Ensaios Não Destrutivos de Aços
Ensaios não destrutivos de aços
Ensaios não destrutivos (END) de aços é um grupo de técnicas de análise usadas para avaliar as propriedades de materiais de aço, componentes ou soldas sem causar danos a eles. As técnicas de END são usadas para detectar e avaliar defeitos internos e superficiais (como imperfeições, descontinuidades e falhas, etc.) que podem causar falhas nas condições operacionais projetadas. Esses defeitos internos e superficiais podem ser as áreas de menor integridade em comparação com outras partes do material de aço ou podem consistir na presença de trincas, vazios e outras imperfeições. O END fornece resultados indiretos, mas válidos e, por definição, deixa o objeto de teste adequado ao uso pretendido.
Os termos exame não destrutivo (NDE), inspeção não destrutiva (NDI) e avaliação não destrutiva (NDE) também são usados para essas técnicas de teste. Como não há alteração permanente no material de aço sendo testado por técnicas de END, as técnicas de END são consideradas muito importantes para a inspeção do material. O NDT economiza dinheiro e tempo na avaliação do produto, solução de problemas e pesquisa.
As técnicas de END constituem um tipo de trabalho muito especializado que desempenha uma função crítica. Estas técnicas necessitam do serviço de técnicos altamente especializados e qualificados que utilizam equipamentos e métodos sofisticados para avaliar áreas do componente de aço que são difíceis ou impossíveis de examinar a olho nu.
As técnicas de END são usadas para detectar defeitos durante a fabricação e fabricação, bem como os defeitos desenvolvidos durante o serviço dos componentes de aço. No entanto, não é possível detectar todos os possíveis defeitos examinando um componente por END. Além disso, no END, não é o defeito que é detectado, mas o efeito resultante no material, como a modificação das propriedades físicas (atenuação ao ultra-som ou condutividade elétrica, etc.). As técnicas de END não fornecem informações diretas, mas indiretas que precisam ser interpretadas. Algumas técnicas de END são mais diretas e precisas do que outras.
Há uma variedade de técnicas de END que podem ser usadas para avaliar os materiais de aço, componentes ou soldas. Todas as técnicas de END compartilham vários elementos comuns que incluem o seguinte.
- Existe alguma fonte de energia de sondagem ou algum tipo de meio de sondagem.
- Há uma descontinuidade que deve causar uma mudança ou alteração do meio de sondagem.
- Existem alguns meios de detectar a alteração.
- Existem alguns meios de indicar a mudança.
- Existem alguns meios de observar e/ou registrar essa indicação para que uma interpretação possa ser feita.
A adequação de uma técnica de END para uma determinada aplicação é determinada considerando os elementos acima. A fonte da energia de sondagem ou meio de sondagem deve ser adequada para o objeto de teste e para detectar o defeito ou descontinuidade procurado. Se presente, um defeito ou descontinuidade deve ser capaz de de alguma forma modificar ou alterar o meio de apalpação. Uma vez alteradas, deve haver alguma maneira de detectar essas alterações. Essas mudanças no meio de sondagem pela descontinuidade devem formar alguma indicação ou ser registradas. Por fim, essa indicação precisa ser revisada para que possa ser interpretada e classificar a descontinuidade.
Várias técnicas de END foram desenvolvidas, cada uma com vantagens e limitações tornando-a mais ou menos apropriada para uma determinada aplicação. Com a variedade de técnicas de END disponíveis, é importante selecionar a técnica que fornece os resultados necessários. Uma combinação de diferentes técnicas de END também pode ser aplicada para garantir que o material ou componente seja adequado para uso.
Existem muitos métodos diferentes de END de materiais e componentes de aço. Os métodos de END mais comuns usados para a avaliação de materiais, componentes ou soldas de aço são (i) inspeção visual, (ii) inspeção por penetrante de corante, (iii) teste de partículas magnéticas, (iv) inspeção radiográfica, (v) teste ultrassônico, e (vi) teste de correntes parasitas.
Inspeção visual
A inspeção visual é a forma mais comum, primária, barata e mais antiga de exame END. Ele se baseia na detecção de imperfeições da superfície usando o olho, não requer nenhum equipamento de teste especial (exceto auxílios simples como lupa) e pode ser concluído de forma mais rápida e econômica. No entanto, devido à natureza subjetiva das inspeções visuais, a variabilidade dos resultados das inspeções é comum. Também não é possível detectar esses defeitos por inspeção visual que não são visíveis aos olhos. Os três requisitos básicos para a inspeção visual são (i) boa visão para poder ver a descontinuidade que está sendo procurada, (ii) boa iluminação, o tipo correto de luz é importante e (iii) experiência, para ser capaz de reconhecer a descontinuidade.
Inspeção de corante penetrante
No método de inspeção por penetrante de corante, um penetrante de corante é usado para detectar defeitos de superfície pelo “sangramento” de um meio penetrante contra um fundo contrastante. O corante penetrante é aplicado à superfície pré-limpa do material de aço a ser testado e deixado por um período prescrito (tempo de permanência), pois a ação capilar o atrai para quaisquer defeitos de superfície. O excesso de penetrante é então removido e um revelador é aplicado. O revelador reverte a ação capilar e extrai o penetrante da falha. As indicações resultantes revelam a presença da falha para que ela possa ser visualizada e os defeitos possam ser observados e avaliados pelo técnico. O método de inspeção de corante penetrante é mostrado na Fig 1.
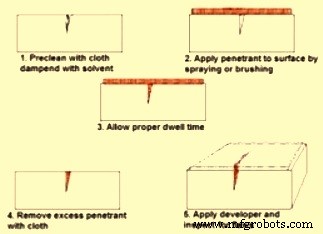
Fig 1 Inspeção de corante penetrante
Existem dois métodos pelos quais os penetrantes de corantes são classificados:(i) pelo tipo de indicação produzida e (ii) pelo método de remoção. Os resultados do teste de penetrante de corante também são exibidos de duas maneiras, visível e fluorescente. O tipo de penetrante visível produz uma linha vermelha em negrito ou indicação de tensão contra um fundo de revelador branco quando visto sob boas condições de luz branca. O penetrante fluorescente produz uma indicação verde fluorescente quando observado sob luz ultravioleta. Uma vez que o olho humano pode perceber mais prontamente uma indicação fluorescente do que uma indicação visível, o uso da inspeção por penetrante fluorescente é um teste mais sensível.
O segundo método de classificação do penetrante é baseado na maneira pela qual o excesso de penetrante é removido da superfície de teste. Os penetrantes são laváveis com água, removíveis com solvente ou pós-emulsionáveis. Os penetrantes laváveis com água contêm um emulsificante que permite que o penetrante seja enxaguado usando um spray de água de baixa pressão. Os penetrantes de remoção de solvente requerem um solvente para remover o excesso de penetrante da superfície de teste. Os penetrantes pós-emulsificáveis são removidos adicionando um emulsificante após o tempo de permanência do penetrante.
Esse processo é simples, versátil e econômico e pode ser aprimorado ainda mais com o uso de corantes de cores vivas ou fluorescentes. A única desvantagem é que só pode detectar defeitos de superfície.
Teste de partículas magnéticas
O teste de partículas magnéticas é usado para localizar descontinuidades ou defeitos superficiais e subsuperficiais leves em materiais ferromagnéticos como aços. Tais falhas presentes em uma peça magnetizada fazem com que um campo magnético (fluxo) saia da peça. Se partículas magnéticas forem aplicadas a esta superfície, elas serão mantidas no lugar pelo vazamento de fluxo para dar uma indicação visual. Embora vários métodos diferentes de testes de partículas magnéticas possam ser usados, todos eles se baseiam nesse mesmo princípio geral. É um processo muito simples e econômico.
Um teste de partículas magnéticas é realizado criando um campo magnético na peça a ser testada, aplicando as partículas magnéticas na superfície de teste. O processo é feito tanto em campo, usando garfos magnéticos portáteis, quanto em uma oficina, usando uma bancada magnética. A bancada é mais eficiente para grandes volumes de trabalho.
O teste de partículas magnéticas de aço geralmente é realizado usando um certo tipo de eletroímã. Um eletroímã baseia-se no princípio de que existe um campo magnético associado a qualquer condutor elétrico. Tanto a corrente alternada (AC) quanto a corrente contínua (DC) podem ser usadas para induzir um campo magnético. O campo magnético criado por AC devido ao “efeito de pele” é mais forte na superfície do objeto de teste. A CA também fornece maior mobilidade de partículas na superfície do objeto, permitindo que ela se mova livremente para localizar áreas de vazamento de fluxo, mesmo que a superfície do objeto possa ser irregular. DC induz campos magnéticos que têm maior poder de penetração e podem ser usados para detectar descontinuidades próximas à superfície.
Inspeção radiográfica
A inspeção radiográfica é uma técnica baseada no uso de radiação eletromagnética de comprimento de onda curto que passa através do material de aço. O método tradicional de radiografia é o processo de fazer um registro permanente em filme radiográfico de objetos de teste para detectar defeitos. Isso é feito expondo o objeto de teste a raios X gerados eletricamente ou raios gama de uma fonte de radiação. A radiação da fonte passa pelo objeto e é registrada em filme radiográfico. O filme é processado e o filme processado (radiografia) é visualizado por técnicos qualificados que são capazes de detectar defeitos e anomalias de acordo com os códigos e normas aplicáveis.
O princípio utilizado nesta técnica é que objetos de aço com áreas de espessura reduzida ou menor densidade de material permitem maior passagem das radiações e, portanto, absorvem menos radiação. A radiação, que atinge o filme após passar pelo material, forma uma imagem de sombra na radiografia. As áreas de baixa absorção (escória, vazios e porosidade) aparecem como áreas escuras na radiografia, enquanto as áreas de alta absorção (inclusões densas) aparecem como áreas claras na radiografia.
As descontinuidades de subsuperfície que são prontamente detectadas por este método são vazios, falhas, inclusões metálicas e não metálicas e rachaduras.
Avanços recentes na inspeção radiográfica é a radiografia digital, que não requer o uso de filmes caros e equipamentos de revelação.
Teste ultrassônico
O teste ultrassônico (UT) é um método de inspeção que utiliza ondas sonoras de alta frequência (ultrassom) que estão acima do alcance da audição humana, para medir propriedades geométricas e físicas em materiais de aço. Este método usa ondas sonoras geradas eletricamente para penetrar no objeto de aço e detectar defeitos. A reflexão sônica, a refração e a absorção são então exibidas e registradas em uma tela CRT (tubo de raios catódicos) para interpretação. Este processo requer significativamente mais habilidade e experiência para fornecer interpretações precisas.
Um dos principais benefícios do UT é que ele é considerado um teste verdadeiramente volumétrico. Ele é capaz de determinar não apenas o comprimento e a localização de uma falha, mas também fornece ao operador informações sobre o tipo de falha encontrada. A principal vantagem do UT é que ele requer acesso apenas a um lado do material que está sendo testado. Outra vantagem importante é que o UT detecta descontinuidades planares críticas, como rachaduras e fusão incompleta. UT é mais sensível a descontinuidades que se encontram perpendiculares ao feixe de som. Uma vez que uma variedade de ângulos de feixe pode ser usada, o UT pode detectar laminações, fusão incompleta e trincas que são orientadas de tal maneira que a detecção com testes radiográficos não seria possível. UT tem capacidade de penetração profunda.
Os avanços nos equipamentos de UT, incluindo phased array e tecnologia tridimensional (3D), aumentaram muito a flexibilidade e a adaptabilidade do UT para todos os tipos de trabalho END.
Teste de corrente parasita
No teste de correntes parasitas (ET), uma bobina transportando uma corrente CA é colocada perto da superfície da amostra ou ao redor da amostra. A corrente na bobina gera correntes parasitas circulantes na amostra perto da superfície e estas, por sua vez, afetam a corrente na bobina por indução mútua. Falhas e variações de material na amostra afetam a força das correntes parasitas. A presença de falhas é, portanto, medida por mudanças elétricas na bobina de excitação. Ambas as mudanças de tensão e fase podem ser medidas, mas alguns instrumentos mais simples medem apenas as mudanças de tensão.
A força das correntes parasitas produzidas depende da condutividade elétrica do corpo de prova, da permeabilidade magnética do corpo de prova, da distância entre o corpo de prova e a bobina, da frequência CA usada na bobina de excitação, das dimensões da bobina e do corpo de prova e da presença de falhas. Grande parte do sucesso dos testes ET depende da separação dos efeitos dessas variáveis. A maioria dos instrumentos de correntes parasitas requer calibração em um conjunto de amostras de teste e a sensibilidade à falha pode ser muito alta.
A técnica de teste de correntes parasitas é usada para detecção de trincas, medições de espessura de material, medições de espessura de revestimento e medições de condutividade para identificação de material, detecção de dano térmico, determinação de profundidade de caixa, desgaste de sela, pitting, rachadura transversal, protuberâncias por congelamento, rachaduras, amassados, tratamento térmico monitoramento, classificação rápida de pequenos componentes para defeitos, variação de tamanho ou variação de material.
A corrente parasita é uma ferramenta útil para detectar danos por corrosão e outros danos que causam afinamento do material nas paredes da tubulação, como trocadores de calor e tubos de caldeiras. O método de correntes parasitas é muito bom para defeitos superficiais e próximos à superfície, é sensível a pequenas rachaduras e outros defeitos e requer muito pouca preparação de peças. É limitado ao uso em materiais condutores, com a superfície acessível à sonda.
Processo de manufatura
- Técnicas de polarização (JFET)
- Técnicas de polarização (IGFET)
- O que são técnicas de teste:tipos, vantagens e desvantagens
- Carlos presidirá o Comitê ASTM de Testes Não Destrutivos
- O que é teste destrutivo e quais são suas aplicações
- O que é teste não destrutivo (NDT) e como ele é usado
- O que é Ensaio Não Destrutivo (END)?- Métodos
- 16 técnicas de ferraria
- Introdução ao END (ensaios não destrutivos) para peças fundidas
- Diferentes maneiras de testar um alternador