Certifique-se de que os projetos de moldagem por injeção estejam prontos para produção com esta lista de verificação
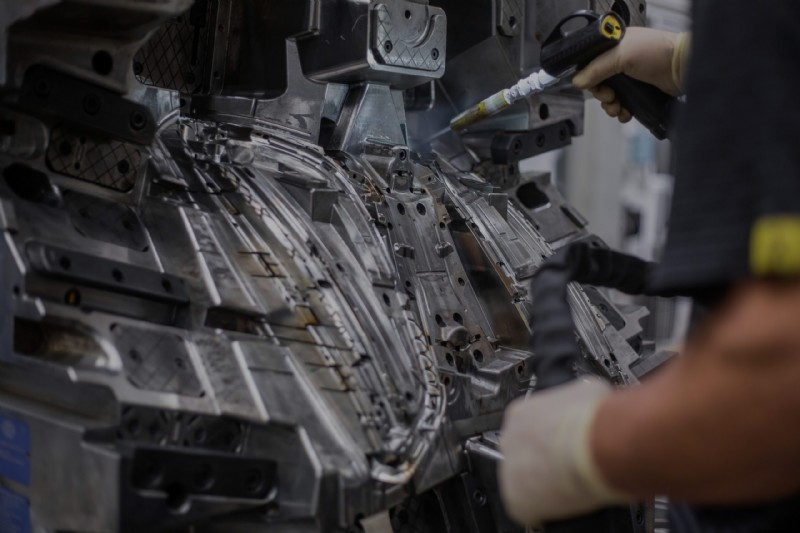
A moldagem por injeção permite a produção de alto volume de peças idênticas a um baixo preço por peça. O processo envolve a injeção de material fundido em moldes de metal duráveis por meio de um bico pressurizado, ejetando a peça assim que o material endurecer e repetindo. Uma ampla variedade de itens do dia a dia, incluindo garrafas de água, brinquedos de plástico e caixas de eletrônicos, são feitos com moldagem por injeção. Embora os termoplásticos e os termofixos sejam os materiais mais comuns usados na moldagem por injeção, o metal também pode ser moldado por injeção.
Ao fazer uma peça com moldagem por injeção, você precisa considerar uma série de variáveis que impactam na qualidade e funcionalidade do produto final. Há muitas maneiras pelas quais uma peça moldada por injeção pode falhar - incluindo linhas de fluxo, marcas de afundamento e empenamento - mas você pode evitar a maioria dos problemas seguindo alguns princípios-chave de design.
Aqui na Fast Radius, trabalhamos com os clientes em suas peças moldadas por injeção todos os dias. Os engenheiros muitas vezes vêm até nós com grandes projetos de peças que precisam ser ajustados antes que possam ser feitos de forma eficaz. Nossos especialistas em design para fabricação (DFM) avaliaram e ajustaram milhares de designs de peças e identificaram e compilaram os problemas mais comuns encontrados. Corrigir esses erros comuns em seu projeto pode evitar erros dispendiosos e economizar muito tempo nas revisões de projeto.
Antes de enviar seu projeto de peça para ser moldado por injeção, verifique-o em relação a esta lista de regras de projeto:
Use ângulos de inclinação apropriados
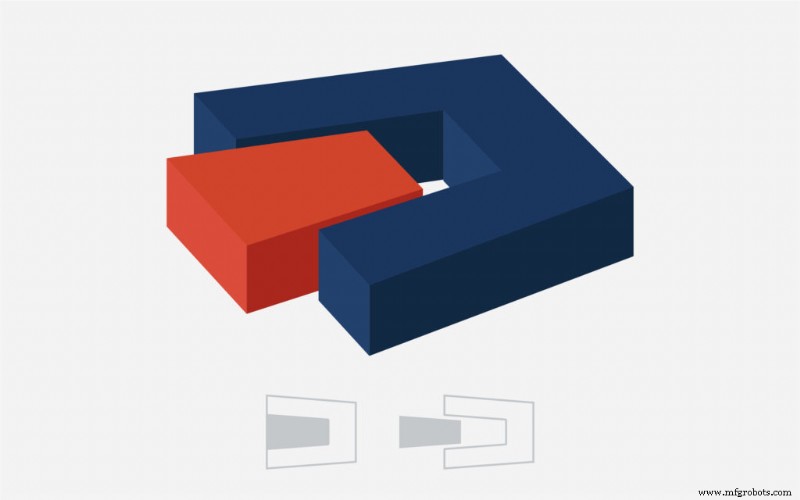
1,5-2 graus de calado normalmente é um mínimo seguro para a maioria das peças.
Os ângulos de inclinação referem-se à conicidade suave adicionada às superfícies de uma peça moldada por injeção que se alinham com a direção de tração, permitindo que a peça seja removida do molde sem ser danificada por atrito ou sucção.
O ângulo de inclinação necessário para uma peça depende de alguns fatores, incluindo a espessura da parede, a taxa de contração do material da peça, a profundidade do desenho e se a peça exigirá acabamento de superfície ou texturização durante a pós-produção. Embora o calado médio deva aumentar em 1 grau para cada polegada adicional de profundidade da peça, 1,5-2 graus de calado é normalmente um mínimo seguro para a maioria das peças.
Mantenha a espessura uniforme da parede, se possível
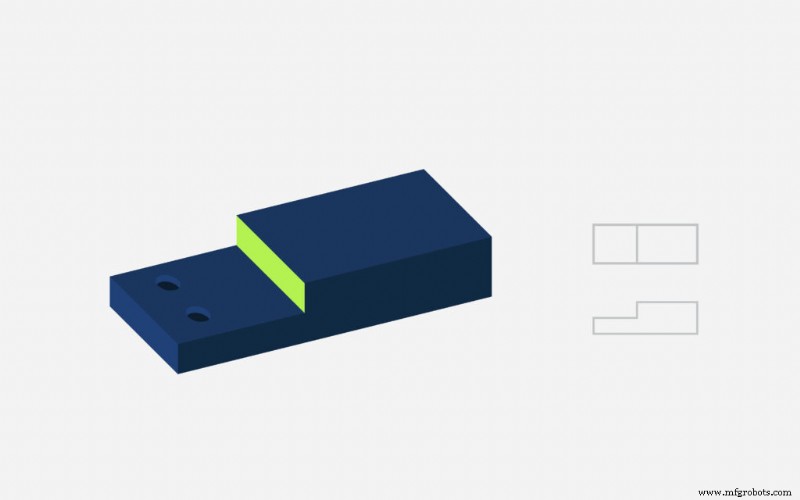
Se possível, os componentes moldados por injeção devem ter uma espessura de parede uniforme em toda a peça. Variações na espessura da parede podem fazer com que o material injetado esfrie em taxas diferentes, o que pode levar a marcas de afundamento, vazios e deformações.
Geralmente, espessuras de parede entre 1,2 mm e 3 mm são ideais (embora algumas variações possam ser esperadas dependendo do material). A espessura da parede quase sempre deve ficar abaixo de 5 mm porque paredes mais grossas aumentam os tempos de ciclo de produção e também podem afetar negativamente as propriedades mecânicas da peça.
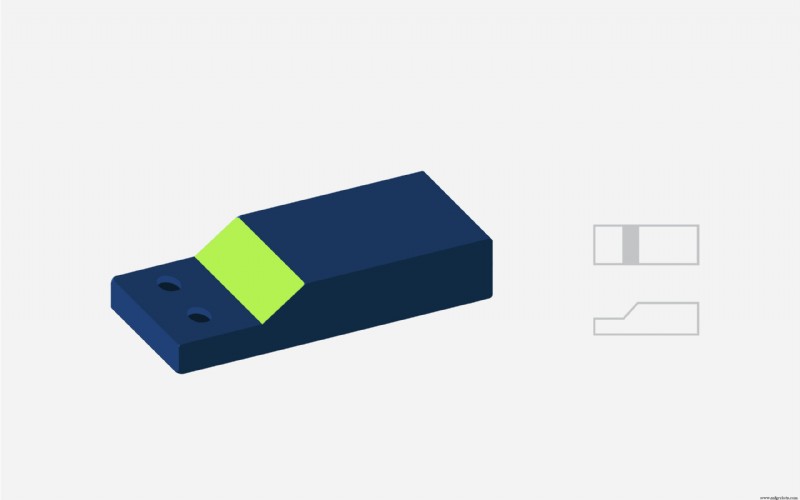
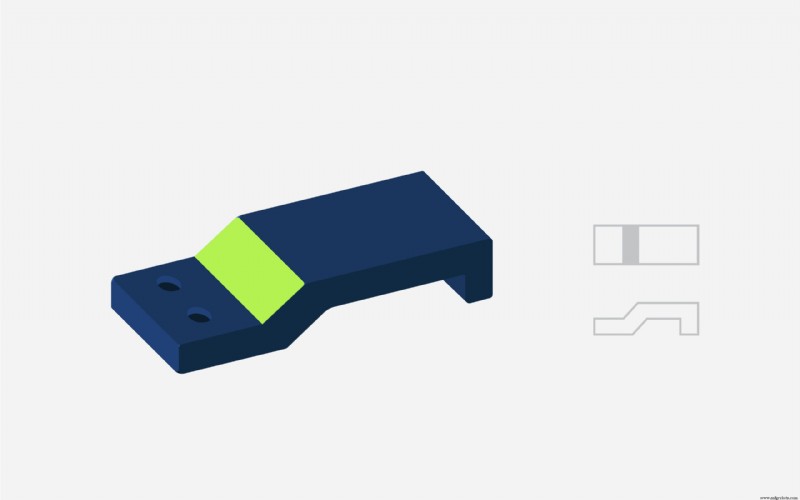
Se uma peça requer variações na espessura da parede, você deve fazer a transição entre as seções o mais gradual possível. Você pode fazer isso incorporando chanfros (cantos ou arestas inclinadas) ou filetes (cantos ou arestas arredondadas) no design da peça, que ajudam a garantir que a injeção de plástico derretido preencha totalmente o molde, resfrie completamente e uniformemente e evite deformações ou não -encolhimento uniforme.
Como regra geral, o comprimento da transição entre seções com diferentes espessuras de parede deve ser 3x a mudança na espessura da parede (por exemplo, se a espessura da parede diminuir em 1 mm, a transição deve ocorrer em 3 mm).
Evite cortes
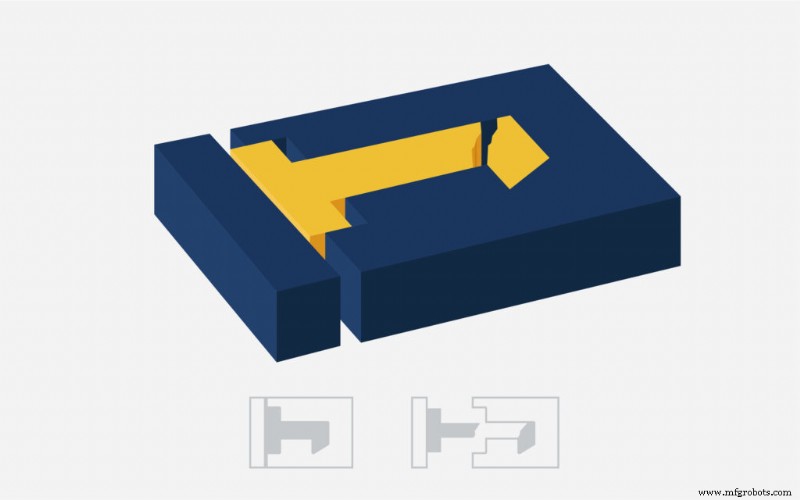
Os rebaixos são superfícies ou recursos rebaixados ou salientes - como roscas, ranhuras ou encaixes - que impedem que uma peça seja ejetada do molde com um único puxão unidirecional sem danos. É possível evitar rebaixos orientando recursos paralelamente à linha de desenho ou incorporando ações em seu projeto de molde.
Arredonde bordas e cantos vivos
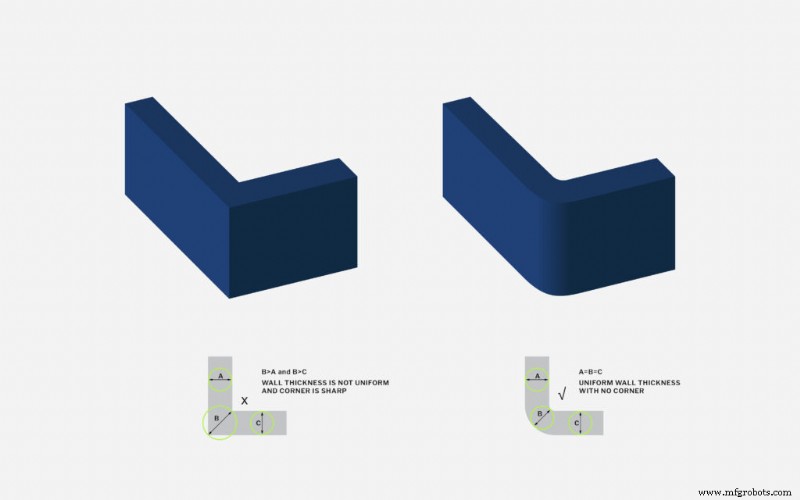
Sempre que possível, designers e engenheiros devem optar por recursos redondos em vez de arestas e cantos vivos. As bordas requerem pressão adicional para serem preenchidas, o que torna mais difícil para uma injeção fluir de forma eficiente e uniforme no molde. As arestas vivas também tendem a se agarrar ao molde durante a ejeção, aumentando o risco de danos e defeitos nas peças. Você pode evitar esses problemas com cantos internos e externos arredondados.
Os cantos internos, ou aqueles onde as paredes das peças encontram o piso, devem ter um raio de pelo menos 50% da espessura da parede adjacente. Os cantos externos, ou aqueles no topo das paredes das peças, devem ter um raio de 150% da parede adjacente para permitir que o plástico flua com mais eficiência e eficácia. Isso também ajuda a minimizar o estresse residual e rachaduras.
A base de todos os recursos verticais dentro de uma peça (como ressaltos, nervuras ou encaixes instantâneos) também deve ser arredondada. Os raios da saliência devem ser 25% da parede adjacente, com um raio mínimo de 0,015” (ou 0,381mm).
Situe as linhas de separação estrategicamente
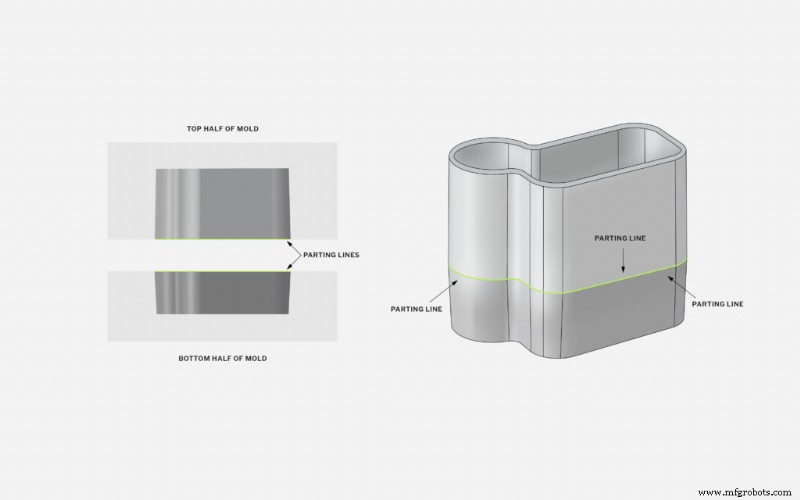
Uma marca física, conhecida como linha de partição, aparecerá onde as duas metades de um molde se encontram. Em muitos casos, as linhas divisórias podem ser facilmente vistas e sentidas, mas é mais do que uma questão estética. A colocação da linha de partição determina como o molde é aberto (e, portanto, a direção na qual você precisa adicionar inclinação aos recursos da peça) e pode influenciar tanto o custo das ferramentas do molde quanto qualquer pós-processamento necessário.
Muitas vezes, você pode melhorar a aparência e a funcionalidade de uma peça colocando a partição longa ao longo de uma aresta em vez de em uma superfície plana. Isso ajuda a esconder a costura e também reduz as chances de rebarbas (excesso de material ao redor de onde o molde se junta).
Considere o posicionamento do pino ejetor
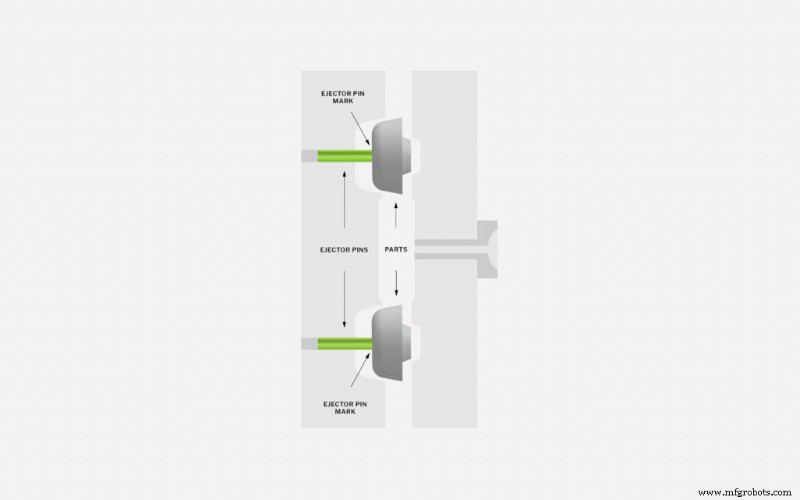
Para funcionar corretamente, os pinos ejetores requerem superfícies planas, ou almofadas, colocadas perpendicularmente à direção do movimento do pino. A colocação e o número de pinos devem ser informados pela forma da peça, ângulos de inclinação, textura da parede lateral e profundidade da parede – todos os quais influenciam como uma peça irá aderir às paredes do molde.
A escolha do material também deve ser levada em consideração na colocação ou tamanho dos pinos. Resinas mais pegajosas, por exemplo, tendem a exigir mais força para ejetar. Da mesma forma, plásticos mais macios provavelmente precisarão de um número maior de pinos ou pinos mais largos para distribuir efetivamente a força de ejeção e evitar danos à peça.
Otimize o tamanho das nervuras de suporte
As nervuras são frequentemente usadas para fortalecer paredes de peças em situações em que duas paredes de peças se encontram em um ângulo de 90 graus, ou onde o comprimento de uma seção específica é enfraquecido pela espessura da parede da seção.
É importante notar que nervuras mais grossas não significam necessariamente maior suporte - na verdade, nervuras muito grossas geralmente levam a marcas de afundamento. A espessura da base das nervuras de suporte deve ser no máximo dois terços da espessura da parede adjacente.
Esteja ciente da espessura da parede do molde
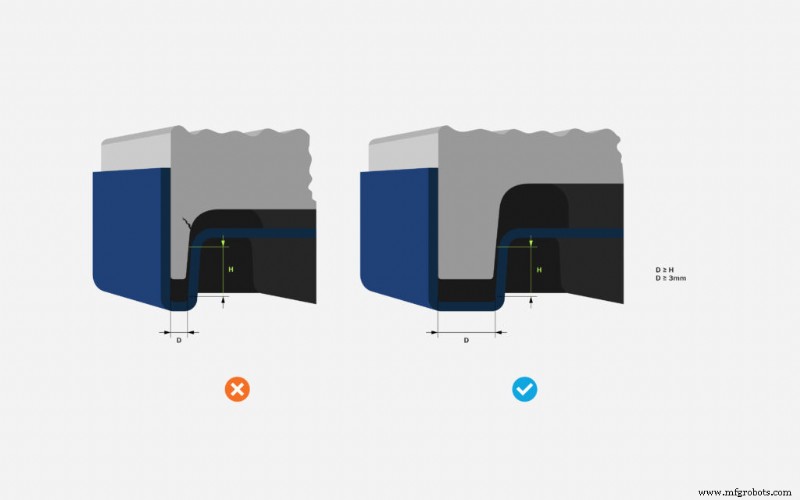
A espessura das paredes do molde é outra consideração importante – e que será determinada principalmente pelo espaço entre os recursos da peça. Certifique-se de que os recursos verticais, como nervuras e saliências, não estejam muito próximos uns dos outros, de paredes divisórias ou de áreas finas, pois isso complica o processo de resfriamento.
A espessura da parede do molde também pode afetar os custos de ferramentas. A maioria dos moldes de injeção são criados através de usinagem CNC e paredes mais finas de metal no molde são mais difíceis de usinar adequadamente. Paredes mais finas também resultam em ciclos de vida do molde mais curtos.
Embora a espessura mínima permitida da parede do molde seja ditada pelas qualidades físicas e mecânicas do material da peça, uma folga de 3 mm entre as características da peça é geralmente aceitável.
Projetar peças moldadas por injeção de forma eficiente e eficaz
Erros de design são caros. Recortar uma ferramenta para corrigir um erro de design pode atrasar as equipes de produto em semanas e custar milhares de dólares. Um bom parceiro de fabricação ajudará você a evitar revisões dispendiosas com o DFM, mas esse processo também aumenta sua linha do tempo. Verificar seu projeto quanto aos problemas neste guia antes de enviá-lo a um parceiro de fabricação ajudará você a obter peças melhores mais rapidamente.
Há muitas coisas que podem dar errado na moldagem por injeção, então você precisa encontrar um parceiro em quem possa confiar para acertar suas peças. Aqui na Fast Radius, estamos aqui para facilitar as coisas para você e investimos no sucesso do seu projeto. Entre em contato conosco hoje para começar seu próximo projeto de moldagem por injeção.
Para saber mais sobre moldagem por injeção - desde a seleção de materiais até as diferenças entre moldes de cavidade única e multicavidade e como aproveitamos o processo para fabricar máscaras faciais que combatem a disseminação do COVID-19 - visite o centro de aprendizado Fast Radius .
Pronto para fazer suas peças com Fast Radius?
Comece sua cotaçãoTecnologia industrial
- Moldagem por Injeção com Tecnologia PolyJet
- Robôs de seis eixos de interface com prensas de moldagem por injeção
- Como as principais empresas de moldagem por injeção geram mais oportunidades com marketing digital
- O que são defeitos de moldagem por injeção e como evitá-los:10 defeitos em peças plásticas
- Micromoldagem com poliuretanos
- O que é moldagem por injeção de reação
- Fundição x moldagem por injeção
- Moldagem por injeção versus moldagem por injeção de reação (RIM)
- Moldagem por fundição versus moldagem por injeção de reação
- Quais são os benefícios da moldagem por injeção de plástico?