Calcário – seu processamento e aplicação na indústria siderúrgica
Calcário – Seu Processamento e Aplicação na Indústria de Ferro e Aço
O calcário é uma rocha sedimentar abundante e natural que consiste em altos níveis de carbonato de cálcio (CaCO3) na forma do mineral calcita. Alguns calcários podem conter pequena porcentagem de carbonato de magnésio (MgCO3). Esses calcários são conhecidos como calcários dolomíticos.
O calcário também é um mineral industrial muito importante. Suas propriedades químicas o tornam um mineral valioso para uma ampla gama de usos industriais/manufatureiros. O calcário também é uma das matérias-primas vitais usadas na produção de ferro e aço.
O calcário, por definição, é uma rocha que contém pelo menos 50% de CaCO3 na forma de calcita em peso. Pode haver pequenas partículas de quartzo (sílica), feldspato (aluminossilicatos), minerais argilosos, pirita (sulfeto de ferro), siderita (carbonato de ferro) e outros minerais associados ao calcário. Todos os calcários contêm pelo menos alguns por cento de outros materiais. As impurezas na lata de calcário consistem em sílica (SiO2), alumina (Al2O3), óxido de ferro (Fe2O3), enxofre (como sulfetos ou sulfatos), fósforo (P2O5), potássio (K2O) e soda (Na2O). Sílica e alumina são as principais impurezas do calcário. O calcário utilizado na produção de ferro deve conter pelo menos 85 % de carbonato de cálcio e uma baixa percentagem de alumina. Da mesma forma, o calcário usado para a fabricação de aço deve conter pelo menos 92% de carbonato de cálcio e uma porcentagem muito baixa de impurezas, especialmente a porcentagem de sílica.
Os principais usos do calcário na indústria siderúrgica são (i) como material fundente, e (ii) outros usos que consistem em agente dessulfurante, revestimento de moldes de máquina de fundição de suínos, neutralização de água ácida, tratamento de água, águas residuais ( efluentes), tratamento de gases de combustão e tratamento de lodo e esgoto. É também um componente da escória sintética. O calcário é normalmente usado em três formas. São eles (i) o calcário bruto que também é a forma natural do calcário, (ii) o calcário calcinado ou cal viva, ou simplesmente cal, e (iii) como cal hidratada. Quando o calcário é usado como material fundente, ele é usado como calcário bruto ou como calcário calcinado. A cal hidratada é geralmente produzida a partir de cal viva com alto teor de cálcio e contém 72% a 74% de óxido de cálcio com 23% a 24% de água combinada quimicamente.
Processamento de calcário
O calcário após sua mineração deve passar por vários processamentos antes de poder ser usado em vários processos. Os processos básicos na produção de calcário são (i) extração de calcário bruto, (ii) preparação de calcário extraído para uso por britagem e dimensionamento, (iii) calcinação de calcário bruto, (iv) processamento adicional do calcário calcinado por hidratação para produzir cal hidratada, se necessário para uso, e (v) operações diversas de transferência, armazenamento e manuseio. Todos esses processos podem não ser necessários para estar presentes em todas as plantas.
Basicamente três tipos de produtos de calcário são usados em siderúrgicas. São eles (i) produtos de calcário bruto, (ii) produtos de calcário calcinado ou cal viva e (iii) produtos de cal hidratada. O processamento do calcário para esses produtos é descrito abaixo.
O primeiro processo ocorre em minas de calcário onde o minério extraído passa por britagem e peneiramento para a separação das diferentes frações de tamanho do minério. Na siderúrgica, em alguns locais, o calcário bruto é processado. Um exemplo é a planta de sinterização onde o calcário bruto é triturado em moinhos de martelo para tamanhos de – 3 mm (geralmente na faixa de 85% a 90%).
A calcinação do calcário é um processo de tratamento térmico para realizar a decomposição térmica do calcário bruto e remoção de LOI (perda ao fogo) ou dióxido de carbono (CO2) parte de sua composição. O processo de calcinação consiste em uma reação endotérmica que é realizada no estado sólido. A cal de alta qualidade usada na fabricação de aço geralmente contém cerca de 90% a 95% de CaO. Teoricamente 56 kg de CaO são produzidos a partir de 100 kg de CaCO3 durante a calcinação completa. No entanto, na prática real, varia devido a vários fatores. Durante a calcinação do calcário, uma vez que o CO2 é removido, a cal (i) é porosa (ii) tem maior área superficial, (iii) tem alta reatividade e (iv) é higroscópica. Cerca de 1,8 t de calcário é necessário para produzir 1 t de cal viva.
A calcinação do calcário, por ser uma reação química endotérmica, requer considerável aporte de energia. Quando o calcário é aquecido, o carbonato de cálcio é decomposto de acordo com a seguinte equação.
CaCO3 + cerca de 42,5 kcal de calor =CaO + CO2
A calcinação do calcário é um processo simples de queima de estágio único que é realizado em um forno de eixo ou um forno rotativo. Consiste em cinco etapas do processo. Estes são (i) transferência de calor do ambiente para a superfície da partícula, (ii) condução de calor da superfície para a frente de reação, (iii) cinética química na frente, (iv) difusão do CO2 através da camada de óxido porosa para a superfície e (v) ) em seguida, transfira para o ambiente. O calcário é carregado no forno e, enquanto avança pelo forno, está sendo decomposto ou calcinado. A decomposição do CaCO3 começa em 810 graus C.
O processo de calcinação pode ser explicado usando um pedaço de calcário parcialmente decomposto, cujos perfis de pressão parcial de CO2 e temperatura são mostrados na Fig. 1. A amostra compreende um núcleo de carbonato denso circundado por uma camada porosa. No forno de calcinação a uma temperatura Tgás o calor é transferido por radiação e convecção (simbolizado por 'h') para a superfície sólida a uma temperatura de Tsurface. Por condução térmica (A) o calor penetra através da camada de óxido para atingir a frente de reação, onde a temperatura é Trc. Como a entalpia da reação é muitas vezes maior que a energia interna, o calor que flui para dentro do núcleo é desprezível durante a reação. Portanto, a temperatura central é apenas ligeiramente inferior à temperatura frontal. Uma vez que o calor é fornecido, a constante de reação química (k) então ocorre para a qual a força motriz é o desvio da pressão parcial de CO2 do equilíbrio (p-eq – p-f). O CO2 liberado se difunde (Dp) através da camada porosa de óxido até a superfície e finalmente passa por convecção (B) para o ambiente onde existe a superfície p de pressão parcial de CO2. As propriedades químicas e físicas da cal são influenciadas pela calcinação que, por sua vez, é influenciada pela condutividade, coeficiente de transferência de massa e difusividade da camada de cal.
Fig 1 Perfil da amostra de calcário durante a calcinação
Para a calcinação total do calcário e para que não haja núcleo residual de calcário não calcinado, é necessário que o calor fornecido à superfície do calcário penetre por transferência de calor condutiva para o núcleo. Uma temperatura de 900 graus C deve ser alcançada no núcleo pelo menos por um curto período de tempo, uma vez que a atmosfera dentro do material é CO2 puro. A superfície do calcário deve ser aquecida a mais de 900 graus C para manter o gradiente de temperatura necessário e superar o efeito isolante do material calcinado na superfície do calcário. No entanto, ao produzir cal viva, a temperatura da superfície não deve exceder 1.100 graus C a 1.150 graus C, caso contrário ocorre a recristalização do CaO e resulta em menor reatividade e, portanto, reduz as propriedades de extinção da cal viva.
Um certo tempo de retenção ou residência é necessário para transferir o calor dos gases de combustão para a superfície do calcário e depois da superfície para o núcleo do calcário. Pedaços maiores de calcário requerem mais tempo para calcinar do que pedaços menores. Em princípio, a calcinação em temperaturas mais altas reduz o tempo de retenção necessário. No entanto, temperaturas muito altas afetam negativamente a reatividade do produto. A relação entre a temperatura de calcinação e o tempo de retenção necessário para diferentes tamanhos de calcário é mostrada na Tab 1.
Tab 1 Relação entre temperatura de calcinação e tempo de residência | |||
Sl. No. | Tamanho da pedra calcária | Temperatura de calcinação | Tempo de residência (aproximado) |
Unidade | mm | graus C | Horas |
1 | 50 | 1000 | 2.1 |
1200 | 0,7 | ||
2 | 100 | 1000 | 8,3 |
1200 | 2,9 |
Vários tipos diferentes de fornos são usados para o processo de calcinação. Esses fornos podem ser fornos rotativos ou fornos de eixo. O tipo de forno a ser selecionado depende fortemente das características do calcário, taxa de produção prevista, custo do combustível, custos de investimento, combustível disponível, condições locais, infraestrutura e outras coisas. Em geral, todos os dados, incluindo testes de laboratório, devem ser avaliados antes de selecionar o forno de calcinação.
Os fornos rotativos, com ou sem pré-aquecedores, geralmente processam calcário com tamanho de material entre 10 mm e 50 mm. O balanço térmico deste tipo de fornos é categorizado um pouco pelas altas perdas com os gases de escape e através da carcaça do forno. Os valores típicos para as perdas de gás estão na faixa de cerca de 25% e para as perdas no casco do forno estão na faixa de cerca de 20% da necessidade total de calor. Apenas cerca de 60% da energia do combustível introduzida no forno com pré-aquecedor é utilizada para o processo de calcinação.
No caso de fornos verticais de eixo único, existe um desequilíbrio entre o calor disponível da zona de calcinação e o calor necessário na zona de pré-aquecimento. Mesmo com o processo de calcinação ideal, a temperatura dos gases residuais pode ser superior a 100 graus C. No caso de fornos do tipo regenerativo de fluxo paralelo (PFR), há melhor aproveitamento do calor da zona de calcinação e minimização da perda de calor nos gases residuais, resultando em menor consumo de calor por tonelada de cal.
O diagrama esquemático de um forno vertical de eixo único mostrando o fluxo de material e fluxo de gás, os principais componentes de um forno rotativo de cal e o mecanismo de transferência de calor em um forno rotativo são mostrados na Figura 2.
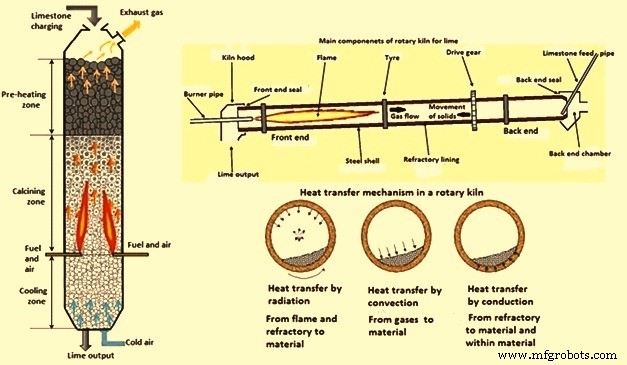
Fig 2 Diagrama esquemático de um forno vertical de eixo único, componentes do forno rotativo e mecanismo de transferência de calor em um forno rotativo
A comparação de dados para diferentes fornos normalmente usados para calcinação de calcário com valores importantes de consumo e tamanho típico de matéria-prima é fornecida na Tabela 2.
Tab 2 Comparação de vários tipos de fornos de calcinação | |||||
Tipo de forno de calcinação | Capacidade do forno | Tamanho da pedra calcária | Consumo específico de combustível | Consumo de energia específico | Observações |
td | mm | kcal/kg | kWh/ton | ||
Forno PFR retangular | 100-400 | 30-120 | 810-870 | Cerca de 20 | É produzida cal altamente reativa |
Forno circular PFR | 300-800 | 30-160 | 810-870 | Cerca de 20 | É produzida cal altamente reativa |
Forno de cal fina | 200-400 | 15-40 | 790-850 | Cerca de 20 | É produzida cal altamente reativa |
Forno de eixo anular | 200-600 | 15-200 | 910-980 | Cerca de 30 | Alto teor de CO2 nos gases de escape |
Forno de eixo único | 50-300 | 10-100 | 980-1100 | Cerca de 35 | É produzida cal queimada de dureza média |
Forno rotativo com pré-aquecedor | 300-1200 | 10-50 | 1150-1350 | Cerca de 30 | É produzida cal altamente reativa, alta taxa de produção e baixo teor de enxofre |
Fornos rotativos longos sem pré-aquecedor | 300-1000 | 20-50 | 1600-1700 | Cerca de 20 | Altas taxas de produção, cal reativa e baixo teor de enxofre |
Calcinação de suspensão | 300-1200 | 0,03-2 | 1300-1400 | Matéria-prima muito fina |
A seguir estão os fatores e parâmetros operacionais que influenciam a calcinação do calcário.
Tipos de fornos – Existem dois tipos de fornos que são usados para calcinar calcário. Eles são fornos de eixo vertical ou fornos rotativos horizontais. Dependendo do tipo de forno, o tamanho da carga de calcário é diferente. Nos fornos verticais, o calcário se move para baixo e os gases quentes fluem para cima através do calcário, portanto, as pedras devem ser grandes o suficiente para fornecer passagem para que os gases de combustão se movam para cima. Esses fornos geralmente usam tamanhos de calcário que variam de 130 mm a 200 mm. Nesses tipos de forno, o aumento da temperatura deve ser lento e, portanto, o tempo de residência resultante é longo. Os fornos verticais são eficientes em termos de combustível, mas de capacidade limitada. No caso de fornos horizontais, o corpo do forno gira, permitindo que o calcário tombe e expondo todas as superfícies ao gás quente. O tamanho típico do calcário para esses tipos de fornos varia de 25 mm a 40 mm. A uniformidade do tamanho do calcário para carregar o forno é muito importante para um processo de calcinação uniforme. Mas, do ponto de vista prático, o dimensionamento apertado é caro devido à triagem múltipla necessária. O calcário de tamanho pequeno, como 6 mm e menor com uma certa porcentagem de finos em um forno horizontal, tende a tombar em massa, reduzindo assim a exposição das partículas aos gases quentes. Este processo resulta em exposição desigual, reduzindo assim a qualidade da cal virgem. Nos fornos verticais, a presença de calcário de tamanho muito pequeno bloqueia os vazios entre o calcário, interferindo na passagem do gás e, portanto, na transferência de calor, causando calcinação irregular. Além disso, pequenas partículas de calcário (menos de 3 mm) tendem a se degradar e causar a geração de finos que precisam ser removidos por coletores de pó.
Tamanho e gradação do calcário -Durante o processo de calcinação, a dissociação do calcário normalmente progride gradualmente da superfície para o interior do calcário. Quanto maior o tamanho do calcário, mais difícil é calcinar e também requer mais tempo. Uma ampla faixa de distribuição de tamanho de partículas na alimentação do forno também interfere na distribuição de calor no forno. As pequenas pedras acumulam-se entre os vazios formados por grandes pedras em fornos de fuste, bloqueando assim a tiragem e o fluxo de chamas e gases de combustão. Além disso, durante a calcinação de uma ampla gama de tamanhos de calcário, temperaturas que calcinam adequadamente os tamanhos menores sem calcinar excessivamente, apenas calcinam a casca externa do calcário com dimensões maiores. Assim, calcários com gradações restritas, independentemente do tamanho, são muito mais fáceis de calcinar. O tamanho do calcário também é elemento crítico no processo de calcinação. À medida que o calcário entra no forno, ele é exposto aos gases quentes dentro do forno. A taxa de penetração do calor depende da temperatura do calcário e dos gases circundantes. Além disso, leva tempo para o calor penetrar no calcário. Quanto menor o tamanho do calcário, menor é o tempo de penetração do calor. No caso do calcário pulverizado, esse tempo pode ser de uma fração de minuto.
Estrutura cristalina e densidade do calcário – A estrutura cristalina do calcário afeta a taxa de calcinação, a resistência interna do calcário, bem como o tamanho do cristal resultante do CaO na cal. Os cristais menores se aglomeram durante a calcinação, formando cristais maiores, causando encolhimento e redução de volume. Temperaturas mais altas do forno auxiliam no processo de aglomeração. Quanto maior a aglomeração, maior a retração de volume do produto final. A densidade do calcário e sua estrutura cristalina estão um pouco relacionadas. A forma dos cristais determina o espaço vazio entre os cristais e, portanto, a densidade do calcário. Vazios maiores permitem a passagem fácil de gases CO2 durante a calcinação, mas também resulta em uma redução de volume durante a calcinação. Alguns tipos de calcário, devido à sua estrutura cristalina, desfazem-se no processo de calcinação. Estes tipos de calcário não são adequados para calcinação. Existem alguns outros tipos de calcário que se comportam de maneira oposta e se tornam tão densos durante a calcinação que impedem a fuga de CO2 e se tornam não porosos. Novamente, esses tipos de calcário não são adequados para calcinação.
Temperatura de calcinação – A calcinação do calcário inicia-se a cerca de 810 graus C à pressão atmosférica e numa atmosfera constituída por 100 % de CO2. A dissociação prossegue progressivamente da superfície externa para a superfície interna. Para que a dissociação penetre no interior do calcário, são necessárias temperaturas mais altas. As temperaturas requerem um aumento adicional para que a dissociação do núcleo do calcário possa ocorrer. Quanto maior o tamanho do calcário, maior a temperatura necessária para a dissociação do núcleo devido ao aumento da pressão interna à medida que o gás CO2 força sua fuga. Um aumento na temperatura exerce uma influência muito maior na taxa de dissociação do que na retenção de temperatura. Além disso, a temperatura teórica necessária para a calcinação é de cerca de 1.000 graus C. No entanto, na prática, as temperaturas mantidas no forno são muito mais altas (cerca de 1.350 graus C). A temperatura correta no forno depende do tamanho do calcário, bem como do tipo de forno e do tipo de combustível utilizado. O operador do forno normalmente experimenta para determinar a temperatura exata para o tamanho e a qualidade do calcário que está sendo usado. Em geral, é melhor usar a temperatura mais baixa com o menor tempo de residência possível para obter a calcinação completa. Temperaturas de calcinação mais altas causam maior encolhimento e redução de volume. Temperaturas de calcinação mais altas também causam carbonatação da superfície do calcário calcinado, com a presença de CO2 liberado da pedra, bem como subproduto da combustão, o que torna a cal não porosa e, portanto, menos reativa.
Taxa de aumento de temperatura – O aumento da temperatura deve ser gradual e uniforme. É particularmente importante quando se utiliza calcário de grandes dimensões (100 mm a 150 mm). Ao calcinar calcário de tamanho grande, o calcário deve permanecer poroso durante o processo. À medida que a temperatura aumenta, a camada externa de calcário é aquecida até a temperatura de dissociação, onde o CO2 escapa do calcário, deixando passagens capilares tornando a cal porosa. À medida que o gás escapa, o calcário encolhe em volume até 40%. Essa contração de volume restringe a passagem de gás do centro do calcário, evitando que qualquer gás CO2 adicional escape. Um tempo de residência muito longo facilita a combinação do CaO e CO2 de volta ao CaCO3 (carbonatação) em temperaturas acima de 1350 graus C. Se o aumento de temperatura for muito rápido, a camada externa dos pedaços de calcário será calcinada muito rapidamente. À medida que a temperatura aumenta, a superfície dos pedaços de calcário encolhe e os poros criados pelo escape de CO2 são fechados. Isso produz um aumento da pressão interna dentro do calcário. Como o gás não pode escapar, ele faz com que o calcário exploda e se desintegre. Isso resulta na produção de finos indesejados, reduzindo a qualidade da cal viva resultante.
Tempo de calcinação – Observa-se que, independentemente do tipo de calcário e de sua qualidade, uma temperatura de queima mais alta e um período de calcinação mais longo produz uma cal virgem de queima mais dura, com alta retração, alta densidade, baixa porosidade e baixa reatividade química. O oposto ocorre em temperaturas de queima mais baixas com menor duração de calcinação, resultando na produção das desejadas cales altamente reativas, de queima suave, de baixa retração e densidade e alta porosidade. A calcinação de pedras pequenas e grandes em termos de seus tempos relativos de aquecimento e calcinação é diretamente proporcional ao quadrado da espessura (ou diâmetro médio para pedras de formato irregular. O tempo de retenção no forno depende do tamanho do calcário, bem como da calcinação temperatura. O tamanho do calcário é o elemento mais crítico para a calcinação. À medida que o calcário entra no forno, ele é exposto aos gases quentes dentro do forno. A taxa de penetração de calor é baseada na diferença de temperatura do calcário e do temperatura dos gases. Além dessa diferença de temperatura, leva tempo para o calor penetrar no calcário. Quanto menor o tamanho do calcário, menor o tempo de penetração do calor. No caso do calcário pulverizado, esse tempo pode reduzir a menos de 1 minuto. Se a retenção for muito curta, o núcleo do calcário permanece não calcinado, enquanto a superfície externa fica calcinada. Se o tempo de retenção for muito longo, o n a superfície das peças de calcário encolhe e os poros criados pelo gás CO2 escapam para perto, produzindo uma superfície impermeável. Este tipo de cal é chamado de cal queimada dura ou cal queimada. Esta cal tem uma reactividade muito baixa e não extingue bem. Além disso, um tempo de retenção mais longo significa menos produção e custos de produção mais altos.
Concentração de CO2 no forno – A concentração de CO2 na atmosfera do forno aumenta com a liberação do calcário durante a calcinação. Para uma calcinação adequada, o CO2 deve ser removido continuamente. Se o CO2 não for removido, então uma combinação de alta concentração de CO2 e alta temperatura de calcinação causa a carbonatação dos pedaços de calcário calcinado e converte CaO novamente em CaCO3. Além disso, o CO2 também reage com as impurezas do calcário.
Reatividade química – Existe uma inter-relação entre porosidade, densidade e distribuição do tamanho dos poros. Esses fatores exercem uma grande influência nas propriedades mensuráveis padrão da cal viva, como reatividade, cal disponível e distribuição de tamanho de partícula e área de superfície. Foi observado que um tempo de retenção de 1 hora a 4 horas tem muito pouco ou nenhum efeito sobre a porosidade, área de superfície ou reatividade na faixa de temperatura de calcinação de 950°C a 1070°C e a densidade aparente da cal viva permanece constante . Temperaturas de calcinação excessivas e períodos prolongados de calcinação levam à queima dura do calcário e isso resulta na produção de cal com baixa reatividade.
Característica de encolhimento – A retração da cal viva pode ser calculada a partir das densidades do calcário e da cal após considerar a perda ao fogo (LOI). É calculado pela fórmula S =100*{[100/Ds-(100-L)/Dl]/100*Ds} Onde S é o encolhimento em porcentagem, Ds é a densidade do calcário em gramas/cc, Dl é a densidade da cal viva em gramas/cc e L é a perda de ignição do calcário em porcentagem. A retração do calcário tem grande influência na densidade aparente da carga de calcário no forno. Quanto maior o encolhimento, menores são os vazios na carga de calcário. Isso resulta no empacotamento do calcário no forno, o que leva a uma alta queda de pressão no leito do forno, com a consequente influência na tiragem dos gases de combustão do forno.
Qualidade e tipo de combustível – A qualidade e o tipo de combustível têm grande influência na eficiência do forno e na qualidade da cal produzida. Combustíveis brutos sólidos, como madeira, carvão e carvão estão sendo usados desde os primeiros dias. Carvão pulverizado, gás de produção, gás natural e óleo combustível estão sendo usados nos fornos. O gás natural é o combustível mais conveniente e o gás de produção é o mais problemático. A escolha final do combustível também é determinada por considerações ambientais, uma vez que alguns combustíveis têm maior tendência a poluir o meio ambiente por meio de emissões nocivas. Normalmente, os fornos verticais usam óleo ou gás natural como combustível, enquanto os fornos horizontais rotativos usam carvão. No entanto, qualquer tipo de forno pode usar qualquer um desses combustíveis. Tanto o petróleo quanto o carvão contêm certas porcentagens de compostos de enxofre que podem variar de 0,5% a 3%. O enxofre geralmente se combina com o CaO em temperaturas apropriadas e produz sulfeto de cálcio ou sulfato de cálcio. Isso geralmente acontece na superfície do material calcinado e torna o material não poroso, reduzindo sua reatividade. Além disso, uma alta porcentagem de cinzas no carvão resulta no acúmulo nos refratários do forno rotativo, interferindo no fluxo de carga de calcário no forno. O forno deve ser resfriado periodicamente e o acúmulo de cinzas removido manualmente, o que é uma operação muito tediosa e dispendiosa. O gás natural é o combustível mais limpo e usado principalmente em fornos verticais.
O terceiro tipo de processamento do calcário consiste na produção de cal hidratada, que é um pó seco obtido por tratamento de cal viva com água suficiente para satisfazer sua afinidade química com a água, convertendo assim os óxidos em hidróxidos. A cal hidratada também é às vezes chamada de cal apagada. Para a dessulfurização dos gases de combustão, a característica da cal hidratada requer maior finura média, maior área superficial e maior volume dos poros. A reação de hidratação é quimicamente simples, mas fortemente exotérmica, com geração de calor em torno de 276 kcal/kg de CaO. A reação é dada abaixo.
CaO + H2O =Ca(OH)2 + calor
Para efeito de comparação, o calor exotérmico desenvolvido a partir da hidratação de 1.000 toneladas de cal viva com alto teor de cálcio é igual ao valor calorífico total de cerca de 35 toneladas de carvão. Os termos hidratação e slaking são usados muitas vezes de forma intercambiável. No entanto, há uma diferença definida e distinta. A hidratação é normalmente definida como um processo pelo qual quantidades estequiométricas de água e cal reagem para formar um produto, hidrato, que é um pó seco. Contém menos de 1% de umidade livre e é manuseado como um pó. A extinção, por outro lado, é definida como um processo pelo qual a cal reage com uma quantidade excessiva de água para formar uma pasta de cal que é tratada como um líquido.
A hidratação rápida é propensa a produzir as partículas mais finas, uma vez que os cristais de hidrato têm menos chances de aglomerar. No entanto, a reação mais rápida não é necessariamente a melhor condição. Em princípio, uma reação típica de cal altamente reativa se desenvolve em três fases diferentes (Fig. 3). Essas fases são denominadas (i) cinética, (ii) transitória e (iii) difusão. A fase cinética é normalmente muito curta (menos de 10 segundos) e mostra um aumento acentuado da temperatura, que pode chegar a 50% do aumento total da temperatura. A duração da fase transitória (geralmente menos de um minuto) pode mudar devido ao tamanho dos pedaços de cal que alimentam o hidratante. Mostra uma curva visível do aumento de temperatura. Na fase de difusão, a temperatura volta a subir bruscamente até se achatar rapidamente para mostrar o fim da reação.
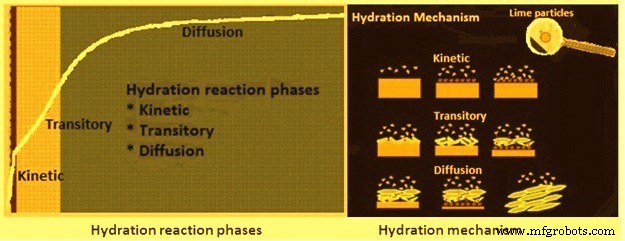
Fig 3 Fases da reação de hidratação e mecanismo de hidratação
O mecanismo de hidratação também é mostrado na Figura 3. O mecanismo de hidratação das partículas de cal mostra que após o contato inicial com a água a reação começa muito forte em poucos segundos devido ao contato desobstruído entre a cal e a água. Depois que a primeira camada de cal parcialmente hidratada é gerada na superfície, ela atua como um escudo para as camadas de cal viva por baixo, uma vez que tende a permanecer perto da superfície das partículas. Assim, a camada de cal parcialmente hidratada retarda a penetração da água. Quando os cristais de Ca(OH)2 são gradualmente formados até sua forma final, eles começam a se separar. Isso melhora a penetração de água que retoma a tendência de reação. O outro fator importante é que o desenvolvimento da reação é função do tamanho do grumo da cal viva.
Aplicação de calcário e cal em siderurgia
Durante a produção de ferro por rota de alto-forno (BF), o calcário é adicionado no processo de sinterização ou como alimentação direta no alto-forno. O calcário é normalmente adicionado durante a fabricação de ferro para obter escória BF neutra ou levemente básica. A adição de calcário através da sinterização é a rota mais preferida, uma vez que o CO2 do calcário é expelido durante o processo de sinterização. No caso de sinterização, o calcário é triturado a -3 mm (na faixa de 85% a 90%) em britadores de martelo antes de misturá-lo na mistura de sinterização. No caso de alimentação direta ao alto-forno, são utilizados pedaços de calcário de 10 mm a 40 mm.
No caso de adição de calcário por sinterização, atualmente também está sendo usado diretamente o calcário calcinado (cal). O uso de cal virgem no processo de sinterização tem as vantagens de (i) melhoria nas características de ligação da mistura de sinterização, (ii) melhoria na produtividade da máquina de sinterização, (iii) melhoria na resistência de sinterização e (iv) redução na volume de gases de escape com vantagens associadas.
O alto teor de sílica (SiO2) no calcário usado para sinterização é preferido, pois o SiO2 contraria o efeito da alumina (Al2O3) no alto-forno.
O segundo maior uso do calcário é na siderurgia. Está sendo utilizado para manter a basicidade da escória (CaO/SiO2) em torno de 3. Na siderurgia, o calcário é utilizado na forma calcinada. Para uso na fabricação de aço, o teor de SiO2 (devido à sua natureza ácida) no calcário deve ser muito baixo, de preferência inferior a 1%. Além disso, a reatividade da cal deve ser muito boa, devido ao menor tempo disponível, já que o processo de fabricação do aço é um processo muito rápido. Todo o processo de fabricação de aço leva menos de 20 minutos para ser concluído.
Os usos menores de cal (seja calcinada ou hidratada) consistem em agente dessulfurante, revestimento de moldes de máquina de fundição de porco, neutralização de água ácida, tratamento de água, tratamento de águas residuais (efluentes), tratamento de gases de combustão e tratamento de lodo e esgoto etc. às vezes também é adicionado como um componente de escória sintética.
Processo de manufatura
- Aplicação do Nióbio na Siderurgia
- Aplicação do metal molibdênio e suas ligas
- Ferro Reduzido Direto e seus Processos de Produção
- Tundish e seu papel na fundição contínua de aço
- Opções de descarga para ferro reduzido direto e seu transporte a quente
- Tendências do mercado de ferro e aço para conhecer
- Máquinas CNC e suas vantagens na engenharia industrial
- Uma visão geral sobre o aço ferramenta e suas aplicações
- Uma visão geral do aço ferramenta e suas aplicações que o acompanham
- Matérias-primas usadas na fabricação de ferro e aço