O que é Strain Wave Gear, também conhecido como Harmonic Drive? Um conjunto de equipamentos perfeito para aplicações de robótica!?
Neste tutorial vamos aprender o que é Strain Wave Gear, também conhecido como Harmonic Drive. Primeiro, explicaremos seu princípio de funcionamento, depois projetamos nosso próprio modelo e o imprimimos em 3D para que possamos vê-lo na vida real e entender melhor como funciona.
Você pode assistir ao vídeo a seguir ou ler o tutorial escrito abaixo.
O que é Strain Wave Gear?
A Strain Wave Gear é um tipo único de sistema de engrenagem mecânica que permite uma taxa de redução muito alta em um pacote compacto e leve. Comparado aos sistemas de engrenagens tradicionais, como engrenagens helicoidais ou engrenagens planetárias, ele pode atingir taxas de redução muito mais altas de até 30 vezes no mesmo espaço. Além disso, possui característica de folga zero, alto torque, precisão e confiabilidade. Portanto, este sistema de engrenagens é usado em muitas aplicações, incluindo robótica, aeroespacial, máquinas médicas, fresadoras, equipamentos de fabricação e assim por diante.
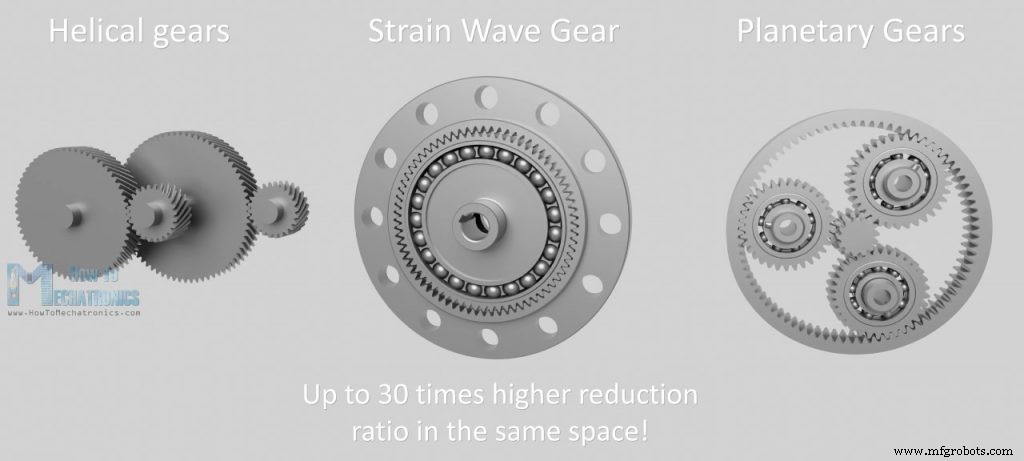
A Strain Wave Gear foi inventada em 1957 por C. Walton Musser, e o outro nome que é comumente usado para ela, “Harmonic Drive”, é na verdade uma marca de strain wave gear registrada pela empresa Harmonic Drive.
Como funciona
Tudo bem, então vamos dar uma olhada como funciona agora. Um acionamento harmônico tem três componentes principais, um gerador de ondas, um spline flexível e um spline circular.
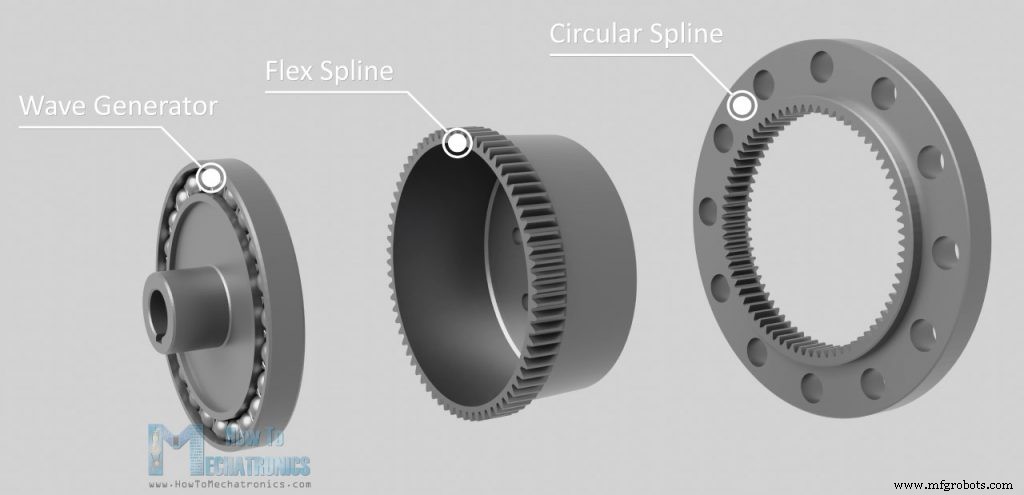
O gerador de ondas tem uma forma elíptica e consiste em um cubo elíptico e um mancal especial de parede fina que segue a forma elíptica do cubo. Esta é a entrada do conjunto de engrenagens e está conectada ao eixo do motor.
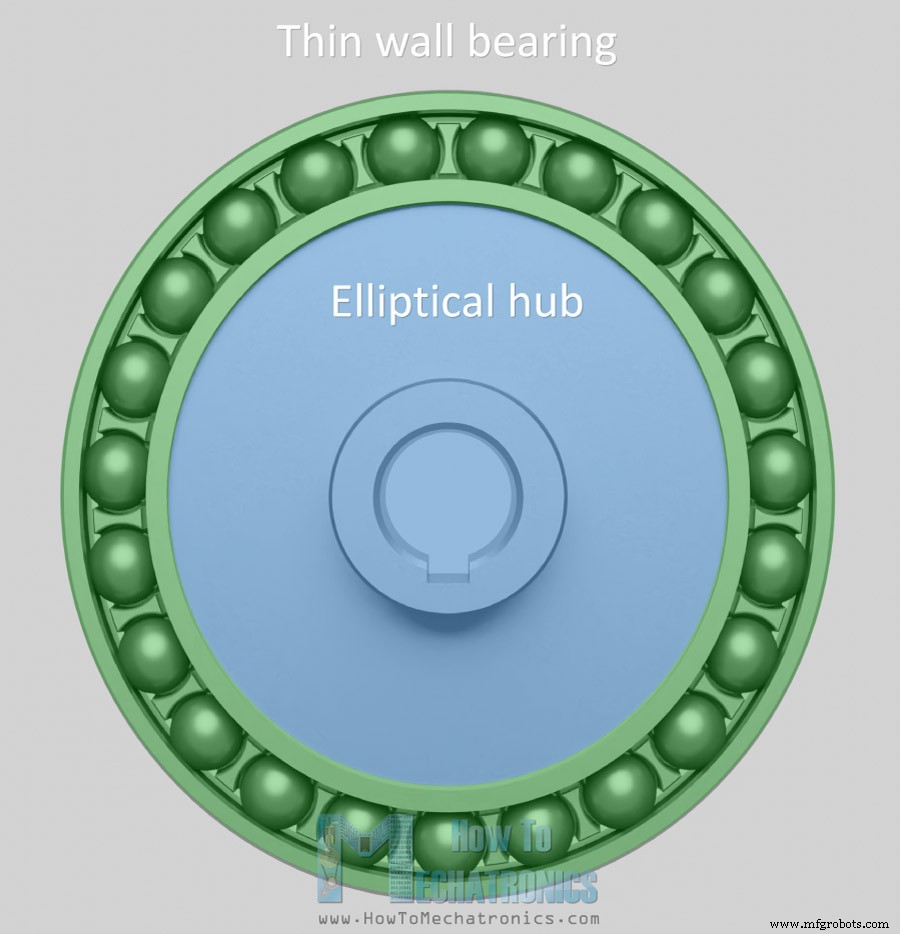
À medida que o gerador de ondas gira, ele gera um movimento de onda.
O spline Flex tem a forma de um copo cilíndrico e é feito de material de liga de aço flexível, mas torcionalmente rígido. Os lados do copo são muito finos, mas o fundo é grosso e rígido.
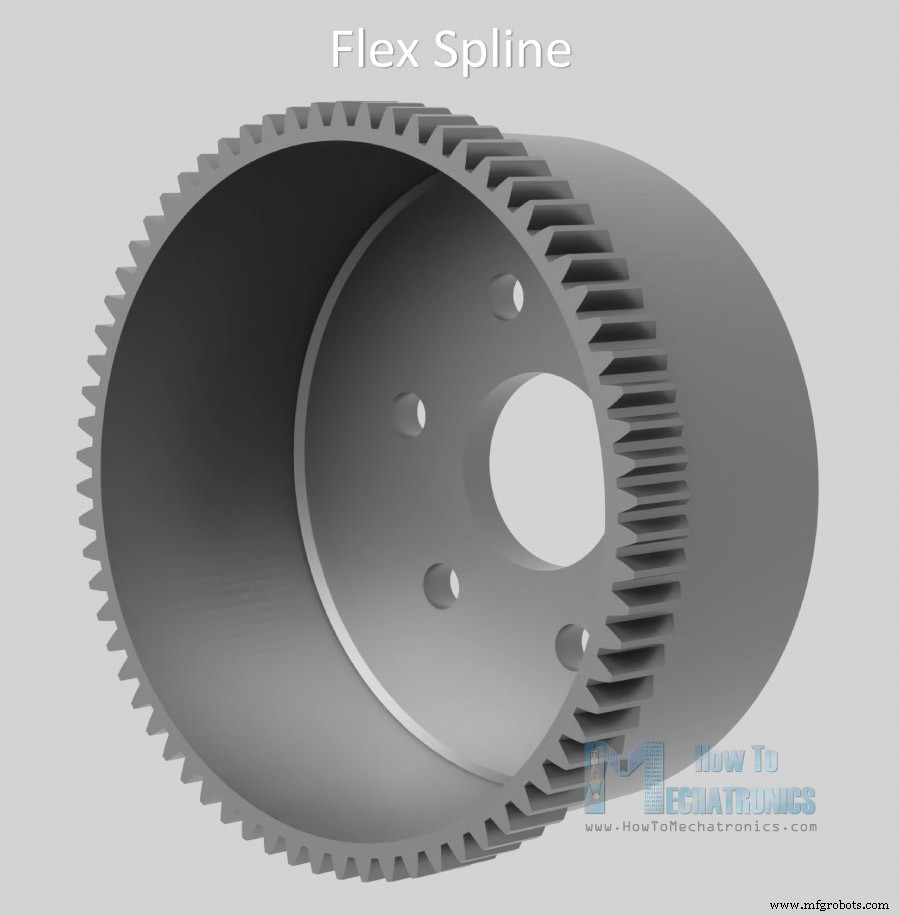
Isso permite que a extremidade aberta do copo seja flexível, mas a extremidade fechada seja bastante rígida e, portanto, podemos usá-la como saída e conectar o flange de saída a ela. O spline flexível possui dentes externos na extremidade aberta do copo.
Por outro lado, o spline circular é um anel rígido com dentes no interior. O spline circular tem mais dois dentes que o spline flexível, que na verdade é o design principal do sistema de engrenagem de onda de tensão.
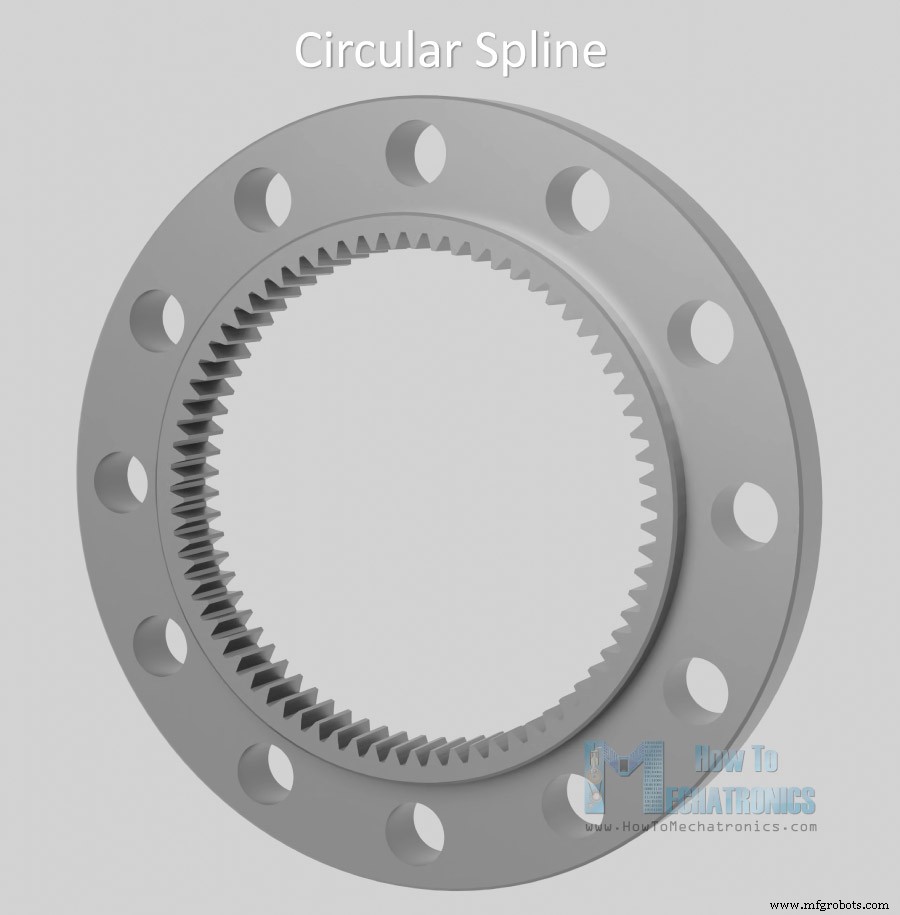
Assim, quando inserimos o gerador de ondas no Flex spline, o flex spline toma a forma do gerador de ondas.
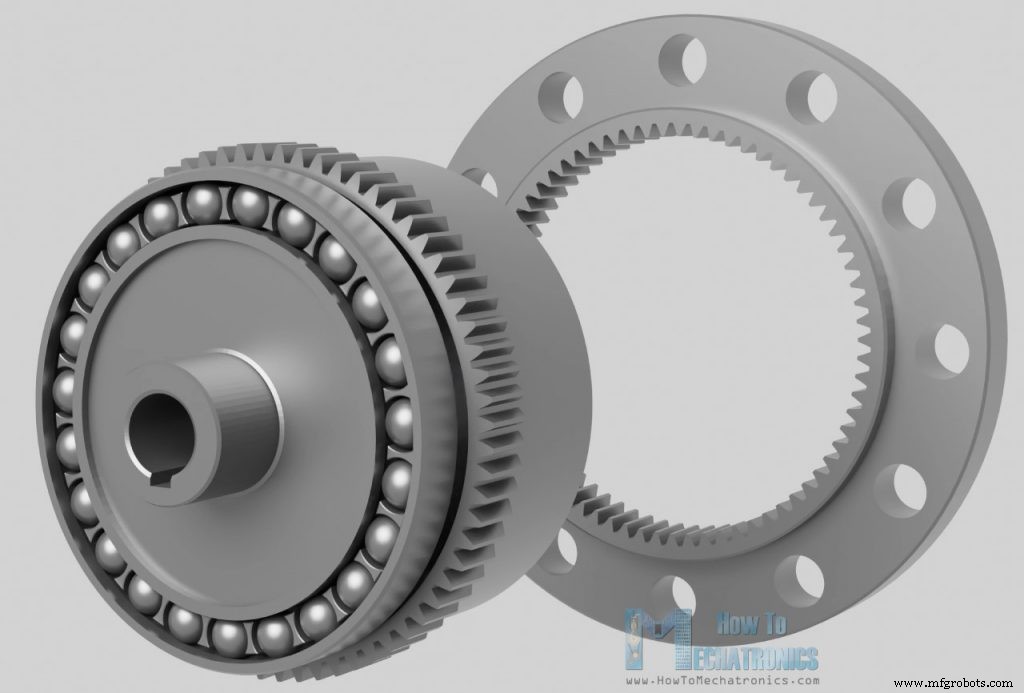
À medida que o gerador de ondas gira, ele deforma radialmente a extremidade aberta do spline flexível. O gerador de ondas e o spline flexível são então colocados dentro do spline circular, entrelaçando os dentes.
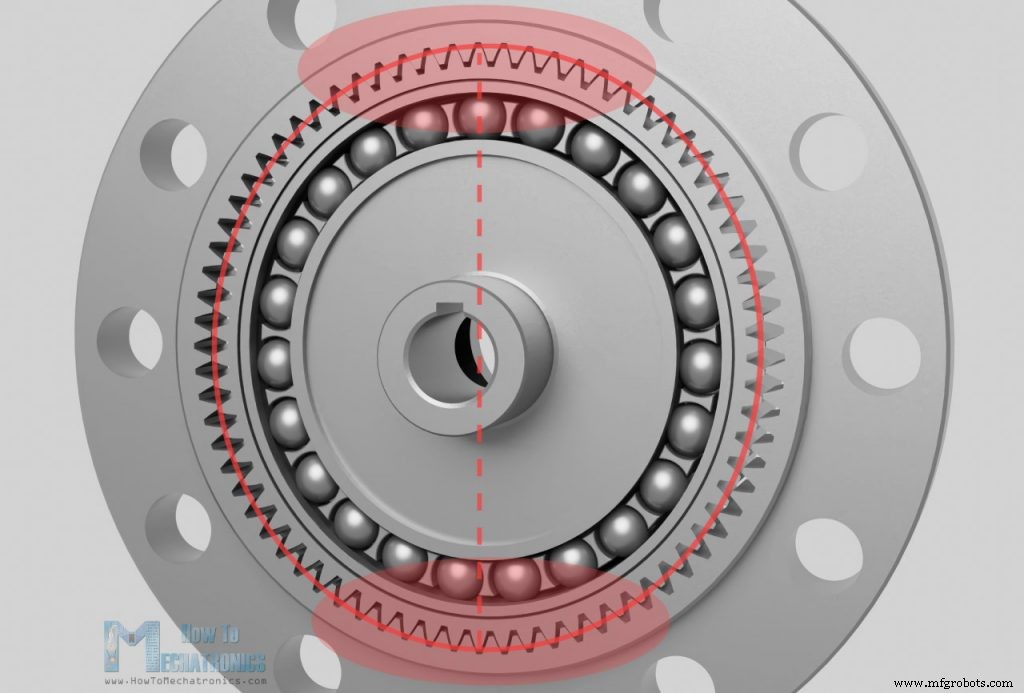
Por causa da forma elíptica do flex spline, os dentes se encaixam apenas em duas regiões nos lados opostos do flex spline, e isso está no eixo principal da elipse do gerador de ondas.
Agora, à medida que o gerador de ondas gira, os dentes do spline Flex que são engrenados com os do spline circular mudarão lentamente de posição. Devido à diferença de contagem de dentes entre o spline flexível e o spline circular, para cada rotação de 180 graus do gerador de ondas, o engrenamento dos dentes fará com que o spline flexível gire um pouco para trás em relação ao gerador de ondas. Em outras palavras, a cada rotação de 180 graus do gerador de ondas, a malha dos dentes do spline flexível com o spline circular avançará apenas um dente.
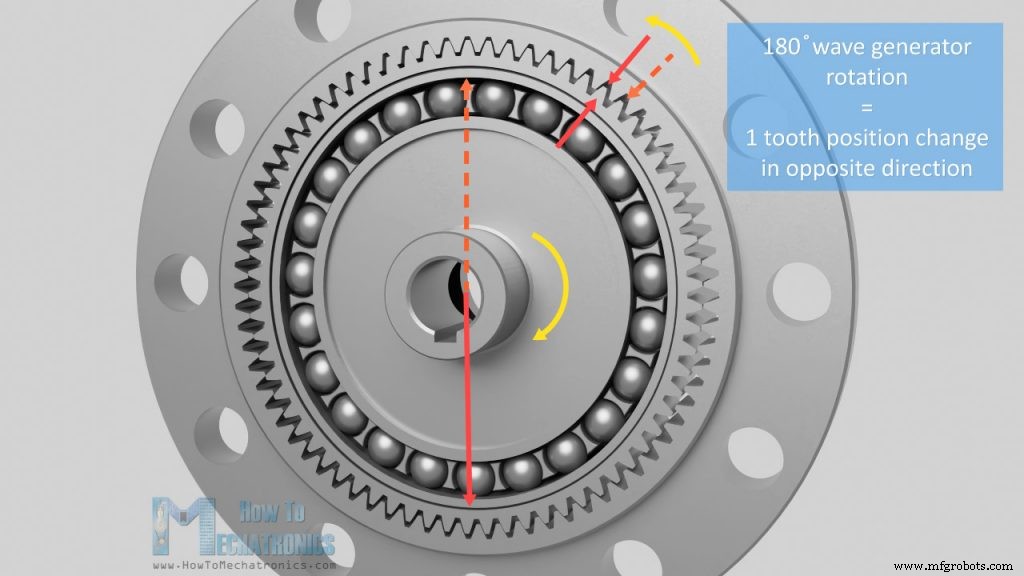
Assim, para uma rotação completa de 360 graus do gerador de ondas, o spline flexível mudará de posição ou avançará dois dentes.
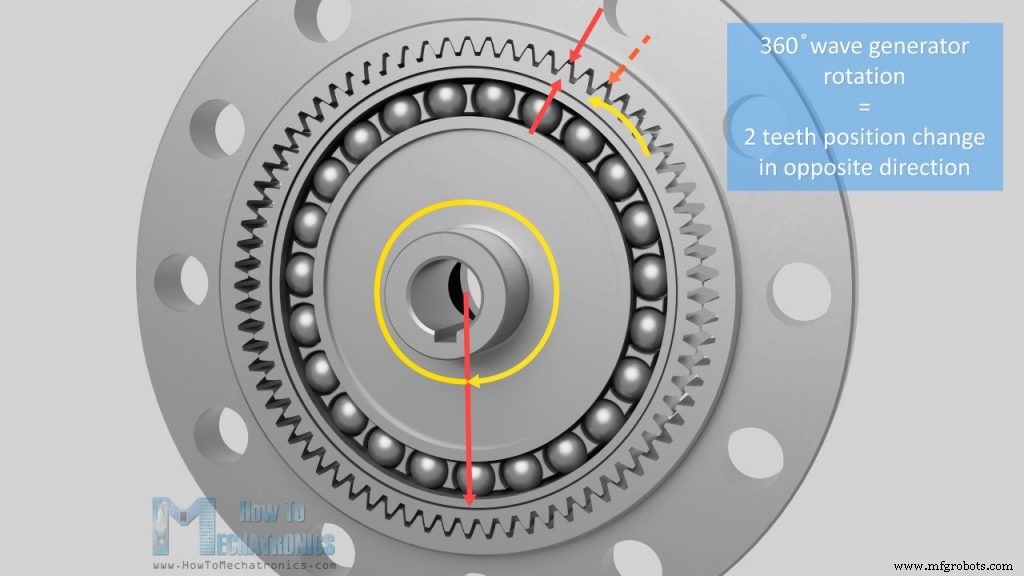
Por exemplo, se o flex spline tem 200 dentes, o gerador de ondas precisa fazer 100 revoluções para que o flex spline avance 200 dentes, ou isso é apenas uma única rotação para o flex spline. Essa é uma proporção de 100:1. Nesse caso, o spline circular terá 202 dentes, pois o número de dentes do spline circular é sempre maior que os dentes do spline flexível em dois.
Podemos calcular facilmente a razão de redução com a seguinte fórmula. A proporção é igual aos dentes spline flexíveis – dentes spline circulares, divididos pelos dentes spline flexíveis.
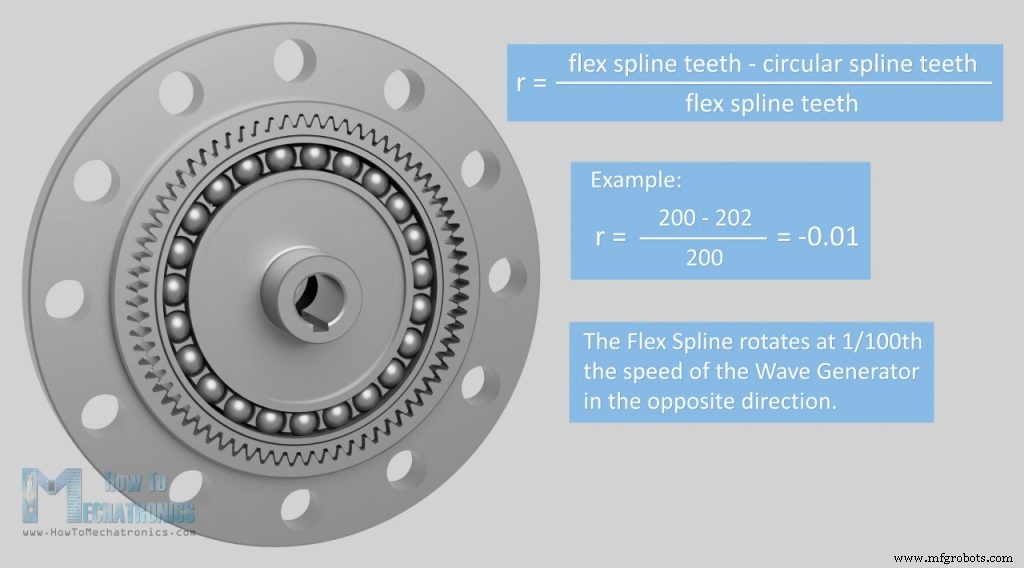
Assim, com o exemplo de 200 dentes no spline flexível e 202 dentes no spline circular, a taxa de redução é -0,01. Isso é 1/100 da velocidade do gerador de ondas e o suspiro negativo indica que a saída está na direção oposta.
Podemos obter diferentes taxas de redução alterando o número ou os dentes.
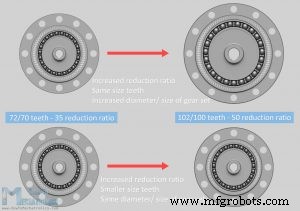
Podemos conseguir isso alterando o diâmetro do mecanismo com dentes do mesmo tamanho ou alterando o tamanho dos dentes preservando o tamanho e o peso do conjunto de engrenagens.
Strain Wave Gear – Modelo 3D de acionamento harmônico
Ok, agora que conhecemos a teoria por trás do Strain Wave Gear, deixe-me mostrar como eu projetei um para que possamos construí-lo usando apenas uma impressora 3D.
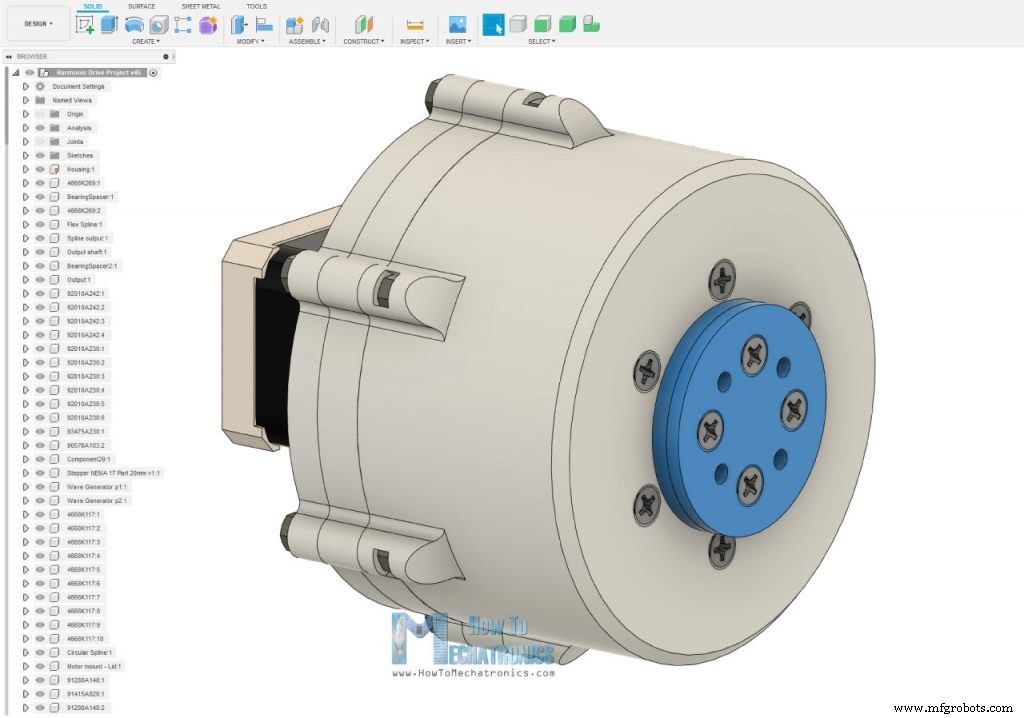
Eu projetei este modelo de Strain Wave Gear usando o Fusion 360. Todas essas peças podem ser impressas em 3D, então só precisamos de alguns parafusos e porcas e alguns rolamentos para completar a montagem. Quanto à entrada optei por usar um motor de passo NEMA 17.
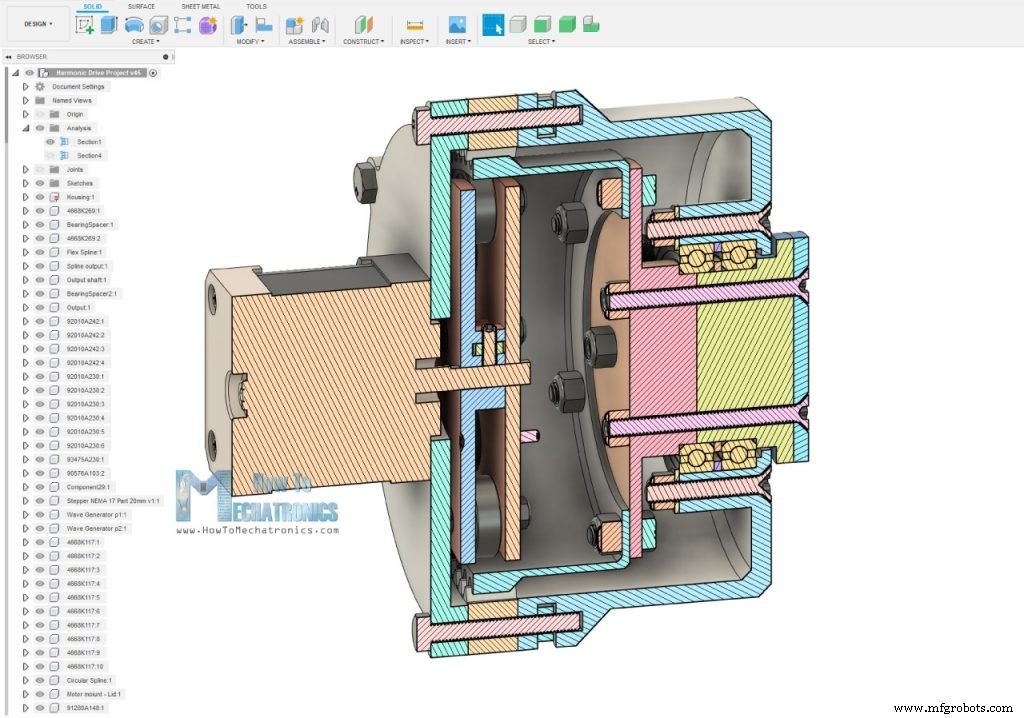
Veja como eu projetei os 3 elementos-chave da Strain Wave Gear, o spline circular, o spline flexível e o gerador de ondas. Como as impressoras 3D têm suas próprias limitações de quão bom, preciso e preciso podem imprimir, o primeiro que tive que decidir foi o módulo das engrenagens ou quão grandes ou pequenos serão os dentes. Escolhi um módulo de 1,25 e 72 dentes para o spline circular.
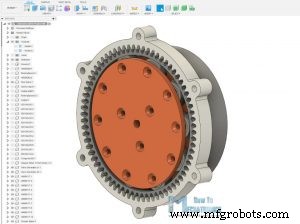
É claro que o spline flexível precisa ter 2 dentes a menos, ou seja, 70 dentes. Isso resultará em uma proporção de 35:1, tendo um tamanho relativamente pequeno do conjunto de engrenagens.
Quanto ao gerador de ondas, não podemos realmente usar esses tipos especiais de rolamentos de parede fina mencionados anteriormente, pois não são fáceis de encontrar. Em vez disso, usaremos rolamentos de esferas normais dispostos em torno de uma circunferência de uma elipse. As dimensões da elipse devem ser feitas de acordo com as dimensões da parede interna do flex spline.
Eu fiz o raio do eixo principal da elipse ser 1,25mm maior que o raio da parede interna do flex spline. Por outro lado, o raio do eixo menor da elipse é 1,25 mm menor.
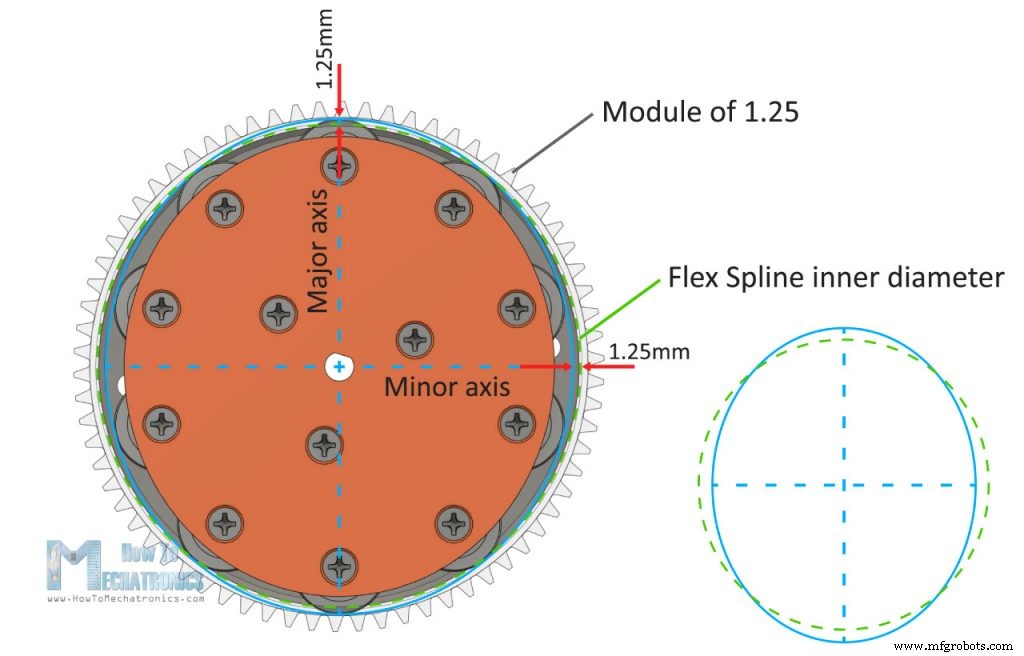
O gerador de ondas será feito de duas seções nas quais os 10 rolamentos podem ser facilmente fixados. Uma dessas seções também possui um acoplador de eixo adequado para fixar o motor de passo NEMA 17.
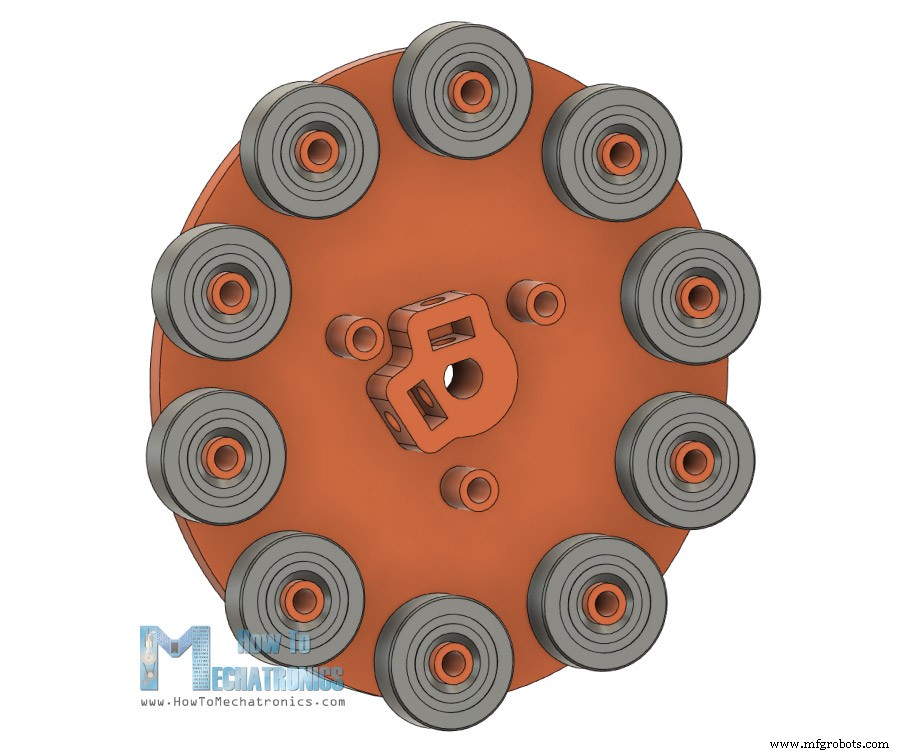
O resto das peças são projetadas em torno desses 3 componentes principais. No lado de saída da carcaça vamos inserir dois rolamentos com 47mm de diâmetro externo, e vamos fixá-los com a ajuda de alguns parafusos e porcas.
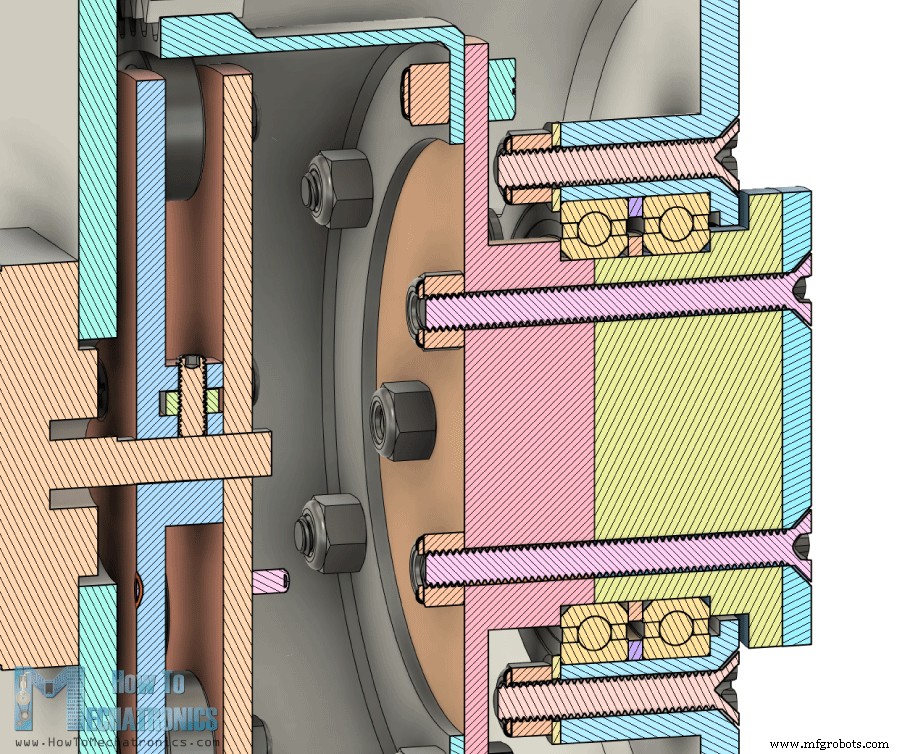
O flange de saída é feito de duas partes conectadas com parafusos e porcas para que possamos prendê-lo facilmente aos dois rolamentos.
Arquivos STL necessários para impressão 3D abaixo.
Você pode baixar este modelo 3D, bem como explorá-lo em seu navegador no Thangs.
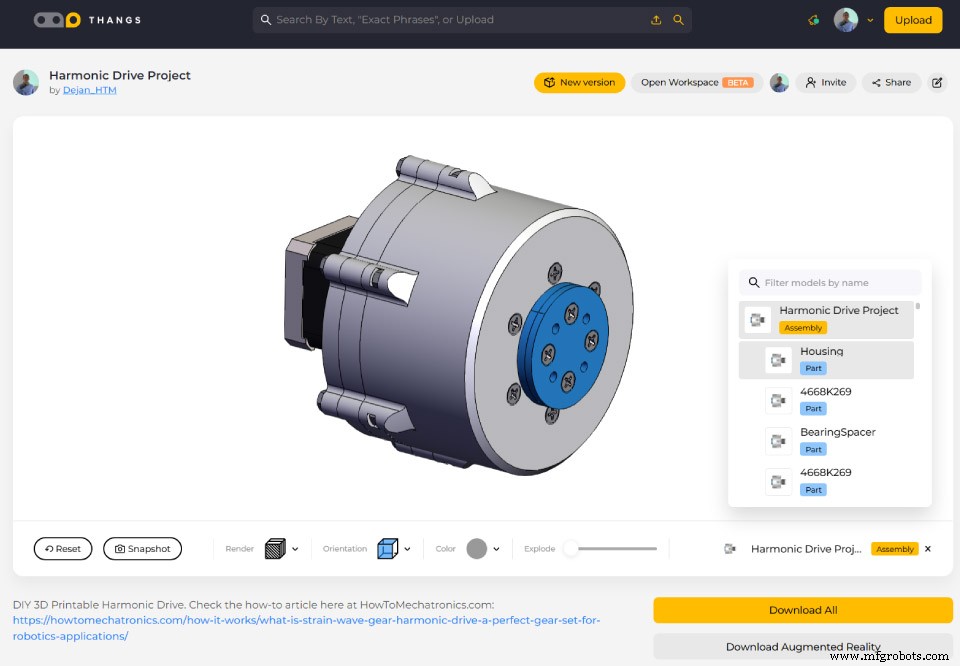
Baixe o modelo 3D em Thangs.
Arquivos STL necessários para impressão 3D:
Veja também: Melhores impressoras 3D para iniciantes e criadores [atualização de 2021]
Equipamento Strain Wave Impresso em 3D – Acionamento Harmônico
Ok, é hora de imprimir as peças em 3D agora. Ao imprimir as engrenagens em 3D, é importante usar o recurso de expansão horizontal em seu software de fatiamento.
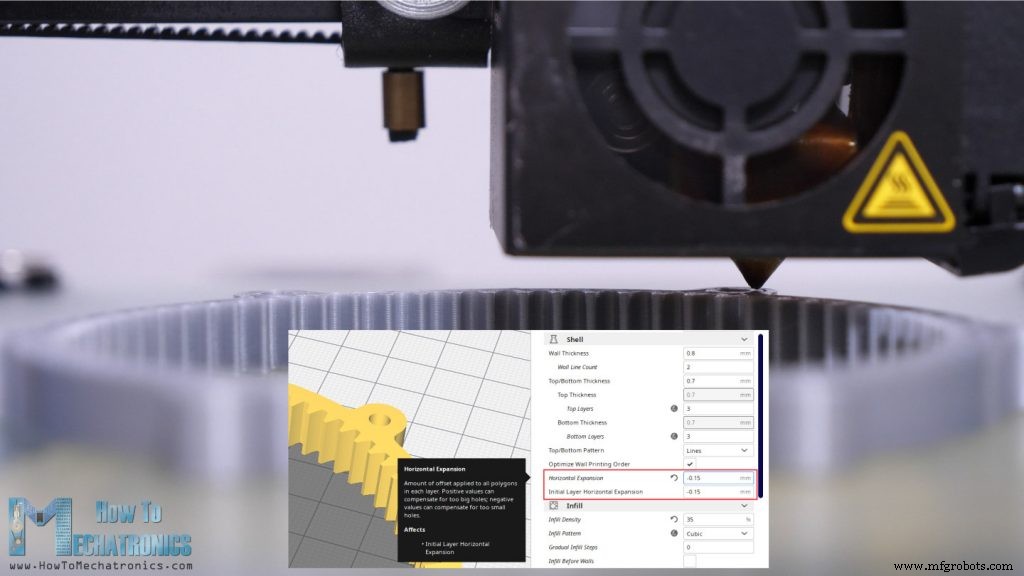
Eu configurei o meu para -0,15 mm e obtive uma precisão relativamente decente nas impressões. Observe que isso pode variar de impressora para impressora. Se não usarmos este recurso, as impressões serão um pouco maiores devido à expansão do filamento ao imprimir, e as peças ou engrenagens não poderão se encaixar adequadamente.
Usei minha impressora 3D Creality CR-10 para imprimir todas as peças e acho que fez um bom trabalho considerando o preço.
Então, aqui estão todas as peças impressas em 3D.
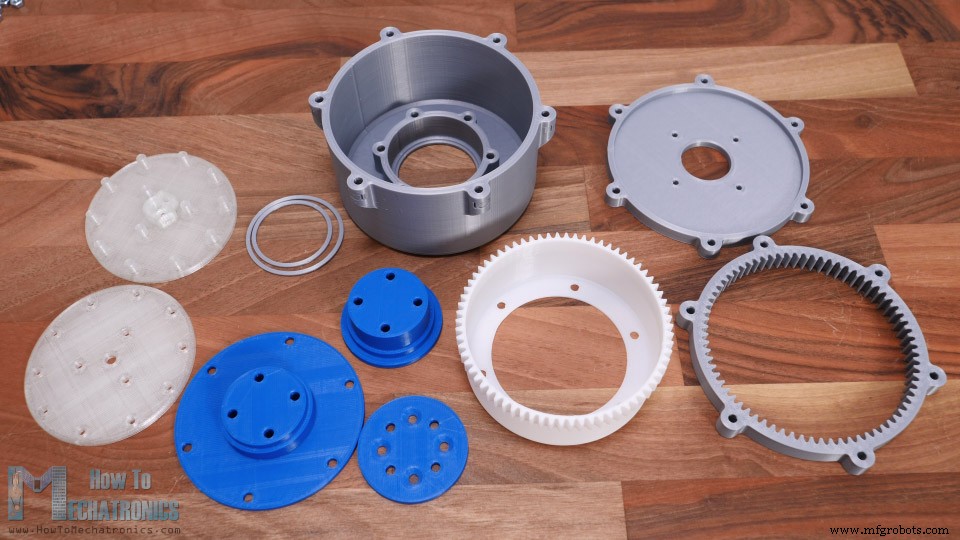
Precisamos apenas de alguns parafusos, porcas e alguns rolamentos para completar a montagem do acionamento Harmônico.
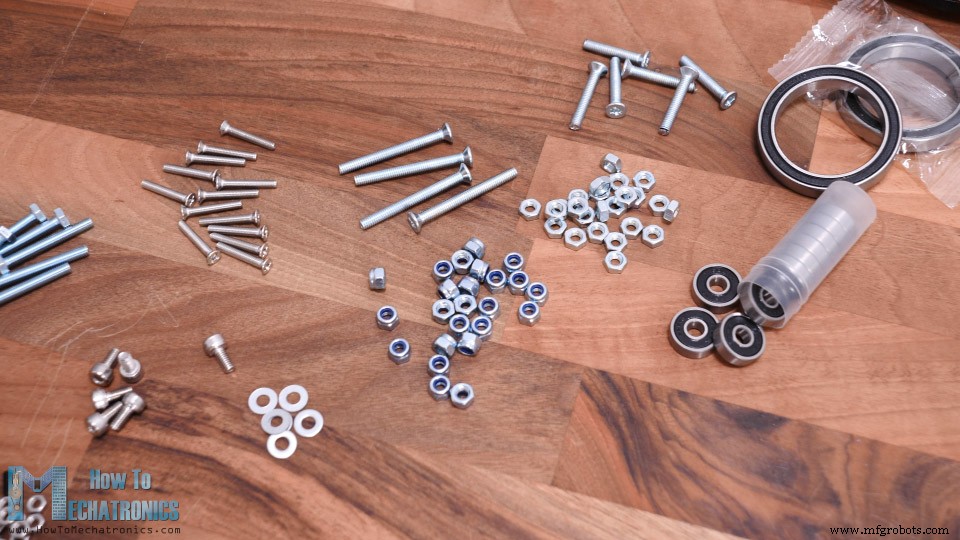
Aqui está uma lista completa de todos os componentes:
- Parafusos:
- M3x16 – 13 peças
- M3x12 – 4
- M4x12 – 6
- M4x25 – 6
- M4x30 – 6
- M4x40 – 4
- Nozes:
- M3 autotravamento – 13
- M4 autotravamento – 16
- M4 – 10
- Rolamentos:
- (OD) 16mm x (IN) 5mm x (W) 5mm – 10 ………….. Amazon
- (OD) 47mm x (IN) 35mm x (W) 7mm – 2 ………….. Amazon
- Eletrônicos:
- Motor de passo – NEMA 17………………
- Driver de passo A4988…………………..…
- Arduíno ………………………………………..…
- Fonte de alimentação CC ……………………………. Amazônia / Banggood
Comecei a montagem inserindo os dois rolamentos de saída na carcaça. Os rolamentos têm diâmetro externo de 47 mm e diâmetro interno de 35 mm. Como eu disse, usei compensação de expansão horizontal de -0,15 mm ao cortar as peças, de modo que os rolamentos se encaixaram bem na caixa.
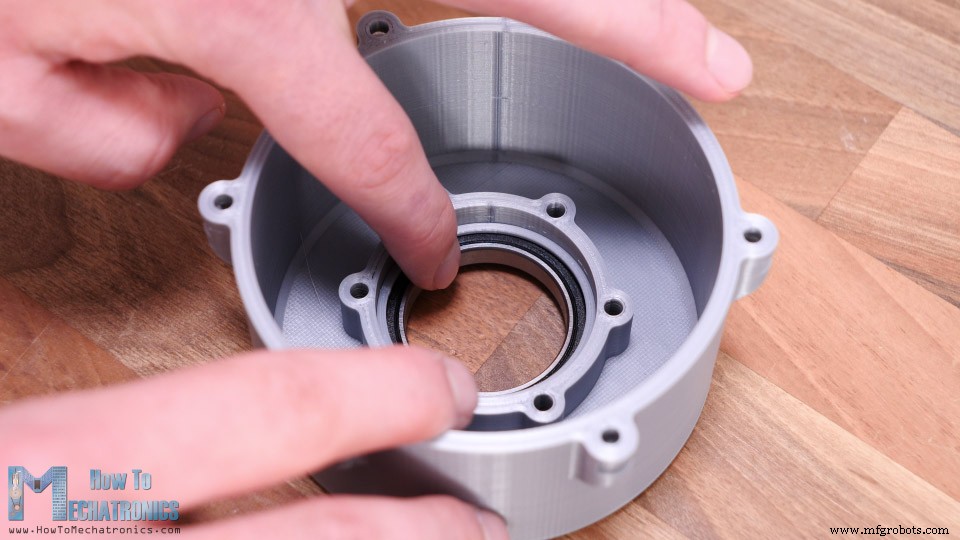
Entre os dois rolamentos, coloquei anéis de distância impressos em 3D de 1,5 mm. Para fixar os rolamentos na caixa, precisamos de seis parafusos escareados M4 com 25 mm de comprimento. Também usaremos arruelas M4 que tocarão apenas o suficiente no anel externo do rolamento e assim manterão o rolamento preso à caixa.

Em seguida é o spline Flex. As paredes do copo têm apenas 1,2 mm de espessura, portanto, embora seja impresso em PLA, ainda é flexível na extremidade aberta.
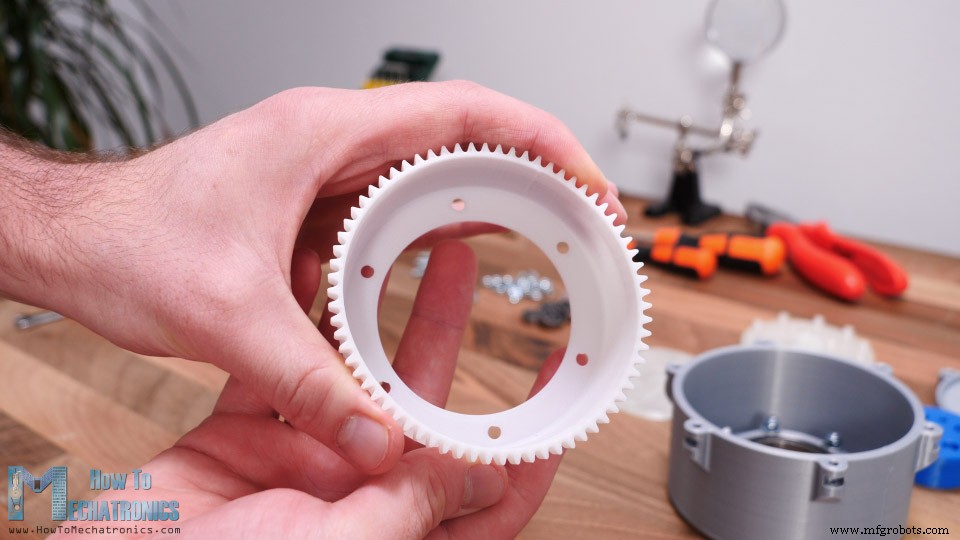
Na extremidade fechada do Flex spline podemos fixar o flange de saída usando seis parafusos M4. Uma vez seguro, o spline flexível agora é um pouco menos flexível do que anteriormente, mas a extremidade fechada agora é bastante rígida.
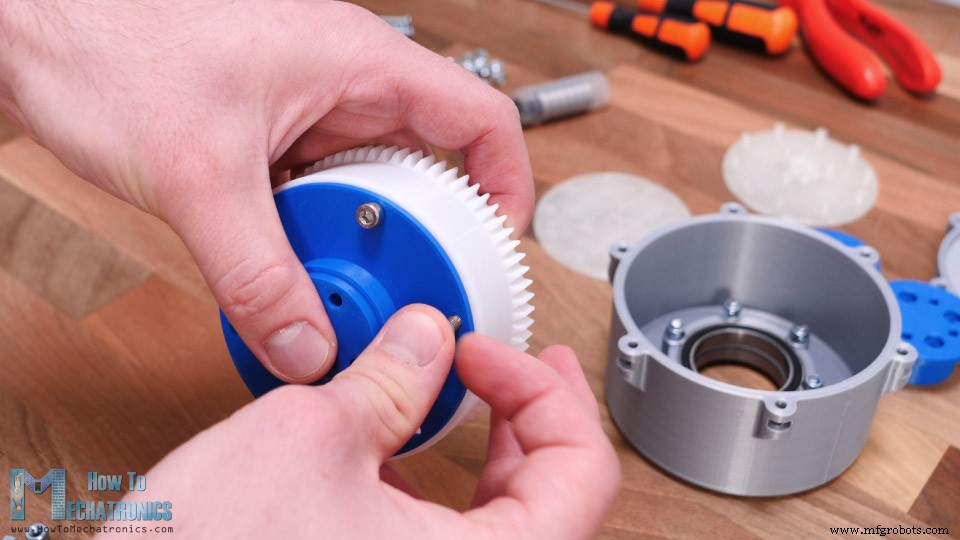
Em seguida, precisamos inserir o spline flexível através do rolamento. O flange de saída passa pela metade do primeiro rolamento. Do outro lado inseriremos a outra parte do flange de saída que se encaixará exatamente entre os dois rolamentos.
Continuei colocando quatro porcas M4 nas ranhuras do eixo de saída. Essas porcas servirão para prender ou conectar coisas à saída do conjunto de engrenagens.
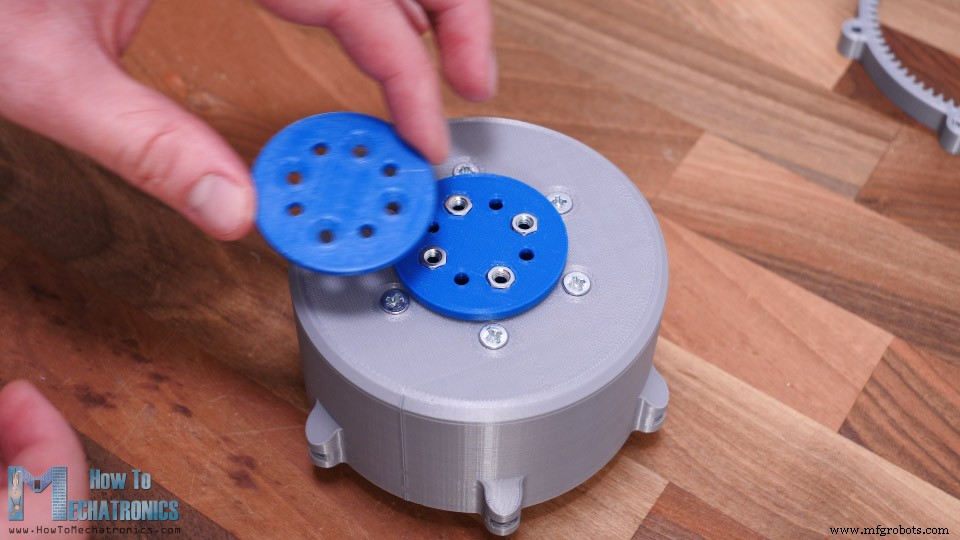
Para finalizar o eixo de saída, em cima deste coloquei outra peça que cobrirá as porcas, e usando 4 parafusos M4 com 40mm de comprimento posso finalmente prender as duas partes de saída juntas. Agora, o spline flexível e o eixo de saída podem livremente enquanto estão presos ao alojamento.
Ok, a seguir temos o spline circular que será fixado na carcaça junto com a tampa do conjunto de engrenagens e o suporte do motor. Mas antes de fazermos isso, precisamos montar o gerador de ondas. Aqui primeiro precisamos inserir duas porcas M3. Essas porcas servirão para fixar o gerador de ondas ao eixo do motor usando dois parafusos sem cabeça.
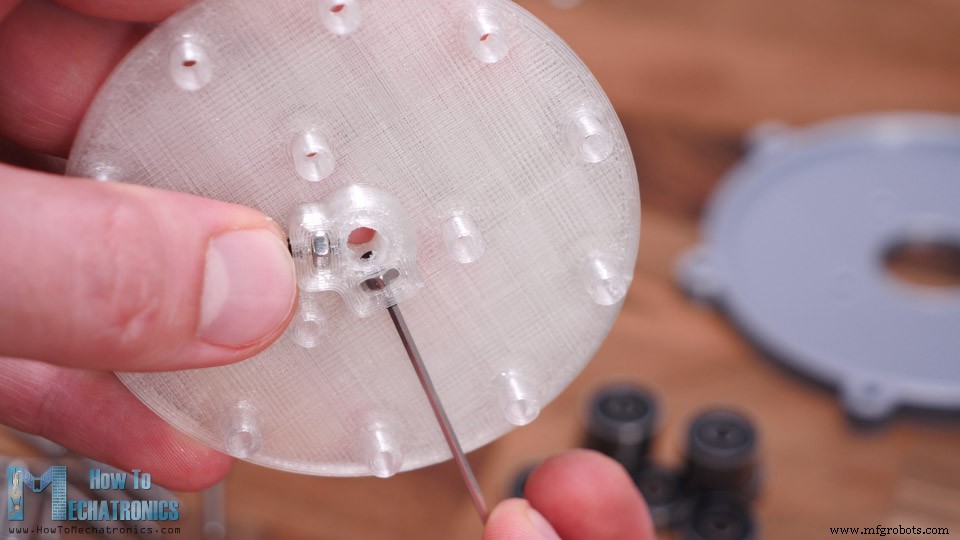
Em seguida, podemos começar a inserir os 10 rolamentos no lugar. Podemos notar aqui como os rolamentos se distanciam um pouco da parede com a pequena borda na parte inferior dos eixos. A outra parte do gerador de ondas também tem essas bordas para que os rolamentos não toquem na parede. Vamos fixar os rolamentos e, na verdade, todo o gerador de ondas, com parafusos M3 de 16 mm de comprimento e algumas porcas.
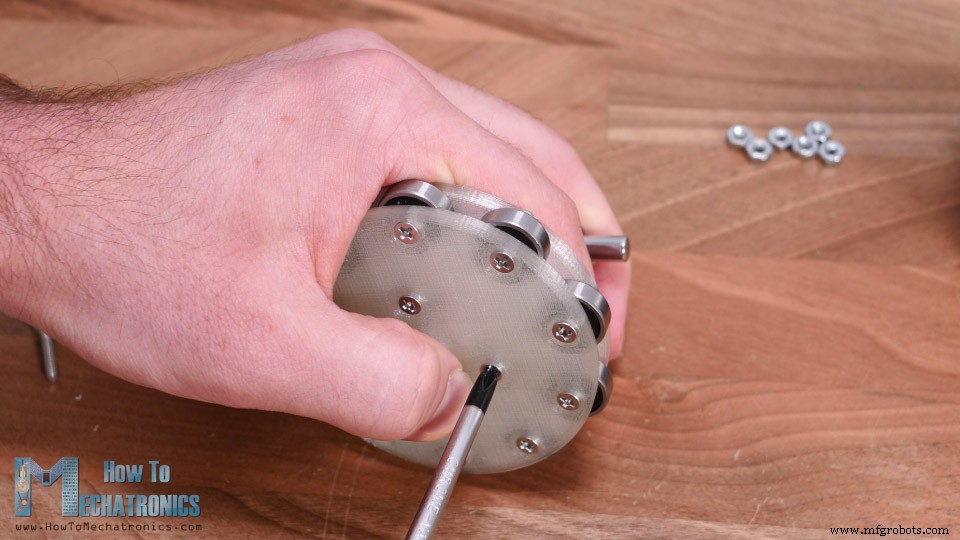
Em seguida, precisamos prender o gerador de ondas ao motor, mas antes de fazer isso, precisamos conectar o motor ao suporte do motor e à tampa do conjunto de engrenagens. O gerador de ondas deve estar a 2mm de distância da tampa do motor, então usei duas arruelas como guias ao inserir o gerador de ondas no lugar. Em seguida, basta apertar os parafusos sem cabeça que estão posicionados de forma que possam ser alcançados entre os rolamentos.
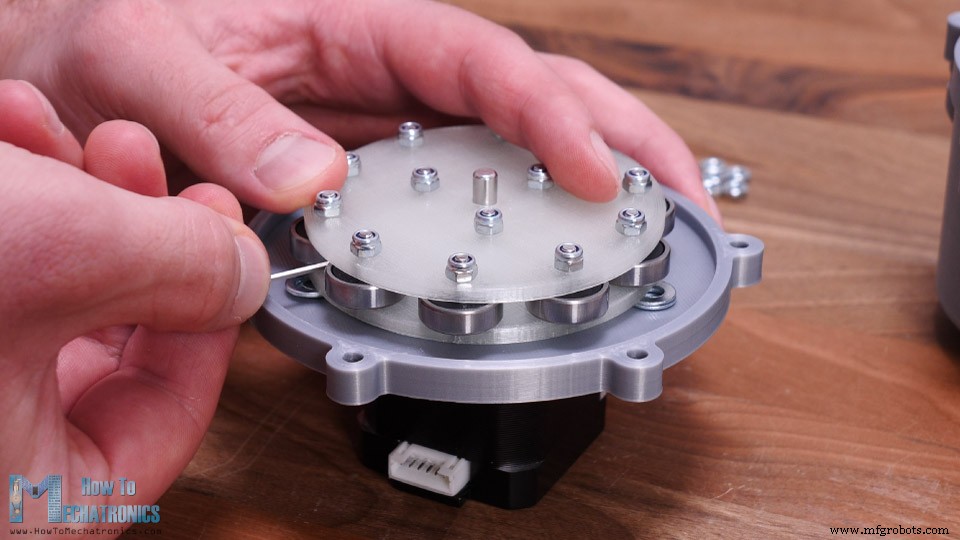
Finalmente, podemos inserir o gerador de ondas no flex spline e conectar tudo junto. Devemos primeiro ajustar o flex spline para ser mesclado com o spline circular de forma elíptica e, em seguida, inserir o gerador de ondas na mesma direção.
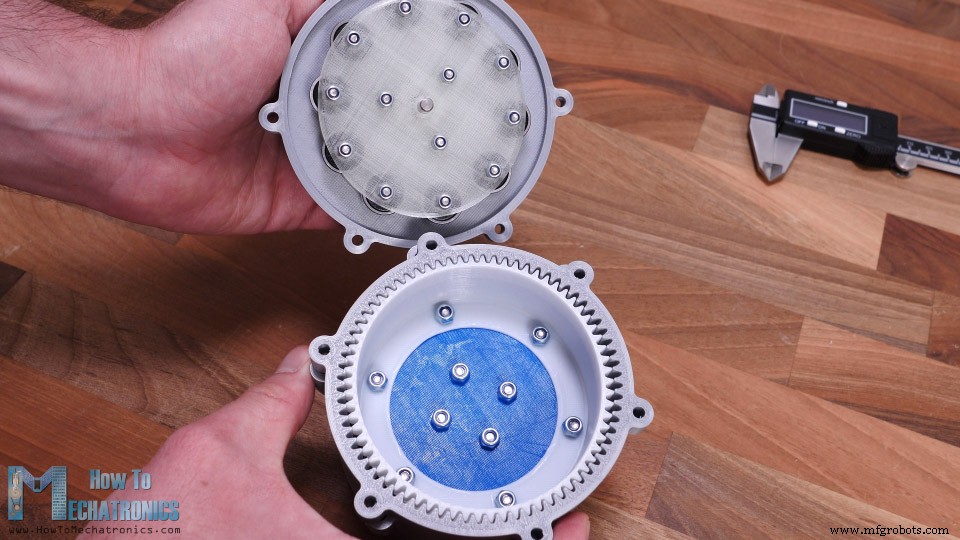
Para ser honesto, pode ser um pouco difícil fazer isso porque não temos controle sobre o spline flexível por causa da montagem do motor. Eu poderia ter projetado isso um pouco diferente, mas ainda acho que é bom o suficiente para fins de demonstração.
O que resta agora é inserir as porcas M4 nesses soquetes do alojamento e prender tanto a ranhura circular quanto o gerador de ondas ao alojamento.
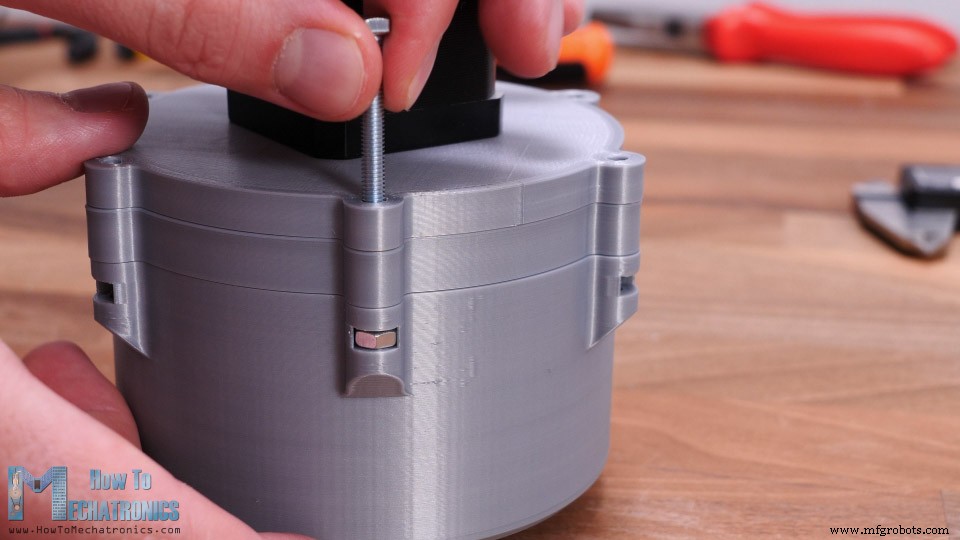
E é isso, nosso Strain Wave Gear ou Harmonic Drive está pronto. Mas quando terminei, pensei que completar o conjunto de engrenagens assim é meio chato porque não podemos ver nada além de um eixo de saída de rotação lenta. Lá, decidi substituir a tampa do conjunto de engrenagens impressa em 3D por uma de acrílico para que também possamos ver o que está acontecendo lá dentro.
Eu tinha uma placa de acrílico de 4 mm, então marquei o formato da tampa e, usando uma serra manual, cortei o formato grosseiramente.
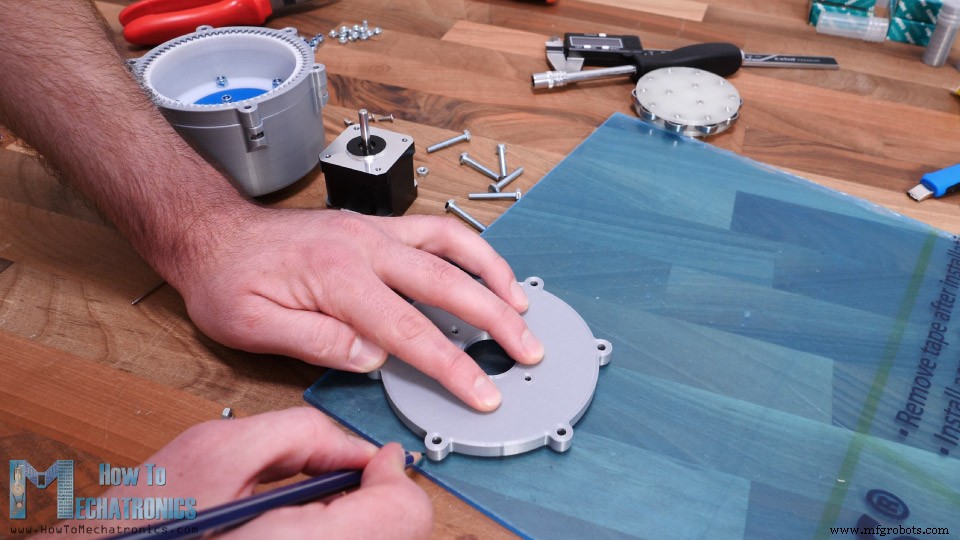
Em seguida, usando uma grosa, ajustei a forma do acrílico. Fiz os furos com uma broca de 3mm e o furo grande para o motor com uma broca Forstner de 25mm. A forma saiu bastante decente no final.
Eu remontei o motor e o gerador de ondas de volta como mostrado anteriormente. Podemos notar aqui que adicionei algumas porcas entre o acrílico e a carcaça para obter a distância adequada como a tampa tinha anteriormente.
Agora este conjunto de engrenagens parece muito mais legal.
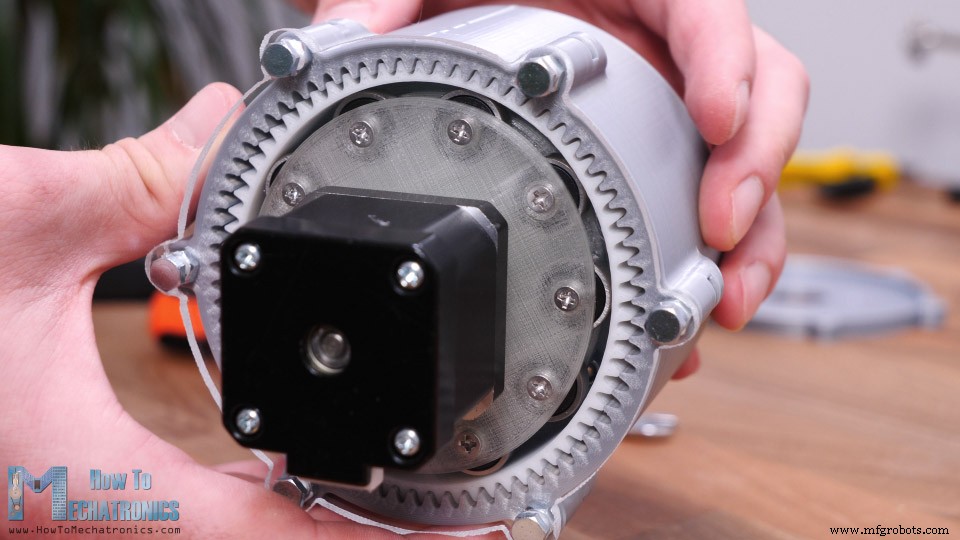
Conectei o motor de passo a um Arduino para poder controlar a velocidade e a direção do motor para melhor examinar e ver como o sistema funciona.
Então aqui está. Agora podemos ver como o Harmonic Drive funciona na vida real. Neste caso, o eixo de saída é 35 vezes mais lento que o eixo de entrada.
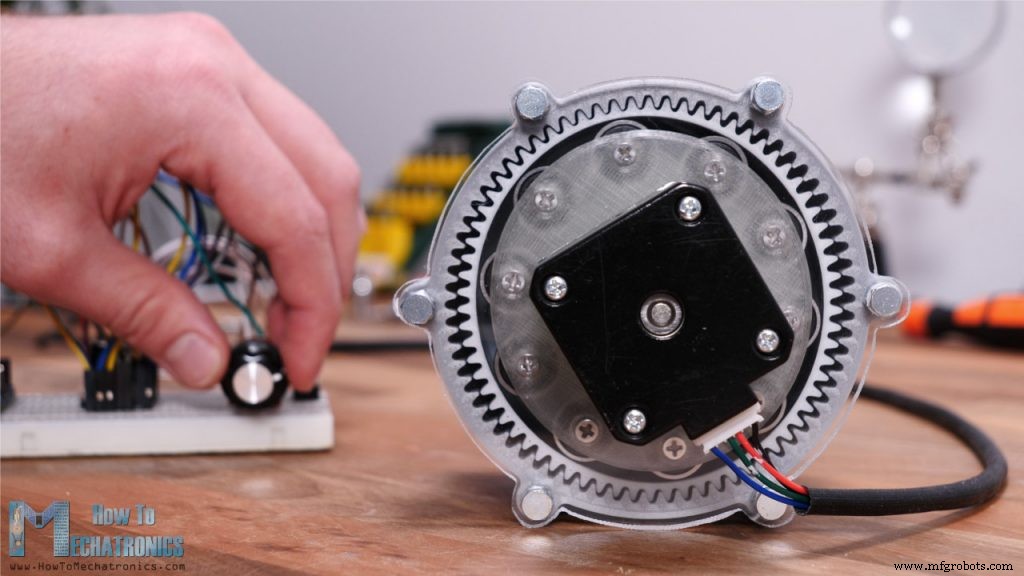
Aqui marquei um dente do flex spline com a cor vermelha para que possamos rastreá-lo melhor e ter noção do movimento do flex spline. Para ser honesto, é muito divertido ver como essa coisa funciona.
No entanto, notamos que o spline flexível às vezes se agita ou o movimento não é tão suave. Há várias razões para isso. Nessa configuração, o problema é que fiz a montagem do motor de acrílico manualmente, então o motor não fica montado perfeitamente no centro. Ao usar o suporte de motor impresso em 3D original, o movimento é muito mais suave.
Também podemos notar que nosso drive harmônico está longe de ter folga zero. Isso é por causa, como eu disse anteriormente, das limitações dessas impressoras 3D do tipo e quão boas elas podem imprimir. Não se trata apenas de quão bom o perfil do dente pode ser impresso, mas também de quão precisas são as dimensões gerais. Por exemplo, aqui usei uma fita isolante na parte interna do linho spline, que tem apenas 0,18mm de espessura, e com ela obtive melhores resultados.
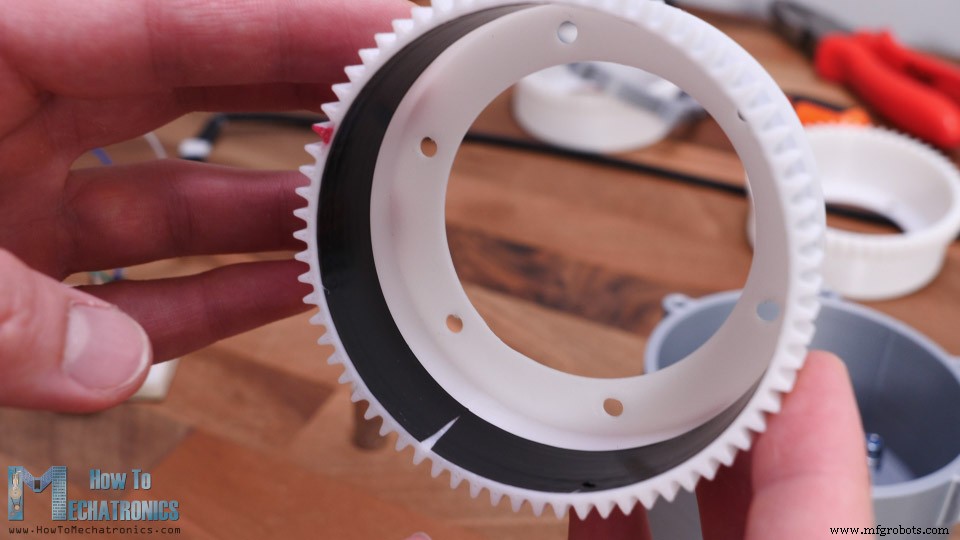
Então, eu acho, é tudo uma questão de testar e ajustar as impressões para obter melhores resultados. Também tentei imprimir as engrenagens com um módulo de 1,75, mas não obtive bons resultados.
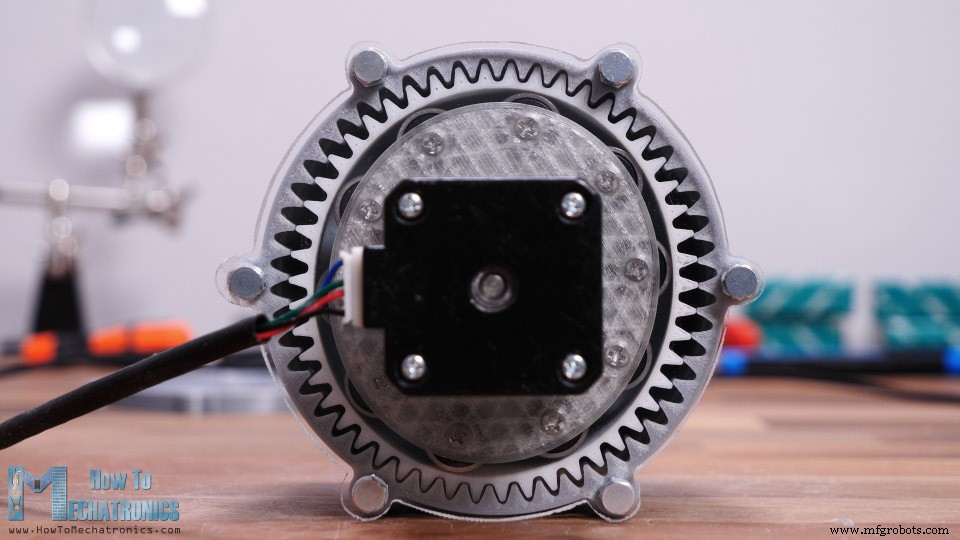
Na verdade, ao usar a tampa original impressa em 3D, o movimento era mais suave, mas ainda não era bom o suficiente.
Eu também tentei levantar alguns pesos. A uma distância de 25cm conseguiu levantar 1,25kg. Isso é um torque de cerca de 3Nm, que é pelo menos 10 vezes maior do que este motor de passo NEMA 17 é classificado.
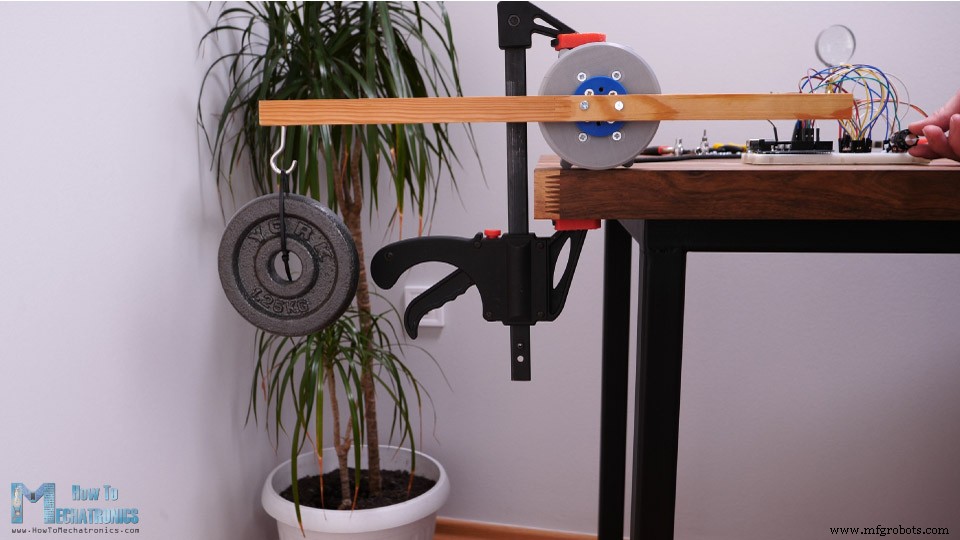
Então, isso é praticamente tudo para este vídeo. Gostaria apenas de acrescentar que este sistema de engrenagens pode ser facilmente projetado para ter eixo oco, o que é muito útil para aplicações robóticas. Então, eu posso usar Harmonic Drives em alguns dos meus vídeos futuros ao fazer alguns projetos de robôs.
Espero que tenham gostado deste vídeo e aprendido algo novo. Não se esqueça de se inscrever e para mais tutoriais e projetos, visite HowToMechatronics.com
Tecnologia industrial
- Sundance:Módulo de processador embutido VCS-1 para aplicações de robótica de precisão
- O que é impressão 3D? Princípio de funcionamento | Tipos | Aplicativos
- Ai! 5 dicas para evitar a tensão do tubo
- Uma visão geral para iniciantes:o que é fabricação de metal?
- ETSI se move para definir padrões para aplicativos de IoT em comunicações de emergência
- O que é uma fresadora e para que ela é usada?
- Para que são usados os atuadores pneumáticos? Tipos, aplicativos e usos
- Para que serve o Monel?
- Quais são as aplicações mais comuns para corrente CA?
- Aplicativos para serviços de lapidação plana de precisão