Materiais necessários para a Produção de Aço em Forno Básico de Oxigênio
Materiais necessários para a produção de aço em forno de oxigênio básico
Os seguintes tipos de materiais são necessários para a produção de aço líquido no processo de fabricação de aço com forno de oxigênio básico (BOF) (Fig. 1).
- Matérias-primas básicas, como metal quente, sucata, cal etc.
- Matérias-primas secundárias, como desoxidantes e carburadores.
- Gases utilitários, como oxigênio, nitrogênio e argônio, etc.
- Refratários e materiais refratários, como material de revestimento, material de projeção e materiais de remendo, etc.
- Sondas consumíveis, como sondas de temperatura e sondas de amostragem, etc.
- Água de resfriamento para resfriamento da lança de sopro de oxigênio e gases de exaustão.
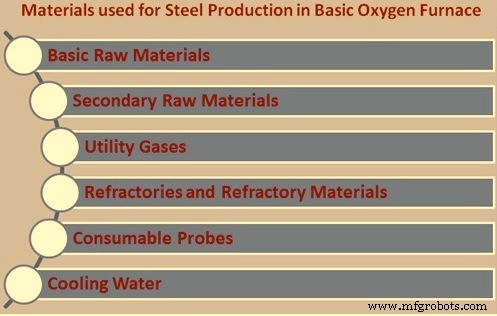
Fig 1 Materiais necessários para a produção de aço em forno de oxigênio básico
Matérias-primas básicas
As matérias-primas básicas necessárias para a fabricação de aço no conversor BOF incluem (i) metal quente do alto-forno, (ii) sucata de aço e/ou qualquer outra fonte de ferro metálico, (iii) minério de ferro e (iv) fundentes. A sucata, carregada de uma caixa de sucata, é o primeiro material a ser carregado no BOF. O metal quente é então despejado no conversor a partir de uma panela de carga de metal quente, após o que o sopro com gás oxigênio é iniciado. Os fluxos, geralmente em forma de grumos, são carregados no BOF através de um sistema de bin após o início do sopro de oxigênio. Os fluxos também podem ser injetados no forno na forma de pó através de ventaneiras de fundo. A composição e as quantidades de matérias-primas básicas utilizadas no conversor BOF variam de uma aciaria para outra, dependendo de sua disponibilidade e da economia do processo.
O metal quente ou ferro líquido é a principal fonte de unidades de ferro e energia. O metal quente é recebido dos altos-fornos em carros de topo aberto ou torpedos. No caso de panelas de topo aberto, o metal quente é derramado em um misturador de metal quente para manter sua temperatura antes de seu uso no conversor BOF. A composição química do metal quente pode variar substancialmente, mas normalmente contém cerca de 3,8% a 4,5% de carbono, 0,5% a 1,5% silício, 0,25% a 1,5% manganês, 0,05% a 0,15% fósforo e 0,03% a 0,08% enxofre.
O nível de enxofre do metal quente pode ser reduzido para tão baixo quanto 0,001% em uma planta de dessulfuração de metal quente. A composição do gusa depende da prática e carga no alto-forno. Geralmente, ocorre diminuição do teor de silício e aumento do teor de enxofre do gusa quando o alto-forno opera em regime mais frio. O teor de fósforo do metal quente aumenta se o teor de fósforo for alto na carga do alto-forno.
Carbono e silício são os principais contribuintes de energia. O silício metálico quente afeta a quantidade de sucata que pode ser carregada no calor do conversor BOF. Por exemplo, se o silício de metal quente for alto, há mais quantidade de calor gerada devido à sua oxidação, portanto, mais sucata pode ser carregada no calor. O silício metálico quente também afeta o volume de escória e, portanto, o consumo de cal e o rendimento de ferro resultante.
O metal quente é geralmente saturado com carbono e sua concentração de carbono depende da temperatura e da concentração de outros elementos do soluto, como silício e manganês. O teor de carbono do metal quente aumenta com o aumento da temperatura e do teor de manganês e diminui com o aumento do teor de silício.
É importante conhecer a temperatura e o teor de carbono do metal quente no momento em que é derramado no conversor BOF para fins de controle do processo no conversor BOF. A temperatura do metal quente é normalmente medida na panela de carga do metal quente antes de ser carregada no conversor BOF. Normalmente, a temperatura do metal quente está na faixa de 1300 graus C a 1350 graus C.
A dessulfurização é favorecida em altas temperaturas e baixos potenciais de oxigênio. Além disso, a presença de outros elementos solutos no metal quente, como carbono e silício, aumenta a atividade do enxofre, que por sua vez aumenta a dessulfuração. Assim, o baixo potencial de oxigênio e os altos teores de carbono e silício tornam as condições mais favoráveis para remover o enxofre do metal quente do que do aço no conversor BOF. Nem todo metal quente é dessulfurizado. O metal quente usado para fabricar tipos de aço com especificações rigorosas de enxofre é dessulfurizado na planta de dessulfurização de metal quente, onde os reagentes de dessulfuração podem reduzir o enxofre do metal quente para tão baixo quanto 0,001%, mas mais tipicamente na faixa de 0,004% a 0,005%. É importante que a escória produzida após a dessulfuração do metal quente seja removida de forma eficaz através da escumação da escória. Esta escória contém grandes quantidades de enxofre, e qualquer escória transportada para o conversor BOF, onde as condições não são boas para a dessulfuração, causa a captação de enxofre no aço líquido.
A pesagem do metal quente é feita em uma balança antes de ser despejada no conversor BOF. É muito importante que o peso do metal quente seja conhecido com precisão, pois qualquer erro pode causar problemas na química de turndown, temperatura e tamanho do calor no conversor BOF. Esse peso também é uma entrada importante para o modelo de carga estática.
A sucata é a segunda maior fonte de unidades de ferro no conversor BOF depois do metal quente. A sucata é basicamente ferro ou aço reciclado, que é gerado dentro da usina siderúrgica (por exemplo, colheitas na CCM, sucata da usina, sucata recuperada dos resíduos da fundição de aço ou sucata de manutenção) ou comprada de uma fonte externa.
É importante que os vários tipos de sucata sejam carregados em quantidades corretas para atender aos requisitos de mistura de sucata na caixa de sucata. A caixa de sucata é pesada para saber a quantidade exata de sucata na caixa de sucata. A mistura de sucata e o peso da sucata são parâmetros importantes; caso contrário, o desempenho de redução do calor no conversor BOF é afetado negativamente.
Geralmente, a sucata mais leve é carregada na parte frontal e a sucata mais pesada na extremidade traseira da caixa de sucata. Isso faz com que a sucata mais leve aterrisse primeiro no conversor BOF à medida que a caixa de sucata é inclinada. É preferível que a sucata mais leve caia primeiro no revestimento refratário, antes da sucata mais pesada, para minimizar seu impacto e, portanto, danificar o revestimento refratário. Além disso, uma vez que a sucata pesada é mais difícil de derreter do que a sucata leve, é preferível que fique no topo de modo que fique mais próximo da área de impacto do jato de oxigênio e, portanto, possa derreter mais rapidamente. Pedaços de sucata que são muito grandes para serem carregados no forno são cortados em pedaços menores por meio de cisalhamento, corte por chama ou por punção de oxigênio. Pedaços finos e pequenos de sucata, como cisalhamento de chapas e punções, são comprimidos em fardos usando prensas hidráulicas especiais. Normalmente, pedaços maiores e mais pesados de sucata são mais difíceis de derreter do que pedaços menores e mais leves. A sucata não fundida pode causar problemas significativos no controle do processo. Isso pode resultar em altas temperaturas ou produtos químicos perdidos na abertura.
A prática combinada de sopro no conversor BOF pode melhorar significativamente as características de mistura e, portanto, melhora a fusão de pedaços maiores de sucata. Certos elementos presentes na sucata, como cobre, molibdênio, estanho e níquel, são introduzidos no conversor BOF através da carga de sucata. Esses elementos não podem ser oxidados e, portanto, não podem ser removidos durante o sopro do calor BOF. Esses elementos se dissolvem uniformemente no banho líquido durante o sopro de oxigênio. Alguns outros elementos como alumínio, silício e zircônio presentes na sucata podem ser totalmente oxidados durante o processo de sopro e serem incorporados à escória. Elementos que se enquadram na categoria intermediária em termos de tendência a reagir, como fósforo, manganês e cromo, distribuem-se entre o metal e a escória. O zinco e o chumbo são removidos principalmente durante o sopro do calor BOF como vapor. As fundições de aço normalmente usam cerca de 10% a 35% de sua carga metálica total como sucata, com a quantidade exata dependendo das condições e economia locais. Tecnicamente a proporção de sucata de metal quente na carga metálica BOF depende de fatores como o silício, carbono e temperatura do metal quente, uso de uma lança de pós-combustão.
O ferro reduzido direto (DRI) é usado em algumas aciarias como refrigerante e como fonte de unidades de ferro. DRI normalmente contém cerca de 89% a 94% do ferro total (cerca de 88% a 96% de metalização), 0,1% a 4% de carbono, 2,8% a 6% de alumina e sílica combinados, 3% a 8% de FeO e pequenas quantidades de CaO e MgO. DRI pode conter fósforo na faixa de 0,005% a 0,09%, enxofre na faixa de 0,001% a 0,03% e baixas concentrações de nitrogênio (geralmente inferiores a 20 ppm).
O DRI é normalmente alimentado no BOF em forma de pedaços ou em forma de briquetes de tamanho em torno de 25 mm a 30 mm. Os briquetes DRI são passivados para eliminar qualquer tendência à queima espontânea para que possam ser manuseados convenientemente na aciaria. O DRI geralmente é alimentado no conversor BOF através do sistema bin.
Em algumas siderúrgicas, o ferro-gusa também é utilizado como fonte de unidades de ferro. O ferro-gusa precisa de calor para seu derretimento e, uma vez derretido, se comporta no conversor BOF como metal quente. O ferro-gusa é carregado no conversor através da caixa de sucata juntamente com outra mistura de sucata.
O minério de ferro geralmente é carregado na forma de caroço no conversor BOF como refrigerante e é frequentemente usado como substituto de sucata. Os minérios de ferro são substitutos úteis da sucata, pois contêm quantidades menores de elementos residuais, como cobre, zinco, níquel e molibdênio. O efeito de resfriamento do minério de ferro é cerca de três vezes maior que o da sucata. A redução do óxido de ferro no minério é endotérmica e maiores quantidades de metal quente e menores quantidades de sucata são necessárias quando o minério de ferro é usado para resfriamento. Os minérios de ferro devem ser carregados no início do golpe quando o teor de carbono no banho líquido é alto, de modo a reduzir efetivamente o óxido de ferro no minério de ferro. A redução dos óxidos de ferro no minério produz quantidades significativas de gás e, consequentemente, aumenta a tendência de formação de espuma e slopping da escória. A adição tardia do minério de ferro resulta em um efeito prejudicial no rendimento do ferro e na química da escória final. Se o minério de ferro for usado apenas como refrigerante logo antes da extração do calor do conversor, a escória se tornará altamente oxidada e fluida, aumentando a transferência de escória para a panela. O atraso na reação de resfriamento do minério de ferro não reduzido causa uma diminuição repentina na temperatura ou uma reação violenta na panela resultando em superoxidação do aço líquido.
É possível usar carepa de laminação como refrigerante no conversor BOF em quantidades adequadas. A carepa de laminação é muito eficaz para aumentar a proporção de metal quente para sucata. No entanto, causa um desmoronamento pesado durante o processo. A carepa de laminação e outras adições de óxido de ferro são reduzidas durante o golpe principal, liberando ferro e oxigênio. Este oxigênio adicional fica disponível para remoção de carbono, acelerando assim a reação geral. O slopping é provavelmente causado pelo aumento do volume de escória associado ao uso de mais metal quente (mais quantidades de silício e carbono geram mais SiO2 e CO, respectivamente) e pelo aumento da taxa de reação.
Durante a fabricação de aço no conversor BOF, o consumo de cal calcinada depende do silício do metal quente, da relação metal quente/sucata na carga do conversor, dos teores de enxofre e fósforo inicial (metal quente) e final (meta de aço). A cal calcinada é produzida pela calcinação do calcário. A qualidade da cal calcinada necessária na fabricação de aço do conversor BOF é descrita em artigo separado disponível no link http://www.ispatguru.com/quality-of-lime-for-steelmaking-in-converter/.
Como uma grande quantidade de cal calcinada é carregada no conversor BOF em um curto período de tempo, a seleção cuidadosa da qualidade da cal é importante para melhorar sua dissolução na escória. Em geral, pequenos grumos com alta porosidade apresentam maior reatividade e promovem rápida formação de escória. Os problemas de qualidade mais comuns com cal calcinada são núcleos internos não calcinados, hidratação, excesso de finos e reatividade muito baixa.
A dolomita calcinada é carregada com a cal calcinada para saturar a escória com MgO e reduzir a dissolução de MgO dos refratários do forno na escória. Tipicamente, a dolomita calcinada contém cerca de 36% a 40% de MgO e 54% a 58% de CaO. A adição de dolomita calcinada no banho do conversor BOF deve ser tal que mantenha o nível de escória de MgO acima do limite de saturação. O nível de MgO da escória acima do limite de saturação torna a escória menos corrosiva e reduz/elimina o ataque químico da escória nos refratários do forno.
Em algumas fundições de aço, a dolomita bruta é adicionada diretamente ao conversor BOF. Este atua como refrigerante e como fonte de MgO para saturar a escória, mas há um efeito retardado, pois a reação de calcinação ocorre no conversor BOF. Quando a dolomita bruta é aquecida, ocorre a reação de calcinação endotérmica, causando uma queda de temperatura no conversor BOF.
A dolomita calcinada também é adicionada para o condicionamento da escória antes do respingo da escória. É importante que a química e o tamanho da dolomita calcinada sejam controlados.
Em algumas lojas de conversão BOF, o calcário ou a dolomita bruta são frequentemente usados como refrigerante e não como fluxo. O calcário é comumente usado para resfriar o banho se a temperatura de abertura for maior do que o objetivo especificado. Quando o calcário é aquecido, ocorre a reação de calcinação endotérmica produzindo CaO e CO2, causando uma queda de temperatura no conversor BOF. A extensão da queda de temperatura imediatamente antes da torneira depende do tamanho do calor e da condição da escória. Por exemplo, em um tamanho de calor de 150 toneladas, a adição de 1 tonelada de calcário causa queda da temperatura do banho em cerca de 12 graus C.
O fluoreto de cálcio ou espatoflúor (CaF2) é um fluidificador de escória que reduz a viscosidade da escória. Quando adicionado ao BOF promove a rápida dissolução da cal na escória ao dissolver a camada de silicato dicálcico (2CaO.SiO2) formada ao redor das partículas de cal que retarda a dissolução da cal na escória. Atualmente, espatoflúor é usado com muita moderação devido ao seu ataque muito corrosivo de todos os tipos de refratários, incluindo o conversor BOF e a panela de aço. Além disso, os fluoretos formam ácidos fortes no sistema de coleta de gases residuais que corroem as peças estruturais e que também são emissões indesejáveis.
Matérias-primas secundárias
As matérias-primas secundárias são desoxidantes e carburadores. Estes são normalmente adicionados na panela de aço durante a extração do calor do conversor.
A desoxidação é o último estágio na fabricação de aço. Durante a fabricação do aço, o banho de aço no momento da extração contém 400 a 800 ppm de atividade de oxigênio. A desoxidação é realizada durante o rosqueamento, adicionando na panela cheia quantidades apropriadas de ligas de ferro ou outros desoxidantes especiais.
Os desoxidantes são geralmente as ligas de ferro a granel, como ferro-silício, silício-manganês e ferro-manganês. Eles são usados na fabricação de aço para desoxidação, bem como para a introdução de elementos de liga. Eles são a maneira mais econômica de introduzir elementos de liga no aço. Ferroligas conferem qualidades distintas aos aços.
Ferroligas também são adicionadas para controle de tamanho de grão, bem como para melhorar as propriedades mecânicas do aço. Dependendo do processo de fabricação do aço e do tipo de aço que está sendo feito, a exigência de diferentes ferroligas varia muito. A adição de ferroligas ao aço aumenta sua resistência à corrosão e oxidação, melhora sua temperabilidade, resistência à tração em alta temperatura, resistência ao desgaste e abrasão com adição de carbono e aumenta outras propriedades desejadas no aço, como resistência à fluência etc. produzindo todos os tipos de aço. São utilizados como matéria-prima na produção de ligas de aço e aço inoxidável.
Se ao final do golpe o teor de carbono do aço estiver abaixo das especificações, o aço líquido também é recarburado. Isso é feito pela adição controlada de carburadores na panela cheia. Carburadores comuns são coque brisa e coque de petróleo.
No entanto, grandes adições na panela cheia têm o efeito adverso sobre a temperatura do aço líquido.
Gases utilitários
No processo de fabricação de aço do conversor BOF, uma lança refrigerada a água é usada para injetar oxigênio em velocidades muito altas no banho líquido para produzir aço. Com as crescentes demandas para produzir aços de maior qualidade com níveis mais baixos de impurezas, o oxigênio de pureza muito alta deve ser fornecido. Portanto, o oxigênio para a fabricação de aço deve ser pelo menos 99,5% puro e, idealmente, 99,7% a 99,8% puro. As partes restantes são de 0,005% a 0,01% de nitrogênio e o restante é argônio.
No conversor BOF, o oxigênio é injetado em velocidades supersônicas (Mach>1) com bicos convergentes/divergentes (Laval) na ponta da lança refrigerada a água. Um forte jato de gás penetra na escória e colide com a superfície do metal líquido para refinar o aço. Hoje, a maioria dos BOFs opera com pontas de lança contendo quatro a cinco bicos e com taxas de fluxo de oxigênio que variam de 640 N cum/min a 900 N cum/min.
O nitrogênio é normalmente usado no conversor BOF para sopro combinado e respingo de escória. O gás nitrogênio necessário para melhorar a mistura do banho de metal é soprado através das ventaneiras montadas no fundo ou elementos permeáveis. A agitação do banho é realizada com gás nitrogênio na faixa de alto carbono da massa fundida no banho. As taxas de fluxo de fundo são normalmente inferiores a 0,2 N Cum/t minuto. Na prática típica, o gás nitrogênio é introduzido pelo fundo nos primeiros 60% a 80% do sopro de oxigênio. A rápida evolução do gás CO na primeira parte do fluxo de oxigênio evita a captação de nitrogênio no aço.
O nitrogênio também é usado para respingar a escória líquida condicionada nas paredes do conversor BOF após a extração do calor do conversor BOF para criar uma camada protetora de revestimento de escória sobre os refratários.
O argônio é normalmente usado no conversor BOF para sopro combinado. O gás argônio necessário para melhorar a mistura do banho de metal é soprado através das ventaneiras montadas no fundo ou elementos permeáveis. A agitação do banho é realizada com gás argônio na faixa de baixo carbono da massa fundida no banho. As taxas de fluxo de fundo são normalmente inferiores a 0,2 N Cum/t minuto. Na prática típica, o gás argônio é introduzido pelo fundo nos últimos 20% a 40% do sopro de oxigênio.
Refratários e materiais refratários
Existem três tipos de materiais refratários necessários para a fabricação de aço com conversor BOF. Estes são tijolos básicos geralmente refratários de carbono de magnésia, composto de armamento à base de magnésia para a parte danificada dos refratários e material de remendo (geralmente tijolos usados quebrados) para remendar o fundo erodido do conversor. Estes são descritos no artigo fornecido no link http://www.ispatguru.com/refractory-lining-of-a-basic-oxygen-furnace/.
Sondas consumíveis
Os consumíveis necessários para a produção de aço no conversor BOF são sondas do tipo descartável para amostragem do aço para análise após o término do sopro e para medição de temperaturas do metal quente na panela de carregamento de metal quente e do aço líquido no conversor BOF após o golpe acabou.
Água de resfriamento
A água é necessária para a produção de aço no conversor BOF para o resfriamento da lança e bocal de sopro de oxigênio, bem como para o resfriamento dos gases de escape.
A água de resfriamento é necessária na lança para evitar a queima da lança de oxigênio no conversor BOF. Tanto o bocal da lança de cobre quanto a lança de aço são resfriados por recirculação de água a uma pressão de cerca de 6 kg/sq cm. Os componentes importantes de uma lança são os canais de resfriamento de água onde a água de resfriamento flui através do centro do bocal e sai pelo tubo externo da lança. Ele é projetado para obter a velocidade máxima da água de resfriamento na área do bocal, que é exposta às temperaturas mais altas. A água de resfriamento é fundamental para manter a alta vida útil da lança. As taxas de fluxo precisam ser mantidas na taxa de projeto. A temperatura de saída da água de resfriamento não deve exceder 60 graus C a 65 graus C.
O gás rico em CO que sai do conversor é primeiro resfriado no capô do conversor indiretamente por água de resfriamento ou por sistema de resfriamento evaporativo (ECS) para reduzir sua temperatura nominal de 1600 -1700 graus C para cerca de 900 graus C. Em caso de A água desmineralizada do sistema de resfriamento evaporativo é necessária para o resfriamento dos gases de exaustão, pois neste sistema o calor é recuperado na forma de vapor.
Em algumas fundições de aço, o cone superior do conversor BOF é resfriado a água. Os dois componentes no cone superior do conversor BOF que podem ser beneficiados pelo resfriamento a água como meio de manter sua baixa temperatura de operação são o próprio invólucro cônico e o anel labial no canto superior do cone.
A qualidade da água é um parâmetro importante. Se a água estiver contaminada com óxidos ou sujeira, os depósitos normalmente se formam no interior das tubulações, resultando em um efeito negativo na transferência de calor.
Processo de manufatura
- 7 Materiais Metálicos Comuns e Usos Típicos
- Materiais de impressão 3D de metal
- Quais são as matérias-primas mais confiáveis para estamparia de metal?
- Revestimento refratário de um forno de oxigênio básico
- Utilização de Metal Quente para Siderurgia em Forno a Arco Elétrico
- Sistema Básico de Recuperação e Limpeza de Gás de Forno de Oxigênio
- Química da Siderurgia por Forno Básico de Oxigênio
- Opção de metal para usinagem CNC
- Propriedades dos materiais de aço e ferramentas usadas para punções
- Melhores materiais para peças torneadas