Aciaria a Hidrogênio
Fabricação de aço com hidrogênio
A indústria de produção de ferro e aço é o maior setor em termos de emissões totais globais fósseis e industriais, representando cerca de 7% a 9% das emissões de gases de efeito estufa (GEE). Ao mesmo tempo, o aço é o principal componente material para as sociedades industriais modernas. O aumento do consumo de aço vai ocorrer devido à necessidade de expandir e melhorar a infraestrutura e aumentar os padrões de vida globais em um ritmo suficiente para atingir um nível satisfatório. Portanto, existe o desafio de encontrar um processo de fabricação de aço que permita o uso social do aço como material e, ao mesmo tempo, evite os impactos ambientais negativos de sua produção. No contexto da redução das emissões de CO2 (dióxido de carbono) da siderurgia, a rota de fabricação de aço baseada em hidrogênio (H2) está recebendo muita atenção atualmente, pois oferece uma escolha atraente.
A redução de minério de ferro com H2 é bem conhecida, pois as reações de redução com H2 também ocorrem tanto na produção de gusa em alto-forno (BF) quanto na produção de ferro reduzido direto (DRI)/ferro briquetado a quente ( HBI) em um forno de cuba. Na siderurgia BF, as fontes de H2 são jato de ar quente umidificado e carvão pulverizado injetado. No caso da rota siderúrgica baseada em DR-EAF (redução direta – forno elétrico a arco), ela sempre foi historicamente caracterizada pelo uso de H2, que normalmente é gerado a partir de gás natural (GN) por meio de reformadores catalíticos. Como a fonte de hidrocarboneto é o GN, o H2 produzido pode ser de concentração variável e misturado com monóxido de carbono (CO), dependendo da proporção de oxidante utilizada.
A redução de H2 do minério de ferro tem sido estudada por muitas décadas. Houve investigações pioneiras na Suécia por Wiberg e Edstrom já na década de 1950, que foram seguidas por uma série de investigações descrevendo a cinética do processo, bem como a reatividade do produto produzido. A primeira planta de redução direta de H2 de minério de ferro (H2-DRI) em escala comercial baseada na tecnologia de leito fluidizado, Circored, foi construída pela Cliffs and Associates Ltd. no Complexo Industrial Point Lisas em Trinidad em 1998. A planta tinha um projeto de 500.000 toneladas por ano de HBI. A planta não teve sucesso comercial e foi fechada em 2016.
No cenário global atual, diversas atividades estão em andamento para encontrar um processo que utilize a redução do minério de ferro com H2 de forma a reduzir bastante as emissões de CO2, se não eliminá-lo totalmente. Existem inúmeras questões que devem ser superadas antes que o sucesso seja alcançado, o que pode proporcionar uma forte concorrência aos processos atuais que estão sendo usados para fabricação de ferro e siderurgia. Algumas das principais questões que devem ser superadas são descritas nos parágrafos subsequentes.
Uma das questões importantes é encontrar um método econômico para a produção de H2 a granel que use energia produzida a partir de processos com emissões de CO2 magras. As fontes de energia renovável são a energia solar, a energia eólica, a energia hídrica, a energia marinha e a energia geotérmica. Na energia nuclear também é usado combustível livre de fóssil. De todas as energias renováveis, as duas fontes mais confiáveis de energia renovável são a energia solar fotovoltaica (PV) e as turbinas eólicas. No entanto, ambas as tecnologias são caracterizadas pela flutuação do fornecimento de energia elétrica devido à natureza volátil da radiação solar e do vento, de modo que há momentos em que o fornecimento de eletricidade é escasso e momentos em que é abundante. Para integrar uma alta proporção de energia eólica e solar ao sistema de energia, é necessária uma solução de armazenamento em larga escala para compensar os desequilíbrios temporais entre produção e demanda.
A segunda questão é o armazenamento do H2 a granel (armazenamento gasoso de alta pressão ou armazenamento liquefeito criogênico). O armazenamento de H2 oferece benefícios de uma perspectiva de fornecimento/preço de eletricidade, mas não é tão crítico para o conceito de processo. Hoje, a alternativa mais econômica para o armazenamento de H2 é o armazenamento subterrâneo pressurizado, onde há armazenamento de H2 nas formações salinas subterrâneas. No cenário atual, esta é a única tecnologia de armazenamento de H2 testada em escala industrial. Outras soluções que estão atraindo muito interesse hoje em dia incluem a utilização de gasodutos de gás natural e a conversão em amônia ou hidrocarbonetos como armazenamento intermediário de H2. A avaliação inicial da tecnologia Lined Rock Cavern (LRC) usada atualmente na Suécia para gás natural é considerada promissora. Outros métodos alternativos de armazenamento de H2 em desenvolvimento são o armazenamento em hidretos metálicos e em materiais porosos.
A terceira questão é que o ferro produzido através da redução por H2 não contém carbono (C) ao contrário de metal quente e DRI/HBI que contém C em porcentagem variável. C é necessário na fabricação de aço para a fervura C. Além disso, o aço deriva suas propriedades por causa de seu teor de C e, portanto, a porcentagem variável de C está presente em diferentes graus de aço. No entanto, não são previstas dificuldades técnicas reais a este respeito, uma vez que alguns C adicionais podem ser adicionados ao EAF.
A quarta questão são as emissões de CO2 que ocorrem durante a mineração, beneficiamento e beneficiamento do minério de ferro e durante a produção de pelotas, bem como o transporte desses materiais. Os processos que utilizam a redução de H2 precisam preferencialmente de pellets como material de alimentação. A este respeito, existe a possibilidade de eliminar algumas das emissões de CO2 através da utilização de fontes de energia renováveis.
O primeiro processo é a produção em larga escala de H2, que atualmente está sendo alcançada pela reforma a vapor do metano. Essa opção pode ser mantida e até otimizada para fabricação de ferro à base de H2, por exemplo, visando uma pureza de 97% a 98% de H2 em vez dos 99,9% normais de pureza. No entanto, como com base em recursos fósseis, o desempenho em termos de mitigação de CO2 permanece na média geral, a menos que uma unidade de captura de CO2 seja adicionada, o que representa uma estratégia diferente da adotada atualmente. A outra opção preferível é produzir H2 por eletrólise da água. A produção de H2 precisa ser livre de fósseis e, portanto, o método de produção apropriado é a eletrólise da água com eletricidade pobre em CO2, ou seja, energia elétrica renovável ou nuclear. O desafio é alcançar a produção massiva de H2 em condições econômicas aceitáveis. Embora a eletrólise da água seja uma tecnologia bem conhecida, alguns desenvolvimentos são necessários para atingir a meta de grandes quantidades de H2 que é pobre em CO2 e, acima de tudo, que é acessível para a fabricação de ferro. O tamanho da planta pode ser alcançado multiplicando as células eletrolíticas. Tecnologias novas e aprimoradas também foram identificadas, como membranas de troca de prótons e eletrólise de alta pressão ou alta temperatura.
O segundo processo é a produção de ferro pela redução direta do minério de ferro em um forno de cuba que funciona apenas com H2. É o coração do processo de fabricação de ferro H2. O forno de cuba é alimentado com pelotas ou minério granulado no topo, que descem por gravidade e encontram um fluxo ascendente de H2, alimentado lateralmente na meia altura do reator e saindo pelo topo. As reações de redução ocorrem na seção superior entre a saída e a entrada do gás redutor. A conversão em ferro é completada ao nível da entrada de gás. Abaixo, uma seção cônica pode ser usada para resfriar o DRI, mas preferencialmente usando H2 em vez de metano (CH4). O restante do circuito de gás é muito mais simples do que no processo DRI convencional com GN reformado, com o gás superior consistindo em H2-H2O resfriado para condensar água. O H2 separado é reciclado, misturado com H2 fresco da planta de eletrólise e reaquecido à temperatura desejada (cerca de 800 graus C a 900 graus C).
A partir da modelagem matemática da zona de redução de um forno de cuba operado com 100 %. H2, verificou-se que, devido à cinética de redução rápida com H2, a metalização completa pode ser teoricamente alcançada mais rapidamente do que com a mistura de H2-CO, resultando em reatores menores que os atuais eixos DR.
O terceiro processo é a fusão do DRI livre de C em um EAF para produzir aço. Um processo de redução baseado em H2 resulta em um produto de ferro com zero carbono, indicando que uma fonte de C livre de fóssil é necessária para produzir o produto de aço com a química necessária na etapa de fabricação de aço.
Na melhor rota de siderurgia baseada em H2 estudada no projeto ULCOS (ultra low CO2 steelmaking) (Fig1), considera-se que o H2 é produzido por eletrólise da água usando eletricidade hidráulica ou nuclear. O minério de ferro é considerado reduzido a DRI por H2 em um forno de cuba, e o DRI livre de C é considerado tratado em um EAF para produzir aço. Esta rota mostra um desempenho promissor em relação às emissões de CO2 inferiores a 300 kg CO2 / tonelada de aço, incluindo o custo de CO2 da eletricidade com as emissões do próprio forno DR (redução direta) sendo quase zero. Isso representa uma redução de 85% nas emissões de CO2 em relação aos atuais cerca de 1.850 kg CO2/ton de aço da rota BF-BOF (forno de oxigênio básico). Esta nova rota é, portanto, uma forma mais sustentável de fazer aço. No entanto, seu desenvolvimento futuro depende em grande parte do surgimento da chamada economia do H2, quando esse gás se torna disponível em grandes quantidades, a custo competitivo e com baixas emissões de CO2 para sua produção.
Fig 1 Rota de fabricação de aço à base de hidrogênio
Na redução à base de H2, o minério de ferro é reduzido por meio de uma reação gás-sólido, semelhante às rotas DRI. O único fator de diferenciação é que o agente redutor é H2 puro em vez de gás CO, gás de síntese ou coque. A redução do minério de ferro por H2 ocorre em duas ou três etapas. Para temperaturas superiores a 570°C, o minério de hematita (Fe2O3) é primeiro transformado em magnetita (Fe3O4), depois em wustita (FexO) e finalmente em ferro metálico, enquanto em temperaturas abaixo de 570°C, a magnetita é transformada diretamente em ferro, pois a wustita não é termodinamicamente estável.
As reações de redução envolvidas na redução do minério de ferro por H2 são representadas pelas equações (i) 3 Fe2O3 + H2 =2 Fe3O4 + H2O, (ii) x Fe3O4 + (4x-3) H2 =3 FexO + (4x-3 ) H2O, e (iii) FexO + H2 =x Fe + H2O onde x é igual a 0,95. Conforme indicado por essas reações, a redução do minério de ferro com H2 libera vapores de água inofensivos (H2O) em vez do gás de efeito estufa CO2. A reação global para a redução do minério de hematita com H2 é Fe2O3 + 3H2 =2Fe + 3H2O que é uma reação endotérmica com um calor de reação, delta H a 298 graus C =95,8 kJ/mol, que é negativo para o balanço de energia do processo e demanda um acréscimo de energia com a mistura gás de redução/gás injetada. O foco no desenvolvimento da linha de produção é a otimização baseada na temperatura de redução, cinética da reação, composição do pellet e tecnologia de pré-aquecimento do gás de redução.
O consumo estequiométrico de H2 para redução de minério de hematita (Fe2O3) é de 54 kg por tonelada de ferro. Assim, uma usina siderúrgica de 1 milhão de toneladas por ano requer uma usina de H2 com capacidade de até 70.000 cum/hora de H2 em temperatura e pressão padrão (STP). Com H2 como gás de redução, é importante antecipar a mudança no comportamento do reator em relação ao reator com misturas de H2-CO como gás de redução (Fig. 2). Vários fatores podem interagir de diferentes maneiras, como cinética, termodinâmica, transferência de calor e fluxo de gás. Em relação à cinética, estudos de laboratório sobre a redução de óxidos de ferro com misturas de CO, H2 e CO-H2 mostraram claramente que, tudo o mais constante, a cinética com H2 é mais rápida (até 10 vezes) do que com CO. das características da reação são muito semelhantes às da redução por CO e muitos mecanismos são comuns a ambas. No entanto, também existem diferenças significativas.
Fig 2 Comparação da cinética de redução de pellets de hematita com misturas de H2, CO e H2-CO
O primeiro fator importante é a termodinâmica, que favorece o CO em baixas temperaturas, como evidenciado pelo diagrama de Chaudron (Fig. 3). As setas verticais azuis representam a força motriz para a redução de wustita em ferro, que aumenta com a temperatura com H2 e diminui com a temperatura com CO.
Fig 3 Diagrama de fase de Chaudron do domínio de fase de ferro em função da temperatura e poder oxidante do gás
O segundo fator é o calor das reações de redução, conforme mostrado na Guia 1. A reação hematita-magnetita é menos exotérmica com H2 do que com CO, a reação magnetita-wustita é mais endotérmica e, principalmente, a wustita- a reação ao ferro é endotérmica com H2 e exotérmica com CO. No geral, o equilíbrio é uma redução endotérmica com H2 e uma redução exotérmica com CO. Como resultado, a temperatura e as composições no eixo mudam muito com a composição do gás de entrada. Ao sair da zona de injeção de gás, a temperatura diminui devido ao craqueamento do metano, mas com maior teor de CO, o leito é mantido a uma temperatura mais alta como resultado do calor exotérmico das reações de redução, enquanto a temperatura é menor com mais H2 .
Tab1 Valores de calor das reações de redução | |
Reação | Delta H, 800 graus C |
J/mol | |
3Fe2O3 +H2 + 2 Fe3O4 =H2O | – 6.020 |
3Fe2O3 + CO =2 Fe3O4 + CO2 | – 40.040 |
Fe3O4 + H2 =3 FeO + H2O | 46.640 |
Fe3O4 + CO =3 FeO + CO2 | 18.000 |
FeO + H2 =Fe + H2O | 16.410 |
FeO + CO =Fe + CO2 | – 17.610 |
Observação:um sinal de menos indica uma reação exotérmica |
Mesmo que em todos os casos se utilize mais H2 do que CO para as três reduções (resultado da cinética), este último efeito, ou seja, a redução do CO na zona central no caso do gás CO, é decisivo para o resultado final. grau de metalização. Além disso, ao usar apenas H2 (tanto na entrada do gás redutor quanto na entrada inferior) a zona central mais fria não existe, as temperaturas são mais uniformes radialmente, e a redução, devido à cinética eficiente, chega ao fim (100 % metalização).
Como visto acima, a redução com H2 é endotérmica, enquanto é exotérmica com CO. Por outro lado, a termodinâmica é mais favorável com H2 do que com CO acima de 800°C. Isso torna a operação industrial diferente. Com H2, o gás quente alimentado tem que trazer calorias suficientes para aquecer e manter o sólido a uma temperatura suficientemente alta para que a reação ocorra. Portanto, é necessário operar com uma taxa de fluxo de gás superior à estequiometria. A cinética também é relatada como mais rápida com H2. Isso, por sua vez, pode modificar a morfologia do produto final (ferro), que depende de uma competição entre difusão e reação química. Em particular, a formação de bigodes parece uma característica específica da redução por H2. Os bigodes são grãos de ferro que se projetam da fase wustita e crescem como dedos em direção ao exterior das partículas. Os bigodes tornam os contatos ferro-ferro mais frequentes e podem assim explicar o fenômeno de aderência das partículas sólidas, às vezes experimentado em reatores industriais operados com alto teor de H2. Outro fenômeno estranho observado com a redução de H2 é a ocorrência, em algumas temperaturas, de uma desaceleração ao final da reação para atingir o último percentual do grau de conversão.
Em um forno de cuba com H2 puro, não há fonte de C. Devido à natureza endotérmica das reações, uma grande quantidade de calor é absorvida e a temperatura interna na camada de material a granel diminui rapidamente. Como resultado, as reações de redução que precisam consumir uma grande quantidade de calor causam a deterioração da taxa de utilização do gás. A quantidade de H2 como transportador de calor deve ser aumentada para manter a produtividade preferida. Como exemplo, quando a pressão no topo é de 0,4 MPa, a quantidade de H2 com uma temperatura de 900 graus C deve ser de pelo menos 2.600 cum por tonelada de DRI para atender à demanda de calor da redução do forno de cuba. Se a adição de H2 permanecer inalterada, a produção DRI é um terço menor que a atual, levando a um grande aumento no custo de produção do DRI.
A gravidade específica do H2 é baixa e a densidade do H2 é apenas 1/20 vezes a do CO. Como resultado, a molécula de gás H2 que entra escapa rapidamente para cima. Em comparação com o caminho e a direção de um gás redutor misto, os de H2 em um forno mudam tão rapidamente que o H2 não pode permanecer na zona de alta temperatura na parte inferior do forno de poço para completar a tarefa de reduzir pelotas de minério de ferro. Teoricamente, os produtos DRI também podem atingir o índice projetado mantendo o H2 de entrada com pressão acima de 1 MPa e temperatura acima de 1.000 graus C.
Além disso, o H2 é uma substância extremamente inflamável e explosiva, e o forno de cuba precisa de uma produção altamente eficiente e estável a longo prazo. Se for permitido que o sistema de forno de cuba funcione por um longo tempo sob as condições finais de alta temperatura e alta pressão, a segurança se torna um problema. Em suma, a taxa de redução direta e a eficiência de produção são afetadas por diversos fatores, como proporção de H2, temperatura, pressão, taxa de utilização do gás, tempo de residência do minério de ferro, transferência de calor, transferência de massa e projeto do forno de cuba.
A iniciativa HYBRIT
HYBRIT é a abreviação de 'tecnologia de fabricação de ferro HYdrogen BReakthrough'. Em 4 de abril de 2016, as três empresas suecas – SSAB, LKAB e Vattenfall AB lançaram um projeto destinado a investigar a viabilidade de um processo de produção DRI baseado em H2, com eletricidade livre de emissões de CO2 como fonte de energia primária. Uma empresa de joint venture foi formada, HYBRIT Development AB, com as três empresas sendo proprietárias. Isso dá acesso total à competência superior em toda a cadeia de valor, desde produção de energia, mineração, beneficiamento de minério e produção de pelotas, redução direta, fusão e produção de aço bruto. Em 2017, foi realizado um estudo de pré-viabilidade de redução direta baseada em H2. O estudo concluiu que a rota de processo proposta é tecnicamente viável e, tendo em vista as tendências futuras de custos de emissões de CO2 e eletricidade, também é economicamente atraente para condições em norte da Suécia / Finlândia.
O processo HYBRIT substitui o carvão por H2 para a redução direta (DR) do ferro, combinado com um EAF. O processo é quase totalmente isento de fósseis e resulta em uma redução substancial de suas emissões de gases de efeito estufa. O processo está entre as várias iniciativas que utilizam uma configuração H2-DR/EAF, combinando a redução direta de minério de ferro pelo uso de H2 com um EAF para posterior processamento em aço. O produto do processo H2-DR é DRI ou ferro-esponja, que é alimentado em um EAF, misturado com partes adequadas de sucata e processado posteriormente em aço.
O fluxograma principal do processo de produção HYBRIT é mostrado na Figura 4. As principais características do processo são (i) combustíveis não fósseis são usados na produção de pellets, (ii) H2 é produzido com eletrólise usando eletricidade livre de fósseis, (iii) armazenamento de H2 em uma unidade especialmente projetada é usado como amortecedor para a rede, (iv) um forno de cuba é usado para redução de minério de ferro, (v) pelotas feitas sob medida são usadas como alimentação de minério de ferro, (vi) o gás de redução / mistura gasosa é pré-aquecida antes da injeção no eixo, (vii) o produto pode ser DRI ou HBI isento de C ou cementado, e (viii) o DRI/HBI é fundido junto com sucata reciclada em um EAF.
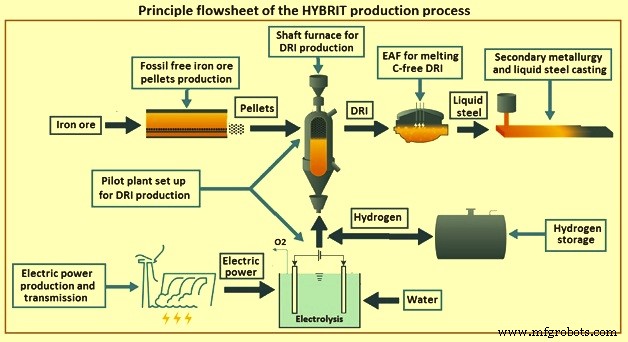
Fig 4 Fluxograma de princípios do processo de produção HYBRIT
O uso do H2 produzido por eletrólise da água com eletricidade livre de fóssil para reduzir pelotas de minério de ferro em um forno de poço é a principal alternativa escolhida para a iniciativa HYBRIT. Sob esta iniciativa, uma conversão para uma cadeia de valor livre de fósseis da mina para o aço acabado inclui muitas questões a serem desenvolvidas, levando em consideração também o mercado local e as condições geográficas. A Suécia tem uma situação única com excesso de capacidade de energia elétrica na parte norte do país, proximidade de minas de minério de ferro, bom acesso de biomassa e siderurgia e uma forte rede entre indústria, institutos de pesquisa e universidades.
O processo HYBRIT se enquadra em uma categoria de conceitos tecnológicos substancialmente mais próximos da implantação comercial. Baseia-se na utilização do H2 como agente redutor, sendo o H2 produzido por eletrólise com base em eletricidade renovável. Do ponto de vista ambiental, a vantagem mais importante disso é que o escape desse processo é água (H2O) em vez de CO2, com conseqüente redução das emissões de GEE. Assim como na fabricação de aço DRI convencional, o ferro produzido usando a rota DRI baseada em H2 pode ser processado em aço usando a tecnologia EAF disponível comercialmente. As etapas de produção de H2 e fabricação de aço EAF podem ser livres de C se a energia elétrica e o H2 forem produzidos usando fontes renováveis, como eletrólise solar / eólica / hidrelétrica fotovoltaica, produção fotoquímica de H2 ou água solar térmica divisão.
Tecnologia flash de fabricação de ferro usando hidrogênio
Uma nova tecnologia de transformação para a produção de ferro alternativa está sendo desenvolvida por um consórcio de organizações e institutos sob o apoio financeiro do American Iron and Steel Institute nos EUA. Esta tecnologia baseia-se na redução gasosa direta do concentrado de óxido de ferro em um processo de redução instantânea. A nova «tecnologia flash de produção de ferro (FIT) tem potencial para reduzir o consumo de energia de 32% a 57% e reduzir as emissões de CO2 de 61% a 96% em comparação com a operação média atual baseada em BF. Essa tecnologia reduz o concentrado de minério de ferro em um reator flash com um gás redutor adequado, como H2 ou gás natural, e possivelmente bio/gás de carvão ou uma combinação destes. É o primeiro processo de fabricação de ferro flash. Esta tecnologia é adequada para uma operação industrial que converte concentrado de minério de ferro (menos de 100 mícrons) em metal sem tratamento adicional.
Essa tecnologia transformadora produz ferro ao mesmo tempo em que ignora a pelotização ou sinterização, bem como as etapas de fabricação de coque. Além disso, o processo é intensivo devido ao fato de que as partículas finas do concentrado são reduzidas a uma taxa rápida de 1.150 graus C a 1.350 graus C. Assim, os tempos de residência necessários neste processo são da ordem de segundos, em vez do minutos e horas necessários para pelotas e até mesmo finos de minério de ferro. As reduções de 90% a 99% ocorrem em 2 segundos a 7 segundos a 1200 graus C a 1500 graus C. O tempo de residência é uma combinação de velocidade de reação devido à temperatura, tamanho do material de alimentação e quantidade de excesso de gás / distância de linha de equilíbrio. A necessidade energética do processo com H2 como gás de redução é de 5,7 GJ (1.360 Mcal)/ton de ferro líquido. O diagrama de equilíbrio Fe/FeO é mostrado na Fig 5.
Fig 5 Diagrama de equilíbrio Fe/FeO
A porção de aquecimento do reator é onde a bobina de aquecimento por indução aquece o susceptor de grafite. O susceptor aquece a parede refratária por radiação. Tanto o susceptor quanto o refratário aquecem o gás e a partícula por convecção e radiação. Após serem aquecidos até a temperatura, o gás e as partículas entram na zona de reação, onde um bom isolamento é assumido, então a condição da parede é definida como adiabática. Após a zona de reação, existe uma zona de resfriamento com painel de resfriamento para resfriar gases e partículas. A Fig. 6 mostra o fluxograma da tecnologia de fabricação de ferro flash.
Fig 6 Fluxograma da tecnologia de fabricação de ferro flash
No caso de FIT com H2 como gás redutor, as emissões de CO2 são de 0,04 toneladas de CO2 por tonelada de ferro líquido. Essas emissões são 2,5% das emissões da rota BF de siderurgia. O processo de ferro flash é realizado a uma temperatura alta o suficiente para que as partículas individuais tenham energia suficiente para fechar os poros criados pela remoção do oxigênio. Assim, as partículas individuais são muito menos suscetíveis a pegar fogo por oxidação rápida. A Universidade de Utah realizou pesquisas em pequenas amostras de pó e determinou que elas não são pirofóricas.
O processo utiliza agentes redutores gasosos como NG, H2, syngas ou uma combinação destes. Deve ser aplicado à produção de ferro como alimentação para o processo de fabricação de aço ou como parte de um processo de fabricação de aço direto contínuo. Justificado por dados experimentais obtidos durante a fase anterior do projeto, o trabalho de desenvolvimento em escala está atualmente em andamento na Universidade de Utah. Os testes em um forno flash de laboratório resultaram no estabelecimento de um banco de dados cinético em amplas faixas de condições operacionais e um projeto completo de um reator de bancada mais avançado. Com o objetivo de desenvolver um FIT industrialmente viável, uma campanha abrangente de testes em escala de bancada está planejada. Espera-se que os resultados desta fase do projeto sejam a determinação da escalabilidade do processo, resultados substantivos de simulação de processo e dados fundamentais de engenharia que levem ao projeto e construção de uma planta piloto industrial.
Processo de manufatura
- Liga de armazenamento de hidrogênio titânio-ferro
- O que é a fabricação de aço com oxigênio básico?
- Kazoo
- Harpa
- Espuma de poliestireno expandido (EPF)
- Sensores Raspberry Pi
- Nanossilício para produzir hidrogênio
- Introdução à fragilização por hidrogênio
- O que é uma pedreira?
- Vários métodos de processo de fabricação de aço