Têmpera a Seco de Coca-Cola Quente
Extinção a Seco de Coca-Cola Quente
A têmpera a seco de coque (CDQ) é um processo de economia de energia usado durante a produção de coque na bateria do forno de coque. Uma planta de CDQ também é chamada de planta de resfriamento a seco de coque (CDCP). No processo tradicional CWQ (quenching úmido de coque), o coque incandescente que é empurrado do forno de coque é resfriado por pulverização de água no coque quente. A água utilizada para o resfriamento é vaporizada e liberada na atmosfera. Um problema com este sistema convencional é a perda de energia quando a energia térmica do coque incandescente é convertida em vapor que é vaporizado e liberado sem uso. Outra desvantagem é que o processo CWQ também produz pó de coque no ar e, portanto, o processo CWQ está associado a altas emissões de CO2 e perda de energia térmica.
Durante o processo CWQ para resfriamento do coque de forno, o calor sensível do coque quente é dissipado na atmosfera e é perdido. Além disso, há emissões no ar (0,5 tonelada de vapor por tonelada de coque, que é carregado com fenol, cianeto, sulfeto e poeira) e uma grande quantidade de água (cerca de 0,6 cum por tonelada de coque) é necessária para a têmpera úmida . Os contaminantes da água também são lançados no meio ambiente. A aba 1 mostra a comparação das propriedades típicas do coque produzido pelo processo CWQ e pelo processo CDQ.
Tab 1 Comparação das propriedades típicas do coque produzido pelos processos CWQ e CDQ | ||||
Sl. No. | Parâmetros | Unidades | Processo CWQ | processo de CDQ |
1 | Conteúdo de água | % | 2-5 | 0,1-0,3 |
2 | Conteúdo de cinzas | % | 11,35 | 11,39 |
3 | Componentes voláteis | % | 0,5 | 0,41 |
4 | Tamanho médio de partícula | mm | 65 | 55 |
5 | Taxa de brisa de coque (após corte em -15 mm) | % | 10 | 13 |
6 | Porosidade | % | 49 | 48 |
7 | Índice de bateria | % | 83,5 | 85 |
8 | Força do coque após reação (CSR) | % | 58 | 60 |
No processo CDQ, o coque incandescente é resfriado pelo gás que circula em um sistema fechado, evitando assim a liberação de pó de coque no ar. A energia térmica do coque incandescente, que é perdida no processo CWQ convencional, é coletada e reutilizada como vapor no sistema CDQ. Esta tecnologia utiliza menos combustível fóssil e resulta em menores emissões de CO2, contribuindo assim para a prevenção do aquecimento global. Atualmente, as usinas de CDQ têm despertado muita atenção do mundo devido à sua eficiente recuperação de energia e à característica de reduzir a poluição do meio ambiente. Eles estão sendo considerados como uma facilidade essencial para a contramedida contra problemas ambientais como o aquecimento global por CO2 e poluição do ar. Em um estudo, no qual o cálculo da economia de energia foi realizado com base na operação de um processo CDQ existente, foi demonstrado que 85% do calor residual gerado durante a carbonização do carvão está sendo recuperado pelo processo CDQ.
Histórico
A técnica CDQ foi introduzida na Suíça pelos irmãos Sulzer na década de 1920. Algumas décadas depois, uma concepção aprimorada do processo CDQ para operação contínua foi produzida pelo Instituto Giprokoks na Rússia. Após testes piloto e piloto/comercial, a primeira instalação de planta CDQ em escala real foi comissionada em 1965 na Cherepovets Iron and Steel Works na então URSS. Em 1978, cerca de 50 módulos CDCP de 56 toneladas por hora estavam em operação na então URSS. Nas últimas duas décadas, o processo CDQ foi gradualmente aceito, embora o processo CWQ ainda seja popular. No entanto, um grande número de plantas CDQ está operando em muitos países. A Fig 1 mostra um módulo de planta CDQ do projeto Giprokoks com capacidade de 56 toneladas por hora.
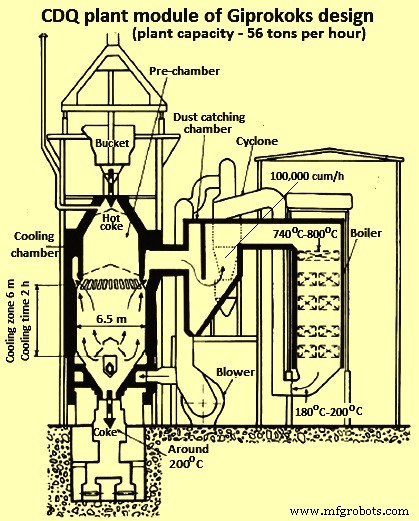
Fig 1 O módulo da planta CDQ do projeto Giprokoks tem uma capacidade de 56 toneladas por hora
O Japão comprou a licença da URSS em 1975 e três instalações japonesas foram comissionadas em 1976-77. Como a capacidade de produção de fornos de coque está aumentando nos últimos anos, a capacidade de CDQ também foi exigida para se adaptar a essa tendência de mudança. A fim de seguir esta tendência e satisfazer os vários requisitos dos clientes, o desenvolvimento de uma planta de CDQ de grande escala composta por câmara única (CDQ de câmara única) para a têmpera de uma grande quantidade de coque ocorreu no Japão. Para CDQ de câmara única, a disponibilidade é um fator muito importante porque não há instalações sobressalentes. Para obter alta disponibilidade, a operação estável é essencial. Para o operador inexperiente, no entanto, é difícil obter uma operação estável ajustando vários parâmetros. Nos últimos anos, uma nova tecnologia de automação para plantas CDQ também foi desenvolvida. O aumento progressivo da capacidade das câmaras CDQ desde 1975 é mostrado na Fig 2.
Fig 2 Aumento progressivo da capacidade da câmara CDCP desde 1975
processo CDQ
O coque quente depois de empurrado é trazido da bateria do forno de coque para a planta CDQ no balde de abertura inferior mantido no carro de têmpera. Esta caçamba é levantada na planta CDQ por um dispositivo de içamento/carregamento até o topo da câmara CDQ e o coque incandescente é descarregado na pré-câmara pelo dispositivo de carregamento. O coque quente (temperatura em torno de 1000°C a 1100°C) é resfriado na câmara pelo gás circulante. Na câmara o gás circulante se move em contracorrente ao movimento do coque, ou seja, o gás circulante se move para cima enquanto o coque se move para baixo pela gravidade.
O gás circulante em uma planta CDCP de operação contínua é um gás misto que consiste principalmente de nitrogênio (N2) juntamente com pequenas quantidades de dióxido de carbono (CO2), monóxido de carbono (CO) e hidrogênio (H2). A composição típica do gás circulante é N2 – 70% a 75%, CO2 – 10% a 15%, CO – 8% a 10% e H2 – 2% a 3%. O coque quente, enquanto desce na câmara, é resfriado a uma temperatura inferior a 200°C pelo gás circulante soprado da zona inferior da câmara de resfriamento e é descarregado da instalação de descarga na parte inferior da câmara. O tempo de passagem do coque pela câmara é em torno de 5 horas a 6 horas. Os parâmetros operacionais típicos para uma planta CDQ com capacidade de 56 toneladas/hora são dados na Tab 2.
Tab 2 Parâmetros típicos para planta CDQ com capacidade de 56 toneladas/hora | |||
Sl. No. | Parâmetro | Unidade | Valor |
1 | Capacidade | tonelada/hora | 56 |
2 | Temperatura de carga do coque | graus C | 1.000 – 1.050 |
3 | Temperatura de saída do coque | graus C | 200 |
4 | Temperatura de entrada do gás | graus C | 170 |
5 | Temperatura de saída de gás | graus C | 800 -850 |
6 | Geração de vapor | tonelada/hora | 25 |
7 | Pressão de vapor | kg/sq cm | 40 |
8 | Temperatura do vapor | graus C | 440 |
9 | Volume total de gás | N cm/hora | 84.000 |
O gás de circulação de alta temperatura (em torno de 800 ° C a 850 ° C) após um processo de troca de calor na câmara de resfriamento passa pelo coletor de poeira primário e é fornecido à caldeira. O gás de circulação após um processo de troca de calor na caldeira é resfriado a cerca de 180 graus C. O vapor gerado na caldeira é usado como vapor de processo de uso geral ou convertido em vapor de alta pressão superaquecido para a geração de energia elétrica energia através de um gerador de turbina.
O gás circulante passa pelo coletor de pó secundário para o soprador de circulação de gás, pelo qual sua pressão é aumentada, e sua composição é corrigida pela adição de gás N2 e, em seguida, o gás circulante é injetado no fundo da câmara CDQ. Se necessário, um sub-economizador é instalado para diminuir a temperatura do gás de circulação para cerca de 130 graus C, melhorando a eficiência de resfriamento da câmara de resfriamento.
Existem algumas facilidades auxiliares que incluem dispositivo de corte para cortar o coque da câmara, sistema de despoeiramento para remover o pó do gás inerte circulante e o coletor de pó secundário instalado antes do soprador de circulação. O fluxo de processo do processo CDQ é mostrado na Fig 3.
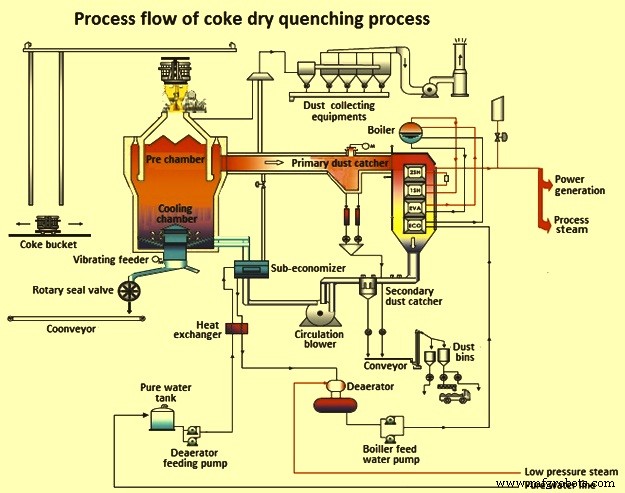
Fig 3 Fluxo do processo do CDQ
Benefícios do processo CDQ
O processo CDQ tem muitas vantagens em comparação com o processo CWQ convencional. As principais vantagens são descritas abaixo.
Utilização do calor sensível do coque quente – A energia elétrica pode ser gerada por têmpera a seco de coque sem o consumo de combustíveis fósseis. Isso leva à redução das emissões de CO2. Como exemplo (Fig. 4), o CDQ com capacidade de 200 toneladas por hora (t/h) pode gerar cerca de 36 MW de energia elétrica. Para a geração da mesma energia elétrica com uma caldeira a óleo pesado, são necessárias 12 t/h de óleo pesado e isso resulta em 36 t/h de emissão de CO2 para a atmosfera. Assim, uma planta CDQ oferece vantagens econômicas e ambientais. Por recuperar o calor sensível do coque, há economia líquida de energia. A economia de energia é de cerca de 0,25 Gcal/ton de coque. O processo CDQ permite assim a utilização eficaz da energia que é dispersa na atmosfera no processo CWQ.
Proteção do meio ambiente – No CDQ, não há fumaça branca que normalmente é vista saindo da torre de têmpera no caso do processo CWQ. Esta fumaça branca tem um alto teor de poeira. A ausência de fumaça branca no caso do processo CDQ é porque todos os processos são totalmente fechados. Como resultado, o ambiente de trabalho em torno dos equipamentos CDQ é melhorado.
Em geral, com o processo CWQ, é emitida grande quantidade de pó de coque (em torno de 300 g/t de coque a 400 g/t de coque) contido no vapor emitido para o meio ambiente. O processo recentemente desenvolvido de 'quenching estabilizador de coque (CSQ) reduz o volume de emissão de poeira. Mas o processo CDQ ainda é mais eficiente na prevenção da emissão de poeira. O volume de emissão de poeira do CDQ é inferior a 3 g/t de coque (Fig. 4). Este valor melhorou ainda mais com as melhorias contínuas do processo de CDQ que está ocorrendo.
O processo CDQ também é favorável ao meio ambiente no que diz respeito à poluição da água e à conservação da água. Isso ocorre porque nenhuma água é usada no processo CDQ, em comparação com o processo CWQ, onde o meio de têmpera é água.
Fig 4 Benefícios do processo CDQ
Contribuição do processo CDQ na melhoria da produtividade na BF – A melhoria da qualidade do coque produzido pelo processo CDQ leva à melhoria da produtividade no alto-forno (BF). No que se refere ao coque produzido pelo processo CDQ, possui duas excelentes características em relação à qualidade do coque produzido pelo processo CWQ. Essas características são (i) maior resistência mecânica do coque e (ii) baixíssimo teor de umidade no coque (quase zero). Esses recursos fornecem certos benefícios no BF que são descritos abaixo.
O consumo de combustível no BF é reduzido em alguns por cento, uma vez que a energia térmica extra não é necessária para a evaporação da umidade contida no coque. Contribui também para a redução de CO2 no BF, e uma melhoria da geração de energia no TRT (turbina de recuperação de pressão superior) devido ao aumento da temperatura no topo do BF.
Ao utilizar o coque temperado com processo CDQ, a permeabilidade no BF é melhorada devido à alta resistência do coque. A maior permeabilidade no BF melhora a eficiência da reação de redução no BF, e isso melhora a produtividade do metal quente do BF. BFs usando coque produzido pelo processo CDQ tem operação comparativamente mais estável. Além disso, à medida que a resistência do coque é aumentada, o interior do BF pode manter a permeabilidade suficiente e, portanto, taxas mais altas de injeção de carvão pulverizado podem ser alcançadas no BF.
Melhoria da qualidade do coque – A qualidade do coque é melhorada pelo processo CDQ em comparação com o coque produzido pelo processo CWQ. A qualidade do coque é mais estável devido ao baixo desvio padrão (geralmente em torno de 1,25%). Uma qualidade uniforme do coque auxilia na operação do BF. Isso ocorre porque o coque é resfriado gradativamente pelo gás circulante na câmara CDQ em vez de ter uma têmpera rápida pela pulverização de água com jatos de água no caso do processo CWQ. Além disso, a reação água-gás é evitada. A melhora esperada na resistência mecânica (índice de tambor) é em torno de 1,5% e a melhora na resistência do coque após a reação (CSR) é em torno de 2,5%. Esta melhoria ocorre porque o coque quente, que é resfriado gradualmente pelo gás circulante, está livre de poros superficiais e trincas internas que geralmente estão presentes no coque temperado a úmido.
Geralmente, observa-se que a taxa de aumento da resistência do coque é relativamente menor, caso haja alta porcentagem de carvão de coque de alta qualidade na mistura de carvão usada para carbonização do carvão. O maior uso de carvão de baixo coque na mistura de carvão proporciona uma vantagem de custo adicional pelo processo CDQ.
Processo de manufatura
- Gelo seco
- Cachorro-quente
- Balão de ar quente
- Cortina quente formando
- Temperabilidade do aço
- Uso de Nut Coke em um Alto Forno
- Têmpera a Seco de Coca-Cola Quente
- Apresentando as máquinas de venda automática de refeições quentes
- Uma introdução à bomba de água quente
- Processo de Laminação a Quente e Frio