Destaques:Convenção de Compósitos 2019
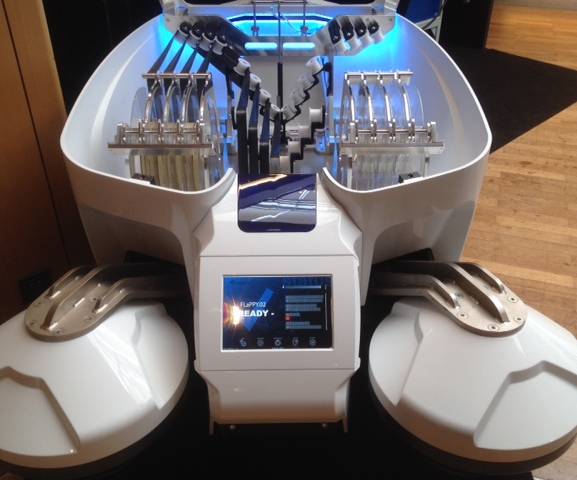
O protótipo do DLR intrigantemente chamado Flappybot (robô autônomo flexível de produção, colocação e montagem) é uma partida radical das grandes e caras máquinas estáticas comuns na fabricação de grandes componentes aeroespaciais. Esta unidade AFP autônoma compacta é projetada para "conduzir" diretamente sobre o molde. Fonte | DLR
Para que a indústria de compósitos continue a crescer e melhorar sua competitividade, ela deve explorar as oportunidades que a digitalização e a automação trazem. Duas conferências recentes com foco no setor aeroespacial na Alemanha analisaram o que o futuro da fabricação de compósitos pode trazer.
Visitando a fábrica do futuro no Stade
A Future Factory for Composites foi o tema da Convenção de Compósitos deste ano em Stade, Alemanha, realizada de 12 a 13 de junho. Organizado em conjunto por CFK Valley e.V. (Stade, Alemanha) e Carbon Composites e.V. (Augsburg, Alemanha), o evento atraiu um público recorde de cerca de 450 pessoas. Uma forte presença nos EUA resultou de uma colaboração com a Iniciativa de Fabricação e Materiais Avançados de Utah (UAMMI, Kaysville, Utah, EUA) como rede de parceiros e os Estados Unidos como país parceiro.
Na apresentação de abertura, intitulada “Digitalização:Transição da Manufatura Auxiliada por Computador para a Automação Humana,” Dr. Jan Stüve, chefe do Centro de Tecnologia de Produção Leve do Centro Aeroespacial Alemão (Deutsches Zentrum für Luft- und Raumfahrt; DLR; Stade, Alemanha) ofereceu uma amostra do programa que viria. As futuras tecnologias de fábrica em desenvolvimento na DLR incluem vários robôs cooperativos que trabalham juntos para reduzir o tempo de produção e gêmeos digitais de máquinas que permitem a otimização do processo. Outra área importante diz respeito a robôs autônomos móveis para cenários de produção flexíveis. Isso inclui o protótipo FlappyBot, um compacto unidade de colocação de fibra que percorre o molde. Stüve alertou sobre os perigos potenciais do excesso de automação e discutiu como a digitalização deveria reinventar os humanos no processo de fabricação.
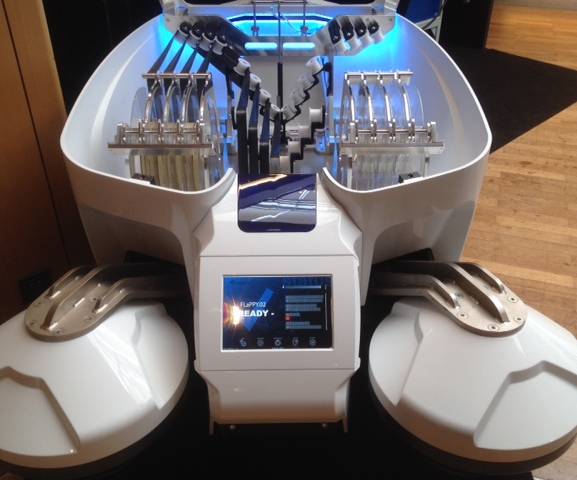
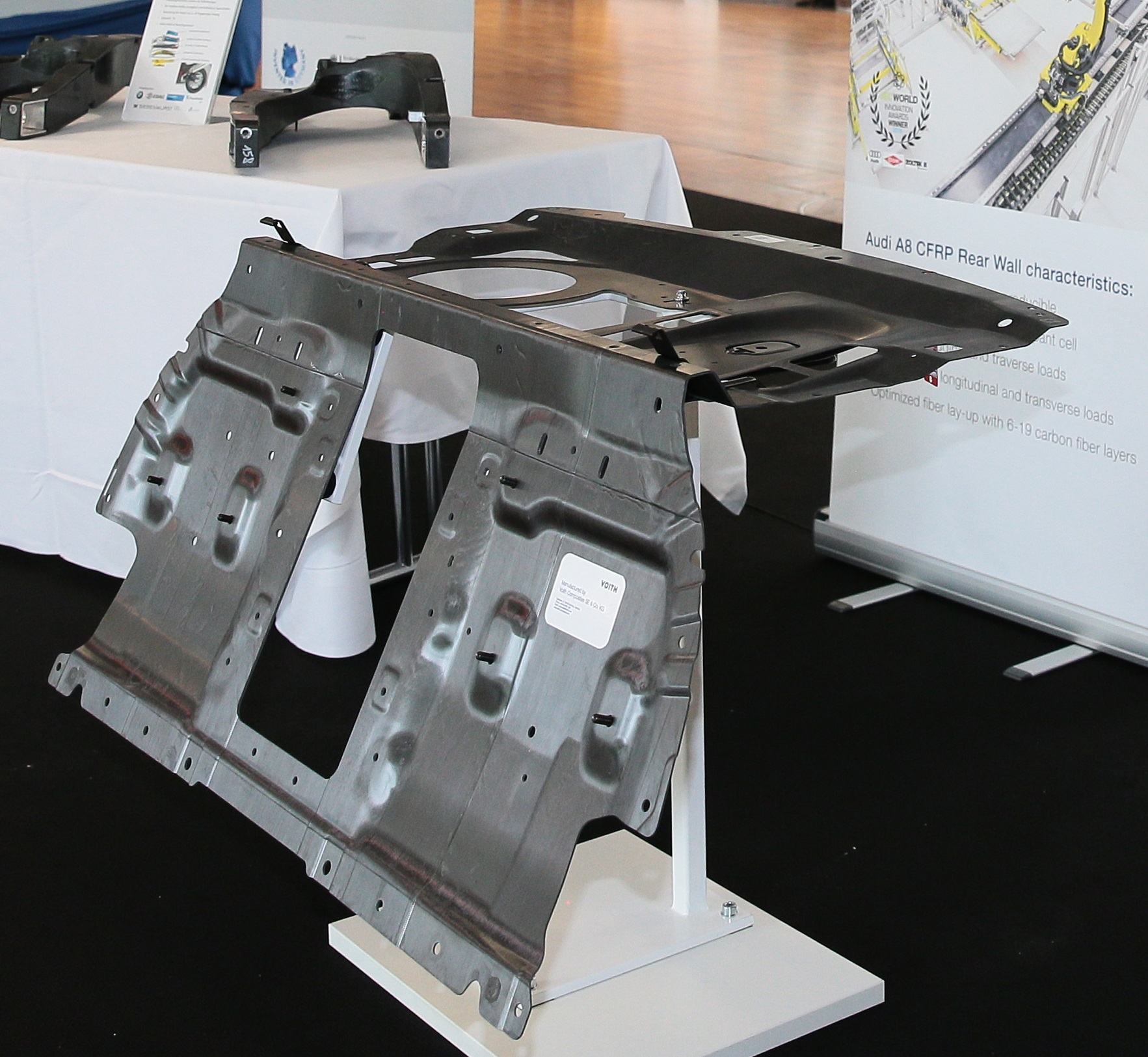
A parede traseira do Audi A8 CFRP, o maior componente da célula de passageiros, é fabricada pela Voith Composites em um processo altamente automatizado que permite volumes de produção de 65.000 componentes por ano. Fonte | Vale CFK
Em uma segunda palestra, "Manufatura Rápida e Compósitos Termoplásticos - Tendências e Tecnologias", o Dr. Robert G. Bryant, engenheiro de materiais sênior do Centro de Pesquisa Langley da NASA (Hampton, Virgínia, EUA), tirou os delegados dos confins do fábrica terrestre rumo à construção no espaço. Uma presença humana de longo prazo no espaço exigirá abrigo e plataformas como um primeiro passo. O desenvolvimento de foguetes cada vez maiores para colocar estruturas cada vez mais complexas fora do planeta não é economicamente sustentável. As soluções requerem fabricação próxima ou no local. O uso de um processo de colocação de fita avançada sem ferramentas (ATP), permitindo a consolidação in-situ de peças compostas termoplásticas pode ser a resposta. Nessa nova técnica, dois robôs ATP trabalham frente a frente, um para depositar a fita termoplástica pré-impregnada e o outro atuando como ferramenta. A fabricação sem ferramentas pode reduzir o custo da fabricação aeroespacial, melhorando a economia da exploração espacial, bem como beneficiando outros setores do mercado (saiba mais em “Processo de desenvolvimento de compósitos termoplásticos sem ferramentas em geral Atômica Aeronáutica”).
Sustentabilidade
Os avanços na fabricação também devem ser acompanhados por reduções no impacto ambiental. Nesse sentido, na próxima sessão, Jörg Spitzner, fundador da Spitzner Engineers GmbH (Finkenwerder, Alemanha), argumentou que, para cumprir as metas climáticas, são necessárias tecnologias de emissões negativas. A empresa de Spitzner afirma que seu conceito de turbina eólica Blancair patenteada melhora a eficiência da turbina e remove CO 2 da atmosfera. O ar é puxado para um módulo de filtro montado na nacela, onde CO 2 é separado para armazenamento e reciclagem na produção de combustíveis sintéticos e outras aplicações. O ar limpo é liberado através de aberturas nas pontas das pás do rotor. Um vídeo explicando o conceito está disponível no site da Blancair.
Os organizadores da sessão também apresentaram um conceito para avaliação inteligente de ecoeficiência na produção de compósitos (DLR) e em temperatura ambiente fora da autoclave, pré-impregnados temperados com capacidade de fogo, fumaça e toxicidade (FST) (Compostos TCR; Ogden, Utah, NÓS).
Capacitação por meio de simulação
No restante do primeiro dia da conferência, a atenção se voltou para a simulação.
O Dr. Lars Herbeck, diretor de tecnologia da Voith Composites (Garching, Alemanha), discutiu como a máquina de colocação automatizada de fibras (AFP) Voith Roving Applicator simplifica a cadeia de processo, permitindo um processo de pré-formação automatizado eficiente com tempos de ciclo reduzidos. Ele descreveu a simulação estrutural e de processo realizada para a linha de manufatura automatizada, capaz de produzir 65.000 componentes por ano para a parede traseira de plástico reforçado com fibra de carbono (CFRP) do Audi A8.
Mark Bludszuweit da MET Motoren- und Energietechnik GmbH (Rostock, Alemanha) explicou como a simulação oferece uma visão sobre a melhor maneira de carregar peças em uma autoclave, permitindo a otimização do processo de cura e maior produtividade. Um gêmeo digital desenvolvido para a maior autoclave na instalação Stade do DLR pode ser executado em paralelo com o processo real, ou mais rápido para oferecer previsões do comportamento da peça.
Outros tópicos de desenvolvimento de processo virtual cobriram a modelagem de processos SMC (ESI Group; Chartres-de-Bretagne, França) e simulação de processo de painéis sanduíche para entender o esmagamento do núcleo e problemas de enrugamento pré-impregnado na autoclave (Airbus Helicopters; Marignane, França).
Voltando-se para a modelagem de segurança virtual, Jochen Rühl da Reichenbacher Hamuel GmbH (Dörfles-Esbach, Alemanha), parte do Scherdel Gruppe, discutiu como uma abordagem baseada em simulação para gerenciar poeira e partículas produzidas durante a usinagem de peças CFRP trouxe benefícios para clientes como como Airbus e Premium Aerotec (Augsburg, Alemanha). Simulações de usinagem e visualização de distribuições de partículas ajudam os fabricantes a cumprir a legislação de saúde e segurança de aperto e melhorar os resultados da usinagem, bem como reduzir o tempo de inatividade e manutenção da máquina, tudo o que acaba se traduzindo em um menor custo por peça.
A sessão de simulação também apresentou um projeto patrocinado pela Boeing sobre modelagem virtual de custos de fabricação de compósitos, levando em consideração as complexas interações entre design, produção e finanças para identificar direcionadores de custos (Massachusetts Institute of Technology; Cambridge, Massachusetts, EUA), e um conceito de planejamento de fábrica digital baseado em modelagem simulada de cadeias de valor de compostos ideais (Fraunhofer IGCV; Augsburg, Alemanha).
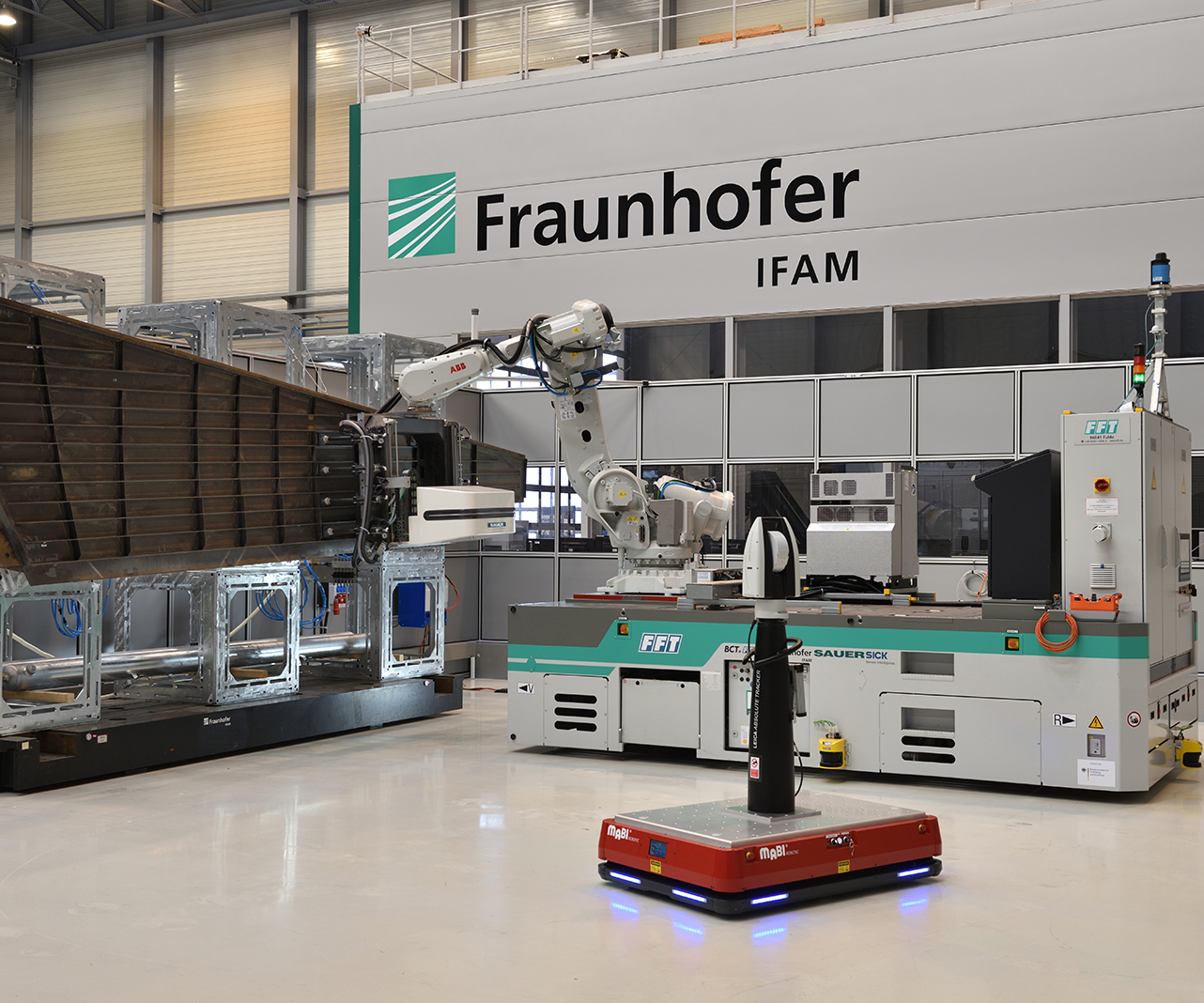
O conceito de usinagem móvel MBFast18 é composto por um veículo guiado por automação, robô e máquina CNC portátil e oferece maior produtividade na fabricação de peças grandes de CFRP para aeronaves. Fonte | Fraunhofer IFAM
Vencedores do prêmio
Este ano, dois projetos compartilharam o CFK Valley Innovation Award e o prêmio em dinheiro de € 7.500.
O primeiro lugar (e € 4.500) foi para o projeto de sistemas robóticos móveis MBFast18, que desenvolveu um sistema de usinagem CNC móvel baseado em veículo guiado automatizado (AGV) para grandes peças de aeronaves CFRP.
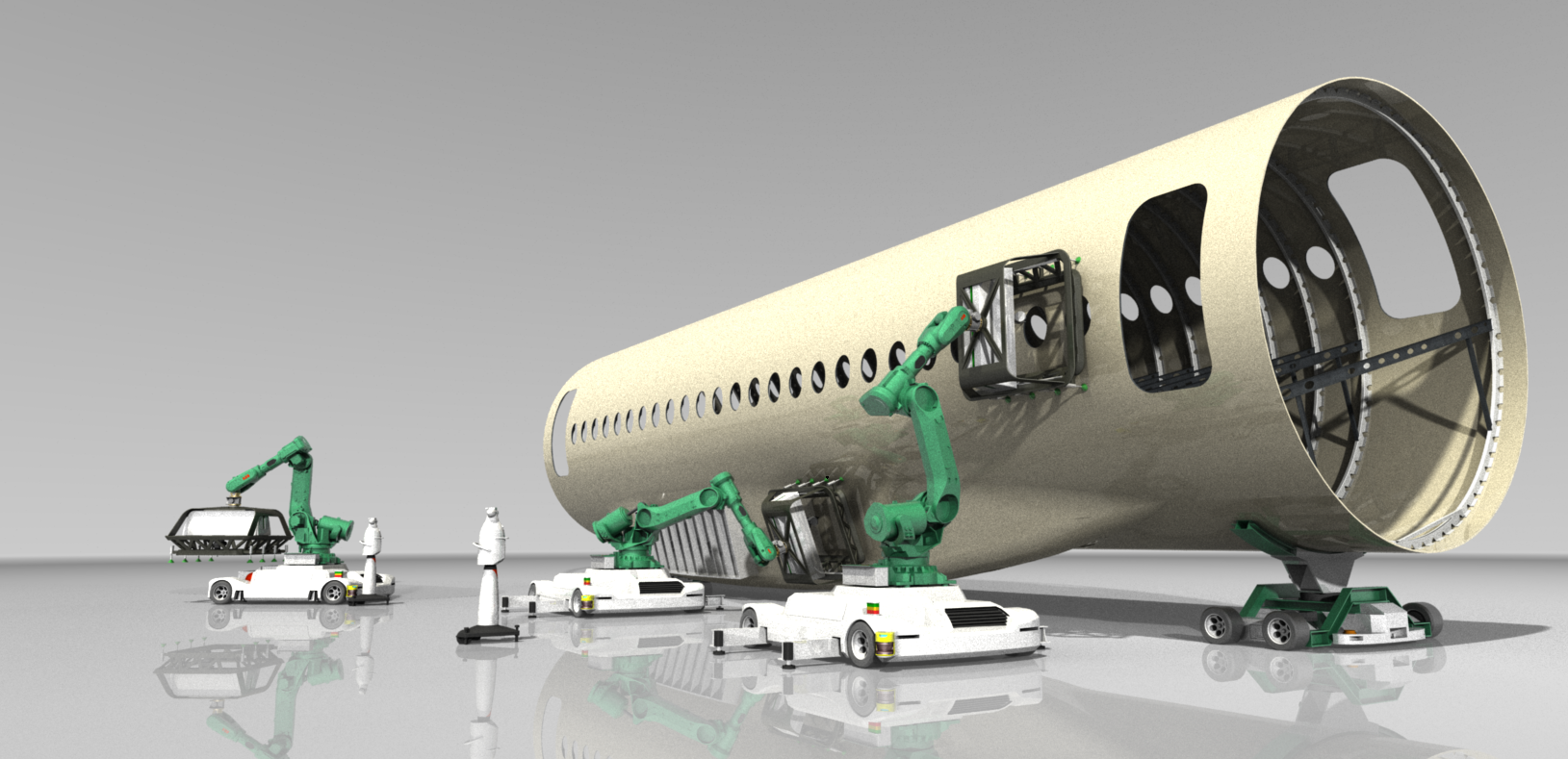
Fonte | Fraunhofer IFAM
Em comparação com os caros sistemas de usinagem estáticos de hoje para grandes estruturas de aeronaves, os sistemas robóticos móveis menores permitem uma manufatura flexível e maior produtividade.
O sistema MBFast18 emprega uma plataforma autônoma de 4,6 metros construída pela FFT Produktionssysteme GmbH &Co. KG (Fulda, Alemanha), sensores de navegação e segurança fornecidos pela SICK AG (Waldkirch, Alemanha) e uma máquina CNC de 5 eixos da SAUER / DMG MORI (Suhl e Bielefeld, Alemanha). Um rastreador a laser móvel desenvolvido pelo Instituto Fraunhofer de Tecnologia de Fabricação e Materiais Avançados (IFAM; Stade, Alemanha) posiciona o robô com precisão. A unidade de furação, com área de trabalho de até 0,5 metros quadrados, é fixada ao componente por meio de garras a vácuo; as posições de perfuração são calculadas e transmitidas para a máquina usando um software desenvolvido pela BCT GmbH (Dortmund, Alemanha). Este conceito também se aplica a operações de manuseio e montagem e outras indústrias, como energia eólica e ferroviária.
Assista a um vídeo sobre o projeto MBFast18:
O segundo lugar foi para a start-up Hyconnect GmbH (Hamburgo, Alemanha) por sua tecnologia de junção de metal compósito FAUSST. A empresa tem como alvo inicial o setor de construção naval, onde a união de compósitos ao metal é a principal barreira para a adoção mais ampla de compósitos. A solução FAUSST emprega um tecido híbrido que consiste em fibras de vidro e metal tricotadas em teia que permite que metais e compostos sejam firmemente unidos mecanicamente. O lado da fibra metálica é unido a um perfil de aço que pode ser soldado às estruturas metálicas, e o outro lado é laminado ao componente composto. A tecnologia patenteada acelera significativamente o projeto e o processo de colagem. Os aplicativos de protótipo inicial estão atualmente em teste.
Assista a uma introdução ao processo de adesão FAUSST:
Ativação por meio de automação
O segundo dia viu o premiado projeto MBFast18 explorado em mais detalhes nas apresentações de Christoph Brillinger, gerente de projetos da Fraunhofer IFAM, e do Dr. Gregor Graßl da FFT, que discutiu os desafios do desenvolvimento de processos inteligentes e sistemas de controle de planta para operações multi-robôs . Jerome Berg, engenheiro da equipe Northrop Grumman Innovation Systems (Clearfield, Utah, EUA), descreveu a fabricação automatizada de longarinas para aeronaves Airbus nas instalações da empresa em Utah usando um processo AFP desenvolvido internamente e Uwe Lang da Evonik Resource Efficiency GmbH (Darmstadt , Alemanha) apresentou a “Sandwich Technology 4.0”, uma tecnologia de manufatura automatizada para altas taxas de produção que emprega o material de núcleo de espuma ROHACELL da empresa. Um processo de pré-formação altamente automatizado para a porta do trem de pouso do nariz de uma aeronave foi demonstrado em uma colaboração com o DLR e o hub de tecnologia da Airbus CTC GmbH (Stade, Alemanha).
Assista a um vídeo do processo de pré-formação:
Fazendo uma jornada para a realidade virtual, Felix Hünecke, chefe de desenvolvimento de negócios da ABSOLUTE Reality GmbH (Hamburgo, Alemanha), mostrou como modelos 3D de edifícios podem ser criados, editados e complementados com imagens, documentos e vídeos para criar ambientes virtuais que podem ser visto de qualquer lugar do mundo. A empresa criou um tour 3D em uma sala de produção DLR em Stade.
Dê um passeio pela sala de produção do DLR:
Felix Schreiber, CEO, ARK Group (Aachen, Alemanha), discutiu o processo e os benefícios de custo de dados de máquina estruturados em uma linha de produção de moldagem por transferência de resina automatizada (RTM), enquanto Sascha Backhaus da CTC GmbH discutiu a automação modular na fabricação de compósitos e o Hybr -iT projeto, que está desenvolvendo equipes onde humanos e robôs trabalham em conjunto com sistemas de assistência baseados em software.
Nenhum evento sobre a futura fábrica poderia negligenciar o tópico de inteligência artificial (IA), e Amir Ben-Assa, CMO de Plataine (Waltham, Massachusetts, EUA) discutiu as oportunidades e desafios da implementação de IA na fabricação de compósitos. Ele apresentou aplicações práticas de IA, de alertas (por exemplo, atrasos na produção ou problemas de qualidade) a recomendações (por exemplo, seleção otimizada de material). Assistentes digitais baseados em IA no Google Glass podem ser outra possibilidade, oferecendo interação do usuário “sem usar as mãos” com IA na área de produção e apresentação de alertas de áudio e vídeo em tempo real.
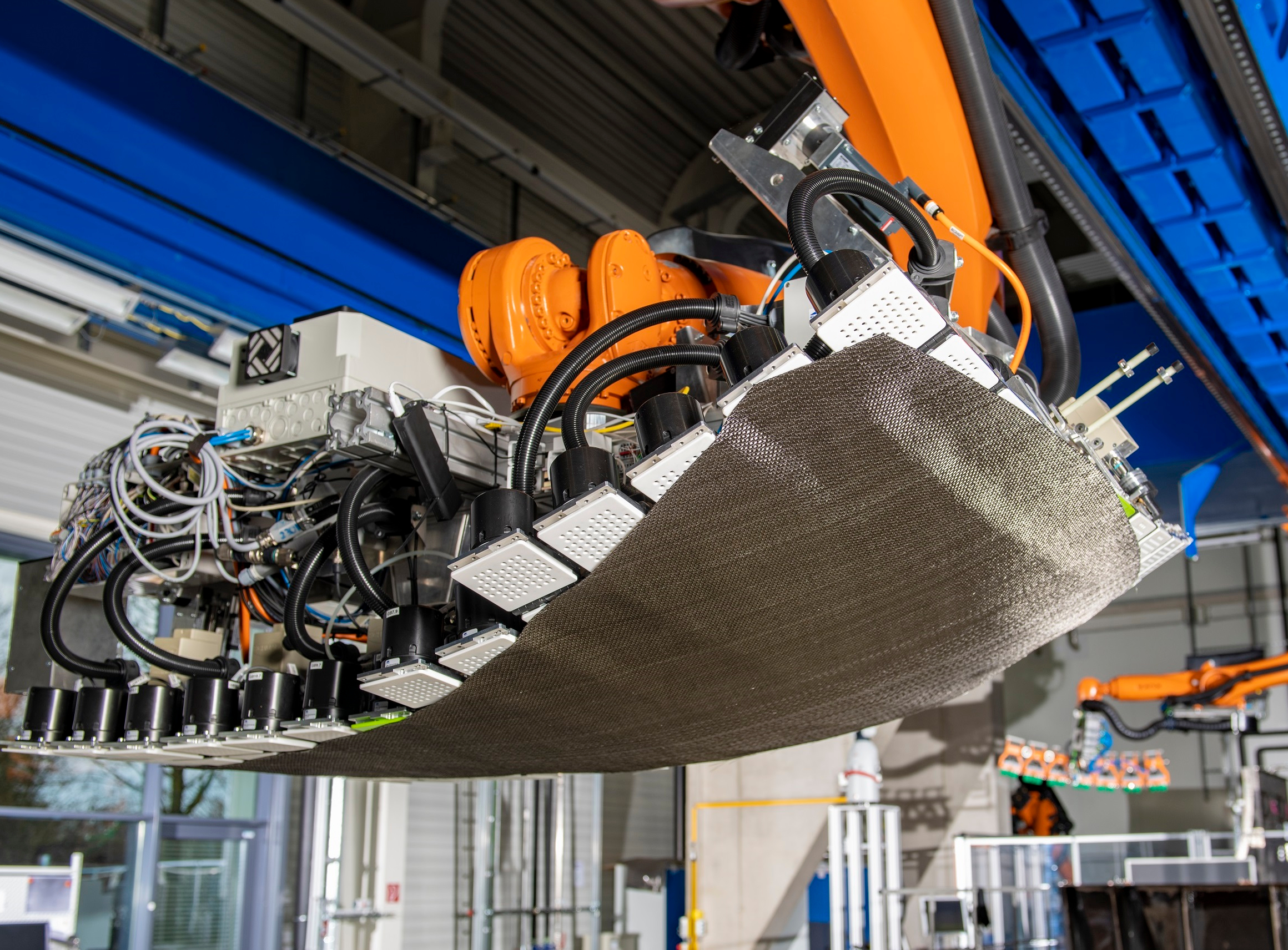
A célula robótica multifuncional da ZLP Augsburg foi projetada para permitir o desenvolvimento de processos integrados para a fabricação de grandes componentes compostos em escala industrial. Fonte | DLR
Outros tópicos incluíram:
- Sensor de fibra óptica para monitoramento inteligente de processos em grandes estruturas compostas (MT Aerospace AG; Augsburg, Alemanha);
- Um sistema de controle inteligente para fabricação automatizada de compósitos (National Composites Center, Bristol, Reino Unido);
- Um sistema de controle de qualidade baseado em modelo para termoformação de pequenos componentes (Faserinstitut Bremen e.V .; FIBER, Bremen, Alemanha);
- Um processo para moldagem por compressão de termoplásticos reforçados com fibra descontínua para aplicações em aeronaves, com base em automação flexível e dimensionável para peças grandes (ACT Aerospace; Gunnison, Utah, EUA);
- Um processo RTM isotérmico que oferece tempos de ciclo reduzidos para produção de peças CFRP de alto volume (Airbus Helicopters)
- Produção em larga escala de perfis termoplásticos complexos de fibra de carbono de alto desempenho para escoras, tubos e eixos de transmissão usando pré-formas de fita em formato quase líquido e conformação por injeção (herone GmbH; Dresden, Alemanha). Saiba mais sobre o herone e este processo em “Moldagem por injeção para estruturas termoplásticas unitizadas de alto desempenho”.
10 anos de progresso em Augsburg
Em um evento separado, o 5º Colóquio sobre Tecnologia de Produção do DLR em 15 de maio teve cerca de 200 convidados reunidos em seu Centro de Tecnologia de Produção Leve (Zentrum für Leichtbauproduktionstechnologie, ZLP) em Augsburg. O evento celebrou o 10º ano da ZLP em Augsburg, onde hoje cerca de 60 funcionários se concentram na automação e digitalização da produção de compósitos.
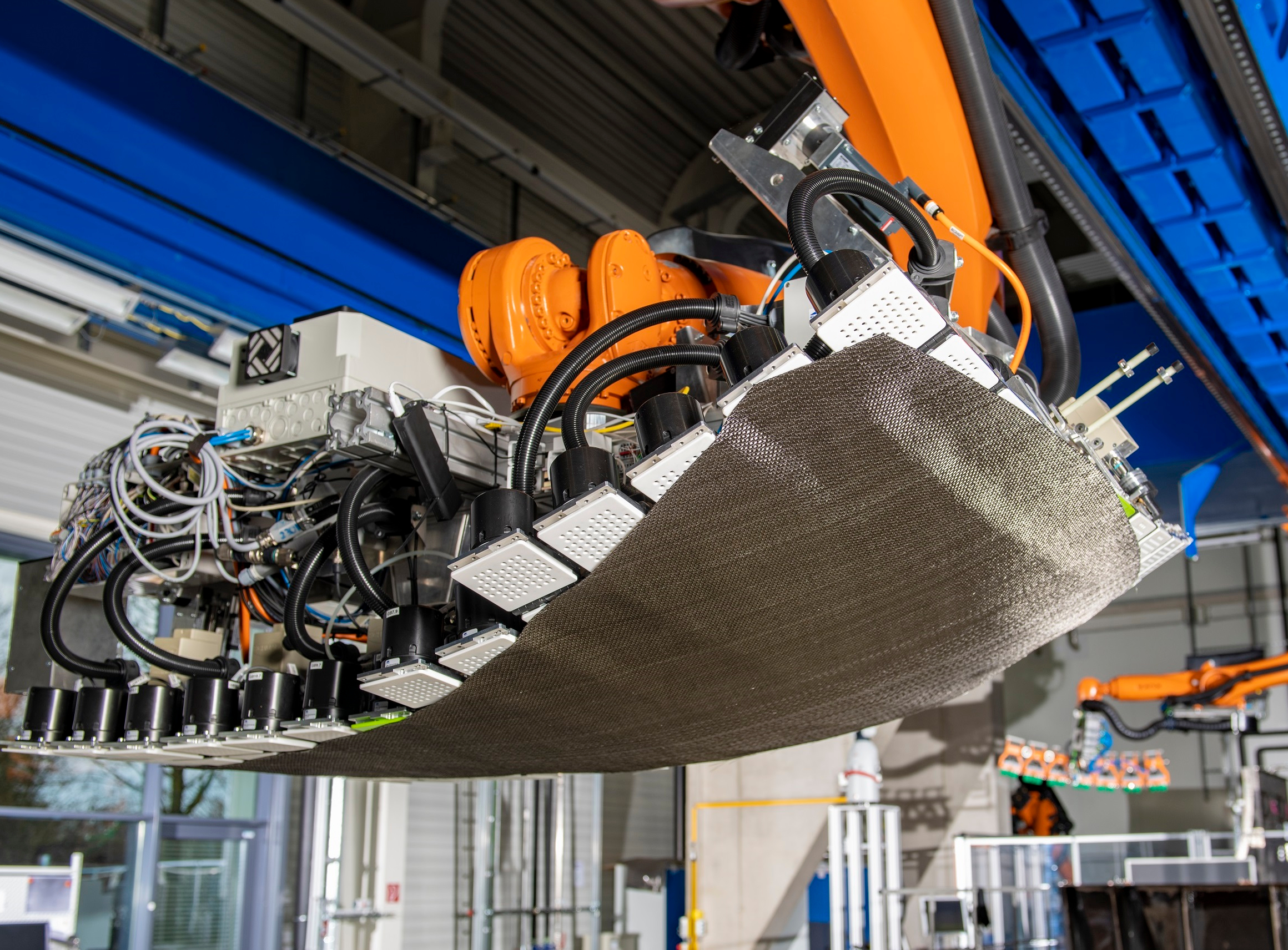
Uma garra robótica para drapeamento automatizado, parte do processo de manufatura integrado da ZLP Augsburg para componentes estruturais em escala real. Fonte | DLR
O dia começou com duas apresentações da University of British Columbia (UBC; Vancouver, Canadá), que iniciou uma cooperação com a DLR em 2016. O Prof. Dr. Anoush Poursartip, codiretor da Digital Learning Factory Initiative da UBC, apresentou o conceito de uma fábrica de aprendizado de compósitos inspirada em hospitais de ensino médico. A fábrica de aprendizagem de compósitos, a ser localizada no campus Okanagan da UBC, será projetada para integrar pesquisa e educação com atividades industriais. Um gêmeo digital hospedado na UBC Vancouver combinará dados da fábrica física com simulação para otimizar os processos de produção de compostos aeroespaciais. Em seguida, o Prof. Dr. Homayoun Najjaran da UBC e Marian Körber da DLR discutiram a otimização de processos de manufatura complexos em um ambiente virtual e como a experiência da UBC em técnicas de aprendizado de máquina e inteligência artificial estão sendo usadas para reduzir o tempo e o custo do desenvolvimento de sistemas robóticos na DLR . Um método de aprendizado profundo foi usado para treinar a garra robótica da ZLP para drapeamento automatizado, uma parte fundamental da cadeia de processo automatizado da instalação de Augsburg para a fabricação de grandes peças de CFRP. A pinça, que possui 127 módulos de sucção com força de sucção variável, reconhece e coleta o material cortado; os módulos assumem a geometria necessária para colocá-lo em posição no molde.
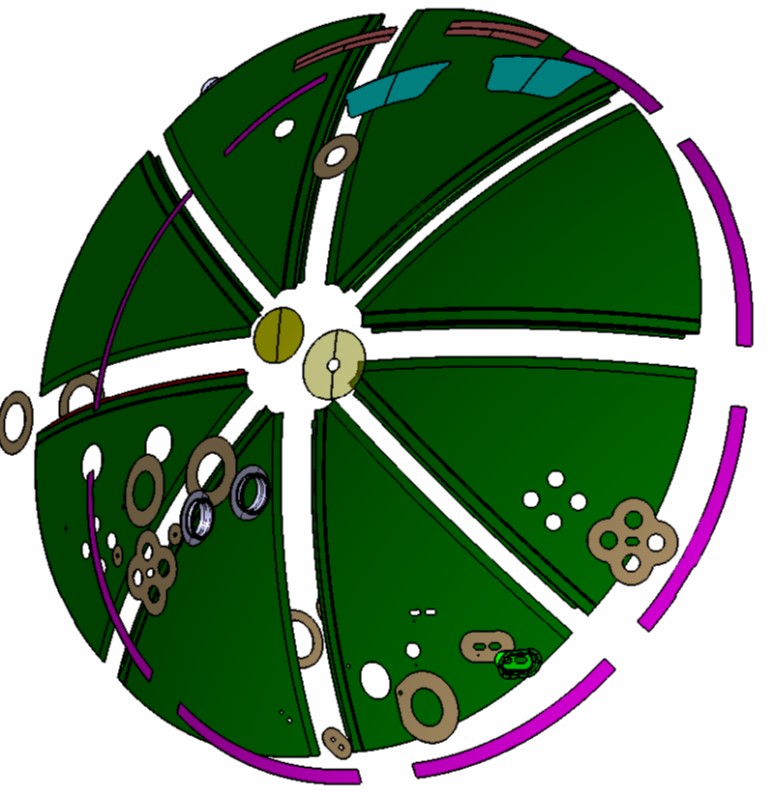
Os componentes do composto termoplástico para o projeto da antepara de pressão traseira do Premium Aerotec são unidos usando uma técnica de soldagem por resistência desenvolvida na ZLP Augsburg. Fonte | Aerotec Premium
As tecnologias de termoplásticos são outro foco da ZLP Augsburg. Um projeto para desenvolver a primeira antepara de pressão traseira termoplástica (RPB) do mundo para aeronaves de corredor único foi delineado por Ralph Männich e Alexander Sänger da Premium Aerotec GmbH. A empresa está colaborando com a ZLP Augsburg, Toray Advanced Composites e o Institute for Composite Materials (IVW) em um projeto que consiste em oito segmentos CFRP com longarinas integradas unidas usando uma tecnologia de soldagem por resistência desenvolvida pela ZLP. Processos automatizados com tempos de ciclo curtos permitem uma produção de alto volume. A conclusão da tecnologia (para TRL 6) está programada para 2020 com a implementação prevista para 2021/2022. No Paris Air Show de junho, a Premium Aerotec exibiu um demonstrador 1:1 para uma aeronave da série Airbus A320. Em comparação com as anteparas de pressão A320 atuais feitas de componentes de alumínio rebitados, a peça termoplástica oferece as mesmas propriedades mecânicas com economia de peso de 10-15% e redução de 50% no tempo de produção. Na palestra a seguir, o Dr. Stefan Jarka e Manuel Endraß da DLR continuaram o tema da soldagem termoplástica, investigando mais profundamente as capacidades de junção e NDT da ZLP Augsburg e seu papel no projeto RPB.
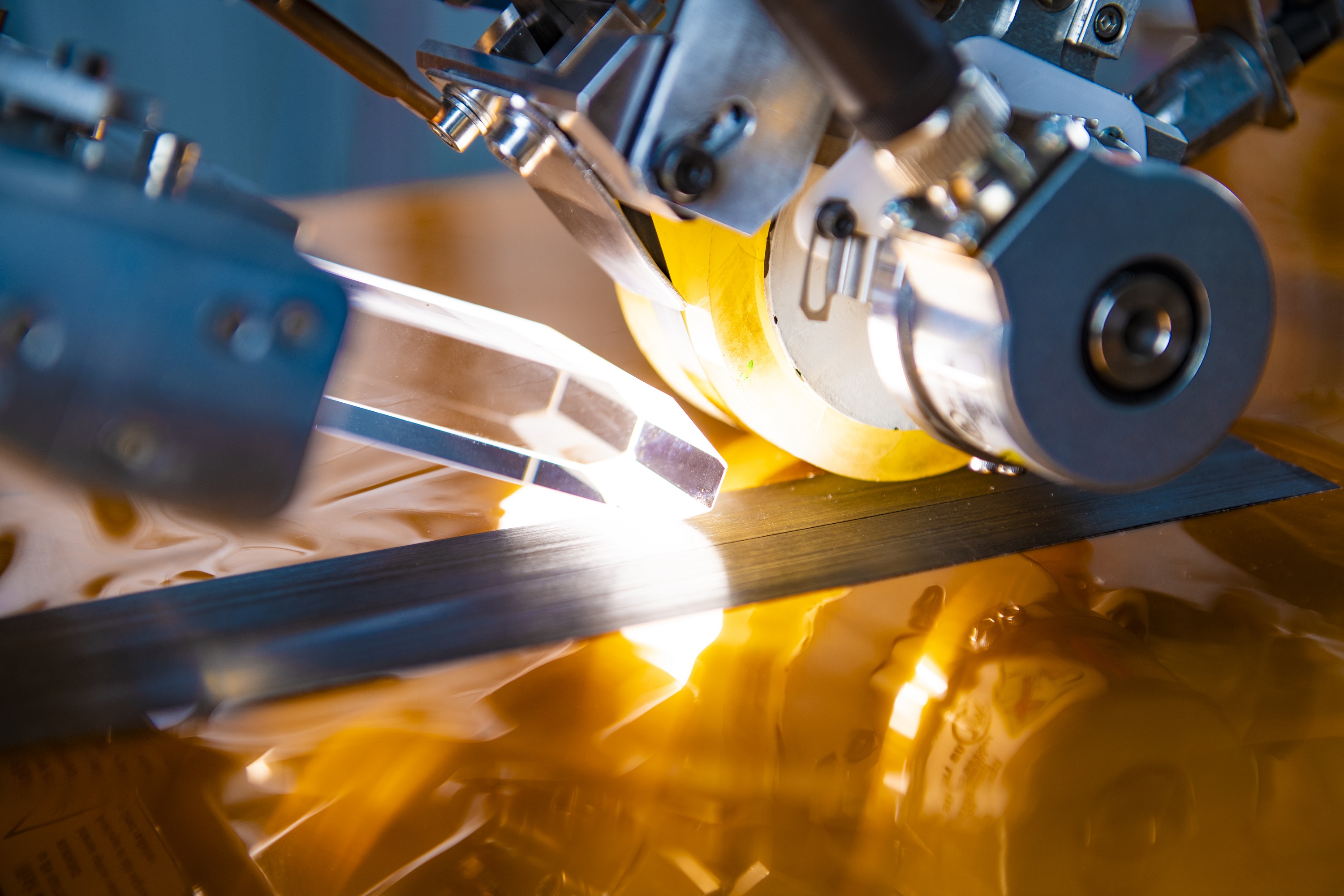
A ZLP Augsburg está investigando o AFP in-situ baseado em lâmpada flash de compostos termoplásticos, uma solução de energia pulsada que elimina os invólucros de segurança necessários para AFP baseado em laser. Fonte | DLR
Os compósitos termoplásticos também oferecem oportunidades em aplicações espaciais. Apresentações de Ralf Hartmond, MT Aerospace AG e Lars Brandt, gerente de projeto para aplicações relacionadas ao espaço na DLR, delineou o desenvolvimento de um estágio superior termoplástico reforçado com fibra de carbono para a próxima geração Ariane lançador de foguetes. Brandt detalhou o trabalho do DLR na triagem de materiais para o tanque de hidrogênio líquido (LH 2 ) tanque - onde a fibra de carbono PEEK e PAEK de baixo derretimento (LM) oferecem promessa - e o desenvolvimento de um processo AFP composto termoplástico in-situ para permitir uma abordagem de manufatura aditiva enxuta. A ZLP está comparando um novo processo de AFP in-situ assistido por lâmpada flash em comparação com o AFP assistido por laser tradicional.
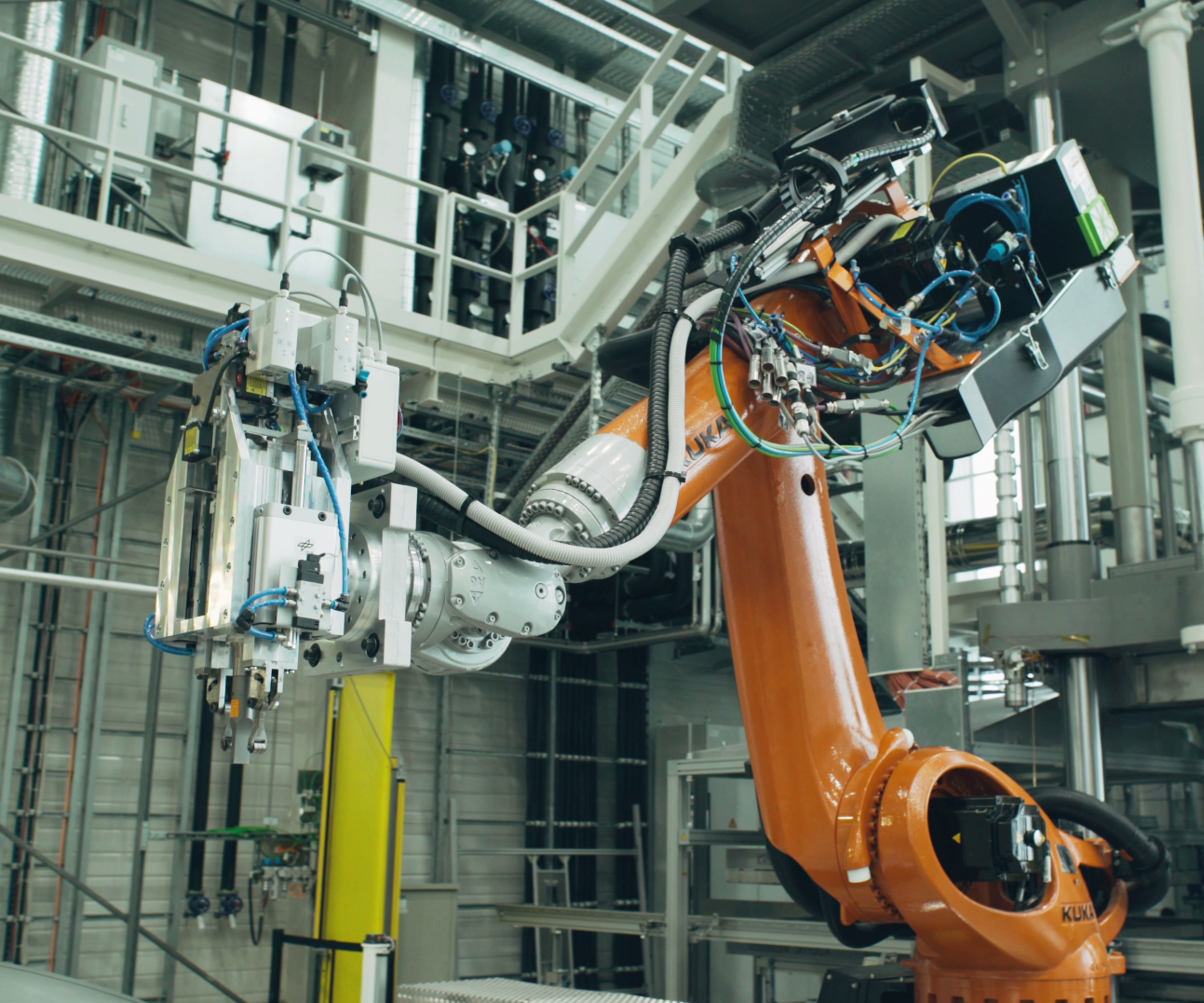
A união de tecnologias será a chave para o sucesso da introdução de compósitos termoplásticos em futuras aplicações aeroespaciais. A ZLP em Augsburg desenvolveu um sistema de soldagem ultrassônica contínua baseado em robô, que consiste em um atuador montado em um robô KUKA QUANTEC KR210 em uma pista linear de 7 m. Isso foi comprovado em componentes, incluindo um painel de fuselagem reforçado e uma antepara de pressão traseira. Fonte | DLR
O dia terminou com uma palestra instigante do Prof. Dr. Michael Kupke, chefe da ZLP Augsburg, intitulada “Digitalização e Produção Flexível”. Ele perguntou se a ascensão da economia da plataforma digital apresenta oportunidades ou riscos para os fabricantes de compósitos e apontou que a TI está se tornando uma competência essencial e deve ser tratada como uma vantagem competitiva que agrega valor, em vez de um centro de custo. Ele também disse que há uma mudança de paradigma em andamento do planejamento detalhado para a auto-organização (produção enxuta) e automação combinada com digitalização. A IA, diz ele, torna a produção autônoma e flexível possível. Porém, concluiu Kupke, é fundamental valorizar e integrar as competências humanas, vitais para a tomada de decisões e melhoria de processos.
Resina
- 4 questões candentes para fabricação de aditivos em 2019
- 25 marcos importantes para a fabricação de aditivos em 2019
- 3 Previsões de fabricação para 2019
- Os 10 principais avanços na tecnologia de fabricação de compósitos
- Mais do JEC World 2019
- Antevisão do JEC World 2019:SABIC
- People in Compposites - Janeiro de 2019
- Tecnologia de automação destaca segurança, fabricação flexível
- 2019:previsões de fabricação
- Práticas recomendadas de marketing de fabricação para 2019