Kits fáceis de usar permitem o reparo interno de estruturas compostas
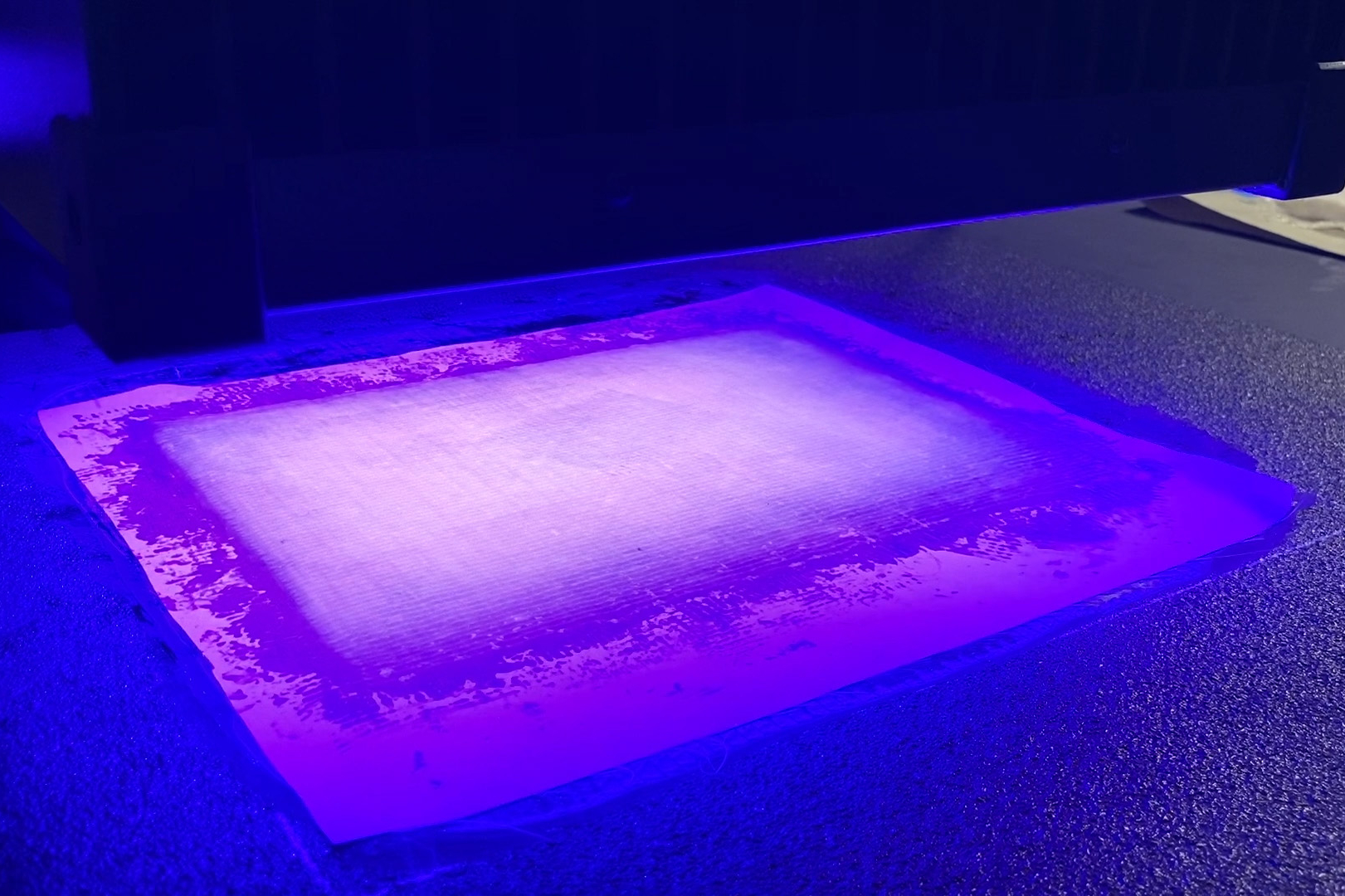
As pontes modulares implantáveis são um recurso chave em operações táticas militares e logística, bem como para restaurar a infraestrutura de transporte durante desastres naturais. A construção composta está sendo investigada para reduzir o peso dessas pontes, o que, por sua vez, reduz a carga sobre os veículos de transporte e os mecanismos de lançamento e recuperação. Os compósitos também oferecem o potencial de aumentar a capacidade de transporte de carga e estender a vida útil em comparação com as pontes de metal.
A Advanced Modular Composite Bridge (AMCB) é um exemplo, projetada e construída usando laminados de epóxi reforçados com fibra de carbono (Fig. 1) por Seemann Composites LLC (Gulfport, Miss., EUA) e Materials Sciences LLC (Horsham, Penn., EUA ) No entanto, a capacidade de reparar tais estruturas em campo tem sido um problema que dificulta a adoção de compósitos.
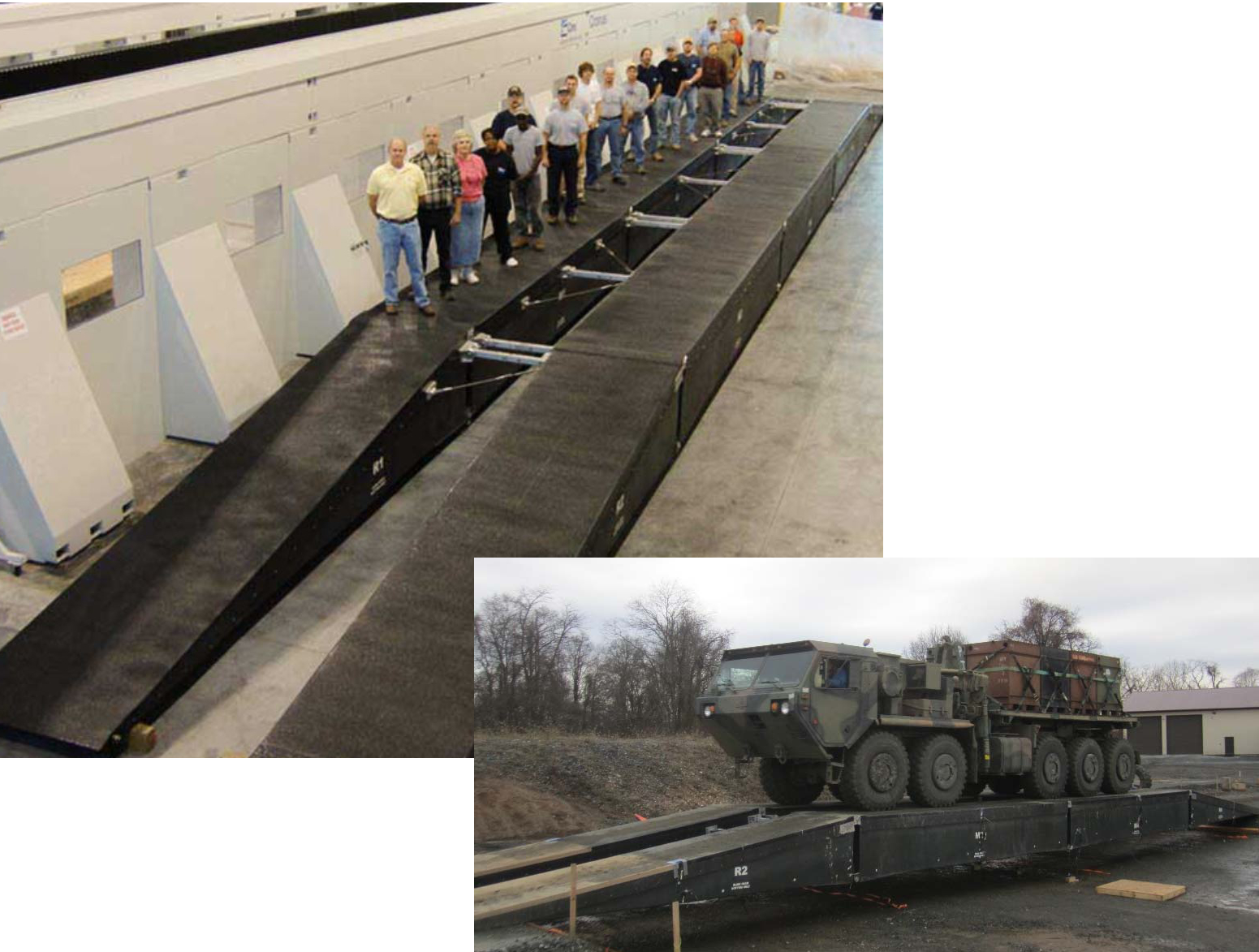
Em 2016, a Custom Technologies LLC (Millersville, Md., EUA) recebeu uma bolsa de Fase I de Pesquisa de Inovação em Pequenas Empresas (SBIR) financiada pelo Exército dos EUA para desenvolver um método de reparo que pode ser executado com sucesso por soldados em campo. Com base neste método, uma bolsa SBIR de Fase II foi concedida em 2018 para demonstrar novos materiais e equipamentos operados por bateria que poderiam restaurar 90% ou mais da resistência original da estrutura, mesmo quando o reparo do remendo é realizado por um novato sem treinamento prévio . A viabilidade da tecnologia foi estabelecida por meio da realização de uma série de tarefas analíticas, seleção de materiais, fabricação de corpos de prova e testes mecânicos, bem como reparos em pequena e grande escala.
De convés de navios rachados a conveses de pontes
O investigador principal para ambas as fases do SBIR foi Michael Bergen, fundador e presidente da Custom Technologies LLC. Bergen se aposentou do Naval Surface Warfare Center (NSWC) Carderock com um mandato de 27 anos no Departamento de Estruturas e Materiais, onde gerenciou o desenvolvimento e a aplicação de tecnologias compostas para a frota da Marinha dos EUA. O Dr. Roger Crane ingressou na Custom Technologies em 2015 após se aposentar da Marinha dos Estados Unidos em 2011 com 32 anos de serviço. Sua experiência em compostos inclui publicações técnicas e patentes que cobrem tópicos como novos materiais compostos, fabricação de protótipos, métodos de união, compostos multifuncionais, monitoramento de integridade estrutural e reparo de compostos.
Esses dois especialistas já haviam desenvolvido um processo exclusivo que usava compósitos para reparar rachaduras em 5456 superestruturas de alumínio no cruzador de mísseis guiados classe USS Ticonderoga CG-47. “Esse processo foi desenvolvido para reduzir o crescimento de rachaduras e servir como uma alternativa acessível para uma substituição de placa de convés de $ 2-4 milhões”, diz Bergen. “Assim, demonstramos que sabíamos fazer reparos fora do laboratório e em um ambiente de serviço real. Mas o desafio era que os métodos atuais para recursos militares não são muito bem-sucedidos. As opções são um reparo dobrador ligado [essencialmente, colar uma placa no topo da área danificada] ou remover o ativo de serviço para reparos no nível de depósito (nível D). Existem tantos ativos parados de lado porque um reparo de nível D é necessário. ”
O que é necessário, continua, “é um método que possa ser executado por um soldado sem experiência em compósitos, usando apenas um kit e manual de reparo. Nosso objetivo era tornar o processo fácil:Leia o manual, avalie os danos e faça o reparo. Não queríamos nenhuma mistura de resinas líquidas porque isso requer uma medição precisa para garantir a cura completa. Também precisávamos de um sistema sem resíduos HAZMAT para lidar após a conclusão do reparo. E teve que ser embalado como kits que podem ser implantados pelas redes já instaladas. ”
Novos materiais de remendo colados
Uma solução que a Custom Technologies demonstrou com sucesso é um kit portátil que permite um remendo de composto colado, feito sob medida para o tamanho do dano - até um máximo de 12 polegadas quadradas - usando um adesivo epóxi temperado. As demonstrações foram concluídas em compostos representativos do convés AMCB de 3 polegadas de espessura, que apresenta um núcleo de balsa de 3 polegadas de espessura (15 libras por pé cúbico de densidade) com películas de rosto compreendendo duas camadas de Vectorply Corp. (Phenix City, Ala., US) C-LT 1100 carbono 0 ° / 90 ° tecido biaxial costurado, uma camada de fibra de carbono C-TLX 1900 0 ° / + 45 ° / -45 ° triaxial e mais duas camadas de C-LT 1100 para cinco camadas no total. “Decidimos que o kit usaria remendos pré-fabricados em uma disposição quase isotrópica de multiaxiais semelhantes para que a orientação do tecido não fosse um problema”, diz Crane.
O próximo problema foi a matriz de resina para reparos de laminação. Para evitar a mistura de resinas líquidas, o patch usaria prepregs. “No entanto, o desafio para eles é o armazenamento”, explica Bergen. Para desenvolver uma solução de adesivo armazenável, a Custom Technologies se uniu à Sunrez Corp. (El Cajon, Califórnia, EUA) para desenvolver um pré-impregnado de fibra de vidro / éster de vinil que cura em seis minutos usando luz ultravioleta (UV). Também funcionou com a Gougeon Brothers (Bay City, Michigan, EUA), que sugeriu o uso de um novo filme de resina epóxi flexível.
As primeiras investigações já haviam demonstrado que o epóxi era a resina mais adequada para um pré-impregnado de fibra de carbono - éster de vinil de cura por UV funciona muito bem com fibras de vidro translúcidas, mas não cura sob fibras de carbono bloqueadoras de luz. Com base no novo filme dos irmãos Gougeon, o prepreg epóxi final demonstrou uma cura de uma hora a 210 ° F / 99 ° C com uma longa vida útil em temperatura ambiente - nenhum armazenamento em baixa temperatura é necessário. A resina também irá curar em temperaturas mais altas, diz Bergen, por exemplo a 350 ° F / 177 ° C se uma temperatura de transição vítrea mais alta (T g ) É necessário. Ambos os pré-impregnados são fornecidos no kit de reparo portátil como layups de remendos pré-impregnados pré-fabricados selados em envelopes de filme plástico.
Como os kits de reparo podem ficar armazenados por um longo tempo, a Custom Technologies foi solicitada a realizar um estudo de prazo de validade. “Compramos quatro caixas de plástico rígido - típicas do tipo que os militares usam para o transporte de equipamentos - e colocamos amostras dos adesivos epóxi e do pré-impregnado de éster de vinil em cada uma”, diz Bergen. As caixas foram então colocadas em quatro locais diferentes para teste:no telhado das instalações dos irmãos Gougeon em Michigan, no telhado de um aeroporto em Maryland, ao ar livre em uma instalação em Yucca Valley (deserto da Califórnia) e em um laboratório de teste de corrosão ao ar livre no sul da Flórida. Todos os casos tinham registradores de dados, Bergen observa, “e coletávamos dados e amostras de materiais a cada três meses para avaliação. Uma temperatura máxima de 140 ° F foi registrada pelas caixas na Flórida e na Califórnia, o que é um verdadeiro desafio para a maioria das resinas de reparo. ” Além disso, a Gougeon Brothers testou internamente a resina epóxi pura recém-desenvolvida. “Amostras mantidas por meses em um forno a 120 ° F começaram a polimerizar”, diz Bergen. “No entanto, para amostras correspondentes mantidas a 110 ° F, a química da resina avançou apenas uma pequena quantidade.”
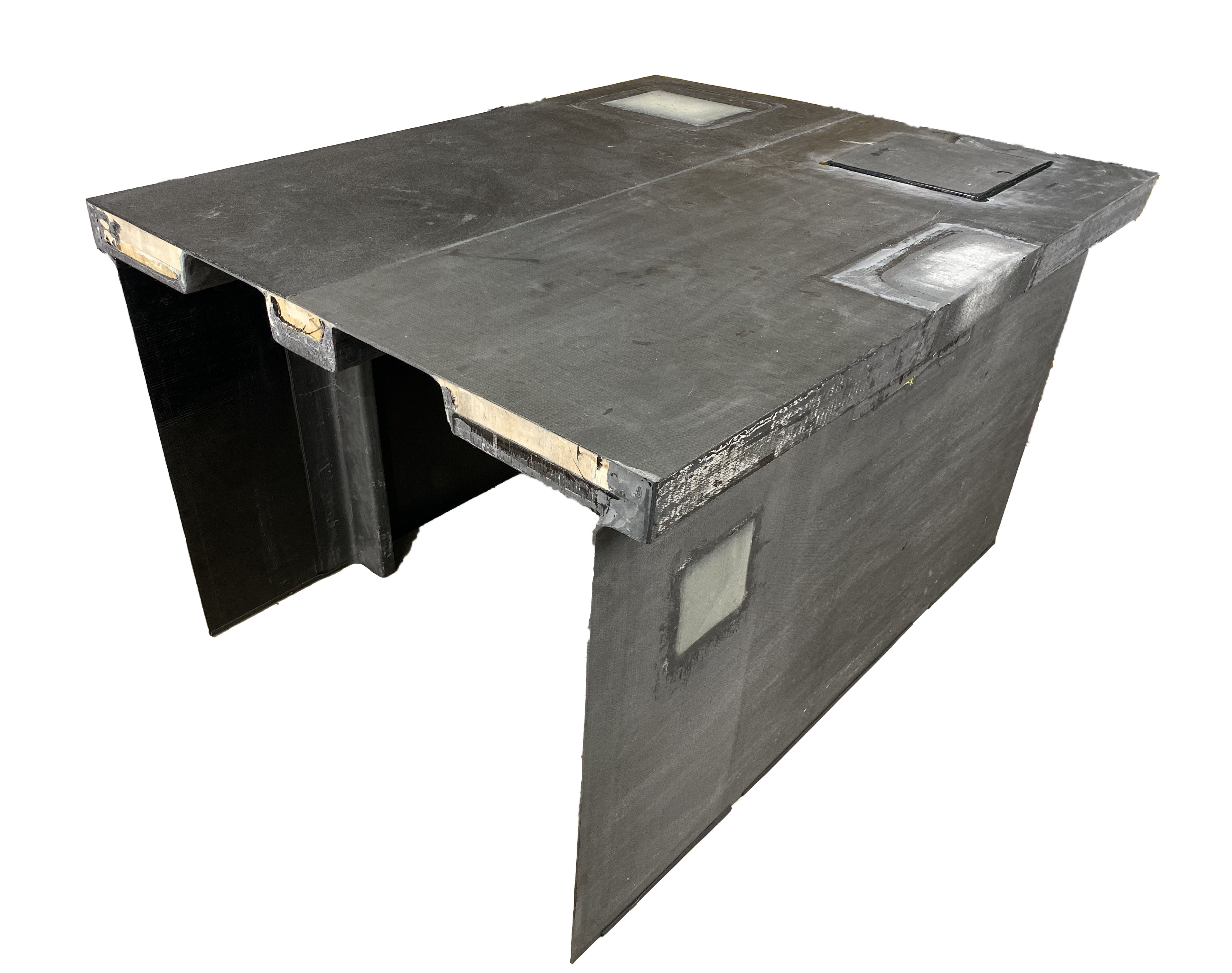
Teste de reparo
Para demonstrar a tecnologia de reparo, laminados representativos tiveram que ser fabricados, danificados e então reparados. “No projeto da Fase I, trabalhamos inicialmente com vigas de 4 x 48 polegadas em pequena escala e testes de dobra de quatro pontos para avaliar a viabilidade de nosso processo de reparo”, diz Crane. “Em seguida, fizemos a transição para painéis de 12 x 48 polegadas no projeto de Fase II, aplicando carga para criar um estado de tensão biaxial até a falha e, em seguida, avaliamos o desempenho do reparo. No projeto da Fase II, também concluímos os reparos em um modelo da AMCB que havíamos construído. ”
Os painéis de teste usados para demonstrar o desempenho do reparo foram fabricados usando o mesmo pedigree em laminado e núcleo que o AMCB construído por Seemann Composites, diz Bergen, “mas reduzimos a espessura da folha de rosto de 0,375 polegadas para 0,175 polegadas, com base nos eixos paralelos teorema. Esta abordagem, junto com elementos adicionais da teoria do feixe e teoria clássica do laminado [CLT], foi usada para relacionar o momento de inércia e a rigidez efetiva do AMCB em escala real a artigos demonstrativos reduzidos mais tratáveis e econômicos. Em seguida, usamos modelos de análise de elemento finito [FEA] desenvolvidos pela XCraft Inc. (Boston, Mass., EUA) para refinar o projeto dos reparos estruturais. ” Os tecidos de fibra de carbono para os painéis de teste e o modelo AMCB foram adquiridos da Vectorply e o núcleo balsa foi fornecido pela Core Composites (Bristol, R.I., U.S.).
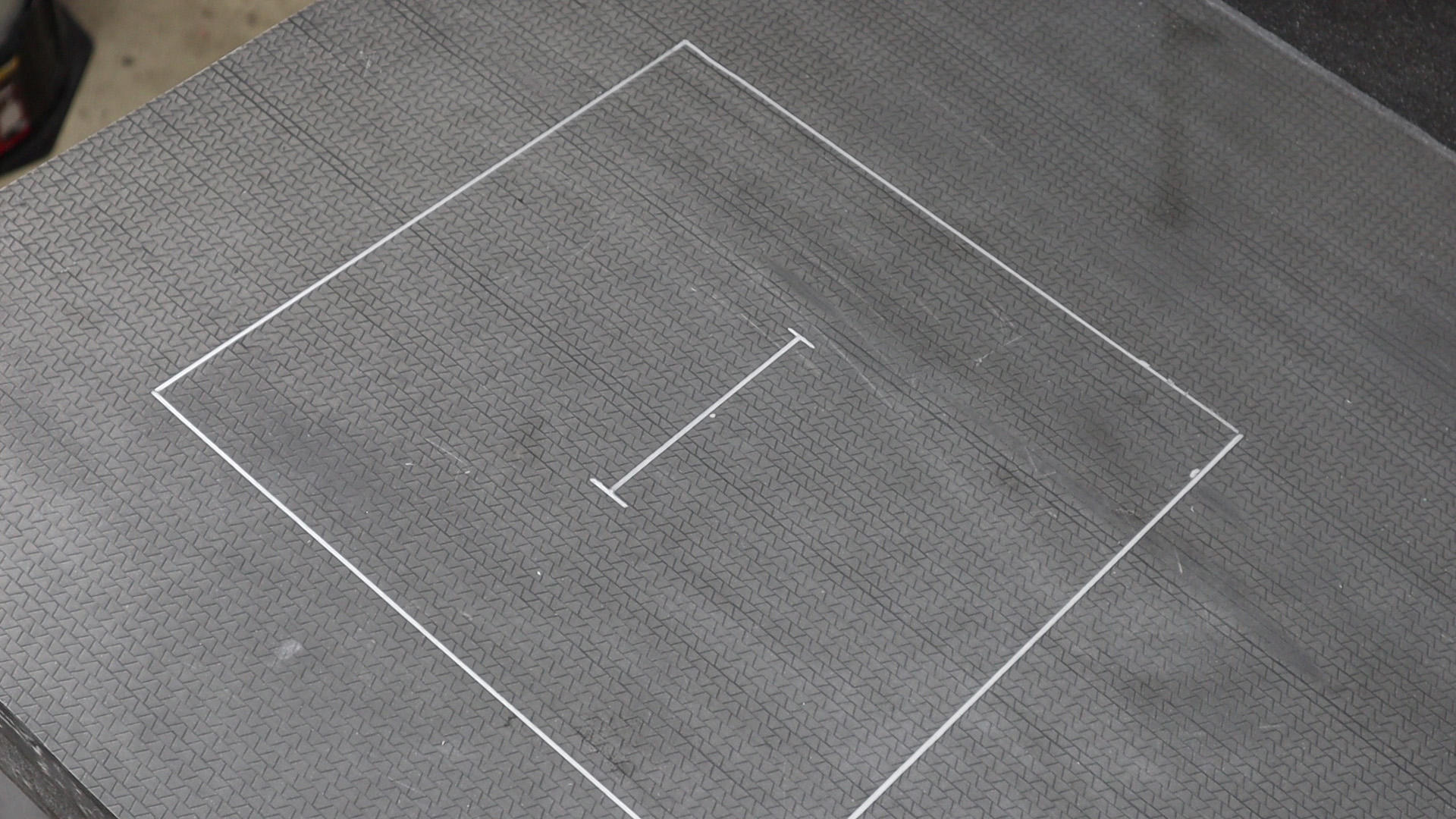
Etapa 1. Este painel de teste mostra o diâmetro do furo de 3 polegadas para simular os danos marcados no centro, bem como o perímetro de reparo. Crédito da foto para todas as etapas:Custom Technologies LLC.
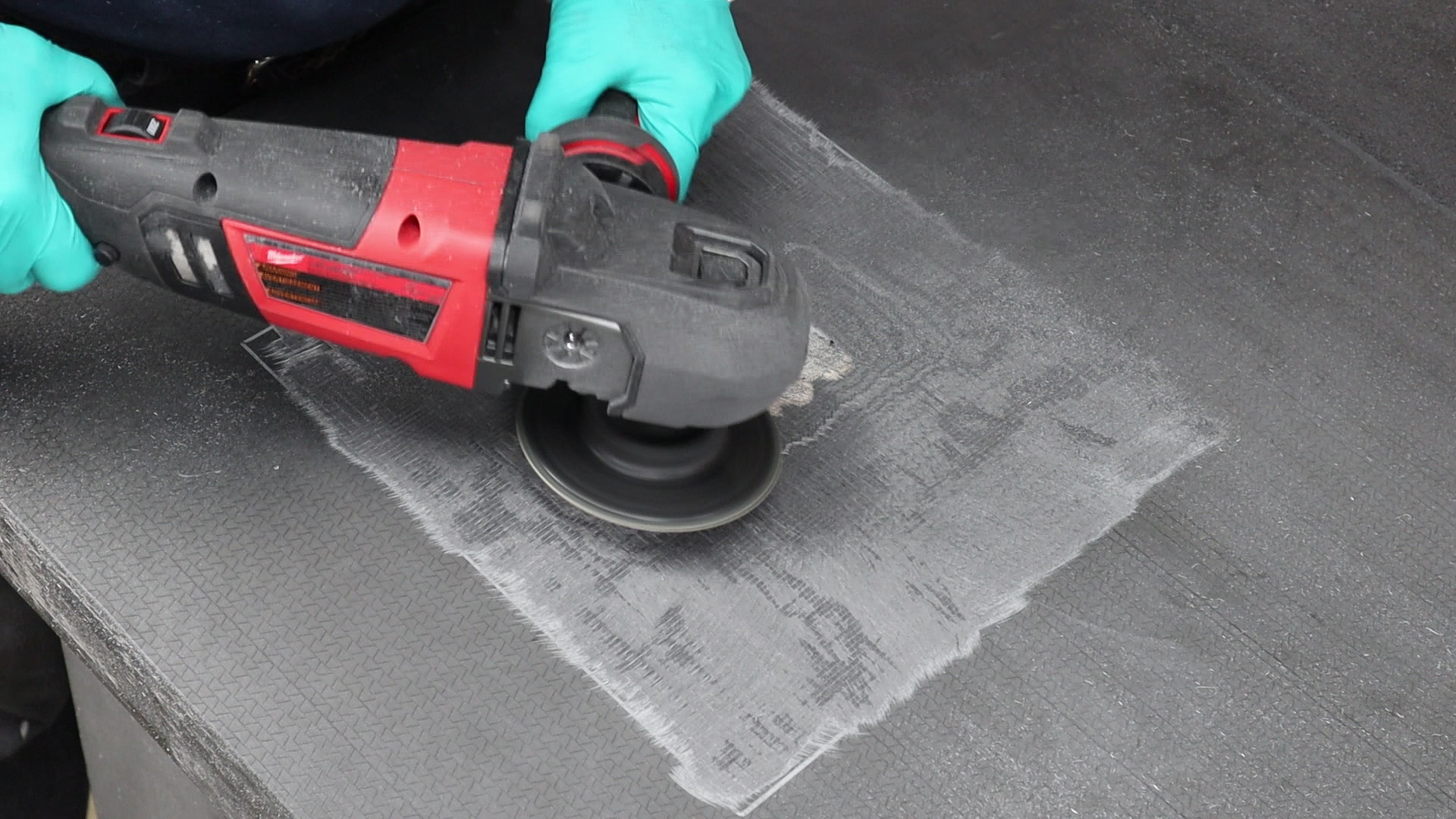
Etapa 2. Uma esmerilhadeira manual movida a bateria é usada para remover o material danificado e um cone de 12:1 para receber o remendo de reparo.
“Queríamos simular um grau de dano mais alto nos painéis de teste do que o que provavelmente será visto nos conveses das pontes em campo”, explica Bergen. “Então, nossa abordagem foi usar uma serra copo para fazer um furo de 3 polegadas de diâmetro. Em seguida, retiramos o plugue do material danificado e executamos um lenço 12:1 usando um moedor pneumático de mão. ”
Para o reparo de fibra de carbono / epóxi, explica Crane, uma vez que o material da folha de rosto “danificado” foi removido e o lenço apropriado aplicado, o pré-impregnado foi cortado na largura e no comprimento para coincidir com a conicidade da área danificada. “Para nossos painéis de teste, isso exigiu quatro camadas de prepreg que permitiram que o material de reparo ficasse nivelado com o topo da folha de carbono original não danificada. Depois disso, três sobreposições do pré-impregnado de carbono / epóxi foram centralizadas sobre esta seção de reparo. Cada camada sucessiva se estendeu 1 polegada em todos os lados da camada abaixo, o que proporcionou uma transferência de carga gradual do material circundante "bom" para a área reparada. ” O tempo total para realizar esse reparo - incluindo preparação da área de reparo, corte e colocação do material de reparo e aplicação do procedimento de cura - foi de aproximadamente 2,5 horas.
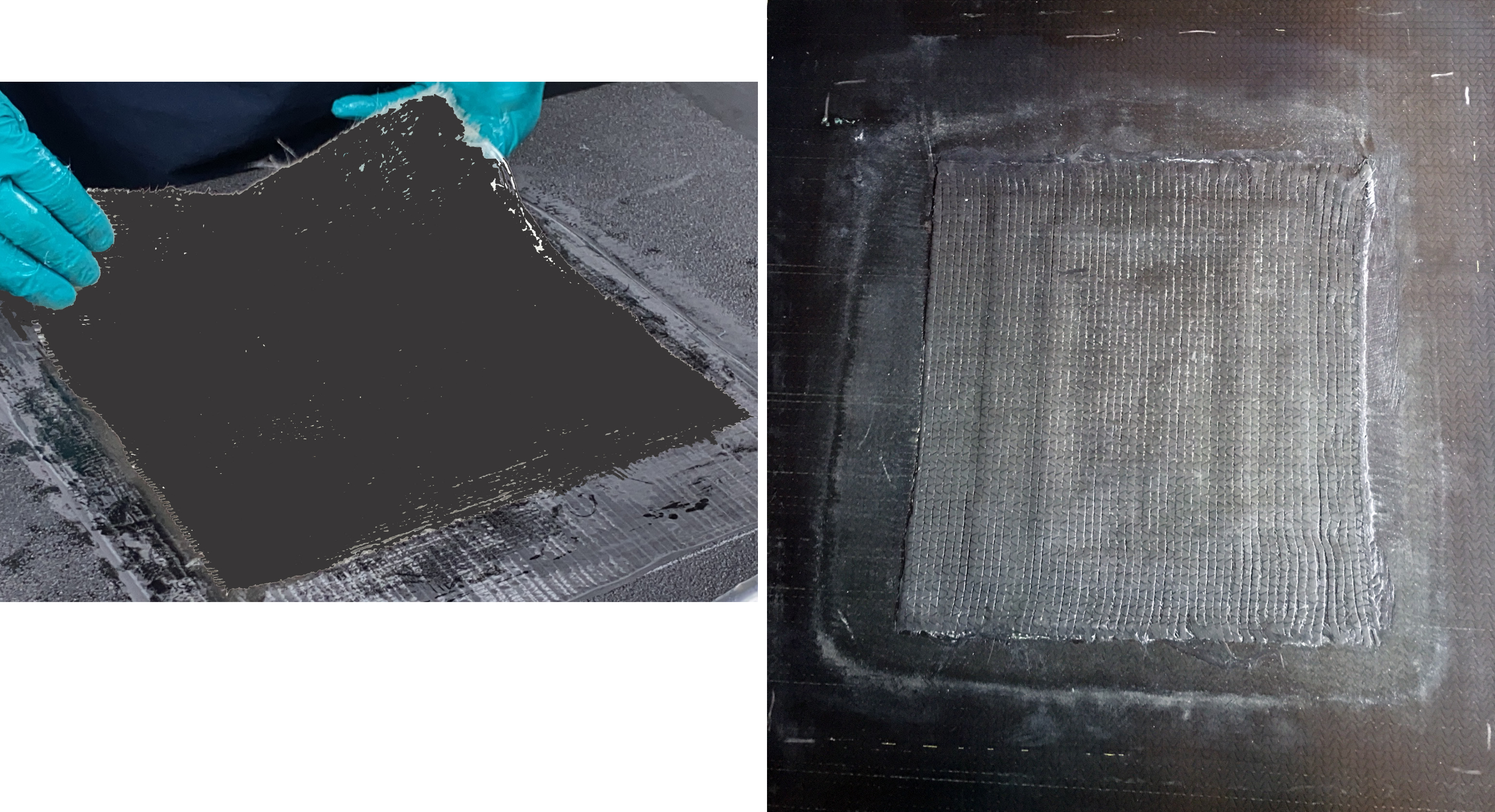
Mesmo que o reparo de carbono / epóxi seja simples e rápido, a equipe reconheceu a necessidade de uma solução ainda mais expedita que pudesse restaurar o desempenho. Isso levou à exploração do pré-impregnado curado por ultravioleta (UV). “O interesse na resina de éster de vinil Sunrez foi baseado na experiência anterior da Marinha com Mark Livesay, que fundou a empresa”, explica Bergen. “Começamos fornecendo à Sunrez um tecido de vidro quase isotrópico para pré-impregnar com seu éster de vinil e avaliamos o perfil de cura em condições variadas. Além disso, sabendo que a resina de éster de vinil não fornece propriedades de ligação secundária tão adequadas quanto o epóxi, houve um esforço adicional para avaliar vários agentes de acoplamento de linha de ligação e qualificar um para esta aplicação ”.
Outro problema é que a fibra de vidro não oferece as mesmas propriedades mecânicas da fibra de carbono. “Isso foi resolvido com o uso de uma camada adicional de éster de vidro / vinil em comparação com o patch de carbono / epóxi”, diz Crane. “O motivo pelo qual apenas uma única camada adicional foi necessária foi que o material de vidro era um tecido mais pesado.” Isso resultou em um adesivo adequado que poderia ser aplicado e, em seguida, curado em seis minutos, mesmo em temperaturas internas do campo muito frias / congelantes, sem a necessidade de fornecer calor. Crane observa que esse reparo pode ser concluído em uma hora.
Ambos os sistemas de patch foram demonstrados e testados. Para cada reparo, a área a ser danificada era marcada (etapa 1), confeccionada com a serra copo e removida com uma esmerilhadeira manual a bateria (etapa 2). A área de reparo foi então reduzida a uma redução de 12:1. A superfície escareada foi limpa com compressas embebidas em álcool (etapa 3). Em seguida, o remendo de reparo foi cortado no tamanho adequado, posicionado na superfície limpa (etapa 4) e consolidado com um rolo para remover as bolhas de ar. Para o pré-impregnado com fibra de vidro / éster de vinil de cura por UV, uma peel ply foi então colocada sobre a área de reparo e o adesivo foi curado usando uma luz UV sem fio por seis minutos (etapa 5). Para o pré-impregnado de fibra de carbono / epóxi, a área de reparo foi ensacada a vácuo e curada usando um adesivo quente pré-programado, de um botão e operado por bateria, por uma hora a 210 ° F / 99 ° C.
Etapas de reparo
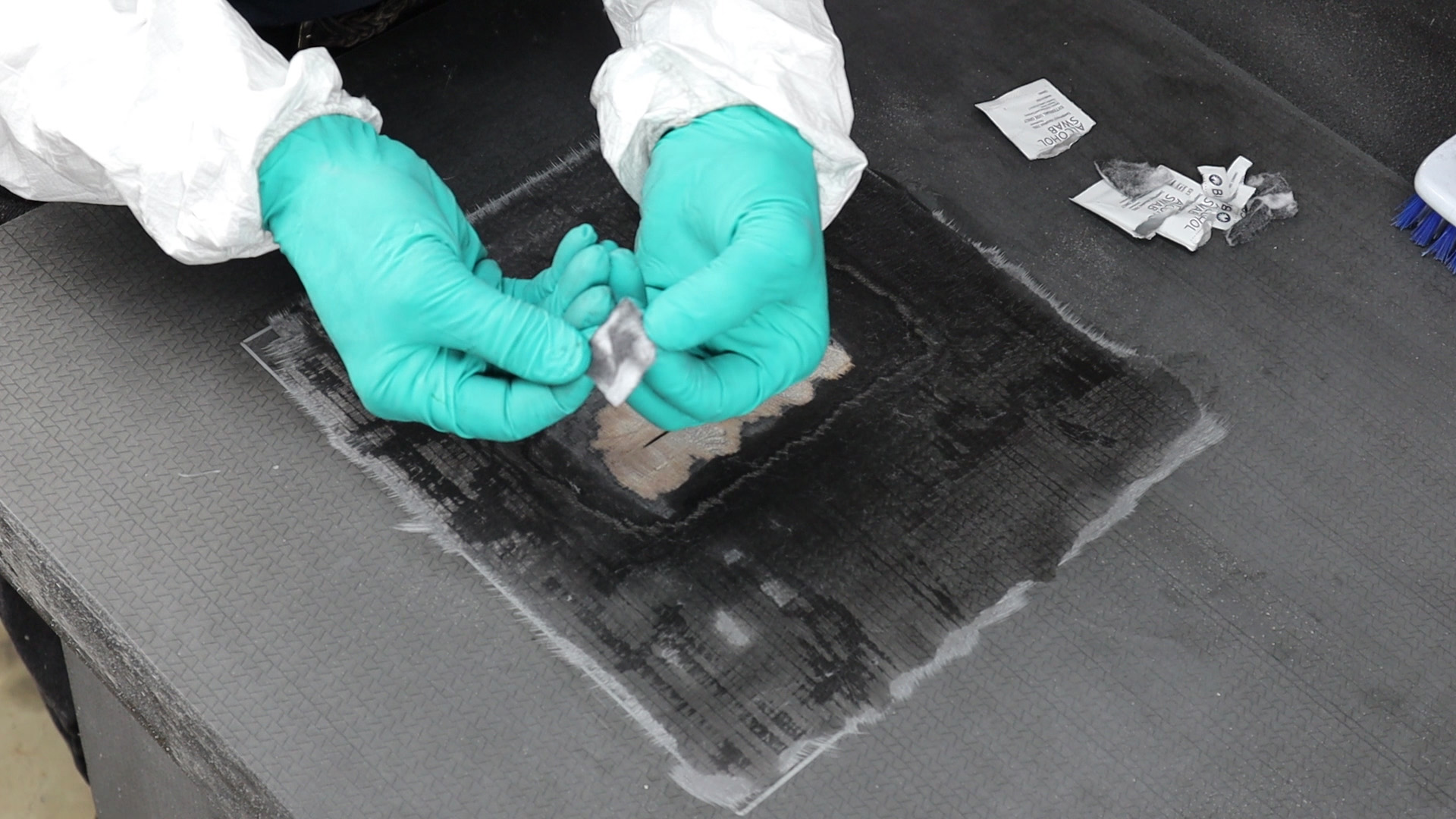
Etapa 3. A área de reparo preparada é então limpa com um pano com solvente usando compressas embebidas em álcool.
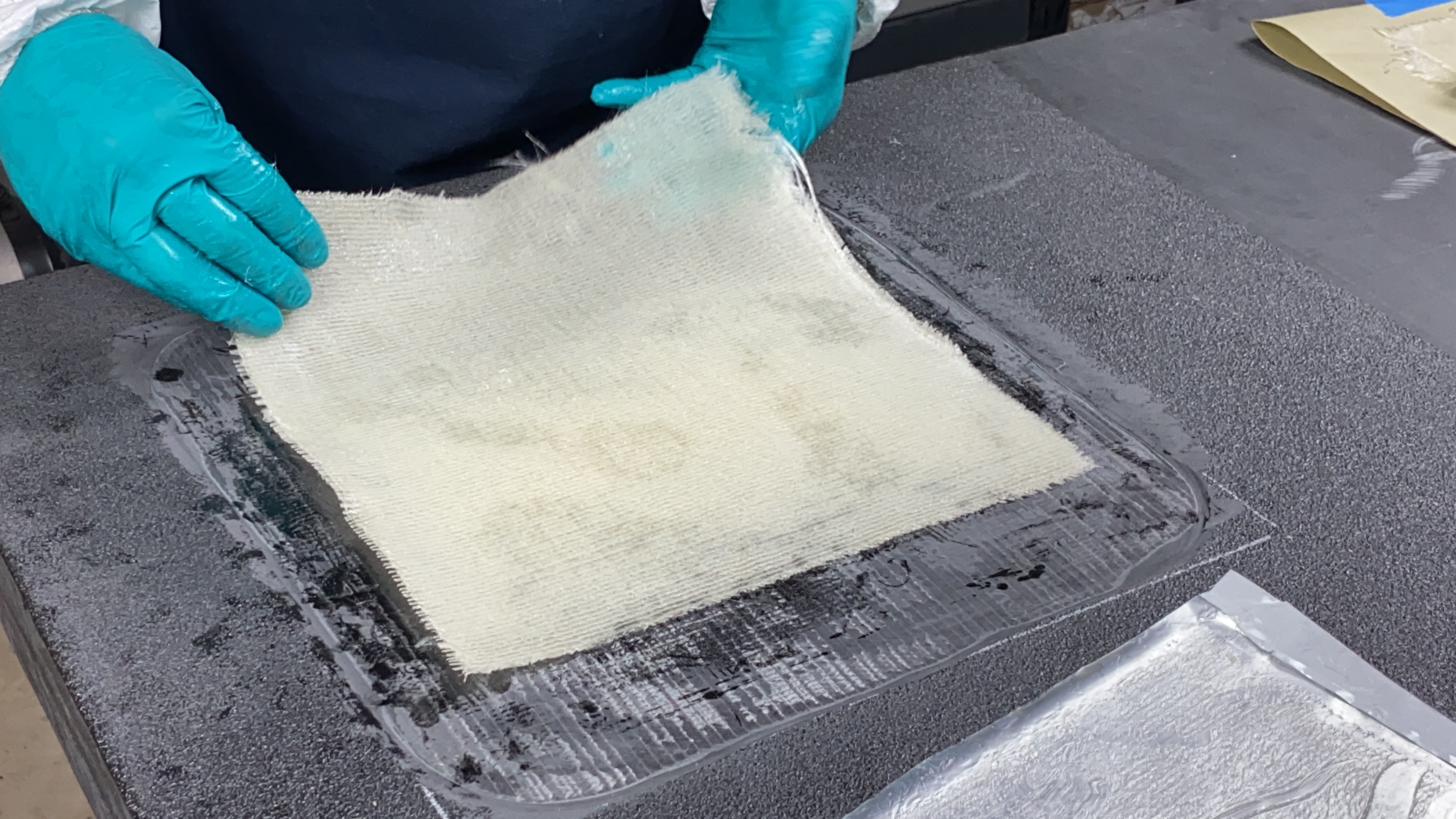
Etapa 4. O remendo de reparo de fibra de vidro / vinil éster é cortado no tamanho certo e posicionado na área de reparo.
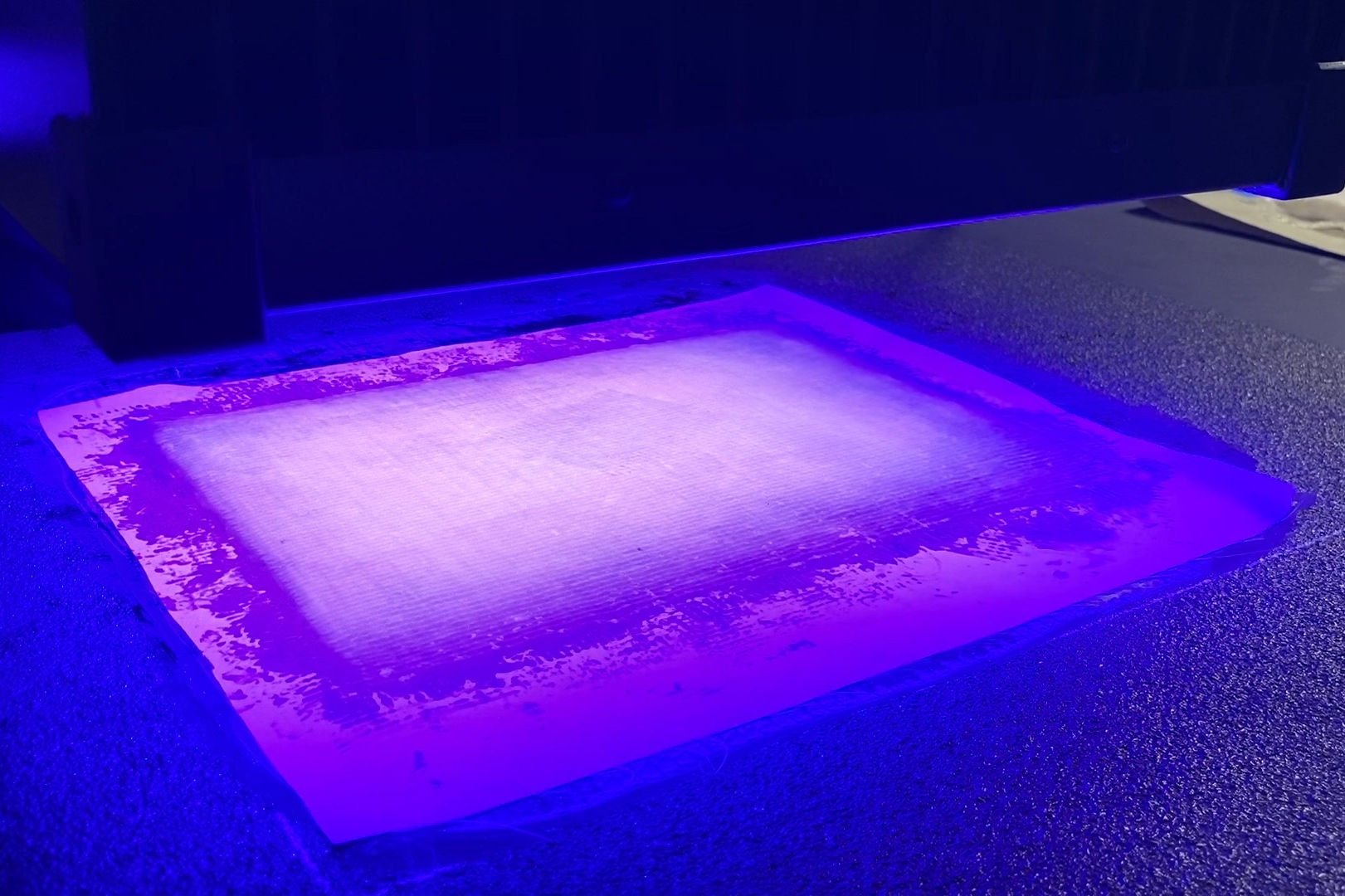
Etapa 5. Depois que um peel ply é colocado sobre a área de reparo, o reparo do patch é curado usando uma luz ultravioleta sem fio por seis minutos.
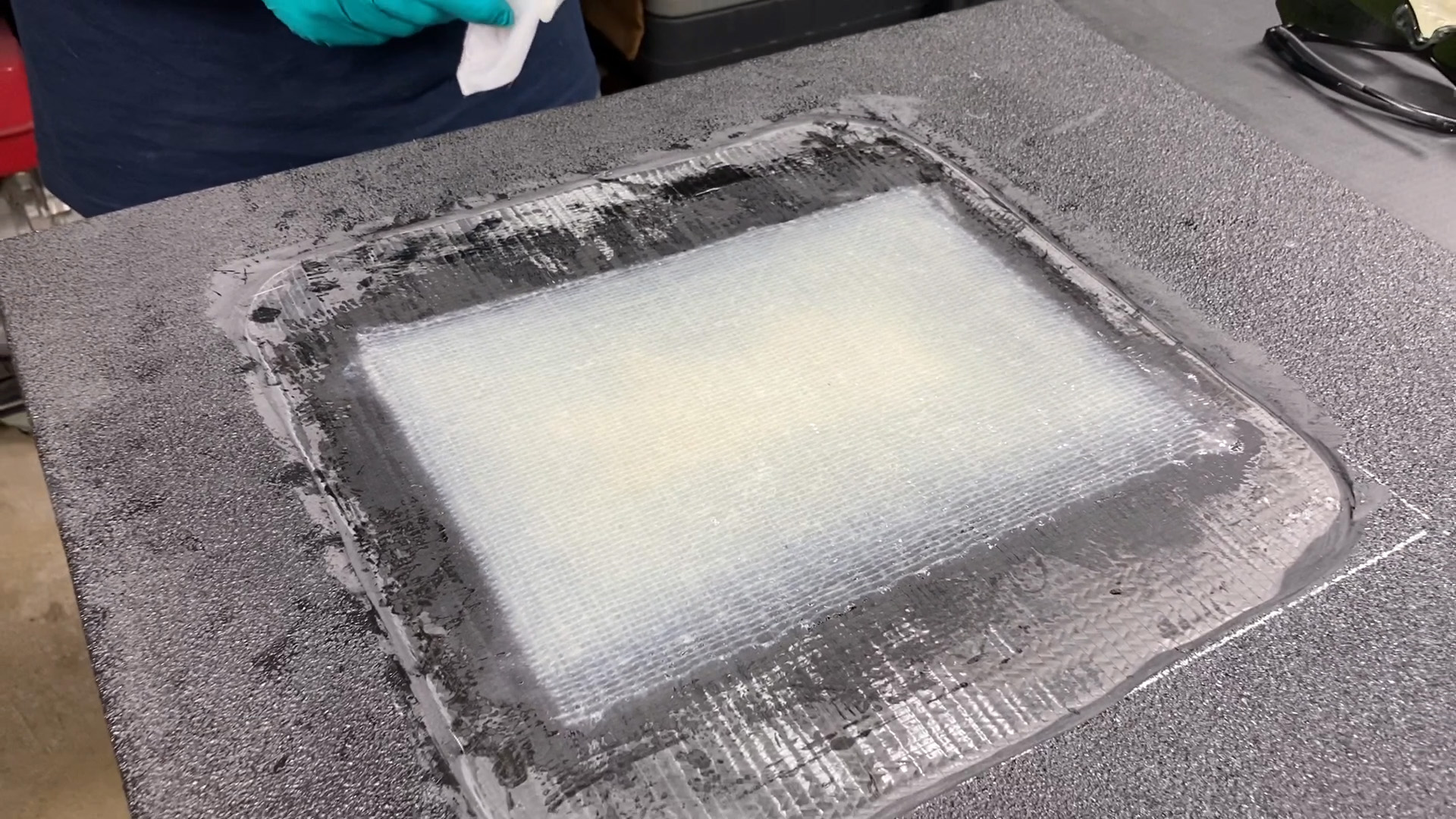
Etapa 6. Concluído o reparo do patch de pré-impregnado de fibra de vidro / éster de vinil curado por UV.
Anterior Próximo
“Em seguida, realizamos testes para avaliar a ligação adesiva do remendo e a capacidade de restaurar a capacidade de carga da estrutura”, diz Bergen. “Na Fase 1, fomos obrigados a demonstrar facilidade de aplicação e capacidade de restaurar pelo menos 75% da resistência. Isso foi realizado em vigas de fibra de carbono / epóxi e vigas de balsa de 4 x 48 polegadas em dobra de quatro pontos após o reparo do dano simulado. O projeto da Fase 2 usou painéis de 12 x 48 polegadas e teve que mostrar mais de 90% de exigência de resistência sob cargas de deformação complexas. Atendemos a todos esses requisitos e, em seguida, filmamos os métodos de reparo no modelo AMCB para fornecer uma referência visual de como usar as técnicas e equipamentos do campo interno. ”
Sucesso de principiante, aplicações futuras
Um aspecto fundamental do projeto era provar que um novato poderia facilmente concluir o reparo. Para isso, Bergen teve uma ideia:“Eu havia prometido uma demonstração aos nossos dois pontos técnicos de contato no Exército:Dr. Bernard Sia e Ashley Genna. Na revisão final do projeto da Fase I, pedi a Ashley, que não tinha experiência anterior em reparos, para fazer o reparo. Usando os kits e o manual que fornecemos, ela aplicou o patch e concluiu o reparo sem problemas ”.
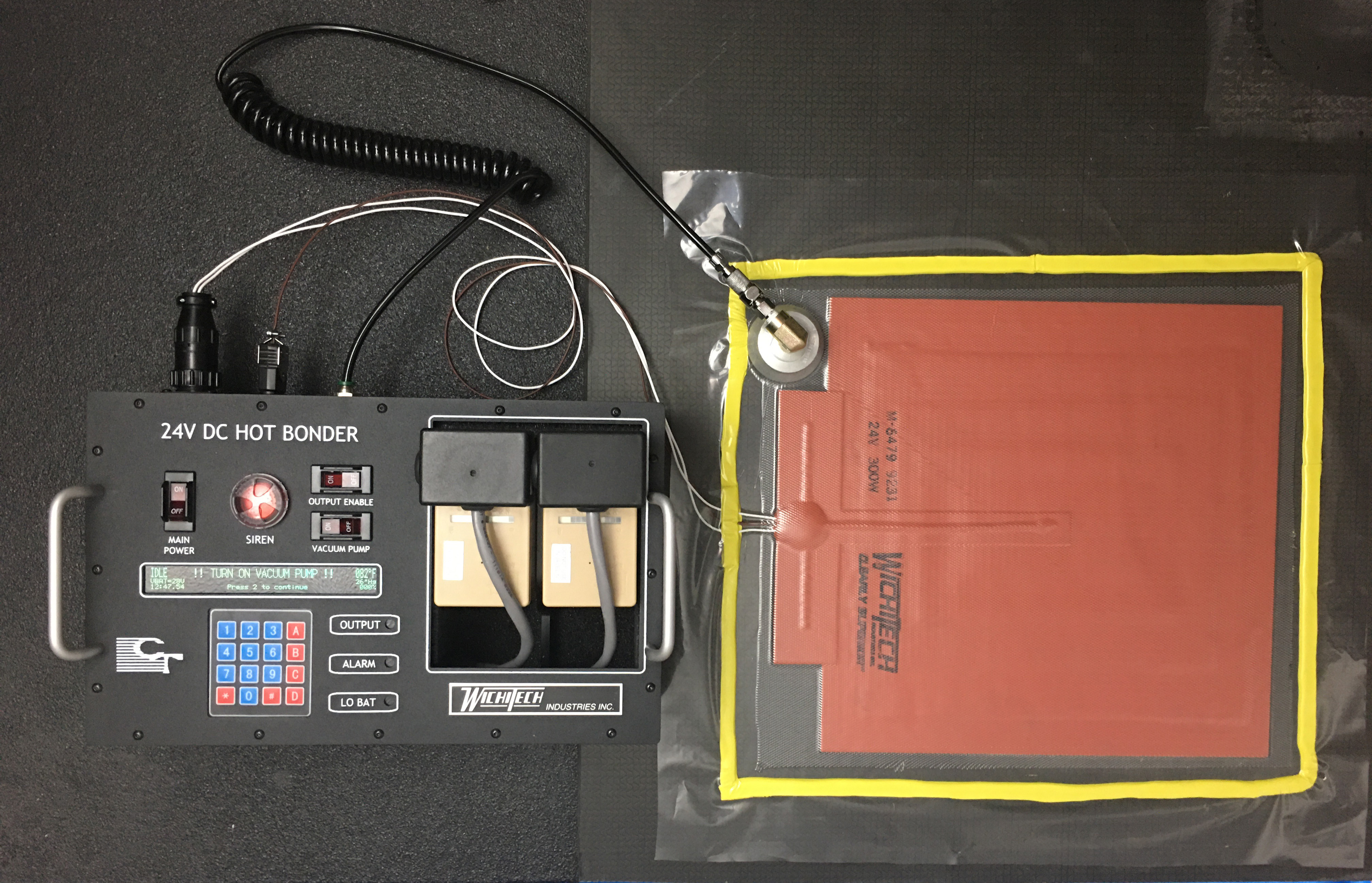
Outro desenvolvimento importante é o sistema de cura alimentado por bateria (Fig. 2). “Com o reparo interno, você só tem energia da bateria”, observa Bergen. “Todo o equipamento de processo em nosso kit de reparo desenvolvido é sem fio.” Isso inclui o adesivo a quente alimentado por bateria que a Custom Technologies desenvolveu com o fornecedor de adesivo a quente WichiTech Industries Inc. (Randallstown, Md., EUA). “Este aglutinante de calor alimentado por bateria é pré-programado para completar a cura, então o novato não precisa se programar para o ciclo de cura”, diz Crane. “Eles simplesmente apertam o botão e ele conclui a rampa e patamar apropriados.” As baterias usadas atualmente duram um ano antes de precisarem ser recarregadas.
Com o projeto de Fase II agora concluído, a Custom Technologies está preparando uma proposta de aprimoramento subsequente e coletando cartas de interesse e apoio. “Nosso objetivo é amadurecer essa tecnologia para TRL 8 e colocá-la em campo”, diz Bergen. “Também vemos potencial para aplicações não militares.”
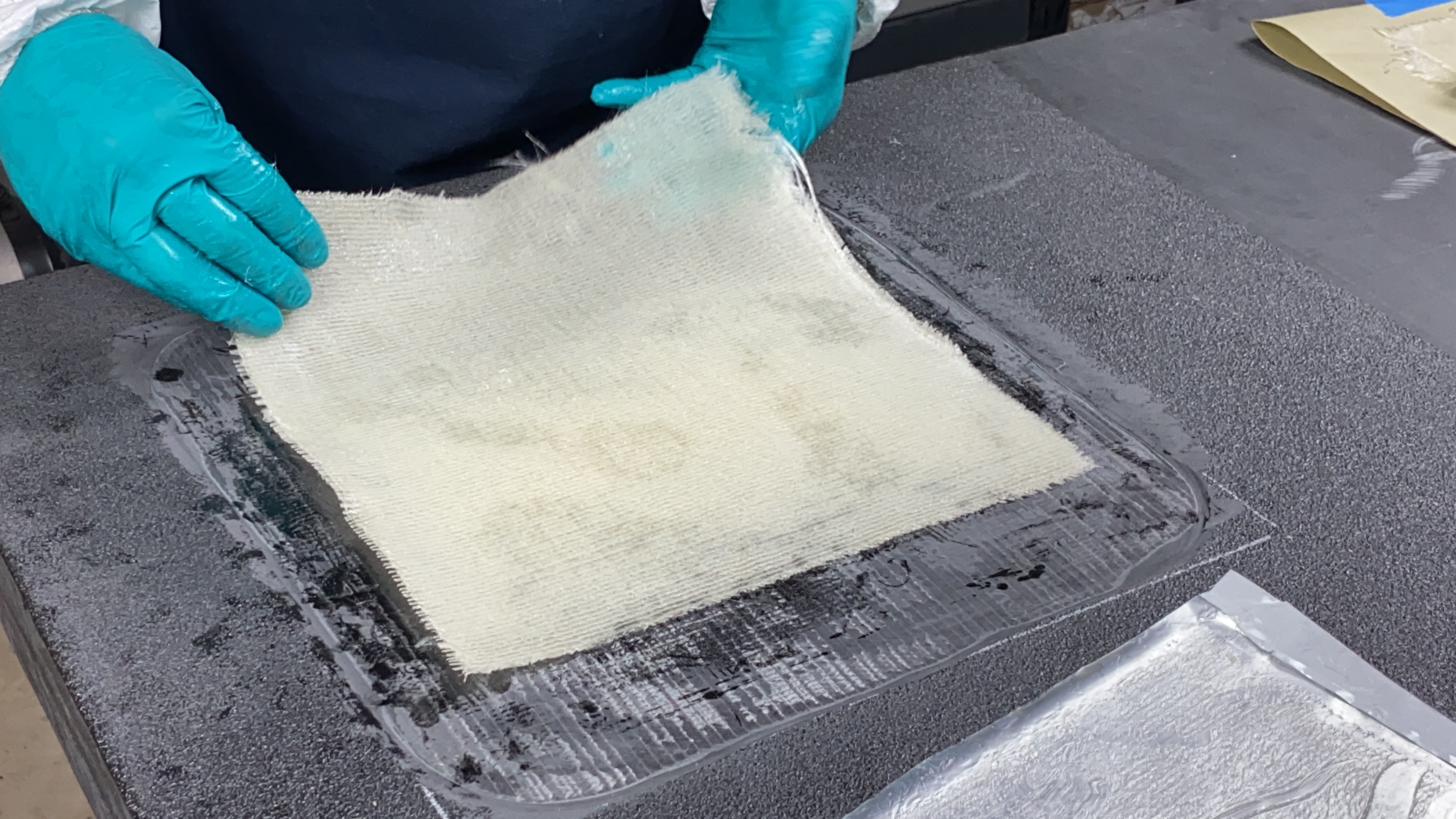
Resina
- 3 Aplicações mais comuns de engenharia de compostos termofixos
- Fabricação de compostos:A fabricação de materiais compostos
- Estruturas termoplásticas o foco da presença de Engel na China Composites Expo
- Desenvolvimento de estruturas de isogrelhas compostas usando tecnologia de deposição inovadora
- Alveus vai comercializar serviço de conserto de navios composto da Compa Repairs
- A pesquisa do AFRL avança compostos de CF / epóxi para impressão em 3D
- Hexcel faz parceria com Lavoisier Composites, Arkema
- AMRC e Parceiro Prodrive para avançar na fabricação de componentes de compósitos recicláveis
- TenCate celebra montagem de consórcio de compósitos termoplásticos no Brasil
- Materiais compostos:onde encontrá-los na NPE2018