Qualidade da Cal para Siderurgia no Conversor
Qualidade da cal para fabricação de aço no conversor
A cal é um sólido cristalino branco com um ponto de fusão de 2572 graus C. É um óxido básico e é usado para reagir com os óxidos ácidos (por exemplo, sílica). É o óxido de cálcio (CaO) produzido no aquecimento (calcinação) do calcário (CaCO3) a uma temperatura de 900 graus C e acima (geralmente 1100 graus C).
CaCO3(s) + calor =CaO(s) + CO2 (g)
Esta reação é reversível. O óxido de cálcio reage com o dióxido de carbono para formar carbonato de cálcio. A reação é conduzida para a direita pela descarga de dióxido de carbono da mistura à medida que ela é liberada.
A cal hidratada Ca(OH)2 é formada pela reação da cal com água (extinção). A cal hidratada também é conhecida como cal apagada.
CaO + H2O =Ca(OH)2 + calor
A cal como fundente básico na produção de aço e desempenha um papel importante na sequência de reações metalúrgicas que ocorrem em um conversor. O aço é produzido a partir de metal quente oxidando enxofre (S), fósforo (P), carbono (C), silício (Si), manganês (Mn) e outras impurezas para que possam entrar nas fases de escória ou gás, separando-se assim do a fase metálica. A cal na siderurgia é utilizada principalmente na produção de escória para a remoção desses elementos nocivos em banho líquido e otimizar a qualidade do aço líquido.
O processo de oxigênio básico oxida as impurezas em um conversor de oxigênio também conhecido como forno de oxigênio básico (BOF), onde o metal quente entra em contato com o oxigênio. As impurezas oxidadas do metal quente são absorvidas em uma escória, que é formada com a ajuda de cal calcinada.
A cal metalúrgica nos anos 50 consistia em uma mistura de partículas de todos os tamanhos, de muito grossas a muito finas, com componentes adicionais como dióxido de silício e enxofre concentrados nas partículas finas. A qualidade da cal era obviamente menos importante naquela época porque o processo de forno aberto para fazer aço tinha um período de fundição de 6 a 8 horas. Com a introdução do conversor básico de oxigênio (BOF), o processo de fabricação do aço foi acelerado com períodos de sopro de oxigênio de 18 a 20 minutos. As velocidades das reações que ocorrem no BOF são muito rápidas. Uma vez que uma grande quantidade de cal calcinada é carregada no conversor em um curto período de tempo, a seleção cuidadosa da qualidade da cal é importante para melhorar sua dissolução na escória e lidar com a velocidade das reações. É muito importante prestar atenção às propriedades químicas e físicas da cal.
Propriedades químicas da cal
Atribui-se grande importância ao teor de CaO da cal, que deve ser o mais elevado possível, mas nunca inferior a 90 %. O teor de dióxido de carbono deve ser o mais baixo possível, o que é importante para o equilíbrio térmico e para as condições silenciosas de sopro de oxigênio no conversor. O CO2 depende da extensão da calcinação durante a produção de cal e o limite superior para cal de grau de conversão macio é normalmente 1,5% de CO2.
O teor de sílica (SiO2) da cal é muito importante. O SiO2 é um óxido ácido e tem uma grande influência corrosiva no revestimento refratário básico de magnésia-carbono do conversor. Uma das principais finalidades da adição de cal no conversor é neutralizar o SiO2 produzido pela oxidação do Si presente no gusa e na sucata. Qualquer introdução de SiO2 através da cal no conversor é contraproducente. Portanto, o teor de SiO2 da cal deve ser o mais baixo possível. O ideal é que seja inferior a 1,0%.
O teor de óxido de magnésio (MgO) da cal é de importância crescente. Há uma influência favorável da cal contendo MgO na vida útil do revestimento refratário do conversor. Algumas cales metalúrgicas, utilizadas no processo de conversão, possuem teor de MgO em torno de 2%.
O teor de enxofre da cal, que limita a dessulfuração no conversor, é importante. Em algumas condições, o teor de enxofre da cal pode resultar em uma ressulfuração crescente do aço. O teor de enxofre é de grande importância para aços macios e com baixo teor de manganês. Menor teor de enxofre ajuda a controlar o teor de enxofre no aço. O teor de enxofre na cal depende do tipo de combustível usado na calcinação da cal, da qualidade do calcário e das condições de calcinação. Normalmente, o enxofre na cal calcinada deve ser restrito a 0,05%. A análise típica de cal mostra 0,025% de enxofre.
A cal devidamente calcinada auxilia na desfosforização do banho líquido no conversor. A introdução de fósforo através da cal no conversor é contraproducente. Portanto, o teor de P da cal deve ser o mais baixo possível. Normalmente deve ser inferior a 0,03%.
Propriedades físicas da cal calcinada
O tamanho da cal calcinada para o processo BOF de fabricação de aço é muito importante. Normalmente a cal nas frações de granulometria entre 8 mm a 40 mm é utilizada no conversor, pois auxilia na sua dissolução no banho do conversor e auxilia na formação da escória. Se o tamanho da cal for inferior a 8 mm, a maior parte da fração mais fina de cal (menos de 8 mm) é expelida com os gases de escape do conversor e cria uma condição favorável para a formação de acreções na coifa. O limite permitido para a fração mais fina de cal carregada no conversor é normalmente em torno de 5%.
A segunda propriedade física da cal calcinada que tem grande influência na formação da escória durante o processo BOF é a reatividade da cal. A reatividade da cal é a propriedade da cal que determina sua dissolução mais rápida e maior capacidade de reação para a remoção dos elementos nocivos do banho do conversor. Como não é possível determinar a reatividade da cal no aço líquido, ela geralmente é determinada em água usando um procedimento de teste padronizado para que resultados de teste reprodutíveis possam ser alcançados.
A cal calcinada obtém sua propriedade de reatividade devido à boa porosidade que resulta em uma grande superfície específica. A grande superfície específica tem um efeito favorável nas reações metalúrgicas.
Se a cal ficar excessivamente calcinada durante sua produção no forno, os poros se fecham e há redução na área superficial específica da cal e, portanto, perda de reatividade. Da mesma forma, no caso de cal subcalcinada, o núcleo de cal não é calcinado. Essa cal possui dióxido de carbono residual (CO2) e, portanto, tem baixa reatividade. A cal subcalcinada gera mais finos durante seu manuseio. A reatividade da cal depende de sua homogeneidade, do grau de decomposição térmica e de sua área superficial específica.
Devido à alta porosidade, a cal calcinada é altamente higroscópica por natureza. A superfície dos torrões de cal absorve a umidade do ar e fica hidratada. Durante o manuseio da cal, a superfície hidratada cai como pó e expõe a superfície fresca da cal à umidade para se hidratar. Com a absorção da umidade, a cal perde sua reatividade. A cal hidratada não participa das reações no conversor que ocorrem em altas velocidades. Por isso é essencial que a cal calcinada seja consumida no conversor no menor período de tempo após sua produção.
O método comum para a determinação da reatividade da cal é por titulação com ácido clorídrico 4N (HCl). Neste teste são retiradas 12,5 g de amostra de cal na faixa de tamanho de 1 mm a 3 mm e uma solução saturada é preparada com 100 ml de água a 60°C. Duas gotas de reagente laranja de metila são adicionadas a esta solução. Em seguida, adiciona-se ácido HCl de concentração 4N (mole) gota a gota até que seja totalmente neutralizado. O ponto final é o conhecido pela mudança de cor de laranja para rosa. O volume de HCl usado para neutralização é então multiplicado por 4 e o valor é geralmente referido como valor de reatividade. Quanto maior o volume de HCl necessário para a neutralização, maior é a reatividade da cal.
Características físicas de uma boa cal calcinada
As principais características físicas da cal (Fig. 1) devidamente calcinada no forno de cal são apresentadas a seguir.
- Tem baixa densidade a granel com valor variando na faixa de 1,5 toneladas/cum a 1,7 toneladas/cum.
- Sua porosidade é normalmente alta e está na faixa de cerca de 50%.
- Sua área de superfície específica é maior que a área de superfície. Está na faixa de 1,5 m²/kg a 2,0 m²/kg.
- Seus cristais minerais são pequenos.
- Sua reatividade deve ser muito alta. Normalmente, o valor de reatividade é superior a 300 ml de HCl 4N.
- O teor de CO2 residual é baixo. O valor geralmente é inferior a 2%.
- O teor de finos é baixo. Normalmente, deve ser inferior a 5%.
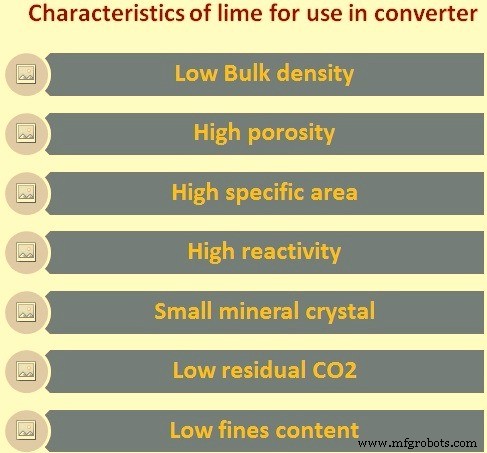
Fig 1 Características do cal para uso no conversor
Escória de cal e siderurgia
A cal é fundamental para a siderurgia. Perto do início do sopro, cal calcinada e dolomita calcinada são adicionados, embora às vezes estes sejam adicionados gradualmente ao longo do calor. O CaO da cal calcinada e o CaO + MgO da dolomita calcinada reagem com as impurezas oxidadas e o óxido de ferro para formar uma escória. A escória é então composta por silicatos complexos de cálcio e magnésio, alumino-silicatos, ferritas, fosfatos etc. A formação de uma boa escória básica é essencial para garantir a qualidade do aço. Os níveis de basicidade (CaO/SiO2) são normalmente mantidos na faixa de 2,8 e 3,5.
O termo basicidade da escória é um meio pelo qual se determina quão ácida ou básica é uma escória em relação ao refratário básico utilizado no conversor. Se a escória for mais ácida, irá erodir os tijolos, se for mais básica, protegerá os tijolos. A basicidade da escória é normalmente fixada pela quantidade de cal e dolomita calcinada adicionada. O valor mais baixo da razão indica que a escória é ácida e à medida que a razão aumenta a escória se torna cada vez mais básica
Uma cal devidamente calcinada e com boa basicidade favorece a desfosforação e a dessulfuração, e facilita o processo siderúrgico com redução do esguicho. A distribuição do enxofre entre o banho e a escória é melhor com a cal calcinada adequada do que com a cal sobrecalcinada mesmo com escórias de mesma basicidade. O mesmo se aplica em menor grau para a desfosforização. Também neste caso, especialmente com baixos teores de óxido de ferro na escória, os teores de fósforo no aço são reduzidos pelo uso da cal devidamente calcinada.
Com o uso de uma cal devidamente calcinada, é possível reduzir as adições de cal no conversor e assim ter um melhor controle de escórias e temperaturas no conversor. Também ajuda a aumentar o rendimento do aço líquido no conversor.
Processo de manufatura
- Tungstênio Molibdênio Liga de Ferro para Siderurgia
- Melhoria da Qualidade na Fabricação:Alívio para o Gerente de Operações
- Plex lança novo sistema de gestão de qualidade para fabricantes
- O que procurar em um parceiro de fabricação de uretano
- 5 das marcas industriais da mais alta qualidade a serem procuradas
- Solukon lança ferramenta de fábrica digital para gerenciamento de qualidade
- Metais para fabricação de alta mistura e baixo volume
- Punções e matrizes de qualidade para fabricação de ferramentas
- 7 fatores a serem considerados para um projeto de PCB de boa qualidade
- Maquinário confiável para massas italianas de qualidade