Métodos de Inspeção de Superfície e Qualidade Interna de Fundidos
A inspeção de fundidos inclui principalmente inspeção dimensional, inspeção visual de aparência e superfície, análise de composição química e teste de propriedades mecânicas. Para peças fundidas com altas exigências, também são necessários ensaios não destrutivos. Por exemplo, técnicas de teste não destrutivo para inspeção de qualidade de fundidos de ferro dúctil incluem teste de líquido penetrante, teste de corrente parasita, teste de partículas magnéticas, teste radiográfico e teste ultrassônico.
Testes de defeitos superficiais e próximos à superfície de peças fundidas
Teste de líquido penetrante
O teste de líquido penetrante é usado para inspecionar vários defeitos de abertura na superfície das peças fundidas, como rachaduras na superfície, furos na superfície e outros defeitos difíceis de encontrar a olho nu.
O teste de penetrante comumente usado é o teste de corante, que é molhar ou pulverizar o penetrante de alta permeabilidade na superfície de fundição, infiltrar o penetrante nos defeitos de abertura, limpar rapidamente a camada de penetrante e depois pulverizar o revelador fácil de secar na fundição superfície. Após a sucção do penetrante que permanece nos defeitos de abertura, o revelador será tingido, de modo a refletir a forma, o tamanho e a distribuição dos defeitos.
Ressalta-se que quanto mais lisa a superfície a ser testada, melhor o efeito do teste de penetração. A superfície polida pelo moedor vem com a mais alta precisão de teste, e até rachaduras intergranulares podem ser detectadas.
Além do teste de corante, o teste de penetrante fluorescente também é um método de teste de líquido penetrante comumente usado. Ele precisa ser equipado com uma lâmpada ultravioleta para observação de irradiação, e a sensibilidade do teste é maior do que o teste de corante.
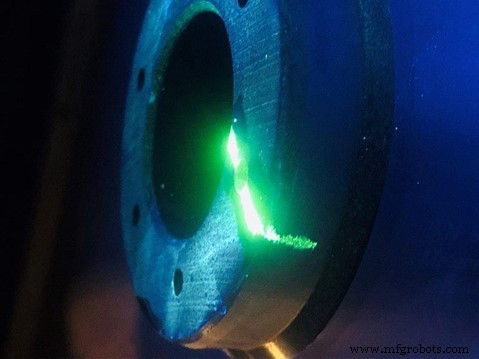
Teste de correntes parasitas
O teste de correntes parasitas é adequado para testar defeitos abaixo da superfície que geralmente não têm mais de 6 a 7 mm de profundidade. O teste de corrente parasita é dividido em dois tipos:o método de bobina do tipo colocado e o método de bobina do tipo passante.
Quando a peça de teste é colocada perto da bobina com corrente alternada, o campo magnético alternado que entra na peça de teste pode induzir a corrente parasita que flui na direção perpendicular ao campo magnético de excitação na peça de teste. A corrente parasita produzirá um campo magnético oposto à direção do campo magnético de excitação, o que reduzirá parcialmente o campo magnético original na bobina, resultando na alteração da impedância da bobina.
Se houver defeitos na superfície de fundição, as características elétricas da corrente parasita serão distorcidas, de modo a detectar a existência de defeitos. As principais desvantagens do teste de correntes parasitas são que ele não pode exibir diretamente o tamanho e a forma dos defeitos detectados. Geralmente, ele só pode determinar a posição da superfície e a profundidade dos defeitos. Além disso, sua sensibilidade ao teste de pequenos defeitos de abertura na superfície do fundido não é tão sensível quanto o teste de penetrante.
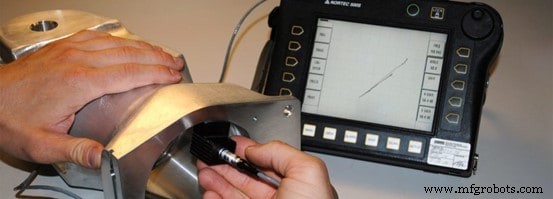
Teste de partículas magnéticas
O teste de partículas magnéticas é adequado para testar defeitos de superfície e defeitos vários milímetros abaixo da superfície. Requer equipamento de magnetização DC (ou AC) e partícula magnética (ou líquido de suspensão magnética) para teste.
O equipamento de magnetização é usado para gerar um campo magnético nas superfícies interna e externa do fundido, e partículas magnéticas ou líquido de suspensão magnética são usados para revelar defeitos. Quando um campo magnético é gerado dentro de uma determinada faixa do fundido, os defeitos na área magnetizada irão gerar um campo magnético de fuga. Quando a partícula magnética ou líquido em suspensão é aspergido, a partícula magnética é atraída, de modo que os defeitos podem ser exibidos.
Os defeitos revelados pelo teste de partículas magnéticas são basicamente aqueles que atravessam a linha de força magnética, mas os defeitos de tiras longas paralelas à linha de força magnética não podem ser exibidos. Portanto, é necessário mudar constantemente a direção de magnetização durante a operação para garantir que cada defeito na direção desconhecida possa ser testado.
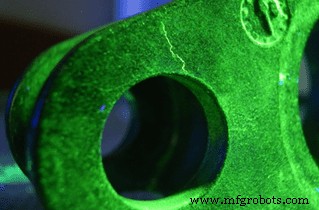
Testes de defeitos internos de peças fundidas
Para defeitos internos, os métodos de teste não destrutivos comumente usados são testes radiográficos e testes ultrassônicos. Entre eles, o efeito do teste radiográfico é o melhor. Ele pode obter uma imagem intuitiva refletindo o tipo, forma, tamanho e distribuição dos defeitos internos. No entanto, para fundidos grandes mais espessos, o teste ultrassônico é muito eficaz, o que pode medir com precisão a localização, tamanho equivalente e distribuição de defeitos internos.
Testes radiográficos
São necessários testes radiográficos, geralmente raios X ou raios γ como fonte de raios, o equipamento gerador de raios e outras instalações auxiliares. Quando a peça fundida é exposta ao campo de raios, a intensidade da radiação do raio será afetada pelos defeitos internos da peça fundida. A intensidade de radiação emitida através do gesso varia localmente com o tamanho e a natureza dos defeitos, formando uma imagem radiográfica dos defeitos, que é fotografada e gravada por filme radiográfico.
O método de registro por imagem de filme radiográfico é o método mais comumente usado, que é comumente referido como teste radiográfico. A imagem do defeito refletida pela radiografia é intuitiva, e a forma, tamanho, quantidade, posição do plano e faixa de distribuição dos defeitos podem ser apresentados.
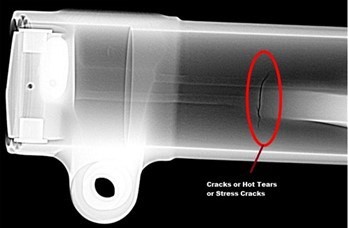
Testes ultrassônicos
O teste ultrassônico usa a propagação de feixes de som com energia sonora de alta frequência dentro da fundição para gerar reflexões quando atingem as superfícies internas ou defeitos. A magnitude da energia acústica refletida é uma função da diretividade e propriedades das superfícies internas ou defeitos e a impedância acústica de tal refletor. A energia acústica refletida de vários defeitos ou superfícies internas pode assim ser aplicada para detectar a localização dos defeitos, a espessura da parede ou a profundidade dos defeitos abaixo da superfície.
Como um método de teste não destrutivo amplamente utilizado, o teste ultrassônico traz as principais vantagens:alta sensibilidade de teste, que pode testar pequenas rachaduras; grande capacidade de penetração, que pode detectar peças fundidas de seção grossa. Suas principais limitações são:dificuldade de interpretar formas de onda de reflexão para defeitos descontínuos com dimensões de contorno complexas e baixa diretividade; estruturas internas indesejáveis, como tamanho de grão, microestrutura, porosidade, conteúdo de inclusão ou precipitados finamente dispersos, também dificultam a interpretação da forma de onda.
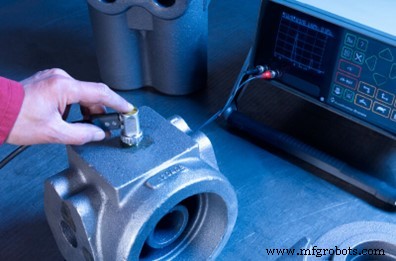
Tecnologia industrial
- Melhoria da qualidade e segurança na rastreabilidade do produto
- 4 razões pelas quais o teste e a inspeção de equipamentos são importantes
- O que é teste de qualidade de solda? - 10 defeitos comuns de solda
- Guia de métodos de teste de PCB
- Introdução ao END (ensaios não destrutivos) para peças fundidas
- Noções básicas de controle de qualidade e inspeção em usinagem CNC
- Esmerilhadeira de Superfície Rotativa e Qualidade de Processamento
- Teste de PCB:um foco em testes funcionais e em circuito
- Métodos especializados de moagem interna
- Informações:teste e inspeção de peças robóticas