Grandes tampas compostas protegem muita água
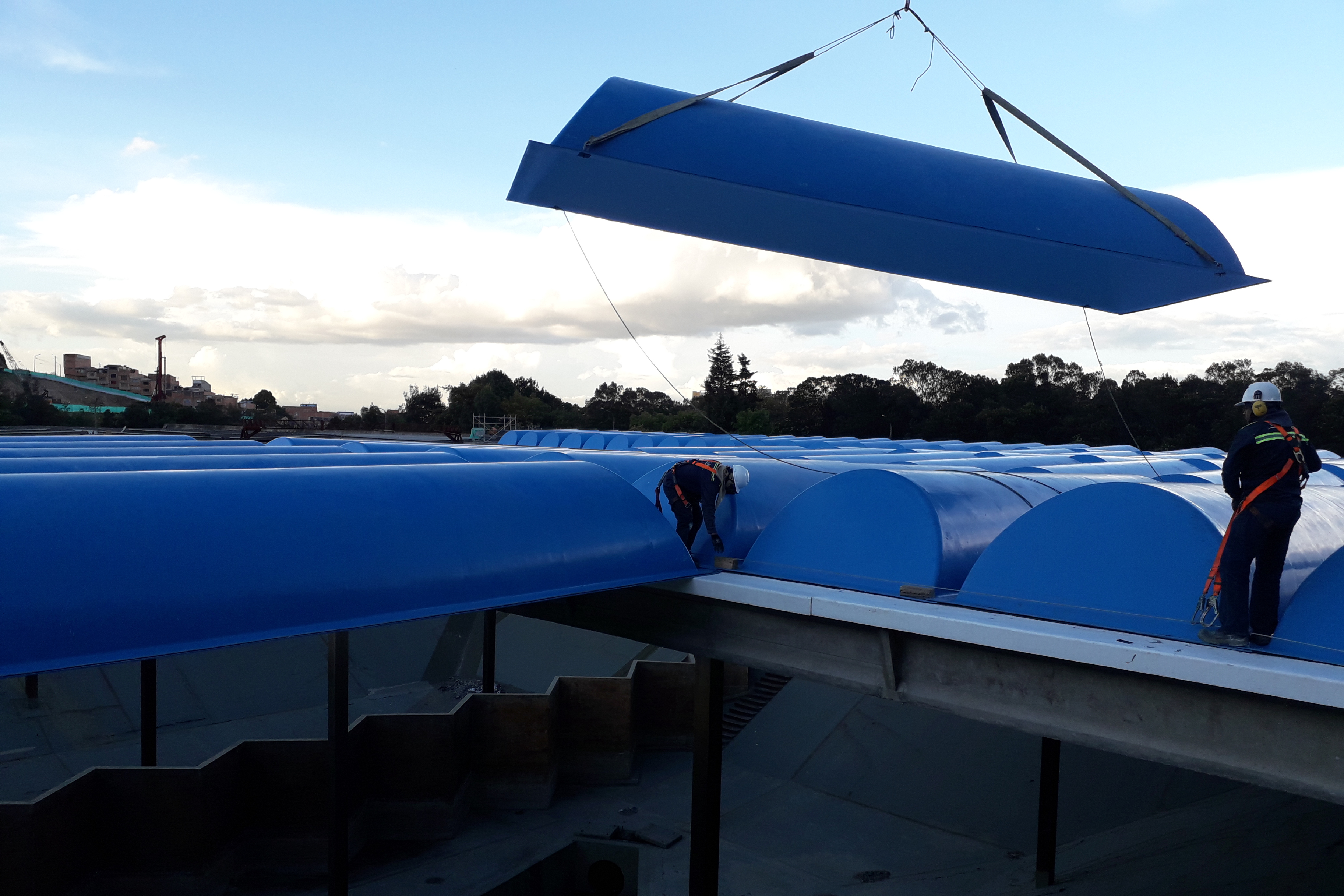
O armazenamento e entrega de água em Bogotá, Colômbia, como em qualquer grande área urbana, é complicado. O desafio não é de abastecimento, pois a cidade de cerca de 9 milhões de habitantes recebe 32 polegadas (824 milímetros) de chuva a cada ano, além do rio Bogotá fluir pela cidade. O desafio é captar essa água, tratá-la e armazená-la para que permaneça potável e disponível conforme a necessidade de residentes e empresas. Para isso, a Empresa de Acueductos y Alcantarillados (Empresa de Aquedutos e Esgotos, EAAB, Bogotá) construiu, ao longo dos anos, uma série de 59 tanques em toda a cidade para armazenar água tratada e garantir o abastecimento aos clientes.
Alguns desses tanques são tanques reais - totalmente fechados para proteger a água dos elementos externos. Outros, muitos deles mais antigos, são enormes bacias de concreto protegidas das intempéries por uma série de tampas removíveis. Um desses tanques, chamado Casablanca e localizado no bairro Ciudad Bolivar, no sul de Bogotá, atende a uma população de cerca de 3 milhões de pessoas. Casablanca, o maior tanque de armazenamento de água da rede EAAB e o maior tanque de armazenamento de água da Colômbia, mede 144 metros (472 pés) de comprimento x 110 metros (361 pés) de largura x 9 metros de profundidade e tem capacidade para armazenar 143.000 metros cúbicos ( 38 milhões de galões) de água. O tanque é dividido ao meio por um divisor de concreto que desce pelo meio, de modo que a água é armazenada em duas seções iguais.
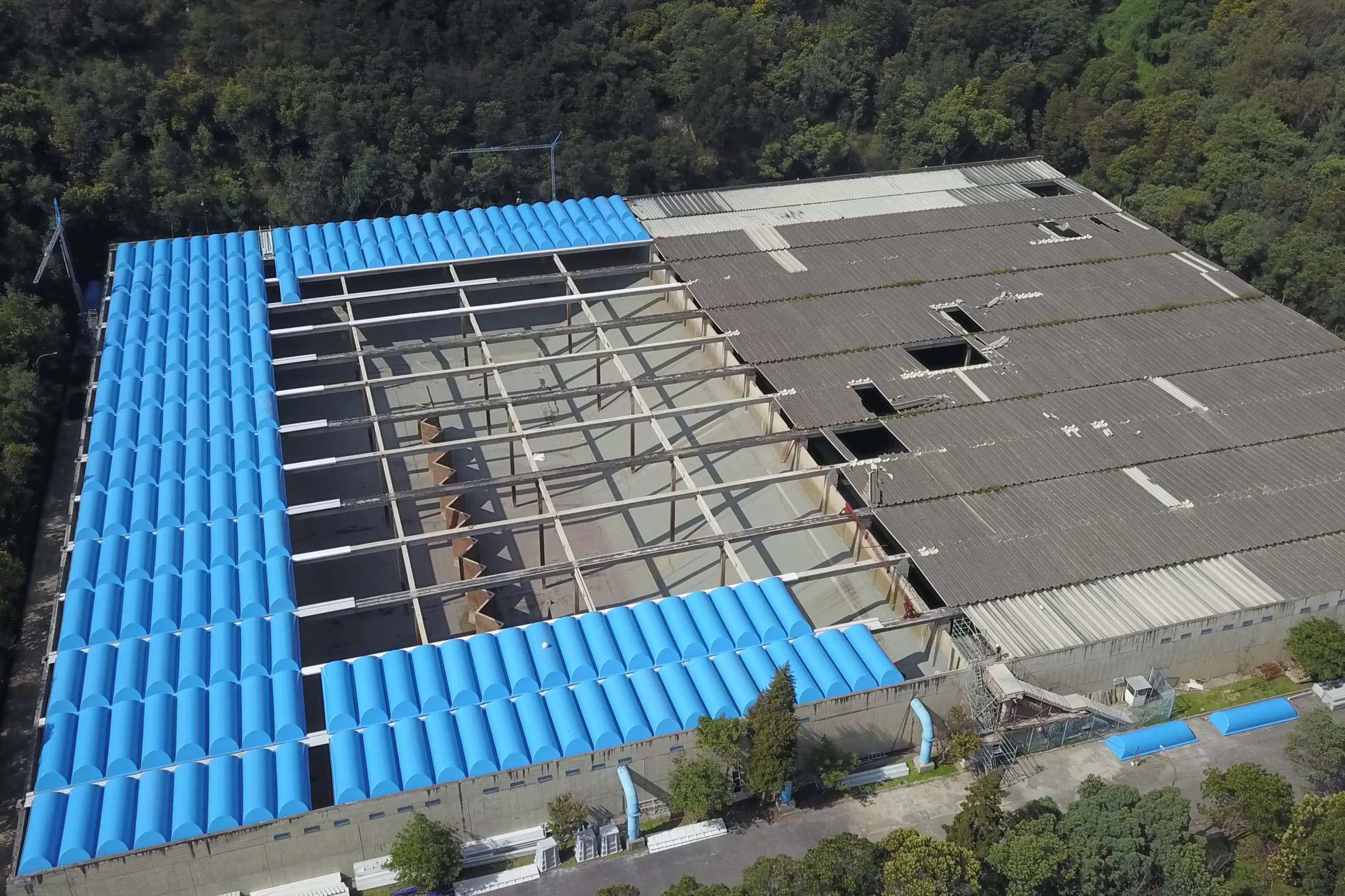
Manter a Casablanca de 66 anos não é uma tarefa fácil. Em 2009, foi descoberto que rachaduras no piso de concreto do tanque estavam permitindo que 360.000 litros (95.000 galões) de água escapassem a cada hora . Reparos no concreto com revestimento de poliureia reduziram o vazamento a zero. Casablanca, porém, ainda tinha um problema acima do concreto. A água do tanque era protegida por uma série de tampas que consistiam em uma mistura de concreto e amianto, o que representava uma ameaça significativa à qualidade da água e à saúde humana. As capas antigas também estavam sujeitas a falhas e eram caras de manter. A EAAB precisava substituir as tampas antigas por uma alternativa mais segura, mais leve e mais durável.
Capas grandes, e muitas delas
A EAAB decidiu buscar uma solução de compósitos para as tampas, mas foi imediatamente desafiada pela escala do projeto. Casablanca é atravessada por uma série de pilares de concreto que sustentam uma rede de vigas sobre as quais repousam as coberturas. Essas vigas são espaçadas cerca de 7,2 metros (23,6 pés) uma da outra, portanto, as novas tampas teriam que ser autossustentáveis e cobrir esse vão para fazer uso da infraestrutura existente. A EAAB propôs que tais coberturas fossem fabricadas por moldagem por transferência de resina leve (LRTM). O desafio? Estruturas compostas deste tamanho necessárias para esta aplicação nunca foram fabricadas via LRTM na Colômbia. Muitos fabricantes simplesmente não conseguiram assumir o projeto.
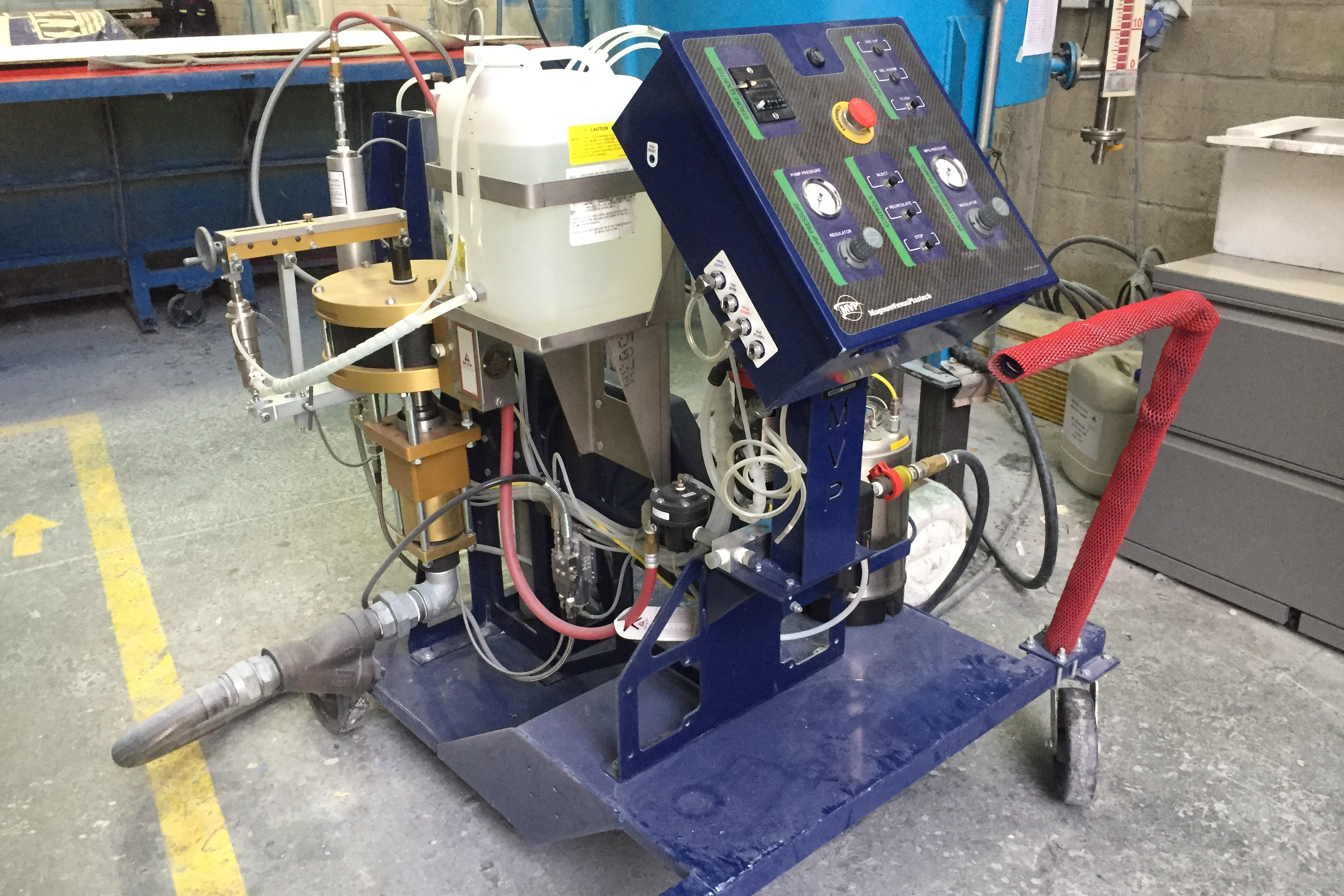
A exceção foi a Innovative Engineering Solutions, ou Soling, uma fabricante de compósitos localizada em La Estrella, Antioquia, Colômbia, ao sul de Medellín. Soling foi fundada em 2014 por Javiar Moreno, que possui e opera várias empresas de manufatura de compósitos na Colômbia e arredores. Rodrigo Vergara, coordenador de engenharia da Soling, diz que o tamanho das tampas foi um obstáculo para muitos fabricantes. “Ninguém tinha experiência com isso na Colômbia por causa do tamanho da peça”, observa. “É a maior peça composta fabricada na Colômbia.” Para Moreno, porém, o tamanho das capas era um desafio interessante. “Para o nosso dono [Moreno]”, diz Vergara, “foi um sonho que se tornou realidade. ‘Impossível’ é uma palavra que ele não entende. Ele disse:‘Faremos isso!’ Eu disse ‘OK!’ ”
Soling propôs uma solução específica para o projeto de Casablanca:uma série de 840 estruturas compostas retangulares em forma de cúpula, cada uma medindo 7,6 metros de comprimento e 2,4 metros de largura (24,9 x 7,9 pés). O desenho da cúpula semicircular foi escolhido, diz Vergara, porque “a forma geométrica que apresenta maior resistência mecânica é a circunferência. Esse foi o principal fator para garantir que as coberturas fossem autossustentáveis. Por outro lado, tivemos que encontrar a maneira mais fácil de despachá-los do local de fabricação até o ponto de instalação, que ficava a 260 milhas de distância. ”
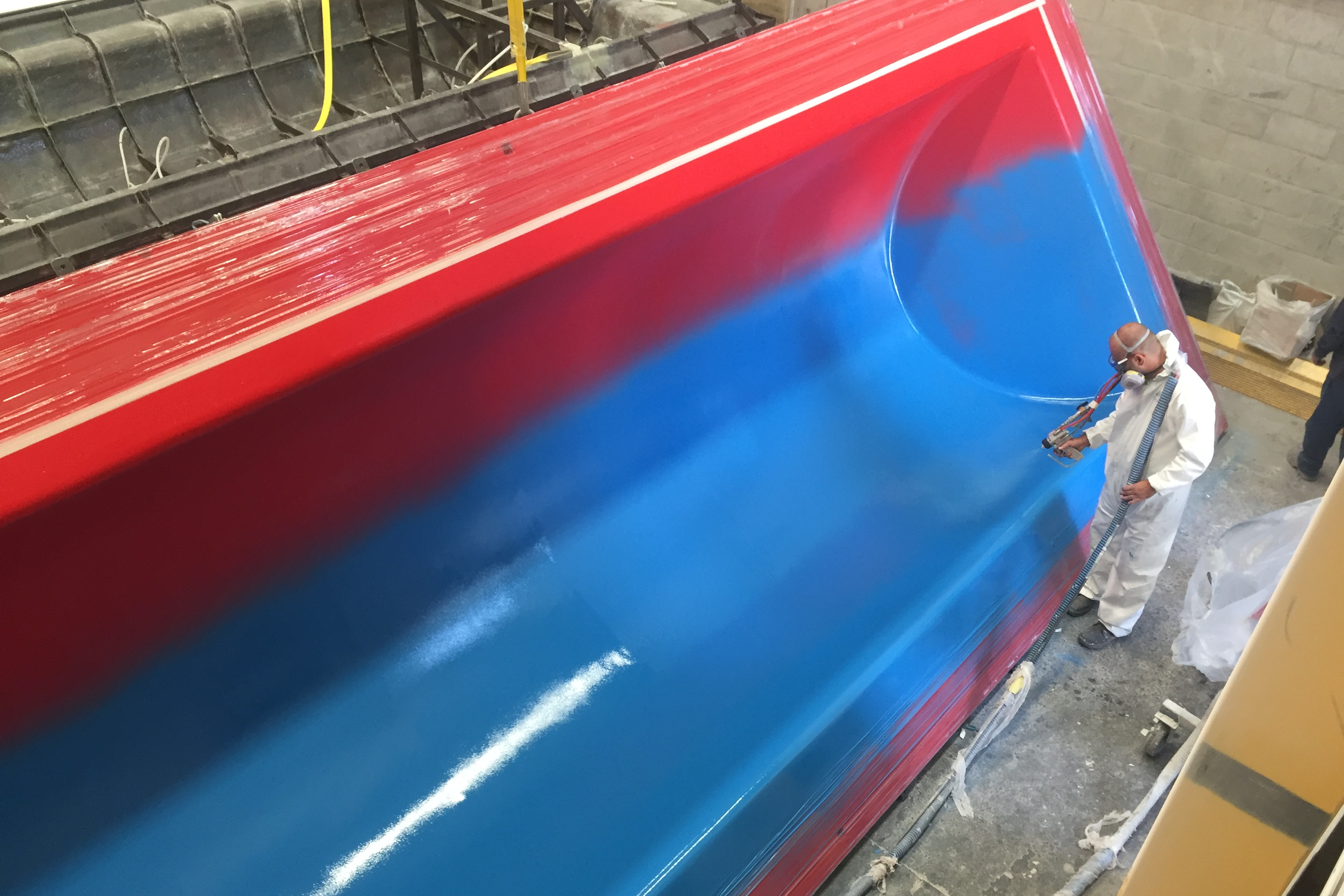
As coberturas seriam fabricadas via LRTM com, de acordo com as especificações da EAAB, um gel coat azul na superfície externa e um gel coat branco na superfície interna. Composta por tecidos de fibra de vidro e uma resina de poliéster, a capa, com uma área de superfície de 28,5 metros quadrados (207 pés quadrados), pesaria 320 quilos (705 libras), dos quais 208 quilos seriam de resina. Com o design em mãos e o compromisso de entregar as capas, Vergara e Soling puseram-se a trabalhar.
Construindo a cobertura perfeita
É claro que Soling não assumiu o projeto de Casablanca sem ajuda. Trabalhando com a empresa havia uma rede de abastecimento que incluía um distribuidor, um fornecedor de materiais e um fornecedor de equipamentos. O distribuidor Minepro SAS (Medellín, Colômbia) forneceu suporte técnico e trabalhou com o fornecedor de equipamentos Magnum Venus Products (MVP, Knoxville, Tenn., EUA), que forneceu bombas e equipamentos auxiliares para o processo LRTM. Os fornecedores de materiais são Andercol (Medellín), que forneceu a matriz de resina de poliéster, gel coats e suporte técnico, e Jushi (Tongxiang City, China), que forneceu os tecidos de fibra de vidro E.
A fabricação, naturalmente, começa com ferramentas. A questão era quantos moldes o projeto exigia. Para determinar isso, Vergara diz que Soling primeiro teve que estabelecer o ritmo de fabricação para atender aos requisitos de entrega da EAAB. Este, por sua vez, foi afetado pelas necessidades do local de trabalho. Para evitar contaminar potencialmente o abastecimento de água durante a instalação das novas tampas, a EAAB concordou em esvaziar a metade de Casablanca sobre a qual as tampas estavam sendo entregues e baixadas no local. Reduzir a capacidade de armazenamento de água de Casablanca pela metade apresenta desafios, portanto, a EAAB precisava que a entrega e a instalação acontecessem o mais rápido possível.
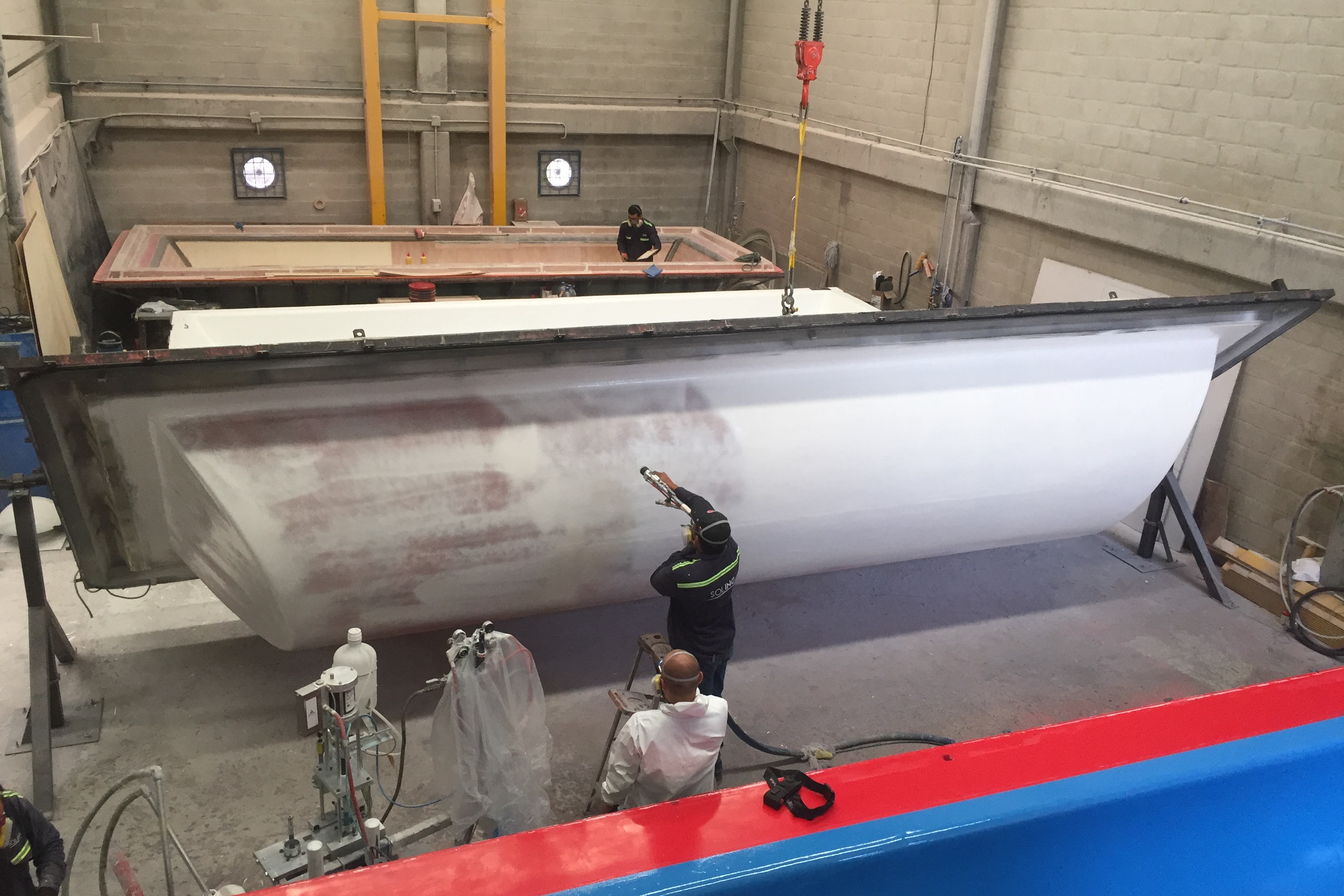
Soling, trabalhando com a EAAB, explica Vergara, estabeleceu uma programação de produção que entregaria seis capas por dia. Em uma instalação com três turnos de oito horas por dia, eram necessários dois moldes, cada um capaz de fabricar uma capa por turno. Os moldes, diz ele, foram construídos internamente e compostos por um design macho / fêmea composto de fibra de vidro apoiado por uma estrutura de suporte de aço.
Com os moldes construídos, Soling iniciou então o trabalho de estabelecer como, especificamente, as cúpulas seriam fabricadas. Trabalhando com Minepro e MVP, Vergara diz que foi decidido que cada molde seria alimentado por duas portas de injeção de resina, com uma porta de vácuo. Para injeção de resina, o MVP recomendou o uso de sua unidade de bomba de moldagem por transferência de resina de alto volume (RTM) Patriot Innovator, que é capaz de fornecer o grande volume de resina exigido por cada tampa. A MVP também forneceu suas válvulas Turbo Autosprue, bem como acopladores universais, vedações e acessórios para moldes.
Para iniciar a produção de uma capa, diz Vergara, a metade feminina do molde foi borrifada com gel coat branco e a metade masculina do molde com gel coat azul. Conforme observado, ambos os gel coats foram fornecidos pela Andercol. Em seguida, os tapetes e tecidos de vidro E fornecidos pela Jushi foram colocados à mão na metade feminina do molde. Em seguida, baixou-se, por meio de uma grua, a metade macho do molde para a metade fêmea, com as duas metades presas uma à outra. Depois que o vácuo foi puxado, a injeção de resina começou. Vergara diz que a injeção de cada cobertura foi concluída em cerca de 40 minutos, seguida de cura à temperatura ambiente. Depois que cada tampa foi desmoldada, ela foi aparada para as dimensões finais e canais de alimentação para mitigação da água da chuva foram cortados na superfície do flange da tampa.
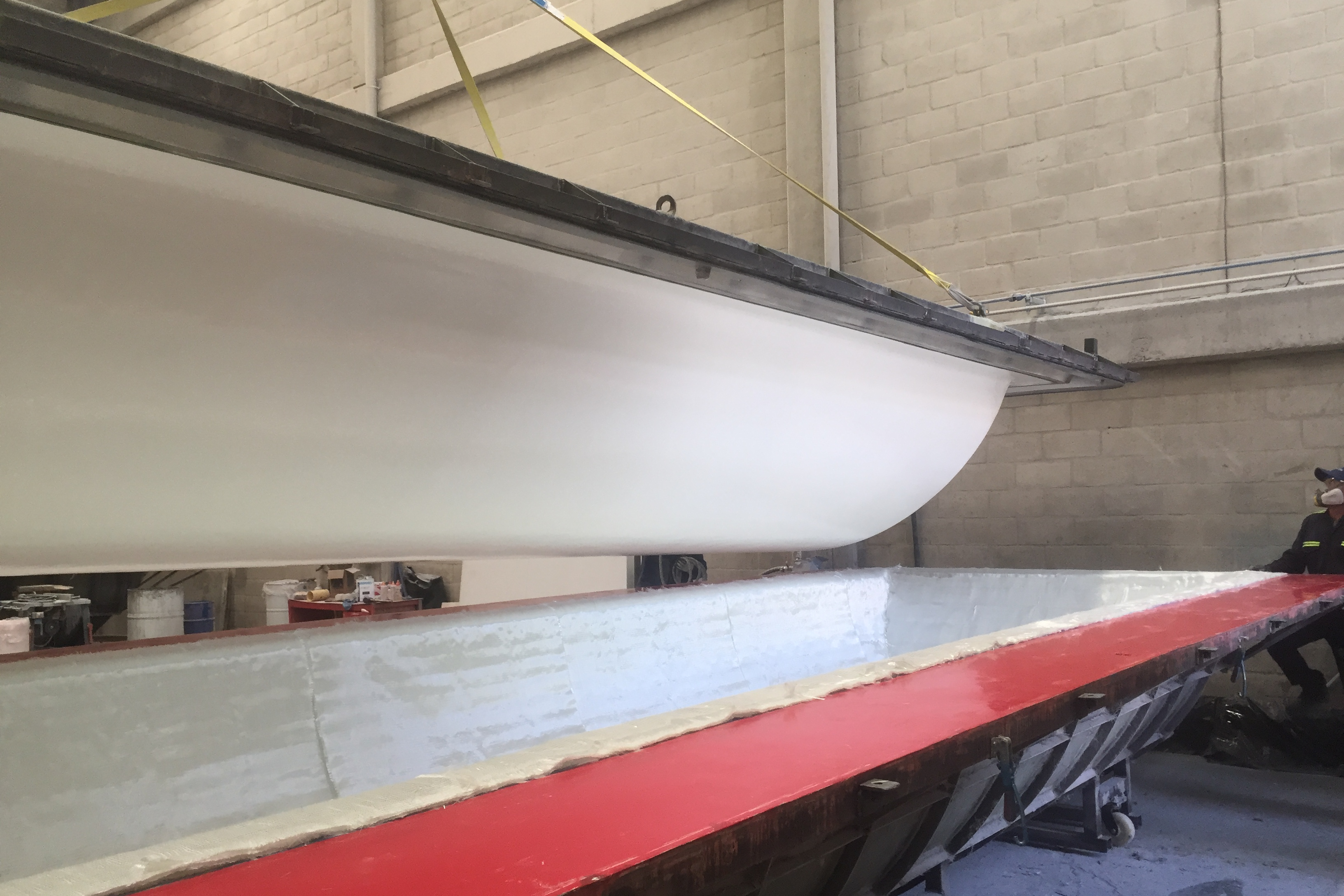
Vergara diz que o tamanho das tampas, combinado com os requisitos rígidos de peso e dimensão, representam o maior desafio para sua fabricação. Determinar a localização da porta de injeção e gerenciar o tempo de injeção exigiu muitas tentativas e erros e consultas com especialistas técnicos. Eventualmente, no entanto, Vergara diz que Soling decidiu por um processo de fabricação que se mostrou altamente repetível e confiável.
“O maior desafio era o peso dos elementos que íamos instalar, pois não podíamos ultrapassar a capacidade de carga da estrutura existente”, diz Vergara. “Isso exigia que todas as peças tivessem as mesmas características, tanto em geometria quanto em peso. A única maneira de garantir essas condições era usar um processo que garantisse a repetibilidade. ”
Tampas concluídas foram enviadas por 418 quilômetros (260 milhas) da instalação de Soling perto de Medellín para o local de trabalho de Casablanca em Bogotá e, em seguida, instaladas por meio de guindaste, baixadas sobre a estrutura de suporte e posicionadas pelos trabalhadores de pé nas vigas sobre as quais as tampas repousariam. Embora as tampas não sejam fixadas mecanicamente às estruturas de suporte, Vergara afirma que também não foram projetadas para serem movidas ou removidas, a menos que “algo muito sério acontecesse”.
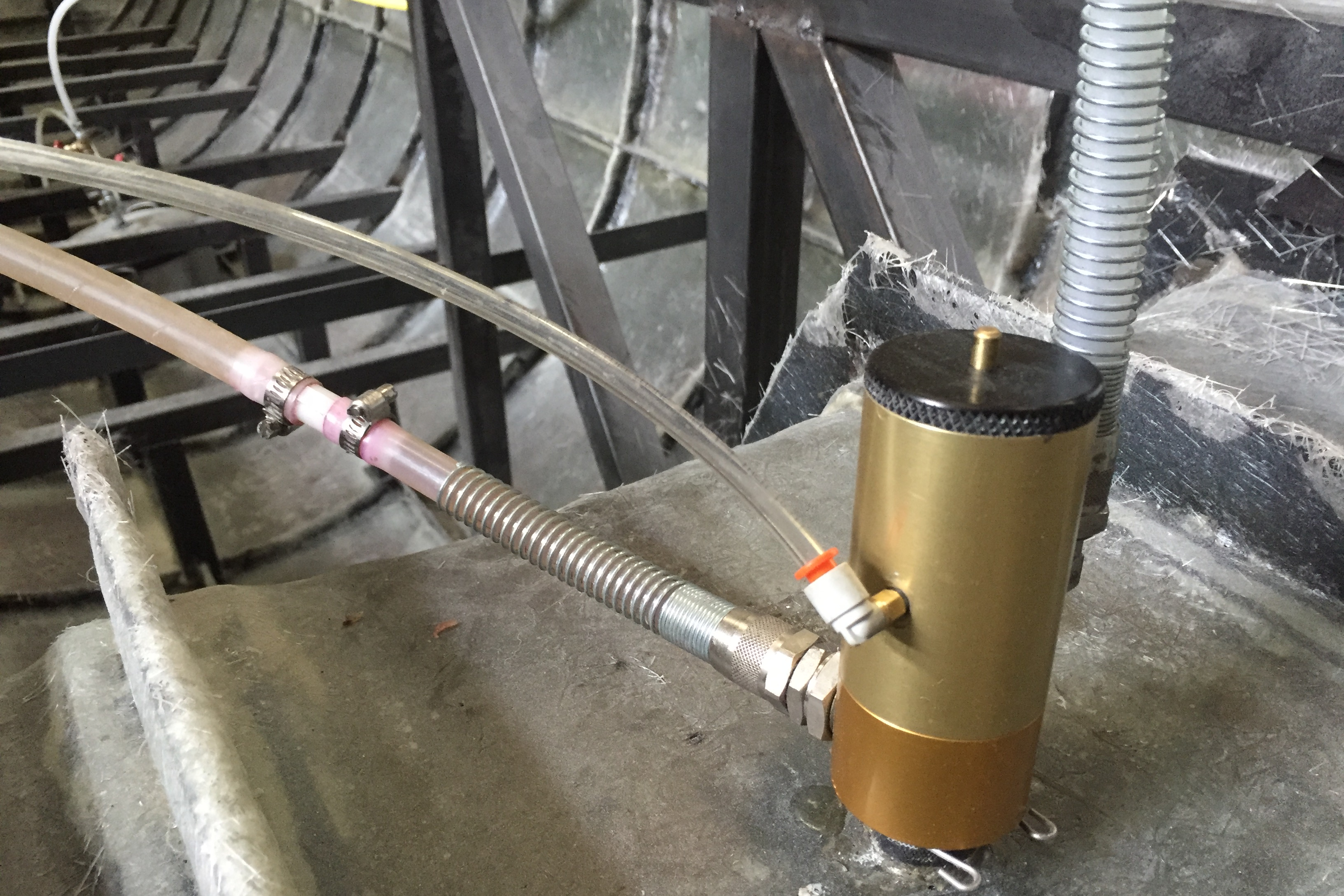
Soling começou o trabalho de design das tampas no início de 2019 e começou a fabricação das primeiras tampas em 2020. A pandemia de coronavírus e ocasionais desafios mecânicos fizeram a fabricação parar e começar, mas Vergara diz que Soling concluiu a produção de todas as 840 tampas em um período de 7 a 8 meses, terminando no final de 2020. Espera-se que as novas tampas durem substancialmente mais e exijam muito menos manutenção do que as substituídas.
O projeto de Casablanca, diz Vergara, demonstrou as capacidades da Soling como fabricante de grandes estruturas compostas de alta qualidade e alto desempenho e abriu portas para outras oportunidades. “Esse projeto foi um desafio em que tivemos que quebrar paradigmas que diziam que peças dessa magnitude não poderiam ser feitas com esse método de manufatura, e ainda assim fizemos”, afirma. “Para o futuro da Soling, algo está muito claro:não há projeto que não sejamos capazes de realizar.”
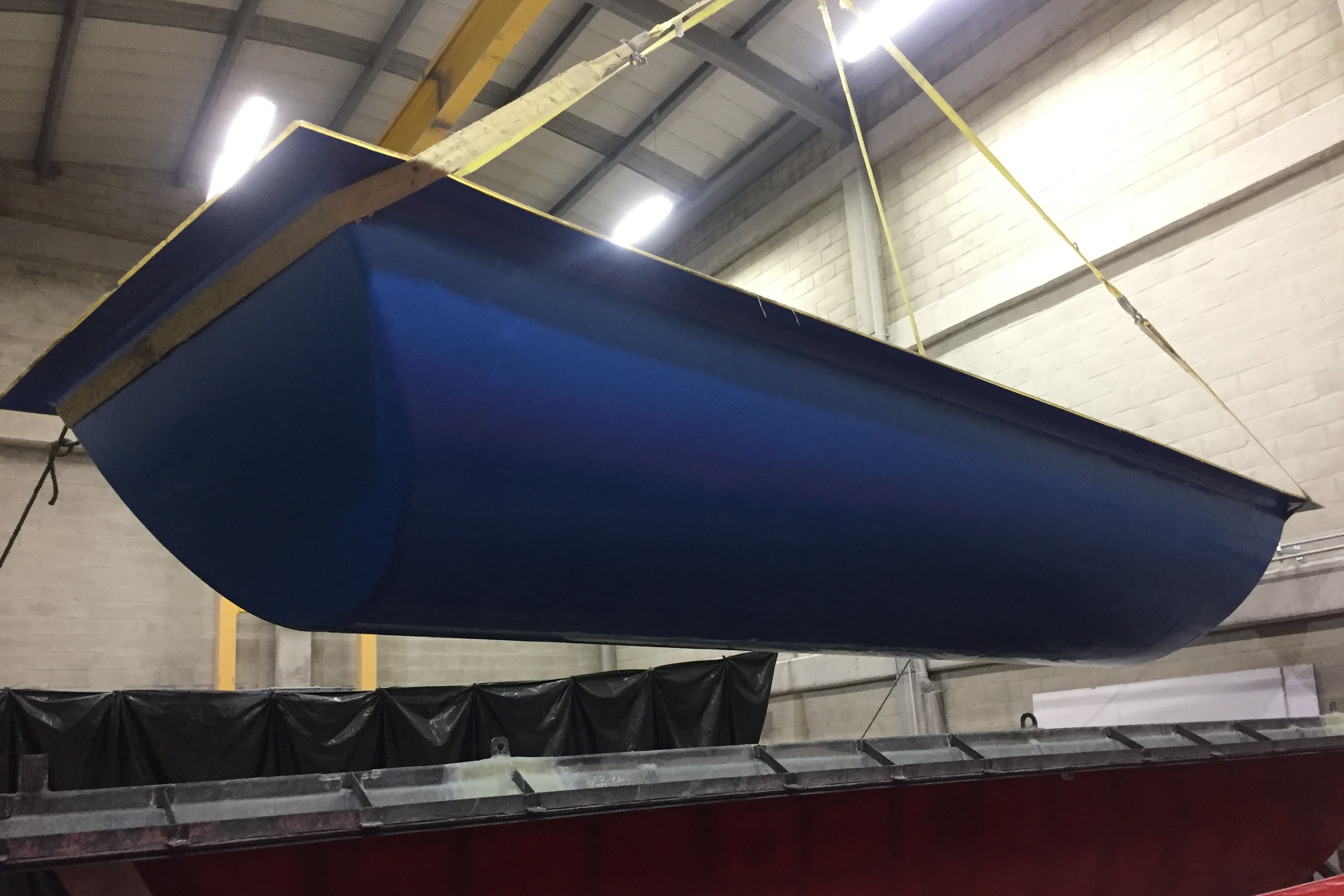
Resina