Automóvel elétrico
Antecedentes
Ao contrário do automóvel movido a gás, o automóvel elétrico não se desenvolveu facilmente em um meio de transporte viável. No início do século XX, o carro elétrico foi perseguido vigorosamente por pesquisadores; no entanto, o automóvel movido a gasolina facilmente produzido em massa esmagou o interesse no projeto. A pesquisa diminuiu de 1920-1960 até que as questões ambientais de poluição e diminuição dos recursos naturais despertaram a necessidade de um meio de transporte mais ecológico. As tecnologias que suportam uma bateria confiável e o peso do número necessário de baterias elevaram o preço de fabricação de um veículo elétrico. Do lado positivo, os eletrônicos automotivos se tornaram tão sofisticados e pequenos que são ideais para aplicações em veículos elétricos.
História
O desenvolvimento inicial do automóvel concentrava-se na energia elétrica em vez da energia a gasolina. Em 1837, Robert Davidson, da Escócia, parece ter sido o construtor do primeiro carro elétrico, mas foi somente na década de 1890 que os carros elétricos foram fabricados e vendidos na Europa e na América. Durante o final da década de 1890, as estradas dos Estados Unidos eram ocupadas por mais automóveis elétricos do que aqueles com motores de combustão interna.
Um dos construtores de carros elétricos de maior sucesso nos Estados Unidos foi William Morrison, de Des Moines, Iowa, que começou a comercializar seu produto em 1890. Outros pioneiros incluíram SR e Edwin Bailey, uma equipe de pai e filho de fabricantes de carruagens em Amesbury, Massachusetts , que instalou um motor elétrico e bateria em uma de suas carruagens em 1898. A combinação era muito pesada para a carruagem puxar, mas os Baileys persistiram até 1908, quando produziram um modelo prático que podia viajar cerca de 80 km antes a bateria precisava ser recarregada.
Grande parte da história do carro elétrico é na verdade a história do desenvolvimento da bateria. A bateria de chumbo-ácido foi inventada por H. Tudor em 1890, e Thomas Alva Edison desenvolveu a bateria de níquel-ferro em 1910. A versão de Edison aumentou a produção de carros e caminhões elétricos, e o próprio inventor estava interessado no futuro do elétrico carro. Ele combinou esforços com os Baileys quando eles instalaram uma de suas novas baterias de armazenamento em um de seus veículos e o promoveram em uma série de demonstrações públicas. A Bailey Company continuou a produzir carros elétricos até 1915 e estava entre as mais de 100 empresas de automóveis elétricos que prosperaram no início do século apenas nos Estados Unidos. A Detroit Electric Vehicle Manufacturing Company foi a última a sobreviver e encerrou as operações em 1941.
Os automóveis elétricos eram populares porque eram limpos, silenciosos e fáceis de operar; no entanto, dois desenvolvimentos melhoraram tanto o veículo movido a gasolina que a competição era inexistente. Em 1912, Charles Kettering inventou a partida elétrica que eliminou a necessidade de uma manivela. Ao mesmo tempo, Henry Ford desenvolveu um processo de linha de montagem para fabricar seu carro Modelo T. A montagem foi eficiente e menos onerosa do que a fabricação do veículo elétrico. Assim, o preço de um veículo movido a gás diminuiu o suficiente para tornar viável para todas as famílias comprar um automóvel. Apenas carrinhos elétricos, veículos de entrega que faziam paradas frequentes e alguns outros veículos movidos a eletricidade sobreviveram após a década de 1920.
Na década de 1960, o interesse pelo carro elétrico voltou a crescer devido ao aumento do custo e à diminuição da oferta de petróleo e à preocupação com a poluição gerada pelos motores de combustão interna. O ressurgimento do carro elétrico na última parte do século XX foi, no entanto, repleto de problemas técnicos, sérias questões relativas a custo e desempenho e crescente e decrescente interesse público. Os crentes defendem os carros elétricos para baixo consumo e custo de energia elétrica, baixos requisitos e custos de manutenção, confiabilidade, emissão mínima de poluentes (e conseqüente benefício para o meio ambiente), facilidade de operação e baixo ruído.
Parte do interesse reavivado foi impulsionado por regulamentos. A legislatura da Califórnia determinou que 2% dos carros novos vendidos no estado fossem movidos por motores de emissão zero até 1998. Essa exigência aumenta para 4% até 2003. Os fabricantes investiram em carros elétricos com base no pressuposto de que o interesse público seguiria a regulamentação e o suporte proteção da qualidade do ar e do meio ambiente. A General Motors (GM) introduziu o Impact em janeiro de 1990. O Impact tinha uma velocidade máxima de 110 mph (176 km / h) e podia viajar 120 mi (193 km) a 55 mph (88 km / h) antes de uma parada de recarga. O impacto era experimental, mas, mais tarde, em 1990, a GM começou a transformar o carro de teste em um modelo de produção. As baterias eram o ponto fraco desse carro elétrico, pois precisavam ser substituídas a cada dois anos, dobrando o custo do veículo em comparação com as despesas operacionais de um modelo a gasolina. As estações de recarga não estão amplamente disponíveis, e essas complicações de inconveniência e custo dissuadiram os compradores em potencial. Em 1999, a Honda anunciou que descontinuaria a produção de seu carro elétrico, que foi introduzido no mercado em maio de 1997, citando a falta de apoio público devido a esses mesmos impedimentos.
Componentes
Ao contrário das baterias primárias que têm uma vida útil limitada de reações químicas que produzem energia, as baterias do tipo secundário encontradas em veículos elétricos são células de armazenamento recarregáveis. As baterias estão situadas em formação em T no meio do carro com a parte superior do "T" na parte traseira para fornecer melhor distribuição de peso e segurança. As baterias para carros elétricos têm sido feitas com níquel-ferro, níquel-zinco, zinco-cloreto e chumbo-ácido.
O peso do carro elétrico também tem sido uma dificuldade recorrente no design. Em carros elétricos, a bateria e o sistema de propulsão elétrica são normalmente 40% do peso do carro, enquanto em um carro movido a combustão interna, o motor, o sistema de refrigeração e outros dispositivos de alimentação específicos somam apenas 25% do peso de o carro.
Outras tecnologias em desenvolvimento podem fornecer alternativas mais aceitáveis para o público e com baixas (senão zero) emissões. O uso da célula de combustível em um automóvel híbrido é o desenvolvimento mais promissor no horizonte, a partir de 1999. O automóvel híbrido tem duas usinas, uma elétrica e um motor de combustão interna. Eles operam apenas nas condições mais eficientes para cada um, com energia elétrica para parar e arrancar em baixas velocidades e propulsão a gasolina para velocidades e distâncias em rodovias. O motor elétrico conserva gasolina e reduz a poluição, e a parte movida a gasolina torna as paradas inconvenientes para recarga menos frequentes.
As células a combustível têm uma fonte química de hidrogênio que fornece elétrons para a geração de eletricidade. Etanol, metanol e gasolina são essas fontes químicas; se a gasolina for usada, as células de combustível se consomem com mais eficiência do que o motor de combustão interna. Protótipos de células de combustível foram testados com sucesso, e os japoneses começaram a fabricar um veículo híbrido em 1998. Outra esperança futura para automóveis elétricos é a bateria de íon-lítio, que tem uma densidade de energia três vezes maior do que uma bateria de chumbo-ácido. Três vezes o armazenamento deve levar a três vezes o intervalo, mas o custo de produção ainda é muito alto. As baterias de lítio agora estão se revelando as mais promissoras, mas o fornecimento limitado de matéria-prima para fazer todas essas variedades de baterias prejudicará a probabilidade de todos os veículos serem convertidos para energia elétrica.
Matérias-primas
O esqueleto do carro elétrico é chamado de estrutura espacial e é feito de alumínio para ser forte e leve. As rodas também são feitas de alumínio em vez de aço, novamente como um método de redução de peso. As peças de alumínio são vazadas em uma fundição usando moldes especialmente projetados e exclusivos do fabricante. As armações dos assentos e o coração do volante são feitos de magnésio, um metal leve. O corpo é feito de um plástico composto resistente a impactos que é reciclável.
As baterias de carros elétricos consistem em invólucros de plástico que contêm ânodos e cátodos de metal e fluido chamado eletrólito. Atualmente, as baterias de chumbo-ácido ainda são usadas com mais frequência, embora outras combinações de fluidos e metais estejam disponíveis com baterias de hidreto de metal de níquel (NiMH), a próxima fonte de energia mais provável no horizonte de carros elétricos. Baterias de carros elétricos retêm seu fluido em almofadas absorventes que não vazarão se forem rompidas ou perfuradas durante um acidente. As baterias são fabricadas por fornecedores especializados. Um carro elétrico como o General Motors EV1 contém 26 baterias em uma unidade em forma de T.
O motor ou sistema de tração possui peças de metal e plástico que não precisam de lubrificantes. Também inclui eletrônicos sofisticados que regulam o fluxo de energia das baterias e controlam sua conversão em potência motriz. Os componentes eletrônicos também são componentes essenciais para o painel de controle alojado no console; o sistema de computador de bordo opera portas, janelas, um sistema de monitoramento da pressão dos pneus, ar-condicionado, partida do carro, CD player e outras facilidades comuns a todos os carros.
Plásticos, enchimento de espuma, vinil e tecidos formam a tampa do painel, forros das portas e assentos. Os pneus são de borracha, mas, ao contrário dos pneus padrão, são projetados para inflar a pressões mais altas, de modo que o carro rola com menos resistência para economizar energia. Os pneus dos carros elétricos também contêm selante para selar automaticamente eventuais vazamentos, também para economia de energia elétrica. Os pneus autovedantes também eliminam a necessidade de um pneu sobressalente, outro recurso de economia de peso e material.
O pára-brisa é de vidro solar que evita o superaquecimento do interior ao sol e a formação de geada no inverno. Os materiais que fornecem conservação térmica reduzem o consumo de energia que o aquecimento e o ar condicionado impõem às baterias.
Design
Os carros elétricos de hoje são descritos como "veículos elétricos de produção da era moderna" para distingui-los da série de falsos começos ao tentar projetar um carro elétrico com base em modelos de produção existentes de carros movidos a gasolina e de carros de "kit" ou carros elétricos de engenharia privada que pode ser divertido e funcional, mas não digno de produção. De 1960 a 1980, o interesse pelo carro elétrico foi profundo, mas o desenvolvimento foi lento. O obstáculo do projeto da alta demanda de energia das baterias não pôde ser resolvido pela adaptação dos projetos. Finalmente, no final da década de 1980, os engenheiros automotivos repensaram o problema desde o início e começaram a projetar um carro elétrico do zero, levando em consideração a aerodinâmica, o peso e outras eficiências de energia.
A estrutura espacial, as estruturas dos assentos, as rodas e o corpo foram projetados para oferecer alta resistência para segurança e o peso mais leve possível. Isso significou novas configurações que fornecem suporte para os componentes e ocupantes com massa mínima e uso de materiais de alta tecnologia, incluindo alumínio, magnésio e plásticos compostos avançados. Como não há sistema de escapamento, a parte inferior é aerodinâmica com uma barriga cheia. Todos os detalhes extras tiveram que ser eliminados, deixando o conforto que os motoristas acham desejável e adicionando novas considerações exclusivas aos automóveis elétricos. Um detalhe eliminado foi o estepe. O detalhe das antenas de rádio em forma de haste foi removido; causa resistência ao vento que rouba energia e usa energia para aumentá-la e diminuí-la. Uma consideração adicional foi o sistema de alerta de pedestres; testes de protótipos mostraram que os carros elétricos andam tão silenciosamente que os pedestres não os ouvem se aproximando. Luzes piscantes ativadas pelo motorista e bipes avisam os pedestres que o carro está se aproximando e funcionam automaticamente quando o carro dá ré. Os pára-brisas de vidro solar também foram um acréscimo importante para regular a temperatura interior e minimizar a necessidade de ar condicionado e aquecimento.
Entre as muitas outras características de design e engenharia que devem ser consideradas na produção de carros elétricos estão as seguintes:
- As baterias que armazenam energia e acionam o motor elétrico são uma ciência própria no design de carros elétricos, e muitas opções estão sendo estudadas para encontrar as baterias mais eficientes que também sejam seguras e econômicas. Um motor elétrico que converte energia elétrica da bateria e a transmite para o trem de força. Os motores de corrente contínua (DC) e de corrente alternada (AC) são usados nesses sistemas de tração ou propulsão para carros elétricos, mas os motores AC não usam escovas e exigem menos manutenção.
- Um controlador que regula o fluxo de energia da bateria para o motor permite velocidade ajustável. Os resistores que são usados para esse propósito em outros dispositivos elétricos não são práticos para carros porque eles próprios absorvem muita energia. Em vez disso, são usados retificadores controlados de silício (SCRs). Eles permitem que a potência total vá da bateria para o motor, mas em pulsos, de forma que a bateria não fique sobrecarregada e o motor não tenha potência insuficiente.
- Qualquer tipo de freio pode ser usado em automóveis elétricos, mas os sistemas de frenagem regenerativos também são preferidos em carros elétricos porque eles recapturam parte da energia perdida durante a frenagem e a canalizam de volta para o sistema de bateria.
- Duas variedades de carregadores são necessárias. Um carregador de tamanho normal para instalação em uma garagem é necessário para recarregar o carro elétrico durante a noite, mas um recarregador portátil (chamado de recarregador de conveniência) é um equipamento padrão para o porta-malas para que as baterias possam ser recarregadas em uma emergência ou fora de casa ou um estação para carregar. Por segurança, foi criado um carregador indutivo para carros elétricos com uma pá que é inserida na frente do carro. Ele usa energia magnética para recarregar as baterias e limitar o potencial de eletrocussão.
O processo de fabricação
O processo de fabricação exigia quase tanta consideração de design quanto o próprio veículo; e esse design inclui artesanato e simplificação, bem como algumas abordagens de alta tecnologia. Os montadores trabalham em equipes de estação de construção para promover o espírito de equipe e apoio mútuo, e as peças são armazenadas em unidades modulares chamadas cremalheiras de tubos de plástico flexíveis e juntas que são fáceis de preencher e reformar para diferentes peças. No lado da alta tecnologia, cada estação é equipada com uma chave de torque com várias cabeças; quando o montador trava no tamanho apropriado do cabeçote, os controles do computador para a máquina selecionam a configuração de torque correta para os prendedores que se encaixam naquele cabeçote.
Body Shop
A carroceria do carro elétrico é feita à mão em seis estações de trabalho.
- 1 Partes da estrutura espacial de alumínio são colocadas juntas em seções chamadas subconjuntos que são construídos com peças pré-fabricadas que são soldadas ou coladas. A cola é um material adesivo e fornece uma conexão mais durável e rígida do que a soldagem. À medida que os subconjuntos para o chassi do carro são concluídos, eles são unidos entre si até que todo o chassi esteja concluído.
- 2 Os subconjuntos da parte superior do corpo também são unidos para formar seções maiores. As seções concluídas são soldadas ou coladas de forma semelhante até que a estrutura do corpo seja concluída. O corpo é adicionado à parte inferior. O adesivo usado durante a montagem em estágios da estrutura é então curado ao transportar o corpo por um forno de dois estágios.
- 3 O telhado está conectado. Como outras partes do exterior, já foi pintado. A parte inferior da carroceria e o resto da estrutura são revestidos com selantes de proteção e a carroceria acabada é movida para a área de montagem geral.
Assembleia geral
A montagem geral dos componentes operacionais e do interior do carro elétrico é concluída em outras oito estações de trabalho.
- Na primeira estação de montagem, o primeiro conjunto de eletrônicos complexos do carro elétrico é colocado no lugar. Isso inclui a fiação do corpo e o assento do compartimento de eletrônicos de energia que contém o Módulo de Controle de Propulsão, a unidade de acionamento integrada e um pequeno radiador. A unidade de acionamento integrada consiste no motor de indução de corrente alternada e em uma redução de engrenagem e diferencial de dois estágios. Essas unidades são pré-montadas em seus
O processo de fabricação usado para fazer um veículo elétrico é tão complexo quanto o projeto do veículo. São necessárias seis estações de trabalho para criar a carroceria de um veículo elétrico. Cada estação está equipada com uma chave dinamométrica com várias cabeças; quando o montador trava no tamanho apropriado do cabeçote, os controles do computador para a máquina selecionam a configuração de torque correta para os prendedores que se encaixam naquele cabeçote. próprias caixas. Os componentes do console de controle também são instalados.
- O interior é equipado. Pisos, bancos, carpetes, console e painel são colocados no carro. O processo é simples porque o painel de instrumentos e a tampa do console são feitos de uretano reforçado com fibra de vidro moldado que foi revestido com mais uretano de qualidade de acabamento e com uma superfície não refletiva. Essas duas peças são fortes e não precisam de outros suportes, suportes ou placas de montagem. A montagem é direta e o desempenho é superior porque menos peças reduzem as possibilidades de chocalhos e rangidos.
- Na terceira estação de trabalho, o sistema de ar condicionado, aquecimento e circulação é inserido e o sistema é abastecido.
- A bateria é adicionada. A unidade em forma de T é assentada levantando a mochila pesada usando um guincho especial para cima do carro. O pacote é preso ao chassi, assim como os eixos completos com rodas e pneus. Com as baterias e a unidade de propulsão instaladas, o carro não precisa mais ser movido de uma estação para outra em carrinhos especialmente projetados. Em vez disso, ele é direcionado para as estações de trabalho restantes. O sistema é ligado e verificado antes de ser direcionado para a próxima equipe.
- O pára-brisa é instalado e outros fluidos são adicionados e verificados. Os sistemas de portas (completos com interiores de vinil, apoios de braço, eletrônicos e janelas) também estão fixados e todas as conexões são concluídas e verificadas. Os painéis externos são adicionados. Semelhante ao telhado e às portas, eles foram preparados e pintados antes de serem levados para a estação de trabalho. O acabamento final é anexado para completar o exterior superior.
- Na estação de trabalho final, o alinhamento é verificado e ajustado e o painel sob a carroçaria é aparafusado no lugar. O processo termina com a última e abrangente verificação de controle de qualidade. Água pressurizada é borrifada no veículo por oito minutos, e todas as vedações são verificadas quanto a vazamentos. Em uma pista de teste especializada, o carro é verificado quanto a ruídos, guinchos e chocalhos em um test drive baseado na qualidade. Uma inspeção visual longa e completa conclui a auditoria de qualidade.
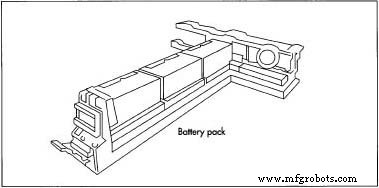
Controle de qualidade
A indústria provou que as estações de trabalho são um método altamente eficaz de fornecer controle de qualidade em todo o processo de montagem. Cada estação de trabalho tem dois membros da equipe que se apoiam mutuamente e fornecem verificações internas de sua parte no processo. Em uma linha de montagem relativamente pequena como esta para o carro elétrico (75 montadores em uma fábrica da General Motors), todos os trabalhadores se conhecem, então há também um espírito de equipe maior que aumenta o orgulho e a cooperação. Consequentemente, a única operação importante de controle de qualidade conclui o processo de montagem e consiste em um conjunto abrangente de testes e inspeções.
Exclusivo na fabricação de carros elétricos, o funcionamento do carro foi testado durante as etapas finais de montagem. O carro não tem escapamento e não emite gases ou poluentes, portanto, após a instalação da bateria e da unidade de propulsão, o carro pode ser conduzido dentro da planta. A prova de que o produto funciona várias etapas antes de ser finalizado é uma verificação de qualidade tranquilizadora.
Subprodutos / resíduos
Não há subprodutos da fabricação de carros elétricos. O desperdício dentro da fábrica de montagem também é mínimo ou inexistente porque as peças, componentes e submontagens foram todos feitos em outro lugar. Aparas e outros resíduos são recapturados por esses fornecedores e a maioria é reciclável.
O Futuro
Os carros elétricos são extremamente importantes para o futuro da indústria automobilística e para o meio ambiente; entretanto, a forma que o carro elétrico irá assumir e sua aceitação pelo público ainda são incertas. O consumo de suprimentos decrescentes de petróleo, as preocupações com a poluição do ar e sonora e a poluição causada (e energia consumida) por carros abandonados e as complicações da reciclagem de carros movidos a gasolina são todas as forças motrizes que parecem estar empurrando para o sucesso do carro elétrico.
Processo de manufatura