas e máquinas usadas para fazer o trabalho de montagem são a parte mais crítica de qualquer linha. Na década de 1950, a confiabilidade dos equipamentos da fábrica estava se tornando uma parte importante das operações. Se uma única máquina parasse de funcionar, toda a linha seria desligada até que os reparos pudessem ser feitos. Máquinas e montadoras ociosas reduziram a eficiência e impactaram os custos. A manutenção tornou-se importante.
Ao longo da última metade do século 20, a maioria das manutenções de fábricas consistia em manutenções periódicas programadas. Isso melhorou a confiabilidade e a vida útil das máquinas, mas não ajudou os operadores da fábrica a prever e evitar qualquer mau funcionamento do equipamento ou tempo de inatividade não programado. Nos últimos vinte anos, o monitoramento da condição da máquina tornou-se uma parte importante das operações da fábrica. Às vezes chamadas de Fábrica Inteligente, IoT Industrial (IIoT) ou Indústria 4.0, as fábricas estão adicionando sensores e sistemas analíticos que monitoram a integridade dos equipamentos de fabricação.
O monitoramento de condições é o processo de equipar equipamentos com sensores que podem identificar mudanças paramétricas significativas indicativas de uma falha ou falha iminente. Esses sistemas procuram duas coisas. Primeiro:a máquina está operando fora de seus parâmetros de projeto, exigindo uma resposta rápida? Segundo:Quais são as tendências de longo prazo dos parâmetros críticos para prever quando a máquina precisará de manutenção, reparo ou substituição.
Motores elétricos de fábrica
Uma das máquinas mais onipresentes nas fábricas é o motor elétrico. Estima-se que existam hoje 300 milhões de motores funcionando em fábricas em todo o mundo. Eles fornecem o poder de fabricar, montar e movimentar produtos em uma fábrica. A falha de um único motor pode interromper uma linha de produção, custando US$ 10.000 por hora. Sensores e análises de monitoramento de condições fornecem um aviso antecipado de problemas. Tratar esses problemas rapidamente resulta em menor custo de manutenção, menos interrupções no fluxo do processo e maior segurança para os operadores do equipamento.
A saúde de qualquer motor pode ser determinada monitorando três parâmetros operacionais:
-
Vibração — medida com um acelerômetro.
-
Temperatura — medida com um sensor de temperatura do tipo contato.
-
Corrente — medida com um sensor de corrente do tipo indutivo ou shunt.

Os acelerômetros fornecem dados sobre a saúde mecânica do motor. Os sensores de temperatura fornecem dados sobre a integridade mecânica e elétrica, e os sensores de corrente analisam a integridade elétrica. Os sensores também podem fornecer dados sobre a condição dos equipamentos e ferramentas conectadas ao motor.
Acelerômetros
Todos os motores rotativos têm uma armadura que é suspensa por rolamentos e gira em várias velocidades. As armaduras são balanceadas para não vibrar durante a rotação. No entanto, uma armadura desequilibrada ou danificada cria vibração que pode afetar os rolamentos. Se as vibrações estiverem em frequências ressonantes de outros equipamentos conectados ao motor, os danos podem ser graves e rápidos. A frequência de vibração de um motor coincide com a RPM do motor e normalmente varia de alguns Hz a 4 kHz. Os acelerômetros são adequados para medir essas vibrações.
Os acelerômetros também são usados como microfones de contato que ouvem ruídos de alta frequência (guinchos) dos rolamentos onde a lubrificação foi esgotada. Essas frequências variam de 5kHz a 15kHz. Os acelerômetros piezoelétricos funcionam bem porque têm uma ampla resposta de frequência que cobre ambas as faixas de frequência com um único dispositivo.
Normalmente, uma Transformada Rápida de Fourier (FFT) é usada para analisar o sinal. Os dados FFT mostram cada banda de frequência de vibração e sua intensidade. A Figura 2 indica as frequências e amplitudes naturais de vibração de um motor típico.
Os novos motores têm frequências naturais de vibração que são registradas e usadas como linha de base para comparação com os dados obtidos posteriormente na vida útil do motor. Se essas medições permanecerem na mesma faixa dos dados originais, o motor está em boas condições. Se as frequências ou intensidades começarem a mudar com o tempo, é uma indicação de desgaste em partes do motor e uma falha pode ser iminente. Portanto, os reparos podem ser agendados antes que ocorra uma falha. Isso elimina paradas catastróficas de linha e melhora a eficiência da fabricação.

A Figura 3 mostra o sensor de vibração modelo 8911 da TE Connectivity Sensors Business Unit. Ele contém um acelerômetro piezoelétrico e um microcontrolador que realiza uma conversão FFT para um formato que os clientes precisam. Além disso, este sensor é alimentado por bateria e transmite os dados sem fio em frequências LoRa. Isso elimina a fiação rígida. O sensor pode ser facilmente montado em um motor com adesivo, pino de montagem ou base magnética. Sem fiação e montagem simples, o sensor pode passar de pronto para uso para operação total em um período muito curto de tempo e a um custo muito baixo.
Sensores de temperatura
As duas partes de um motor mais afetadas por altas temperaturas são os rolamentos e os enrolamentos do estator. Para serem eficazes, os sensores que medem esses parâmetros devem estar em contato físico íntimo com as partes do motor de interesse, de modo que geralmente são necessários projetos exclusivos para aplicações de motores.
Em operação, os rolamentos do motor normalmente funcionam entre 60° – 70°C (140° – 160°F). Quando carregados e lubrificados adequadamente, os rolamentos podem ter uma vida útil extremamente longa. O problema mais comum ocorre quando os lubrificantes desaparecem devido a vazamentos ou falham devido ao superaquecimento do ambiente. Esses modos de falha podem ocorrer durante longos períodos de operação – 1000s de horas. À medida que o lubrificante se esgota, a temperatura do rolamento começa a subir e pode ser facilmente rastreada com um sensor de temperatura e um software analítico.
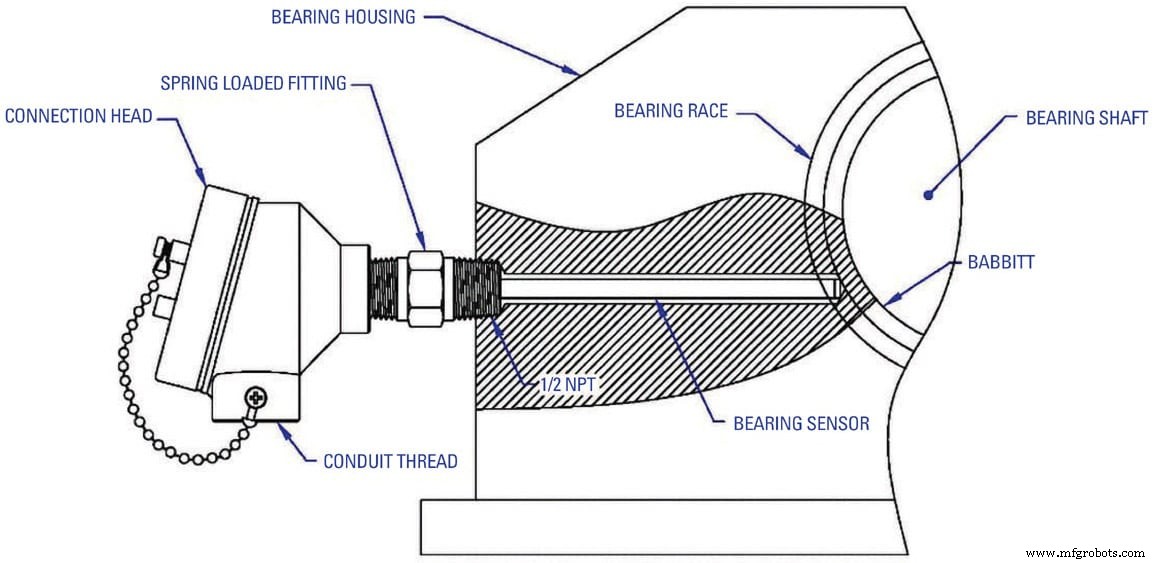
A Figura 4 mostra um sensor de temperatura do tipo NTC ou RTD com mola que é projetado para estar em contato direto com uma pista de rolamento externa. Esta montagem fornece as medições de temperatura mais precisas. A caixa do mancal deve ter recursos projetados para acomodar o sensor de temperatura e fornecer acesso próximo ao mancal.
Sensores de temperatura também são usados para medir a temperatura dos enrolamentos elétricos do estator. Estas são as bobinas que geram os campos magnéticos para impulsionar a rotação da armadura. Se esses enrolamentos forem danificados por impacto ou corrosão, a resistência do fio aumenta e sua capacidade de conduzir corrente diminui. Isso faz com que os fios afetados aqueçam. Eles podem chegar a temperaturas que derreterão o isolamento e até causarão um incêndio.

As Figuras 5a e 5b mostram sensores de temperatura (TE Connectivity Sensors Business Unit) sendo incorporados aos enrolamentos do estator em um motor. Os sensores tornam-se uma parte permanente do dispositivo.
Tal como acontece com os sensores de vibração, a temperatura de operação inicial é medida e registrada. Com o passar do tempo, as temperaturas são medidas periodicamente e comparadas com a linha de base. Se as temperaturas começarem a se desviar do normal, é uma indicação de problemas mecânicos nos mancais ou problemas elétricos nos enrolamentos do estator. Novamente, a manutenção pode ser programada antes que ocorra uma falha grave, evitando um desligamento inesperado da linha.
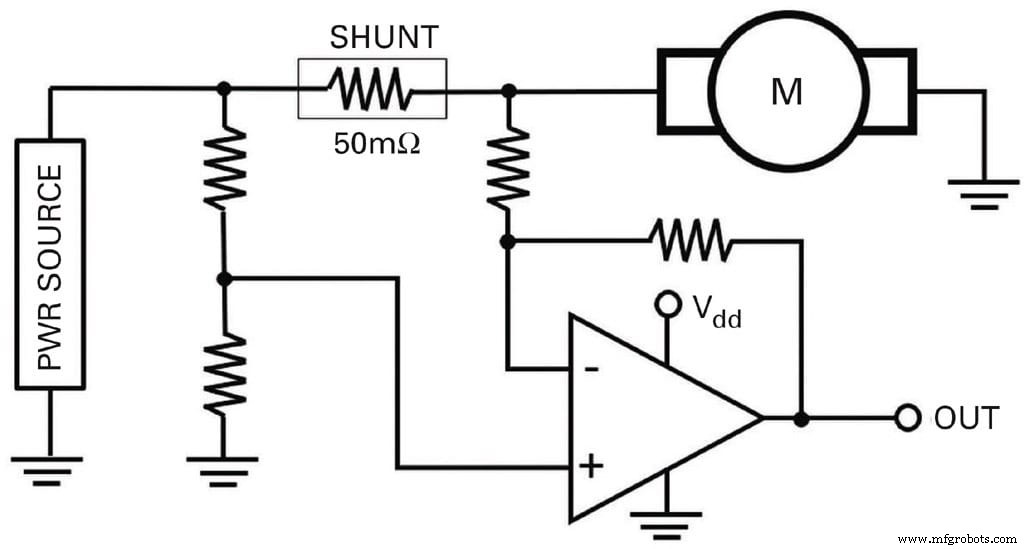
Sensores de corrente
Enquanto os sensores de vibração e temperatura podem relatar a saúde física de um motor, um sensor de corrente pode verificar sua saúde elétrica. Os sensores de corrente vêm em duas configurações básicas:projetos em derivação ou indutivos. Cada um tem vantagens e desvantagens. A quantidade de corrente que um motor consome é afetada por muitas coisas:a tensão aplicada, a velocidade do motor, a carga no eixo do motor e a condição das escovas da armadura. Correntes fora da faixa podem sinalizar problemas de tensão de alimentação, curtos nos enrolamentos do estator ou da armadura, escovas desgastadas ou problemas com ferramentas conectadas.

Um sensor de corrente shunt é um resistor de potência de valor muito baixo colocado em série com a linha de energia elétrica do motor. A tensão desenvolvida através do resistor é proporcional à corrente que flui através dele. Usando a lei de Ohm (I =E/R) e conhecendo os valores de tensão e resistência, a corrente pode ser calculada. Os shunts são usados onde é necessária uma precisão muito alta ou para motores sem escova de alta frequência. A Figura 6 mostra o esquema de um sensor shunt.
Os sensores de corrente indutivos usam um anel de alta permissividade ao redor do fio de alimentação. A corrente através do fio induz um campo magnético no anel (Bin). Um sensor de efeito Hall embutido no anel mede o campo magnético e, através de um amplificador e bobina enrolados ao redor do anel, induz um campo magnético reverso (BF) para neutralizar Bin. A tensão necessária para criar o campo BF é o sinal de saída. O efeito líquido dos dois campos magnéticos aparecerá como um campo nulo no sensor Hall. Quanto maior o fluxo de corrente no fio de alimentação, maior deve ser a tensão BF. (Veja a Figura 7)
Além do Motor

Muitas vezes, o equipamento conectado ao motor também pode ser monitorado quanto à saúde. A Figura 8 mostra um exemplo de uma fresadora que usa uma fresa rotativa multicanal para usinar uma superfície plana em uma peça de trabalho. A condição da ferramenta de corte rotativa é muito importante para a qualidade da operação de corte. Quanto mais afiadas as estrias no cortador, mais preciso será o corte e melhor será a superfície do trabalho acabado. À medida que cada flauta faz um corte, a corrente do motor aumenta para fornecer a potência necessária. Flautas afiadas requerem menos energia para cortar o metal. Flautas maçantes requerem mais potência.

Ao monitorar a corrente do motor para esta fresadora, é possível determinar quais das ranhuras da ferramenta de corte estão afiadas e quais estão cegas e precisam ser afiadas.
As contribuições do monitoramento de condições para a IIoT
Desde a invenção da linha de produção e a revolução industrial que ela criou, houve inúmeras inovações técnicas que impulsionaram o progresso na fabricação. As fábricas tiveram ganhos médios de produtividade de 2,8% ao ano nos últimos 70 anos. Tecnologias como ferramentas elétricas, moldagem por injeção, equipamentos pick &place, testes automáticos e robótica contribuíram. Hoje, o monitoramento da condição da máquina está sendo adicionado à mistura. O monitoramento de condições bem-sucedido começa com sensores localizados nas máquinas da fábrica que relatam constantemente dados sobre sua integridade e operação. Usando análises em tempo real, os operadores de fábrica podem identificar pontos problemáticos e agendar os reparos e manutenções necessários sem esperar por falhas catastróficas. Isso proporcionará ganhos de produtividade à manufatura. Tudo começa com sensores, no entanto.
Este artigo foi escrito por Pete Smith, gerente sênior, suporte de vendas e marketing, TE Connectivity Sensor Solutions — TES (Schaffhausen, Suíça/Berwyn, PA). Para mais informações, entre em contato com o Sr. Smith em Este endereço de e-mail está protegido contra spambots. Você precisa habilitar o JavaScript para visualizá-lo. ou visite aqui .
Sensor
- Mercado de monitoramento de condição para atingir $ 3,9 bilhões em 2025
- Como o monitoramento de condição aprimora um programa PdM
- Produto SKF Machine Condition Advisor ganha prêmio
- Fábrica de motores Honda beneficia-se do monitoramento da máquina
- O dispositivo SKF permite o diagnóstico da condição da máquina
- B&R apresentará solução de monitoramento de condições na Agritechnica
- Monitoramento da saúde do maquinário da fábrica
- Armadilhas de monitoramento de condições e potencial para manutenção de fábrica
- Monitoramento de condições em seu equipamento
- Monitoramento de condições:5 tipos comuns de falhas e sua importância