Introdução à análise de falhas na fabricação
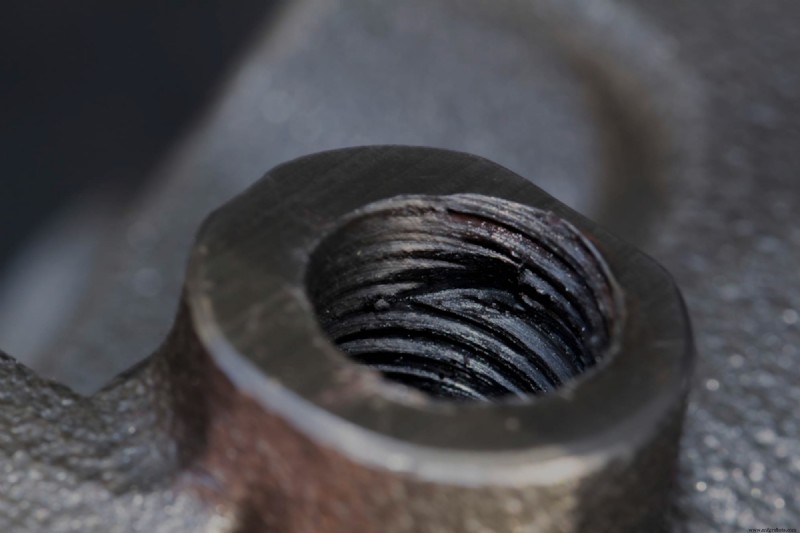
O desenvolvimento de produtos é um processo em constante evolução, e você pode não acertar na primeira tentativa. Não se preocupe – alguma quantidade disso é esperada. Se e quando uma peça falhar ou não funcionar conforme o esperado, você deseja descobrir o máximo possível sobre a falha para que possa aprender com os erros do passado e fazer produtos melhores. É aí que entra a análise de falhas.
O que é análise de falhas?
A análise de falhas é o processo de investigação de falhas do produto para solucionar problemas e reparar o problema subjacente. A análise de falhas pode ajudar a identificar os estágios ou operações específicos em que surgem diferentes tipos de problemas e fornecer uma estrutura para estabelecer processos internos para neutralizar essas oportunidades de erro. Isso ajuda a identificar discrepâncias e outras imprecisões desde o início, permitindo refinar os projetos de suas peças enquanto ainda é econômico fazê-lo.
Depois de identificar precisamente o que está causando problemas, a próxima etapa é tomar as medidas corretivas apropriadas para evitar que o problema reapareça durante os ciclos de produção subsequentes. Práticas robustas de análise de falhas não apenas ajudam a evitar falhas futuras do produto, mas também fornecem vários outros benefícios.
- A análise de falhas permite chegar à causa raiz do problema. Isso envolve a coleta de métricas de dados para determinar se o material, processo de fabricação, uso indevido ou outra coisa está com defeito.
- Ele minimiza os riscos potenciais para as equipes de produto e o ambiente de produção.
- Ajuda a melhorar os resultados financeiros, evitando contratempos dispendiosos causados por componentes de peças com falha. Interrupções, paralisações de produção e litígios podem aumentar significativamente seus custos. Os processos de análise de falhas ajudam a resolver essas preocupações, atendem aos padrões regulatórios e do setor e também determinam a responsabilidade por falhas.
Estratégias de análise de falhas na fabricação
O processo básico de análise de falhas é bastante direto – identifique e documente o problema, analise os dados e refine seus projetos com base nessas descobertas. No entanto, cada uma dessas etapas pode se tornar complicada quando traduzida em termos práticos. Vamos decompô-los com mais detalhes.
Quando ocorre um erro, as amostras de peças quebradas devem ser coletadas, em vez de descartadas - essa é a evidência que você documentará e analisará. É importante estabelecer diretrizes claras sobre quem receberá amostras de peças que quebram, não funcionam, estão envolvidas em eventos de segurança, etc. Da mesma forma, recursos suficientes, conhecimento técnico e equipamentos de teste precisam ser alocados. O uso de listas de verificação e soluções de logística também pode ajudar a minimizar o erro humano.
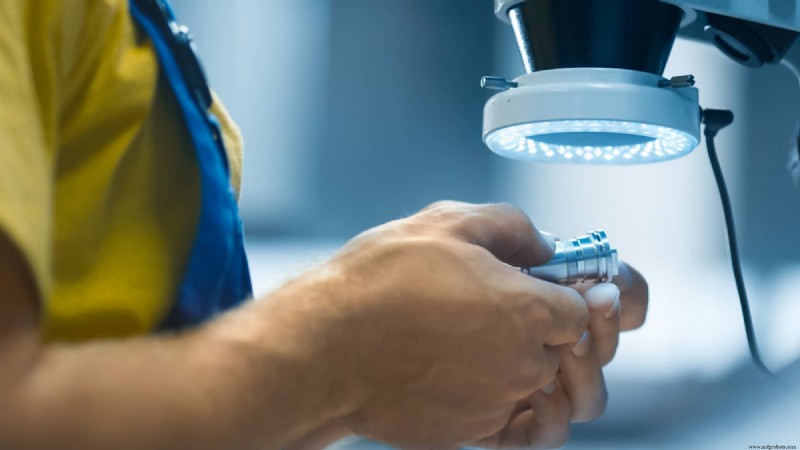
A próxima etapa é documentar os sintomas ou problemas de processo e criar critérios de teste que permitirão detectar o problema subjacente na compilação de desenvolvimento. Documentar os sintomas da falha muitas vezes pode servir como uma rodada leve de análise preliminar. Você pode organizar amostras de peças por tipo ou modo de falha (elétrica, mecânica etc.), se a peça ainda está funcional, mas tem capacidade reduzida, se o problema é cosmético ou se o sintoma é um problema comum normalmente causado por projetos de peças ou problemas de fabricação. A criação de um corpo de documentação também facilita a identificação de problemas repetidos em lotes e processos diferentes.
Conjunturas críticas, as etapas do processo que alteram a forma ou função de uma peça ou que a expõem a danos, devem ser monitoradas especialmente de perto. Também é útil que os membros da equipe descrevam os eventos que levaram à falha ou problema, incluindo condições ambientais como temperatura e umidade ou qualquer coisa fora do comum. Esse tipo de informação contextual pode ser essencial para solucionar problemas de confiabilidade e qualidade. Você também deve documentar o lote de fabricação do qual a peça com falha faz parte em caso de recall.
A próxima fase da análise de falha de causa raiz envolve isolar cada fator potencial para testar se ele está com falha. Depois que a causa subjacente for determinada, você poderá desenvolver e implementar um plano de solução de problemas eficaz. Documentar suas etapas e os resultados em um banco de dados também pode ser útil no futuro.
Aspectos a serem considerados ao realizar a análise de falhas de engenharia
Aqui estão algumas perguntas a serem feitas durante o processo de análise de falhas:
- Que tipo de falha é?
- Qual é a gravidade da falha?
- A falha pode ser repetida em partes futuras?
- Existem outros fatores contribuintes em potencial?
- Sua solução afetará outras equipes ou processos em andamento?
- Que medidas você pode tomar para evitar que o problema se repita?
As falhas do produto que causam sérios problemas de segurança são as mais urgentes para responder, e deve haver planos de contingência para esses cenários. Se a falha não estiver causando sérios problemas de segurança, você provavelmente terá mais tempo para elaborar um curso adequado de ação corretiva. Isso pode significar voltar à prancheta e prototipar novas peças para demonstrar como as melhorias sugeridas beneficiarão clientes e fabricantes.
Melhore suas etapas do processo de fabricação hoje mesmo
A análise de falhas é fundamental para entender o que deu errado durante a produção, o que causou os problemas e como evitar problemas no futuro. A análise de falhas ajuda a transformar erros e erros em oportunidades de aprendizado para que você possa refinar seus processos de desenvolvimento com base em experiências anteriores.
Embora as equipes de produto possam começar a investigar falhas por conta própria, elas precisarão de um parceiro de fabricação para realizar uma análise de falhas aprofundada. Fast Radius pode ajudar. Nossa equipe de engenheiros e projetistas é especializada em estabelecer processos de produção eficientes e documentação detalhada, além de garantir que cada trabalho seja realizado da forma mais eficiente possível. Entre em contato conosco hoje para saber mais sobre como podemos ajudar a tornar seus projetos uma realidade.
Tecnologia industrial
- Opções de análise
- Análise de falha de componente
- Análise de falha de componente (continuação)
- Vantagens da fabricação de aditivos
- Utilizando Análise de Causa Raiz de Falha na Fabricação
- Ferramenta de estimativa de análise RCM Blitz
- Electrivert apresenta a análise do sistema de fabricação
- Fabricação de PCB para 5G
- O que é Manufatura Inteligente?
- 6 maneiras de evitar a frustração da análise de falhas por corrosão