Analises falhas
Análise de falhas
Falhas de componentes e montagens de equipamentos ou estruturas na indústria podem causar perda de vida, paradas não programadas, aumento dos custos de manutenção e reparo e disputas judiciais prejudiciais.
Para evitar a recorrência futura do problema causado pelas falhas, é essencial realizar uma investigação em cada falha. A realização de uma investigação de falha é conhecida como análise de falha.
A análise de falhas é um processo de coleta e análise de dados e é realizado para determinar as causas ou fatores que levaram à perda indesejada de funcionalidade ou falhas de componentes e conjuntos de equipamentos ou estruturas. É um processo multinível que inclui investigação física. O escopo normal de uma análise de falha é encontrar o mecanismo de falha e a causa mais provável da falha. O termo mecanismo de falha é normalmente descrito como o processo metalúrgico, químico, mecânico ou tribológico que leva a um modo de falha particular.
As falhas dos componentes e montagens do equipamento, ou estruturas, ocorrem como resultado de algum tipo de erro que causa um elo fraco na cadeia do processo contínuo de engenharia, projeto, fabricação e operação. A causa de uma falha pode ser qualquer um ou mais dos seguintes.
- Falha no projeto
- Defeitos no material
- Deficiências durante o processamento e fabricação
- Defeitos de montagem ou instalação
- Condições de serviço fora do projeto ou não intencionais
- Deficiências na manutenção (negligência e procedimentos etc.)
- Operação inadequada
As principais etapas durante a realização de uma análise de falha são fornecidas na Fig 1.
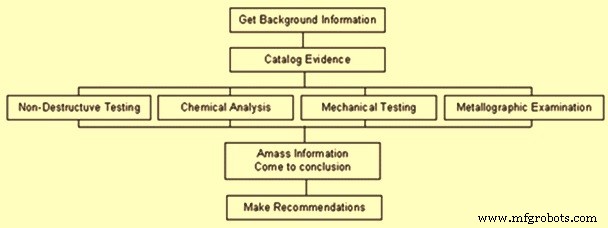
Fig 1 Principais etapas na análise de falhas
O princípio principal de uma análise de falha é preservar a evidência e as informações necessárias da peça ou montagem em questão na condição como recebida e a mesma é capturada antes que qualquer coisa seja feita para alterar sua condição. Além disso, durante a análise de falhas, é necessário realizar testes de natureza menos destrutiva para mais destrutiva.
A análise de falhas começa com a coleta de informações referentes ao histórico do componente envolvido na falha, como (i) processo envolvido, (ii) aplicação, (iii) tipo de material, suas especificações, formato, dimensões e técnica de processamento, (iv) parâmetros de projeto, (v) condições de serviço, (vi) histórico de manutenção, (vii) sequência de eventos que antecedem a falha, (viii) frequência de falha e se é de natureza localizada, etc.
A inspeção do local da falha é uma etapa muito importante que auxilia na análise da falha. Um exame completo da condição do componente com falha no local da falha pode fornecer muitas informações. Durante a inspeção do local, é necessário prestar atenção a características como localização de rachaduras, características de fratura, perfurações, depósitos, afinamento de paredes, flacidez e peças destacadas etc. Além disso, sempre que possível, é necessário obter o máximo de informações possível de testemunhas oculares sobre quaisquer condições anormais anteriores à falha. Em alguns casos, a inspeção visual do componente com falha pode revelar informações que não podem ser obtidas de outra forma.
Durante a inspeção visual é importante fotografar a máquina e arredores, a peça com falha e a peça de acoplamento. A documentação fotográfica do componente defeituoso é sempre necessária para referência futura e inspeção adicional após deixar o local. É importante fotografar todos os recursos do componente com falha.
A definição clara do problema é uma parte essencial de uma análise de falhas. A profundidade das informações obtidas, a inspeção do local, bem como a habilidade e julgamento da pessoa que realiza a análise de falhas ajudam a definir claramente o problema. Por exemplo, o problema pode ser definido como metalúrgico, mecânico ou ambiental ou uma combinação de dois ou mais deles. Além disso, por meio de discussões com o pessoal envolvido no local e por meio de inspeção visual, a pessoa que realiza a análise de falhas pode restringir as várias possibilidades. Além disso, a falha pode se assemelhar a um caso anterior de falha.
Com base na provável causa da falha conforme o problema definido durante a inspeção do local, um programa experimental é desenvolvido para determinar a causa da falha. A natureza e o número de experimentos selecionados devem ser tais que levem à identificação da causa do fracasso. As amostras necessárias para realizar os experimentos selecionados devem ser cuidadosamente desenhadas de forma que representem o máximo possível todos os recursos do componente com falha. Depósitos ou peças destacadas do componente podem fornecer informações valiosas. Sempre que possível, amostras retiradas das seções de som, bem como amostras nunca utilizadas em serviço, também devem ser coletadas para fins comparativos.
As ferramentas de investigação usadas em estudos de análise de falhas são geralmente de dois tipos:(i) ferramentas que podem ser usadas no local e (ii) ferramentas de laboratório.
A verificação do material em relação à especificação é um componente importante da análise de falhas. Análise química e análise de macroestrutura, bem como microestrutura é realizada para este propósito. Também são realizados testes mecânicos caso haja material suficiente disponível para determinar a resistência à tração, resistência ao impacto, etc., para avaliar as propriedades do componente com falha. Em muitos casos, são realizados testes de dureza superficial e microdureza para avaliar a resistência mecânica. Esses testes são realizados no componente com falha para descobrir a conformidade dos resultados com as especificações
Análise de tensão, mecânica de fratura e análise de falha de corrosão são atividades muito valiosas em investigações de análise de falha. Essas análises fornecem informações à pessoa que investiga a falha se o material utilizado foi a escolha certa para atender aos requisitos de sua aplicação.
A partir do conhecimento das condições de serviço, como cargas ou pressões aplicadas, geometria e tamanho do componente, é possível calcular as tensões principais desenvolvidas na peça. A comparação da tensão principal máxima com a resistência do material usado na aplicação fornece informações importantes para a pessoa que investiga a falha sobre a adequação do material para a aplicação e se os parâmetros de projeto foram rigorosamente seguidos durante o serviço.
A análise usando os princípios da mecânica da fratura fornece informações valiosas para a pessoa que investiga a falha sobre a tensão desenvolvida no componente falhado no momento da fratura em relação à tensão de projeto, particularmente no caso de propagação de trinca por um mecanismo frágil.
Em caso de falha por fadiga, é importante determinar o número de ciclos que precedem a fratura por um mecanismo de fadiga. O método baseado na medição do espaçamento das estrias de fadiga geralmente é conveniente, desde que as estrias sejam claramente visíveis nas superfícies da fratura.
Um exame cuidadoso e minucioso da macroestrutura (aumento usual de 10) e microestrutura do material envolvido na falha pode fornecer pistas importantes. Se possível, as características estruturais das amostras removidas do componente com falha com aquelas representativas das amostras removidas das seções de som, bem como das amostras nunca usadas em serviço, devem ser comparadas. Também é necessário consultar as recomendações específicas do fabricante do equipamento quanto ao uso do material.
O exame macroestrutural pode fornecer informações sobre o caminho da fratura e o local de origem, por exemplo, superfície interna ou superfície externa.
A seleção da técnica adequada para o exame microestrutural depende do tipo de informação necessária. No entanto, a microscopia óptica geralmente é empregada para começar a conhecer as características microestruturais gerais, como tamanho e forma do grão, precipitados secundários e sua distribuição e microfissuras e sua localização. Um tamanho de grão incomumente grande é uma indicação de que o material está exposto a uma temperatura excessivamente alta. A forma do grão e a forma dos gêmeos de recozimento fornecem informações sobre a quantidade de trabalho a frio. O alongamento dos grãos indica que o material é trabalhado a frio pesadamente. Limites gêmeos dobrados indicam que o material está deformado plasticamente. Linhas de deslizamento finas dentro dos grãos também indicam a deformação plástica do material. Se precipitados secundários são vistos na microestrutura, então sua natureza e morfologia precisam ser examinadas.
Durante o exame das características microestruturais é necessário prestar atenção à presença das microfissuras. Por exemplo, trincas no contorno de grão podem resultar de deformação por fluência ou fragilização dos contornos de grão por precipitados de uma fase secundária.
Embora seja possível obter muitas informações sobre as características da fratura por exame visual, ainda é necessário o exame da microestrutura da superfície da fratura usando um microscópio eletrônico de varredura para conhecer o mecanismo responsável pela fratura. Uma fratura pode ocorrer por sobrecarga repentina ou pela propagação de uma trinca a ponto de causar fratura. A propagação da trinca pode ocorrer por diferentes mecanismos. Portanto, é necessário conhecer a morfologia da superfície da fratura para encontrar o mecanismo que causou a fratura.
Durante o exame visual, se forem observados depósitos de corrosão, é necessário determinar a natureza dos depósitos. O depósito pode ser de óxido, sulfeto, cloreto ou carboneto etc. No caso de depósitos de corrosão, é necessário conhecer a natureza do ambiente operacional e a resistência à corrosão do material nesse ambiente.
É muito importante para a pessoa que investiga a falha distinguir entre o modo de falha e a causa da falha. Às vezes, os dois termos são misturados, levando a uma grande confusão. Para evitar falhas futuras, é essencial identificar a causa da falha. Por exemplo, o modo de falha é a dureza superficial inadequada do componente com falha, mas a causa da falha pode estar relacionada à seleção errada do material ou condições operacionais inadequadas.
A interpretação precisa e detalhada de todos os dados obtidos durante os vários estágios da análise de falhas é importante para uma análise de falhas. Sem ele, as inferências apropriadas que são necessárias para encontrar a causa exata da falha não podem ser feitas. A determinação inadequada da causa durante a análise de falhas leva a ações corretivas erradas que não ajudam na prevenção de falhas futuras.
A investigação da análise de falhas não é concluída sem um relatório detalhado. O relatório deve incluir um conjunto de recomendações para prevenir falhas futuras. As recomendações devem ser consistentes com os resultados da investigação. Além disso, as recomendações podem fornecer soluções de curto prazo, bem como soluções de longo prazo.
Processo de manufatura
- Análise da forma de onda
- Opções de análise
- Análise de falha de componente
- Análise de falha de componente (continuação)
- O que é análise de rede?
- Mais sobre análise de espectro
- Ferramenta de estimativa de análise RCM Blitz
- Simplifique o relatório de falhas na manutenção
- Prolongue a vida útil da vedação com a análise de falha da vedação Sundyne da HDS
- 6 maneiras de evitar a frustração da análise de falhas por corrosão