Espumação de Escória em Forno a Arco Elétrico
Espuma de escória em forno elétrico a arco
A espumação de escória tornou-se uma prática importante e crítica para o moderno forno elétrico a arco (EAF), uma vez que uma boa espumação de escória contribui com eficiência considerável e outros benefícios para o processo. A qualidade da espumação da escória é um fator importante no processo de fabricação do aço EAF, pois garante que o calor do banho líquido não seja perdido pelas paredes do EAF. A espuma de escória é benéfica para o processo de fabricação de aço EAF em termos da grande área de superfície formada e da proteção fornecida contra o contato direto do fundido com a atmosfera.
A formação de espuma de escória é uma técnica que é útil e econômica. É uma técnica muito utilizada, não só porque permite poupar energia, mas pelas várias vantagens que oferece, nomeadamente (i) aumento da eficiência energética, uma vez que o calor do arco é captado pela escória, (ii) protecção dos painéis de água e do telhado por radiação, (iii) diminuição das vibrações e poluição sonora, e (iv) diminuição da incorporação de nitrogênio pelo banho.
A formação de escória espumosa pode ser dividida em 3 etapas. Estas são (i) a etapa 1 que é a injeção de oxigênio na fase de aço líquido, (ii) a etapa 2 que é a injeção de carbono na escória e (iii) a etapa 3 que é quando o oxigênio é injetado na escória. Inicialmente, o oxigênio é injetado no metal fundido (etapa 1). Este oxigênio reage com o carbono existente formando bolhas de CO (monóxido de carbono). O oxigênio também reage com o ferro presente no banho. À medida que o ferro é perdido na forma de óxido de ferro, o carbono é injetado na escória (etapa 2), realizando a reação de redução do óxido de ferro. Essa etapa gera gás CO e também faz com que o ferro retorne ao banho, melhorando o desempenho do forno. Na etapa 3, o oxigênio é injetado na escória, para causar a oxidação do carbono presente na escória. Nesta etapa, carbono e oxigênio também podem ser injetados simultaneamente, permitindo melhor geração de CO e melhor formação de espuma.
Normalmente existe uma densa camada de escória sob a espuma. No entanto, é possível que toda a escória presente seja necessária para produzir a espuma e não exista nenhuma camada densa. Nesse caso, a quantidade de escória presente é insuficiente para produzir toda a espuma que a escória e o gás podem formar.
Também foi relatado que o processo de formação de espuma de escória pode economizar 3% a 10% e 25% a 63% do consumo de energia e refratário, respectivamente. Existem basicamente dois requisitos para a formação de espuma, a saber (i) reações ou processos que geram pequenas bolhas de gás e (ii) propriedades de escória adequadas para manter as bolhas como espuma estável. Normalmente, gases resultantes de reações químicas tendem a espumar a escória com bolhas menores, enquanto a injeção de fases gasosas (oxigênio, argônio, etc.) resulta em bolhas maiores e espumas menos estáveis.
Uma certa espumabilidade das escórias usadas para o processo EAF é desejada, por várias razões. Durante o processo, a escória espumante protege os eletrodos de grafite do desgaste e cobre os arcos. Isso permite uma maior produtividade no forno, pois aumenta a transferência de calor entre o eletrodo e o metal fundido. Também reduz as perdas de radiação, pois a escória isola os feixes de luz. Isso, por sua vez, protege os refratários do desgaste, o que reduz o tempo de inatividade para trabalhos de manutenção. A escória espumante também contribui para a estabilização do arco, garantindo maior eficiência. Além disso, a espuma ajuda a reduzir o ruído do EAF, o que proporciona um melhor ambiente de trabalho. Outra vantagem da escória espumante é a redução das flutuações de potência e tensão.
As consequências de uma boa escória espumante no EAF e seu controle adequado incluem (i) a diminuição dos harmônicos devido à imersão do eletrodo na escória pode aumentar a potência nas mesmas configurações do transformador em 6% a 9%, (ii) um aumento na potência em 15% quando as pontas dos eletrodos estão de 300 mm a 600 mm de profundidade na escória devido ao plasma de arco mais quente ao redor da ponta do eletrodo, e (iii) uma boa escória espumante permite que os queimadores de oxigênio-combustível (quando usados) soprem no escória, aumentando a eficiência energética dos queimadores de 40% para 70%. No entanto, para obter o máximo benefício de uma escória espumante, a escória deve ser construída no início do calor e a química da escória deve ser rigidamente controlada limitando a descarga da escória e colocando cal ou carepa de laminação no fundo da primeira carga balde. Os benefícios térmicos de uma boa escória espumante são devidos ao deslocamento no caminho de transferência de calor para o banho e para longe das paredes laterais. De acordo com um estudo, as variações na qualidade da escória espumante podem responder por +/- 0 kWh/t na demanda de energia elétrica
É útil saber o que se entende por espuma de escória. A geração de gás é indispensável para ter sucesso com uma prática de escória espumante. O gás é gerado principalmente pela redução de óxido de ferro (FeO) com carbono formando CO-gás. O gás faz com que bolhas de espuma se formem no topo de uma densa camada de escória. A espuma pode ser bolhas de espuma relativamente pequenas, como espuma na cerveja ou bolhas maiores, como espuma de bolha de sabão na água. As pequenas bolhas resultam de reações químicas e a espuma resultante é bastante estável. A injeção de gás, no entanto, produz bolhas maiores e espuma menos estável. A verdadeira formação de espuma não deve ser confundida com a simples retenção de gás de bolhas em um líquido. No caso de retenção de gás, as bolhas de gás são distribuídas por todo o líquido e a expansão da escória é devido às bolhas de gás no líquido. Para retenção de gás, a expansão decai rapidamente após o gás parar. A espuma verdadeira pode ser bastante estável e permanecer assim por vários minutos após a interrupção da geração de gás.
A reação de geração de bolhas de gás, a redução de FeO na escória por adição de carbono e carbono dissolvido no metal. No processo de formação de espuma de escória, o carbono é injetado na escória, reage com o óxido de ferro na escória para produzir gás CO, que espuma a escória. A reação é dada por C (injetado) + (FeO) =Fe + CO. O gás CO para formação de espuma também é produzido pela descarbonetação do metal dada pela reação C (no metal) + 1/2 O2 =CO. O FeO é gerado in situ como o principal produto de oxidação do sopro de oxigênio e, portanto, é o principal componente da escória (superior a 20%). Se a consistência da escória for adequada para sustentar a espuma, a simples injeção de carbono na escória faz com que a escória espume. A taxa de redução relativamente alta dá ao FeO o potencial de gerar uma grande quantidade de gás dentro da espuma. A taxa de redução de FeO por carbono é consideravelmente rápida. Além disso, a reação de redução também consome calor, o que resulta em um aumento local da viscosidade da escória.
As variáveis do processo que afetam a formação de espuma são composição da escória, velocidade superficial do gás, temperatura do banho, tamanho da bolha, basicidade da escória, densidade da escória, viscosidade da escória e tensão superficial da escória. A velocidade superficial do gás é normalmente medida em metros por segundo (m/s) e é a velocidade real do gás multiplicada pela fração de volume do gás.
O índice de espumação (FI) é um parâmetro importante para a espumação da escória. Pode ser visto como o tempo para o gás passar pela escória. É uma indicação da extensão da espuma e é a razão entre a altura da espuma e a velocidade superficial do gás. Assim, a unidade do FI é o tempo que normalmente é em segundos. Assim, o FI pode ser interpretado como uma medida do tempo que leva para os gases do processo passarem verticalmente pela espuma. O FI está relacionado com as propriedades da escória, como a viscosidade. Quanto maior a viscosidade, maior o FI. A consequência óbvia é que um aumento da viscosidade leva automaticamente a um aumento da altura da espuma.
O FI diminui com o aumento do tamanho da bolha. É geralmente visto que pequenas bolhas são formadas pela primeira reação dada acima e resulta uma espuma relativamente estável. Na fabricação de aço EAF, verificou-se que, no final do processo, a espuma torna-se menos estável e a altura da espuma diminui. Isso acontece porque inicialmente à medida que o teor de FeO aumenta, a taxa de reação do punho e a geração de CO aumentam e, portanto, a formação de espuma aumenta. No entanto, à medida que o teor de FeO aumenta, a viscosidade da escória diminui e a densidade aumenta, fazendo com que as bolhas de espuma drenem mais rapidamente, diminuam e a espuma decaia. Portanto, existe um teor crítico de FeO abaixo do qual a formação de espuma aumenta com o teor de FeO e acima do qual a espuma é menos estável. Isso ocorre em torno de 20% a 40% de FeO, dependendo de outras condições.
A formação de espuma de escória quando foi introduzida foi auxiliada pela injeção de pó de grafite feito de eletrodos (80% de malha -200) na interface metal-escória usando equipamento de injeção adequado com ar como gás de arraste. Através de cálculos anteriores e procedimentos de tentativa e erro, verificou-se que uma vazão mássica de grafite igual a 25 kg/min era boa o suficiente para produzir espuma estável. Valores superiores a este, no início de uma bateria, promoviam um forte slopping de escória afetando as operações no piso de trabalho e tornando os arcos elétricos instáveis dificultando as operações com arcos longos de alta tensão e baixa corrente.
No processo de fabricação de aço EAF, a operação de arco longo ocorre em conjunto com uma prática de escória espumosa. Ao espumar a escória através da injeção de carbono, a altura da camada de escória pode ser elevada até cobrir completamente os arcos, interceptando a radiação do arco e o flare, transferindo o calor para o banho e reduzindo a carga térmica nas paredes laterais. No entanto, se uma boa escória espumante não puder ser mantida, é preferível reduzir a tensão secundária e, portanto, o comprimento do arco para evitar o risco de danos à estrutura do forno.
O fenômeno de formação de espuma de escória é dependente das propriedades da escória e da taxa de evolução do gás, devido às reações na escória. Assim, para obter espuma em uma escória, é necessário um fluxo de gás. O fluxo de gás é gerado quando carbono (C) e oxigênio gasoso (O2) são adicionados à escória e ao banho de metal, respectivamente. O controle da altura de espuma é necessário para manter uma operação estável.
Dependendo das propriedades físicas da escória (que são influenciadas pela composição e temperatura), a formação de espuma ocorre em graus variados. Na siderurgia EAF é bastante comum que o carbono (na forma de coque ou carvão) seja adicionado à camada de escória. O consumo de carbono ocorre através da reação de Boudouard e, portanto, a taxa de geração de CO é proporcional à taxa de adição de carbono a uma escória de EAF, uma vez que a reação atingiu o estado estacionário.
A formação de espuma da escória é significativamente afetada pelo fluxo de gás no forno, mas também é afetada pelas propriedades da escória, esta última controlada pela viscosidade, densidade e tensão superficial. Essas propriedades físicas são, por sua vez, dependentes da temperatura do sistema e da composição da escória.
Para o processo EAF, a composição da escória depende do grau do aço, bem como do método de refinamento utilizado. Ao escolher uma composição para a escória, várias coisas devem ser consideradas. A escória é composta por vários óxidos, que podem ser divididos em três categorias, a saber (i) óxidos básicos (como CaO, MgO e FeO), óxidos ácidos (como SiO2) e óxidos anfotéricos (como Al2O3). Para escórias básicas, o teor de FeO é geralmente considerado em um nível ótimo variando de 15% a 25%. Para formar espuma em uma escória, a viscosidade precisa ser alta o suficiente para constituir um obstáculo para a ascensão das bolhas. Para obter uma viscosidade adequada, é importante ter uma basicidade adequada da escória. A basicidade é geralmente referida como a razão dos componentes básicos na escória para os componentes ácidos. Os componentes básicos fornecem os íons O2 ao fundido e os componentes ácidos os ligam. A viscosidade pode ser alterada através de uma mudança de composição, que provoca uma mudança na relação CaO/SiO2, diminuindo ou aumentando a basicidade da escória.
Uma mudança de viscosidade também pode ser alcançada através de uma alteração do teor de FeO. Ao aumentar a quantidade de FeO, a viscosidade é reduzida. Outra maneira de modificar a viscosidade da escória é aumentar a quantidade de partículas sólidas na escória, por exemplo, pela adição de cal. Foi observado que a viscosidade da escória diminui com o aumento da basicidade, mas quando passa de um valor crítico e uma fase sólida é precipitada, ela aumenta novamente. Assim, a presença de partículas sólidas contribui para um aumento da viscosidade aparente. As partículas sólidas também atuam como sítios de nucleação para as bolhas. No entanto, uma quantidade excessiva de partículas sólidas impede que as bolhas subam pela escória.
Em um sistema de líquidos, um gradiente de tensão superficial ou interfacial pode induzir movimento. Isso é chamado de efeito Marangoni. Na interface entre escórias e metais líquidos geralmente existe um grande gradiente de tensão interfacial. A concentração de FeO é considerada menor do que no restante da escória na interface entre escória e metal, onde ocorrem reações que formam CO. Isso permite a formação de bolhas, uma vez que menor teor de FeO resulta em menor tensão superficial, o que dá origem ao efeito Marangoni. Assim, a capacidade de criar novas superfícies, que ocorre quando bolhas são formadas na escória, é facilitada quando a tensão superficial é baixa.
A tensão superficial também afeta a degradação da espuma, referindo-se à estabilidade das bolhas. Vários estudos mostraram que a estabilidade pode ser melhorada pela adição de um componente ativo de superfície. Também foi observado no processo de fabricação do aço que a presença de componentes ativos de superfície promove a formação de espuma. No entanto, o fluxo de Marangoni, que auxilia na remoção de bolhas de CO da interface, pode ser gerado sem elementos ativos de superfície. A densidade da escória afeta a altura da espuma. Uma baixa densidade significa que há menos peso para suportar, o que permite uma maior altura da espuma, em comparação com uma escória com alta densidade. Para suportar a carga, a superfície precisa ter propriedades elásticas. Isso pode ser alcançado através da adição de elementos ativos de superfície que resultam em uma tensão superficial variável.
A escória espumante nas operações siderúrgicas resulta da geração de bolhas de CO, através das reações de redução, (i) CO2 + C(s) =2CO (a reação de Boudouard), (ii) CO + Fe2O3 =CO2 + 2FeO, (iii) CO + FeO =CO2 + Fe, e (iv) C(s) + FeO =CO + Fe. A reação de Boudouard e a redução de FeO por carbono sólido são reações altamente endotérmicas, enquanto a redução de Fe2O3 por CO é neutra em energia e a redução de FeO por CO é apenas ligeiramente exotérmica. É importante notar que o óxido de ferro é a fonte para o componente de oxigênio necessário para a combustão do carbono, não o oxigênio gasoso e, portanto, alguma oxidação do banho de aço é necessária para a formação de espuma de escória.
A força motriz para a formação de espuma de escória é uma energia pneumática fornecida pela geração de CO durante o processo de fusão-refinação no EAF. No processo de espumação da escória, o carbono é injetado na escória, reage com o óxido de ferro (FeO) na escória para produzir monóxido de carbono (CO), que espuma a escória. A reação é dada por C (injetado) + (FeO) =Fe + CO. O CO para formação de espuma também é produzido pela descarbonetação do metal dada pela reação C (no metal) + 1/2 O2 =CO. Essas reações são responsáveis para a formação de CO. A segunda reação representa uma reação direta entre oxigênio gasoso e carbono em banho, enquanto a primeira reação é uma reação direta de redução de óxido de ferro por carbono na escória. Todas essas reações são formadoras de CO dando energia de agitação para transferência de massa entre as fases de escória metálica, carbono e gás e podem ser consideradas como uma condição necessária para a formação de espuma de escória. Algumas reações são consumidoras de CO como (i) CO + Fe2O3 =CO2 + 2FeO, e (ii) CO + FeO =CO2 + Fe, que pode ser controlada pela reação de Boudouard CO2 + C(s) =2CO.
Os locais dessas reações podem ser localizados como (i) na interface metal-escória, (ii) na interface metal-gás, (iii) na interface escória de carbono e (iv) nas interfaces gás-escória e gás-carbono . A Fig. 1 mostra um diagrama esquemático de reações químicas para formação de espuma de escória em EAF. O diagrama mostra os locais de reação durante a injeção de carbono durante os processos de fusão-refinação do aço em um EAF. Pode ser visto a partir do diagrama que a formação de CO é uma função muito complexa de várias variáveis de processo que consistem em tamanho, tipo e vazão mássica do material carbonáceo, vazão do gás de arraste, teor de carbono no banho, química da escória e escória-metal. área interfacial etc.
Fig 1 Diagrama esquemático de reações químicas para formação de espuma de escória em EAF
Por outro lado, é necessário cumprir outra condição para a formação de espuma de escória. Esta condição está diretamente relacionada às propriedades de transporte (que afetam a estabilidade da espuma) das escórias de aciaria em temperaturas de refino. FI da escória determina essas propriedades. FI é medido em unidades de tempo, isto é, segundos e é uma função da química da escória. As curvas de estabilidade para FI das escórias são mostradas na Fig. 2. As inferências das curvas são dadas abaixo.
- As escórias ácidas têm o maior índice de formação de espuma, o que pode ser chamado de espuma homogênea.
- Escórias com baixo teor de óxido de ferro (menos de 10%) formam espuma mais estável do que escórias altamente oxidadas (mais de 40% FeO em qualquer basicidade) que, portanto, podem ser chamadas de escórias não espumantes.
- Em baixos teores de óxido de ferro, a basicidade da escória influencia fortemente a estabilidade da espuma. Em basicidades mais altas, sob um determinado teor de óxido de ferro, FI diminui. Em altos teores de óxido de ferro, a basicidade da escória não desempenha nenhum papel.
- As escórias com teores intermediários de óxido de ferro e altas basicidades próximas à zona de saturação de cal também possuem FIs intermediários e a presença de partículas sólidas de solução de cal pode auxiliar na estabilização da formação de espuma. Por esse motivo, essa zona pode ser chamada de espuma heterogênea.
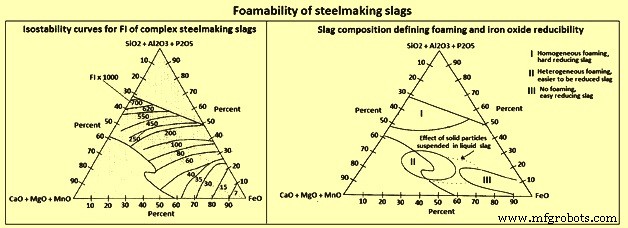
Fig 2 Espumabilidade das escórias de aciaria
A Fig. 2 também mostra a composição da escória e a formação de espuma. Partículas sólidas que estão suspensas na escória líquida afetam sua viscosidade. Observa-se normalmente que com apenas 20% de fração volumétrica de partículas sólidas na escória líquida, há um aumento de duas vezes na viscosidade da escória e a zona para formação de espuma heterogênea pode ser consideravelmente ampliada, abrangendo parcialmente a zona não espumante, como é mostrado pela linha pontilhada na Fig 2.
Para se ter uma visão mais completa da formação de espuma da escória durante a injeção de carbono, a atividade do óxido de ferro em escórias complexas tem sido objeto de vários estudos. Esses estudos mostraram o seguinte.
- A zona espumante homogênea com baixa atividade de óxido de ferro (menos de 10%) mostra uma forte resistência à redução de ferro por carbono, não apenas devido às baixas atividades de óxido de ferro, mas principalmente devido à natureza tensoativa da sílica nas escórias. A redução de ferro nesta zona é mista controlada por transferência de massa e mecanismos de reação química.
- As escórias altamente oxidadas são facilmente reduzidas pelo carbono, pois as atividades do óxido de ferro são altas o suficiente, mas não formam espumas estáveis.
- Composições normais de escórias siderúrgicas observam um comportamento intermediário. No entanto, as escórias finais tendem a ser muito oxidadas.
Crítico para manter a escória espumante é o monitoramento de sua condição. Quando a espuma de escória foi introduzida pela primeira vez, ela foi monitorada manualmente, os operadores do forno usando seus olhos e ouvidos, juntamente com sua experiência, para julgar se a escória estava correta ou não e as etapas necessárias para corrigi-la. A partir de meados da década de 1980, o monitoramento eletrônico e o controle computadorizado da formação de espuma de escória foram introduzidos, com vários sinais possíveis estudados, como distorção do arco, ruído do arco e emissões de luz. Atualmente, a distorção do arco parece ser o sinal mais amplamente utilizado nas operações do forno AC para monitorar a condição da espuma, pois os sensores e programas necessários são frequentemente integrados ao sofisticado regulador de eletrodo. Muitos EAFs utilizam harmônicos gerados na alimentação elétrica pelos arcos como um monitor de escória espumante, pois uma escória espumante melhor leva a um arco mais estável e menos harmônicos. O monitoramento por meio de emissões de som e luz do EAF também foi tentado como um método de monitoramento de espuma.
A formação de espuma em EAF, no entanto, tornou-se parte integrante do processo de fabricação de aço, especialmente durante a fase de refino do calor. O atual processo de arco longo maximiza a transferência de energia para a sucata ao redor dos eletrodos e arcos. Assim, a sucata intercepta a maior parte da radiação do arco e pouco passa para as paredes laterais.
No entanto, uma vez que a sucata derrete, toda a radiação do arco pode colidir com as paredes laterais. Ao cobrir o máximo possível do arco exposto, uma escória espumante intercepta essa energia, impede que ela atinja as paredes e a passa para o banho de aço. A escória espumante pode ser acumulada lentamente à medida que a sucata derrete e as paredes laterais e o teto do forno ficam progressivamente expostos ao calor irradiado dos arcos, atingindo uma altura máxima durante o estágio de refino do calor. O carbono e o CO injetados também ajudam a reduzir qualquer óxido de ferro na escória de volta ao ferro metálico.
Processo de manufatura
- Guitarra elétrica
- Chaleira Elétrica de Chá
- Cobertor Elétrico
- Automóvel elétrico
- Escória de alto forno e seu papel na operação do forno
- Automação de Controle e Modelagem de Forno Elétrico a Arco
- Granulação de escória de alto-forno na casa de fundição
- Utilização de Metal Quente para Siderurgia em Forno a Arco Elétrico
- Diferentes tipos de processo de soldagem a arco elétrico
- Entendendo a soldagem a arco elétrico