O que é Extrusão? Diferentes tipos de processos de extrusão?
O processo de extrusão é um dos tipos de processos de conformação em massa em que o metal de trabalho é forçado ou comprimido através de um orifício de matriz para obter uma determinada forma de seção transversal necessária.
Em palavras simples, a extrusão é um procedimento metalúrgico que envolve forçar o metal através de um furo de matriz sob pressão aumentada para comprimir sua seção transversal.
Desde a evolução do processo de extrusão, o mundo tornou-se dependente da extrusão para produzir barras, tubos e seções de qualquer formato oco ou sólido.
Como esta operação envolve empurrar ou puxar o tarugo através da matriz, as forças necessárias para extrudar o tarugo são bastante grandes. A extrusão a quente é o método mais comum porque a resistência à deformação do metal é baixa em altas temperaturas, enquanto a extrusão a frio geralmente é realizada apenas em metais macios.
Histórico:
Embora o conceito de extrusão nasça do processo de conformação. Está registrado que em 1797, um engenheiro chamado Joseph Bramah patenteou o processo de extrusão.
O teste envolveu o pré-aquecimento do metal e, em seguida, forçá-lo através de uma cavidade da matriz para fazer um tubo com o tarugo. Ele usou um êmbolo manual para forçar o metal.
Bramah então inventou o processo hidráulico após a invenção da Extrusão. Então, Thomas Burr usou a tecnologia de prensa hidráulica e técnica básica de extrusão combinando as tecnologias individuais para produzir um tubo (oco). Também foi patenteado no ano de 1820.
A tecnologia tornou-se então uma necessidade básica no mundo em crescimento, enquanto o processo não podia funcionar nos metais duros. No ano de 1894, Thomas Burr introduziu a extrusão com ligas de cobre e latão que trouxeram uma evolução na técnica de extrusão.
Desde a invenção da técnica de extrusão, o processo evoluiu para uma variedade de técnicas capazes de produzir uma ampla gama de produtos com estruturas complexas ao menor custo possível.
Classificação ou Tipos de Processo de Extrusão:
Diferentes tipos de processos de extrusão :
- Extrusão a quente
- Extrusão a frio
- Extrusão a quente
- Extrusão por fricção
- Microextrusão
- Extrusão direta
- Extrusão indireta
- Extrusão hidrostática e
- Extrusão de impacto Processo.
#1. Processo de extrusão a quente:
Neste processo de extrusão a quente, o tarugo é trabalhado acima de sua temperatura de recristalização. Este trabalho a quente permite evitar que a peça de trabalho endureça e faz com que o aríete a empurre facilmente através da matriz.
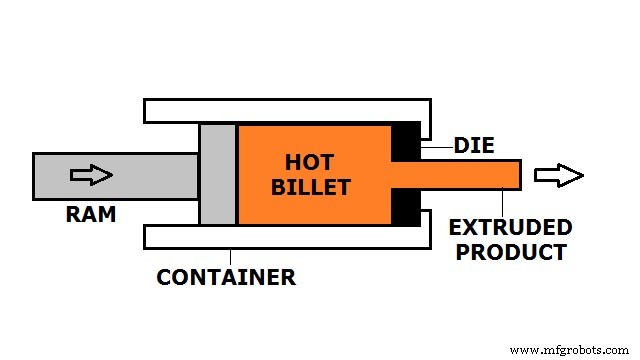
As extrusões a quente são geralmente realizadas em prensas hidráulicas horizontais. A pressão envolvida neste processo pode variar de 30 MPa a 700 MPa. Para manter a alta pressão intacta, a lubrificação é empregada. Óleo ou grafite é usado como lubrificante em extrusões de baixa temperatura e pó de vidro é usado para extrusões de alta temperatura.
O tarugo recebe um calor entre 0,5 Tm a 0,75 Tm para obter uma operação de qualidade.
As temperaturas de extrusão a quente de alguns materiais comumente usados estão listadas:
Material | Temperatura (˚C) |
Alumínio | 350 a 500 |
Cobre | 600 a 1100 |
Magnésio | 350 a 450 |
Níquel | 1.000 a 1.200 |
Aço | 1200 a 1300 |
Titânio | 700 a 1200 |
PVC | 180 |
Nilon | 290 |
Vantagens do processo de extrusão a quente:
- A deformação pode ser controlada conforme os requisitos.
- O tarugo não é submetido ao reforço devido ao endurecimento por trabalho.
- Forças menores são necessárias para pressionar.
- Materiais com rachaduras prematuras também podem ser trabalhados.
Desvantagens do processo de extrusão a quente:
- Acabamento de superfície ruim.
- A precisão dimensional é comprometida.
- Diminua a vida útil do contêiner.
- Possibilidade de oxidação da superfície.
#2. Extrusão a frio:
É o processo de moldar o metal golpeando-o com uma bala. Este golpe é realizado com um punção ou aríete em uma cavidade fechada. O aríete força o metal através da cavidade da matriz para transformar o tarugo sólido em uma forma sólida.
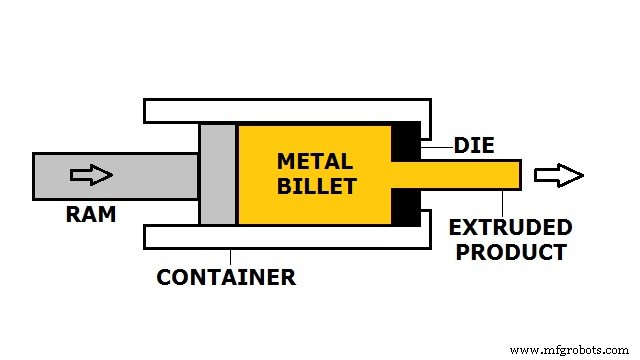
Neste processo, a peça de trabalho é submetida a deformação à temperatura ambiente ou ligeiramente acima da temperatura ambiente.
Para que as forças necessárias sejam muito altas, uma poderosa prensa hidráulica é usada nesta técnica. A pressão varia até 3000 MPa.
Vantagens:
- Sem oxidação.
- Melhor resistência do produto.
- Tolerâncias mais estreitas.
- Acabamento de superfície aprimorado.
- A dureza é melhorada.
Desvantagens:
- Forças mais altas são necessárias.
- É necessária mais energia para operar.
- Materiais não dúcteis não podem ser trabalhados.
- O endurecimento por deformação do material que está sendo extrudado é uma limitação.
#3. Processo de extrusão a quente:
A extrusão a quente é o processo de extrusão de um tarugo acima da temperatura ambiente e abaixo da temperatura de recristalização do material. Este processo é usado onde o material deve ser impedido de mudanças microestruturais que ocorrem durante o processo de extrusão.
Este processo é importante para alcançar o equilíbrio adequado de forças e ductilidade necessárias. A temperatura de qualquer metal usado nesta operação pode estar entre 424 graus Celsius a 975 graus Celsius.
Vantagens do processo morno:
- Força aprimorada.
- Melhorou a dureza do produto.
- Ausência de oxidação.
- Tolerâncias muito próximas podem ser alcançadas.
Desvantagens:
- Materiais não dúcteis não podem ser extrudados.
- Um equipamento de aquecimento é adicional.
#4. Extrusão por fricção:
Na técnica de extrusão por fricção, o tarugo e o recipiente são forçados a girar um contra o outro enquanto trabalham simultaneamente, o tarugo é empurrado através da cavidade da matriz para produzir o material desejado.
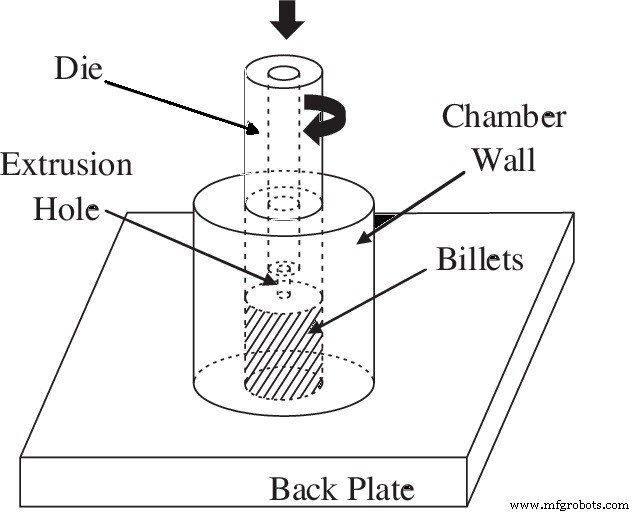
O processo é influenciado pela velocidade de rotação relativa entre o tarugo e a matriz. O movimento de rotação relativo da carga e da matriz tem uma implicação significativa no processo.
Primeiro, resulta na geração de um grande número de tensões de cisalhamento fazendo com que o tarugo se deforme plasticamente. Em segundo lugar, uma grande quantidade de calor é gerada durante o movimento relativo entre o tarugo e a matriz, portanto, nenhum pré-aquecimento é necessário tornando o processo mais eficiente.
Ele pode gerar fios, hastes, tubos e outras geometrias metálicas não circulares substancialmente consolidadas diretamente de uma variedade de cargas precursoras, como pó metálico, flocos, resíduos de usinagem (cavacos ou limalhas) ou tarugos sólidos.
Vantagens do processo de fricção:
- Não é necessário aquecimento.
- A geração de tensões de cisalhamento resulta em maior resistência à fadiga do produto.
- Qualquer tipo de material pode ser usado como tarugo, tornando esse processo econômico.
- Baixa entrada de energia.
- Melhor resistência à corrosão.
Desvantagens do atrito Processo:
- Oxidação esperada.
- Configuração inicial alta.
- Máquinas complexas.
#5. Processo de microextrusão:
Entende-se por sua nomenclatura que este processo trata da produção de produtos de faixa submilimétrica.
Semelhante à extrusão de nível macro, o tarugo aqui é forçado através do orifício da matriz para gerar a forma esperada no tarugo. A saída pode passar por um quadrado de 1 mm.
Microextrusão direta ou direta e inversa ou indireta são as duas técnicas mais fundamentais usadas nesta era para produzir microelementos.
A microextrusão para frente tem o aríete que impulsiona o tarugo para frente e o tarugo viajando na mesma direção, enquanto a microextrusão para trás tem o aríete e o tarugo se movendo em direções opostas.
A microextrusão é amplamente utilizada na produção de componentes para dispositivos médicos reabsorvíveis e implantados, desde stents biorreabsorvíveis até sistemas de liberação controlada de fármacos.
Enquanto, no campo mecânico, a aplicação pode ser amplamente observada na fabricação de pequenas engrenagens, minúsculos tubos, etc.
Vantagens do microprocesso:
- Seções transversais muito complexas podem ser feitas.
- Pequenos elementos podem ser produzidos.
- Tolerâncias geométricas aprimoradas.
Desvantagens :
- Criar uma pequena matriz e um contêiner para atender às nossas necessidades é um desafio.
- É necessário um trabalhador habilidoso.
#6. Extrusão direta ou direta:
No processo de extrusão direta, um tarugo de metal é primeiro colocado no recipiente. O recipiente tem um orifício de molde contornado. Um aríete é utilizado para conduzir o tarugo de metal através do orifício da matriz e o produto é fabricado.
Neste tipo, a direção do fluxo de metal é a mesma que a direção do movimento do aríete.
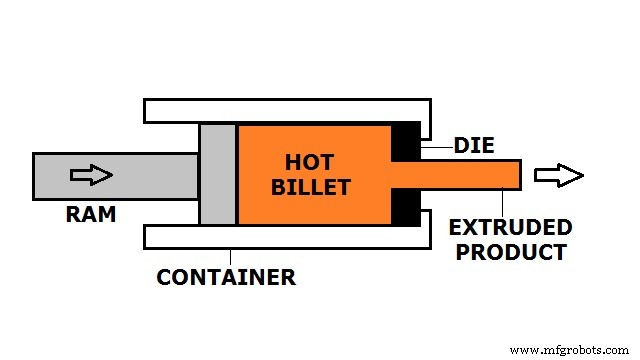
À medida que o tarugo é forçado a se mover em direção à abertura da matriz, uma grande quantidade de atrito é produzida entre a superfície do tarugo e as paredes do recipiente. A existência de atrito exige um aumento significativo na força do aríete, consumindo assim mais energia.
Nesse processo, a extrusão de metais frágeis, como tungstênio e ligas de titânio, é difícil porque eles são fraturados durante o processo. As forças de tração ao longo do processo induzem a formação rápida de microfissuras, resultando em fraturas.
A extrusão de metais frágeis como ligas de tungstênio e titânio é difícil porque eles fraturam durante o processo. As forças de tração induzem a formação rápida de microfissuras, resultando em fraturas.
Além disso, a presença de uma camada de óxido na superfície do tarugo intensifica o atrito. Essa camada de óxido tem o potencial de causar falhas no produto extrudado.
Para superar esse problema, um bloco fictício é colocado entre o aríete e o tarugo de trabalho para ajudar a mitigar o atrito.
Tubos, latas, copos, engrenagens de pequeno porte, eixos e outros produtos extrudados são exemplos.
Algumas partes do tarugo sempre permanecem no final de cada extrusão. É chamado de bumbum . Ele é removido do produto cortando-o imediatamente após a saída da matriz.
Vantagens do processo direto:
- O processo é capaz de extrudar peças mais longas.
- Propriedades mecânicas melhoradas do material.
- Bom acabamento de superfície.
- Extrusões a frio e a quente são possíveis.
- Capacidade de operar continuamente.
Desvantagens do processo direto:
- Metais frágeis não podem ser extrudados.
- Grande força e exigência de alta potência.
- Possibilidade de oxidação.
#7. Extrusão indireta ou inversa:
Neste processo de extrusão para trás, a matriz permanece estacionária, enquanto o tarugo e o recipiente se movem em combinação. A matriz é montada no aríete e não no recipiente.
O metal flui através do orifício da matriz no lado do aríete na direção oposta ao movimento do aríete conforme é comprimido pelo aríete.
Quando o tarugo é comprimido, o material passará entre o mandril e, portanto, a abertura da matriz.
Como não há movimento relativo entre o tarugo e o recipiente, nenhum atrito é registrado. Isso eleva o processo sobre o processo de extrusão direta, fazendo com que a força de aríete usada seja menor do que na extrusão direta.
Para manter a matriz estacionária, é usada uma “haste” maior que o comprimento do recipiente. A resistência da coluna da haste determina o comprimento final e máximo de extrusão.
Como o tarugo se move em combinação com o recipiente, todas as forças de atrito são facilmente eliminadas.
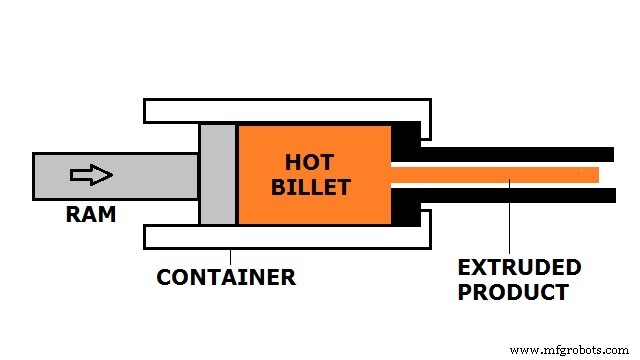
Vantagens dos processos indiretos:
- É necessária menos força de extrusão.
- Seções transversais menores podem ser extrudadas.
- Redução do atrito em 30%.
- Velocidade de operação aprimorada.
- Muito pouco desgaste é registrado.
- Falhas de extrusão ou zonas de anel de granulação grossa são menos prováveis de surgir porque o fluxo de metal é mais consistente.
Desvantagens do processo indireto.
- A seção transversal do material extrudado é limitada pelo tamanho da haste empregada.
- Possibilidade de tensões residuais após a extrusão.
- Impurezas e defeitos afetam o acabamento da superfície e tornam o produto compromissível.
#8. Extrusão hidrostática:
No processo de extrusão hidrostática, o tarugo é cercado por fluido dentro do recipiente, que é empurrado contra o tarugo pelo movimento para frente do aríete. Não há atrito dentro do recipiente devido ao fluido e há muito pouco atrito no orifício da matriz.
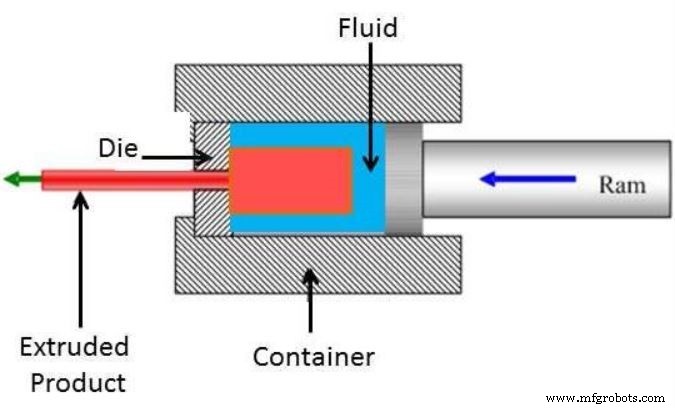
O tarugo não é perturbado ao encher o orifício do recipiente, pois é submetido a uma pressão hidrostática uniforme. Isso resulta com sucesso em um tarugo com uma enorme relação comprimento-diâmetro, mesmo bobinas de fio podem ser extrudadas sem falhas ou uma seção transversal irregular.
A principal diferença entre extrusões hidrostáticas e diretas é que não há contato direto entre o recipiente e o tarugo durante a extrusão hidrostática.
Trabalhar em altas temperaturas requer o uso de fluidos e processos especializados.
Quando um material é submetido à pressão hidrostática e não há atrito, sua ductilidade aumenta. Como resultado, esse método pode ser usado em metais que são muito frágeis para métodos típicos de extrusão.
Essa abordagem é usada em metais dúcteis e permite altas taxas de redução.
Vantagens:
- Os produtos extrudados têm um excelente polimento de superfície e são dimensionalmente precisos.
- Sem dúvida.
- Requisitos de força minimizados.
- Nenhum resíduo de tarugo permanece no processo.
- O fluxo de material é uniforme.
Desvantagens:
- Ao operar em altas temperaturas, fluidos e procedimentos especiais devem ser usados.
- Cada tarugo deve ser preparado e afunilado em uma extremidade antes do trabalho.
- É difícil conter o fluido.
#9. Extrusão de impacto:
A extrusão de impacto é outro método importante para a produção de perfis extrudados de metal. Em contraste com o processo de extrusão tradicional, que requer altas temperaturas para amolecer o material, a extrusão de impacto geralmente usa tarugos de metal frio. Esses tarugos são extrudados em alta pressão e eficiência.
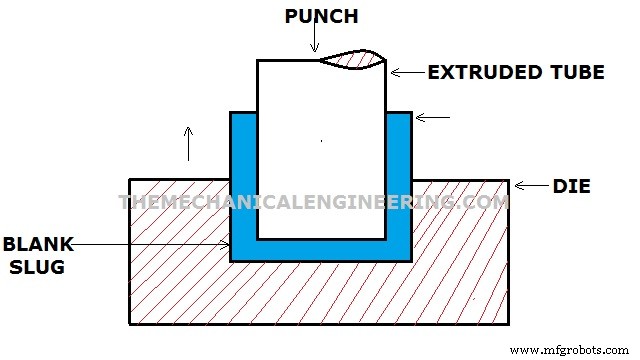
Um slug adequadamente lubrificado é colocado em uma cavidade da matriz e atingido com um punção em um único golpe durante uma operação de extrusão de impacto convencional. Isso faz com que o metal flua de volta ao redor do punção através de um espaço entre a matriz e o punção.
Esse processo funciona melhor com materiais mais macios, como chumbo, alumínio ou estanho.
Este processo é sempre realizado a frio. O processo de impacto para trás permite paredes muito finas. Faça tubos de pasta de dente ou caixas de bateria, por exemplo.
É realizado a uma taxa mais rápida e com cursos mais curtos. Em vez de exercer pressão, a pressão de impacto é empregada para extrudar o tarugo através da matriz. O impacto, por outro lado, pode ser realizado por extrusão de avanço ou retrocesso, ou uma mistura dos dois.
Vantagens:
- Grande redução no tamanho.
- Processo rápido. Tempo de usinagem reduzido em até 90%.
- Taxa de produção aumentada.
- Aumento da integridade da tolerância.
- Até 90% de economia de matéria-prima.
Desvantagens:
- É necessária uma força de compressão muito alta.
- O tamanho do boleto é uma limitação.
Fatores que afetam a força de extrusão:
Os seguintes fatores afetam a força de extrusão são:
- Temperatura de trabalho.
- Design do equipamento, horizontal ou vertical.
- Tipo de extrusão.
- A proporção de extrusão.
- Quantidade de deformação.
- Parâmetros de fricção.
Aplicação ou usos do processo de extrusão:
- É amplamente utilizado na produção de tubos e tubos ocos. E também é usado para produzir objetos de plástico.
- O processo de extrusão é usado para produzir molduras, portas, janelas, etc. nas indústrias automotivas.
- O metal Alumínio é usado em obras de estrutura em muitas indústrias.
Tecnologia industrial
- O que é Brochar? - Processo, Trabalho e Tipos
- O que é forjamento? - Definição, processo e tipos
- O que é extrusão? - Trabalho, tipos e aplicação
- Quais são os diferentes tipos de dobra de tubo?
- Quais são os diferentes tipos de trabalhadores de manutenção?
- Quais são os diferentes tipos de soldagem?
- Quais são os diferentes tipos de prototipagem?
- Quais são os 4 tipos de processo de fabricação?
- Diferentes tipos de processo de soldagem a arco elétrico
- Diferentes tipos de processos de conformação de chapas metálicas