Entrevista com especialista:Yves Hagedorn, diretor administrativo da Aconity3D, sobre como ajudar empresas a inovar com manufatura aditiva
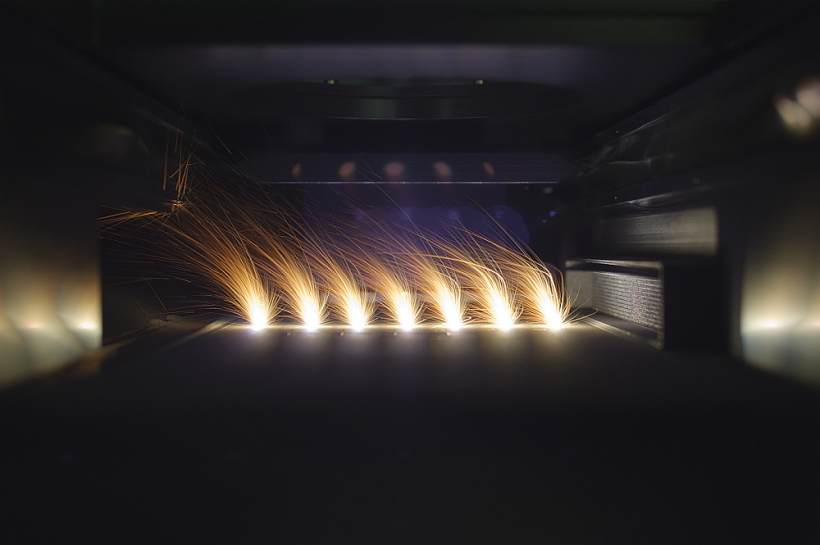
A adoção da impressão 3D em metal pode ser um desafio devido à necessidade de desenvolver aplicações, qualificar materiais e processos. Para superar esses desafios, a empresa alemã Aconity3D fornece sistemas flexíveis de impressão 3D de metal de laboratório que permitem aos clientes fazer experiências com parâmetros de processo e pesquisar novas aplicações para a tecnologia.
Na Entrevista com Especialista desta semana, Yves Hagedorn, Diretor Administrativo da Aconity3D, discute os benefícios dos sistemas de hardware com arquitetura aberta e porque o software de design é um dos principais desafios na impressão 3D de metal.
Você poderia me falar sobre Aconity3D?
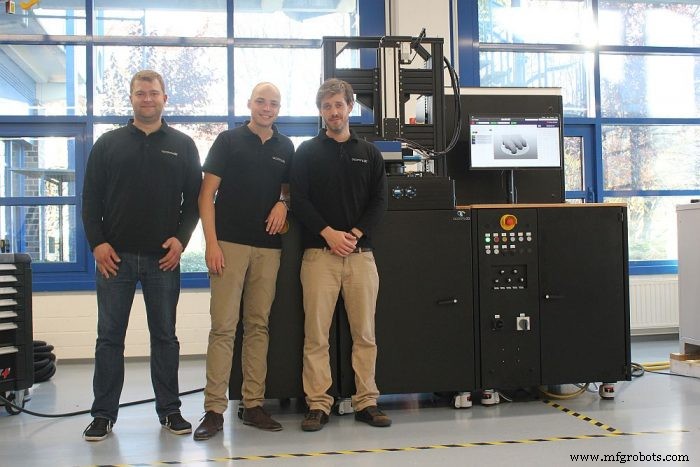
Na Aconity3D, oferecemos tudo o que é necessário para a fabricação de aditivos de metal.
Nós fornecemos componentes de máquinas especiais e diferentes módulos, que podem ser combinados para criar equipamentos projetados para aplicações especializadas. Isso porque acreditamos que não existe um sistema que possa se adequar a todas as aplicações possíveis em todo o mercado.
Nossa jornada do cliente começa com consultoria. Por exemplo, um cliente pode nos abordar para ver se é possível imprimir magnésio em 3D. Neste caso, faríamos algumas pesquisas em nossa segunda unidade de negócios, que é a distribuição de material, e descobriríamos para nosso cliente onde conseguir o material específico em questão.
Em nossa terceira unidade de negócios, faríamos alguns testes para garantir que o material fosse viável para ser processado com manufatura aditiva. E se tudo isso funcionar, e um cliente estiver satisfeito, agiríamos como uma oficina e fabricaríamos esse aplicativo específico para o cliente.
A longo prazo, o cliente pode decidir comprar nosso equipamento, que foi projetado para essa aplicação específica.
Nossa abordagem permite que nossos clientes conduzam pesquisas eficientes em termos de extensão do escopo dos materiais aplicáveis.
Se os clientes possuem determinados materiais para aplicações especiais que ainda não são qualificados, eles podem fazer muitas pesquisas para a qualificação com nosso equipamento. Eles podem usar vários parâmetros, são totalmente gratuitos do lado do software e também podem realizar alterações no hardware, dependendo dos parâmetros de que precisam.
Em última análise, queremos ser um balcão único para os clientes. No entanto, a venda de equipamentos é o nosso principal negócio.
Qual foi a motivação por trás da fundação da empresa?
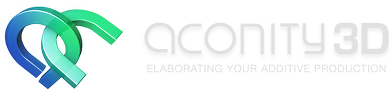
Vimos que não havia nenhum sistema no mercado que lhe permitisse fazer isso. E foi então que tivemos a ideia de oferecer aos clientes a possibilidade de ajustar seus processos. Foi quando Aconity3D nasceu.
Logo percebemos que temos um ativo real e que podemos atender a uma necessidade real do cliente de ter acesso ao hardware e ao software.
Existem setores específicos que se beneficiariam ao máximo com a tecnologia e os serviços que a Aconity3D fornece?
Não existe uma indústria específica, já que as aplicações industriais de aditivos são tão múltiplas quanto as possibilidades.
Vejamos a indústria médica, onde existe um enorme campo de aplicações. Por exemplo, você pode ter implantes de titânio ou mesmo magnésio, que é bioabsorvível. Também existem aplicações na indústria de sensores médicos.
O mesmo se aplica à indústria aeroespacial. A indústria aeroespacial tem interesse em estender o escopo de ligas aplicáveis para galvanização, por exemplo, ou ligas de alta temperatura.
O setor automotivo também é outro exemplo interessante porque a indústria se preocupa muito com os custos. Isso significa que as empresas automotivas só querem pagar pelo que recebem.
Nossa proposta de valor é nossa alta flexibilidade, o que nos permite deixar de fora tudo o que não é necessário para aquela aplicação específica. Isso nos permite competir com as tecnologias de fabricação tradicionais.
Quando se trata de impressão 3D de metal, quais aplicativos são mais adequados para a tecnologia e como as empresas podem começar a identificar os tipos certos de aplicativos?
É bom considerar a manufatura aditiva se você tiver componentes de tamanhos pequenos e estruturas complexas. Outra razão para usar aditivo pode ser combinar novos materiais onde antes era impossível fazê-lo - pegue o cobre e o cromo como exemplo.
O principal obstáculo aqui é que, para quase todas as aplicações, produzir uma peça é mais caro com manufatura aditiva quando comparado com fresamento ou outras tecnologias de manufatura tradicionais.
Uma exceção são as restaurações dentárias:para estas, a manufatura aditiva é mais barata do que a fresagem. É por isso que foi uma das primeiras aplicações industriais para fusão a laser à base de pó. Outra exceção são as armações de óculos, que também são uma ótima aplicação para aditivos.
Mas para todos os outros, muitas vezes há um conflito entre o caso de negócio e os custos do ciclo de vida do produto. Esse é o principal obstáculo porque muitos clientes simplesmente não têm ideia sobre os custos do ciclo de vida do produto.
Em outras palavras, agora você pode ter uma integração funcional. Então, por exemplo, você pode integrar canais de resfriamento em uma caixa, mas é realmente difícil colocar um preço nisso. Portanto, o principal desafio é fazer a triagem da peça e encontrar um caso de negócios válido para sua aplicação e produção de aditivos.
Quais são os principais desafios da impressão 3D em metal e como você os enfrentou?
Na minha opinião, um dos principais desafios está no design da peça e nas soluções de software correspondentes para preparação de dados. Quando se trata de manufatura aditiva, a padronização ainda é um desafio e acredito que isso se deva em parte ao fato de o software não ser realmente padronizado. Por exemplo, pegue os vários formatos de dados diferentes para cada provedor de sistema individual. Além disso, em termos de projeto de peças, não há limites para nenhuma orientação como consequência da flexibilidade absoluta da produção de aditivos. Esta é também a razão pela qual as estruturas de restauração dentária foram a primeira verdadeira aplicação industrial:Um projeto de peças totalmente automatizado e uma estrutura de preparação de dados - uma pré-condição para a produção em série de peças de lote único.
Pela primeira vez desde os anos 70, estamos agora em uma situação em que podemos construir peças mais complexas do que podemos projetar ou simular.
Assim, design e preparação de dados ainda são um gargalo nesta indústria enquanto a ênfase é colocada em sistemas de hardware de maior produtividade, com soluções de software inteligentes sendo excluídas desta equação. Preparar as peças de forma que sejam adequadas para a manufatura aditiva é uma habilidade chave e também requer muito tempo.
Já vi exemplos em que o design da peça e a preparação dos dados levaram mais de duas semanas, enquanto a impressão da peça demorou apenas dois dias. Isso é simplesmente ineficiente para projetar uma peça para esse período de tempo. E é aí que entra o problema, na minha opinião.
Você poderia compartilhar algumas das histórias de sucesso de seus clientes?
Sim definitivamente. Tivemos clientes que agora estão produzindo peças de magnésio para aplicações médicas. Temos outros que obtiveram a aprovação do FDA para seus implantes de titânio.
Na indústria automotiva, tínhamos um pedido específico de um sistema de alta produtividade. Portanto, fornecemos um sistema de quatro laser com sobreposição total em uma placa de 400 milímetros de diâmetro. Acho que somos os únicos no mercado que conseguem fazer isso, e isso tem um impacto significativo na produtividade.
Outros clientes exploram a possibilidade de pré-aquecimento a alta temperatura para expandir o escopo dos materiais aplicáveis em aços-ferramenta de alta liga, Aluminetos de titânio e certas superligas à base de níquel.
Como você vê a evolução da indústria de AM nos próximos anos?
A indústria definitivamente amadureceu nos 12 anos em que estive envolvido com aditivos. Quando comecei, havia muito exagero. Agora, o hype diminuiu um pouco.
A evolução da tecnologia ajudou a desbloquear muitas aplicações para a manufatura aditiva, mas todas essas aplicações ainda requerem um alto nível de especialização.
Hoje, você pode comprar certas impressoras 3D de mesa por menos de 1000 euros, o que faz muitas pessoas acreditarem que você pode comprar máquinas de ferramentas industriais, como aqueles caros sistemas de fusão a laser baseados em pó, pressione play e você imediatamente terá seu caso de negócios.
Obviamente, esse não é o caso da manufatura aditiva industrial. Existe um grande desafio no treinamento e no desenvolvimento de competências. E eu acho que é onde toda a indústria precisará continuar a evoluir.
Ter mais expertise na indústria e, acima de tudo, ter processos mais padronizados e produtos confiáveis será a chave para a adoção industrial da manufatura aditiva.
Há algum desenvolvimento na indústria de AM que o entusiasme?
Sim definitivamente. Temos um forte foco não apenas no monitoramento em processo, o que significa usar diferentes sensores para obter o máximo de informações possível fora do seu processo, mas também em usar essas informações para fazer o controle em processo.
Acho que esse é o Santo Graal da AM porque, com o controle do processo, você pode reagir quase imediatamente às deficiências do seu processo.
Isso tornará os sistemas muito mais inteligentes.
Você poderia falar um pouco mais sobre monitoramento e controle em processo, e o que Aconity3D está fazendo nesse espaço?
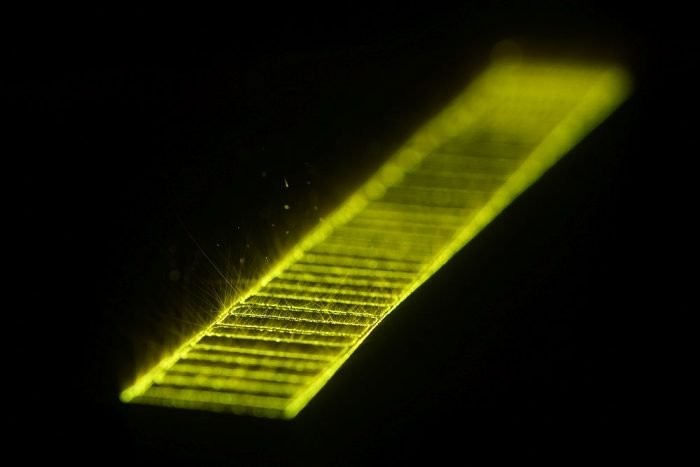
Nossa empresa é um spin-off do Fraunhofer Institute for Laser Technology, onde se originou a fusão a laser em leito de pó.
Com esse pano de fundo, fomos capazes de implementar diferentes sensores ópticos para acompanhar o laser de processamento. E isso permite que você extraia muitas informações imediatamente da zona de interação, piscina de fusão e laser.
Isso, no entanto, leva a outros desafios associados ao Big Data. O que você faz com essa enorme quantidade de dados gravados? Como você se certifica de pular os dados de que realmente não precisa? E como você distingue entre dados úteis e inúteis?
Eu acho que é onde a indústria está atualmente. E é isso que também estamos fazendo. Usamos uma câmera de alta velocidade para observar o processo e aprender com ele, e também temos diferentes sensores que permitem um circuito fechado no controle do processo.
Então, se você tiver esse sistema, você pode detectar se sua piscina de fusão está muito quente ou muito grande, e você pode regular isso por meio da potência do laser, reagindo assim ao sinal do processo.
Isso é realmente fascinante para mim. E acho que ainda há muito potencial aqui.
Aconity3D anunciou recentemente uma parceria com a Aerosint. O que essa parceria significa para sua empresa no futuro?
Desde que estou no setor, as pessoas se interessam por peças de metal multimateriais. E sempre foi o problema do que deveria vir primeiro, a aplicação ou o desenvolvimento técnico.
Por algum tempo, nada realmente aconteceu nesse sentido. E então nos encontramos com a Aerosint, uma empresa belga que desenvolveu um dispositivo de deposição de pó capaz de depositar dois materiais diferentes nas dimensões X e Y em um leito de pó. Isso é basicamente o que tem faltado na manufatura aditiva de multimateriais.
Agora chegamos à equação com a capacidade de reagir ao padrão de pó alterado ou padrão de material em nossa placa de impressão, alterando os parâmetros de processo necessários para cada material individual.
Isso significa que ambos os parceiros, Aconity3D e Aerosint, têm uma base sólida para tornar esse sonho AM multimaterial em realidade.
Que novas aplicações podem ser abertas com a possibilidade de impressão 3D em metal multimaterial?
Uma indústria que poderia realmente se beneficiar é a joalheria.
Criar materiais graduados, de cobre a cromo, pode ser outra oportunidade. Eles poderiam ser usados para ferramentas nas indústrias de moldagem ou forja. Por exemplo, com a impressão 3D multimaterial, você pode usar cobre para criar estruturas de resfriamento e cromo ou aço para criar a superfície externa da peça.
Se você tiver gradientes, também poderá classificar suas propriedades mecânicas. Isso pode ser útil no campo médico para a redução da proteção contra tensões. Esse efeito ocorre quando os implantes de metal são muito densos, fazendo com que o osso perca sua resistência. A proteção contra tensões também pode ser reduzida alterando as propriedades mecânicas do implante com a ajuda da impressão 3D multimaterial.
No entanto, antes de novas aplicações serem desenvolvidas, acho que é necessário um impulso tecnológico para mostrar as capacidades semelhantes às capacidades atuais da manufatura aditiva.
O que o futuro reserva para Aconity3D?
Continuaremos a expandir o escopo de materiais aplicáveis que, da mesma forma que os multimateriais, nos permitirão oferecer novas aplicações para nossos parceiros industriais. Queremos nos aprofundar nas aplicações de séries especializadas.
Entendemos que, com aplicações de nicho, pode ser muito difícil qualificar novos materiais, especialmente quando é apenas para um cliente. No entanto, nosso objetivo é garantir que nossos clientes fiquem satisfeitos e possam explorar as aplicações que eles têm em mente.
Em última análise, queremos ser o capacitador da inovação para nossos clientes.
Para saber mais sobre Aconity3D, visite: aconity3d.com
impressao 3D
- Como as empresas aeroespaciais podem levar a fabricação de aditivos ao próximo nível com o MES?
- Por que as empresas deveriam abraçar a manufatura aditiva distribuída?
- Entrevista com especialista:Pat Warner, especialista em fabricação de aditivos da equipe Renault de Fórmula 1
- Entrevista com um especialista:Professor Neil Hopkinson, Diretor de Impressão 3D da Xaar
- Entrevista com um especialista:Dr. Alvaro Goyanes da FabRx
- Entrevista com um especialista:Dr. Bastian Rapp da NeptunLab
- Entrevista com especialista:Felix Ewald, CEO da DyeMansion
- Entrevista com um especialista:Ibraheem Khadar de Markforged
- Aprimoramento da fabricação de aditivos com engenharia reversa
- Entrevista com especialista:James Hinebaugh da Expanse Microtechnologies