Manufatura Contínua Explicada:Como configurar e manter um sistema de produção contínua
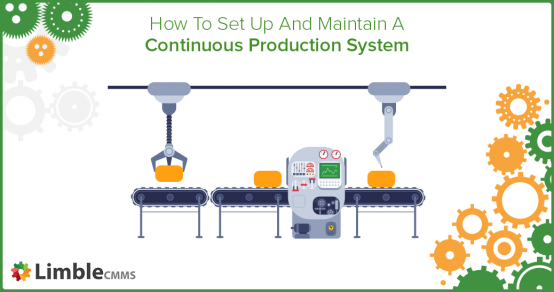
Os fabricantes usam várias configurações de produção para serem eficientes na produção em massa. Um sistema de produção contínua representa uma dessas configurações e vem com benefícios, desafios e requisitos de manutenção distintos.
O que é produção contínua?
A produção contínua, também conhecida como produção em massa, é um dos três principais métodos de fabricação - os outros dois sendo a produção em lote e por trabalho. É usado para fabricar grandes quantidades de produtos com poucas variações e depende de processos, sequências de processos, ferramentas e equipamentos altamente padronizados.
Em um sistema de produção contínua, o material flui por uma série de operações sem pausa, com manuseio otimizado e constante. Naturalmente, a força de trabalho deve operar 24 horas por dia, 7 dias por semana, em turnos rotativos. É a única maneira de gerenciar problemas de qualidade e desperdício de produtos.
Exemplos de produção de condições em diferentes setores
Os sistemas de produção contínua são usados por operações que podem maximizar as vantagens do fluxo de produção contínua. Abaixo estão alguns exemplos específicos.
Automotivo
Com os fabricantes automotivos mais conhecidos por processos de produção, as instalações de manufatura da Toyota na Indonésia são um bom estudo de caso em produção contínua. Composta por três fábricas integradas, as instalações funcionam como uma, fundição de metal, estamparia, construção de motores, montagem de veículos e embalagem - em um exemplo longo e complexo de aplicação de produção contínua.
Produtos farmacêuticos
As empresas farmacêuticas eram conhecidas pelo processamento em lote. No entanto, muitos começaram a se mover para a produção contínua.
O sistema de fabricação produz comprimidos revestidos a partir de pós brutos em um fluxo de produção contínuo. Ele permite vários fluxos contínuos de compactação de rolo ou granulação úmida para oferecer soluções especializadas às necessidades dos clientes. A GlaxoSmithKline recentemente abriu duas novas instalações de manufatura contínua em Cingapura e expandiu a terceira, após um investimento de $ 95 milhões.
Mineração e metais
As indústrias de mineração e metais usam produção contínua para extrair e transformar matérias-primas. Líder global na produção de alumínio, a Rio Tinto extrai o mineral bauxita, transformando-o em alumina, que é o principal constituinte do alumínio. É enviado para fundições de alumínio para conversão em metal.
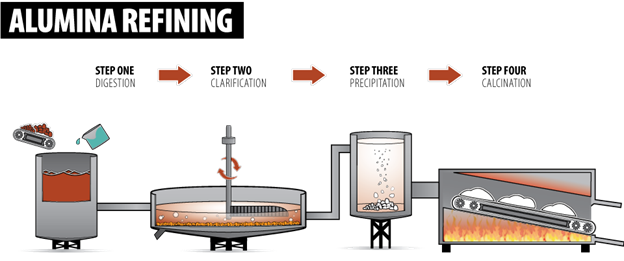
Processo de refino de alumina - Fonte: Aluminimum.org.au
Biotecnologia
A biotecnologia usa organismos vivos e biologia molecular para produzir vários produtos, incluindo genômica, produção de alimentos, medicamentos e biocombustíveis. Em 2019, a Sanofi abriu as primeiras instalações digitais do mundo usando a produção intensiva e contínua de produtos biológicos para a produção de produtos terapêuticos.
Processo contínuo versus fabricação em lote
Muitos fabricantes de pequeno e médio porte começam como oficinas de trabalho, produzindo uma gama diversificada de produtos customizados, onde uma pessoa ou uma equipe fabrica um produto do início ao fim antes de iniciar o próximo.
Conforme a empresa cresce, eles precisam se concentrar na eficiência. Em essência, eles precisam decidir com qual tipo de processo de fabricação se comprometerão. A decisão é baseada em fatores como a demanda do produto, o estado das matérias-primas e os recursos disponíveis.
A discussão geralmente se resume à fabricação em lote vs. fabricação contínua, portanto, vale a pena dedicar um minuto para aprender as diferenças.
Processo de fabricação em lote
A fabricação em lote usa um processo de parada / início de fabricação em que os produtos são fabricados em grupos ou lotes. Essa produção pode ser:
- orientado pela demanda: devido a execuções de produção menores necessárias para um produto específico
- orientado pela qualidade: devido à necessidade de verificação rigorosa da conformidade do produto para definir padrões
O período entre os lotes é conhecido como tempo de ciclo e facilita quaisquer alterações necessárias na especificação do material, ajuste do processo ou intervenções de manutenção.
A fabricação em lote é menos interrompida pela quebra da máquina, pois os trabalhos podem ser alternados entre as estações de trabalho. Ele também limita as perdas financeiras de desvios de qualidade, minimizando as quantidades de refugo. No entanto, as taxas de utilização da máquina mais baixas podem compensar os ganhos em qualidade e flexibilidade operacional.
Processo de fabricação contínua
A produção contínua não cessa, com matérias-primas e trabalhos em andamento em movimento contínuo. Correias transportadoras e tubulações tornam-se instalações de armazenamento móvel, reduzindo os requisitos de armazenamento e estocagem.
O motivador para a produção contínua é parcialmente devido à intensidade de capital do processo, que exige alta utilização da máquina para amortecer os custos sobre as maiores quantidades de produção. Ainda assim, muitos dos próprios processos não podem parar e reiniciar sem incorrer em penalidades significativas (há um grande risco de sedimentação de sólidos suspensos ou cristalização e endurecimento de materiais em tubulações e tanques).
Paradas frequentes também aumentam os tempos de ciclo, ciclos térmicos e ciclos de pressão no equipamento, aumentando a fadiga e encurtando sua vida útil.
Ao contrário da produção em lote, manutenção e atualizações de equipamentos em instalações de fabricação contínua ocorrerão anualmente - no melhor. Algumas plantas operam de dois a três anos sem paralisação, e os sistemas de transformação de alta temperatura, como altos-fornos, funcionam sem pausa por cinco a dez anos.
Os prós e contras da fabricação contínua
Já tocamos em alguns prós e contras ao explicar o processo, mas vamos sistematizar todos os pontos em um só lugar.
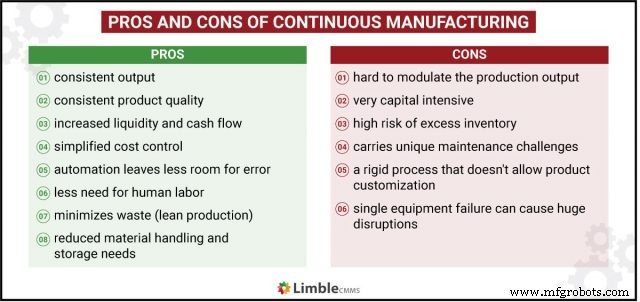
Vantagens da produção contínua:
- O controle e monitoramento do processo rigoroso garantem a qualidade consistente do produto .
- O uso da entrega just-in-time de matérias-primas e o balanceamento das sequências de fabricação reduzem o trabalho em andamento. Isso reduz o risco do negócio e oferece benefícios financeiros, como maior liquidez e melhor fluxo de caixa .
- Manuseio de materiais e áreas de armazenamento reduzidas custos de capital de construção da planta mais baixos e requisitos de investimento em manuseio de materiais.
- O controle de custos do material é simplificado .
- Dada a intensidade de capital da produção contínua, a amortização dos custos de capital sobre altas taxas de produção permite um custo de capital por unidade mais baixo .
Desvantagens da produção contínua:
- O processo de fluxo contínuo necessita de uma padronização de produtos, travada em uma rigidez que torna mais difícil customizar os produtos para mudar as necessidades do cliente.
- A interdependência dos fluxos de produção sequenciais reduz a tolerância a falhas, com um único falha do equipamento parando ou criando interrupções severas aos volumes do produto.
- A produção contínua é sensível à demanda. Usado onde há uma demanda alta ou contínua por um produto, há pouca capacidade de modular os fluxos de produção quando a demanda vacila ou cai.
- O investimento em equipamentos avançados, caros e muitas vezes personalizados torna o processo de produção muito intensivo em capital .
- Carrega um alto risco de excesso de estoque segurando no caso de uma interrupção downstream.
Se ainda não era óbvio, um dos desafios da manufatura contínua são seus requisitos de manutenção exclusivos. Como um sistema com um único ponto de falha que precisa operar 24 horas por dia, 7 dias por semana, a produção contínua precisa de um plano de monitoramento e manutenção bem elaborado.
Quais são os requisitos de manutenção das plantas de produção contínua?
Projeto de planta e processo, filosofias de manutenção, estratégias, táticas e intervenções operacionais requerem consideração séria dada a complexidade, criticidade e natureza 24/7 da manufatura contínua.
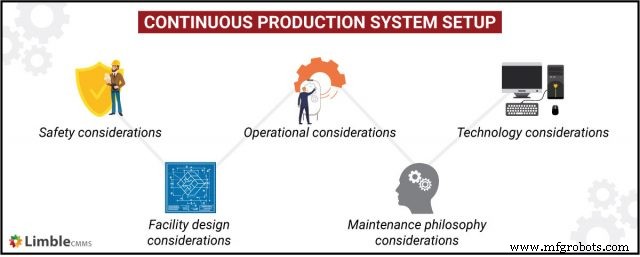
Considerações sobre o projeto da instalação
As considerações acima geralmente ocorrem somente depois que a planta foi construída e a equipe de operações empregada. Para aumentar a capacidade de manutenção de uma planta de produção contínua, as avaliações de engenharia e manutenção devem acontecer durante a fase de projeto do ativo / planta de manufatura.
Com intervenções de manutenção planejadas anualmente, na melhor das hipóteses, a confiabilidade em serviço do equipamento individual deve ser considerada nas decisões de custo total de propriedade (TCO) que orientam as recomendações de compra.
Da mesma forma, deve-se realizar estudos FMECA em fluxos de processo para conduzir decisões sobre layout de fábrica, avaliações de redundância de equipamentos e estoque de peças sobressalentes.
Considerações sobre a filosofia de manutenção
A filosofia de manutenção exigirá reflexão. É altamente recomendável realizar a manutenção centrada na confiabilidade antes de se comprometer com uma ou uma combinação de estratégias e tecnologias de manutenção.
Alguns fabricantes também podem querer considerar a manutenção produtiva total e a manutenção centrada nos negócios. Ambos apresentam muitas práticas interessantes, algumas das quais podem ser uma boa combinação para suas necessidades operacionais.
Em geral, as decisões estratégicas sobre manutenção reativa, preventiva, baseada na condição e preditiva irão evoluir a partir dos estudos RCM, FMECA e uma seleção de filosofia de manutenção.
Em instalações de produção contínua, a manutenção preventiva geralmente ocorre em processos paralelos, proporcionando redundância do sistema. As práticas de manutenção com base nas condições formarão a maior parte da estratégia, dada a infrequência de paradas para manutenção. A manutenção preditiva e prescritiva terá como alvo os ativos que incorrem em altos custos de tempo de inatividade ou manutenção.
Considerações sobre tecnologia
O RCM, assim como a manutenção preditiva e prescritiva, exige coleta, armazenamento e análise extensa e abrangente de dados.
Além de software especializado, as empresas podem usar sistemas CMMS modernos para gerenciar dados de condição e desempenho provenientes de ativos de produção contínua. Antes disso, os ativos devem ser adaptados ou vir com equipamentos de sensor adequados.
Fornecendo uma visão sobre a função de manutenção, um CMMS reduz a necessidade de intervenções de manutenção reativas, que podem ter implicações de custo proibitivas em um sistema de produção contínua.
Quando combinado com a análise de manutenção preditiva, os usuários do CMMS podem observar as tendências de deterioração para prever quando o ativo irá falhar. Dessa forma, os planejadores e gerentes de manutenção têm bastante tempo para alocar os recursos necessários e programar a manutenção - o que é extremamente benéfico no contexto da fabricação contínua.
Considerações operacionais
Os tempos de paralisação planejados são muito distantes e há uma grande pressão de tempo sobre a duração dessas paralisações. Isso pode complicar seriamente as decisões sobre a equipe de manutenção.
Você deve manter a manutenção interna ou terceirizar tudo? Dependerá muito do custo e da disponibilidade de empreiteiros devidamente qualificados. Esta é uma decisão muito importante, pois afeta diretamente o tamanho do seu estoque de peças de reposição, garantindo o acesso a ferramentas especializadas e a organização de outros recursos internos.
Por último, a obsolescência da tecnologia e as atualizações de equipamentos também exigem uma consideração cuidadosa para garantir que sejam planejados, dotados de recursos e programados de maneira adequada.
Considerações de segurança
Embora a segurança seja um componente crítico de todas as intervenções de manutenção, as paralisações para manutenção em instalações de produção contínua exigem planejamento extra. Com restrições de tempo estritas, as pressões econômicas de exceder os prazos planejados de fechamento criam pressões comerciais.
O que os incidentes de segurança e as falhas de equipamento têm em comum? Ambos são frequentemente causados por erros humanos. E esses erros são mais prováveis de acontecer quando você está com pressa.
Isso não é tudo. Uma paralisação de manutenção planejada de um sistema de produção contínua exigirá que vários negócios trabalhem próximos ou um sobre o outro.
Os testes feitos por uma equipe de manutenção devem ser cuidadosamente coreografados com outras pessoas na área para evitar exposição a equipamentos em movimento, eletricidade ou energia armazenada. É fundamental que os trabalhadores sigam as diretrizes da LOTO e outros procedimentos de segurança.
Instalações de produção contínua, como fábricas de produtos químicos, terão preocupações adicionais de segurança a serem tratadas durante as paralisações para manutenção. Alguns produtos químicos requerem circulação contínua, agitação ou aquecimento - mesmo quando desligados para manutenção. Tie-ins ou cut-ins para atualizações ou substituição irão expor as equipes de manutenção ao perigo. O planejamento de tais períodos de manutenção normalmente começa com meses, ou até anos, antes do tempo.
Como configurar um sistema de produção contínua
Com a intensidade de capital e a complexidade de grandes instalações de produção contínua, o planejamento e a preparação são essenciais. No entanto, mesmo um fabricante de pequeno a médio porte que busca passar para a produção contínua a partir do processamento ou da fabricação em lote precisará pensar seriamente.
Iniciar uma mentalidade de projeto para tal configuração é útil.
via GIPHY
1) A fase de viabilidade
Chefiada por um indivíduo com profundo conhecimento de produção, uma fase de viabilidade deve ser planejada e financiada com representação interorganizacional. As funções principais envolvidas na fase de planejamento incluiriam pessoal de produção, engenharia e manutenção, financeiro, qualidade e segurança.
2) A fase de planejamento
As decisões necessárias começarão com a filosofia de fabricação que orienta a seleção do equipamento. Produtos altamente padronizados em grandes volumes permitem a seleção ou fabricação de equipamentos especializados ou de tarefa única:
- Existe uma facilidade para usar equipamentos multifuncionais para fornecer redundância ou backup?
- Qual é a probabilidade de uma mudança nas especificações do produto ou requisitos do cliente?
Essas decisões costumam exigir uma compensação entre as despesas de capital agora e as despesas operacionais potenciais no futuro.
As estratégias de controle e monitoramento são cruciais na produção contínua, onde manter a qualidade dentro de uma linha operacional permite a intervenção oportuna de alertas ou avisos, garantindo uma saída consistente nas especificações:
- Como a amostragem será realizada?
- Usando a tecnologia analítica de processo (PAT), as medições de processo utilizarão sensores para medir os atributos de desempenho do próprio processo ou a qualidade do material bruto em processo que o software pode traduzir nos atributos necessários?
- A amostragem será online, online ou offline?
Cada seleção conduzirá as decisões sobre tecnologia e pessoal, mitigando o risco de produtos não conformes.
3) A fase de implementação
Quando tudo está mapeado, a “única” coisa que resta a fazer é colocar as coisas em movimento. Configurar uma fábrica pode ser um artigo em si, então nem tentaremos lutar com isso aqui.
Durante a fase de implementação, mantenha um forte foco na interconexão dos dispositivos e na tecnologia que você usa. A capacidade de produzir, armazenar, rastrear e analisar dados de ativos será fundamental para otimizar o processo de produção.
Seu software de manutenção deve estar vinculado aos dados de desempenho e condição de ativos, análise preditiva, bem como sistemas de inventário e planejamento. Dessa forma, a preparação antes da manutenção e desligamento garantirá o nivelamento da carga de trabalho, a identificação dos requisitos de habilidade, a disponibilidade de peças sobressalentes e a programação correta de manutenção e atualização.
Resumo
A produção contínua fabrica grandes quantidades de produtos com poucas variações, contando com altos níveis de padronização de processos, procedimentos, ferramentas e equipamentos.
Com o material em movimento contínuo por meio de uma série de operações e uma força de trabalho operando 24 horas por dia, 7 dias por semana, a imposição de custos, os problemas de qualidade e o desperdício de produtos resultantes de paralisações exigem considerações abrangentes de design e manutenção.
Com o tempo de inatividade do equipamento restrito a paradas de manutenção infrequentes, o projeto de uma estratégia de manutenção abrangente - apoiada por coleta e análise direcionada de dados usando um sistema de gerenciamento de manutenção computadorizado moderno - são os componentes mínimos necessários para criar um sistema de produção contínua sustentável.
Paradas de manutenção em uma instalação de produção contínua são sempre eventos de alta pressão.
Devemos isso a nós mesmos e a nossa força de trabalho para garantir que os processos necessários de design, planejamento e programação que empregamos apoiem um evento profissional, eficaz e seguro, restabelecendo os padrões de confiabilidade e desempenho esperados que minimizam o custo total de propriedade e maximizam o desempenho do equipamento.
Manutenção e reparo de equipamentos
- Fabricação vs Produção:Como esses processos diferem
- Como melhorar a saúde e a segurança na fabricação
- Como maximizar a vida útil da máquina e dos componentes na fabricação
- Como manter seu equipamento de fabricação industrial
- O que é um sistema de execução de manufatura (MES)?
- Como reduzir o número de erros e melhorar o sistema de qualidade de produção?
- Como a melhoria contínua pode beneficiar a produtividade da manufatura?
- Como simplificar a fabricação e o envio
- Como financiar equipamentos e ferramentas de fabricação
- Como melhorar a produtividade e a qualidade de fabricação em ambientes industriais