Aço Carbono Neutro
Fabricação de aço neutra em carbono
A indústria de produção de ferro e aço é o maior setor em termos de emissões totais globais fósseis e industriais, representando cerca de 7% a 9% das emissões de gases de efeito estufa (GEE). Ao mesmo tempo, o aço é o principal componente material para as sociedades industriais modernas. Um maior consumo de aço ocorrerá devido à necessidade de expandir e melhorar a infraestrutura e aumentar os padrões de vida globais em um ritmo suficiente para atingir um nível satisfatório. Assim, o desafio está em encontrar caminhos que permitam o uso social do aço como material e, ao mesmo tempo, evitar os impactos ambientais negativos de sua produção.
Os processos tradicionais de produção de ferro e aço estão associados a emissões ambientais de GEE muito elevadas. As emissões atuais das siderúrgicas estão em torno de 1,8 toneladas de CO2 (dióxido de carbono) por tonelada de aço bruto (tCO2/tCS). Embora tenha havido esforços significativos em andamento para reduzir as emissões de GEE da siderurgia nas últimas décadas, grandes avanços tecnológicos ainda são necessários para que o setor de ferro e aço acompanhe as reduções de emissões gerais necessárias sob o Acordo de Paris. Acordo, que visa limitar o aumento da temperatura global na virada deste século para bem abaixo de 2°C acima dos níveis pré-industriais, e afirma que os esforços devem ser direcionados para uma meta mais ambiciosa de apenas 1,5°C de aumento da temperatura.
As emissões de CO2 da indústria de ferro e aço estão entre as mais difíceis de diminuir, uma vez que o carbono é usado como agente redutor estequiométrico na produção de ferro e aço na maioria das siderúrgicas. Esse carbono acaba como uma mistura de CO/CO2 nos gases da usina siderúrgica, que são queimados para gerar calor, eletricidade e mais CO2. Estratégias para carbono, captura e armazenamento (CCS), para carbono, captura e utilização (CCU) ou para evitar CO2 existem na produção de ferro e aço, mas são altamente dependentes da disponibilidade de energia elétrica renovável para a produção de hidrogênio ( H2).
As estimativas atuais da demanda futura de aço variam amplamente com a taxa de crescimento anual projetada flutuando entre 1,4% e 3,3%. Com essa taxa de crescimento, a demanda de aço projetada para 2025 chega a 2,4 bilhões de toneladas. A descarbonização parcial dessa crescente indústria siderúrgica só pode ser alcançada por meio de melhorias de eficiência e da integração de energia elétrica renovável nas rotas convencionais de siderurgia, enquanto a descarbonização completa precisa de novas tecnologias de zero carbono e/ou emissões negativas. Por outro lado, as tentativas de descarbonização dos processos de produção de ferro e aço não atingiram um nível de adoção industrial em larga escala, apesar dos esforços substanciais de pesquisa e desenvolvimento (P&D) em andamento atualmente. A viabilidade e aplicabilidade do CCS no contexto da siderurgia permanecem altamente duvidosas no cenário atual.
Na rota convencional alto-forno/forno de oxigênio básico (BF/BOF), o carbono (na forma de coque e carvão) é usado para conduzir as reações de redução endotérmica, bem como para fornecer as altas temperaturas necessárias. Um processo BF-BOF típico produz 1,6 tCO2/tCS a 2,2 tCO2/tCS. Existem diferenças regionais consideráveis nas emissões relacionadas ao aço, com alguns países produtores de aço tendo uma pegada de emissões de CO2 muito maior em comparação com os países da OCDE (Organização para Cooperação e Desenvolvimento Econômico). Existem também diferenças significativas entre as diferentes rotas de produção de aço, como BF-BOF, DRI-EAF (ferro-forno elétrico a arco reduzido direto) e sucata-EAF. Por meio de melhorias tecnológicas, as siderúrgicas reduziram constantemente sua taxa de consumo de combustível nas últimas cinco décadas, a ponto de a rota BF-BOF agora ser considerada amplamente otimizada. Os BFs mais eficientes do mundo estão agora operando cerca de 5% acima do mínimo teórico em termos de emissões de CO2.
A transição da indústria pesada em geral e da siderurgia em particular, para a descarbonização, até muito recentemente, não recebeu muita atenção do ponto de vista da pesquisa energética e climática. No entanto, com emissões industriais quase tão altas quanto as da geração de energia, medidas de mitigação para descarbonização profunda devem ser seguidas com vigor na indústria siderúrgica. As estratégias de descarbonização profunda para a indústria de ferro e aço podem seguir basicamente duas rotas distintas, conforme indicado abaixo.
- Alteração dos processos existentes que devem ser realizados para remover as dependências inerentes aos combustíveis fósseis. Essa rota tende a depender fortemente do uso de energia elétrica, seja diretamente ou através do H2 produzido pela eletrólise.
- Manter os processos existentes como tal e abordar as emissões por meio de uma combinação de aplicação de CCS e CCU e uma mudança para fontes renováveis de energia de processo.
A categorização dessas duas rotas aplicadas à indústria siderúrgica possui diversas características, bem como desafios e oportunidades relacionados à sua implementação, conforme descrito a seguir. A Figura 1 apresenta a redução esperada nas emissões de CO2 para várias alternativas.
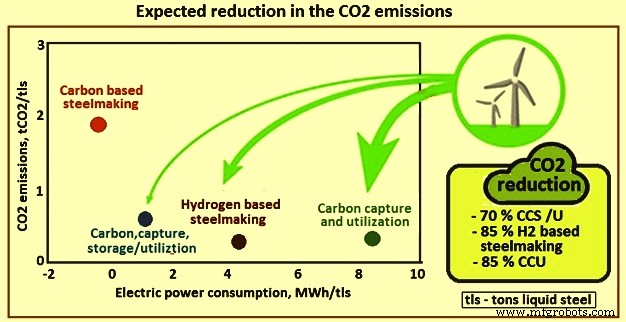
Fig 1 Redução esperada nas emissões de CO2
Alterar processos existentes
Com a crescente disponibilidade de eletricidade renovável de baixo custo, diferentes formas de eletrificação são cada vez mais vistas como opções atraentes para a descarbonização da indústria siderúrgica. Várias soluções tecnológicas diferentes foram sugeridas para esse fim. Entre as tecnologias mais promissoras está a eletrólise ou “eletro-vencedora” do minério de ferro. Isso envolve o uso de energia elétrica como agente redutor, semelhante à produção de alumínio (Al) a partir de óxido de alumínio (Al2O3). Esse processo ainda está em estágio inicial de desenvolvimento e até agora só foi testado em escala de laboratório, mas representa uma opção siderúrgica de alta eficiência com a promessa de grandes reduções de emissões no longo prazo.
Electro-winning é uma das técnicas eletrolíticas mais antigas utilizadas para extração de metais de seus minérios usando eletricidade. Esta tecnologia é normalmente usada para eletro-aproveitamento de metais como chumbo, cobre e elementos de terras raras. Existem algumas tecnologias de extração eletrolítica específicas de minério para ferro disponíveis comercialmente, a saber (i) o processo de Boucher, eletrorrefinação em solução de FeSO4-FeCl2, (ii) o processo de Eustis, eletroextração em solução de FeCl2 usando minério de sulfeto de ferro, e (iii) o processo Pyror, eletro-aproveitamento em solução de FeSO4 utilizando minério de sulfeto de ferro. No entanto, a eletro-extração de Fe a partir de minério de ferro, de aplicação mais geral, só foi estabelecida em escala laboratorial. Dependendo da pegada de carbono do mix de eletricidade usado para eletrólise, essa rota pode ser potencialmente livre de carbono. Em um cenário futurista, em que a oferta global de energia primária é dominada por fontes renováveis, essa tecnologia oferece um potencial significativo de redução de carbono. A presente iniciativa europeia SIDERWIN, que é um projeto no quadro do Horizonte 2020 com uma meta de redução de emissões de CO2 e de consumo de energia de 87% e 31% (em comparação com a rota BF-BOF), visa validar esta tecnologia à escala piloto, respetivamente. , e demonstrar um nível de prontidão tecnológica (TRL) até 2022.
Outra rota eletrolítica que recentemente recebeu interesse para a siderurgia é a eletrólise do óxido fundido do minério de ferro (também conhecida como piroeletrólise). O processo é semelhante ao método padrão para a redução do Al a partir do Al2O3 através do processo Hall-Heroult, no qual o Al2O3 é dissolvido em um banho de criolita fundida a 800°C (fluoreto de sódio e alumínio) e então eletrolisado entre ânodos de grafite (acima ) e um cátodo de alumínio fundido (abaixo). Espera-se que a operação de um processo semelhante para redução de minério de ferro em temperaturas muito altas produza uma diminuição potencial no consumo de energia em comparação com as rotas de eletrólise de baixa temperatura. Provas de conceito foram demonstradas, mas a viabilidade técnica com eficiências aceitáveis ainda é ilusória. Os desafios incluem a corrosividade de eletrólitos fundidos, falta de materiais anódicos adequados e compreensão mecanicista limitada de processos eletrolíticos de temperatura muito alta. Embora a produção de aço por eletrólise de óxido fundido ofereça potenciais vantagens econômicas e ambientais sobre a metalurgia extrativa clássica, sua viabilidade está longe de ser demonstrada de forma convincente como uma alternativa imediata de zero carbono.
Um estudo comparou a necessidade de energia e as emissões de CO2 de quatro diferentes rotas de produção de aço, a saber, caso de referência BF-BOF, BF-BOF com captura de carbono (BF-CCS), H2-DRI e processo eletro-vencimento. A via eletro-vencedora teve um requerimento de energia 50% menor do que o caso de referência BF-BOF, seguido por H2-DRI e BF-CCS com requerimentos de energia 28% e 13% menores, respectivamente. É importante ressaltar que a análise também conclui que não é possível uma redução de mais de 50% nas emissões de CO2 através da rota BF-CCS, ao passo que tanto a redução de H2 quanto as rotas de eletro-ganho podem levar à descarbonização completa do setor siderúrgico. As entradas de mercado para H2-DRI e eletro-ganho não são esperadas até 2035 e 2040, respectivamente.
O consumo estequiométrico de H2 para a redução de hematita é de 54 kg por tonelada de ferro. Uma planta de ferro e aço de 1 Mtpa (milhão de toneladas por ano) precisa de uma capacidade de planta H2 de até 70.000 cum em STP/hora. A produção de H2 em larga escala é atualmente alcançada pela reforma a vapor do metano. Essa opção pode ser mantida e até otimizada para fabricação de ferro à base de H2, por exemplo, visando uma pureza de 97% a 98% de H2 em vez dos 99,9% normais de pureza. No entanto, como com base em recursos fósseis, o desempenho em termos de mitigação geral de CO2 permanece médio, a menos que uma unidade de captura de CO2 seja adicionada, o que representa uma estratégia diferente da adotada atualmente. A outra opção preferível é produzir H2 por eletrólise da água, desde que a energia elétrica necessária seja livre de combustíveis fósseis. O tamanho da planta pode ser alcançado multiplicando as células eletrolíticas. Tecnologias novas e aprimoradas também foram identificadas, como membranas de troca de prótons e eletrólise de alta pressão ou alta temperatura.
Na redução à base de H2, o minério de ferro é reduzido por meio de uma reação gás-sólido, semelhante às rotas DRI. O único fator de diferenciação é que o agente redutor é H2 puro em vez de gás CO (monóxido de carbono), gás de síntese ou coque. HYBRIT, abreviação de 'HYdrogen BReakthrough Ironmaking Technology', é uma joint venture entre três empresas suecas, SSAB, LKAB e Vattenfall. Tem como objetivo eliminar completamente o carbono da siderurgia, usando redução de H2. O processo HYBRIT se enquadra em uma categoria de conceitos tecnológicos substancialmente mais próximos da implantação comercial.
O processo HYBRIT baseia-se na utilização de H2 como agente redutor, sendo o H2 produzido por eletrólise com base em eletricidade renovável. Do ponto de vista ambiental, a vantagem mais importante disso é que o escape desse processo é água (H2O) em vez de CO2, com conseqüente redução das emissões de GEE. Assim como na fabricação de aço DRI convencional, o ferro produzido usando a rota DRI baseada em H2 pode ser processado em aço usando a tecnologia EAF disponível comercialmente. A produção de H2 e as etapas de fabricação de aço EAF podem ser feitas sem carbono se a energia elétrica e o H2 forem produzidos usando fontes renováveis, como PV (fotovoltaica) / eletrólise eólica / hidrelétrica, produção fotoquímica de H2 ou separação de água solar-térmica .
O processo HYBRIT substitui o carvão por H2 para a redução direta (DR) do ferro, combinado com um EAF. O processo é quase totalmente isento de fósseis e resulta em uma redução substancial de suas emissões de gases de efeito estufa. O processo está entre as várias iniciativas que utilizam uma configuração H2-DR/EAF, combinando a redução direta de minério de ferro pelo uso de H2 com um EAF para posterior processamento em aço. O produto do processo H2-DR é DRI ou ferro-esponja, que é alimentado em um EAF, misturado com partes adequadas de sucata e processado posteriormente em aço. O fluxograma típico do processo H2-DR/EAF é mostrado na Fig 2.
Fig 2 Fluxograma típico do processo de redução direta de hidrogênio
Embora essa combinação específica de processos não tenha sido implementada em escala comercial, vários dos componentes individuais já são amplamente utilizados na indústria global de ferro e aço. O aço à base de EAF representa cerca de 30% da produção global anual. O processo DR também é amplamente empregado, sendo a base para cerca de 7% da produção global total de ferro e normalmente integrado ao EAF. Enquanto o H2 puro tem sido usado comercialmente como agente redutor na redução direta, a capacidade de produção de DRI existente depende do gás natural que é reformado a vapor para obter o agente redutor, uma mistura de CO e H2. Recentemente, foi desenvolvido o processo de reforma zero (ZR) que reduziu substancialmente o consumo de gás natural.
Como o custo do gás natural é um fator chave para a viabilidade econômica dessa configuração, a maior parte da produção de DRI está localizada em regiões ricas em gás natural de baixo custo (CH4). Apesar do fato de vários componentes da configuração H2-DR/EAF terem sido testados e implantados em ambientes industriais, os principais desafios ainda permanecem para o processo. Estes estão relacionados à integração de processos, qualidades dos produtos, ampliação da infraestrutura H2 (produção e armazenamento) e a integração de uma usina siderúrgica H2-DR/EAF em um sistema de energia baseado em fontes renováveis de eletricidade. Um dos principais desafios é como obter carbono no ferro para transformá-lo em aço.
Manter os processos existentes
A CCS tem sido um tema importante no estudo do controle das emissões de GEE. O interesse cresceu na década de 1990 com uma análise mais aprofundada da tecnologia. O conceito entrou mais amplamente nas discussões sobre políticas climáticas no início dos anos 2000 como uma tecnologia potencial pela qual o uso global de combustíveis fósseis pode continuar sem contribuir para os níveis de GEE na atmosfera. A própria tecnologia de captura de carbono é bastante madura, após a comercialização em meados do século 20 nas indústrias de alimentos e produtos químicos. O armazenamento também foi testado com sucesso em reservatórios de gás natural. Na fase inicial dos estudos de CCS para fins de mitigação das mudanças climáticas, o foco era predominantemente em aplicações para o setor de geração de energia elétrica, especialmente a produção de energia elétrica a carvão. No entanto, apesar de uma longa lista de plantas piloto e projetos de teste, o CCS comercial não se concretizou. Isso se deve em parte aos custos excedentes, em parte devido à oposição pública ao armazenamento subterrâneo de CO2 e em parte devido à queda dos custos de outros meios de geração de energia menos poluentes, como energias renováveis e gás natural.
Embora as expectativas para o papel da CCS no setor de energia tenham diminuído, no entanto, os recentes desenvolvimentos na captura de carbono da geração de energia a gás natural, pelo uso do chamado ciclo Allam, parecem promissores. Ainda é considerada uma opção fundamental para reduzir as emissões de GEE da indústria pesada, incluindo a siderurgia, sem grandes alterações nos processos existentes. A CCS na indústria tem certas características distintivas no que diz respeito às condições de implementação. Uma vantagem é que os fluxos de CO2 tendem a ser bastante puros na indústria em comparação com a produção de energia elétrica, o que pode tornar as etapas de separação e captura menos complicadas. Além disso, espera-se que a oposição pública seja menos severa, pois há poucas alternativas baseadas em energias renováveis para várias indústrias, como a indústria de cimento.
No entanto, a indústria de ferro e aço também possui algumas características que podem dificultar as aplicações de CCS. Primeiro, diferentemente da indústria de geração de energia elétrica, a indústria de ferro e aço compete globalmente, o que a torna ainda mais vulnerável a aumentos de custos e mais problemática para levar aumentos de custos para os clientes. Outra desvantagem para a opção CCS é que um local industrial hospeda várias fontes de CO2 de concentração e volumes variados. A maioria das avaliações de CCS se concentra apenas na principal fonte de CO2, enquanto a captura de todo o CO2 de uma planta pode ser muito mais difícil e precisa de uma grande reconstrução. Capturar e armazenar 50% a 60% das emissões de CO2 em um local industrial pode custar cerca de US$ 70 a US$ 80 por tonelada de CO2, de acordo com várias avaliações. No entanto, para capturar parcelas maiores de emissões, a estrutura de custos é mais incerta. Notavelmente, não existem estimativas de custos confiáveis para capturar mais de 90% das emissões.
O projeto 'Ultra-Low Carbon Dioxide Steelmaking' (ULCOS) identificou uma série de tecnologias que podem apoiar a implementação de CCS na indústria de ferro e aço. Um deles, o processo TGR-BF (Top Gas Recycling – Alto Forno) foi testado com sucesso em plantas piloto, resultando em um potencial de redução de 24% nas emissões de CO2. No entanto, a captura e o armazenamento reais do CO2 não faziam parte desta configuração piloto.
Em suma, atualmente o CCS parece ser uma solução mais promissora na indústria do que na geração de energia, mas ainda existem problemas inerentes. Em primeiro lugar, as potenciais reduções de emissões de GEE da CCS são limitadas a cerca de 50%, devido a fontes de emissão pequenas e difusas, falta de espaço para instalações e outros problemas. Em segundo lugar, questões relacionadas ao armazenamento, como supervisão e integridade de longo prazo dos reservatórios de armazenamento, ainda permanecem sem solução. Em terceiro lugar, CCS vem com muito poucos co-benefícios, e a presença de co-benefícios foi identificada como um facilitador chave quando se trata de acelerar os processos de transição. Este é um fator que pode dificultar a aceitação generalizada. Se a captura de carbono for combinada com alguma forma de utilização de CO2 (CCU), pode haver maiores oportunidades, mas ainda há muito a ser feito no processo de desenvolvimento. Além disso, mesmo que o CO2 seja utilizado como matéria-prima, como em alguma forma de especialidade química ou combustível, no entanto, eventualmente acaba na atmosfera.
O papel da biomassa
Durante a maior parte da história do processamento de ferro e aço, a biomassa foi um recurso fundamental. O carvão vegetal à base de madeira atuou tanto como agente redutor necessário para liberar o minério de ferro de seus componentes de oxigênio, quanto como fonte de energia necessária para atingir as altas temperaturas necessárias. Foi só por volta de 1875 que o coque, produzido a partir do carvão, assumiu o poder, embora seja importante notar que o carvão continuou a ser utilizado até meados do século XX. O carvão vegetal produzido a partir de eucaliptos de crescimento rápido ainda é usado como o principal agente redutor em siderúrgicas menores no Brasil, mas isso provavelmente não é viável em siderúrgicas maiores devido aos limites impostos pela menor resistência à compressão do carvão em comparação com o coque. Além disso, as grandes quantidades necessárias e os desafios significativos na manutenção da qualidade tornam altamente improvável uma mudança completa do coque para o biocoque.
Mas a biomassa ainda pode ter um papel importante a desempenhar na descarbonização do setor de ferro e aço, e várias opções diferentes foram sugeridas. No lado incremental da escala está a possibilidade de misturar 5% a 10% de carvão vegetal com carvão metalúrgico na produção de coque metalúrgico para uso em BFs existentes. Outra opção é usar biomassa no processamento de minério de ferro bruto, seja como combustível para o próprio processo ou para produzir uma pelota composta de minério de ferro-biocarbono que pode ser usada em um processo DR. Também foram realizados ensaios com o objetivo de utilizar biomassa gaseificada em processos de DR. Esta abordagem é viável, mas precisa de mais ensaios e estudos. A Höganäs AB, uma empresa sueca que usa um processo de DR à base de carvão para produzir pós de ferro, iniciou testes reais de um processo usando gaseificação de madeira para produzir tanto biocoque, para ser usado como agente de redução, quanto gás de síntese, para ser usado para energia de processo (e possivelmente também para redução.
O biometano também será uma importante opção de baixo carbono para aquecimento no processo de metalurgia secundária se o gás de coqueria da coqueria e da planta de subprodutos não estiver mais disponível. Em uma siderúrgica integrada, o gás de coqueria da coqueria e da planta de subprodutos é utilizado para aquecimento nos processos de metalurgia secundária. Com um conceito H2-DR, essa energia deve ser substituída. A longo prazo, existem diferentes opções de aquecimento elétrico, mas o biometano pode substituir diretamente o gás natural e o gás de coqueria usados atualmente, com alterações mínimas no processo.
No entanto, os desafios sistêmicos para a biomassa tendem a ser substanciais. Ao contrário do carvão, os recursos de biomassa não estão concentrados em um local específico (como uma mina), o que leva a altos custos de aquisição, pois a biomassa de áreas geograficamente dispersas deve ser coletada, processada e transportada para a siderurgia. Em segundo lugar, uma demanda crescente por madeira pode levar à competição com usuários existentes (como a indústria florestal), bem como outros setores que pretendam utilizar biomassa para alcançar ambições de mitigação. Isso, por sua vez, pode levar a preços mais altos, a menos que o foco seja mudado para resíduos florestais que são menos procurados. Finalmente, para garantir a redução das emissões de GEE, é crucial que a biomassa seja proveniente de florestas geridas de forma sustentável.
Em resumo, a biomassa pode vir a desempenhar um papel importante tanto na rota renovável quanto na CCS. Ambos necessitam de grandes quantidades de calor no processamento de minério de ferro, metalurgia secundária e processos de laminação a quente. Isso pode muito bem ser fornecido através da combustão do biometano. Na rota CCS, o carvão vegetal pode substituir pelo menos parcialmente o coque, desde que a estabilidade mecânica da carga de BF seja mantida. No conceito HYBRIT, a biomassa está prevista também para servir como fonte de carbono para processos de ferro e aço e potencialmente também no processo de usinagem a jusante.
Processo de manufatura
- Tungstênio Molibdênio Liga de Ferro para Siderurgia
- Ferro vs Aço:Qual é a diferença?
- Como se tornar neutro em carbono em 5 etapas
- Aço Carbono vs Aço Inoxidável
- Efeitos do forjamento em aço carbono
- Diferenças entre aço carbono e aço inoxidável
- O que é aço inoxidável com alto teor de carbono?
- O que é aço carbono médio?
- Aço carbono ASTM A595 grau A
- Vários métodos de processo de fabricação de aço