Refratários para Forno Básico de Oxigênio
Refratários para Forno Básico de Oxigênio
O principal objetivo no desenvolvimento de refratários para fornos básicos de oxigênio (BOF) é obter uma vida útil do revestimento de desgaste para obter a máxima disponibilidade do BOF. A vida útil mais longa do revestimento não apenas resulta em menor custo de refratários, mas também permite maior produtividade por meio do aumento da disponibilidade do forno.
A seguir estão os requisitos básicos dos refratários do BOF.
- Resistência à fragmentação térmica
- Resistência à corrosão
- Resistência à abrasão
- Resistência à oxidação
- Módulo de ruptura a quente
O BOF é revestido normalmente com um forro permanente e acima dele há um forro de desgaste. A espessura do revestimento permanente pode variar de 100 mm a 120 mm e é feito de revestimento permanente cromo-magnesita que é dado em toda a altura do BOF.
Os refratários disponíveis para uso em revestimentos de desgaste de BOF variam de dolomita ou magnésia (MgO), cromo magnesita ou magnésio-cromo até os refratários avançados que são feitos com ligações de resina, metálicos, grafites e sinterizados e/ou magnésia fundida que pode ter uma pureza de 99%. Os tijolos são projetados com uma combinação de propriedades físicas críticas para suportar as altas temperaturas e as condições/ambientes que mudam rapidamente ao longo do ciclo de calor do BOF. Um equilíbrio de diferentes propriedades, como resistência a quente, resistência à oxidação e resistência à escória, é necessário dos refratários BOF para um bom desempenho.
Quando o processo BOF de fabricação de aço foi introduzido na década de 1950, os conversores foram revestidos com tijolos de dolomita de alcatrão e tijolos de dolomita queimados estabilizados. Esses refratários foram então substituídos por tijolos de dolomita queimados semi-estabilizados e tijolos de alcatrão e queimados feitos de clínquer de dolomita de magnésia sintética. Magnesita de cromo, ou refratários de cromo de magnésio foram usados para o revestimento de alguns BOFs. Tijolos de magnésia queimados de alta pureza também foram usados em alguns dos revestimentos BOF. Durante o final da década de 1970, tijolos de magnésia-carbono com resistência à corrosão e fragmentação foram desenvolvidos e rapidamente colocados em uso para o revestimento do BOF. Esses tijolos utilizam a resistência da magnésia à escória corrosiva de alta basicidade e a alta condutividade térmica e baixa molhabilidade do grafite (carbono). Hoje a prática de usar refratários de magnésia-carbono para o revestimento de BOFs tornou-se muito comum.
A estabilidade dos tijolos de magnésia – carbono pode ser aumentada prevenindo a oxidação do grafite e melhorando a resistência à corrosão do clínquer de magnésia. A oxidação do grafite é evitada pela adição de metais fáceis de oxidar, como alumínio e magnésio – alumínio, carbonetos, como carbeto de silício (SiC) e carboneto de boro (B4C), e boretos, como boreto de cálcio (CaB6). O uso de grafite de alta pureza também evita a oxidação. A resistência à corrosão da magnésia é melhorada aumentando o nível de pureza do clínquer de magnésia usando magnésia eletrofundida ou magnésia da água do mar. Também é melhorado otimizando a distribuição do tamanho das partículas de clínquer de magnésia. Tijolo de carbono de magnésia ao qual zircão (ZrSiO4) é adicionado para aliviar o estresse térmico em serviço também foi desenvolvido.
A magnésia moderna de alta pureza é produzida por processos bem controlados. As principais fontes de magnésia são salmouras, muitas vezes de poços profundos ou da água do mar. O hidróxido de magnésio, Mg(OH)2, é precipitado a partir dessas fontes por reação com dolomita calcinada ou calcário. A pasta de hidróxido de magnésio resultante é filtrada para aumentar seu teor de sólidos. A torta de filtro é então alimentada diretamente a um forno rotativo para produzir magnésia de grau refratário. Atualmente, a torta de filtro é calcinada a cerca de 900°C a 1000°C em vários fornos para converter o hidróxido de magnésio em magnésia ativa. Esta magnésia calcinada é então briquetada ou peletizada para queima em magnésia de grau refratário denso, geralmente em fornos de eixo a temperaturas de cerca de 2000 graus C. O produto final é magnésia sinterizada. A magnésia fundida é produzida pela fusão de magnésia de grau refratário ou outro precursor de magnésia em um forno elétrico a arco. A massa fundida é então removida do forno, resfriada e quebrada para uso na fabricação de refratários. As impurezas na magnésia são controladas pela composição da fonte original da magnésia (salmoura ou água do mar), pela composição da dolomita ou calcário calcinado e pelas técnicas de processamento. Em particular, as porcentagens e a proporção de CaO e SiO2 são efetivamente controladas, e o B2O3 é mantido em níveis muito baixos. A magnésia refratária de alto grau produzida é usada para a produção de refratários de magnésia.
Diferentes fatores são responsáveis pelo desgaste do revestimento BOF em diferentes zonas do BOF. Portanto, o revestimento zonal do BOF é praticado onde diferentes tipos de tijolos de carbono de magnésia ou outros tijolos são instalados em diferentes zonas do BOF para garantir o equilíbrio de desgaste e, através dele, é alcançada a extensão da vida útil do revestimento do BOF. . O revestimento zonal típico do BOF é mostrado na Fig 1.
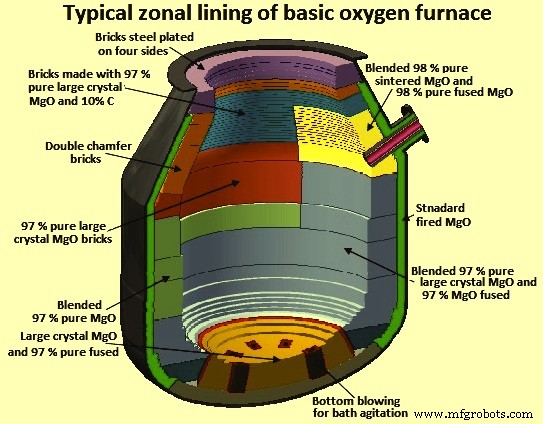
Fig 1 Revestimento zonal típico de um BOF
Para otimizar o projeto do revestimento de desgaste, é essencial desenvolver um revestimento balanceado, ou seja, um revestimento no qual diferentes qualidades e espessuras refratárias sejam atribuídas a várias zonas do revestimento do conversor com base em um estudo cuidadoso dos padrões de desgaste. Em um revestimento balanceado, os refratários são zoneados de tal forma que um determinado segmento de revestimento conhecido por receber menos desgaste recebe uma qualidade inferior ou menor espessura de refratário, enquanto refratários de maior resistência ao desgaste e geralmente de custos mais altos são reservados para aqueles segmentos do revestimento. forno que será submetido ao desgaste mais severo. As condições de desgaste e refratários propostos em diferentes zonas de BOF para o revestimento zonal são fornecidas na Tab 1 abaixo.
Guia 1 Condições de desgaste das zonas do conversor e refratários propostos | ||
Zona do conversor | Condições de desgaste | Refratários propostos |
Cone | 1) Atmosfera oxidante | 1) Magnésia de qualidade padrão – tijolos de carbono contendo antioxidantes |
2) Abuso mecânico | 2) Tijolos de magnésia colados com piche | |
3) Estresse termomecânico | 3) Tijolos de baixo carbono ligados a resina com antioxidantes | |
4) Alta temperatura | ||
Tronões | 1) Atmosfera oxidante | 1) Magnésia de qualidade premium – tijolos de carbono contendo antioxidantes |
2) Corrosão de escória | 2) Magnésia de qualidade premium – tijolos de carbono contendo MgO fundido e antioxidantes | |
3) Escória e erosão metálica | 3) Magnésia de alta resistência e qualidade premium – tijolos de carbono | |
Botão de carregamento | 1) Impacto mecânico | 1) Tijolos de magnésia queimado impregnados de piche |
2) Abrasão de sucata e metal quente | 2) Magnésia de alta resistência de qualidade padrão – tijolos de carbono contendo antioxidantes | |
3) Tijolos de magnésia com baixo teor de carbono de alta resistência contendo antioxidantes | ||
Toque no teclado | 1) Erosão de escória | 1) Magnésio de qualidade premium – tijolos de carbono contendo antioxidantes |
2) Alta temperatura | 2) Tijolos de magnésia de baixo carbono de alta resistência com aditivos metálicos | |
3) Erosão mecânica | 3) Magnésia de qualidade padrão – tijolos de carbono contendo antioxidantes | |
Slaglines de redução | 1) Corrosão de escória severa | 1) Magnésio de qualidade premium – tijolos de carbono contendo antioxidantes |
2) Alta temperatura | 2) Magnésia de qualidade premium – tijolos de carbono contendo magnésia fundida e antioxidantes | |
Inferior e Estádio (vasos com agitação inferior) | 1) Erosão por movimentação de metal, escória e gases | 1) Magnésia de qualidade padrão de alta resistência - tijolos de carbono contendo antioxidantes |
2) Esforços termomecânicos como resultado da expansão | 2) Magnésia – tijolos de carbono sem aditivos metálicos caracterizados por baixa expansão térmica e boa condutividade térmica | |
3) Tensões internas como resultado de gradientes térmicos entre as ventaneiras refrigeradas a gás e o revestimento circundante | 3) Tijolos de magnésia queimado impregnados de piche |
Com a grande variedade de qualidades de tijolos disponíveis, há uma grande variedade de custos dos refratários. O tijolo mais caro pode custar até seis vezes mais do que um tijolo convencional de dolomita colado com alcatrão. Com a atualização dos projetos de revestimento, mais refratários com custos mais altos são usados em um revestimento BOF atualmente. No entanto, o uso de refratários de alto custo tem que justificar a economia tecnológica geral da loja BOF.
Por exemplo, quando o custo de um revestimento é aumentado em 25% em uma oficina de BOF com média de 4.000 aquecimentos, a vida útil do revestimento precisará aumentar para 5.000 aquecimentos para que os custos de refratários sejam mantidos. No entanto, em oficinas onde a disponibilidade do forno é necessária para a produtividade, um menor aumento na vida útil do revestimento e um maior custo refratário podem ser justificados se a disponibilidade do forno for maior durante períodos de alta necessidade de produção.
À medida que os projetos de revestimento são atualizados para otimizar o desempenho e os custos, é importante conhecer os efeitos das variáveis operacionais no desgaste do revestimento. Com essas informações, a possibilidade de controlar os parâmetros que afetam negativamente o desgaste do revestimento e as compensações econômicas de aumentar os custos operacionais para prolongar a vida útil do revestimento podem ser melhor avaliadas. Em geral, as práticas que melhoram o controle do processo, como as sub-lanças, beneficiam a vida útil do revestimento. Além disso, a vida útil do revestimento é auxiliada pela carga de cal dolomítica para fornecer MgO de escória, minimizando os níveis de carga de espatoflúor, controlando adições de fluxo e práticas de sopro para produzir baixos níveis de FeO nas escórias. Essas práticas precisam ser otimizadas para produzir o desempenho de revestimento mais econômico.
Mesmo quando muitas condições de operação são melhoradas, os projetos de revestimento são otimizados para um desgaste equilibrado, e a melhor tecnologia de tijolos é utilizada, o desgaste não ocorre de maneira uniforme e, geralmente, as práticas de manutenção que envolvem o canhão de refratários e revestimento com escória são usadas para estender a vida de um forro.
Processo de manufatura
- O que é a fabricação de aço com oxigênio básico?
- 5 dicas básicas de segurança de rede para pequenas empresas
- Automação, Controle e Modelagem da Aciaria de Oxigênio Básico
- Revestimento refratário de um forno de oxigênio básico
- Papel do MgO na prevenção da corrosão do revestimento em fornos básicos de oxigênio
- Utilização de Metal Quente para Siderurgia em Forno a Arco Elétrico
- Sistema Básico de Recuperação e Limpeza de Gás de Forno de Oxigênio
- Química da Siderurgia por Forno Básico de Oxigênio
- 3 razões para a manutenção de dispositivos de detecção de gás
- Dicas básicas de manutenção para suas máquinas de corte e vinco